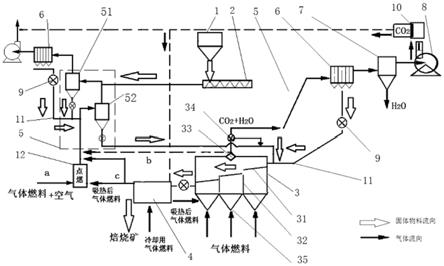
1.本发明属于冶金选矿技术领域,尤其涉及一种锰矿的还原焙烧及其co2减排方法及系统。
背景技术:2.电解金属锰是钢铁、铝合金、磁性材料和化工等工业不可缺少的原料之一。我国电解金属锰行业大都以菱锰矿(mnco3)为原料,采用“h2so4浸出
→
除杂
→
电解”工艺进行生产。由于我国高品位菱锰矿资源已消耗殆尽,菱锰矿原料锰品位已降低至10%~12%且仍难以为继,这导致生产过程酸耗高、渣量大、生产成本高,每吨电解金属锰产渣量高达7吨。随着我国环保政策的日趋完善,电解金属锰生产企业面临日益严重的环保压力。以高品位软锰矿(mno2)为原料,采用“还原焙烧
→
h2so4浸出
→
除杂
→
电解”工艺生产电解金属锰,可减少电解金属锰生产的固废量约70%,同时降低浸出过程酸耗、简化浸出液的除杂作业,是电解金属锰生产的必然趋势。
3.以软锰矿为原料生产电解金属锰的关键工序是将不溶于酸的高价mn还原转化为溶于酸的mn
2+
。软锰矿还原焙烧的方法有回转窑还原、竖炉还原和流态化还原等。近期,流态化还原焙烧方法得到较大发展,申请了大量专利,如:cn104878193a“一种低品位氧化锰矿流态化还原焙烧的系统及方法”、cn104911334a“一种高品位二氧化锰矿流态化还原的系统及方法”、cn111500854a“一种工业化处理铁锰矿石的悬浮焙烧系统及方法”、cn101591731a“一种含铁锰矿的悬浮焙烧综合利用系统及方法”等,这些专利公开了采用煤气或燃烧烟气为流化和还原介质、在流态化状态下对软锰矿还原焙烧的方法。
4.我们的研究发现,因空气中79%为惰性气体n2,因而,煤气和燃料燃烧产生的尾气中60%以上为惰性气体n2。惰性气体n2的大量存在造成很大的不良影响:(1)惰性气体n2在工艺过程中不参与反应,却需要历经“从室温加热至还原反应温度-由还原反应温度冷却至合理温度后排放”的无效加热过程,耗费大量的输送动力及燃料,导致焙烧能耗大幅增加,进而增加了工艺外排co2量;(2)还原焙烧系统尾气的co2浓度约20%、分离提纯难度大成本高,因而,co2不能利用,只能外排至大气中,不符合当前二氧化碳减排政策;(3)惰性气体n2在高温过程中与o2反应,生成少量no
x
,造成不良环境影响;(4)工艺过程处理的气体体积大,需要加大设备及管道尺寸,增加建设投资。
5.针对现阶段氧化锰矿还原焙烧过程中存在的实际问题,如何综合实现co2减排、节能降耗、降低投资及减少环境污染,对氧化锰矿的还原焙烧工艺及金属锰的后续生产利用具有重要意义。
技术实现要素:6.本发明所要解决的技术问题是,克服以上背景技术中提到的不足和缺陷,提供一种高效、经济、节能、环保、减排co2、焙烧质量还可得到保证的多级预热锰矿还原焙烧方法
及多级预热锰矿还原焙烧系统。
7.为解决上述技术问题,本发明提出的技术方案为一种可实现节能减排的多级预热锰矿还原焙烧方法,其特征在于,以低氮气含量的气体燃料为原料,利用该气体燃料与锰矿反应进行还原焙烧,该气体燃料与锰矿的反应可实现自热,且反应产物气相中几乎只含co2和/或h2o,所述锰矿为经过多级预热(至少两级)后的锰矿粉料。本发明的锰矿还原焙烧方法还与多级预热进行了结合,通过对锰矿进行多级预热处理,不仅能更好地节约能耗,提升锰矿进入反应器前的温度,还能更好地保证后续气体燃料与锰矿进行充分完全的反应实现自热,提高气体燃料的利用率。
8.进一步优选的,所述多级预热采用二级悬浮预热方式,且二级悬浮预热的高温气流来自所述气体燃料燃烧后、还原焙烧后或热交换后产生的高温排放气体。采用本发明的气体燃料燃烧后或还原焙烧后产生的气体,其优势较为明显,因为不会引入新的杂质以及氮气等无效气体,而且对后续的还原焙烧反应有促进作用。通过使矿粉与燃烧后或还原焙烧反应尾气进行接触式预热,不仅可降低反应尾气温度(尾气可以冷却至250℃以下),而且可实现余热利用,降低后期自热还原器中的热量消耗。另外也可以采用气体燃料先进行热交换吸热后再通入二级悬浮预热装置中。
9.上述的多级预热锰矿还原焙烧方法,优选的,所述气体燃料中至少含有ch4、co、h2中的一种或多种且几乎不含其他气体成分的气体燃料,更优选所述气体燃料为主要含ch4且几乎不含其他气体成分的气体燃料,例如天然气本身或者经裂解或提纯后的气体燃料;所述锰矿主要以mno2作为载氧体(尤其优选单一的软锰矿)。
10.当气体燃料和锰矿原料为前述优选物质时,则几乎主要发生以下化学反应:
11.ch4+4mno2=4mno+co2+2h2o-60.16kcal/mol
