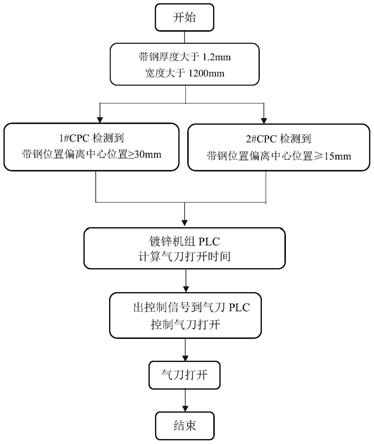
1.本发明涉及一种控制方法,尤其是涉及一种用于带钢在炉内跑偏后气刀自动打开的控制方法,属于轧钢生产工艺技术领域。
背景技术:2.cpc和气刀功能简介:退火炉内一般设置有一至两套cpc检测装置。cpc检测装置是用来检测带钢是否偏离机组的中心线以及计算出带钢的跑偏量,如果是一台cpc检测装置,则将其安装在距离气刀至少200米,如果是两台cpc检测装置,则将第二台cpc检测装置安装装在距离气刀60米;气刀位于锌锅后方,主要喷吹空气或者氮气,带钢出锌锅后经气刀吹扫刮掉多余的锌液,所以气刀吹扫的目的是控制带钢的锌层厚度,同时气刀两边带有边部挡板,作用是防止边部气流对冲以及防止边部锌液飞溅。
3.带钢炉内跑偏后气刀自动打开的控制系统介绍:机组生产时带钢从气刀前后刀体之间穿过,且带钢与两刀体和边部挡板的位置很近,生产中的带钢会发生偏离机组中心线运行的情况,通过退火炉加热后更容易引起跑偏。现有技术中,当焊缝经过气刀时操作人员手动移开气刀和边缘挡板,但是气刀刀架离带钢位置近,当带钢跑偏后再手动打开气刀和边缘挡板来不及操作,带钢容易挂在边缘挡板和气刀处,引起带钢挂裂断带。
技术实现要素:4.本发明所要解决的技术问题是:提供一种能有效的降低带钢跑偏后在气刀处被挂裂断带的用于带钢在炉内跑偏后气刀自动打开的控制方法。
5.为解决上述技术问题所采用的技术方案是:一种用于带钢在炉内跑偏后气刀自动打开的控制方法,所述的控制方法先通过安装在退火炉内的检测装置检测带钢在退火炉内的跑偏量,然后再依据跑偏量适时起动计算程序计算当前跑偏位置到达气刀的时间,最后根据计算获得的时间到点控制气刀的打开完成气刀的控制工作。
6.进一步的是,所述的检测装置至少包括一组cpc位置检测组件,所述的cpc位置检测组件沿带钢移动方向布置在所述的退火炉中,计算程序起动计算的时间节点通过cpc位置检测组件检测到的带钢的跑偏量确定。
7.上述方案的优选方式是,所述的cpc位置检测组件为两组,两组所述的cpc位置检测组件沿带钢移动方向顺序的布置在所述的退火炉中,计算程序起动计算的时间节点至少满足一组cpc位置检测组件检测到的带钢的跑偏量。
8.进一步的是,两组所述的cpc位置检测组件在退火炉内安装的位置距离气刀的位置分别为250米和54米,两组cpc位置检测组件检测到的带钢跑偏的量分别达到30mm或15mm,并延时5秒输出气刀打开指示。
9.上述方案的优选方式是,每一组所述的cpc位置检测组件还包括emg控制器,cpc位置检测组件的检测部件检测到的带钢的跑偏量通过所述的emg控制器传递给计算程序。
10.进一步的是,所述的计算程序镶嵌在智能控制中心的plc可编程输入模块上,cpc
位置检测组件的emg控制器和气刀的控制系统分别同时与所述的plc可编程输入模块连接。
11.上述方案的优选方式是,在通过计算程序计算当前跑偏位置到达气刀的时间时需要的机组中心辊的转速,通过连入plc可编程输入模块内的机组中心辊转速测量装置测定。
12.进一步的是,所述的机组中心辊转速测量装置为与电机连接的脉冲编码器,所述的脉冲编码器信息输送端与plc可编程输入模块连接。
13.进一步的是,被检测的带钢的厚度不低1.2mm,宽度不低于1200mm,打开气刀的指令相对于计算获得的时间节延时两秒发出。
14.本发明的有益效果是:本技术提供的控制方法以现有安装在退火炉内的检测装置为基础,通过将其检测到的带钢在退火炉内的跑偏量在计算程序的配合下计算出当前跑偏位置到达气刀的时间,然后根据计算获得的时间到点控制气刀的打开完成气刀的控制工作。这样改变了现有技术中在通过检测装置检测到带钢跑偏后,需要通过人工进行估计然后再打开气刀的操作,达到能有效的降低带钢在吹扫过程中因跑偏被挂裂断带的目的。
附图说明
15.图1为本发明控制方法涉及到的流程图。
具体实施方式
