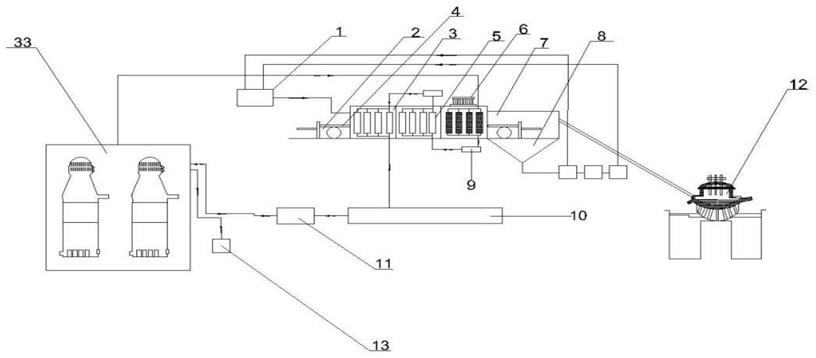
1.本发明属于钢铁冶金直接还原炼铁技术领域,具体涉及一种强化传质传热的蜂窝状导流料块制备及直接还原炼铁方法。
背景技术:2.高炉炼铁工艺是现代钢铁工业的基石,在整个钢铁工业中起着举足轻重的作用。高炉炼铁的主要流程包括焦化、造块(烧结和球团)、高炉冶炼等,然而这些工序无一例外都对资源有着较强的依赖,对环境有着较大的污染。高炉炼铁对入炉原燃料的要求比较苛刻,需要使用高品位同时具有一定粒级的铁矿石,对于一些贫矿或粉矿则需要经过选矿和造块工艺的进一步处理,这个过程中又会加大对冶金焦的需求,但是由于高质量焦煤的储量有限,大大增加了高炉炼铁的成本。此外,在选矿、造块、炼焦、高炉炼铁的过程中会产生大量对环境有害的的物质。在以焦化—烧结—高炉—转炉为主的长流程生产中,接近60%的能耗、70%的吨钢成本、90%污染物排放集中在焦化、烧结和高炉炼铁过程。目前,我国大高炉平均焦比可达450kg/t,冶炼每吨生铁大约需要1.6吨矿石,而在我国炉料结构中烧结矿占比大约在75%,以2020年我国生铁产能9亿吨计算,就有11亿吨的矿粉需要烧结成块,整个高炉炼铁流程每年会产生烟气粉尘约128万吨,产生so2气体约205万吨,产生氮氧化物约77万吨。这些种种都表明高炉炼铁并非是一个长久之策。同时,为了响应国家“碳达峰、碳中和”的号召,迫切需要开发出一种不依赖焦煤和高品位铁矿石同时又经济环保的非高炉炼铁方法。
3.非高炉炼铁工艺以非焦煤为主要能源,不需要进行选矿和造块等工序,对于原燃料的要求和适应性都好于传统的高炉炼铁工艺,因而大大缩短了生产流程,具备可控性强、成本低、污染小、排放低的特点。根据使用还原剂的不同,直接还原工艺又分为气基直接还原和煤基直接还原,气基直接还原法中广泛应用的以天然气、氢气或一氧化碳为主的还原气体同样存在资源供给方面的压力。而我国又是一个煤炭储量大国,拥有丰富的煤炭资源。因此,发展煤基直接还原工艺将是我国未来发展非高炉炼铁技术的重中之重。
4.煤基隧道窑生产直接还原铁工艺又称赫格纳斯煤基隧道窑直接还原法,引进于瑞典的赫格纳斯公司,在我国隧道窑工艺最初广泛应用于粉末冶金领域,并在该行业占据主导地位。近年来,随着煤基直接还原工艺的发展,我国开始将该工艺应用于炼钢直接还原铁领域并取得了重大进展,这对于缓解我国炼钢用优质废钢的供给矛盾有着重要意义。在原料准备阶段,目前主流的做法包括两种,一是将铁矿粉直接装入容器,二是将原料压制成球团或其他形状。专利cn 110195139b中提到的一种铁矿石低温还原—常温渣铁分离—电炉制钢工艺中将粒状的球团矿、铁矿石和残炭作为还原反应的原料装入回转窑;专利cn 104195276 a中提到的铁矿粉内配碳多孔块直接还原工艺当中将铁矿石、还原剂等原料混合制成料块。对于前者而言,虽说省去了成型过程,但是由于物料特性的关系,反应过程的传质传热是很大的限制性因素。同时,因为传质传热的不均匀也容易造成物料局部和高温
炉气接触时间过长而出现局部软熔结块的现象。另外,粉状料处理过程繁琐且不易实现连续化规模化生产。而对于后者,也常常因料块密实程度、供热方式、供热均匀程度等因素而影响到最终产品的质量。
5.无论是哪一种对于原料的处理方法,其表面的受热速度都远大于物料内部热传导的速度,这必然会出现物料表面已经初熔而内部尚未到达反应所需温度的情况,这对反应速度、还原率、还原产物的金属化率都有不好的影响。在这种条件下,只能通过延长高温还原反应的时间来维持产品的质量,随之而来的就是更加高昂的成本。因此,如何在直接还原过程中改善物料的传质传热条件,增加传质传热速度、反应界面、产物金属化率、整体还原效率就成了当务之急。在此基础上,现有技术人员提出将物料处理成带有孔洞的料块,现有技术中提到了一种具有气体通道的用于热风炉的格子砖,但是对于料块具体的开孔特征和料块表面的细节处理却鲜有提及。此外还有一个亟待解决的问题就是还原工艺的选择问题,气基直接还原工艺作为目前比较成熟的非高炉炼铁工艺而受到广泛应用,但其始终受资源的制约。而传统的煤基直接还原工艺又局限于小规模生产且部分生产工艺还不完善。
