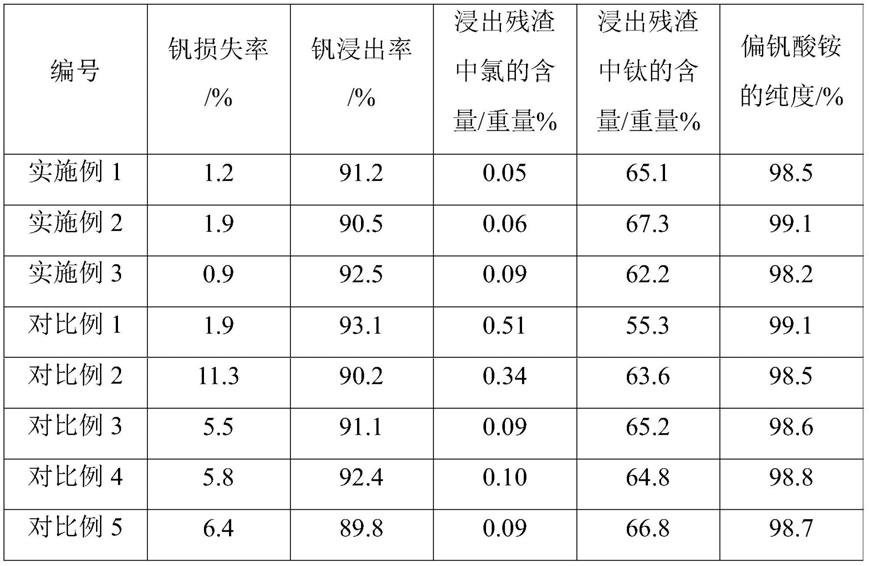
1.本发明涉及冶金化工领域,具体涉及一种利用四氯化钛精制尾渣提钒的方法。
背景技术:2.钒钛磁铁矿经高炉冶炼后产生的高炉渣中含有约45%的tio2,高炉渣采用高温碳化-低温氯化工艺提钛技术,一般将氯化得到的四氯化钛称为粗四氯化钛液,其中含有钒等杂质需要处理,采用有机物除钒法处理粗四氯化钛液具有除钒成本低、工艺流程简单等优点,是目前的主流工艺。得到的四氯化钛精制尾渣中含有大量的钒、钛、氯(四氯化钛精制尾渣中的钒主要以氯化物或氯氧化物形式存在),具有较高的回收价值,但此种四氯化钛精制尾渣遇空气易发生氧化和水解反应,产生挥发性hcl、cl2气体,部分钒氯化物也易挥发,处理难度较大。目前,有机物除钒法得到的四氯化钛精制尾渣的处理技术主要有高温焙烧-浸出、高温氯化工艺,实现钒钛的选择性分离。一般均需要对四氯化钛精制尾渣进行脱氯处理,但目前采用高温焙烧的方式,不仅焙烧阶段能耗较高,同时会产生大量烟气,造成环境污染,在焙烧过程中还会导致大量钒挥发损失。
3.专利申请cn104004920a公开了一种从四氯化钛精制尾渣中提钒的方法,将四氯化钛精制尾渣与碳酸钙、碳酸镁等熔剂混合,在840℃-950℃下进行高温焙烧2h-5h,再将焙烧后的熟料破碎后与水混合并加入硫酸进行浸出,提钒率达到90wt%以上。该方法需采用硫酸浸出,成本较高且会导致浸出液中杂质含量偏高,后续需要净化除杂处理。
4.专利申请cn103540751a公开了一种四氯化钛精制尾渣的处理方法,以铝粉除钒法得到四氯化钛精制尾渣为原料,采用氧化钙水溶液进行中和固氯处理,料浆ph=8-10搅拌20min-60min,经固液分离后,得到滤饼与滤液两种物质,滤饼干燥即可用做钒合金冶炼的原料,所得水溶液可用于溶液中磷、硅的净化处理。该方法利用氧化钙和钒反应生产钒酸钙盐沉淀,一方面氧化钙耗量高,同时会导致滤饼含钙较高,对钒合金冶炼不利。
5.专利申请cn106929696a和cn107032400a分别公开了一种ticl4精制尾渣铵浸和碱浸提钒的方法,均采用将ticl4精制尾渣焙烧处理后进行浸出,得到浸出液经净化除杂沉钒工序制得五氧化二钒。但在高温氧化焙烧过程中大量钒、氯挥发进入烟气,钒损失率较高。
6.专利申请cn110683579a公开了一种从四氯化钛精制除钒尾渣生产高纯五氧化二钒的方法,精制除钒尾渣经预处理、氯化、除尘、淋洗等七个工序,可制得高纯五氧化二钒粉体。该工艺相对流程较长,且仍需要焙烧预处理。
技术实现要素:7.本发明的目的是为了克服现有技术中对四氯化钛精制尾渣的处理焙烧阶段能耗较高,同时会产生大量烟气,造成环境污染,在焙烧过程中还会导致大量钒挥发损失的问题,提供一种利用四氯化钛精制尾渣提钒的方法,该方法通过两段焙烧实现了脱氯过程,同时能有效减少钒的挥发损失。
8.为了实现上述目的,本发明提供一种利用四氯化钛精制尾渣提钒的方法,该方法
包括以下步骤:
9.(1)将四氯化钛精制尾渣在100-300℃下焙烧5-30min,得到预处理渣;
10.(2)将步骤(1)得到的预处理渣与碳酸钠混合,在600-900℃下焙烧60-120min,得到焙烧熟料;
11.(3)向步骤(2)得到的焙烧熟料中加水,进行搅拌浸出,然后固液分离,得到含钒浸出液和浸出残渣。
12.优选地,在步骤(1)中,所述四氯化钛精制尾渣中钒的含量为10-30重量%。
13.优选地,在步骤(1)中,所述四氯化钛精制尾渣中氯的含量为10-50重量%。
14.优选地,在步骤(1)中,所述焙烧的气氛为含氧气氛。
15.优选地,在步骤(1)中,所述含氧气氛为空气和/或氧气。
16.优选地,在步骤(2)中,所述碳酸钠与所述四氯化钛精制尾渣中的钒的物质的量的比为(1-4):1。
