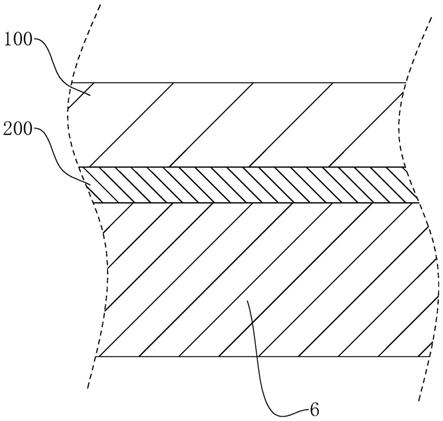
1.本技术涉及氮化物涂层的领域,更具体地说,它涉及一种氮化物涂层制备方法、氮化物涂层及其应用。
背景技术:2.物理气相沉积法(physical vapor deposition,简称:pvd)制备涂层,顾名思义是以物理的方式,通过物质产生相变化而制备涂层的技术。如蒸镀是藉由蒸镀源将欲涂层的固体靶材加热至变成气态后使之涂层在基材表面上的一项技术。而溅镀则通过高能量的原子碰撞靶材并产生动量转移现象,将靶材原子轰击出来并沉积于基材表面而形成涂层。工具镀所使用大多为多弧离子镀的方式,其采用电弧放电的方法,从固体的靶材上直接蒸发金属离子,并沉积到基材表面形成涂层。
3.氮化物涂层作为一层覆盖在基体材料外的固态连续膜,由于多具有较高的硬度,而在切削刀具等领域有着广泛的使用。氮化物涂层可由多弧离子镀、磁控溅射等方式制得。如通过多弧离子镀的方式可制得tin、crn、altin、ticn、alcrsin及tisicn等氮化物涂层。
4.目前,随着工业加工向高速化发展,对切削刀具的要求越来越严苛;通常要求切削刀具具有高硬度、高耐磨性与耐高温性,使刀具具有良好的切削稳定性,并增加刀具的加工寿命。因此,对于镀制在刀具表面,起增硬耐磨作用的氮化物涂层也提出了更高的要求;制备具有高硬度、高耐磨性以及耐高温的氮化物涂层,以使切削刀具具有良好的切削稳定性和使用寿命成了目前研究的热点之一。
技术实现要素:5.为了能制备出具有高硬度、高耐磨性以及耐高温的氮化物涂层,使刀具在加工过程中保持良好的切削稳定性,并增加刀具表面的耐磨保护性,进而增加刀具加工寿命,本技术提供一种氮化物涂层制备方法、氮化物涂层及其应用。
6.第一方面,本技术提供一种氮化物涂层制备方法,采用如下的技术方案:氮化物涂层制备方法,包括:采用多弧离子镀在基材上镀制cr中间过渡层;将多弧离子镀电源接连alcrwsi靶,磁控溅射电源接连alcrsi靶;多弧离子镀和磁控溅射同时作用,在基材上镀制alcrsiwn功能层。
7.通过采用上述技术方案,多弧离子镀电源接连alcrwsi靶,藉由多弧离子源的高能量而获得大量的等离子体进而形成高纯度氮化物薄膜,使氮化物涂层具有良好的致密性与高硬度。另一方面,以磁控溅射电源接连alcrsi靶,相较于多弧离子镀,溅射电源能量较低,可以对alcrsiwn功能层的成分进行优化微调,使alcrsiwn功能层中的钨元素和硅元素达到较佳配比进而提高了氮化物涂层的硬度、耐磨性以及耐高温性。同时,使用多弧离子镀技术镀制cr中间过渡层,可以提高alcrsiwn功能层和基材之间的结合性,从而进一步提高了氮化物涂层的硬度、耐磨性以及耐高温性。
8.可选的,所述alcrwsi靶的电流控制在45~65a,所述alcrsi靶的电流控制在0.8~1.2a。
9.通过采用上述技术方案,随着alcrwsi靶电流的提高,alcrsiwn功能层中钨元素的含量提高,从而提高了氮化物涂层的韧性使刀具在加工过程中可承受更多振动而不易崩损,对提高氮化物涂层及刀具的耐磨性和使用寿命具有积极意义。另一方面,随着alcrsi靶电流的提高,alcrsiwn功能层中硅元素的含量增加,硅能够在氮化物涂层内形成一层非晶态的sin
x
,该层sin
x
具有抑止晶粒成长使氮化物涂层结构致密的功能,从而有利于氮化物涂层硬度的提高,同时也能够有效改善氮化物涂层的耐高温氧化能力,赋予氮化物涂层良好的耐高温性能。通过对alcrwsi靶电流和alcrsi靶电流的配伍,可以获得具有高硬度、高耐磨性以及耐高温的氮化物涂层;同时也利于改善氮化物涂层表面的粗糙度。
10.可选的,镀制所述alcrsiwn功能层时:工作气氛为氮气,工作压力为1
