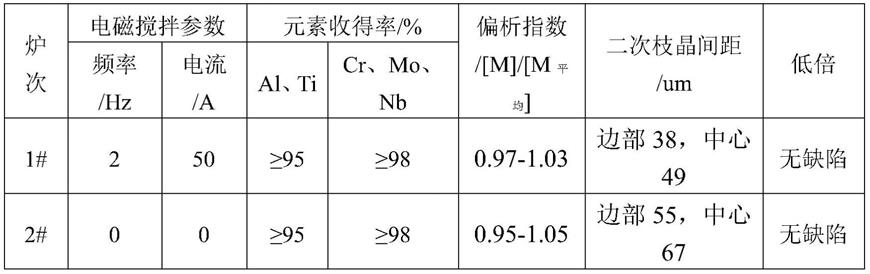
1.本发明属于冶金技术领域,涉及一种电渣重熔方法,尤其是一种镍基高温合金的电渣重熔方法。
背景技术:2.镍基高温合金具有卓越的使用性能,广泛用于航空航天、电力、造船、石油化工等领域。该合金在工作温度600~1000℃下,具有一定的持久强度、蠕变强度、热疲劳强度和韧性,还具有很强的抗氧化性能和耐蚀性能,合金具有单一稳定的γ固溶体组织,在大幅度的温度变化下组织基本不发生变化,为合金部件的安全使用提供了保障。
3.高温合金的生产一般有真空感应熔炼+电渣重熔、真空感应熔炼+真空自耗两种工艺流程,其中以真空感应熔炼+电渣重熔工艺生产的高温合金产量约占总高温合金产量的80%以上,所以作为终端工序电渣重熔,其冶金质量的好坏直接影响后续的热冷加工、热处理及焊接等工艺性能。目前,国内的航空发电机导向叶片、涡轮叶片、涡轮盘、燃烧室、火箭发动机涡轮盘、轴类部件、进气导管、喷嘴、600mpa及以上的燃气轮机的涡轮叶片、导向叶片用高温合金基本完全依赖进口,国产高温合金仅用于部分民用领域,如柴油机、汽油机的废气增压涡轮、石油催化裂化装置用烟气涡轮等,究其原因,主要是国产高温合金的高温强度和组织稳定性较差,这都归因于电渣冶金质量特别是组织成分的不均和不稳定性。
4.电渣重熔工艺中有许多关键参数影响高温合金铸锭的质量,化学元素的收得率影响成分的精确控制,局部凝固时间则影响电渣凝固组织的均匀性,所以,如何稳定电渣过程中元素收得率和局部凝固时间是电渣冶金的关键。
技术实现要素:5.为解决上述技术问题,本发明提供一种镍基高温合金的电渣重熔方法,其包括以下步骤:
6.(1)将配比好的caf
2-cao-al2o
3-tio2渣系通电熔化,注入结晶器中,启动电渣重熔电源,将渣温升至1600~1700℃;所述渣系中al2o3、tio2的重量含量与镍基高温合金中的al和ti的重量含量之比η相关,具体关系式为:
[0007][0008]
其中,al/ti=η;
[0009]
(2)进入重熔期,控制熔速v=(0.8~1.5)*10-2
d,待金属熔池末端50~100mm范围全部位于电磁搅拌线圈区域时开启电磁搅拌电源,所述v为熔速,单位:kg/min,d为结晶器内直径,单位:mm;
[0010]
(3)开启抽锭系统至重熔期结束,抽锭速度(3)开启抽锭系统至重熔期结束,抽锭速度
[0011]
其中:γ-抽锭速度,单位:mm/min;
两相区-固相-渣皮热传导则比较慢,特别是镍基材料,所以,如何提高热量在金属熔池-渣皮的传导速率是减少局部凝固时间的关键。
[0031]
本发明在凝固前沿中施加电磁搅拌,均匀成分减轻偏析,搅动钢液使原有的传热方式由传导传热转变为对流传热,提高传热效率,减少局部凝固时间。本发明在结晶器内部距结晶器上沿200~400mm处设置co60液位检测装置和电磁搅拌线圈,用于检测液位和提供频率2~8hz、电流50~400a旋转磁场,在熔炼过程中仅对固液两相区和其上部液相区50~100mm范围内区域进行搅拌,打破凝固前沿的成分过冷,使溶质富集程度减轻,从而减轻凝固偏析;另一方面,通过搅动液相旋转使原有的液固相传导传热转变为液固相对流传热,使凝固前沿的温度梯度陡然加大,极大地提高传热速率,有效降低局部凝固时间,经检测铸态组织,合金二次枝晶间距减少了30~40%。
[0032]
采用上述技术方案所产生的有益效果在于:本发明根据镍基高温合金中铝钛比,合理设计电渣渣系中al2o3和tio2的含量,有效抑制重熔过程中液滴穿越渣池中的反应进程,可稳定保持铝、钛收得率在95%以上;电渣过程中,采用抽锭式结晶器,利用co60液位检测装置定位金属熔池,在凝固前沿50~100mm范围内施加旋转磁场,可减轻成分过冷、减少元素偏析,转变传热模式、提高传热效率,电渣锭中nb、cr、ni、al、ti等主要元素宏观偏析指数为0.95~1.05之间,二次枝晶间距比传统电渣减少30~40%。