17.优选地,在步骤(2)中,所述焙烧的气氛为空气和/或氧气。
18.优选地,在步骤(3)中,所述水与所述焙烧熟料的液固比为1-10ml/g。
19.优选地,在步骤(3)中,所述搅拌浸出的温度为50-95℃。
20.优选地,在步骤(3)中,所述搅拌浸出的时间为30-120min。
21.本方法通过两段焙烧实现了对四氯化钛精制尾渣的脱氯过程,同时能够有效减少钒的挥发损失。
具体实施方式
22.以下对本发明的具体实施方式进行详细说明。应当理解的是,此处所描述的具体实施方式仅用于说明和解释本发明,并不用于限制本发明。
23.在本文中所披露的范围的端点和任何值都不限于该精确的范围或值,这些范围或值应当理解为包含接近这些范围或值的值。对于数值范围来说,各个范围的端点值之间、各个范围的端点值和单独的点值之间,以及单独的点值之间可以彼此组合而得到一个或多个新的数值范围,这些数值范围应被视为在本文中具体公开。
24.本发明提供一种利用四氯化钛精制尾渣提钒的方法,该方法包括以下步骤:
25.(1)将四氯化钛精制尾渣在100-300℃下焙烧5-30min,得到预处理渣;
26.(2)将步骤(1)得到的预处理渣与碳酸钠混合,在600-900℃下焙烧60-120min,得到焙烧熟料;
27.(3)向步骤(2)得到的焙烧熟料中加水,进行搅拌浸出,然后固液分离,得到含钒浸出液和浸出残渣。
28.在本发明中,在步骤(1)中,所述四氯化钛精制尾渣中钒的含量为10-30重量%。具体地,所述四氯化钛精制尾渣中钒的含量可以为10重量%、12.5重量%、15重量%、17.5重量%、20重量%、22.5重量%、25重量%、27.5重量%或30重量%。
29.在本发明中,在步骤(1)中,所述四氯化钛精制尾渣中氯的含量为10-50重量%。具体地,所述四氯化钛精制尾渣中氯的含量可以为10重量%、15重量%、20重量%、25重量%、30重量%、35重量%、40重量%、45重量%或50重量%。
30.在本发明中,在步骤(1)中,所述焙烧的气氛为含氧气氛。优选地,在步骤(1)中,所
述含氧气氛为空气和/或氧气。
31.在具体的实施方式中,在步骤(1)中,所述焙烧的温度可以为100℃、125℃、150℃、175℃、200℃、225℃、250℃、275℃或300℃,所述焙烧的时间可以为5min、7.5min、10min、12.5min、15min、17.5min、20min、22.5min、25min、27.5min或30min。
32.在优选情况下,在步骤(2)中,所述碳酸钠与所述四氯化钛精制尾渣中的钒的物质的量的比为(1-4):1。具体地,所述碳酸铵与所述四氯化钛精制尾渣中的钒的物质的量的比可以为1:1、1.5:1、2:1、2.5:1、3:1、3.5:1或4:1。
33.在本发明中,在步骤(2)中,所述焙烧的气氛为空气和/或氧气。
34.在具体的实施方式中,在步骤(2)中,所述焙烧的温度可以为600℃、625℃、650℃、675℃、700℃、725℃、750℃、775℃、800℃、825℃、850℃、875℃或900℃,所述焙烧的时间可以为60min、65min、70min、75min、80min、85min、90min、95min、100min、105min、110min、115min或120min。
35.在优选情况下,在步骤(3)中,所述水与所述焙烧熟料的液固比为1-10ml/g。具体地,所述水与所述焙烧熟料的液固比可以为1ml/g、2ml/g、3ml/g、4ml/g、5ml/g、6ml/g、7ml/g、8ml/g、9ml/g或10ml/g。
36.在优选情况下,在步骤(3)中,所述搅拌浸出的温度为50-95℃。具体地,所述搅拌浸出的温度可以为50℃、55℃、60℃、65℃、70℃、75℃、80℃、85℃、90℃或95℃。