×
10
‑2~3
×
10
‑2mbar,工作温度为300~450℃,基材偏压为
‑
100~
‑
50v。
11.通过采用上述技术方案,优化了控制参数,有利于获得更好性能的氮化物涂层。
12.可选的,镀制所述alcrsiwn功能层的时间为40~80min。
13.通过采用上述技术方案,镀制时间在40~80min的范围内,有利于获得性能优良的氮化物涂层。
14.可选的,镀制所述cr中间过渡层时:工作气氛为氩气,工作压力为3
×
10
‑2~5
×
10
‑2mbar,工作温度为350~500℃,靶材为cr,靶材电流为40~60a,基材偏压为
‑
80~
‑
50v,镀制时间为4~8min。
15.可选的,采用多弧离子镀在镀制所述cr中间过渡层前对基材进行金属离子刻蚀;对基材进行金属离子刻蚀时:工作气氛为氩气,氩气流速为100~120sccm,工作压力为3
×
10
‑2~5
×
10
‑2mbar,靶材为cr,靶材电流为45~55a,基材偏压为
‑
575~
‑
525v,刻蚀时间为5~15min。
16.通过采用上述技术方案,通过多弧离子镀技术而获得大量等离子并轰击基材,对基材表面进行金属离子刻蚀,有利于使基材表面活化,从而有利于后续氮化物涂层的镀制以及氮化物涂层与基材的结合。
17.可选的,还包括:在对基材进行金属离子刻蚀前对其进行氩离子辉光清洁;氩离子辉光清洁时:氩气流速为90~120sccm,工作压力为3
×
10
‑2~5
×
10
‑2mbar,基材偏压为
‑
575~
‑
525v,清洁时间为3~8min。
18.通过采用上述技术方案,去除基材表面的碳氢氧化合物,有利于提高氮化物涂层与基材的结合性。
19.第二方面,本技术提供一种氮化物涂层,采用如下的技术方案:氮化物涂层,采用上述氮化物涂层制备方法制得;所述氮化物涂层包括alcrsiwn功能层以及设置在alcrsiwn功能层和基材之间的cr中间过渡层。
20.通过采用上述技术方案,cr中间过渡层的设置提高了alcrsiwn功能层与基材的结合性。
21.可选的,所述alcrsiwn功能层中硅含量为8~12at.%、钨含量为3~5at.%。
22.第三方面,本技术提供一种刀具,采用如下的技术方案:刀具,表面镀制有上述氮化物涂层。
23.通过采用上述技术方案,通过氮化物涂层的镀制,提高了刀具的硬度、耐磨性以及耐高温性,从而使刀具在加工过程中保持良好的切削稳定性,并增加了刀具加工的寿命。
24.综上所述,本技术至少具有以下有益技术效果之一:1、本技术所制得的氮化物涂层具有较高的硬度、较佳的耐磨性以及较好的耐高温性;将该氮化物涂层镀制在刀具上,赋予了刀具良好的硬度、耐磨性和耐高温性,使刀具在加工过程中能保持良好的切削稳定性,同时还增加了刀具的使用寿命。
25.2、本技术将多弧离子镀电源接连alcrwsi靶、将磁控溅射电源接连alcrsi靶;通过两者的协同作用,制得了兼具硬度、耐磨性以及耐高温性的alcrsiwn功能层。
26.3、本技术通过cr中间过渡层的制备,提高了alcrsiwn功能层和基材的结合性,从而进一步提高了氮化物涂层的性能。
27.4、本技术在镀制氮化物前对基材表面进行清洁处理和金属离子刻蚀处理,通过具有足够动能的等离子体对基材表面的冲击,清洁了基材表面的碳氢氧化合物并使表面活性化。
附图说明
28.图1是本技术实施例1中制备氮化物涂层所用设备的正视结构示意图。
29.图2是本技术实施例1中制备氮化物涂层所用设备的俯视结构示意图。
30.图3是本技术实施例1中的氮化物涂层的结构示意图。
