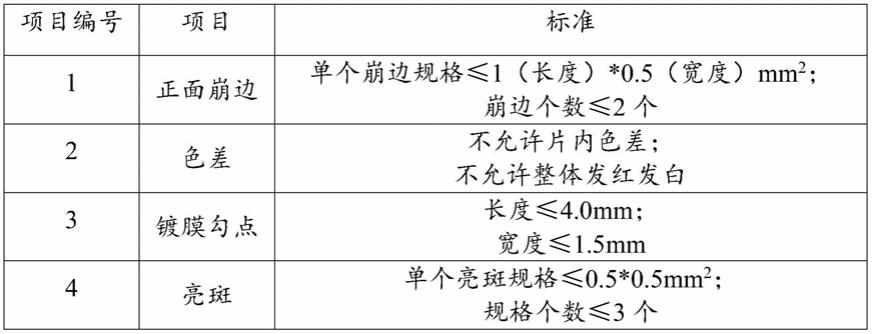
1.本技术涉及太阳能电池领域,具体而言,涉及一种镀膜工艺。
背景技术:2.硅片作为光伏发电最主要的原料之一,是太阳能电池加工成本中最昂贵的部分,因此降低硅片的成本是降低光伏发电成本最有效的方法之一。目前,降低硅片成本最有效的方法就是硅片薄片化。然而,硅片做薄之后,相应地对太阳能电池制程有更高的要求。
3.镀膜作为太阳能电池生产过程中的一道工序,在镀膜过程中需要把硅片插进石墨舟,然后通过射频放电在硅片表面镀上一层氮化硅薄膜,在镀膜过程中,需要在较高的温度条件下进行,同时需要进行射频放电。
4.在目前的镀膜工艺中,容易出现高频,在出现高频时,需要重新进行镀膜,导致产能受到影响,并使得产品不良率升高。
技术实现要素:5.本技术的目的在于提供一种镀膜工艺,能减少镀膜中高频出现的次数,从而能提高产能并降低产品不良率。
6.本技术的实施例是这样实现的:
7.本技术实施例提供一种镀膜工艺,包括:
8.在进舟后,依次进行升温处理、第一次抽真空处理、检漏处理、第二次抽真空处理、恒压处理以及镀膜处理;
9.其中,在进舟步骤之后且升温处理步骤之前,不进行充氮处理。
10.本技术实施例提供的镀膜工艺,有益效果包括:
11.在进舟后,直接进行升温处理然后进行抽真空,使得硅片和石墨舟能够较好地贴合,在后续的镀膜工艺中,能减少镀膜中高频出现的次数,从而能提高产能并降低产品不良率。
附图说明
12.为了更清楚地说明本技术实施例的技术方案,下面将对实施例中所需要使用的附图作简单地介绍,应当理解,以下附图仅示出了本技术的某些实施例,因此不应被看作是对范围的限定,对于本领域普通技术人员来讲,在不付出创造性劳动的前提下,还可以根据这些附图获得其他相关的附图。
13.图1为本技术一些实施例提供的镀膜工艺的工艺流程图;
14.图2为本技术对比例1提供的镀膜工艺的工艺流程图;
15.图3为试验例1中不同月份中不同镀膜工艺下每天出现高频的次数以及产品的不良比例的统计图。
具体实施方式
16.为使本技术实施例的目的、技术方案和优点更加清楚,下面将对本技术实施例中的技术方案进行清楚、完整地描述。实施例中未注明具体条件者,按照常规条件或制造商建议的条件进行。所用试剂或仪器未注明生产厂商者,均为可以通过市售购买获得的常规产品。
17.需要说明的是,在本技术的描述中,除非另有说明,“多个”、“多项”中的“多”的含义是指数量在2及2以上;“数值a~数值b”的范围包括两端值“a”和“b”,“数值a~数值b+计量单位”中的“计量单位”代表“数值a”和“数值b”二者的“计量单位”。
18.下面对本技术实施例的镀膜工艺进行具体说明。
19.发明人研究发现,在目前的镀膜工艺中,硅片在镀膜处理时易碎,而碎片的产生会导致高频,因此,需要停止镀膜处理并清理碎片,然后重新进行镀膜处理。
20.发明人还研究发现,在目前的镀膜工艺中,考虑到镀膜工艺需要在较高温度下进行射频放电,为了防止空气中氧气等对镀膜工艺造成影响,通常在进舟后,先进行抽真空处理,然后通入氮气进行气氛处理,然后在氮气气氛条件下进行升温处理,再进行后续的抽真空处理、检漏处理和镀膜处理等步骤。而在通入氮气的过程中,氮气会对硅片造成扰动,导致在升温处理后硅片不能很好地和石墨舟贴合,并最终导致在后续的镀膜工艺中硅片易碎。
21.基于上述考虑,发明人进一步地研究发现,在镀膜工艺中,镀膜腔本身就是高压且富氮的环境,在进舟后,即使不先进行抽真空处理和通入氮气,而是直接进行升温处理,对后续的硅片镀膜效果也基本没有影响。因此,提出一种镀膜工艺中,在进舟后,不先进行抽真空处理和通入氮气,而是直接进行升温处理,有效缓解硅片在镀膜工艺中易碎的现象,能减少镀膜中高频出现的次数,从而能提高产能并降低产品不良率。
22.本技术实施例提供一种镀膜工艺,包括:在进舟后,依次进行升温处理、第一次抽真空处理、检漏处理、第二次抽真空处理、恒压处理以及镀膜处理;其中,在进舟步骤之后且升温处理步骤之前,不进行充氮处理。