具体实施方式
[0033]
实施例1
[0034]
本实施例电渣重熔自耗电极为φ120
×
1500mm规格镍基高温合金,成分:c 0.1%,si 0.03%,mn 0.04%,p 0.012%,s 0.005%,cr 17%,mo 3.3%,ni 50%,ti 1.15%,al 0.2%,nb 4.75%,余量为铁及不可避免的杂质。结晶器规格φ150
×
600mm,内部距结晶器上沿200~400mm处内置co60液位检测装置和搅拌线圈。按下述步骤进行电渣重熔:
[0035]
(1)η=al/ti=0.2/1.15=0.174,
[0036][0037]
根据上述公式计算出渣系中al2o3、tio2的重量含量分别为23.6%、4.9%,渣系其它成分的重量含量分别为caf2:55%、cao:16.5%;
[0038]
将配比好的caf
2-cao-al2o
3-tio2渣系5kg通电熔化,熔清后升温至1450℃,维持30min充分脱除水分后,注入结晶器中,下降气氛保护罩,接通氩气,维持罩内压力1000pa,启动电渣重熔电源,以25v电压、1.5ka电流供电,将渣温升至1600℃。
[0039]
(2)进入重熔期,调整电压为30v、电流为2.5ka,控制熔速v为1.2kg/min,启动co60液位检测装置,待金属熔池末端50mm范围全部位于电磁搅拌线圈区域时开启电磁搅拌电源,电磁搅拌的频率2hz、电流50a。
[0040]
(3)开启抽锭系统,根据公式γ=4ξ*106v/[πρ(d-2)2],计算抽锭速度γ为8.62mm/min,至重熔期结束;
[0041]
其中,ξ为结晶器参数,此处取值为1;
[0042]
ρ为合金固相密度,为8.1g/cm3;
[0043]
d为结晶器内直径,为150mm。
[0044]
(4)补缩期逐步调整电压至25v、电流1.5ka,持续时间15min,熔炼结束。
[0045]
(5)熔炼结束30min后脱模,所得铸锭置于400℃加热炉内缓冷。
[0046]
进行两炉次试验,1#炉次按照上述工艺步骤操作,对比炉次2#炉次不开启电磁搅拌,其他步骤及参数与上述一致,两炉次所得铸锭进行分析,在距铸锭底部150mm和200mm处切片,在150mm截面取低倍样,分析低倍质量;在200mm截面中心处、r/4处、r/2处、3r/4处、边部取五个屑状样和金相样,检测化学成分和二次枝晶间距,得出元素收得率和偏析指数等参数,结果见表1。
[0047]
表1.所得铸锭质量及各元素的收得率情况
[0048][0049]
可以看出,1#、2#铸锭均无低倍缺陷;1#铸锭偏析指数优于2#铸锭,二次枝晶间距1#铸锭也小于2#铸锭30-40%。由此可见,该渣系选择非常合理,铸锭各项指标优良,特别是磁控电渣铸锭均匀性明显优于传统电渣。
[0050]
实施例2
[0051]
本实施例电渣重熔自耗电极为φ210
×
1800mm规格镍基高温合金,成分:c 0.08%,si 0.025%,mn 0.035%,p 0.015%,s 0.005%,cr 19%,mo 3%,ni 52%,ti 0.65%,al 1.25%,nb 5.05%,余量为铁及不可避免的杂质。结晶器规格φ300
×
700mm,内部距结晶器上沿200~400mm处内置co60液位检测装置和搅拌线圈。按下述步骤进行电渣重熔:
[0052]
(1)η=al/ti=1.25/0.65=1.92,
[0053][0054]