技术实现要素:6.因此,为了解决以上问题,本发明一方面结合热风炉格子砖的设计理念以及速度场、温度场、浓度场三场协同理论,发明设计了一种在具有导流效果的同时还可以最大程度强化传质传热的蜂窝状物料块。另一方面在传统煤基直接还原方法的基础上结合烧结台车和带式焙烧机的工作原理提出了一种强化传质传热的蜂窝状导流料块制备及直接还原炼铁方法。由此,本发明针对并克服了现有技术中存在的不足,旨在解决的技术问题是直接还原炼铁过程中出现的物料与还原物质反应动力学条件差、传质传热不充分、反应时间长、还原效率低、金属化率低等问题。所提供的强化传质传热化学反应的蜂窝状导流料块制备及直接还原炼铁工艺,显著提高了铁矿石直接还原过程中物料与高温还原气反应的动力学条件,同时大幅提高了还原产物的金属化率、缩短了还原时间。
7.为解决上述技术问题,本发明提供的技术方案如下:
8.根据本发明技术方案,提供一种强化传质传热的蜂窝状导流料块制备及直接还原炼铁方法,其特征在于,所述方法包括以下步骤:
9.步骤1,将含铁物料、炭质还原剂、复合粘结剂、水均匀混合形成混合物料;
10.步骤2,将混合物料经充分混捏、压块后得到蜂窝状导流料块;
11.步骤3,将所述蜂窝状导流料块送入台车式焙烧还原装置之中进行处理,得到初始还原炉料;
12.步骤4,将第一部分初始还原炉料直接热装送往电弧炉熔分作为电弧炉炼钢的原料,第二部分初始还原炉料进行磁选,得到金属化炉料和以残炭为主的其他杂质,将所得到的金属化炉料进一步破碎筛分再经磁选得到高纯铁粉和尾矿。
13.这里,所述第一部分与第二部分的比例视个体情况而定,如只有第一个方面的需求,则可以将所有初始还原炉料用于“第一部分”,以此类推。
14.进一步地,所述步骤1中,含铁物料、炭质还原剂、复合粘结剂、水的配比以重量比计算,质量比为:100:15~20:2~4:12~18。
15.进一步地,所述步骤1中,所述含铁物料包括且不限于铁矿石(磁铁矿、赤铁矿、褐
铁矿、钒钛磁铁矿、钛铁矿、高硅铁精矿、共生矿等)、难选低品位细粒铁矿石、高炉布袋灰、转炉铁鳞粉、烧结除尘灰等。
16.进一步地,所述步骤1中,所述炭质还原剂的选择包括兰炭、低煤阶煤粉、炭粉、含碳粉尘、冶金焦粉之中的一种或多种。
17.进一步地,所述步骤1中,所述复合粘结剂的选择包括无机粘结剂(膨润土、消石灰、水玻璃)和有机粘结剂(羧甲基纤维素钠、木质素磺酸钙)。
18.进一步地,所述步骤1中,混合物料时为了提高成品料块的成块性能和还原效率,至少要保证50%的含铁物料过200目筛,同时要有55%的炭质还原剂过100目筛。
19.进一步地,所述步骤2中,所述蜂窝状导流料块上开设有数个椭圆形通孔,所述椭圆形通孔贯穿于蜂窝状导流料块的正反两个端面,同时在所述蜂窝状导流料块的至少一个端面上开设数条用于气体导流的半圆形导流凹槽和用于气流交换汇集的圆形汇流凹槽。
20.进一步地,根据椭圆形通孔孔径大小不同,所述蜂窝状导流料块包括大孔径尺寸料块和小孔径尺寸料块。
21.进一步地,布料时,大孔径尺寸料块和小孔径尺寸料块的铺设方式如下:
22.第一层:将大孔径尺寸料块或小孔径尺寸料块中的任意一种铺在最底层;
23.第二层:将另一种型号的料块以其椭圆形通孔长轴方向与下层料块通孔长轴平行的方式铺于其上,至此利用此种铺设方法可以起到与缩放管相同的效果,使得气流在流经由这两层料块组成的通道时产生垂直于主流方向的径向流;