31.附图标记说明:1、工作腔;2、基材旋转支架;21、基材旋转台;3、cr靶;4、alcrwsi靶;5、alcrsi靶;6、刀具;100、alcrsiwn功能层;200、cr中间过渡层。
具体实施方式
32.多弧离子镀具有较高的能量,可以获得大量的等离子体进而形成高纯度的涂层主体;磁控溅射电源相较于多弧离子镀,能量较低,可以对涂层的成分进行优化微调;通过两者的协作配合,可获得综合性能好的氮化物涂层。本技术就是在此基础上得出的。
33.以下结合附图1
‑
3以及实施例对本技术作进一步详细说明。
34.实施例所用的相关原材料中:cr靶的纯度99.9wt.%;alcrwsi靶的合金质量比为al:cr:w:si为13:4:2:1;alcrsi靶的合金质量比为al:cr:si为6:3:1。
35.实施例1本技术实施例公开了一种氮化物涂层制备方法,包括以下步骤:s1、将基材置于工作腔内;对工作腔内抽真空到5
×
10
‑4mbar,之后加热工作腔到400℃,预热60min。
36.在本实施方案中,基材具体为4刃立铣刀,其材质为碳化钨硬质合金;刀具规格为ф6
×
f4。在其他的实施方案中,基材也可为其他常规硬质合金刀具、陶瓷刀具或不锈钢刀具。
37.s2、保持工作腔内的温度;向工作腔内通入流速为50sccm的氩气,控制工作腔内压力为4
×
10
‑2mbar。将多弧离子镀电源接连cr靶,打开多弧离子镀电源,并控制cr靶的电流为50a;同时打开负偏压电源,控制基材的偏压为
‑
60v;采用多弧离子镀的方式在基底材料上沉积cr,而形成cr中间过渡层,镀制时间为5min。
38.s3、保持工作腔内的温度;向工作腔内通入流速为70sccm的氮气,控制工作腔内压力为2
×
10
‑2mbar。将多弧离子镀电源接连alcrwsi靶,磁控溅射电源接连alcrsi靶;同时打开多弧离子镀电源和磁控溅射电源,并控制alcrwsi靶的电流为45a、alcrsi靶的电流为1a;另外,基材的偏压控制为
‑
60v。利用高能量的多弧离子镀源(接连多弧离子镀电源的alcrwsi靶)获得大量等离子体而构成纯度高、结构致密、硬度高的涂层主体;同时利用相对能量较低的磁控溅射源(接连磁控溅射电源的alcrsi靶)调节涂层的成分;通过两者的共同作用,逐渐在cr中间过渡层上形成alcrsiwn功能层。alcrsiwn功能层的镀制时间控制在60min。
39.s4、镀制结束后,关闭多弧离子镀电源、磁控溅射电源等电源,停止通入气体;停止对工作腔的加热,待工作腔温度降至120℃后开启工作腔,取出基材,完成氮化物涂层在基材上的制备。
40.本技术实施例中制备氮化物涂层所使用设备的简易示意图如图1和图2。该设备包括工作腔1、基材旋转支架2、cr靶3、alcrwsi靶4以及alcrsi靶5。其中,基材旋转支架2竖直设置在工作腔1中;通过常规的电机驱动,可使基材旋转支架2绕其轴线旋转。基材旋转支架2上均布有多个圆盘形的且由电机驱动的基材旋转台21,基材旋转台21的转动轴线的延伸方向与竖直方向一致。多个作为基材的刀具6竖直地安装在基材旋转台21上,且沿基材旋转台21的周向均匀排布。
41.cr靶3、alcrwsi靶4及alcrsi靶5均设置在工作腔1的内侧壁上,且每一个alcrsi靶5均仅对应于一个cr靶3或一个alcrwsi靶4。每一个alcrsi靶5与所对应的cr靶3或alcrwsi靶4对称设置在基材旋转支架2的相对两侧;该设置可以减少等离子体之间由于相互干扰而形成的偏折问题。
42.需要说明的是,上述设备中其他部件,如各个电源、进气阀、加热部件等均为常规设置,在此不做赘述。
