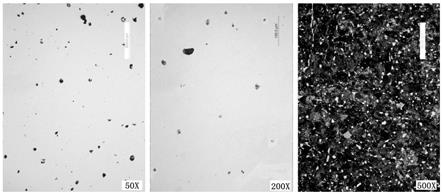
1.本发明属于钢铁冶金行业用轧辊制造领域,尤其涉及一种在钢液中采用原位再生方法制备含有氮化钛的半钢基钢坯连轧辊及其制备方法。
背景技术:2.现阶段两辊热轧钢基冶金轧辊包括开坯轧机用bd轧辊,钢坯连轧机用轧辊,板带粗轧机用轧辊,型钢粗、中、精轧用轧辊及辊环,其单件净重从3吨到49吨,铸件单重从5吨到近80吨,均属超大型铸件。
3.其中,钢坯连轧机,作为特种钢企业的一种特殊机型,介于开坯与型材轧制之间的中间加工工序,是将不便于采用大规模连铸生产的大断面合金钢坯料通过轧制成下道工序所需规格的坯料,与传统普碳低合金钢轧材相比其特点,被加工的钢种合金含量高、材料的变形抗力大、硬度高,对轧辊要求一方面要有较好的强度抵抗轧制冲击,同时要具有较高的耐磨性能。
4.另外,两辊板带可逆粗轧机,通常作为中宽带半连轧机的一种机型,主要用于板坯粗轧工序,将来料厚度较厚的板坯,通过可逆往复轧制,加工成后道精轧机组所需的坯料厚度,与型材轧机相比,其轧制坯料宽度较宽,轧辊承受的轧制负荷较大,除了要满足板材表面质量所需的耐磨性外,必须有较高的抗破断强度。
5.现用传统轧辊材质包括:传统合金钢、半钢、石墨钢。对于抗破断强度较高的合金钢,由于其耐磨性较差已被传统半钢、石墨钢所替代。
6.对于传统半钢与石墨钢目前主要使用的合金化元素为cr、ni、mo等。与合金钢相比,为了提高其耐磨性除了对应cr、ni、mo合金元素调整外,主要含碳量的得到大幅度提高,伴随含碳量的提高,半钢轧辊铸态组织中出现一次碳化物;石墨钢由于对si含量的调整,组织中除了形成一定数量一次碳化物外,同时还有一定数量的石墨析出;借助孕育+变质处理手段,改变组织中石墨以及一次碳化物形态及比例;再借助于热处理(扩散、淬火、回火)细化和调整基体组织、改善一次碳化物形态及比例,以实现所需的强度、硬度等使用性能。
7.随着含碳量的进一步提高一次碳化物、石墨百分比的增多,轧辊耐磨性提高的同时,轧辊强度显著下降,脆性增大,进而限制了含碳量的进一步提高,为了降低碳化物对材料脆性的影响,业内曾采用锻造半钢的制造工艺,使用性能虽得到一定程度提高,制造成本也大大增加。
8.同样,随着技术进步,在合金化、高合金化方面,用于棒线材轧机、四辊带钢轧机用轧辊的制备过程中,除了cr、ni、mo合金比例的大幅提高(以cr元素为例,从1.0%到2.0%、3.0%甚至到4.0%),同时添加一定数量的v、w、nb等合金,衍生出了高铬钢、高速钢、半高速钢轧辊,轧辊的耐磨性能得到了显著提高。
9.然而,对于两辊钢坯连轧机用辊及两辊板带粗轧可逆轧机用辊来说,随着合金含量的提高,在耐磨性提升的同时,对钢的淬透性、淬硬性,以及淬火脆性、开裂甚至断裂倾向显著增加,制造难度以及轧辊抗事故能力显著下降,制约了超大断面轧辊耐磨性的提升。因
此,限制了超大断面两辊轧机用轧辊cr、ni、mo合金含量进一步提高。
10.特别对于孔型较深、轧制力较大,对抗断裂性能要求较高的开坯及型钢粗轧机轧辊,为了解决孔型内耐磨性不足及孔型形状的保持能力差问题,有些钢厂不得已采用了在合金钢材质基础上,孔型内激光熔覆工艺,从而使生产运行费用增加,轧钢生产轧辊车修过程复杂化。
11.如何在现用钢基轧辊材质基础上(包括合金钢、半钢、石墨钢材质),在不破坏现用材料强韧性指标前提下,通过向轧辊中添加一种或几种微量元素(如钨、铌、钒、ti等)从而大大提升轧辊的耐磨性能,一直是行业技术人员研究的方向。