16.为了解决现有技术中存在的上述技术问题,本发明提供了一种能有效的降低带钢跑偏后在气刀处被挂裂断带的控制方法。所述的控制方法先通过安装在退火炉内的检测装置检测带钢在退火炉内的跑偏量,然后再依据跑偏量适时起动计算程序计算当前跑偏位置到达气刀的时间,最后根据计算获得的时间到点控制气刀的打开完成气刀的控制工作。本技术提供的控制方法以现有安装在退火炉内的检测装置为基础,通过将其检测到的带钢在退火炉内的跑偏量在计算程序的配合下计算出当前跑偏位置到达气刀的时间,然后根据计算获得的时间到点控制气刀的打开完成气刀的控制工作。这样改变了现有技术中在通过检测装置检测到带钢跑偏后,需要通过人工进行估计然后再打开气刀的操作,达到能有效降低带钢跑偏后在气刀处被挂裂断带的目的。
17.上述实施方式中,为了提高检测的准确性,所述的检测装置至少包括一组cpc位置检测组件,所述的cpc位置检测组件沿带钢移动方向布置在所述的退火炉中,计算程序起动计算的时间节点通过cpc位置检测组件检测到的带钢的跑偏量确定。此时,所述的cpc位置检测组件优选为两组,两组所述的cpc位置检测组件沿带钢移动方向顺序的布置在所述的退火炉中,计算程序起动计算的时间节点至少满足一组cpc位置检测组件检测到的带钢的跑偏量。并且将两组所述的cpc位置检测组件在退火炉安装的位置距离气刀的位置分别为250米和54米,两组cpc位置检测组件检测到的带钢跑偏的量分别达到30mm或15mm,并延时5秒输出气刀打开指示。
18.进一步的,为了提高计算的准确性,同时提高控制的精准性,每一组所述的cpc位置检测组件还包括emg控制器,cpc位置检测组件的检测部件检测到的带钢的跑偏量通过所述的emg控制器传递给计算程序;以及本技术将所述的计算程序镶嵌在智能控制中心的plc可编程输入模块上,cpc位置检测组件的emg控制器和气刀的控制系统分别同时与所述的plc可编程输入模块连接。相应的,在通过计算程序计算当前跑偏位置到达气刀的时间时需
要的机组中心辊的转速,通过连入plc可编程输入模块内的机组中心辊转速测量装置测定。优选的方式为,所述的机组中心辊转速测量装置为与电机连接的脉冲编码器,所述的脉冲编码器信息输送端与plc可编程输入模块连接。
19.根据实际需要,本技术被检测的带钢的厚度不低1.2mm,宽度不低于1200mm,打开气刀的指令相对于计算获得的时间节延时两秒发出。
20.本技术所述的计算程序可以是plc供应商根据客户要求事先嵌入的软件程序,也可以是用户根据需要自行编写的代码程度。
21.综上所述,本技术提供的控制方法可以应用到各类涂镀机组,当带钢在退火炉跑偏时,由炉内检测装置epc检测到的跑偏量在机组plc做控制程序,判断是否打开气刀,当给出气刀打开信号时,再跟踪带钢位置,当跑偏带钢移动到气刀时,气刀刀体和边部挡板向外横移打开,保证了带钢不会在气刀处挂断停机。
22.实施例一
23.如图1所示,本技术提供的控制系统在带钢经过退火炉时,带钢规格满足的条件为带钢厚度大于1.2mm、宽度大于1200mm时(此规格的带钢跑偏后易挂断,且造成的质量损失较大,故障处理难度较大,检测到跑偏量大于设定条件,即1#cpc处检测带钢偏移量大于等于30mm,2#cpc处检测带钢偏移量大于等于15mm,cpc的emg控制器接收到数据后将信号传送到镀锌机组的可编程控制器plc中,通过西门子的s7程序块进行计算,即机组plc根据当前跑偏位置距离气刀的距离即250m或者54m与5#s辊的2#张力辊速度即机组中心辊速度计算出跑偏位置到达气刀的时间,到达计算时间后再将打开指令传送到气刀plc的输入模块中,控制气刀前后刀体和边部挡板进行打开动作。
24.效益计算:
25.断带损失/年=损失金额/次
×
断带次数/年=66.67万元/次
×
3次≈200万元/年。
26.统计历史数据发现实施此改进前每年于气刀处断带次数约为3次,机组停机造成的生产损失、断带造成的质量损失以及退火炉等处造成的介质损失等,每次断带损失约为67万元/次,即200万元/年;改进实施后未在气刀处发生过断带,所以此项改进预计收益为每年200万元。