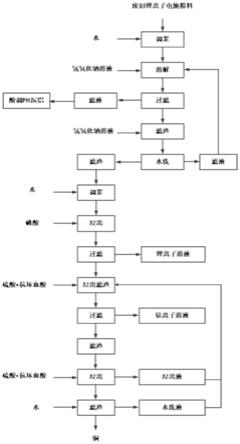
1.本发明涉及废旧钴酸锂电池回收利用技术领域,具体而言,涉及一种废旧钴酸锂电池粉料中有价金属的浸出方法。
背景技术:2.目前废旧钴酸锂离子电池的浸出方法有酸浸法、碱浸
‑
酸浸法、还原浸出法、焙烧水浸法、微生物法和选择性浸出。
3.酸浸法浸出废旧钴酸锂离子电池中的锂和钴浸出时间较长消耗酸较多。且会带入较多的铝杂质,铝杂质含量较高,萃取过程会使p204萃取剂钝化,不利于后续的萃取。还原浸出缺点是反应过程产生二氧化硫有害气体,浸出过程混有较多锂离子、钴离子和铜离子。焙烧水浸法浸出废旧锂离子电池温度较高,能耗较高,易污染。微生物浸出周期长,效率低。
4.鉴于此,特提出本发明。
技术实现要素:5.本发明的目的在于提供一种废旧钴酸锂电池粉料中有价金属的浸出方法,该方法工艺简单、效率高、环保,浸出液杂质含量低。
6.本发明可这样实现:
7.本技术提供一种废旧钴酸锂电池粉料中有价金属的浸出方法,包括以下步骤:
8.浸出铝:将待处理的废旧钴酸锂电池粉料与第一氢氧化钠溶液反应,固液分离,得到第一滤渣和第一滤液;将第一滤渣与第二氢氧化钠溶液反应,固液分离,得到第二滤渣和第二滤液,第一滤液和第二滤液共同作为含铝的第一浸出液,第二滤渣作为第一浸出渣;第一氢氧化钠溶液的浓度高于第二氢氧化钠溶液的浓度且第一氢氧化钠溶液的浓度为2.5
‑
3mol/l;
9.浸出锂:将第一浸出渣与磷酸反应,固液分离,得到第二浸出渣以及含锂的第二浸出液;
10.浸出钴:将第二浸出渣与硫酸及抗坏血酸的混合溶液反应,固液分离,得到第三浸出渣以及含钴的第三浸出液。
11.在可选的实施方式中,上述废旧钴酸锂电池粉料的粒径不超过100目。
12.在可选的实施方式中,第一氢氧化钠溶液与待处理的废旧钴酸锂电池粉料反应的条件包括:第一氢氧化钠溶液与废旧钴酸锂电池粉料的液固比为50
‑
80ml/g,反应时间为2
‑
3h,反应温度为60
‑
80℃。
13.在可选的实施方式中,第一氢氧化钠溶液与待处理的废旧钴酸锂电池粉料反应于搅拌速度为10
‑
50r/min的条件下进行。
14.在可选的实施方式中,第一滤渣与第二氢氧化钠溶液反应的条件包括:第二氢氧化钠溶液的浓度为0.5
‑
1mol/l,第二氢氧化钠溶液与第一滤渣的液固比为50
‑
60ml/g,反应时间为3
‑
4h,反应温度为60
‑
80℃。
15.在可选的实施方式中,第一滤渣与第二氢氧化钠溶液反应于搅拌速度为10
‑
50r/min的条件下进行。
16.在可选的实施方式中,磷酸与第一浸出渣反应的条件包括:磷酸的浓度为0.7
‑
0.9mol/l,反应时间为60
‑
120min,反应温度为45
‑
60℃,磷酸与第一浸出渣的液固比为60
‑
80ml/g。
17.在可选的实施方式中,浸出钴包括:用硫酸及抗坏血酸的混合液与第二浸出渣反应,固液分离,得到第三浸出渣以及含钴的第三浸出液。将硫酸与抗坏血酸的混合溶液与第三滤渣反应,固液分离,得到第四滤渣和第四滤液,第三滤液和第四滤液共同作为含钴的第三浸出液,第四滤渣作为第三浸出渣。
18.在可选的实施方式中,混合溶液与第二浸出渣反应的条件包括:硫酸的浓度为1
‑
3mol/l,抗坏血酸的浓度为0.11
‑
0.3mol/l,硫酸与抗坏血酸的混合溶液与第二浸出渣的液固比为100
‑