12.例如ti作为有益元素,已广泛用于航空航天、医疗、精密仪器、仪表、刀具等领域,在抗高温、耐磨、耐蚀、抗氧化等方面发挥了重要作用。然而,对于冶金轧辊领域该大型特别是超大型铸钢类(轧辊)产品上,由于溶入合金熔液中的单质ti,在凝固过程极容易在晶界析出,造成晶界偏析,恶化钢的材料性能,在高温热处理过程中出现晶界断裂至整个大型铸件报废。也有人曾采用向钢液中利用机械混合的方式如喷吹氮化钛(tin)粉状陶瓷颗粒的方式力求提高材料耐磨性。但由于tin粉末比重比钢液轻,喷吹的固态陶瓷颗粒容易漂浮在钢液表面(收得率很低);另外,由于tin陶瓷颗粒表面活性较低,且其与钢液之间的表面张力将导致陶瓷颗粒表面与钢基金属很难形成完全冶金结合,而以杂质形式存在于轧辊材料当中,使用时极易出现脱落。
13.如何利用ti合金在钢中的有利作用,消除和解决ti合金在超大铸钢件中的不利影响,在传统钢基轧辊材质基础上,用较低的成本,通过少量的合金化,在不恶化轧辊性能为条件下,提升传统轧辊的综合机械性能,提高轧辊寿命是本发明所要解决的技术问题。
技术实现要素:14.为解决上述技术问题,本发明提供一种原位再生氮化钛石墨半钢基钢坯连轧辊的制备方法,通过该制备方法制备而成的轧辊,在不破坏原钢基基体强度性能指标的前提下,具有提升耐磨性能的作用。
15.一种原位再生氮化钛石墨半钢基钢坯连轧辊的制备方法,是以钢基轧辊原料配比为c1.4
‑
1.8%、si0.6
‑
1.5%、mn0.5
‑
1.2%、cr0.8
‑
2.0%、ni0.5
‑
1.5%、mo0.2
‑
1.5%、v0.01
‑
0.2%、al0.02
‑
0.03%为基础,其余为fe的石墨半钢基合金材料,通过常规熔炼去除有害杂质至其含量为p≤0.03%、s≤0.025%、[o]≤0.0015%后,向合金熔液中添加含钛合金与含氮合金,使合金熔液中钛含量达ti0.02
‑
0.05%、氮含量达[n]≥0.020%~0.03%;在中频炉中于1500℃~1680℃下利用电磁感应自然搅拌≥40分钟,使高温熔融状态的合金熔液中的ti与n相互充分作用,在原位合金熔液中生成以悬浮状态的熔点为2950℃的纳米级(φ5
‑
20um)tin颗粒(即原位再生氮化钛颗粒);然后在lf精炼钢包(或精炼炉)中向所得合金悬液中吹入纯氮气,使合金悬液中总氮含量达[n]0.03
‑
0.04%,借助于高富氮气泡的作用与合金悬液中残留的ti,进一步生成高熔点纳米级原位再生tin微颗粒,得原位再生氮化钛钢基轧辊的合金悬液;再通过孕育、变质处理得合金混合悬液,浇注、热处理得原位再生氮化钛钢基轧辊。
[0016]
优选地,含钛合金选自氮化铬铁(如fencr
10
)。
[0017]
优选地,含氮合金选自钛铁(如feti
50
)。
[0018]
优选地,浇注是根据不同铸造工艺的需要,采用静态整体铸造、或静态冲洗复合铸造,将经原位再生氮化钛处理的合金混合悬液注入所需的轧辊铸型内。该铸型包括铸造下辊颈部位的底座箱、铸造辊身部位的冷型、铸造上辊颈部位的上箱、冒口箱以及浇道系统。其中:所述底座箱铸型是由金属型箱体内壁挂15
‑
25mm砂型+3
‑
5mm耐高温涂料;所述铸造辊身部位的冷型为静态铸造用冷型,采用金属型箱体内壁挂15
‑
20mm砂型+3