24.第三层:第三层铺设与第二层孔径尺寸相同的料块,且第三层料块以其通孔的长轴与第二层料块通孔长轴垂直的方式铺设,至此利用此种铺设方法可以起到与局部压扁管、交叉椭圆管相同的效果,使得气流在流经由这两层料块组成的通道时产生垂直于主流方向的涡旋二次流;
25.第四层:第四层铺设与第三层孔径尺寸不同的料块,且第四层料块以其通孔的长轴与第三层料块通孔长轴平行的方式铺设,使得气体在流经由这两层料块组成的通道时同样产生径向流;
26.以上四层料块的铺设为一个循环,一直铺设下去直至料层高度到达800mm~1000mm。
27.进一步地,所述蜂窝状导流料块的形状包括但不限于圆柱体、长方体、正方体、正多棱柱。
28.进一步地,所述蜂窝状导流料块具有4条半圆形导流凹槽,所述4条半圆形导流凹槽的一端分别贯穿至料块侧壁的中点处,另一端汇集于以料块端面面心为圆心的圆形汇流凹槽。
29.进一步地,所述蜂窝状导流料块的正反两个端面都开设有所述的半圆形导流凹槽且所述半圆形导流凹槽和圆形汇流凹槽具有相同的深度。
30.进一步地,所述蜂窝状导流料块每个侧壁上开设数个贯穿上下两个端面的半圆形固定凹槽,以达到稳定料层和方便铺设的目的。
31.进一步地,所述蜂窝状导流料块表面共开设有21个椭圆形通孔。
32.进一步地,所述椭圆形通孔所形成的通道内表面刻有螺旋槽。
33.进一步地,所述步骤3具体包括:将所述蜂窝状导流料块铺设在台车上送入台车式
焙烧还原装置之中,在焙烧炉内的干燥段和预热段,料块受到高温还原段反应过后产生的高温烟气的作用开始缓缓升温,经过干燥预热后的料块在高温还原段进行高温还原焙烧,出炉得到初始还原炉料。
34.进一步地,所述步骤3中,所述台车式焙烧还原装置包括:台车式焙烧机、顶燃式热风炉、电弧炉以及除尘设备。
35.进一步地,所述台车式焙烧机包括有台车,所述台车上安装有密封的烟罩,烟罩内为传送装置。
36.进一步地,所述台车包括干燥段、预热段和高温还原段。
37.进一步地,所述干燥段与预热段之间以及所述预热段和高温还原段之间均设置有风箱。
38.进一步地,所述台车的高温还原段中,烟罩正上方安装有平行排列的两组燃烧室。
39.进一步地,所述燃烧室上设置有二次进气管。
40.进一步地,所述燃烧室内的两个侧腔内分别设有方向相反的挡墙,且每个侧腔侧壁都安装有插入在喷嘴砖中的扰流喷嘴。
41.进一步地,所述扰流喷嘴作为一个整体其主体组成包括煤粉喷吹管、与煤粉喷吹管同轴设置的燃烧器、一次进气管、富氧管和扰流器。
42.进一步地,使用一部分生物质燃料取代部分煤粉,连同煤粉一同由煤粉喷吹管喷入。
43.进一步地,所述生物质燃料包括但不限于:玉米、水稻、高粱秸秆在内的农业废弃物;包括树木在内的木质生物(林业废弃物);甘蔗渣、油料渣滓、果壳等(加工废弃物);银杏叶(涉及所有落叶乔木中银杏科)。本发明优选高粱秸秆和银杏叶,其质量比为:7:3,热量置换比为75%,以此生物质燃料代替15%的煤粉。
44.进一步地,为提高所述生物质燃料的固定碳含量,在氮气条件下以不同的加热速率将生物质原料分阶段加热到不同的温度,之后自然冷却到室温,通过该预处理过程增大了生物质燃料的比表面积、反应活性以及固定碳含量。
45.进一步地,所述煤粉喷吹管包括管径较小的进口管段和远离所述进口管段的扩口管段,在扩口管段内设置有与其同轴向分布的分流管,分流管与燃烧器之间形成内风道,分流管与扩口管段之间形成环流通道,在内风道的尾部分别设置有旋流角度略有不同的扰流器;煤粉喷吹管的扩口管段与扰流喷嘴所插入的喷嘴砖的内壁之间形成外风道,所述外风道与一次进气管、富氧管相连通。
