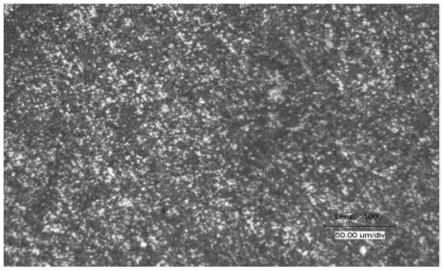
一种pai树脂基砂轮及其制备方法
技术领域
1.本发明涉及高分子树脂技术领域,具体涉及一种pai树脂基砂轮及其制备方法。
背景技术:2.砂轮是由许多极硬的磨粒经过结合剂粘结而成的切削工具。砂轮表面上坚硬的棱角颗粒称为磨料,起到切削作用。把磨料粘结在一起的粘结材料称为结合剂。砂轮的特性由磨料、粒度、结合剂、硬度、组织、形状、尺寸、线速度等因素影响,每种砂轮根据其砂型热性、基材性质、自身的耐热性能等都有一定的适用范围。磨料是砂轮的主要成分,直接担负切削的工作,必须具有很高的硬度、模量和热性能,常用磨料有氧化物陶瓷、碳化物、氮化物等。结合剂是砂轮中用来粘结磨料的物质,它的种类和性质将影响砂轮的强度、耐热性、耐冲击性和耐腐蚀性等性能,结合剂对磨削温度、工件表面粗糙度也有影响,常见结合剂一般有陶瓷类、树脂类、橡胶类、金属类等;其中树脂类结合剂要求具有强度大、弹性好、耐冲击,但存在耐热性差、受温后粘合力下降、脆性模量大、不宜长期存放的问题。
3.目前在对高硬度工件的精密磨削时,为保证最终高光洁度的工件产品质量,都希望采用树脂基砂轮作为加工的最后环节。常规的金刚石树脂砂轮所用结合剂主要是酚醛树脂、环氧树脂等。而酚醛树脂等在使用过程中存在以下不足:
①
耐热温度不高、粘合力小、脆性大,有部分金刚石未充分发挥作用而较早脱落,使其利用率降低,表现为砂轮不耐磨;
②
固化时必须加入固化剂乌洛托品,如果工艺条件控制不当,固化过程中产生的气体使砂轮组织出现气孔,有时致使砂轮报废;
③
不论在砂轮的制造还是使用过程中,经常散发出难闻的气味;
④
当进刀量大时,砂轮经常出现龟裂。另外还有聚酰亚胺(pi)树脂基金刚石砂轮,因选用的pi为热固型树脂,决定了在制备砂轮时,只能加载前段的成形载荷和后期的无、小载荷固化条件,所以会导致这类pi基金刚石砂轮整体致密差、强度低、不耐磨、脆性大的缺陷,在对工件进行磨削加工时,导致加工时间延长、加工效果变差,并且由于砂轮自磨损量增大,间接造成了生产成本提高、安全系数降低的不利因素。
技术实现要素:4.为了解决常规树脂制成的砂轮致密度差、强度低、不耐磨、脆性大所导致的磨削损耗大、加工时间长、加工效果差的技术问题,而提供一种pai树脂基砂轮及其制备方法。本发明以pai树脂作为结合剂与磨料混合,制成磨料均匀分散的砂轮,并在进行后期二次交联固化后能获得更高的强度及耐热性,使制得的砂轮致密度高、强度高、耐磨、耐热、韧性好,磨削的加工时间短、表面光洁度高。
5.为了达到以上目的,本发明通过以下技术方案实现:
6.本发明另一方面提供pai树脂基砂轮的制备方法,包括如下步骤:
7.(1)准备pai树脂、磨料、酸性有机物;对所述磨料进行偶联处理;
8.(2)将物料包括所述pai树脂、偶联处理的所述磨料以及所述酸性有机物进行预应力混合,在所述预应力混合的过程中进行抽真空使产生负压的同时进行加热,得到混合均
匀的物料;
9.(3)将支撑结构件固定在砂轮模具中,加入步骤(2)所述物料进行整体热模压成型,待完成成型后,于180~380℃下进行二次固化得到pai树脂基砂轮。
10.进一步地,所述pai树脂基砂轮中所述pai树脂占30-55wt%、所述磨料占44.7-65wt%、所述酸性有机物占0.3-5%。
11.进一步地,所述pai树脂的微观结构为片层簇状结构。
