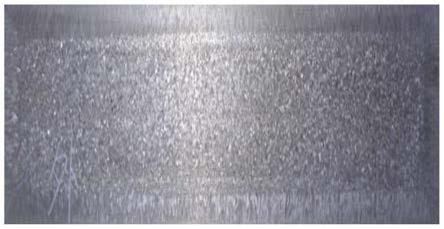
1.本技术属于钢铁冶金技术领域,更具体地说,是涉及一种取向硅钢铸坯的制备方法。
背景技术:2.取向硅钢是一种软磁材料,是变压器铁芯的重要材料之一。取向硅钢中的高斯织构是其出现优异磁性能的根本原因,并且铸坯组织对高斯织构的形成有重要影响。铸坯在凝固时一般形成柱状晶或者等轴晶,等轴晶对高斯织构的演变规律有重大的意义。可在现有的制备方式中,铸坯的等轴晶率的范围较小,不能满足研究及生产需求。
技术实现要素:3.本技术实施例的目的在于提供一种取向硅钢铸坯的制备方法及铸坯系统,以解决现有技术中的制备方法中的等轴晶率范围小的技术问题。
4.为实现上述目的,本技术采用的技术方案是:提供一种取向硅钢铸坯的制备方法,对精炼后的钢水进行连铸处理,所述连铸处理包括以下步骤:
5.进行凝固处理,以使所述精炼后的部分钢水凝固形成坯壳;
6.凝固处理时,进行电磁搅拌,以使所述精炼后的剩余钢水最终形成铸坯,
7.其中,所述电磁搅拌的位置和所述凝固过程中的结晶器出口的间距为0.3~1.5m,所述电磁搅拌的电流范围为0a~900a。
8.根据本技术的一个实施例,所述精炼后的钢水的过热度为3~45℃。
9.根据本技术的一个实施例,在所述凝固处理后,对所述坯壳进行拉坯,所述拉坯的速度为0.7
‑
1.1m/min。
10.根据本技术的一个实施例,所述电磁搅拌的电流范围为300a~900a,所述电磁搅拌的位置和所述结晶器出口的间距为0.4m。
11.根据本技术的一个实施例,所述铸坯断面的宽度为1050
‑
1340mm。
12.根据本技术的一个实施例,所述铸坯的等轴晶率的范围为0~77%,而且满足:
13.等轴晶比例=
‑
8.9+2.02v+0.07473i
‑
0.097t+0.0205l;
14.其中,v代表拉坯速度,i代表电磁搅拌的电流,t代表过热度,l代表铸坯断面的宽度。
15.根据本技术的一个实施例,所述铸坯的成分包括:c:0.03~0.08%,si:2.9~3.5%,mn:0.06~0.3%,p:0.004~0.035%,s:0.003~0.015%,als:0.0120~0.04%,n:0.005~0.01%,cu:0.01%~0.55%,余量包括fe。
16.此外,本技术还提供了一种铸坯系统,包括依次连接的脱硫设备、转炉冶炼设备、rh真空处理设备和连铸机,所述连铸机包括中间包、结晶器和电磁搅拌器,所述中间包的出水口位于所述结晶器的入水口的上方,所述电磁搅拌器位于所述结晶器的下方,所述电磁搅拌器和所述结晶器的出口之间的间距为0.3~1.5m,所述电磁搅拌器的电流范围为0a~
900a。
17.根据本技术的一个实施例,所述电磁搅拌器的电流范围为300a~900a,所述电磁搅拌器的位置和所述结晶器出口之间的间距为0.4m。
18.本技术提供的取向硅钢铸坯的制备方法至少具有如下的有益效果:先对精炼后的部分钢水进行凝固处理,以使精炼后的部分钢水形成坯壳。接着对坯壳进行电磁搅拌,以使坯壳形成铸坯。上述制备方法通过调节电磁搅拌的位置和电流大小来调节电磁搅拌的强度,进而通过电磁搅拌的强度来调节等轴晶的生成量,扩大等轴晶率的范围。
附图说明
19.为了更清楚地说明本技术实施例中的技术方案,下面将对实施例或现有技术描述中所需要使用的附图作简单地介绍,显而易见地,下面描述中的附图仅仅是本技术的一些实施例,对于本领域普通技术人员来讲,在不付出创造性劳动性的前提下,还可以根据这些附图获得其他的附图。
20.图1为本技术的第一实施例提供的等轴晶率为0%的铸坯低倍组织图;