150ml/g,反应温度为80
‑
90℃,反应时间为90
‑
100min。
19.在可选的实施方式中,硫酸与抗坏血酸的混合溶液与第三滤渣反应的条件包括:硫酸的浓度为1
‑
3mol/l,抗坏血酸的浓度为0.11
‑
0.3mol/l,硫酸与抗坏血酸的混合溶液与第三滤渣的液固比为100
‑
150ml/g,反应温度为80
‑
90℃,反应时间为90
‑
100min。
20.在可选的实施方式中,还包括:回收第三浸出渣中的铜。
21.在可选的实施方式中,回收铜包括:对第三浸出渣进行水洗,水洗后过滤获得铜片。
22.在可选的实施方式中,对第三浸出渣进行水洗过程中,水洗的液固比为80ml/g,水洗温度为60℃。
23.本技术的有益效果包括:
24.本技术提供的废旧钴酸锂电池粉料中有价金属的浸出方法能有效分步浸出废旧钴酸锂电池粉料中的铝、锂和钴,并可有效回收铜。浸出铝的过程通过碱浸除废旧钴酸锂电池粉料中的金属铝,具体通过采用高低碱(此处的“高低碱”指反应碱的浓度且高碱浓度为2.5
‑
3mol/l)逆流碱浸的方式可降低除铝过程中碱的消耗量并防止在浸出铝的过程中浸出钴酸锂,有利于后续获得较高的钴和锂的回收率。进一步地,通过磷酸对锂进行浸出,可选择性地浸出大部分锂和少许钴,再在硫酸与抗坏血酸的配合下,可浸出大部分钴并在浸出过程使铜沉淀下来,避免铜在该过程中一并浸出,降低酸的消耗量。
25.上述方法工艺简单、效率高、环保,能够降低所用酸和碱的用量,浸出液杂质含量低,铝、钴、锂、铜的回收率均较高。
附图说明
26.为了更清楚地说明本发明实施例的技术方案,下面将对实施例中所需要使用的附图作简单地介绍,应当理解,以下附图仅示出了本发明的某些实施例,因此不应被看作是对范围的限定,对于本领域普通技术人员来讲,在不付出创造性劳动的前提下,还可以根据这些附图获得其他相关的附图。
27.图1为本技术废旧钴酸锂电池粉料中有价金属的浸出方法的流程图。
具体实施方式
28.为使本发明实施例的目的、技术方案和优点更加清楚,下面将对本发明实施例中的技术方案进行清楚、完整地描述。实施例中未注明具体条件者,按照常规条件或制造商建议的条件进行。所用试剂或仪器未注明生产厂商者,均为可以通过市售购买获得的常规产品。
29.下面对本技术提供的废旧钴酸锂电池粉料中有价金属的浸出方法进行具体说明。
30.发明人提出:酸浸法浸出废旧钴酸锂电池粉料中的钴、锂反应时间较长,浸出率较低,浸出过程铝容易浸出到回收溶液中。也有部分采用碱浸
‑
酸浸的方法浸出铝和钴锂,采用碱浸
‑
酸浸法浸出废旧钴酸锂电池粉料可以将铝去除,可避免浸出液铝杂质含量偏高,但是浸出过程容易将钴酸锂浸出,后续酸浸将钴和锂浸出的时间较长。此外,目前工业上使用较多的浸出钴酸锂有价金属的方法中基本采用亚硫酸钠为还原剂,其缺点是反应过程容易产生二氧化硫有害气体,对生产环境要求较高;且后续浸出的溶液中混有较多锂离子、钴离子和铜离子。选择性浸出的方法一方面添加碱溶液浸出铝,该过程容易将钴酸锂浸出,另一方面将废旧钴酸锂电池中含有li、co、cu浸出,该过程需要加入还原剂加快钴的浸出,但铜容易消耗酸浸出到溶液中,使溶液中存在较高浓度的锂离子和钴离子并混有铜离子。不利于后续回收。
31.鉴于此,本技术提出一种废旧钴酸锂电池粉料(废旧钴酸锂电池正极粉末)中有价金属的浸出方法。该废旧钴酸锂电池粉料的粒径不超过100目(孔径约为0.150mm)。