12.再进一步地,所述pai树脂按照水相合成聚酰胺-酰亚胺树脂的方法获得,在制备过程中控制原材料酸与二胺类化合物的总质量与加入的水的重量之比为1:(21~100),即可制得微观结构为片层簇状的pai树脂。优选地,原材料总质量与加入的水的重量之比为1:(25-80),更优选地原材料总质量与加入的水的重量之比为1:(30-50)。“水相合成聚酰胺-酰亚胺树脂的方法”参照中国专利cn202011184708.9中公开的内容进行制备pai,中国专利cn202011184708.9中公开的原材料对偏苯三甲酸与二胺类化合物总重量与水的重量之比为1:(5~20)其所制得的pai树脂的堆积密度在0.17~0.25g/cm3之间,微观结构并非片层簇状;而采用常规有机溶剂相合成的pai树脂其微观形貌为大小不均匀的颗粒状,堆积密度至少在0.23g/cm3以上;本发明中通过增大水的比例,使得在pai的制备过程中树脂总体的理化指标不变而仅改变树脂的微观形貌,使得到的pai呈现片层簇状结构,堆积密度为0.07-0.11g/cm3,具有较为松散的堆积密度,获得这一结果的原因是通过控制水料比中水的大比例量投入,使原材料单体在反应过程中溶胀,且溶胀过程中原材料分子在大比例水中具有更大的舒展空间,因此在单体聚合过程中改变了产物的微观形貌,最后得到片层簇状结构的pai树脂。由于片层簇状结构之间存在间隙,这种微观结构的pai可以为各种无机磨料预留驻存位,配合本发明的预应力混合方法,使得磨料不会因密度、粒径不同而产生分相,并确保最后制成的砂轮中磨料分布均匀。
13.进一步地,所述酸性有机物为具有α-h的化合物,具有α-h的化合物例如可以是异氰酸酯类、磺酰氯类、醛类、环氧类、羧酸类、酸酐类化合物中的一种或几种,优选地,所述酸性有机物为羧酸类化合物,更优选地,所述酸性有机物为酒石酸、草酸、苹果酸、枸椽酸、抗坏血酸、苯甲酸、水杨酸、咖啡酸中的一种或多种。这里的酸性有机物不能简单理解为广义上的羧酸类ph显酸性的化合物,可以将其理解为分子结构中具有α-h的化合物,α-h由于活性较高,具有一定酸性。酸性有机物可以促进pai在制备砂轮的热成型过程中发生快速的二次固化交联反应,可使制得的pai树脂基砂轮的玻璃化转变温度从约260℃提高到300℃以上,同时显著提升砂轮强度。
14.进一步地,所述磨料包括金刚石和金刚砂,所述金刚石与所述金刚砂的质量比为(6-10):(1-3);所述金刚石的粒径为50-250目、所述金刚砂的粒径为80-300目;所述金刚砂为碳化硅、或者碳化硅与氮化硼的混合物;所述磨料还包括金属粉,所述金属粉为锌粉、锡粉、铜粉、铁粉、锰粉、铝粉中的一种或多种,所述金属粉的粒径为600-1000目,所述金属粉的用量在所述pai树脂基砂轮中占1-20wt%。金属粉在磨料中可以作为填充料填充间隙,且同时作为导热链存在,可提升制得的pai树脂基砂轮的整体硬度,并延长砂轮整体工作寿命。
15.进一步地,所述预应力混合的过程中采用多种直径的钢球与所述物料进行混合,所述钢球的直径范围为10-50mm,所述钢球与所述物料的质量比为(1-3):1,所述预应力混
合的过程中真空度为-0.05~-0.09mpa、加热的温度为100~250℃、混合转速为500-3000rpm、混合的时间为0.5-3h。本发明中采用不同直径的钢球与物料在加热、负压的作用下混合,一方面可使物料表面吸附的水快速脱离,另一方面磨料在钢球、负压的作用力下插层进入到片层簇状pai的层间中,又在加热和外力的作用下使得被插层的片层簇状pai变软后产生层间的真空状态闭合,复合颗粒体积大为收缩,此时的状态可视为片层簇状结构pai的相邻层空间将单颗磨料收纳包含,且在不断转动的混合状态下,钢球的重力下落应力将软化了的片层簇状结构pai压成含料闭合的紧密状态,保证磨料被均匀的分散并在片层簇状pai的层间对磨料实现均匀的单分散包覆。预应力混合相较于常规粒子的常规高速混合等手段具有混合更加均匀的效果,使磨料在固化后得到的砂轮表现出更加稳定、牢固的分散均匀的状态。在预应力混合处理的过程下,整体物料的体积大为收缩,减少了含氧的空间,保证了物料在热模压成型的高温加热阶段发生氧化反应的几率大大降低,树脂在高温热熔时和磨料产生完全黏合,并在周边形成有韧性的保护层,使得砂轮在磨削工作时不会因整体体积的减少而产生脱砂、爆裂的问题,这样就大大提升了工作效率且延长了砂轮的工作寿命。