‑
5mm耐高温涂料;上箱部位采用金属外箱+150~200mm砂型+3
‑
5mm耐高温涂料;冒口箱部位采用金属外箱+200~300mm砂型+50~80mm绝热冒口套;浇道系统由金属外箱+30
‑
50mm砂型+10~15mm耐火砖管。
[0019]
其中,铸造凝固过程:当含有悬浮态原位再生tin颗粒的合金混合悬液浇入铸型后,受铸型的冷却作用,靠近金属附近的合金混合悬液随着温度降低,在后续凝固过程中,凝固前沿初始奥氏体晶粒优先在tin颗粒基础上形核与长大;对于含有一次碳化物的半钢或石墨钢材质,其一次碳化物优先在tin颗粒基础上形核与长大;对于含有石墨的石墨钢材质,共晶石墨也优先在tin颗粒基础上形核与长大;随着凝固的不断进行,结晶前沿由下往上,由外向里,由下辊颈经辊身、上辊颈到冒口推进,通过顺序凝固过程,最终完全凝固。
[0020]
由于原生tin颗粒的非均匀形核作用,起到了细化、均匀组织的效果,起到了细化铸件原始晶粒度的作用,为后续热处理、提高材料机械性能等创造了条件。
[0021]
其中,热处理过程:沿用传统半钢、石墨钢材质轧辊热处理工艺,对于轧辊规格较大的热轧板带粗半钢与石墨钢轧辊,采用毛坯热开箱直接进行扩散球化热处理,然后经粗开孔型加工后,进行淬火+回火热处理;对于规格偏小钢坯连轧机半钢与石墨钢轧辊,也可采用冷开箱,然后经粗开孔型加工后,进行扩散球化+淬火+回火热处理。
[0022]
对于铸件中含有纳米级原位再生tin颗粒的钢基轧辊,在后续热处理(扩散球化热处理、淬火+回火处理)过程当中,在经过再结晶温度(720℃)时,又起到了再结晶非均匀形核核心作用,同时在长时间高温扩散(≥1050℃)过程中,又起到了阻止晶粒过渡长大作用。
[0023]
其中:传统钢基轧辊材料可以根据生产的钢种是半钢、石墨钢轧辊材质。
[0024]
本发明利用了原位再生的原理,与传统(喷吹粉状氮化钛颗粒方法及单纯进行ti微合金化)方法比,主要通过向制备好的高温合金悬液中加入含ti合金与含n合金,在熔炼过程从高温合金悬液中直接生成极微小的纳米级tin颗粒,进一步向合金熔液中通过吹入纯氮气,在高富氮气泡作用下,使溶解在合金悬液中的单质ti和n元素进一步形成tin颗粒,从而使90%以上的ti单质形成2950℃的高熔点、高显微硬度1800~2100hv、颗粒当量直径在φ5~20um的极稳定的高耐磨相tin(氮化钛)颗粒。如此通过tin在冶炼过程从钢液中原位再生,消除了游离在合金悬液中的ti单质在凝固后期晶界偏析倾向的不利影响,与此同时,还具有细化、均匀组织、提高耐磨与强韧性指标作用。
[0025]
由于本发明是通过钢液中原位再生析出的tin颗粒,其本身又是作为后期形核的核心,包括初生奥氏体、石墨、碳化物组织相,以此为核心形核与长大。使其作为金属凝固过程不可分割的一个单元,彻底解决了外加固态粉状tin颗粒与钢液组织间的亲和问题,完全解决了ti在晶界偏析作为有害相的不利影响。
[0026]
tin本身作为高耐磨支点显微硬度较高1800
‑
2100hv,是普通碳化物(fe3c,900
‑
1000hv)的两倍以上,通过控制tin的足够数量,在不破坏原钢基基体强度性能指标的前提下,起到提升耐磨性能的作用。
[0027]
该轧辊广泛用于黑色冶金以及不锈钢热轧制领域,特别是两辊钢坯连轧机、两辊板带钢粗轧机用轧辊的制造领域;利用原位再生氮化钛钢基轧辊的制造原理,还可以制造适合于含碳量c0.55