32.参照图1,该浸出方法包括以下步骤:
33.浸出铝:用第一氢氧化钠溶液与待处理的废旧钴酸锂电池粉料反应,固液分离,得到第一滤渣和含铝的第一滤液;将第一滤渣与第二氢氧化钠溶液反应,固液分离,得到第二滤渣和含铝的第二滤液;
34.第一氢氧化钠溶液的浓度高于第二氢氧化钠溶液的浓度且第一氢氧化钠溶液的浓度为2.5
‑
3mol/l;
35.浸出锂:将第一浸出渣与磷酸反应,固液分离,得到第二浸出渣以及含锂的第二浸出液;
36.浸出钴:将第二浸出渣与硫酸及抗坏血酸的混合溶液反应,固液分离,得到第三浸出渣以及含钴的第三浸出液。
37.可参考地,上述浸出铝的过程中,第一氢氧化钠溶液与待处理的废旧钴酸锂电池粉料反应的条件包括:第一氢氧化钠溶液与废旧钴酸锂电池粉料的液固比为50
‑
80ml/g,反应时间为2
‑
3h,反应温度为60
‑
80℃。
38.在一些具体的实施方式中,第一氢氧化钠溶液的浓度可以为2.5mol/l、2.8mol/l或3mol/l等,也可以为2.5
‑
3mol/l范围内的其它任意浓度值。第一氢氧化钠溶液的浓度过高会导致浸出铝的过程在同时浸出钴酸锂。
39.第一氢氧化钠溶液与废旧钴酸锂电池粉料的液固比可以为如50ml/g、60ml/g、65ml/g、70ml/g、75ml/g或80ml/g等,也可以为50
‑
80ml/g范围内的其它任意液固比。上述固液比过低会导致铝浸出量少。
40.第一氢氧化钠溶液与废旧钴酸锂电池粉料的反应时间可以为2h、2.2h、2.5h、2.8h或3h等,也可以为2
‑
3h范围内的其它任意时间值。
41.第一氢氧化钠溶液与废旧钴酸锂电池粉料的反应温度可以为60℃、65℃、70℃、75℃或80℃等,也可以为60
‑
80℃范围内的其它任意温度值。
42.在一些较佳的实施方式中,第一氢氧化钠溶液与待处理的废旧钴酸锂电池粉料反应于搅拌条件下进行。可参考地,搅拌速度可以为10
‑
50r/min,如10r/min、15r/min、20r/min、25r/min、30r/min、35r/min、40r/min、45r/min或50r/min等。
43.可参考地,第一滤渣与第二氢氧化钠溶液反应的条件包括:第二氢氧化钠溶液的浓度为0.5
‑
1mol/l,第二氢氧化钠溶液与第一滤渣的液固比为50
‑
60ml/g,反应时间为3
‑
4h,反应温度为60
‑
80℃。
44.在一些具体的实施方式中,第二氢氧化钠溶液的浓度可以为0.5mol/l、0.8mol/l或1mol/l等,也可以为0.5
‑
1mol/l范围内的其它任意浓度值。
45.第一滤渣与第二氢氧化钠溶液反应的液固比可以为50ml/g、55ml/g或60ml/g等,也可以为50
‑
60ml/g范围内的其它任意液固比。
46.第一滤渣与第二氢氧化钠溶液反应的反应时间可以为3h、3.2h、3.5h、3.8h或4h等,也可以为3
‑
4h范围内的其它任意时间值。
47.第一滤渣与第二氢氧化钠溶液反应的反应温度可以为60℃、65℃、70℃、75℃或80℃等,也可以为60
‑
80℃范围内的其它任意温度值。
48.在一些较佳的实施方式中,第一滤渣与第二氢氧化钠溶液反应于搅拌条件下进行。可参考地,搅拌速度可以为10
‑
50r/min,如10r/min、15r/min、20r/min、25r/min、30r/min、35r/min、40r/min、45r/min或50r/min等。