46.进一步地,由扰流喷嘴喷出的高温还原气首先进入燃烧室侧腔,在侧腔内进一步反应并在挡墙的作用下实现均压均流,最后两侧侧腔内的还原气一同进入到燃烧室主腔内,在抽风机的作用下穿过堆叠的料层,完成高温还原的过程,高温还原段反应之后的高温烟气经过烟气循环系统先后通过预热段和干燥段完成对料块的预热和干燥,最后在风机的作用下通过除尘设备脱尘,脱尘后与空气风机鼓入的空气一同吹入顶燃式热风炉,产生的热风由一次进气管进入扰流喷嘴。
47.进一步地,所述燃烧室通过密封装置与储料仓连通。
48.进一步地,所述密封装置与电弧炉连通。
49.进一步地,所述台车式焙烧机在箅条之上摆放有布满圆形通孔的正六边形炉箅,
并且沿着干燥段、预热段、高温还原段的方向,正六边形炉箅的大小依次变小,这样一来使得沿干燥段、预热段、高温还原段被抽下的高温烟气速度逐渐增加,并使得干燥段和预热段的料块预反应更加完全。
50.进一步地,所述步骤3中,所述顶燃式热风炉与燃烧室连通,且与空气风机连通。
51.进一步地,所述除尘设备一端与所述台车的干燥段连通,另一端通过抽风机与顶燃式热风炉连通。
52.进一步地,所述步骤4中,第一部分初始还原产物直接热装送入电弧炉熔分作为电炉炼钢的原料,第二部分经一次磁选得到含有残炭的残渣返回到混料阶段重复利用,经一次磁选得到的金属化物料再经破碎筛分后进行二次磁选,得到的尾矿返回至混料阶段重复利用,得到的金属化物料经磨矿后使其粒度90%以上达到200目,得到最终产品高纯铁粉,得到的高纯铁粉可直接用于转炉。
53.本发明的有益效果在于:
54.1、本发明方法涉及的强化传质传热的蜂窝状导流料块通过开设一定数量的椭圆形通孔和各类流槽同时利用三场协同理论,显著提升了料块内外部的传质传热效率及传热均匀性,相比于传统多孔块具有更大的比表面积,可以开设更多通孔而无需担心所开通孔过多而导致气路不通畅。同时得益于料块所具备的强化传质传热能力,在堆料时可以堆至800~1000mm,在某种程度上抵消了由开孔多而导致的单个料块单位体积装料量少的问题。可以实现大规模高效还原。
55.2、本发明方法提出的台车式焙烧还原装置通过对燃烧室结构和喷嘴结构的合理配置,促进了燃烧反应的充分进行,提高了燃烧效率和料块表面气流温度和压力的均匀性,避免料块局部出现过烧、轻烧现象,大幅提高产物的质量。
56.3、本发明方法简单易行,所需设备简单、投资小、生产规模大、对原燃料的要求小、污染小、排放低、易于推广。
附图说明
57.为了更清楚地说明本发明专利实施例或现有技术中的技术方案,下面将对实施例或现有技术描述中所需要使用的附图作简单地介绍。
58.图1为本发明主体结构示意图。
59.图2为台车式焙烧还原装置中燃烧室的分布示意图。
60.图3为燃烧室主体结构示意图。
61.图4为台车式焙烧还原装置用扰流喷嘴结构示意图。
62.图5为本发明工艺提出的强化传质传热的蜂窝状导流料块的俯视图。
63.图6为本发明工艺提出的强化传质传热的蜂窝状导流料块的剖视图。
64.图7为按特定方式堆叠后料块之间形成的气体通路示意图。
65.图8为台车式焙烧机主体结构示意图。
66.附图标记说明:图中:1、进料仓;2、台车;3、烟罩;4、传送装置;5、燃烧室;6、二次进气管;7、台车料面密封装置;8、储料仓;9、风箱;10、除尘设备;11、抽风机;12、电弧炉;13、空气风机;14、扰流喷嘴;15、二次进气口旋流器;16、挡墙;17、燃烧器;18、煤粉喷吹管;19、一次进气管;20、富氧管;21、内风道;22、环流通道;23、扰流器;24、外风道;25、料块本体;26、
椭圆形通孔;27、半圆形凹槽;28、导流凹槽;29、汇流凹槽;30、螺旋槽;31喷嘴砖;32、分流管;33、顶燃式热风炉;34、炉箅。
具体实施方式
67.下面结合附图对本发明进行进一步的说明。
68.本发明提供的一种强化传质传热的蜂窝状导流料块制备及直接还原炼铁工艺是属于用于铁矿粉直接还原的原料和装置的组成部分,下面通过结合附图整体介绍用于铁矿粉直接还原的原料和装置,来说明本发明中用于铁矿粉直接还原的原料和装置的特点。