ꢀꢀꢀꢀꢀꢀꢀꢀꢀꢀꢀꢀ
(1)
12.co+mno2=mno+co
2-34.91kcal/mol
ꢀꢀꢀꢀꢀꢀꢀꢀꢀꢀꢀꢀꢀꢀꢀꢀꢀꢀꢀꢀꢀ
(2)
13.h2+mno2=mno+h2o-25.06kcal/mol
ꢀꢀꢀꢀꢀꢀꢀꢀꢀꢀꢀꢀꢀꢀꢀꢀꢀꢀꢀꢀꢀ
(3)
14.由上可见,反应(1)~(3)均是放热反应,利用这部分化学反应放热,软锰矿的还原焙烧可以实现自热,减少能源消耗;同时,上述反应的气体产物中几乎只含co2和h2o,将尾气冷却至100℃以下,冷凝除去水蒸汽后即可得到高浓度的co2气体,为co2的利用与减排创造良好条件。而且,由于没有惰性气体n2的参与,焙烧过程不仅不产生no
x
,还可大幅度减小工艺气量60%以上,从而降低气体输送动力,减小设备及输送管道体积,降低建设投资,进而实现既经济又环保的锰矿还原焙烧工艺。我们以ch4进行锰矿还原为例,计算可得每吨电解金属锰生产的co2排放量约为280kg/t,与以菱锰矿为原料的电解金属锰生产比较,co2排放量减少65%。
15.进一步优选的,所述原料与锰矿通过无焰燃烧方式进行还原焙烧,所述还原焙烧是在一自热还原器内进行(该自热还原器内优选设有火焰探测器)。无焰燃烧方式不仅能够大大减少能耗,减少气体燃料消耗,而且可以降低副反应发生,使自热反应能够顺利进行。所述还原焙烧产生的高温排放气体经二级悬浮预热、冷凝、净化后收集含高浓度二氧化碳的尾气。
16.进一步优选的,所述自热还原器为内腔设置有阶梯式布风板的流态化反应器,且相邻阶梯之间被隔板分隔成若干个反应区(优选2-5个),进入所述自热还原器的锰矿最先输送到最高阶梯布风板所在的第一反应区,然后依次下行经过各阶梯布风板所在的各个反
应区,最后从最低阶梯布风板所在的最后反应区流出自热还原器。通过设置阶梯布风板使自热还原焙烧分为多个反应区进行,这不仅可以保证矿料在自热还原器内一定的停留时间(优选的停留时间可控制在3min-50min),而且可以充分利用气体燃料以反应完全,防止反应尾气中夹杂气体燃料而影响其中二氧化碳含量的浓度,进而影响尾气的回收利用。自热还原器内流化区的温度优选控制在500℃~900℃。通过这样的优化配置,可使自热还原器内原料中的mn
4+
充分还原成mn
2+
,气体燃料几乎全部反应转化为co2和h2o;还原后的焙烧矿中mn
2+
/tmn>90%。
17.进一步优选的,所述自热还原器的底部设置有气体燃料进气口,顶部设置反应尾气的出气口,所述气体燃料依次经过各个反应区进行反应后生成的反应尾气从出气口排出;
18.出气口附近设置有用于检测气体燃气的传感器以及根据传感器检测数据进行控制的气体分流阀;当传感器采集的气体燃料浓度<5%时(一般为体积浓度),气体分流阀引导尾气送入一可对锰矿进行预热的二级悬浮预热装置中;否则,气体分流阀引导尾气循环至自热还原器的反应区内。
19.通过上述出气口增加设置传感器可以更好地保证反应尾气中可燃气体浓度低于规定的浓度,避免在非正常工况下气体燃料进入到反应尾气中,影响燃料的利用率和尾气co2的回收浓度,而且能够更好地保证各工况条件下的连续化生产。
20.上述的多级预热锰矿还原焙烧方法,优选的,所述气体燃料的进气流速以所述锰矿还原反应理论用量的0.8~1.2倍为控制标准;且气体燃料的进气流速可根据还原焙烧中装设的火焰探测器和/或传感器的采集数据进行调节;所述火焰探测器检测到有火焰或传感器检测到反应尾气气体燃料浓度较高时(例如大于5%时),调低所述气体燃料的进气流速。
21.通过上述气体燃料进气流速的控制,可以更好地实现自热反应完全,保证气体燃料的充分利用。
22.上述的多级预热锰矿还原焙烧方法,优选的,所述气体燃料热交换后产生的高温排放气体是指所述气体燃料经过吸收焙烧矿的余热后以点燃或不点燃方式产出的高温排放气体。若以点燃方式,则相当于气体燃料燃烧后或还原焙烧后实现向二级悬浮预热装置供热,若以不点燃方式送入二级悬浮预热,则相当于吸热后的气体燃料可在二级悬浮预热装置中就实现锰矿的预还原,此种情形下需要适当提高气体燃料的温度和锰矿进入悬浮预热装置后的温度。针对不同的悬浮预热供热方式,后续可以对悬浮预热产生的尾气进行不同的后续处理。我们优选还可以点燃或不点燃交替供应高温排放气体的方式,通过点燃后的高温排放气体先提升锰矿的预热温度,然后再间隔以吸热后不点燃方式直接供应气体燃料实现锰矿在悬浮预热装置中的预还原。