49.上述浸出铝过程涉及的反应方程式包括:
50.2al+2h2o+2naoh=2naalo2+3h2↑
。
51.上述浸出铝过程通过碱浸除废旧钴酸锂电池粉料中的金属铝,具体通过采用高低碱(此处的“高低碱”指反应碱的浓度)的方式可降低除铝过程中碱的消耗量并防止在浸出铝的过程中浸出钴酸锂,有利于后续获得较高的钴和锂的回收率。当氢氧化钠溶液的浓度超过3mol/l后,会造成钴酸锂的浸出,由于铝大部分存在于电池外壳,而根据电池使用时间和使用环境的影响,仅采用第一氢氧化钠进行浸出,会使得铝浸出不干净,发明人发现通过上述范围的高低碱配合可有效将废旧钴酸锂电池粉料中的金属铝基本浸出完。此外,若采用其它碱,会造成与铝反应慢,甚至几乎不反应的情况(如氢氧化钙)。
52.可参考地,上述浸出锂的过程中,磷酸与第一浸出渣反应的条件包括:磷酸的浓度为0.7
‑
0.9mol/l,磷酸与第一浸出渣的液固比为60
‑
80ml/g,应温度为45
‑
60℃,反应时间为60
‑
120min。
53.在一些具体的实施方式中,磷酸的浓度可以为0.7mol/l、0.75mol/l、0.8mol/l、0.85mol/l或0.9mol/l,也可以为0.7
‑
0.9mol/l范围内的其它任意浓度。
54.磷酸与第一浸出渣的液固比可以为60ml/g、65ml/g、70ml/g、75ml/g或80ml/g等,也可以为60
‑
80ml/g范围内的其它任意液固比。
55.磷酸与第一浸出渣反应的温度可以为45℃、50℃、55℃或60℃等,也可以为45
‑
60℃范围内的其它任意温度值。
56.磷酸与第一浸出渣反应的时间可以为60min、70min、80min、90min、100min、110min或120min等,也可以为60
‑
120min范围内的其它任意时间值。
57.上述浸出锂过程涉及的反应方程式包括:
58.licoo2+xh
+
+po
43
‑
=xli
+
+li1‑
x
coo2+po
43
‑
。
59.值得说明的是,上述浸出锂步骤并非将废旧钴酸锂电池粉料中的所有金属锂浸出,而是将其中大部分的金属锂浸出。本技术通过以低浓度的磷酸对锂进行浸出,可选择性地浸出93wt%以上的锂且该过程只浸出2wt%左右的钴。此外,本技术采用介于强酸和弱酸之间的磷酸,可避免在浸出锂的过程中造成浸出过多钴的情况。
60.可参考地,上述浸出钴可采用二级浸出方式进行,例如可包括:用硫酸及抗坏血酸的混合液与第二浸出渣反应(该步骤可理解为“第一级浸出”步骤),固液分离,得到第三浸出渣以及含钴的第三浸出液。将硫酸与抗坏血酸的混合溶液与第三滤渣反应(该步骤可理解为“第二级浸出”步骤),固液分离,得到第四滤渣和第四滤液,第三滤液和第四滤液共同作为含钴的第三浸出液,第四滤渣作为第三浸出渣。
61.可参考地,上述混合溶液与第二浸出渣反应的条件可包括:硫酸的浓度为1
‑
3mol/l,抗坏血酸的浓度为0.11
‑
0.3mol/l,第一混合溶液与第二浸出渣的液固比为100
‑
150ml/g,反应温度为80
‑
90℃,反应时间为90
‑
100min。
62.在一些具体的实施方式中,硫酸的浓度可以为1mol/l、1.5mol/l、2mol/l、2.5mol/l或3mol/l等,也可以为1
‑