23.也就是说,在本技术的实施例中,在进舟后,不进行充氮处理,直接进行升温处理。
24.本技术提供的镀膜工艺,在进舟后,直接进行升温处理,能够避免因通入氮气对硅片造成扰动,使得在完成升温处理并进行第一次抽真空处理后,硅片和石墨舟能够较好地贴合。在后续的镀膜工艺中,由于硅片和石墨舟贴合较好,能够有效缓解硅片在镀膜工艺中易碎的现象,能减少镀膜中高频出现的次数,从而能提高产能并降低产品不良率。
25.发明人还研究发现,在目前的镀膜工艺中,升温过程是在通入了氮气的环境下进行的,而目前通入氮气的步骤中氮气的充入量通常只能达到充满状态的60~80%,也就是说,在通入氮气后氮气处理未充满的状态,使得镀膜腔内的空气分布不均匀,从而会导致升温处理过程中加热的均匀性受到影响。
26.本技术提供的镀膜工艺,在进舟后,直接进行升温处理。和通入氮气后进行升温处理的工艺相比,如果需要升温后达到相当的温度和温度均匀性,则本技术的升温处理的耗时更少;如果采用相当的升温时间,则本技术升温处理后能够达到更好的温度均匀性,有利于后续有更好的镀膜效果。也就是说,和通入氮气后进行升温处理的工艺相比,如果需要达到相当的镀膜效果,则本技术耗时更少,有利于进一步提高产能;如果需要保持相当的产
能,则本技术镀膜效果更好,有利于提高镀膜后产品的性能。
27.考虑到在升温处理步骤中,合适的升温处理条件有利于保证后续镀膜处理的效果,使得镀膜后的硅片的厚度和折射率的不均匀性保持在较低的水平。因此,以下内容对升温处理步骤中的升温处理条件作出了一些示例性的选择。其中,升温处理条件包括加热温度、加热时间和加热方式。
28.关于加热温度:
29.在一些示例的实施例中,在升温处理步骤中,加热温度为450~550℃,或为460~540℃,或为470~540℃,或为480~540℃,或为490~540℃。
30.在升温处理步骤中,按照上述标准控制加热温度,保证有合适的加热速度,并保证后续的镀膜处理工艺中有合适的处理温度。
31.关于加热时间:
32.在一些示例的实施例中,在升温处理步骤中,加热时间≥700s。
33.升温处理步骤中,随着加热时间的增加,温度会逐渐上升;当温度升高到一定后,温度将不再逐渐升高,而是逐渐变得更均匀。
34.加热时间过短,则会导致升温处理步骤达到的温度偏低或者温度均匀性较差。加热时间越长,越有利于达到合适的温度并使温度具有较好的均匀性。
35.在本技术的实施例中,按照上述加热温度标准进行加热,加热700s就能达到与通入氮气的工艺中加热800s相当的加热效果。加热时间控制为≥700s,保证镀膜效果的同时,可以根据需要选择不同的加热时间,以实现提高产能和/或提高镀膜效果的目的。
36.进一步地,在升温处理步骤中,加热时间为700~800s,例如但不限于为700s、710s、720s、730s、740s、750s、760s、770s、780s、790s和800s中的任意一者点值或者任意两者之间的范围值。
37.在升温处理步骤中,加热到一定程度使得温度达到较好的均匀性后,继续增加加热时间对温度均匀性的改善效果有限。
38.在本技术的实施例中,按照上述加热温度标准进行加热,控制加热时间的上限为800s,在有效提高镀膜效果的同时,保证有较高的加热效率,从而能更有效地提高产能。
39.关于加热方式:
40.在一些示例的实施例中,在升温处理步骤中,镀膜腔分为沿预设方向排列的多个温区,预设方向为镀膜气体的通入方向。沿预设方向,多个温区的加热温度逐渐降低。
41.镀膜工艺在镀膜腔中进行,在进舟步骤中,就是将放置有硅片的石墨舟放入镀膜腔内。因此,镀膜腔也是镀膜工艺中升温处理等其他处理步骤的工作场所。
42.上述设计中,将多个温区的加热温度沿镀膜气体的通入方向递减,能够有效平衡镀膜气体通入方向上等离子浓度差异对镀膜效果的影响,能有效保证镀膜后硅片的均匀性。