23.上述的多级预热锰矿还原焙烧方法,优选的,所述二级悬浮预热方式具体包括一级预热器和二级预热器,所述高温排放气体的气源(即高温排放气体发生装置)通过输送管道连通二级预热器的进气口,所述锰矿输送至连接二级预热器出气口与一级预热器进气口的管道内,锰矿悬浮在流出二级预热器的烟气中并随气体流动进入一级预热器,在一级预热器内完成气固分离和初步预热,流出一级预热器的锰矿粉料再次送入连接高温排放气体的气源与二级预热器进气口的管道内,并随高温排放气体再次流动进入二级预热器,在二
级预热器内完成气固分离和循环预热。通过这样的二级循环预热,不仅可以降低多级悬浮预热的投资成本,而且可以降低多级悬浮预热中气体动力及风阻消极影响,实现锰矿的快速预热处理。
24.上述的多级预热锰矿还原焙烧方法,优选的,所述锰矿在进行还原焙烧反应前,需要研磨至粒度1mm以下且水分含量控制在5%以下。通过控制还原焙烧反应前的原料粒度和水分含量,能够更好地让锰矿原料在自热还原器内反应完全,提高焙烧矿的品质。
25.上述的多级预热锰矿还原焙烧方法,优选的,所述锰矿在经过多级预热后的锰矿粉料温度控制达到200℃~800℃。
26.进一步优选的,所述还原焙烧后或多级预热处理后产生的含尘尾气经除尘器进行收尘处理,收尘处理得到的粉尘作为回收料与锰矿合并后回送进行所述还原焙烧;收尘处理得到的净化尾气进入一冷凝器进行非接触式冷却,使其温度降低至100℃以下,其中的水蒸汽冷凝为液态水并从气体中分离,剩余气体收集后用于制作高浓度的co2气体。由于整个锰矿还原焙烧过程没有惰性气体n2参与,产生的净化尾气中几乎仅含co2和水蒸气,将其冷却至100℃以下,水蒸汽即可冷凝为液态水从气体中分离,剩余气体为高浓度的co2气体,可作为化工原料销售、使用,从而减少锰矿还原焙烧的co2排放。
27.作为一个总的技术构思,本发明还提供一种可实现节能减排的多级预热锰矿还原焙烧系统,所述多级预热锰矿还原焙烧系统包括锰矿料仓、计量输送装置、自热还原器、焙烧矿冷却器、二级悬浮预热装置和高温排放气体发生装置;所述锰矿料仓的出料口与计量输送装置进料口相通;所述计量输送装置的出料口与二级悬浮预热装置的进料口相连通;所述二级悬浮预热装置的进气口、出料口分别与高温排放气体发生装置的出气口、自热还原器的进料口相连通;所述自热还原器的出料口连接所述焙烧矿冷却器;所述自热还原器的底部设有与气体燃料输送系统连通的进气口,所述气体燃料中至少含有ch4、co、h2中的一种或多种(气体燃料中不含惰性气体n2,既是还原介质,又是流化介质);所述自热还原器的出气口设有输送几乎只含co2和/或h2o的反应尾气的输送管道;所述高温排放气体发生装置为所述的自热还原器、焙烧矿冷却器或一气体燃料燃烧室中的至少一种。
28.上述的多级预热锰矿还原焙烧系统,优选的,所述自热还原器内可增设补热装置,若自热反应热量不足时可通过控制系统随时补充反应所需热量,以保证还原焙烧过程的稳定性、持续性和连续化进行。
29.上述的多级预热锰矿还原焙烧系统,优选的,所述多级预热锰矿还原焙烧系统还包括除尘器和冷凝器,所述冷凝器优选为间壁式冷却器,冷却介质可以为水或空气。所述二级悬浮预热装置和/或自热还原器的出气口与所述除尘器的进气口相连通,所述除尘器出气口与所述冷凝器的进气口相连,所述冷凝器的出气口通过引风机连接至制作高浓度co2气体的集气装置,进而完成反应尾气的除尘、脱水、输送和提纯。所述集气装置的co2气体的部分或气体燃料输送至所述焙烧矿冷却器中用于对还原焙烧的焙烧矿进行冷却并使焙烧矿维持在隔氧气氛下。
30.上述的多级预热锰矿还原焙烧系统,所述的焙烧矿冷却器可以为间壁式冷却器,焙烧矿与冷却介质进行非接触热交换,但优选的,所述集气装置的co2气体的部分或者气体燃料输送至所述焙烧矿冷却器中用于对还原焙烧的焙烧矿进行冷却(例如150℃以下)并使焙烧矿维持在隔氧气氛下,所述焙烧矿冷却器的出气口再连通至自热还原器、二级悬浮预
热装置、气体燃料燃烧室或其他原料输送管道。通过部分co2气体输送至所述焙烧矿冷却器中,不仅可以就地实现co2气体的循环利用,而且可以防止焙烧矿的再氧化,保证焙烧矿的焙烧质量,同时冷却后升温的co2气体的又可将余热补回至反应系统中,以维持反应系统中的低空气浓度,还可在最后进一步回收co2气体。通过气体燃料气体输送至所述焙烧矿冷却器中,不仅可以实现对焙烧矿余热的利用,还可以为悬浮预热供热并实现锰矿的预还原。
31.上述的多级预热锰矿还原焙烧系统,优选的,所述多级预热锰矿还原焙烧系统为接近密封环境的装置体系以确保空气向多级预热锰矿还原焙烧系统的漏入率<5%,所述多级预热锰矿还原焙烧系统中的固体物料输送管道上均设置锁风器,以防止气体窜动,确保气体按工艺要求的流向流动。另外,通过调节引风机转速,可进一步确保自热还原器出气口至引风机进风口的设备及管道内均为负压,防止气体和粉尘外泄,确保产生环境清洁,并为co2气体的输送提供动力。