3mol/l范围内的其它浓度值。
63.抗坏血酸的浓度可以为0.11mol/l、0.15mol/l、0.2mol/l、0.25mol/l或0.3mol/l等,也可以为0.11
‑
0.3mol/l范围内的其它浓度值。
64.第一混合溶液与第二浸出渣的液固比可以为100ml/g、110ml/g、120ml/g、130ml/g、140ml/g或150ml/g等,也可以为100
‑
150ml/g范围内的其它任意液固比。
65.上述混合溶液与第二浸出渣反应的温度可以为80℃、85℃或90℃等,也可以为80
‑
90℃范围内的其它温度值。
66.上述混合溶液与第二浸出渣反应的时间可以为90min、95min或100min等,也可以为90
‑
100min范围内的其它时间值。
67.类似地,硫酸与抗坏血酸的混合溶液与第三滤渣反应的条件包括:硫酸的浓度为1
‑
3mol/l(如1mol/l、1.5mol/l、2mol/l、2.5mol/l或3mol/l等),抗坏血酸的浓度为0.11
‑
0.3mol/l(如0.11mol/l、0.15mol/l、0.2mol/l、0.25mol/l或0.3mol/l等),硫酸与抗坏血酸的混合溶液与第三滤渣的液固比为100
‑
150ml/g(如100ml/g、110ml/g、120ml/g、130ml/g、140ml/g或150ml/g等),反应温度为80
‑
90℃(如80℃、85℃或90℃等),反应时间为90
‑
100min(如90min、95min或100min等)。
68.上述浸出钴过程涉及的反应方程式包括:
69.licoo2+xh
+
=xli
+
+li1‑
x
coo2+xe
‑
;
70.li1‑
x
coo2+4h
+
+(1
‑
x)e
‑
=(1
‑
x)li
+
+co
2+
+2h2o;
71.c6h8o6+2licoo2+6h
+
=c6h6o6+2li++2co
2+
+4h2o;
72.c6h8o6+cu
2+
=c6h6o6+2h
+
+cu。
73.上述过程中,在上述浓度的硫酸与抗坏血酸的配合下,可以浸出98wt%以上的钴并在浸出过程使铜沉淀下来,避免铜在该过程中一并浸出,降低酸的消耗量。值得说明的是,若以盐酸代替硫酸会导致酸雾产生,而采用其它有机酸会导致浸出速率缓慢。若以其它还原试剂如焦亚硫酸钠代替抗坏血酸不但会产生二氧化硫而且还会在浸出钴的过程中浸
出部分铜,本技术中使用的抗坏血酸有利于使高价的钴还原成低价的钴,提高钴的浸出率,并将二价铜还原成铜单质。
74.进一步地,还可回收第三浸出渣中的铜。可参考地,回收铜包括:对第三浸出渣进行水洗,过滤后获得铜片。
75.可参考地,对第三浸出渣进行水洗过程中,水洗的液固比可以为80ml/g,水洗温度可以为60℃。
76.承上,本技术提供的废旧钴酸锂电池粉料中有价金属的浸出方法至少较现有技术具有以下优势:降低碱的消耗量及溶液中铝杂质的含量,防止钴酸锂浸出;降低酸的消耗,节能环保,可以避免溶液中含有so2;选择性浸出锂和钴,避免铜的浸出,后续可进一步回收铜。
77.以下结合实施例对本发明的特征和性能作进一步的详细描述。
78.实施例1
79.本实施例提供一种废旧钴酸锂电池粉料中有价金属的浸出方法,其采用高低碱
‑
磷酸与硫酸选择性还原浸出工艺流程进行。将拆解后的废旧钴酸锂电池过100目的筛子,获得100目以下废旧钴酸锂电池粉料,其化学元素含量如表1所示。