16.进一步地,所偶联处理的方法是将所述磨料与偶联剂处理液进行干法或湿法表面改性,所述偶联剂处理液是将偶联剂溶于水或酒精中配制成质量浓度为0.5-5wt%的处理液,所述偶联剂为耐300℃以上的硅烷类偶联剂,如kh-570、kh-900、sca-a10e、sca-v71m等,sca-a10e、sca-v71m相对成本较高,可耐高温至400℃,干法表面改性可采用混合设备将偶联剂处理液直接与干燥的磨料进行混合后烘干,湿法表面改性可采用将磨料分散在偶联剂处理液中进行搅拌加热反应后干燥;
17.所述热模压成型的温度为200-380℃、压力为20-100mpa、时间为50-150min,具体过程是通过加载压力排尽所述物料中空气后,开始梯度升温至350-380℃并以在60-100mpa的大载荷压力下保持模具内物料加热密实成型至少60min,然后再进行10-30min、60-100mpa的补压,然后进行恒压反向梯度降温,待降温至低于100℃后卸模完成热模压成型;所述热模压成型过程为梯度升温与梯度降温的过程,升温速率和降温速率为1-20℃/min,优选地升温速率和降温速率为3-15℃/min,更优选地升温速率和降温速率为5-12℃/min;
18.所述二次固化的具体过程为:100-200℃烘30-90min、200-300℃烘30-3000min、150-250℃烘30-80min、50-150℃烘20-100min,此过程为梯度升温与梯度降温的过程,升温速率和降温速率为1-20℃/min,优选地升温速率和降温速率为3-15℃/min,更优选地升温速率和降温速率为5-12℃/min;梯度升温与梯度降温的作用是保证成型后的砂轮在高致密度的状态下有相对稳定受热温度,使其不会因截面距离间的温度不同而产生不应当存在的热胀冷缩的膨胀与收缩应力,从而导致破坏整体砂轮结构的稳定性;另外关于二次固化的时长问题,应当保证树脂在该条件下能进行分子间的充分交联,使树脂基体在成型后具有更好的强度以及耐热性。
19.所述支撑结构件上与所述物料接触的部位需要先经过表面粗糙化处理再进行偶联处理,表面粗糙化处理例如可以进行手工打磨或器械打磨,使其粗糙度达到设定值从而获得更大的比表面积,而后续的偶联处理能够使金属支撑结构件的金属小分子被附着一层中分子量的硅烷偶联剂,使在高温热熔时该耐热硅烷偶联剂产生较大的粘附性能将金属与树脂基体进行有效粘附,起到粘合度与附着力桥梁的作用,增加树脂基体物料对金属支撑
结构件的附着力,并使得砂轮整体材料的应力支撑、热传导效果更好。
20.本发明最后一方面提供由上述制备方法获得的pai树脂基砂轮。
21.有益技术效果:
22.本发明通过采用片层簇状微观形貌结构的pai结合预应力混合技术,将pai与磨料等物质进行混合,在钢球重力作用、抽真空负压作用、以及加热作用下使得磨料被均匀的分散在片层簇状pai的层间并被pai所包覆,使制得的砂轮中的磨料分散的更加均匀。
23.本发明制备pai基树脂砂轮中磨料分散均匀,并能够与结构件高强度偶合粘接,是具有自锐性好、不易堵塞、减少工件烧伤现象的高质量的金刚石树脂砂轮。在高速磨削与超精密研磨的技术领域的实际应用过程中,展现出了加工效果好、磨削负荷大、研磨速度高、使用寿命长等的显著特性。
附图说明
24.图1a为常规金刚石金属烧结砂轮的实物图,图1b为pai树脂基砂轮的实物图。
25.图2为pai树脂基砂轮在金相显微镜下观察到的磨料分散状态图。
26.图3为片层簇状pai树脂的微观显微sem图。
27.图4为常规有机溶剂相合成的pai树脂的微观显微sem图,该常规有机溶剂相合成的pai树脂购自苏威(solvay)集团。
具体实施方式