32.上述的多级预热锰矿还原焙烧系统,优选的,所述二级悬浮预热装置具体包括一级预热器和二级预热器,所述高温排放气体装置通过输送管道连通二级预热器的进气口,所述锰矿输送至连接二级预热器出气口与一级预热器进气口的管道内,锰矿悬浮在流出二级预热器的烟气中并随气体流动进入一级预热器,在一级预热器内完成气固分离和初步预热,流出一级预热器的锰矿粉料再次送入连接所述高温排放气体发生装置与二级预热器进气口的管道内,并随高温排放气体再次流动进入二级预热器,在二级预热器内完成气固分离和循环预热。
33.与现有技术相比,本发明的有益效果为:
34.1)本发明利用mno2与ch4、co、h2反应自热的特点,开发了一种还原尾气没有n2、且只含co2和h2o的锰矿连续还原焙烧方式,由于本发明的还原焙烧方法及还原焙烧系统中没有惰性气体n2参与,系统内无效气体体积因而可减少60%以上,具有显著的优势:由于自热还原器尾气中只有co2、h2o及少量(或没有)气体燃料,反应尾气在冷凝脱水后可以得到纯度至少在80%以上(优选条件下可达90%以上)的co2气体,这为co2的减排及综合利用创造了良好条件,进而可以实现锰矿还原的co2大量减排。
35.2)由于本发明的还原焙烧方法及系统内无效气体体积的占比大幅度减少,这为自热反应创造了良好的反应条件,通过充分利用反应放热,可基本实现焙烧过程自热进行,大幅度降低工艺能耗。
36.3)由于本发明的还原焙烧方法及系统中无惰性气体n2,避免了现有其它还原焙烧方法中存在的n2历经“从室温加热至还原反应温度-由还原反应温度冷却至合理温度后排放”的无效过程,工艺更加节能降耗;同时,由于系统控制了n2的进入则没有生成no
x
的条件,几乎不会产生no
x
,工艺过程更加环保。
37.4)由于本发明的还原焙烧方法及系统中无惰性气体n2,这在等效作用的前提下,也大幅度减少了系统内气体输送动力,工艺过程动力消耗更小。
38.5)由于本发明的还原焙烧方法及系统中无惰性气体n2,相应大幅度减小了工艺设备及管道体积,减少工艺装备建设用地,进而降低了工艺系统的建设投资。
39.6)通过优化控制本发明还原焙烧工艺的参数条件及系统运作(例如原料控制、流量控制、反应条件控制等的综合实现)可以获得至少90%以上的锰矿还原率,技术指标更先进,焙烧矿的质量更容易得到保证。
40.总体而言,本发明的多级预热锰矿还原焙烧方法及系统具有高效、经济、节能、环保、减排co2等各方面优点,更符合当前的节能环保政策,对于我国氧化锰矿资源的绿色开发利用具有重要意义。
附图说明
41.为了更清楚地说明本发明实施例或现有技术中的技术方案,下面将对实施例或现有技术描述中所需要使用的附图作简单地介绍,显而易见地,下面描述中的附图是本发明的一些实施例,对于本领域普通技术人员来讲,在不付出创造性劳动的前提下,还可以根据这些附图获得其他的附图。
42.图1为本发明多级预热锰矿还原焙烧系统结构示意图及工艺原理图。
43.图2为本发明多级预热锰矿还原焙烧系统中自热还原器内部结构示意图。
44.图例说明:
45.1-锰矿料仓,2-计量输送装置,3-自热还原器,31-阶梯式布风板,32-隔板,33-传感器,34-气体分流阀,35-气体燃料进气口,36-火焰探测器,4-焙烧矿冷却器,5-二级悬浮预热装置,6-除尘器,7-冷凝器,8-引风机,9-锁风器,10-集气装置,11-固体物料输送管道,12-气体燃料燃烧室,51-一级预热器,52-二级预热器。
具体实施方式
46.为了便于理解本发明,下文将结合说明书附图和较佳的实施例对本发明做更全面、细致地描述,但本发明的保护范围并不限于以下具体实施例。
47.除非另有定义,下文中所使用的所有专业术语与本领域技术人员通常理解含义相同。本文中所使用的专业术语只是为了描述具体实施例的目的,并不是旨在限制本发明的保护范围。
48.除非另有特别说明,本发明中用到的各种原材料、试剂、仪器和设备等均可通过市场购买得到或者可通过现有方法制备得到。
49.具体实施方式:
50.一种如图1本发明的可实现节能减排的多级预热锰矿还原焙烧系统,该多级预热锰矿还原焙烧系统包括锰矿料仓1、计量输送装置2、自热还原器3、焙烧矿冷却器4和二级悬浮预热装置5;锰矿料仓1的出料口与计量输送装置2进料口相通;计量输送装置2的出料口与二级悬浮预热装置5的进料口相连通;二级悬浮预热装置5的进气口与高温排放气体发生装置的出气口相连通;二级悬浮预热装置5的出料口与自热还原器3的进料口相连通;自热还原器3的出料口连接焙烧矿冷却器4;自热还原器3的底部设有与气体燃料输送系统连通的进气口,气体燃料中至少含有ch4、co、h2中的一种或多种;自热还原器3的出气口设有输送几乎只含co2和/或h2o的反应尾气的输送管道。