37.在优选情况下,在步骤(3)中,所述搅拌浸出的时间为30-120min。具体地,所述搅拌浸出的时间可以为30min、40min、50min、60min、70min、80min、90min、100min、110min或120min。
38.本发明通过对四氯化钛精制尾渣短时间氧化焙烧预处理,再加入碳酸钠高温焙烧后,得到焙烧熟料,将焙烧熟料加水搅拌浸出后,固液分离得到含钒浸出液和浸出残渣,钒浸出率高,含钒浸出液无需除杂,采用弱碱性铵盐沉钒工艺,按加铵系数为2加入氯化铵搅拌均匀后(加铵系数为氯化铵与含钒浸出液中钒的重量比),将ph值调整至7.5-8.5,在50℃下反应2h,经固液分离即可得到98级以上偏钒酸铵产品。
39.本发明与现有技术相比,具有以下积极效果:
40.(1)通过两段焙烧实现了脱氯过程,同时能够有效减少钒的挥发损失。
41.(2)采用水浸工艺实现钒的高效浸出,浸出液中杂质含量少;水浸工艺可有效减少杂质溶解进入含钒浸出液。
42.(3)四氯化钛精制尾渣中的氯得到有效脱除,浸出残渣中氯含量小于0.1重量%,钛含量在60重量%以上,可用作提钛原料,解决了精制尾渣的环境污染问题。
43.以下将通过实施例对本发明进行详细描述,但本发明所述的方法不仅限于此。
44.以下实施例和对比例中所用的四氯化钛精制尾渣均来自于氯化钛白工艺中粗四氯化钛脂肪酸精制除钒产生;
45.实施例中所用四氯化钛精制尾渣主要化学成分如表1所示。
46.表1四氯化钛精制尾渣主要化学成分/重量%
47.编号vclticcafesial1#10101441.16.31.33.22#28.341.610100.54.80.82.6
3#18261240.72.60.71.9
48.实施例1
49.(1)将100g表1中的1
#
四氯化钛精制尾渣在100℃下焙烧30min(焙烧的气氛为氧气),得到预处理渣;
50.(2)将步骤(1)得到的预处理渣与31g碳酸钠混合,在600℃下焙烧120min(焙烧的气氛为空气),得到焙烧熟料;
51.(3)按照水与焙烧熟料的液固比为5ml/g向步骤(2)得到的焙烧熟料中加水,进行搅拌浸出,搅拌浸出的温度为50℃,搅拌浸出的时间为120min,然后固液分离,得到含钒浸出液和浸出残渣;
52.含钒浸出液无需除杂,按加铵系数为2加入氯化铵搅拌均匀后,将ph值调整至8,在50℃下反应2h,固液分离得到偏钒酸铵沉淀。
53.实施例2
54.(1)将100g表1中的2
#
四氯化钛精制尾渣在100℃下焙烧5min(焙烧的气氛为氧气),得到预处理渣;
55.(2)将步骤(1)得到的预处理渣与230g碳酸钠混合,在900℃下焙烧60min(焙烧的气氛为氧气),得到焙烧熟料;
56.(3)按照水与焙烧熟料的液固比为10ml/g向步骤(2)得到的焙烧熟料中加水,进行搅拌浸出,搅拌浸出的温度为95℃,搅拌浸出的时间为30min,然后固液分离,得到含钒浸出液和浸出残渣;
57.含钒浸出液无需除杂,按加铵系数为2加入氯化铵搅拌均匀后,将ph值调整至8,在50℃下反应2h,固液分离得到偏钒酸铵沉淀。
58.实施例3
59.(1)将100g表1中的3
#
四氯化钛精制尾渣在200℃下焙烧20min(焙烧的气氛为氧气),得到预处理渣;
60.(2)将步骤(1)得到的预处理渣与112g碳酸钠混合,在800℃下焙烧90min(焙烧的气氛为空气),得到焙烧熟料;
61.(3)按照水与焙烧熟料的液固比为1ml/g向步骤(2)得到的焙烧熟料中加水,进行搅拌浸出,搅拌浸出的温度为65℃,搅拌浸出的时间为90min,然后固液分离,得到含钒浸出液和浸出残渣;
62.含钒浸出液无需除杂,按加铵系数为2加入氯化铵搅拌均匀后,将ph值调整至8,在50℃下反应2h,固液分离得到偏钒酸铵沉淀。