43.本技术实施例还公开了一种氮化物涂层,该涂层由上述氮化物涂层制备方法制得。参照图3,该氮化物涂层包括直接贴合在刀具6上的cr中间过渡层200以及贴合在cr中间过渡层200上的alcrsiwn功能层100。其中,cr中间过渡层200起到提升alcrsiwn功能层100和刀具6结合性的作用。
44.本技术实施例还公开了一种刀具,其表面镀制有上述氮化物涂层制备方法得到的氮化物涂层;经过对304不锈钢(硬度hrb80)90min的切削测试,该刀具刀刃的磨损量为0.0996mm,显示出良好的耐磨性。其中,切削测试的试验条件为:转速(s)为8500、切削速度(v
c
)为160m/min、进给速度(f)为1600mm/min、每齿进给量(f
z
)为0.05mm/r、切深(a
p
)为5mm、切宽(a
e
)为0.15mm、切削方式为侧铣跟随周边、冷却方式为冷却液冷却。
45.实施例2本技术实施例与实施例1基本相同,不同之处在于:本实施方案中,在氮化物涂层的制备方法中,在镀制cr中间过渡层之前,对基材进行金属离子刻蚀。
46.具体步骤如下:s1、将作为基材的4刃立铣刀置于工作腔内;对工作腔内抽真空到5
×
10
‑4mbar,之后加热工作腔到400℃,预热60min。
47.s2、保持工作腔内的温度;向工作腔内通入流速为100sccm的氩气,控制工作腔内
压力为4
×
10
‑2mbar。将多弧离子镀电源接连cr靶,打开多弧离子镀电源,并控制cr靶的电流为50a;同时打开负偏压电源,控制基材的偏压为
‑
550v;采用多弧离子镀对刀具表面进行金属离子刻蚀10min,使刀具表面活化,有利于后续cr中间过渡层的镀制。
48.s3、保持工作腔内的温度;向工作腔内通入流速为50sccm的氩气,控制工作腔内压力为4
×
10
‑2mbar。将多弧离子镀电源接连cr靶,打开多弧离子镀电源,并控制cr靶的电流为50a;同时打开负偏压电源,控制基材的偏压为
‑
60v;采用多弧离子镀的方式在基底材料上沉积cr,而形成cr中间过渡层,镀制时间为5min。
49.s4、保持工作腔内的温度;向工作腔内通入流速为70sccm的氮气,控制工作腔内压力为2
×
10
‑2mbar。将多弧离子镀电源接连alcrwsi靶,磁控溅射电源接连alcrsi靶;同时打开多弧离子镀电源和磁控溅射电源,并控制alcrwsi靶的电流为45a、alcrsi靶的电流为1a;另外,基材的偏压控制为
‑
60v。通过多弧离子镀和磁控溅射的共同作用,逐渐在cr中间过渡层上形成alcrsiwn功能层。alcrsiwn功能层的镀制时间控制在60min。
50.s5、镀制结束后,关闭多弧离子镀电源、磁控溅射电源等电源,停止通入气体;停止对工作腔的加热,待工作腔温度降至120℃后开启工作腔,取出基材,完成氮化物涂层在基材上的制备。
51.实施例3本技术实施例和实施例2基本相同,不同之处在于:本实施方案中,在氮化物涂层的制备方法中,在对基材进行金属离子刻蚀前先对其进行氩离子辉光清洁。
52.具体步骤如下:s1、将作为基材的4刃立铣刀置于工作腔内;对工作腔内抽真空到5
×
10
‑4mbar,之后加热工作腔到400℃,预热60min。
53.s2、保持工作腔内的温度;向工作腔内通入流速为100sccm的氩气,控制工作腔内压力为4
×
10
‑2mbar。打开负偏压电源,控制基材的偏压为
‑
550v;采用氩离子辉光放电,对刀具进行离子轰击辉光清洗5min,去除刀具表面的碳氢氧化合物,利于后续镀制工序。
54.s3、保持工作腔内的温度;保持向工作腔内通入氩气的流速,并保持工作腔内压力。将多弧离子镀电源接连cr靶,打开多弧离子镀电源,并控制cr靶的电流为50a;同时打开负偏压电源,控制基材的偏压为
‑
550v;采用多弧离子镀对刀具表面进行金属离子刻蚀10min,使刀具表面活化,有利于后续cr中间过渡层的镀制。