69.本发明涉及到一种强化传质传热的蜂窝状导流料块制备及直接还原炼铁工艺。基于速度场、温度场、浓度场的三场协同理论,将含铁物料、炭质还原剂、复合粘结剂等原料按一定的重量配比后均匀混合混捏并压制成特殊的蜂窝状导流式物料块,料块设有椭圆形通孔和用于气体导流汇集的凹槽,对比传统料块具有更大的比表面积且通孔内部刻有的螺旋槽可以起到扰流强化的作用,同时通过独特的铺设方法促进通孔内二次流的产生进而强化传热。所得料块经干燥后送入本发明专利发明的一种台车式焙烧还原装置内作为直接还原炼铁的原料进行冶炼。本发明通过将物料造型成特殊的物料块并辅以特殊的还原装置,大幅提高了还原生产效率、最终产品的含铁品位和金属化率,降低了能耗和排放。另外,本发明工艺简单、设备投资小、流程短、污染小,在具备批量生产能力的同时兼顾资源的回收利用,契合国家提倡的“碳达峰、碳中和”战略目标,是很有应用前景的短流程非高炉炼铁技术,具有代替传统长流程高炉炼铁工艺的潜力。
70.如图1所示,该强化传质传热化学反应的蜂窝状导流料块制备及直接还原炼铁工艺,包括物料混合、压制造块、干燥、还原等步骤。其中:
71.所述物料的混合步骤为:将含铁物料、炭质还原剂、复合粘结剂、水等原料均匀混合,其所对应的质量比为100:15~20:2~4:12~18。含铁物料的质量以其中全铁的质量计算。
72.所述的压制成型步骤为:将配比混匀之后的物料装入预先设计好的模具中,使用压机压制加工成预设的形状,并使料块的密度保持在2.4g/cm2~2.8g/cm2之间。这样一来粉料经压制成型后密度变大,反应过程中料块内生成的还原性气体不易散逸,有利于还原反应的彻底进行。
73.将混合后的物料压制成块,所得压块上开设有21个长轴为20mm~30mm,短轴为13mm~20mm的椭圆形通孔,椭圆形通孔沿所述料块的轴向设置并贯穿料块上下两个端面,两个端面都开设有四个用于气体流通的半圆形导流凹槽和一个用于气体交流汇集的圆形汇流凹槽,所述导流凹槽的一端位于料块侧壁中点处另一端汇集于以料块端面面心为圆心的汇流凹槽。导流凹槽的宽度为20mm~30mm与椭圆形通孔的长轴一致,汇流凹槽的半径为10mm~25mm,且导流凹槽和汇流凹槽拥有相同的深度为2mm~20mm。料块的厚度在80mm~100mm之间。所述料块的形状包括但不限于圆柱体、长方体、正方体、正多棱柱,此处优选为长方体。另外,在所述椭圆形通孔的内部刻有螺旋槽。
74.与现有原料处理技术相比,本发明提出的强化传质传热的蜂窝状导流料块通过在料块上开设通孔使得料块具有很大的比表面积,增加了还原物质与物料的接触面积,显著地提升了多孔块内外部的传质传热效率,并且通过在端面上开设汇流凹槽和多条导流凹槽
并将汇流凹槽和导流凹槽相互连通,加速了单块料块端面处气流的物质交换和热交换速率,提高了料堆整体的均压均流效果。另外,根据对流换热场协同理论可知,通过不同程度的改善速度场、温度场、浓度场的协同程度可以取得换热强化的效果。如果将堆叠后料块的通孔看作是管道型换热器,鉴于流体流动总是产生在温度梯度较大的方向且管道内径向温度梯度远大于轴向温度梯度,也即管内温度梯度主要集中在径向。对于层流来说,管内径向产生较小的速度即可对换热产生显著的影响,由旋转或缩放等途径产生的二次流可明显强化管内的层流换热,而对于管内的湍流换热,场强化也同样适用,只不过与层流不同的是其温度梯度主要发生在壁面附近的径向。因此,可以同时采用壁面突起扰流强化、扩展表面强化和场协同强化来最大限度的强化传质和换热。本发明通过交叉堆叠具有不同椭圆形通孔孔径的料块并在通孔内刻螺旋槽,在管内同时产生旋转流、径向流和涡流,使流体在温度梯度较大的径向产生强烈的混合,促使主流区的流体温度均匀化和壁面处温度梯度增大,从而实现较大程度的传质和传热强化。并且交叉排布的椭圆通孔轴向截面积变化较小,因而在强化换热的同时其流阻较传统圆形通孔增加较少。同时,引入的导流槽也在一定程度上抵消了因强化传热而带来的阻力增加。