28.下面将结合本发明的实施例和附图,对本发明实施例中的技术方案进行清楚、完整地描述,显然,所描述的实施例仅仅是本发明一部分实施例,而不是全部的实施例。以下对至少一个示例性实施例的描述实际上仅仅是说明性的,决不作为对本发明及其应用或使用的任何限制。基于本发明中的实施例,本领域普通技术人员在没有作出创造性劳动前提下所获得的所有其他实施例,都属于本发明保护的范围。
29.除非另外具体说明,否则在这些实施例中阐述的数值不限制本发明的范围。对于相关领域普通技术人员已知的技术、方法可能不作详细讨论,但在适当情况下,所述技术、方法应当被视为说明书的一部分。在这里示出和讨论的所有示例中,任何具体值应被解释为仅仅是示例性的,而不是作为限制。因此,示例性实施例的其它示例可以具有不同的值。
30.实施例1
31.一种pai树脂基砂轮的制备方法,包括如下步骤:
32.(1)准备物料:片层簇状pai树脂45wt%、碳化硅(150目)45wt%、金刚石(60目)8%、酸性有机物(抗坏血酸与水杨酸,两者等质量比)2%;
33.对碳化硅和金刚石两种磨料进行偶联处理:将上述两种磨料与偶联剂处理液进行干法表面改性,偶联剂处理液是sca-a10e的水-乙醇溶液,质量浓度3.5%,按照磨料与偶联剂处理液的质量比为1:2,将偶联剂处理液分至少3批次喷至不断搅拌的磨料中,搅拌过程中加热温度为65℃,待偶联剂处理液全部喷完后,再继续搅拌1h,出料,干燥后待用;
34.(2)将物料包括所述片层簇状pai树脂、偶联处理的所述磨料以及所述酸性有机物进行预应力混合,在所述预应力混合的过程中进行抽真空使产生负压的同时进行加热,得到混合均匀的物料,具体预应力混合的条件为:采用直径分别是10mm、20mm、30mm、50mm的钢
球(四种直径钢球按照质量比为2:2:1:1配置)与所述物料进行混合,钢球总质量与上述物料的质量比为2:1,预应力混合的过程中真空度为-0.08mpa、加热的温度为280℃、混合转速为2000rpm、混合的时间为2h;预应力混合完成后待用;
35.(3)将制备砂轮的金属支撑结构件(与所述物料接触的部位)先进行打磨处理再进行偶联处理,打磨处理可以采用砂纸进行手工打磨或者采用常规打磨设备打磨至金属支撑结构件的表面粗糙度大于n11 ra=25
的国标标注后,偶联处理为采用偶联剂处理液的喷涂处理(偶联剂处理液仍然采用上述步骤1中的进行),然后干燥待用;
36.将打磨及偶联处理后的金属支撑结构件固定在砂轮模具中,在模具以及金属支撑结构件所构成的区域内加入步骤(2)预应力混合均匀的物料,进行整体热热模压成型,通过加载压力排尽物料中空气后,开始梯度升温(升温速率设定5-8℃/min)至370℃并以在10-80mpa的大载荷压力下保持模具内物料的加热密实成型至少80min,然后再进行20min、40mpa的补压,保证成型后砂轮的工作体具有整体致密高、强度大、耐磨削、韧性好,然后进行泄压、并梯度降温(降温速率设定5-8℃/min)至低于100℃后卸模完成热模压成型并得到半成品;
37.然后将半成品在高温烘箱中进行二次固化:200℃烘50min、250℃烘40min、280℃烘500min、230℃烘60min、120℃烘40min,此过程为梯度升温和梯度降温的过程,升温速率和降温速率为5-8℃/min,最后冷却后制得pai树脂基砂轮,制成的pai树脂基砂轮实物图如图1b所示。
38.将本实施例制得的pai树脂基砂轮置于金相显微镜下观察pai树脂中母料的分散状况,结果如图2所示,由图2可知,pai树脂基体中的磨料分散的非常均匀。