55.s4、保持工作腔内的温度;向工作腔内通入流速为50sccm的氩气,控制工作腔内压力为4
×
10
‑
2 mbar。将多弧离子镀电源接连cr靶,打开多弧离子镀电源,并控制cr靶的电流为50a;同时打开负偏压电源,控制基材的偏压为
‑
60v;采用多弧离子镀的方式在基底材料上沉积cr,而形成cr中间过渡层,镀制时间为5min。
56.s5、保持工作腔内的温度;向工作腔内通入流速为70sccm的氮气,控制工作腔内压力为2
×
10
‑2mbar。将多弧离子镀电源接连alcrwsi靶,磁控溅射电源接连alcrsi靶;同时打开多弧离子镀电源和磁控溅射电源,并控制alcrwsi靶的电流为45a、alcrsi靶的电流为1a;另外,基材的偏压控制为
‑
60v。通过多弧离子镀和磁控溅射的共同作用,逐渐在cr中间过渡层上形成alcrsiwn功能层。alcrsiwn功能层的镀制时间控制在60min。
57.s6、镀制结束后,关闭多弧离子镀电源、磁控溅射电源等电源,停止通入气体;停止对工作腔的加热,待工作腔温度降至120℃后开启工作腔,取出基材,完成氮化物涂层在基
材上的制备。
58.通过电感耦合等离子光谱发生仪(icp)的检测,所得到的氮化物涂层中alcrsiwn功能层的硅含量为8at.%、钨含量为5at.%。
59.实施例4
‑
18如表1所示,实施例4
‑
18与实施例3基本相同,不同之处在于:在氮化物涂层制备方法的s5中,镀制alcrsiwn功能层的控制参数不同。
60.表1 实施例3
‑
18中镀制alcrsiwn功能层的控制参数
项目alcrwsi靶电流/aalcrsi靶电流/a基材偏压/v工作压力/mbar工作温度/℃镀制时间/min实施例3451
‑
602
×
10
‑240060实施例4551
‑
602
×
10
‑240060实施例5601
‑
602
×
10
‑240060实施例6651
‑
602
×
10
‑240060实施例7600.8
‑
602
×
10
‑240060实施例8600.9
‑
602
×
10
‑240060实施例9601.2
‑
602
×
10
‑240060实施例10601
‑
502
×
10
‑240060实施例11601
‑
1002
×
10
‑240060实施例12601
‑
601
×
10
‑240060实施例13601
‑
603
×
10
‑240060实施例14601
‑
602
×
10
‑230060实施例15601
‑
602
×
10
‑235060实施例16601
‑
602
×
10
‑245060实施例17601
‑
602
×
10
‑240040实施例18601
‑
602
×
10
‑240080
其中,实施例4
‑
9所得alcrsiwn功能层中硅和钨的原子含量经电感耦合等离子光谱发生仪检测,结果如表2。
61.表2 实施例3
‑
9所得alcrsiwn功能层中硅和钨的含量项目硅的含量/at.%钨的含量/at.%实施例38.05.0实施例49.54.3实施例510.04.0实施例610.83.6实施例712.03.0实施例811.03.5实施例98.74.7由成分结果可见,alcrwsi靶和alcrsi靶两者电流的大小,对所形成的alcrsiwn功能层中硅和钨的含量配比有明显的影响。当alcrwsi靶电流相对较大而alcrsi靶电流相对较小的时候,所形成的alcrsiwn功能层中硅和钨的含量比值相对较小;反之,则所形成的alcrsiwn功能层中硅的含量增大而钨的含量变小。
62.实施例19
‑
20实施例19
‑
