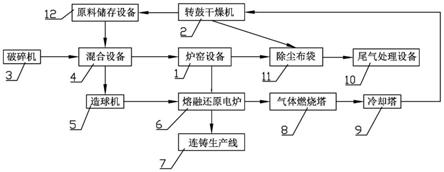
1.本发明属于不锈钢冶炼固废回收技术领域,具体涉及一种不锈钢冶炼固废回收利用方法。
背景技术:2.炼钢(steelmaking)指把炼钢用生铁放到炼钢炉内按一定工艺熔炼,调整钢、铁生产中熔渣成分,炼出钢材。炼钢需要控制碳含量(一般小于2%),消除p、s、o、n等有害元素,保留或增加si、mn、ni、cr等有益元素并调整元素之间的比例,获得最佳性能。通常所讲的钢,一般是指轧制成各种钢材的钢,钢属于黑色金属但钢不完全等于黑色金属,钢的产品有钢锭、连铸坯和直接铸成各种钢铸件等。
3.炼钢中会产生炼钢粉尘,转炉灰,冶炼污泥,氧化铁皮等大量固废,其中有部分固废有较高的回收再利用价值,然而现有技术中没有一种能很好的对固废进行回收的方法。
技术实现要素:4.针对上述背景技术所提出的问题,本发明的目的是:旨在提供一种不锈钢冶炼固废回收利用方法。
5.为实现上述技术目的,本发明采用的技术方案如下:
6.一种不锈钢冶炼固废回收利用方法,包括如下步骤:
7.s1、工作设备准备:准备炉窑设备、转鼓干燥机、破碎机、混合设备、造球机、熔融还原电炉、连铸生产线、气体燃烧塔、冷却塔和尾气处理设备;
8.s2、工作设备连接:所述转鼓干燥机的固体物料输出端与所述混合设备的输入端连接,所述混合设备输入端与所述破碎机输出端连接,所述混合设备混合不达标的固体物料输出端与所述炉窑设备连接,所述混合设备混合达标的固体物料输出端与所述造球机输入端连接,所述造球机和所述炉窑设备的固体物料输出端均与所述熔融还原电炉输入端连接,所述熔融还原电炉固体物料输出端与所述连铸生产线输入端连接,所述熔融还原电炉气体物料输出端与所述气体燃烧塔输入端连接,所述气体燃烧塔输出端与所述冷却塔输入端连接,所述冷却塔气体物料输出端与所述转鼓干燥机气体输入端连接,所述转鼓干燥机和炉窑设备的气体物料输出端均与所述尾气处理设备连接;
9.s3、试运行:将污泥等固废料投入所述转鼓干燥机,将干粉固废料投入所述混合设备,将氧化铁皮投入所述破碎机,启动全部设备,等待结果;
10.s4、批量生产。
11.进一步限定,上述步骤s1中,所述炉窑设备包括干燥区、预热区、初期反应区、主反应区和降温区,这样的设计,充分反应。
12.进一步限定,所述干燥区、预热区、初期反应区、主反应区和降温区的长度占比分别为所述干燥区占15%、所述预热区占10%、所述初期反应区占25%、所述主反应区占40%和所述降温区占10%,这样的设计,保证每个区的停留时间。
13.进一步限定,所述干燥区、预热区、初期反应区、主反应区和降温区的温度范围分别为所述干燥区为25~550℃、所述预热区为550~620℃、所述初期反应区1为620~1050℃、所述主反应区为1050~1250℃和所述降温区为1050~800℃,这样的设计,保证反应强度。
14.进一步限定,所述干燥区的筒体直径为2.5~3m,所述预热区的筒体直径为3~3.2m,所述初期反应区的筒体直径为3.2~4m,所述主反应区的筒体直径为4~5.5m,所述降温区的筒体直径为5.5~3m,这样的设计,阶层结构,流动效果好。
15.进一步限定,所述炉窑设备的倾斜度为2%,转速为0.4~1rpm,内部压力为-0.2~0.5mbar,这样的设计,保证流动和反应效率。
16.进一步限定,批量生产时,物料在所述炉窑设备中的总停留时间为4~10小时,这样的设计,实验证明当温度在800~900度以上时,且反应时间达到4小时以上,混合物料中的锌还原率才能达到99%以上水平。
17.进一步限定,所述转鼓干燥机和炉窑设备与所述尾气处理设备之间均连接有除尘布袋,这样的设计,可以达到回收粗氧化锌的目的。
18.进一步限定,所述转鼓干燥机与所述混合设备之间设有原料储存设备,这样的设计,防止物料堆积。
19.进一步限定,所述主反应区内部温度先升后降,这样的设计,效率更高。
20.采用本发明的有益效果:
21.本发明使用炉窑设备从混合原料投入到最后流出,分为干燥、预热、初期反应、主反应、降温五个工作阶段,物料逐渐向前滑动,最终在窑尾流出,而被加热后尾料从炉窑中流出的温度约800度,将直接流入熔融还原电炉,在该电炉中继续加热,最终得到含fe-cr-ni的合金铸锭,达到回收利用的目的。
附图说明
22.本发明可以通过附图给出的非限定性实施例进一步说明;
23.图1为本发明一种不锈钢冶炼固废回收利用方法实施例的流程示意框图;
24.图2为本发明一种不锈钢冶炼固废回收利用方法实施例的炉窑设备结构示意图;
25.主要元件符号说明如下:
26.炉窑设备1、干燥区101、预热区102、初期反应区103、主反应区104、降温区105、转鼓干燥机2、破碎机3、混合设备4、造球机5、熔融还原电炉6、连铸生产线7、气体燃烧塔8、冷却塔9、尾气处理设备10、除尘布袋11、原料储存设备12。