51.高温排放气体发生装置可以为自热还原器3、焙烧矿冷却器4或一气体燃料燃烧室12中的至少一种。当选用气体燃料燃烧室12时,使气体燃料直接与空气混合后进入气体燃料燃烧室12中点燃,然后将高温排放气体送入二级悬浮预热装置5中(参见图1中的路径a);当选用自热还原器3时,可使自热还原器3的反应尾气直接通入二级悬浮预热装置5中(参见图1中的路径b),而反应尾气温度得以冷却至250℃以下;当选用焙烧矿冷却器4时,可先使
冷却用的气体燃料通过焙烧矿冷却器4进行热交换吸热,吸热后的气体燃料可以先进入气体燃料燃烧室12中点燃再送入二级悬浮预热装置5(即等同于路径a),也可以直接送入二级悬浮预热装置5中,具体根据二级悬浮预热装置5所需的热量情况(参见图1中的路径c)。本具体实施方式的高温排放气体发生装置可同时采用前述路径a+路径c的方式,而且可以通过控制阀实现路径a+路径c的间隔替换,以对矿料进行预热处理的同时,还可部分实现预还原操作,提高后期反应的效率。
52.如图2所示,本具体实施方式的自热还原器3为内腔设置有阶梯式布风板31的流态化反应器,且相邻阶梯之间被隔板32分隔成若干个反应区(本具体实施方式中呈现为3个)。通过设置阶梯式布风板31使自热还原焙烧分为多个反应区进行,通过延长矿料在自热还原器3内的输送路径,这不仅可以保证矿料在自热还原器3内一定的停留时间(停留时间可优选控制在3min-60min),而且可以充分利用气体燃料以实现反应完全,防止反应尾气中夹杂气体燃料而影响其中二氧化碳含量的浓度,进而影响尾气的回收利用。
53.如图2所示,本具体实施方式中的自热还原器3的底部设置有气体燃料进气口35,顶部设置反应尾气的出气口,气体燃料依次经过各个反应区进行反应后生成的反应尾气从出气口排出。出气口附近设置有用于检测气体燃气的传感器33以及根据传感器33检测数据进行控制的气体分流阀34;当传感器33采集的可燃气体浓度<5%时,气体分流阀34引导尾气送入二级悬浮预热装置5或直接送入除尘器6中(本实施方式是送入除尘器6);否则,气体分流阀34引导尾气循环至自热还原器3的第一反应区内。通过上述出气口增加设置传感器33可以更好地保证反应尾气中不夹杂气体燃料,避免在非正常工况下气体燃料进入到反应尾气中,影响燃料的利用率和尾气co2的回收浓度,而且能够更好地保证各工况条件下的连续化生产。
54.另外,如图2所示,本具体实施方式中设置三个反应区,相应可设置三个气体燃料进气口35,由于不同反应区面对的矿料反应状态可能不同,靠近进料口处未反应的矿料更多,参与反应更加充分,而靠近出料口处反应完全的矿料更多,对气体燃料的需求量相对较小,为了保证不同反应区通入的气体燃料反应更加完全,且提高反应效率,我们可以通过控制气体燃料进气口35处的进料阀及流量控制阀等,调节不同反应区中气体燃料的进气量和进气速率,使靠近进料口处的气体燃料进气量和进气速率适当增加,并通过挡板缩短其在自热还原器3内的流经路径,而靠近出料口处的气体燃料进气量和进气速率适当下降,并通过挡板延长其在自热还原器3内的流经路径,这可进一步提高气体燃料的反应效率和反应的充分性。
55.本具体实施方式中的二级悬浮预热装置5具体包括一级预热器51和二级预热器52,高温排放气体发生装置通过输送管道连通二级预热器52的进气口,锰矿输送至连接二级预热器52出气口与一级预热器51进气口的管道内,锰矿悬浮在流出二级预热器52的烟气中并随气体流动进入一级预热器51,在一级预热器51内完成气固分离和初步预热,流出一级预热器51的锰矿粉料再次送入连接高温排放气体发生装置与二级预热器52进气口的管道内,并随高温排放气体再次流动进入二级预热器52,在二级预热器52内完成气固分离和循环预热,最后送入自热还原器3内。
56.本具体实施方式的自热还原器3内还安装有火焰探测器36(可采用现有的红外探测、图像探测等探测设备),气体燃料的进气流速可根据火焰探测器36和/或传感器33的采
集数据进行调节;火焰探测器36检测到有火焰或传感器33检测到反应尾气可燃气体浓度较高(例如大于5%)时,则可调低气体燃料的进气流速。通过上述气体燃料进气流速的控制,可以更好地实现自热反应完全,保证气体燃料的充分利用。