20与实施例5基本相同,不同之处在于:在氮化物涂层制备方法的s2中,氩离子辉光清洁的控制参数不同。具体如表3。
63.表3 实施例5、19
‑
20中氩离子辉光清洁的控制参数项目工作压力/mbar氩气流速/sccm基材偏压/v清洁时间/min实施例54
×
10
‑2100
‑
5505实施例193
×
10
‑290
‑
5253实施例205
×
10
‑2120
‑
5758实施例21
‑
22实施例21
‑
22与实施例5基本相同,不同之处在于:在氮化物涂层制备方法的s3中,对刀具进行金属离子刻蚀的控制参数不同。具体如表4。
64.表4 实施例5、21
‑
22中对刀具离子刻蚀的控制参数
项目工作压力/mbar氩气流速/sccm靶材电流/a基材偏压/v刻蚀时间/min实施例54
×
10
‑210050
‑
55010实施例213
×
10
‑211045
‑
5255实施例225
×
10
‑212055
‑
57515
实施例23
‑
24实施例23
‑
24与实施例5基本相同,不同之处在于:在氮化物涂层制备方法的s4中,镀制cr中间过渡层的控制参数不同。具体如表5。
65.表5 实施例5、23
‑
24中镀制cr中间过渡层的控制参数
项目工作压力/mbar工作温度/℃靶材电流/a基材偏压/v镀制时间/min实施例54
×
10
‑240050
‑
605实施例233
×
10
‑235040
‑
504实施例245
×
10
‑250060
‑
808
对比例1本对比例与实施例3基本相同;不同之处在于,在氮化物涂层制备方法s5中,不采用alcrwsi靶;仅采用多弧离子镀电源接连alcrsi靶。
66.具体如下:s5、保持工作腔内温度为400℃;向工作腔内通入流速为70sccm的氮气,控制工作腔内压力为2
×
10
‑2mbar。将多弧离子镀电源接连alcrsi靶,打开多弧离子镀电源并控制alcrsi靶的电流为45a;另外,控制基材的偏压为
‑
60v。通过多弧离子镀,逐渐在基底材料的cr中间过渡层上形成alcrsin功能层。alcrsin功能层的镀制时间控制在60min。
67.对比例2本对比例与实施例3基本相同;不同之处在于,在氮化物涂层制备方法s5中,多弧离子镀和磁控溅射分开进行。
68.具体如下:s5、保持工作腔内温度为400℃;向工作腔内通入流速为70sccm的氮气,控制工作腔内压力为2
×
10
‑2mbar。先将磁控溅射电源接连alcrsi靶,打开磁控溅射电源并控制alcrsi靶的电流为1a;同时,控制基材的偏压为
‑
60v。通过磁控溅射在cr中间过渡层上形成alcrsin功能层,镀制时间控制在15min。之后将多弧离子镀电源接连alcrwsi靶,打开多弧离子镀电源并控制alcrwsi靶的电流为45a;同时,控制基材的偏压为
‑
60v。通过多弧离子镀在alcrsin功能层上形成alcrwsin功能层,镀制时间控制在45min。
69.对比例3本对比例与实施例3基本相同;不同之处在于,不含有s4,即不镀制cr中间过渡层。
70.性能检测取实施例1
‑
24以及对比例1
‑
3所得的刀具进行性能检测;检测结果列于表6。
71.1、切削测试:对刀具进行切削测试,并测其刀刃的磨损量。切削对象为:304不锈钢(硬度hrb80);切削条件为:转速(s)为8500、切削速度(v
c
)为160m/min、进给速度(f)为1600mm/min、每齿进给量(f
z
)为0.05mm/r、切深(a
p
)为5mm、切宽(a
e
)为0.15mm、切削方式为侧铣跟随周边、冷却方式为冷却液冷却;切削时间为90min。
72.2、刀具维氏硬度测试:参考标准:gb/t 7997
‑