21.图2为本技术的第二实施例提供的等轴晶率为10%的铸坯低倍组织图;
22.图3为本技术的第三实施例提供的等轴晶率为32%的铸坯低倍组织图;
23.图4为本技术的第四实施例提供的等轴晶率为38%的铸坯低倍组织图;
24.图5为本技术的第五实施例提供的等轴晶率为52%的铸坯低倍组织图;
25.图6为本技术的第六实施例提供的等轴晶率为65%的铸坯低倍组织图;
26.图7为本技术的第七实施例提供的等轴晶率为73%的铸坯低倍组织图;
27.图8为本技术的第八实施例提供的等轴晶率为77%的铸坯低倍组织图。
具体实施方式
28.为了使本技术所要解决的技术问题、技术方案及有益效果更加清楚明白,以下结合附图及实施例,对本技术进行进一步详细说明。应当理解,此处所描述的具体实施例仅仅用以解释本技术,并不用于限定本技术。
29.本技术提供了一种取向硅钢铸坯的制备方法,对精炼后的钢水进行连铸处理,连铸处理包括以下步骤:
30.s01、进行凝固处理,以使精炼后的部分钢水凝固形成坯壳;
31.s02、凝固处理时,进行电磁搅拌,以使精炼后的剩余钢水最终形成铸坯,
32.其中,电磁搅拌的位置和凝固过程的结晶器出口的间距为0.3~1.5m,电磁搅拌的电流范围为0a~900a。
33.对精炼后的钢水进行连铸处理时,可以先进行凝固处理,如将精炼后的钢水放入结晶器中,使得精炼后的部分钢水在结晶器中凝固形成坯壳。随后对坯壳进行拉坯、冷却和电磁搅拌以使精炼后的剩余钢水形成铸坯。其中,电磁搅拌可以指利用电磁搅拌辊或者电磁搅拌箱进行电磁搅拌处理。在电磁搅拌处理后,可以利用切割机对铸坯进行切割以便获得符合要求尺寸的铸坯。
34.其中,在电磁搅拌的作用下,能够引起熔体强烈流动,从而打断及熔蚀枝晶臂。并使得一部分枝晶碎片作为金属液凝固时的额外晶核,另一部分富溶质枝晶碎片被钢液流带
到远离枝晶的液穴中重熔。因此,更多形核基底的出现和枝晶碎片重熔带来的温度均匀化将促进更多等轴晶的形成。
35.由于电磁搅拌可以通过流动金属液对树枝晶前段的动力折断及熔蚀作用造成大量枝晶碎片作为等轴晶晶核。因此,可以通过调节电磁搅拌的位置和电流大小来调节电磁搅拌的强度。
36.例如,在一实施例中,电磁搅拌的位置和结晶器出口之间的间距在0.3~1.5m之间,并使得电磁搅拌的电流范围在0a~900a之间。如此,钢水在电磁搅拌的带动下发生流动,在强力流动下可以大大加速液心的传热而使过热度迅速消失、两相区迅速扩大。除此之外,强力流动还可以加速物质,使凝固前沿扩散边界层减薄而浓度梯度增大,两相区成分过冷增加,从而帮助等轴晶发展。如此,增加了等轴晶的生成量,扩大等轴晶率的范围,便于对不同比例等轴晶的演变规律进行相关研究。
37.在其中一个实施例中,电磁搅拌的电流范围为300a~900a,电磁搅拌的位置和结晶器出口的间距为0.4m。如此,可以通过提高电磁搅拌的强度,来提高等轴晶的比例。
38.在其中一个实施例中,可以使得精炼后的钢水的过热度为3~45℃。也就是说,将精炼后的钢水放入中间包后,并使得中间包中的钢水的过热度为3~45℃。如果过热度较高,钢水在温度梯度方向上以树枝状凝固,形成柱状晶。而当过热度耗散,钢水温度在液相线和固相线之间时,会出现微小的等轴晶晶核,随着进一步冷却生长,形成等轴晶。
39.由于过热度越低越有利于等轴晶的生产,因此,通常为了提高等轴晶比例的铸坯采用过热度相对较低的钢水,如,将过热度设置为3~10℃。因为过热度的调节范围较窄,而浇铸过程存在自然温降,所以对钢水的过热度存在较大的限制。而且钢水的过热度较低时,由于过热度较低,而且过热度的可调节范围较窄的原因,很容易出现“死流”的现象。将高过热度下铸坯结晶规律进行研究使得精炼后的钢水的过热度为3~45℃,在不影响等轴晶率的生产量的基础上,扩大了精炼后的钢水的过热度范围。