75.所述物料的干燥和还原步骤为:将料块装入到本发明提供的一种台车式焙烧炉中,其主体包括具有轨道的台车、台车上密封的烟罩和布置在高温还原段正上方的燃烧系统。将料块在台车上堆叠至800~1000mm后按预设的速度沿轨道向前移动,直至移动到高温还原段,大量由扰流喷嘴喷入燃烧室的高温烟气混携着由第二进气口进入的重整后的焦炉煤气,一同涌进烟罩内并在抽风机的作用下贯穿整个料层,伴随着台车的移动逐步完成对料块的还原过程,还原后的料块由台车尾部排出进入具有微正压还原气氛的储料仓。
76.进一步地,使用烟罩将整个炉膛分为相对独立的两个部分,可以避免料块第一时间受到直接加热,通过阀门控制充分反应后的还原烟气由燃烧室进入装有料块的反应室,在连续的反应过程中,燃烧室的热能与反应室的热能接近平衡再加上料块本身具有的通孔和流槽,使得料块各个位置的加热程度十分接近,料块内外温差可以控制在一个合理的范围。
77.进一步地,在燃烧室两侧的侧腔内分别设置有朝向相反的挡墙,避免了侧腔吹入燃烧室主腔的高温还原气正面冲击,规避了可能由此引发的燃烧室烟气排出不畅、燃烧效率低、烟罩内形成局部高、低温区以及料块局部过烧、轻烧等现象。
78.进一步地,扰流喷嘴内设置的扰流器可以加强气体之间的混合并形成旋转流,在高温还原烟气喷出的同时不断卷吸使得一小部分还原烟气得以回流,可以很大程度解决,在反应初期因燃气喷离喷嘴速度与燃料燃烧速度不匹配而造成的脱火、回火问题,提高了反应过程的安全性和稳定性。
79.如图5所示,本发明工艺提出的强化传质传热的蜂窝状导流料块,将料块的形状优选为长方体,在料块本体25上开设有21个长轴为20mm~30mm,短轴为13mm~20mm的椭圆形通孔26,并根据所开通孔孔径的不同将料块分为a、b两个型号。在料块本体25的四个侧面上的1/4、3/4位置处分别开设两个半圆形凹槽27,半圆形凹槽27的直径选取与椭圆形通孔长轴一致。当多块料块沿椭圆形通孔26的轴向层叠码放时,相邻料块的半圆形凹槽即可拼接成一个完整的圆形气流通道,进一步增加了料层整体的通孔率和传质传热效率。同时料块上还开设有导流凹槽28和汇流凹槽29,导流凹槽28的宽度为20mm~30mm与椭圆形通孔的长
轴一致,深度为2mm~20mm并且它的一端在料块侧壁的中点处另一端汇集于汇流凹槽29。而汇流凹槽29则是以料块本体25端面中点为圆心以20mm~50mm为半径的圆形凹槽,其深度同样为2mm~20mm。
80.如此一来,当气体流过料块时就能够在用于气流交换汇集的通道内纵横交错流动,有利于提高料层整体的通气率和传质传热效率。同时也有利于加快单块料块的热交换效率和均压均流效果。
81.具体的,如附图7所示,在料层的堆叠方式上,首先将a型或b型中的任意一种铺在最底层,然后将另一种型号的料块以其椭圆形通孔长轴方向与下层料块通孔长轴平行的方式铺于其上。至此利用此种铺设方法可以起到与缩放管相同的效果,使得气流在流经由这两层料块组成的通道时产生垂直于主流方向的径向流。之后,在第三层铺设与第二层型号相同的料块,不同的是,此时要将第三层料块以其通孔的长轴与第二层料块通孔长轴垂直的方式铺设。至此利用此种铺设方法可以起到与局部压扁管、交叉椭圆管相同的效果,使得气流在流经由这两层料块组成的通道时产生垂直于主流方向的涡旋二次流。最后,将与第三层不同型号的料块以两者长轴平行的方式铺于其上,使得气体在流经由这两层料块组成的通道时同样产生径向流。以这四层料块的铺设为一个循环一直铺设下去直至料层高度到达800mm~1000mm。