57.本具体实施方式的多级预热锰矿还原焙烧系统还包括除尘器6和冷凝器7,二级悬浮预热装置5的出气口与除尘器6的进气口相连通,本具体实施方式中自热还原器3的出气口也可直接与除尘器6的进气口相连通,除尘器6出气口可与冷凝器7的进气口相连,冷凝器7出气口则通过引风机8连接至制作高浓度co2气体的集气装置10,如果除尘器6中的水蒸气含量少也可不经过冷凝直接进入集气装置10。
58.本具体实施方式中集气装置10的co2气体的部分或全部可通过输送管道输送至焙烧矿冷却器4中用于对还原焙烧的焙烧矿进行冷却并使焙烧矿维持在隔氧气氛下,焙烧矿冷却器4的出气口再连通至自热还原器3或二级悬浮预热装置5。
59.本具体实施方式的多级预热锰矿还原焙烧系统为接近密封环境的装置体系(即多级预热锰矿还原焙烧系统中的设备、管道及其连接均要求具有良好密封性能)以确保空气向多级预热锰矿还原焙烧系统的漏入率<5%。另外,通过调节引风机8转速,以控制自热还原器3出气口至引风机8进风口的设备及管道内均为负压;防止气体和粉尘外泄,确保产生环境清洁,并为co2气体的输送提供动力。
60.本具体实施方式的多级预热锰矿还原焙烧系统中的固体物料输送管道11上均设置锁风器9。
61.基于上述本具体实施方式的多级预热锰矿还原焙烧系统对锰矿进行还原焙烧的方法,具体包括以下步骤(从单批次矿料来看是按以下步骤顺序依次进行,但系统运行中各个步骤并未分先后顺序,可相互配合同时实施):
62.s1矿粉准备:
63.将软锰矿破碎、磨矿、干燥至0~1mm的粒度、且水含量小于5%,然后送入至锰矿料仓1内,矿粉从锰矿料仓1的底部出料口流出至计量输送装置2,计量输送装置2进行给矿量的精准计量和调节。
64.s2粉料预热:
65.经计量的锰矿粉料输送至二级悬浮预热装置5内,具体的,锰矿粉料输送至连接二级预热器52出气口与一级预热器51进气口的管道内,锰矿悬浮在流出二级预热器52的烟气中并随气体流动进入一级预热器51,在一级预热器51内完成气固分离和初步预热,流出一级预热器51的锰矿粉料再次送入连接高温排放气体发生装置与二级预热器52进气口的管道内,并随高温排放气体再次流动进入二级预热器52,在二级预热器52内完成气固分离和循环预热,最后送入自热还原器3内,锰矿粉料被预热至200℃~800℃;
66.本具体实施方式选用焙烧矿冷却器4作为高温排放气体发生装置,先使冷却用的气体燃料通过焙烧矿冷却器4进行热交换吸热,吸热后的气体燃料可以先进入气体燃料燃烧室12中点燃再送入二级悬浮预热装置5(即图1中的路径a),也可以直接送入二级悬浮预热装置5中,具体根据二级悬浮预热装置5所需的热量情况(参见图1中的路径c),还可同时采用前述路径a+路径c的方式,而且可以通过控制阀实现路径a+路径c的间隔替换,以对矿料进行预热处理的同时,还可部分实现预还原操作,提高后期反应的效率。
67.s3自热还原:
68.预热后的矿粉流出二级悬浮预热装置5,进入自热还原器3内,自热还原器3为内置阶梯式布风板31的流化床结构,进入自热还原器3的锰矿粉料先输送到最高阶梯布风板所在的第一反应区(a区),此时自热还原器3内不断有气体燃料从气体燃料进气口35进入(系统首次启动时可能需要补热装置预先补热),矿粉将悬浮在气体燃料中,矿粉中的二氧化锰为氧载体,与气体燃料发生无焰燃烧,mn
4+
还原转化为mn
2+
,气体燃料氧化生成co2和h2o;由于反应是放热反应,依靠反应释放热量即可维持自热还原器3内温度在500℃~900℃,反应过程实现了自热。
69.反应过程中,气体燃料的进气流速控制在锰矿还原反应理论用量的0.8~1.2倍(优选1.05倍以上);通过阶梯式布风板31逐级下移至各个反应区(例如本具体实施方式的b区和c区),而气体燃料在自热还原器3内隔板32及其他各种挡板的导向下同样曲折经过各个反应区,最终实现气体燃料与锰矿的充分和完全反应。
70.另外,为了应对非正常工况并确保反应的稳定和持续进行,自热还原器3内还配置有火焰探测器36和传感器33,火焰探测器36检测到有火焰或传感器33检测到反应尾气中气体燃料浓度较高时,则可调低气体燃料的进气流速以尽量实现无焰燃烧和反应完全。此外,气体分流阀34也可根据传感器33的采集数据引导反应尾气输出至二级悬浮预热装置5或循环至自热还原器3的第一反应区内。通过上述气体燃料进气流速的控制,可以更好地实现自热反应完全,保证气体燃料的充分利用。
71.本具体实施方式这样的优化配置,可使自热还原器3内原料中的mn
4+
充分还原成mn
2+
,气体燃料几乎全部反应转化为co2和h2o;还原后的焙烧矿中mn
2+
/tmn>90%。
72.s4尾气净化:
73.二级悬浮预热装置5流出的含尘尾气采用除尘器6进行收尘处理(可选用旋风除尘器和/或布袋除尘器),自热还原器3的反应尾气也采用除尘器6进行收尘处理;含尘尾气得到净化,回收料可与锰矿原料合并后回送进入自热还原器3内继续进行还原焙烧。
74.s5尾气脱水:
75.除去粉尘后的净化尾气可进入至冷凝器7进行非接触式冷却(主要针对自热还原器3的反应尾气),使其温度降低至100℃以下,水蒸汽冷凝为液态水并从气体中分离,剩余气体收集后可用于制作高浓度的co2气体,作为化工过程原料气使用,从而减少锰矿还原焙烧的co2排放。二级悬浮预热装置5流出的含尘尾气可不经过冷凝处理直接进入集气装置10。
76.s6气体输送:
77.冷凝器7的出气口连接引风机8,调节引风机8转速,可使系统内气体流向引风机8,确保自热还原器3出气口至引风机8进风口的设备及管道内均为负压,防止气体和粉尘外泄,确保产生环境安全与清洁,并为co2气体输送提供动力。引风机8可将co2气体导入集气装置10。
78.s7焙烧矿冷却:
79.自热还原器3流出的焙烧矿进入焙烧矿冷却器4内,本具体实施方式可选用间壁式冷却器与接触式冷却相结合的方式,间壁式冷却器中可与水、空气等冷却介质进行间接换热至焙烧矿温度小于100℃,还原焙烧产品得到冷却的同时回收了焙烧矿余热,加热气体燃料得到预热,降低系统能耗。另外,优选的,集气装置10的co2气体的部分可通过输送管道输
送至焙烧矿冷却器4中用于对还原焙烧的焙烧矿进行冷却并使焙烧矿维持在隔氧气氛下;焙烧矿冷却器4的出气口可以再连通至自热还原器3,以再次回收用于冷却的二氧化碳气体。我们还可以优选用本具体实施方式中的气体燃料作为冷却介质,使得冷却介质先进入焙烧矿冷却器4内回收焙烧矿余热,然后再可以直接与二级悬浮预热装置5的进气口相连用于预热和预还原处理,还可以与气体燃料燃烧室12相连,以进一步降低能耗,大大提高余热回收利用率(参见图1中c所示的气流箭头的流向)。
80.由上可见,本具体实施方式的可实现节能减排的多级预热锰矿还原焙烧方法及系统几乎可实现co2及其他污染物的大量减排,真正意义上实现节能降耗,降低污染,同时实现各类资源的综合利用,对循环经济的实现具有示范作用。
81.实施例1
82.本实施例所用软锰矿中tmn=42%、mn
2+
/tmn=1.62%,必须将高价锰(三价或四价锰)还原转化为mn
2+
,再采用硫酸浸出才能获得较理想的浸出效果。
83.使用上述具体实施方式的多级预热锰矿还原焙烧系统进行氧化锰矿还原焙烧,主要包括以下步骤(以下步骤仅列出本实施例中的主要参数,其余未具体描述的操作步骤及设备条件均同上述实施例):
84.s1矿粉准备:将软锰矿破碎、磨矿,制得-0.074mm80%粒度的矿粉,送入至锰矿料仓1内,矿粉从锰矿料仓1底部出料口流出至计量输送装置2。
85.s2矿粉预热:经计量的矿粉输送至二级悬浮预热装置5内,矿粉被预热至400℃。矿粉预热的热源来自气体燃料经焙烧矿冷却器4吸热后进入气体燃料燃烧室12点燃排放的高温气体,以及气体燃料经焙烧矿冷却器4吸热后直接送入的气体;两者可以同时或者交替通入;
86.s3自热还原:预热后的矿粉流出二级悬浮预热装置5,进入自热还原器3内,在悬浮状态下与含ch4、co、h2的气体燃料(气体燃料优选是天然气或裂解、提纯后得到的以甲烷为主的气体燃料)发生反应,反应停留时间20min,矿粉中mn
4+
转化为mn
2+
,气体燃料被充分消耗后生成co2和h2o;利用反应放出的热量,实现反应过程的自热,自热还原器3内温度维持在700℃;气体燃料通入量为锰矿还原反应理论用量的0.98倍。
87.s4尾气净化:自热还原器3排出的反应尾气以及二级悬浮预热装置5流出的含尘尾气采用旋风除尘器进行净化收尘,收集到的粉尘作为原料合并锰矿粉料后可再次循环进入自热还原器3内继续进行还原。
88.s5尾气脱水:除去粉尘的净化尾气中若水蒸气含量较大,可进入至冷凝器7进行非接触式冷却,使其温度降低至70℃,水蒸汽冷凝为液态水并从气体中分离,剩余气体经测定为浓度为94%的co2气体。
89.s6气体输送:冷凝器7出气口连接引风机8进气口,调节引风机8转速,使系统内气体流向引风机8,确保自热还原器3出气口至引风机8进风口的设备及管道内均为负压,防止气体和粉尘外泄,确保产生环境清洁,并将co2气体输送至临近的化工厂作为化工过程原料气使用,实现了锰矿还原焙烧的co2大量减排。
90.s7焙烧矿冷却:自热还原器3流出的焙烧矿进入间壁式冷却器内与水冷却介质及通入的冷却用气体燃料进行间接换热至焙烧矿温度小于80℃,得到还原焙烧产品,产品中mn
2+
/tmn=95.3%。