39.本实施例中片层簇状微观结构的pai树脂的获得参照中国专利cn202011184708.9实施例1的方法,不同之处在于,改变了步骤(2)中水的加入量为13000g,使对偏苯三甲酸212g与二苯醚二胺220g的总质量与水13000g的重量之比为1:30。产物pai的微观形貌sem图如图3所示,由图3可知,pai微观上呈现片层簇状结构,微观结构较为均匀。对片层簇状结构的pai进行特性粘数测试,测得片层簇状pai的特性粘数在0.7-1dl/g的范围内;对片层簇状结构的pai进行差式扫描量热分析(dsc),其玻璃化转变温度在275~285℃的范围内;对片层簇状结构的pai进行堆积密度的测试,测得片层簇状结构的pai堆积密度在0.07-0.11g/cm3范围内,较为松散,该松散的堆积密度与图3的sem的结果相对应,由于微观上表现出片层簇状结构,存在较多的间隙或空隙,宏观上即表现出较小的堆积密度值。而常规有机溶剂相合成的pai树脂其微观形貌如图4所示,由图4可知,有机溶剂相合成的pai树脂颗粒大小不均匀,测得其堆积密度至少在0.23g/cm3以上,颗粒之间的空隙很小;中国专利cn202011184708.9中公开的原材料总重量与水的重量之比为1:(5~20)所制得的pai树脂,其微观结构与图4相似,堆积密度在0.17~0.25g/cm3之间,相较于常规有机溶剂相合成的pai树脂的堆积密度稍小。
40.片层簇状pai树脂的获得只需控制中国专利cn202011184708.9中水料比为(21-100):1,投加的水量越多获得的产物越松散,但是过多的水量加入也是不适宜的,优选水料比为(30-50):1,通过加大水的用量即能够实现对pai树脂微观形貌的改变,得到片层簇状微观结构的pai树脂,且pai树脂的理化性质不发生改变。
41.实施例2
42.一种pai树脂基砂轮的制备方法,包括如下步骤:
43.(1)准备材料:片层簇状pai树脂40wt%、碳化硅(200目)32wt%、金刚石(60目)12%、锌粉(800目)14.5%、酸性有机物(草酸和酒石酸,等质量比)1.5%;
44.对碳化硅、金刚石、锌粉三种磨料进行偶联处理:将上述两种磨料与偶联剂处理液进行干法表面改性,偶联剂处理液是sca-v71m的水-乙醇溶液,质量浓度5%,按照磨料与偶联剂处理液的质量比为1:3,将偶联剂处理液分至少3批次喷至不断搅拌的磨料中,搅拌过程中加热温度为65℃,待偶联剂处理液全部喷完后,再继续搅拌2h,出料,干燥后待用;
45.(2)将物料包括所述片层簇状pai树脂、偶联处理的所述磨料以及所述酸性有机物进行预应力混合,在所述预应力混合的过程中进行抽真空使产生负压的同时进行加热,得到混合均匀的物料,具体预应力混合的条件为:采用直径分别是10mm、20mm、30mm、50mm的钢球(四种直径钢球按照质量比为2:2:1:1配置)与所述物料进行混合,钢球总质量与上述物料的质量比为2:1,预应力混合的过程中真空度为-0.09mpa、加热的温度为280℃、混合转速为1500rpm、混合的时间为2.5h;预应力混合完成后待用;
46.(3)将制备砂轮的金属支撑结构件(与所述物料接触的部位)先进行打磨处理再进行偶联处理,打磨处理可以采用砂纸进行手工打磨或者采用常规打磨设备打磨至金属支撑结构件的表面粗糙度大于n11 ra=25
的国标标注后,偶联处理为采用偶联剂处理液的喷涂处理(偶联剂处理液仍然采用上述步骤1中的进行),然后干燥待用;
47.将打磨及偶联处理后的金属支撑结构件固定在砂轮模具中,在模具以及金属支撑结构件所构成的区域内加入步骤(2)预应力混合均匀的物料,进行整体热模压成型,通过加载压力排尽物料中空气后,开始梯度升温(升温速率设定5-8℃/min)至360℃并以在10-80mpa的大载荷压力下保持模具内物料的加热密实成型至少90min,然后再进行10min、40mpa的补压,保证成型后砂轮的工作体具有整体致密高、强度大、耐磨削、韧性好,然后进行泄压、并梯度降温(降温速率设定5-8℃/min)至低于100℃后卸模完成热模压成型并得到半成品;
48.然后将半成品在高温烘箱中进行二次固化:200℃烘70min、220℃烘50min、260℃烘500min、220℃烘80min、120℃烘60min,此过程为梯度升温和梯度降温的过程,升温速率和降温速率为5-8℃/min,最后冷却后制得pai树脂基砂轮。