43.作为一种示例,在升温处理步骤中,多个温区分为沿预设方向依次排列的第一温区、第二温区、第三温区、第四温区和第五温区。
44.可选地,第一温区的加热温度为530~540℃,或为533~537℃,例如为535℃;第二温区的加热温度为520~530℃,或为523~527℃,例如为525℃;第三温区的加热温度为500~510℃,或为503~507℃,例如为505℃;第四温区的加热温度为495~505℃,498~502℃,
例如为500℃;第五温区的加热温度为490~500℃,或为493~497℃,例如为495℃。
45.需要说明的是,在本技术的镀膜工艺中,在完成镀膜处理步骤后,可以根据需要进行后续步骤。
46.在一些示例的实施例中,镀膜工艺还包括:在镀膜处理步骤之后,依次进行第三次抽真空处理、吹扫处理、第四次抽真空处理以及破真空处理,然后出舟。
47.考虑到进舟步骤和出舟步骤的处理条件会对镀膜腔内的高压富氮产生一定的影响,因此,以下内容对进舟步骤和出舟步骤的条件作出了一些示例性的选择。
48.在一些示例的实施例中,在进舟的步骤中,桨速为500~1000mm/min,例如但不限于为500mm/min、600mm/min、700mm/min、800mm/min、900mm/min或1000mm/min;处理时间为50~70s,例如但不限于为50s、60s或70s。
49.在一些示例的实施例中,在出舟的步骤中,桨速为500~1000mm/min,例如但不限于为500mm/min、600mm/min、700mm/min、800mm/min、900mm/min或1000mm/min;处理时间为50~70s,例如但不限于为50s、60s或70s。
50.需要说明的是,在本技术的镀膜工艺中,对于上述未提及的其他处理步骤,其处理条件可以根据需要或者参照本领域公知的标准进行选择。
51.作为示例,第一次抽真空处理的时间为280~320s,或为290~310s,例如为300s。检漏处理、第二次抽真空处理、恒压处理、第三次抽真空处理、吹扫处理和第四次抽真空处理的时间均为15~25s,或为18~22s,例如为20s。镀膜时间为500~1000s,例如但不限于为500s、600s、700s、750s、800s、900s或1000s。破真空处理的时间为80~120s,或为190s,例如为100s。
52.请参阅图1,在本技术的一些示例性的实施例中,镀膜工艺包括依次进行的进舟处理、升温处理、第一次抽真空处理、检漏处理、第二次抽真空处理、恒压处理、镀膜处理、第三次抽真空处理、吹扫处理、第四次抽真空处理、破真空处理以及出舟处理。
53.以下结合实施例对本技术的特征和性能作进一步的详细描述。
54.实施例1
55.一种镀膜工艺,如图1所示,包括依次进行:
56.进舟处理;其中,桨速为700mm/min,时间为60s。
57.升温处理;其中,镀膜腔分为沿预设方向排列的第一温区、第二温区、第三温区、第四温区和第五温区,第一温区的加热温度为535℃,第二温区的加热温度为525℃,第三温区的加热温度为505℃,第四温区的加热温度为500℃,第五温区的加热温度为495℃;加热时间为700s。
58.第一次抽真空处理;时间为20s。
59.检漏处理;时间为20s。
60.第二次抽真空处理;时间为20s。
61.恒压处理;时间为20s。
62.镀膜处理;时间为750s。
63.第三次抽真空处理;时间为20s。
64.吹扫处理;时间为20s。
65.第四次抽真空处理;时间为20s。
66.破真空处理;时间为100s。
67.出舟处理;其中,700mm/min,时间为60s。
68.实施例2
69.一种镀膜工艺,其与实施例1的不同之处在于:
70.升温处理步骤中,加热时间为800s。
71.对比例1
72.一种镀膜工艺,如图2所示,其与实施例2的不同之处在于:
73.在进舟处理之后且升温处理之前且,预先进行了一次抽真空处理,然后进行了充氮回压处理。