根据上述公式计算出渣系中al2o3、tio2的重量含量分别为36%、4.5%,渣系其它成分的重量含量分别为caf2:44.5%、cao:15%;
[0055]
将配比好的caf
2-cao-al2o
3-tio2渣系30kg通电熔化,熔清后升温至1550℃,维持40min充分脱除水分后,注入结晶器中,下降气氛保护罩,接通氩气,维持罩内压力1500pa,启动电渣重熔电源,以35v电压、3.5ka电流供电,将渣温升至1650℃。
[0056]
(2)进入重熔期,调整电压为45v、电流为5.5ka,控制熔速v为4kg/min,启动co60液位检测装置,待金属熔池末端80mm范围全部位于电磁搅拌线圈区域时开启电磁搅拌电源,电磁搅拌的频率2hz、电流100-200a。
[0057]
(3)开启抽锭系统,根据公式γ=4ξ*106v/[πρ(d-2)2],计算抽锭速度γ为7.17mm/
min,至重熔期结束;
[0058]
其中,ξ为结晶器参数,此处取值为1;
[0059]
ρ为合金固相密度,为8.0g/cm3;
[0060]
d为结晶器内直径,为300mm。
[0061]
(4)补缩期逐步调整电压至35v、电流3.5ka,持续时间45min,熔炼结束。
[0062]
(5)熔炼结束40min后脱模,所得铸锭置于550℃加热炉内缓冷。
[0063]
进行三炉次试验,1#、2#炉次采用不同的电磁搅拌参数,按照上述工艺步骤操作,对比炉次3#炉次不开启电磁搅拌,其他步骤及参数与上述一致,三炉次所得铸锭进行分析,在距铸锭底部200mm和300mm处切片,在200mm截面取低倍样,分析低倍质量;在300mm截面中心处、r/4处、r/2处、3r/4处、边部取五个屑状样和金相样,检测化学成分和二次枝晶间距,结果见表2。
[0064]
表2.各炉次电磁搅拌参数、所得铸锭质量及各元素的收得率
[0065][0066]
可以看出,1#、2#、3#铸锭均无低倍缺陷;1#、2#铸锭偏析指数均优于3#铸锭,二次枝晶间距1#、2#铸锭也小于3#铸锭30-40%,1#、2#铸锭质量差别不大,2#铸锭成分和组织更加均匀。由此可见,本例所选渣系合理,化学成分能够精确控制,铸锭质量优良;与此同时,电磁搅拌对于铸锭组织成分均匀性也起到了积极的作用。
[0067]
实施例3
[0068]
本实施例电渣重熔自耗电极为φ300
×
2000mm规格镍基高温合金,成分:c 0.06%,si 0.035%,mn 0.035%,p 0.005%,s 0.008,cr 21%,mo 2.8%,ni 55%,ti 1.05%,al 1.95%,nb 5.55%,余量为铁及不可避免的杂质。结晶器规格φ400
×
850mm,内部距结晶器上沿200~400mm处内置co60液位检测装置和搅拌线圈。按下述步骤进行电渣重熔:
[0069]
(1)η=al/ti=1.95/1.05=1.86,
[0070][0071]
根据上述公式计算出渣系中al2o3、tio2的重量含量分别为35.6%、4.55%,渣系其它成分的重量含量分别为caf2:30%、cao:30%;
[0072]
将配比好的caf
2-cao-al2o
3-tio2渣系50kg通电熔化,熔清后升温至1600℃,维持60min充分脱除水分后,注入结晶器中,下降气氛保护罩,接通氩气,维持罩内压力2000pa,
启动电渣重熔电源,以60v电压、5.5ka电流供电,将渣温升至1700℃。
[0073]
(2)进入重熔期,调整电压为50v、电流为7.5ka,控制熔速v为6kg/min,启动co60液位检测装置,待金属熔池末端100mm范围全部位于电磁搅拌线圈区域时开启电磁搅拌电源,电磁搅拌的频率6-8hz、电流300-400a。
[0074]