40.在其中一个实施例中,在凝固过程,对坯壳进行拉坯,拉坯的速度为0.7
‑
1.1m/min。
41.随着拉速提高,凝固坯壳变薄,固液两相区温度梯度降低,柱状晶生长缓慢。况且在电磁搅拌的破碎及熔蚀下,不利于柱状晶向铸坯中心方向生长,因而,可以通过提高拉坯的速度,来抑制柱状晶的生长速度,以便提高等轴晶的生长速度,进而提高了等轴晶的比例。
42.在其中一个实施例中,铸坯断面的宽度为1050
‑
1340mm。在坯壳厚度相同的情况下,随着铸坯断面增大,铸坯的液相区面积也不断增大,导致散热变慢。再在电磁搅拌作用下,温度梯度降低,有利于等轴晶的产生。
43.在其中一个实施例中,铸坯的等轴晶率的范围为0~77%,而且满足:
44.等轴晶比例=
‑
8.9+2.02v+0.07473i
‑
0.097t+0.0205l;
45.其中,v代表拉坯速度,i代表电磁搅拌的电流,t代表过热度,l代表铸坯断面的宽度。
46.如此,可以通过控制拉坯速度、电磁搅拌的电流、过热度和铸坯断面的宽度来调节等轴晶率的范围。还可以对等轴晶率的定量控制对不同比例等轴晶演变规律进行相关研究。
47.在其中一个实施例中,铸坯的成分包括:c:0.03~0.08%,si:2.9~3.5%,mn:0.06~0.3%,p:0.004~0.035%,s:0.003~0.015%,als:0.0120~0.04%,n:0.005~0.01%,cu:0.01%~0.55%,余量包括fe。当铸坯的成分包括上述元素时,所得到的铸坯的等轴晶率在0~77%。当然,关于铸坯的成分不限于上述元素。
48.此外,本技术还提供了一种铸坯系统,包括依次连接的脱硫设备、转炉冶炼设备、rh真空处理设备和连铸机,连铸机包括中间包、结晶器和电磁搅拌器,中间包的出水口位于结晶器的入水口的上方,电磁搅拌器位于结晶器的下方,电磁搅拌器和结晶器的出口之间的间距为0.3~1.5m,电磁搅拌器的电流范围为0a~900a。
49.其中,中间包可以用来盛放精炼后的钢水,还能够起减压、稳流、去渣、储钢、分流等作用。经过处理的钢水经中间包流动结晶器,从而在结晶器内形成坯壳,而坯壳从结晶器内的出来后,接着进行拉坯、电磁搅拌等等。
50.由于该连铸机采用了上述所有实施例的全部技术方案,因此至少具有上述实施例的技术方案所带来的所有有益效果,此处不再赘述。
51.在其中一个实施例中,电磁搅拌器的电流范围为300a~900a,电磁搅拌器的位置和结晶器出口的间距为0.4m。这样,可以通过提高电磁搅拌的强度,来提高等轴晶的比例。
52.第一实施例
53.对精炼后的钢水首先放入中间包中,使得钢水在中间包中的过热度为32℃。紧接着将其放入结晶器中凝固形成坯壳。随后对剩余的精炼后的钢水进行电磁搅拌,以使剩余的钢水凝固,随后再进行拉坯等处理。其中,拉坯的速度为1.0m/min,电磁搅拌器的电流为0a。经过上述一系列处理后,以使钢水最终形成铸坯。最后对铸坯进行切割处理,使得最终获得的铸坯的断面为1060mm。对铸坯进行低倍组织分析,结果如图1所示,可见,铸坯的等轴晶比例为0%。
54.第二实施例
55.对精炼后的钢水首先放入中间包中,使得钢水在中间包中的过热度为18℃。紧接着将其放入结晶器中凝固形成坯壳。随后对剩余的精炼后的钢水进行电磁搅拌,以使剩余的钢水凝固,随后再进行拉坯等处理。其中,拉坯的速度为0.8m/min,电磁搅拌器的电流为0a。经过上述一系列处理后,以使钢水最终形成铸坯。最后对铸坯进行切割处理,使得最终获得的铸坯的断面为1070mm。对铸坯进行低倍组织分析,结果如图2所示,可见,铸坯的等轴晶比例为10%。