91.本实施例还原焙烧过程中矿粉悬浮预热和自热还原两个工序的天然气用量约为1∶2,与常规的锰矿还原过程比较,自热还原工序产生的co2作为化工过程原料气使用,再加上工艺过程的节能,本方法的锰矿还原过程可减排70%以上的co2。
92.本实施例试验表明,以天然气为还原剂和气体燃料进行氧化锰矿的还原焙烧,可以得到mn
2+
/tmn在95%左右的焙烧矿。以氧化锰矿为原料的制备硫酸锰的化学反应为:
[0093][0094]
mno+h2so4——
→
mnso4+h2o
[0095]
由上述化学反应式计算,以氧化锰矿为原料制备硫酸锰,吨硫酸锰的co2的理论产出为72.85kg,与以菱锰矿为原料生产的工艺比较,可以减少co2排放70%。实际上,虽然氧化锰矿天然气还原过程是放热反应,还原过程可以充分利用这一反应放热,如果反应放热不足,仅需适当补充热源即可,而作为还原剂的ch4(天然气)又可燃烧为还原过程提供热量。
[0096]
我们以锰含量40%%-45%的氧化锰矿进行还原焙烧的热平衡计算,还原过程中需要燃烧的天然气为25nm3/t(若进行充分的余热利用,还可进一步减少天然气消耗),产生的co2为49.11kg/t。再以该氧化锰矿进行硫酸锰生产,氧化锰矿需要量1.29t/t,折算至硫酸锰产品,燃烧产生的co2排放量为63.34kg/t。因此,以氧化锰矿为原料生产硫酸锰,单位硫酸锰产品的实际co2排放量为136.19kg/t(72.85+63.34);折算至电解金属锰,实际co2排放量为273.90kg/t。这与以菱锰矿为原料的生产工艺比较,可以减少co2排放53.26%。而且,氧化锰矿中mno2矿物含量达到71.18%,杂质矿物含量仅28.82%,以此为原料进行硫酸锰的生产,吨硫酸锰产品的废渣量为372kg,折算至电解金属锰,废渣量为1020kg/t,,与以锰品位12%的菱锰矿为原料生产电解金属锰比较,废渣量减排80%以上。
[0097]
以我国湿法工艺锰产品200万吨/年计,以高品位的氧化锰矿为原料进行锰产品的生产,可以减少固废和co2排放分别为1100万吨/年、105万吨/年,生态环境效益十分显著。
[0098]
实施例2:
[0099]
本实施例所用软锰矿中tmn=38%、mn
2+
/tmn=0.83%,必须将高价锰(三价或四价锰)还原转化为mn
2+
,再采用硫酸浸出才能获得较理想的浸出效果。
[0100]
控制还原焙烧条件与实施例1基本相同,但气体燃料通入量为还原反应理论用量的1.1倍,可获得mn
2+
/tmn为96.8%的还原焙烧产品,还原转化效果良好。
[0101]
另外,实施例1中由于综合运用了传感器33、气体分流阀34以及气体燃料流速的综合优化控制,使得最终收集的气体经测定可达到浓度为94%的co2气体,而本实施例中在不启用传感器33、气体分流阀34以及火焰探测器36的情况下,冷凝脱水后余气中co2气体浓度为90.87%、气体燃料浓度为7.39%,将余气采用碱性溶液吸收,除去co2气体,气体燃料可返回使用。
[0102]
通过该实施例2的对比可发现,启用传感器33、气体分流阀34以及火焰探测器36的情况下,可大大提高co2气体收集浓度和气体燃料的利用率。
[0103]
上述本实施例的多级预热还原焙烧系统亦具有显著优势:
[0104]
(1)焙烧能耗低:工艺充分利用了还原过程的反应放热,天然气流态化还原焙烧能耗仅为30kgce/t(原矿)。与电热回转窑还原工艺焙烧能耗约为300kw.h/t(折标煤36.87kgce/t)比较,天然气流态化还原焙烧工艺的焙烧能耗降低18.63%,从而可减少还原
过程的co2排放;与悬浮闪速还原焙烧能耗48.94kgce/t比较,天然气流态化还原焙烧工艺的焙烧能耗降低38.70%。
[0105]
(2)焙烧尾气可利用,尾气只需要进行简单的除尘、冷却脱水,就制得浓度90%以上的co2气体,可用作化工原料使用。
[0106]
(3)单元设备处理能力大。天然气流态化还原焙烧工艺的单元设备处理能力可在5万吨/年~100万吨/年根据需要确定。
[0107]
(4)加工成本低。采用天然气流态化还原焙烧工艺,氧化锰矿还原焙烧的加工成本约为250元/t(天然气价格3.5元/m3,不含原矿成本)。
[0108]
除非另有定义,本文中所使用的所有专业术语与本领域技术人员通常理解的含义相同。专业术语的使用只是为了方便描述具体实施过程,并不是旨在限制本发明的保护范围。凡属于本发明思路下的技术方案均属于本发明的保护范围,应当指出,对于本领域的技术人员来说,在不脱离本发明原理前提下的替换、改进、润饰及工艺参数的调整,这些替换、改进、润饰和调整也应视为本发明的保护范围。