74.试验例1
75.在16个机台上,先后分别采用对比例1和实施例1的镀膜工艺进行镀膜生产。分别统计不同生产月份中,不同镀膜工艺每天出现高频的次数,以及产品的不良比例。
76.其中,各月份中每天出现高频的次数,取当月的平均数;各月份中产品的不良率,同样取当月的平均数。
77.不良比例=不良产品数量/产品总数量。不良产品按照如表1中的标准进行判断,不满足标准1~13中的任意一项或任意多项的产品均属于不良产品。
78.表1.镀膜产品标准
[0079][0080]
[0081]
不同月份中不同镀膜工艺下每天出现高频的次数以及产品的不良比例如图3所示。
[0082]
根据图3可知,采用本技术实施例提供的镀膜工艺进行镀膜生产,高频次数从16个机台一天高频100次降低为一天高频50次,不良比例从1.2%下降到0.8%。
[0083]
试验例2
[0084]
采用对比例1和实施例1的镀膜工艺进行镀膜生产。分别取多个镀膜后得到的产品,对产品的膜厚不均匀性及折射率不均匀性进行统计。
[0085]
其中,在每个产品中,分别取在四个角各取一个点进行膜厚和折射率的统计,依次标号为第1点、第2点、第3点和第4点,其结果如表2所示。根据表2获得的膜厚和折射率结果,计算不同工艺下膜厚不均匀性及折射率不均匀性,结果如表3所示。
[0086]
对于每个产品,膜厚及折射率均为4个点的平均值。
[0087]
以膜厚平均值最大的产品的膜厚为多个产品的膜厚最大值,以膜厚平均值最小的产品的膜厚为多个产品的膜厚最小值。以折射率平均值最大的产品的折射率为多个产品的折射率最大值,以折射率平均值最小的产品的折射率为多个产品的折射率最小值。
[0088]
对于多个产品的膜厚不均匀性和折射率不均匀性,按照以下公式计算得到。
[0089]
膜厚不均匀性=(膜厚最大值-膜厚最大值)/(膜厚最大值+膜厚最大值)。
[0090]
折射率不均匀性=(折射率最大值-折射率最大值)/(折射率最大值+折射率最大值)。
[0091]
表2.镀膜产品的膜厚(mm)和折射率
[0092][0093]
表3.镀膜产品的膜厚不均匀性和折射率不均匀性
[0094][0095][0096]
根据表2和表3可知,实施例1和对比例1相比,加热时间明显缩短,而镀膜产品的膜厚不均匀性和折射率不均匀性相当。也就是说,和对比例相比,在达到相当的镀膜效果的情况下,本技术实施例耗时更少,能提高产能。
[0097]
试验例3
[0098]
采用对比例1和实施例2的镀膜工艺进行镀膜生产。分别取多个镀膜后得到的产品,对产品的膜厚不均匀性及折射率不均匀性进行统计。
[0099]
其中,在每个产品中,分别取在四个角各取一个点进行膜厚和折射率的统计,依次标号为第1点、第2点、第3点和第4点,其结果如表4所示。根据表4获得的膜厚和折射率结果,计算不同工艺下膜厚不均匀性及折射率不均匀性,结果如表5所示。
[0100]
表4和表5中相关参数的统计和计算方法,参见试验例2。
[0101]
需要说明的是,由于不同试验例之间为平行试验。因此,相同的工艺在不同试验例中的试验结果略有差异,其是可以被理解的。
[0102]
表4.镀膜产品的膜厚(mm)和折射率
[0103][0104][0105]
表5.镀膜产品的膜厚不均匀性和折射率不均匀性
[0106][0107]
根据表4和表5可知,实施例2和对比例1相比,加热时间相同,而镀膜产品的膜厚不均匀性和折射率不均匀性明显改善。也就是说,和对比例相比,在保持相当的产能的情况下,本技术实施例镀膜效果更好,能提高镀膜后产品的性能。
[0108]
以上所描述的实施例是本技术一部分实施例,而不是全部的实施例。本技术的实施例的详细描述并非旨在限制要求保护的本技术的范围,而是仅仅表示本技术的选定实施例。基于本技术中的实施例,本领域普通技术人员在没有作出创造性劳动前提下所获得的所有其他实施例,都属于本技术保护的范围。