2014;其中,测试条件:检测温度为25℃,试验力为294.2n,施加试验力时间为5s,试验力保持时间为10s。
73.表6 实施例1
‑
24及对比例1
‑
3所得刀具的性能检测项目磨损量/mmhv实施例10.0963432实施例20.0863471实施例30.0803500实施例40.0733461实施例50.0703430实施例60.0733375实施例70.0803300实施例80.0743359实施例50.0703430实施例90.0773475实施例100.0783382实施例110.0663441实施例120.0813378实施例130.0653442实施例140.0873350实施例150.0763399实施例160.0733410实施例170.0823371实施例180.0643448实施例190.0803379实施例200.0673438实施例210.0853361实施例220.0703429实施例230.0863356实施例240.0753403对比例10.1103780对比例20.1053180
对比例30.1153157参见表6,由实施例1
‑
24的检测结果可知,本技术实施例所制得的刀具的维氏硬度均在3300以上,显示出高硬度的特性;同时在经过90min的切削试验后,本技术实施例所制得的刀具的刀刃磨损量均在0.10mm以下,表明在高温下,刀具具有良好的耐磨性。故本技术实施例所得氮化物涂层具有较高的硬度、较佳的耐磨性以及较好的耐高温性,并将这些性能赋予了刀具,使刀具在加工过程中能保持良好的切削稳定性,同时还增加了刀具的使用寿命。
74.实施例1和2考察了在镀制cr中间过渡层之前对基材进行金属离子刻蚀对于所得刀具的影响。从试验结果可知:在镀制cr中间过渡层之前先对基材进行金属离子刻蚀由于可以使刀具的表面活化,从而有利于后续氮化物涂层更好的与刀具结合;因此,所得到的刀具的磨损量较小而硬度较高。
75.实施例2和3考察了在对基材进行金属离子刻蚀前先对其进行氩离子辉光清洁对于所得刀具的影响。由试验结果可以看出:对刀具表面进行氩离子辉光清洁,由于可以去除刀具表面的碳氢氧化合物,有利于提高氮化物涂层与刀具基材的结合性,因此能提高刀具的耐磨性和硬度。
76.相比于实施例3,对比例1所得到的功能层为alcrsin层。由试验结果可以发现:镀制了alcrsiwn功能层的刀具相比于镀制了alcrsin功能层的刀具具有更好的耐磨性;说明:相比于alcrsin功能层,由于w的适量引入,alcrsiwn功能层可以赋予刀具更好的耐磨性,对刀具可以起到更好的保护作用。
77.相比于实施例3,对比例2的多弧离子镀和磁控溅射操作分开进行。分析试验结果可以发现:对比例2所得刀具的硬度和耐磨性均低于实施例3。这是由于:采用多弧离子镀和磁控溅射分开进行的方式,仅能得到独立的alcrsin功能层和alcrwsin功能层,两者无法通过协同作用而赋予功能层更好的整体性能。
78.相比于实施例3,对比例3没有镀制cr中间过渡层。分析试验结果可以发现:对比例3所得刀具的耐磨性和硬度均相对较差。这是由于:没有了cr中间过渡层的存在,alcrsiwn功能层在刀具表面的附着性受到了影响,从而影响了刀具的性能。
79.实施例3
‑
9考察了alcrwsi靶电流和alcrsi靶电流对于所得刀具的影响。参看实施例3
‑
6的试验结果:当alcrsi靶电流一定的情况下,随着alcrwsi靶电流的提高,所得刀具的耐磨性先提高后降低,而硬度则呈下降趋势。这是由于:随着alcrwsi靶电流的提高,所得alcrsiwn功能层中钨元素的含量增加,可以使氮化物涂层具有更佳的韧性,使刀具在加工过程中可承受更多振动而不易崩损,有利于提高氮化物涂层及刀具的耐磨性和使用寿命。然而如果钨元素的含量过大,会使氮化物涂层的耐高温氧化能力下降;这是因为在加工过程中所产生的较高切削温度与冷却液所产生的化学反应,使氮化物涂层内的wn与空气中的氧反应形成不稳定的氧化物wo3;因此过高的钨元素含量会降低氮化物涂层的耐磨性、硬度和使用寿命。参看实施例5、7