(3)开启抽锭系统,根据公式γ=4ξ*106v/[πρ(d-2)2],计算抽锭速度γ为4.60mm/min,至重熔期结束;
[0075]
其中,ξ为结晶器参数,此处取值为0.8;
[0076]
ρ为合金固相密度,为8.4g/cm3;
[0077]
d为结晶器内直径,为400mm。
[0078]
(4)补缩期逐步调整电压至45v、电流4.5ka,持续时间60min,熔炼结束。
[0079]
(5)熔炼结束60min后脱模,所得铸锭置于600℃加热炉内缓冷。
[0080]
进行四炉次试验,1#、2#、3#炉次采用不同的电磁搅拌参数,按照上述工艺步骤操作,对比炉次4#炉次不开启电磁搅拌,其他步骤及参数与上述一致,四炉次所得铸锭进行分析,在距铸锭底部300mm和400mm处切片,在300mm截面取低倍样,分析低倍质量;在400mm截面中心处、r/4处、r/2处、3r/4处、边部取五个屑状样和金相样,检测化学成分和二次枝晶间距,结果见表3。
[0081]
表3.各炉次电磁搅拌参数、所得铸锭质量及各元素的收得率
[0082][0083]
试验表明,1#、2#、3#、4#铸锭均无低倍缺陷;1#、2#、3#铸锭偏析指数均优于4#铸锭,1#、2#、3#铸锭二次枝晶间距也小于4#铸锭30-40%;1#、2#、3#铸锭质量差别不大,2#、3#铸锭成分和组织更加均匀。由此可见,本例所选渣系非常合理,元素命中率高,铸锭质量优良,与此同时,磁控电渣铸锭组织成分均匀性明显好于传统电渣。
[0084]
实施例4
[0085]
本实施例电渣重熔自耗电极为φ240
×
1800mm规格镍基高温合金,成分:c 0.04%,si 0.045%,mn 0.020%,p 0.010%,s 0.015%,cr 18%,mo 3.1%,ni 51%,ti 0.92%,al 1.46%,nb 5.33%,余量为铁及不可避免的杂质。结晶器规格φ350
×
750mm,内部距结晶器上沿200~400mm处内置co60液位检测装置和搅拌线圈。按下述步骤进行电渣重熔:
[0086]
(1)η=al/ti=1.46/0.92=1.59,
[0087][0088]
根据上述公式计算出渣系中al2o3、tio2的重量含量分别为34%、4.65%,渣系其它成分的重量含量分别为caf2:42%、cao:19.65%;
[0089]
将配比好的caf
2-cao-al2o
3-tio2渣系40kg通电熔化,熔清后升温至1488℃,维持35min充分脱除水分后,注入结晶器中,下降气氛保护罩,接通氩气,维持罩内压力1810pa,启动电渣重熔电源,以54v电压、2.9ka电流供电,将渣温升至1617℃。
[0090]
(2)进入重熔期,调整电压为33v、电流为6.4ka,控制熔速v为5.5kg/min,启动co60液位检测装置,待金属熔池末端50mm范围全部位于电磁搅拌线圈区域时开启电磁搅拌电源,电磁搅拌的频率3-5hz、电流200-400a。
[0091]
(3)开启抽锭系统,根据公式γ=4ξ*106v/[πρ(d-2)2],计算抽锭速度γ为6.35mm/min,至重熔期结束;
[0092]
其中,ξ为结晶器参数,此处取值为0.9;
[0093]
ρ为合金固相密度,为8.2g/cm3;
[0094]
d为结晶器内直径,为350mm。
[0095]
(4)补缩期逐步调整电压至35v、电流2.8ka,持续时间46min,熔炼结束。
[0096]
(5)熔炼结束53min后脱模,所得铸锭置于445℃加热炉内缓冷。
[0097]
进行四炉次试验,1#、2#、3#炉次采用不同的电磁搅拌参数,按照上述工艺步骤操作,对比炉次4#炉次不开启电磁搅拌,其他步骤及参数与上述一致,四炉次所得铸锭进行分析,在距铸锭底部300mm和400mm处切片,在300mm截面取低倍样,分析低倍质量;在400mm截面中心处、r/4处、r/2处、3r/4处、边部取五个屑状样和金相样,检测化学成分和二次枝晶间距,结果见表4。