80.表1
[0081][0082][0083]
将100目以下的废旧钴酸锂电池粉料通过水进行调浆。
[0084]
将上述调浆后的浆料进行浸出铝操作以将易溶于氢氧化钠的大部分铝浸出:
[0085]
将浆料与第一氢氧化钠溶液反应,固液分离,得到第一滤渣和第一滤液;将第一滤渣与第二氢氧化钠溶液反应,固液分离,得到第二滤渣和第二滤液。第一滤液和第二滤液共同作为含铝的第一浸出液,第二滤渣作为第一浸出渣。
[0086]
上述浆料与第一氢氧化钠溶液反应的条件包括:第一氢氧化钠溶液的浓度为2.5mol/l,液固比为60ml/g、时间为2h、温度为60℃,搅拌速度为45r/min。第一滤渣与第二氢氧化钠溶液反应的条件包括:第二氢氧化钠溶液的浓度为0.6mol/l,液固比为50ml/g,时间为3h,温度为70℃,搅拌速度为45r/min。
[0087]
第一滤液(也即第一级碱浸浸出液)中金属铝的浓度见表2。
[0088]
表2
[0089]
元素allico浓度(g/l)2.30.0050.009
[0090]
第二滤渣(也即第二滤渣或第二级碱浸后废旧电池粉料渣)中金属质量百分比如表3。
[0091]
表3
[0092]
元素licoalcu
质量百分比(%)9.5639.960.124.12
[0093]
将第一浸出渣与磷酸反应,固液分离,得到第二浸出渣以及含锂离子浓度较高的第二浸出液。
[0094]
磷酸与第一浸出渣反应的条件包括:磷酸的浓度为0.8mol/l,液固比70ml/g,反应时间为80min,反应温度为55℃。
[0095]
第二浸出液中金属离子浓度见表4。
[0096]
表4
[0097]
元素licoalcu浓度(g/l)11.690.2630.0020.003
[0098]
将第二浸出渣与硫酸及抗坏血酸的混合溶液反应(第一级浸出),固液分离,得到第三滤渣和含钴的第三滤液;将硫酸与抗坏血酸的混合溶液与第三滤渣反应(第二级浸出),固液分离,得到第四滤渣和第四滤液,第三滤液和第四滤液共同作为含钴离子浓度较高的第三浸出液,第四滤渣作为第三浸出渣。
[0099]
第一级浸出的条件为:硫酸的浓度为2mol/l,抗坏血酸(c6h8o6)的浓度为0.2mol/l,液固比为100ml/g,浸出温度为80℃,浸出时间90min。
[0100]
第二级浸出的条件为:硫酸的浓度为2mol/l,抗坏血酸(c6h8o6)的浓度为0.2mol/l,液固比为100ml/g,浸出温度为80℃,浸出时间90min。
[0101]
第三浸出液中金属离子浓度见表5。
[0102]
表5
[0103]
元素licoalcu浓度(g/l)0.0930.080.00520.009
[0104]
对第三浸出渣进行水洗,回收铜。
[0105]
回收铜后,水洗液中金属渣含量见表6。
[0106]
表6
[0107]
元素licoalcu含量(%)0.00520.00560.0063.98
[0108]
实施例2
[0109]
本实施例提供一种废旧钴酸锂电池粉料中有价金属的浸出方法,其采用高低碱
‑
磷酸与硫酸选择性还原浸出工艺流程进行,具体流程如图1所示。将拆解后的废旧钴酸锂电池过100目的筛子,获得100目以下废旧钴酸锂电池粉料,其化学元素含量如表7所示。
[0110]
表7
[0111][0112]