56.第三实施例
57.对精炼后的钢水首先放入中间包中,使得钢水在中间包中的过热度为25℃。紧接着将其放入结晶器中凝固形成坯壳。随后对剩余的精炼后的钢水进行电磁搅拌,以使剩余的钢水凝固,随后再进行拉坯等处理。其中,拉坯的速度为1.0m/min,电磁搅拌器的电流为300a。经过上述一系列处理后,以使钢水最终形成铸坯。最后对铸坯进行切割处理,使得最终获得的铸坯的断面为1070mm。对铸坯进行低倍组织分析,结果如图3所示,可见,铸坯的等轴晶比例为32%。
58.第四实施例
59.对精炼后的钢水首先放入中间包中,使得钢水在中间包中的过热度为22℃。紧接着将其放入结晶器中凝固形成坯壳。随后对剩余的精炼后的钢水进行电磁搅拌,以使剩余
的钢水凝固,随后再进行拉坯等处理。其中,拉坯的速度为1.1m/min,电磁搅拌器的电流为400a。经过上述一系列处理后,以使钢水最终形成铸坯。最后对铸坯进行切割处理,使得最终获得的铸坯的断面为1060mm。对铸坯进行低倍组织分析,结果如图4所示,可见,铸坯的等轴晶比例为38%。
60.第五实施例
61.对精炼后的钢水首先放入中间包中,使得钢水在中间包中的过热度为43℃。紧接着将其放入结晶器中凝固形成坯壳。随后对剩余的精炼后的钢水进行电磁搅拌,以使剩余的钢水凝固,随后再进行拉坯等处理。其中,拉坯的速度为0.9m/min,电磁搅拌器的电流为500a。经过上述一系列处理后,以使钢水最终形成铸坯。最后对铸坯进行切割处理,使得最终获得的铸坯的断面为1320mm。对铸坯进行低倍组织分析,结果如图5所示,可见,铸坯的等轴晶比例为52%。
62.第六实施例
63.对精炼后的钢水首先放入中间包中,使得钢水在中间包中的过热度为36℃。紧接着将其放入结晶器中凝固形成坯壳。随后对剩余的精炼后的钢水进行电磁搅拌,以使剩余的钢水凝固,随后再进行拉坯等处理。其中,拉坯的速度为1.0m/min,电磁搅拌器的电流为900a。经过上述一系列处理后,以使钢水最终形成铸坯。最后对铸坯进行切割处理,使得最终获得的铸坯的断面为1070mm。对铸坯进行低倍组织分析,结果如图6所示,可见,铸坯的等轴晶比例为65%。
64.第七实施例
65.对精炼后的钢水首先放入中间包中,使得钢水在中间包中的过热度为24℃。紧接着将其放入结晶器中凝固形成坯壳。随后对剩余的精炼后的钢水进行电磁搅拌,以使剩余的钢水凝固,随后再进行拉坯等处理。其中,拉坯的速度为0.9m/min,电磁搅拌器的电流为900a。经过上述一系列处理后,,以使钢水最终形成铸坯。最后对铸坯进行切割处理,使得最终获得的铸坯的断面为1320mm。对铸坯进行低倍组织分析,结果如图7所示,可见,铸坯的等轴晶比例为73%。
66.第八实施例
67.对精炼后的钢水首先放入中间包中,使得钢水在中间包中的过热度为7℃。紧接着将其放入结晶器中凝固形成坯壳。随后对剩余的精炼后的钢水进行电磁搅拌,以使剩余的钢水凝固,随后再进行拉坯等处理。其中,拉坯的速度为1.1m/min,电磁搅拌器的电流为900a。经过上述一系列处理后,以使钢水最终形成铸坯。最后对铸坯进行切割处理,使得最终获得的铸坯的断面为1060mm。对铸坯进行低倍组织分析,结果如图8所示,可见,铸坯的等轴晶比例为77%。
68.由此可见,本技术的取向硅钢铸坯的制备方法可以通过控制拉坯速度、电磁搅拌的电流、过热度和铸坯断面的宽度来调节等轴晶率的范围,使其达到0~77%。
69.以上所述仅为本技术的较佳实施例而已,并不用以限制本技术,凡在本技术的精神和原则之内所作的任何修改、等同替换和改进等,均应包含在本技术的保护范围之内。