‑
9的试验结果:随着alcrsi靶电流的提高,alcrsiwn功能层中硅元素的含量提高,所得刀具的耐磨性先提高后降低,而硬度则呈上升趋势。这是因为:硅会在氮化物涂层内形成一层非晶态的sin
x
,可以抑止晶粒成长使氮化物涂层结构致密,从而有利于氮化物涂层硬度的提高,同时也能够有效改善氮化物涂层的耐高温氧化能力,赋予氮化物涂层良好的耐高温性能。当然,当硅含量过大时,氮化物涂层的韧性受损明显,对
氮化物涂层的耐磨性会造成不利的影响。
80.实施例10
‑
11结合实施例5针对基材偏压进行了对比。由于氮化物涂层表面液滴的密度和直径会随着基材负压绝对值的增加而减少,故参看试验数据可以发现,随着基材偏压绝对值的上升,刀具的硬度呈上升的趋势,相应的刀具的耐磨性也得到了提高。当然,过高的基材偏压的施加,会使能源的损耗和成本上升;故综合而言,实施例5较优。
81.实施例12
‑
13结合实施例5针对工作压力进行了对比。通过试验数据可知:随着工作压力的升高,使所得刀具的硬度和耐磨性均有所提升。这是由于,氮气压力的增加能使氮化物涂层中的熔滴的密度和直径减少,从而提高了氮化物涂层的硬度,进而提升了刀具的性能。
82.实施例14
‑
16结合实施例5针对工作温度进行了对比。由试验结果可知:随着工作温度的升高,刀具的耐磨性和硬度先提高后下降。出现上述现象的原因在于:工作温度升高,能够获得较大的沉积速率,有利于氮化物涂层的生长,从而获得性能优良的氮化物涂层;并且较高的工作温度,也有利于涂层在基材上的附着。但是如果工作温度过高,会引起氮化物涂层内晶粒粗大,从而降低了涂层的硬度。
83.实施例17
‑
18结合实施例5针对镀制时间进行了对比。对比试验结果可以发现:延长镀制时间能够提高刀具的性能。这是由于:镀制时间的延长,有利于氮化物涂层的充分形成,从而能够获得性能更好的氮化物涂层。综合经济性和效率考虑,实施例5较优。
84.实施例5、19
‑
20考察了氩离子辉光清洁的不同控制参数对于氮化物涂层及所镀制的刀具的影响。试验结果表明:工作压力在3
×
10
‑2~5
×
10
‑2mbar,氩气流速在90~120sccm,基材偏压在
‑
575~
‑
525v,清洁时间在3~8min的范围内,均能有效清洁刀具表面,能够得到理想的氮化物涂层和刀具。
85.实施例5、21
‑
22考察了金属离子刻蚀的不同控制参数对于氮化物涂层及所镀制的刀具的影响。试验结果表明:工作压力在3
×
10
‑2~5
×
10
‑2mbar,氩气流速在100~120sccm,靶材电流在45
‑
55a,基材偏压在
‑
575~
‑
525v,清洁时间在5~15min的范围内,均能有效对刀具进行刻蚀,使刀具表面活化,从而获得理想的氮化物涂层和刀具。
86.实施例5、23
‑
24考察了镀制cr中间过渡层的不同控制参数对于氮化物涂层及所镀制的刀具的影响。试验结果表明:工作压力在3
×
10
‑2~5
×
10
‑2mbar,工作温度在350~500℃,靶材电流在40~60a,基材偏压在
‑
80~
‑
50v,镀制时间在4~8min的范围内,均能有效制得cr中间过渡层。
87.本具体实施例仅仅是对本技术的解释,其并不是对本技术的限制,本领域技术人员在阅读完本说明书后可以根据需要对本实施例做出没有创造性贡献的修改,但只要在本技术的权利要求范围内都受到专利法的保护。