[0098]
表4.所得铸锭质量及各元素的收得率情况
[0099][0100]
试验表明,1#、2#、3#、4#铸锭均无低倍缺陷;1#、2#、3#铸锭偏析指数均优于4#铸锭,1#、2#、3#铸锭二次枝晶间距也小于4#铸锭30-40%;1#、2#、3#铸锭质量差别不大,2#、3#铸锭成分和组织更加均匀。由此可见,本例所选渣系非常合理,元素收得率高,铸锭质量优
良,与此同时,磁控电渣铸锭组织成分均匀性明显好于传统电渣。
[0101]
实施例5
[0102]
本实施例电渣重熔自耗电极为φ400
×
2200mm规格镍基高温合金,成分:c 0.05%,si 0.033%,mn 0.045%,p 0.007%,s 0.009%,cr 20%,mo 2.9%,ni 54%,ti 0.76%,al 0.66%,nb 4.89%,余量为铁及不可避免的杂质。结晶器规格φ500
×
800mm,内部距结晶器上沿200~400mm处内置co60液位检测装置和搅拌线圈。按下述步骤进行电渣重熔:
[0103]
(1)η=al/ti=0.66/0.76=0.87,
[0104][0105]
根据上述公式计算出渣系中al2o3、tio2的重量含量分别为29.9%、4.8%,渣系其它成分的重量含量分别为caf2:46%、cao:19.3%;
[0106]
将配比好的caf
2-cao-al2o
3-tio2渣系70kg通电熔化,熔清后升温至1574℃,维持52min充分脱除水分后,注入结晶器中,下降气氛保护罩,接通氩气,维持罩内压力1360pa,启动电渣重熔电源,以52v电压、5.6ka电流供电,将渣温升至1674℃。
[0107]
(2)进入重熔期,调整电压为60v、电流为7.0ka,控制熔速v为8.5kg/min,启动co60液位检测装置,待金属熔池末端50mm范围全部位于电磁搅拌线圈区域时开启电磁搅拌电源,电磁搅拌的频率8-10hz、电流300-500a。
[0108]
(3)开启抽锭系统,根据公式γ=4ξ*106v/[πρ(d-2)2],计算抽锭速度γ为4.2mm/min,至重熔期结束;
[0109]
其中,ξ为结晶器参数,此处取值为0.8;
[0110]
ρ为合金固相密度,为8.3g/cm3;
[0111]
d为结晶器内直径,为500mm。
[0112]
(4)补缩期逐步调整电压至48v、电流4.7ka,持续时间71min,熔炼结束。
[0113]
(5)熔炼结束45min后脱模,所得铸锭置于550℃加热炉内缓冷。
[0114]
进行四炉次试验,1#、2#、3#炉次采用不同的电磁搅拌参数,按照上述工艺步骤操作,对比炉次4#炉次不开启电磁搅拌,其他步骤及参数与上述一致,四炉次所得铸锭进行分析,在距铸锭底部300mm和400mm处切片,在300mm截面取低倍样,分析低倍质量;在400mm截面中心处、r/4处、r/2处、3r/4处、边部取五个屑状样和金相样,检测化学成分和二次枝晶间距,结果见表5。
[0115]
表5.所得铸锭质量及各元素的收得率情况
[0116][0117][0118]
试验表明,1#、2#、3#、4#铸锭均无低倍缺陷;1#、2#、3#铸锭偏析指数均优于4#铸锭,1#、2#、3#铸锭二次枝晶间距也小于4#铸锭30-40%;1#、2#、3#铸锭质量差别不大,2#、3#铸锭成分和组织更加均匀。由此可见,本例所选渣系非常合理,铸锭成分组织优良,与此同时,磁控电渣铸锭组织成分均匀性明显好于传统电渣,相比而言,增加电流比增加频率对组织的均匀性作用更为明显。