具体实施方式
27.为了使本领域的技术人员可以更好地理解本发明,下面结合附图和实施例对本发明技术方案进一步说明。
28.如图1、图2所示,本发明的一种不锈钢冶炼固废回收利用方法,包括如下步骤:
29.s1、工作设备准备:准备炉窑设备1、转鼓干燥机2、破碎机3、混合设备4、造球机5、熔融还原电炉6、连铸生产线7、气体燃烧塔8、冷却塔9和尾气处理设备10;
30.s2、工作设备连接:转鼓干燥机2的固体物料输出端与混合设备4的输入端连接,混
合设备4输入端与破碎机3输出端连接,混合设备4混合不达标的固体物料输出端与炉窑设备1连接,混合设备4混合达标的固体物料输出端与造球机5输入端连接,造球机5和炉窑设备1的固体物料输出端均与熔融还原电炉6输入端连接,熔融还原电炉6固体物料输出端与连铸生产线7输入端连接,熔融还原电炉6气体物料输出端与气体燃烧塔8输入端连接,气体燃烧塔8输出端与冷却塔9输入端连接,冷却塔9气体物料输出端与转鼓干燥机2气体输入端连接,转鼓干燥机2和炉窑设备1的气体物料输出端均与尾气处理设备10连接;
31.s3、试运行:将污泥等固废料投入转鼓干燥机2,将干粉固废料投入混合设备4,将氧化铁皮投入破碎机3,启动全部设备,等待结果;
32.s4、批量生产。
33.本实施案例中,在使用一种不锈钢冶炼固废回收利用方法的时候,向将各设备购置并连接安装,将污泥等固废料投入转鼓干燥机2,将氧化铁皮等材料投入破碎机3,将干粉固废料投入混合设备4,污泥等固废料经转鼓干燥机2加工后进入混合设备4与干粉固废料一并搅拌混合,期间,由破碎机3破碎的物料也进入混合设备4中,混合设备4混合筛选不达标的物料进入炉窑设备1中进行反应,混合筛选达标的物料进入造球机5中进行加工,然后投入熔融还原电炉6中与由炉窑设备1反应完毕的物料一并熔铸,熔铸产生的物料经连铸生产线7加工成铸锭,实现回收利用的目的;熔铸产生的气体经气体燃烧塔8进行处理后,再由冷却塔9处理,由冷却塔9处理的气体作为转鼓干燥机2的气体供应,炉窑设备1和转鼓干燥机2产生的废气经尾气处理设备10处理后安全排放。
34.优选上述步骤s1中,炉窑设备1包括干燥区101、预热区102、初期反应区103、主反应区104和降温区105,这样的设计,充分反应,实际上,也可根据具体情况考虑炉窑设备1的结构。
35.优选干燥区101、预热区102、初期反应区103、主反应区104和降温区105的长度占比分别为干燥区101占15%、预热区102占10%、初期反应区103占25%、主反应区104占40%和降温区105占10%,这样的设计,保证每个区的停留时间,实际上,也可根据具体情况考虑分区占比。
36.优选干燥区101、预热区102、初期反应区103、主反应区104和降温区105的温度范围分别为干燥区101为25~550℃、预热区102为550~620℃、初期反应区103为620~1050℃、主反应区104为1050~1250℃和降温区105为1050~800℃,这样的设计,保证反应强度,实际上,也可根据具体情况考虑温度范围。
37.优选干燥区101的筒体直径为2.5~3m,预热区102的筒体直径为3~3.2m,初期反应区103的筒体直径为3.2~4m,主反应区104的筒体直径为4~5.5m,降温区105的筒体直径为5.5~3m,这样的设计,阶层结构,流动效果好,实际上,也可根据具体情况考虑各区筒体直径。
38.优选炉窑设备1的倾斜度为2%,转速为0.4~1rpm,内部压力为-0.2~0.5mbar,这样的设计,保证流动和反应效率,实际上,也可根据具体情况考虑炉窑设备1的转速和内部压力。
39.优选批量生产时,物料在炉窑设备1中的总停留时间为4~10小时,这样的设计,实验证明当温度在800~900度以上时,且反应时间达到4小时以上,混合物料中的锌还原率才能达到99%以上水平,实际上,也可根据具体情况考虑料在炉窑设备1中的停留时间。
40.优选转鼓干燥机2和炉窑设备1与尾气处理设备10之间均连接有除尘布袋11,这样的设计,可以达到回收粗氧化锌的目的,实际上,也可根据具体情况考虑回收粗氧化锌的方法。
41.优选转鼓干燥机2与混合设备4之间设有原料储存设备12,这样的设计,防止物料堆积,实际上,也可根据具体情况考虑物料储存方法。
42.优选主反应区104内部温度先升后降,这样的设计,效率更高,实际上,也可根据具体情况考虑提升效率的方法。
43.上述实施例仅示例性说明本发明的原理及其功效,而非用于限制本发明。任何熟悉此技术的人士皆可在不违背本发明的精神及范畴下,对上述实施例进行修饰或改变。因此,凡所属技术领域中具有通常知识者在未脱离本发明所揭示的精神与技术思想下所完成的一切等效修饰或改变,仍应由本发明的权利要求所涵盖。