‑
0.75%的合金钢钢基轧辊、含碳量c1.0
‑
2.5%的半钢及石墨钢钢基轧辊与辊环的制造领域。其适用于外圆直径在ф850~2500mm,辊身长度(或辊环轴向长度)l200~2500mm的大型铸造辊环、筒状铸件及整体或复合轧辊生产,具有优良的使用特性、经济实用性和推广价值。
附图说明
[0028]
图1为本发明提供的热处理状态的含原位再生tin的石墨钢辊工作层的金相组织示意图;
[0029]
图2为本发明提供的采用静态整体顶铸方法制造的,原位再生氮化钛钢基轧辊原料制备的石墨半钢钢坯连轧辊示意图;
[0030]
图3为本发明提供的采用静态冲洗复合底铸方法制造的,适用于两辊式热带粗轧机的、原位再生氮化钛钢基轧辊原料制备的石墨半钢轧辊示意图;
[0031]
图4为一种原位再生氮化钛石墨半钢热带粗底铸冲洗复合轧辊浇铸示意图。
具体实施方式
[0032]
下面结合附图和实施例对本发明做进一步具体的说明。
[0033]
本发明提供的原位再生氮化钛的石墨半钢轧辊材料的冶炼方法可以通过现有技术或其改进制备各种石墨半钢轧辊,如通过整体铸造方法生产静态整体原位再生氮化钛石墨半钢轧辊;通过冲洗复合铸造方法生产静态冲洗复合原位再生氮化钛石墨半钢轧辊;还可以通过离心复合铸造方法生产离心复合原位再生氮化钛石墨半钢复合轧辊;还可以通过离心复合铸造+轴环装配机械组合方法生产离心轴环装配的原位再生氮化钛石墨半钢组合轧辊。下面以实施例的形式作部分列举,实际上原位再生氮化钛的钢基轧辊原料可制备的钢基轧辊只需按照所设定的硬度要求进行合理化加工,并不局限于以下实施例。
[0034]
实施例1:
[0035]
如图2所示,是本发明提供的一种采用静态整体顶铸方法制造的,原位再生氮化钛钢基轧辊原料制备的石墨半钢钢坯连轧辊,其具体制备步骤为:
[0036]
(1)造型:根据生产的产品规格及工艺,分别对铸造下辊颈部位用底箱、辊身部位用冷型、上辊颈用上箱及冒口进行造型;烘烤干燥;并将底箱、冷型箱、上箱、冒口箱依次连接后组型(合箱);
[0037]
(2)冶炼:将各原料加入中频炉中熔炼,原始钢基合金熔液的化学成分按如下范围的中下限进行粗调整:c1.4
‑
1.8%、孕育前si0.4
‑
1.0%、mn0.5
‑
1.2%、cr0.8
‑
1.5%、ni0.5
‑
1.5%、mo0.2
‑
0.8%、v0.01
‑
0.2%、ti0.02
‑
0.05%、al0.02
‑
0.03%、[n]0.03
‑
0.04%,其余为fe的钢基合金材料,另外p、s作为有害元素通常p≤0.03、s≤0.025,经脱氧后[o]≤0.0015%(轧辊规格重量相对较小的轧辊,一般在中频炉中经粗调+微调,不使用精炼炉冶炼,但用精炼包吹氮。但如果一次生产支数比较多,也可以使用精炼炉冶炼,一包浇铸多支轧辊),扒渣,加入含钛与含氮合金至ti和[n]含量调整为ti0.02
‑
0.05%、[n]0.02
‑
0.03%,再在1580℃下利用中频炉自带的电磁搅拌保持40分钟以上,使单质ti与钢液中的
[n]相互充分反应进行初步化合形成当量为φ5
‑
20nm的tin颗粒;
[0038]
(3)精炼:将步骤(2)所得合金悬液出至带底吹氮气装置的lf精炼钢包中,由包底吹入工业氮气,使钢液中[n]≥0.03
‑