82.具体的,如附图6所示,在椭圆形通孔的内表面刻有螺旋槽30,在气体流经由料块通孔组成的通道时,会产生垂直于主流方向的旋转流。通过上述方法可以大幅强化反应过程的传热传质效率,从而提升产品质量。
83.所述干燥还原步骤:压制成型后的料块送入进料仓1再由进料仓1送上台车2,台车2上密封安装有烟罩3在烟罩3高温还原段正上方安装有燃烧室5。所述燃烧室5内的侧腔内安装有朝向不同的挡墙16,挡墙16的作用是降低燃烧室5侧腔出口处的气压,有利于燃烧室5主腔内燃烧反应充分进行,提高了燃烧效率,同时可以优化燃烧室5和烟罩3内的气流走向,提高料块表面气流分布和温度的均匀性,避免料块局部产生轻烧或过烧的现象。
84.在正式生产开始时,由煤粉喷吹管18喷入经过筛磨后70%过200目的低阶煤粉,由一次进气管19吹入顶燃式热风炉输出的高温热风,同时视燃烧反应进行的剧烈程度由富氧管20通入少部分氧气助燃。生成的煤气由扰流烧嘴14喷入到燃烧室5之中与二次进气管6喷入的高炉煤气进一步混匀充分,随后高温烟气从燃烧室5出口喷出进入到装有料块的烟罩3中,在台车2底部抽风机11产生的负压作用下穿过平铺的料层,完后对料块的还原。装满料块的台车2以一定的速度沿着焙烧炉中心线的方向前进,依次经过干燥段、预热段、还原段,直至完成全部工艺过程。
85.不同于传统焙烧机燃烧室对称布置,台车式焙烧炉的燃烧室5的侧腔中设置有朝向不同的挡墙16,从燃烧室5喷出的高温烟气气流在离开燃烧室5喷口后避免了与对向气流发生正面冲击,气流得到了充分的发展,降低了燃烧室5出口处的背压,有利于燃烧室5内燃烧反应的充分进行并提高了燃烧效率。此外,从燃烧室5出口处喷出的高温气流得益于挡墙16的设置避免了在狭小空间内正面冲击,因而气流流态更加合理,高温气流可以均匀的充满整个烟罩3,避免在料层表面形成局部的高温区和低温区造成料块过烧和未烧透,因而提高了料层整体的还原效率并提高了产品质量。
86.如附图2-4所示,燃烧室5侧腔的侧壁上安装有扰流喷嘴14。所述扰流喷嘴14作为
一个整体其主体组成包括煤粉喷吹管18、燃烧器17、喷嘴砖31、一次进气管19、富氧管20和扰流器23。其中煤粉喷吹管18被设置为管径较小的进口管段和远离所述进口管段的扩口管段。另外,在扩口管段内设置与其同轴向分布的分流管32,此时分流管32与燃烧器17之间形成内风道21也可称之为内环流通道,分流管32与扩口管段之间形成环流通道22也可称之为外环流通道。在内外环流通道的尾部分别设置有旋流角度略有不同的扰流器23。同时,煤粉喷吹管18的扩口管段与扰流喷嘴14所插入的喷嘴砖31的内壁之间形成外风道24,所述外风道24与一次进气管19、富氧管20相连通。
87.还原产物从高温还原段出来之后,在台车料面密封装置7的保护下免于二次氧化,随后还原产物进入具有微正压还原气氛的储料仓8,一部分初始还原炉料直接热装送入电弧炉熔分作为电炉炼钢的原料,另一部分初始还原炉料先后经过两次磁选和一次破碎筛分,得到的以残炭为主的杂质和尾矿返回至进料仓1重复利用,得到的高纯铁粉可直接用于转炉炼钢。
88.整个还原过程中,与高温还原段料层反应过后的高温还原烟气经过烟气循环系统先后进入到预热段和干燥段,完成对该位置料块的预热和干燥,随后烟气经过除尘设备10降尘后连同空气风机吹出的空气一同鼓入顶燃式热风炉中,热风炉产生的高温热风经由一次进气管吹入扰流喷嘴。由除尘设备10过滤下来的烟尘返回进料仓1作为压制料块的原料。如此一来,充分利用了反应产生的副产物,从而达成节约能源、减少成本、降低排放的目的。
89.如图8所示,台车式焙烧炉在箅条34之上摆放有布满圆形通孔的正六边形炉箅,并且沿着干燥段、预热段、高温还原段的方向,正六边形炉箅的大小依次变小,这样一来使得沿干燥段、预热段、高温还原段被抽下的高温烟气速度逐渐增加,并使得干燥段和预热段的料块预反应更加完全。