将100目以下的废旧钴酸锂电池粉料通过水进行调浆。
[0113]
将上述调浆后的浆料进行浸出铝操作以将易溶于氢氧化钠的大部分铝浸出:
[0114]
将浆料与第一氢氧化钠溶液反应,固液分离,得到第一滤渣和第一滤液;将第一滤渣与第二氢氧化钠溶液反应,固液分离,得到第二滤渣和第二滤液。第一滤液和第二滤液共同作为含铝的第一浸出液,第二滤渣作为第一浸出渣。
[0115]
上述浆料与第一氢氧化钠溶液反应的条件包括:第一氢氧化钠溶液的浓度为3mol/l,液固比为70ml/g、时间为2.5h、温度为70℃,搅拌速度为50r/min。第一滤渣与第二氢氧化钠溶液反应的条件包括:第二氢氧化钠溶液的浓度为0.8mol/l,液固比为55ml/g,时间为3.5h,温度为75℃,搅拌速度为50r/min。
[0116]
第一滤液(也即第一级碱浸浸出液)中金属铝的浓度见表8。
[0117]
表8
[0118]
元素allico浓度(g/l)2.10.0030.008
[0119]
第二滤渣(也即第二滤渣或第二级碱浸后废旧电池粉料渣)中金属质量百分见表9。
[0120]
表9
[0121]
元素licoalcu质量百分比(%)9.3240.020.164.17
[0122]
将第一浸出渣与磷酸反应,固液分离,得到第二浸出渣以及含锂离子浓度较高的第二浸出液。
[0123]
磷酸与第一浸出渣反应的条件包括:磷酸的浓度为0.9mol/l,液固比75ml/g,反应时间为90min,反应温度为60℃。
[0124]
第二浸出液中金属离子浓度见表10。
[0125]
表10
[0126]
元素licoalcu浓度(g/l)11.520.2120.00320.005
[0127]
将第二浸出渣与硫酸及抗坏血酸的混合溶液反应(第一级浸出),固液分离,得到第三滤渣和含钴的第三滤液;将硫酸与抗坏血酸的混合溶液与第三滤渣反应(第二级浸出),固液分离,得到第四滤渣和第四滤液,第三滤液和第四滤液共同作为含钴离子浓度较高的第三浸出液,第四滤渣作为第三浸出渣。
[0128]
第一级浸出的条件为:硫酸的浓度为2.5mol/l,抗坏血酸(c6h8o6)的浓度为0.25mol/l,液固比为120ml/g,浸出温度为85℃,浸出时间95min。
[0129]
第二级浸出的条件为:硫酸的浓度为2.5mol/l,抗坏血酸(c6h8o6)的浓度为0.25mol/l,液固比为120ml/g,浸出温度为85℃,浸出时间95min。
[0130]
第三浸出液中金属离子浓度见表11。
[0131]
表11
[0132]
元素licoalcu浓度(g/l)0.07630.890.0050.008
[0133]
对第三浸出渣进行水洗,回收铜。
[0134]
回收铜后,水洗液中金属渣含量见表12。
[0135]
表12
[0136]
元素licoalcu含量(%)0.00920.00320.00864.01
[0137]
综上,本技术提供的废旧钴酸锂电池粉料中有价金属的浸出方法工艺简单、效率高、环保,能够降低所用酸和碱的用量,浸出液杂质含量低,铝、钴、锂、铜的回收率均较高。
[0138]
以上仅为本发明的优选实施例而已,并不用于限制本发明,对于本领域的技术人员来说,本发明可以有各种更改和变化。凡在本发明的精神和原则之内,所作的任何修改、等同替换、改进等,均应包含在本发明的保护范围之内。