0.04%,并在1600℃下保持吹氮气20分钟以上,在高富氮气泡作用下,高富氮气泡在与合金悬液混合搅拌上升的过程中,完成合金悬液中的单质ti与n反应向tin充分转变(转化率90%以上);形成弥散在1500℃以上的高温合金悬液中的高熔点(2950℃)、高显微硬度(1800
‑
2100hv)、极稳定的、当量直径φ5
‑
20um的高耐磨相tin(氮化钛)悬浮颗粒(同时合金悬液中的单质ti达到痕迹量);对上述含有tin颗粒的合金悬液进行常规孕育和变质处理,得合金混合悬液,合金混合悬液成品中si含量达0.6
‑
1.5%;
[0039]
(4)浇注:将浇注温度控制为比传统过热度值低5℃左右,采用静态整体顶铸式铸造方法对步骤(3)所得合金混合悬液进行浇注,具体是:在步骤(3)所得合金混合悬液的温度为tl液相线温度+(35~40)℃时,将合金混合悬液由冒口箱上口沿中心轴线注入到合好的轧辊型腔(下辊颈箱体底箱+辊身箱体冷型箱+上辊颈箱体上箱+冒口箱)。浇速控制在下辊颈与辊身部位采用快速浇注,并在上辊颈与冒口采用慢速浇注提高补缩效果,同时冒口用发热剂和保温剂覆盖保温;
[0040]
轧辊凝固过程中,弥散悬浮在合金混合悬液中的原位再生tin微小颗粒,除作为初生奥氏体相的初始形核核心外,同时也是伪共晶碳化物相及石墨相的初始形核核心;
[0041]
(5)热处理(扩散退火与正火+回火):步骤(4)所得凝固后轧辊在铸型内缓慢冷却到室温,然后进行冷开箱,进行粗开孔型(单边+10~15mm)加工留热处理余量后,进行扩散(1050
‑
1100℃)+正火(950
‑
980℃)+回火(530
‑
560℃)热处理;分布在原始已凝固的铸件基体当中的微小弥散tin颗粒,在扩散及正火热处理过程当中,在经过再结晶温度时,作为非均匀形核核心在此基础上形核长大进一步细化晶粒,并在高温下阻止晶粒无限长大。
[0042]
(6)精加工各部位尺寸及公差达到客户图纸要求,包装防锈,发运。
[0043]
本实施例所得原位再生tin的石墨半钢钢坯连轧辊,其最终化学成分为:c1.6%、si1.35%、mn0.95%、p0.03%、s0.01%、cr0.95%、ni1.25%、mo0.5%、v0.015%、ti0.035%、[n]0.04%、al0.03%、[o]0.0015%,其余为fe。实物辊身工作层硬度达到53
‑
55hsd;材料抗拉强度达到785mpa。在同钢号、相同硬度级别情况下,较传统工艺抗拉强度、延伸率韧性等性能指标提升30%以上。
[0044]
实施例2:
[0045]
如图3所示,是本发明提供的一种采用静态冲洗复合底铸方法制造的,适用于两辊式热带粗轧机的、原位再生氮化钛钢基轧辊原料制备的石墨半钢轧辊,其具体制备步骤为:
[0046]
本实施例与实施例1的差别仅在于原料的各组分含量为:c1.5
‑
1.8%、孕育前si0.4
‑
0.6%、mn0.5
‑
1.2%、p≤0.03%、s≤0.025%、cr1.0
‑
2.0%、ni0.6
‑
1.5%、mo0.2
‑
0.8%、v0.01
‑
0.2%、ti0.02
‑
0.05%、[n]0.03
‑
0.04%、al0.02
‑
0.03%、[o]≤0.0015%;其余为fe。
[0047]
步骤(4)为静态冲洗复合铸造凝固过程:采用传统底铸方法浇注,浇注温度控制比传统过热度值低5℃左右,在下辊颈与辊身采用快速浇注,合金混合悬液进入上辊颈后减流至50%中速浇至有效辊颈上100