90.实施例1
91.实施例1工艺包括如下步骤:将钒钛磁铁矿、低煤阶煤粉、膨润土、羧甲基纤维素钠和水以质量比100:15:3.5:0.5:15混合均匀,其中钒钛磁铁矿的质量以全铁计算。钒钛磁铁矿中全铁含量为54%,并且为了保证物料的成块性能,需要把钒钛磁铁矿的粒度控制在80%过200目筛,把低煤阶煤粉的粒度控制在70%过100目筛。之后将混合料装入压砖机压制成规格尺寸为200mm*200mm*100mm的长方体料块,然后用特制的模具给料块打21个椭圆形通孔,a型料块椭圆形长轴选择20mm短轴选择15mm,导流凹槽宽度和半圆形凹槽的直径都取20mm,汇流凹槽的半径取15mm,导流凹槽和汇流凹槽的深度取4mm。b型料块椭圆形长轴选择15mm短轴选择10mm,其余参数与a型料块一致。在铺设方式上,每一组中的第二层与第三层料块长轴成90
°
夹角。将料块装入到台车式焙烧炉中,料层厚度为800mm,在1200℃的还原温度下在台车式焙烧炉中反应40min得到金属化料块,出炉时采用氮气保护金属化料块并进一步冷却。在经过破碎、筛分、磁选后,检测还原后金属化料块的金属化率为80%。
92.实施例2
93.实施例2工艺包括如下步骤:将磁铁精矿、低煤阶煤粉、膨润土、羧甲基纤维素钙和水以质量比100:13:2.5:1.0:13混合均匀,其中磁铁精矿的质量以全铁计算,磁铁精矿中全铁含量为60%,并且为了保证物料的成块性能,需要把磁铁精矿的粒度控制在70%过200目筛,把低煤阶煤粉的粒度控制在70%过100目筛。之后将混合料装入压砖机压制成规格尺寸为200mm*200mm*100mm的长方体料块,然后用特制的模具给料块打21个椭圆形通孔,a型料
块椭圆形长轴选择20mm短轴选择15mm,导流凹槽宽度和半圆形凹槽的直径都取20mm,汇流凹槽的半径取15mm,导流凹槽和汇流凹槽的深度取4mm。b型料块椭圆形长轴选择15mm短轴选择10mm,其余参数与a型料块一致。在铺设方式上,每一组中的第二层和第三层料块长轴成60
°
夹角。将料块装入到台车式焙烧炉中,料层厚度为900mm,在1250℃的还原温度下在台车式焙烧炉中反应60min得到金属化料块,出炉时采用氮气保护金属化料块并进一步冷却。在经过破碎、筛分、磁选后,检测还原后金属化料块的金属化率为84%。
94.实施例3
95.实施例3工艺包括如下步骤:将褐铁精矿、低煤阶煤粉、膨润土、聚乙烯醇树脂和水以质量比100:12:2.0:1.5:12混合均匀,其中褐铁精矿的质量以全铁计算,褐铁精矿中全铁含量为48%,并且为了保证物料的成块性能,需要把褐铁精矿的粒度控制在65%过200目筛,把低煤阶煤粉的粒度控制在60%过100目筛。之后将混合料装入压砖机压制成规格尺寸为200mm*200mm*100mm的长方体料块,然后用特制的模具给料块打21个椭圆形通孔,a型料块椭圆形长轴选择20mm短轴选择15mm,导流凹槽宽度和半圆形凹槽的直径都取20mm,汇流凹槽的半径取15mm,导流凹槽和汇流凹槽的深度取4mm。b型料块椭圆形长轴选择15mm短轴选择10mm,其余参数与a型料块一致。在铺设方式上,每一组中的第二层和第三层料块长轴成45
°
夹角。将料块装入到台车式焙烧炉中,料层厚度为1000mm,在1300℃的还原温度下在台车式焙烧炉中反应70min得到金属化料块,出炉时采用氮气保护金属化料块并进一步冷却。在经过破碎、筛分、磁选后,检测还原后金属化料块的金属化率为72%。
96.上面结合附图对本发明的实施例进行了描述,但是本发明并不局限于上述的具体实施方式,上述的具体实施方式仅仅是示意性的,而不是限制性的,本领域的普通技术人员在本发明的启示下,在不脱离本发明宗旨和权利要求所保护的范围情况下,还可做出很多形式,这些均属于本发明的保护之内。