63.对比例1
64.采用现有技术对四氯化钛精制尾渣进行提钒,具体步骤为:按照实施例1所述的方法实施,与之不同的是,不进行步骤(2)的焙烧处理,直接按照水与预处理渣的液固比为5ml/g,向预处理渣中加水进行搅拌浸出,搅拌浸出的温度为50℃,搅拌浸出的时间为120min,然后固液分离,得到含钒浸出液和浸出残渣;
65.含钒浸出液需进行除杂处理,主要杂质为ti,浓度可达12g/l,除杂过程钒损率一般为15%左右,对含钒浸出液除杂后按加铵系数为2加入氯化铵搅拌均匀后,将含钒浸出液ph值调整至8,固液分离得到偏钒酸铵沉淀。
66.对比例2
67.按照实施例1所述的方法实施,与之不同的是,四氯化钛精制尾渣不进行步骤(1)的焙烧处理,直接将与实施例1相同的四氯化钛精制尾渣与31g碳酸钠混合,在600℃下焙烧120min(焙烧的气氛为空气),得到焙烧熟料;
68.(2)按照水与焙烧熟料的液固比为5ml/g向步骤(2)得到的焙烧熟料中加水,进行搅拌浸出,搅拌浸出的温度为50℃,搅拌浸出的时间为120min,然后固液分离,得到含钒浸出液和浸出残渣;
69.含钒浸出液无需除杂,按加铵系数为2加入氯化铵搅拌均匀后,将含钒浸出液ph值调整至8,固液分离得到偏钒酸铵沉淀。
70.对比例3
71.按照实施例2所述的方法实施,与之不同的是,在步骤(1)中,焙烧的温度为80℃;
72.得到含钒浸出液和浸出残渣,含钒浸出液无需除杂,按加铵系数为2加入氯化铵搅拌均匀后,将含钒浸出液ph值调整至8,固液分离得到偏钒酸铵沉淀。
73.对比例4
74.按照实施例2所述的方法实施,与之不同的是,在步骤(1)中,焙烧的时间为3min;
75.得到含钒浸出液和浸出残渣,含钒浸出液无需除杂,按加铵系数为2加入氯化铵搅拌均匀后,将含钒浸出液ph值调整至8,固液分离得到偏钒酸铵沉淀。
76.对比例5
77.按照实施例3所述的方法实施,与之不同的是,在步骤(1)中,焙烧的温度为400℃;
78.得到含钒浸出液和浸出残渣,含钒浸出液无需除杂,按加铵系数为2加入氯化铵搅拌均匀后,将含钒浸出液ph值调整至8,固液分离得到偏钒酸铵沉淀。
79.测试例
80.分别检测实施例1-3,对比例1-5的钒损失率、钒浸出率、浸出残渣中氯的含量、钛的含量以及得到的偏钒酸铵的纯度;
81.钒损失率的计算方法为:四氯化钛精制尾渣中钒重量m1,预处理渣中钒重量m2,钒损失率σ1=1-m2/m1;
82.其中,对比例2中因为没有进行步骤(1)的焙烧处理,因此在对比例2中,钒损失率的计算方法为:四氯化钛精制尾渣中钒重量m1,焙烧熟料中钒重量m2,钒损失率σ1=1-m2/m1。
83.钒浸出率计算方法为:焙烧熟料中钒重量m3,浸出残渣中钒重量m4,钒浸出率σ2=1-m4/m3;
84.其中,对比例1中因为没有进行步骤(2)的焙烧处理,因此在对比例1中,钒浸出率计算方法为:预处理渣中钒重量m3,浸出残渣中钒重量m4,钒浸出率σ2=1-m4/m3。
85.采用x射线荧光光谱检测浸出残渣中氯的含量、钛的含量以及偏钒酸铵的纯度。
86.结果如表2所示。
87.表2
[0088][0089]
通过表1的结果可以看出,采用本发明的方法,在对四氯化钛精制尾渣进行提钒时焙烧过程中钒损失极小,并且钒浸出率在90%以上,浸出残渣中氯含量小于0.1重量%,钛含量在60重量%以上,可用作提钛原料,浸出液无需除杂,经过沉钒步骤可得到98级以上的偏钒酸铵产品。
[0090]
以上详细描述了本发明的优选实施方式,但是,本发明并不限于此。在本发明的技术构思范围内,可以对本发明的技术方案进行多种简单变型,包括各个技术特征以任何其它的合适方式进行组合,这些简单变型和组合同样应当视为本发明所公开的内容,均属于本发明的保护范围。