49.本实施例中片层簇状pai树脂与实施例1中的相同,不同之处在于制备过程中控制水料比为50:1。
50.对比例1
51.本实施例pai树脂基砂轮的制备方法与实施例1相同,不同之处在于,采用的pai树脂为中国专利cn202011184708.9实施例1中制得的pai树脂(即水料比为10:1)。
52.对比例2
53.本实施例pai树脂基砂轮的制备方法与实施例1相同,不同之处在于,采用pai为有机溶剂相合成的pai(购自苏威集团)。
54.对比例3
55.本实施例pai树脂基砂轮的制备方法与实施例1相同,不同之处在于,将物料进行常规高速混合(未抽真空负压、未加钢球),高速混合的转速为3000rpm,高速混合过程其他条件如加热温度、混合时间等均与实施例1中相同。
56.对比例4
57.本实施例pai树脂基砂轮的制备方法与实施例1相同,不同之处在于,在预应力混合过程中未进行抽真空至负压。
58.对比例5
59.本实施例pai树脂基砂轮的制备方法与实施例1相同,不同之处在于,在预应力混合过程中未加入钢球。
60.对比例6
61.本实施例pai树脂基砂轮的制备方法与实施例1相同,不同之处在于,不加入酸性物质且不进行二次固化。
62.实施例3
63.将以上实施例1-2、对比例1-5制得的pai树脂基砂轮应用于加工99%氧化铝(al2o3)陶瓷管(该材料的管材硬度接近金刚石),管材长度为100mm、内径为89mm,需要将其加工至内径为95mm。
64.以上砂轮尺寸:外径80mm、厚度20mm、砂轮工作层(指含pai树脂基及磨料的工作层)厚度10mm。
65.以上砂轮对99%氧化铝(al2o3)陶瓷管的磨削加工时间、砂轮外圈磨损以及对该材料(指99%氧化铝陶瓷)的工作寿命等性能进行了测试,具体见表1。
66.表1实施例1-2、对比例1-5制得的砂轮性能
[0067][0068][0069]
(注:表中常规指的是金刚石金属烧结砂轮,其表面具有金刚石烧结层,金刚石烧结层厚度为0.6mm,其实物图如图1a所示)
[0070]
由表1可知,本发明采用片层簇状pai作为粘结剂,加入磨料和酸性进行预应力混合后进行热模压成型,然后进行二次固化后得到pai树脂基砂轮,本发明得到的砂轮对工件的磨削时间更短,只需20min左右,且磨削后砂轮表面光洁度仍然非常好,不见磨痕,砂轮外
圈的磨损量非常低小于0.15mm,对99%氧化铝陶瓷的工作寿命至少为120个以上,具有较高的工作效率及较长的工作寿命。
[0071]
对比例1的砂轮采用的粘结剂为水料比为10:1制得的pai,对比例2的砂轮采用常规有机溶剂相合成的pai,两者微观结构均不具有片层簇状结构,用其制成的砂轮对工件的磨削时间较长至少为25min,且砂轮外圈磨损量较本发明的稍微大,工作寿命较短。
[0072]
对比例3-5的数据说明因未完全采用优化的预应力混合手段,故无法保证磨料被均匀的分散在片层簇状pai的层间,故无法实现本发明所能达到的均匀单分散包覆状态的技术效果,因此导致磨料是非均匀分散,影响树脂在高温热熔时和磨料的粘合程度,并无法实现在周边形成有韧性的保护层,而这将导致砂轮在磨削工作时产生脱砂,脱砂后即为单纯的pai树脂与陶瓷相磨,因此产生砂轮整体不耐磨的问题。对比例6的砂轮未加入酸性物质则不能进行二次固化,未进行二次固化的砂轮其耐热性较差。
[0073]
本发明采用预应力混合的手段能够很大程度上提升砂轮的工作寿命,这得益于预应力混合手段能够将磨料更加均匀地分散在树脂基体中,实现颗粒的单分散效果。
[0074]
以上所述,仅为本发明较佳的具体实施方式,但本发明的保护范围并不局限于此,任何熟悉本技术领域的技术人员在本发明揭露的技术范围内,根据本发明的技术方案及其发明构思加以等同替换或改变,都应涵盖在本发明的保护范围之内。