‑
200mm,停流、间断小流冲点,防止浇注系统凝固堵塞,待辊身工作层凝固厚度超过要求使用层+30~40mm,更换心部冲洗合金混合悬液(化学成分:c0.8
‑
1.2、si1.4
‑
1.6、mn0.5
‑
1.2、p≤0.03%、s≤0.025%、cr0.1
‑
0.2、ni0.2
‑
0.5、mo0.1
‑
0.2),用小流至30%浇速浇至距冒口上沿200
‑
300mm,改顶铸点冒口至有效高度,冒口用发热剂和保温剂覆盖保温。轧辊凝固过程中,弥散悬浮在合金悬液中的原位再生tin微小颗粒,作为初生奥氏体、一次碳化物以及共晶石墨等相的初始形核核心,进而起到了细化和均匀组织、细化铸件原始晶粒度的作用,为后续热处理、提高材料机械性能等创造了条件。
[0048]
步骤(5)热处理(热开箱扩散+球化退火+粗加工后,正火+回火):凝固后轧辊在铸型中缓慢冷却700
‑
800℃时,脱掉底箱、冷型、上箱及冒口进行热开箱后,热态进高温热处理炉进行整体1050
‑
1100℃扩散空冷后至再结晶转变点一下(550
‑
600℃)进炉,进行780
‑
830℃球化预备热处理,然后炉冷至室温,完成扩散+球化退火热处理后;进行粗加工(单边留15~20mm后续热处理脱碳、变形及热后粗加工所需的余量)后,进行950
‑
980℃正火+530~560℃回火热处理,炉冷至室温进入后续热后粗车、精车工序;
[0049]
在进行扩散热处理+正火热处理过程中,分布在原始已凝固的铸件基体当中的微小弥散tin颗粒,在经过再结晶温度时,作为非均匀形核核心在此基础上形核长大进一步细化晶粒,并在高温下阻止晶粒无限长大。
[0050]
如图3所示,是本实施例提供的原位再生tin的石墨半钢热带粗轧辊,其最终化学成分为:c1.55%、si0.85%、mn0.95%、p0.025%、s0.003%、cr1.5%、ni1.3%、mo0.4%、v0.01%、ti0.03%、[n]0.035%、al0.03%、[o]0.0015%;其余为fe。其实物辊身工作层硬度达到55
‑
58hsd;辊颈抗拉强度达到900mpa。在同钢号、相同硬度级别情况下,较传统工艺抗拉强度、延伸率韧性等性能指标提升30%以上。
[0051]
本发明适用于二辊单机架中宽带钢可逆轧机粗轧工作辊,目的在提高辊身硬度耐磨性基础上,提升辊颈强韧性,提高抗破断能力。
[0052]
原位再生tin的钢基轧辊金相组织与使用效果
[0053]
以原位再生tin的石墨半钢钢坯连轧辊为例,经对成品热处理状态的轧辊工作层进行金相组织检验验证,在未腐蚀的50倍显微镜下观察,在视场中,除含有一定数量的球状石墨分布外,还含有面积百分比在0.3
‑
0.8%的tin(氮化钛)颗粒均匀、弥散分布于金属基体之上,在100、200倍光学显微镜下呈金黄色(菱形、三角形、方形形貌),当量直径φ5
‑
20um,500倍光学显微镜下,可观察到其金黄色tin颗粒,与石墨、一次碳化物、以及基体共生,证实了凝固过程作为石墨、一次碳化物以及初生奥氏体晶粒核心的作用,从金相组织中,未发现晶界tin聚集(偏析)现象,如图1所示。
[0054]
采用原位再生tin的钢基,经上机试轧,除满足了正常工况轧使用环境(未出现因tin引发的断辊、剥落问题)外,其耐磨性能在传统材质基础上提升了30~50%,收到了较好的使用效果。