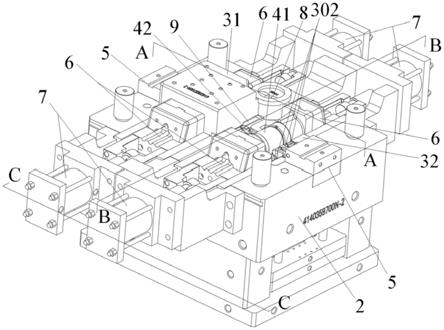
1.本实用新型涉及压铸技术领域,尤其涉及一种压铸形成薄壁壳体用的压铸模具。
背景技术:2.在采用现有的压铸模具压铸形成薄壁壳体时,由于薄壁壳体的壁厚较薄,在压铸过程中易因压铸金属液冷却收缩不均匀而产生变形。另外,当待压铸的薄壁壳体如图1所示的新能源智能驾驶辅助驱动马达的机壳01时,由于机壳01的端部设有凸出结构011,在压铸过程中,易因压铸金属液填充不充分及排气不完全而导致凸出结构01产生气孔、缩孔和缩松。由此可见,采用现有的压铸模具压铸形成薄壁壳体时,压铸形成的薄壁壳体易存在变形、气孔、缩孔及缩松问题,导致压铸形成的薄壁壳体的不良品率高。
技术实现要素:3.为提高压铸形成的薄壁壳体的合格率,本实用新型提出一种薄壁壳体用压铸模具,所述压铸模具包括模芯和镶件,所述模芯中设置有模腔,所述镶件位于所述模腔中,且所述模腔的内壁和所述镶件的外表面上设置有烂纹。这样,在采用本实用新型薄壁壳体用压铸模具压铸形成薄壁壳体时,由于模腔的内壁和镶件的外表面上设置有烂纹,可有效增加压铸形成的薄壁壳体的表面积及结构紧密度,从而可最大程度地降低薄壁壳体上产生气孔的概率;可有效增加压铸形成的薄壁壳体的表面粗糙度及表面强度,从而可在后期表面处理时减少起皮等不良现象的发生;可使压铸形成的薄壁壳体的表面与模腔的表面之间存留少量空气,避免薄壁壳体形成真空吸附,从而可有效减少粘模现象发生,方便脱模,进而可避免薄壁壳体在脱模时发生变形。综上可见,采用本实用新型薄壁壳体用压铸模具压铸形成薄壁壳体时,可减少气孔的产生概率,减少薄壁壳体脱模变形的发生概率,提高薄壁壳体的生产合格率。
4.优选地,所述模芯中设置有渣包槽,且所述模腔通过所述渣包槽与排气块中的排气通道连通。这样,在压铸过程中,可利用渣包槽和排气块来满足本实用新型薄壁壳体用压铸模具的排渣排气需求,避免压铸形成的薄壁壳体出现气孔、涡流孔及冷隔等现象,从而避免压铸形成的薄壁壳体在冷却收缩过程中受到阻力而产生变形。进一步地,所述模芯中,靠近所述模腔中的耳部结构腔处设置有与所述模腔连通的渣包。这样,在靠近模腔中的耳部结构腔即压铸形成薄壁壳体上的耳部结构的部位设置渣包,可使压铸金属液能够快速顺利填充模腔中的耳部结构腔,从而避免薄壁壳体在冷却收缩过程中因收缩不均匀而出现变形,提高薄壁壳体的生产合格率。
5.优选地,所述镶件包括镶柱和连接块,所述镶柱与所述连接块连接,且所述镶柱插装在所述模腔中,所述连接块在所述模腔的外部与所述抽芯滑块连接。这样,在开模时,抽芯滑块可通过连接块带动镶柱移动,从而使镶柱与压铸形成的薄壁壳体分离,快速完成脱模,提高薄壁壳体的生产效率。进一步地,所述抽芯滑块安装在所述压铸模具中的滑槽中并与所述镶件连接。这样,在开模时,抽芯滑块可沿滑槽滑动,避免抽芯滑块在滑动过程中发
生晃动或错位,提高开模稳定性,进而避免压铸形成的薄壁壳体在脱模时因镶件移动方向不稳定而发生变形,提高薄壁壳体的生产合格率。进一步优选地,所述抽芯滑块与固定在动模板上的驱动件连接并在所述驱动件的驱动下滑动。这样,在开模及合模时,本实用新型薄壁壳体用压铸模具可通过驱动件驱动抽芯滑块在滑槽中滑动,既方便控制开模合模速度,又可以减小开模合模时的工作量,提高薄壁壳体的生产效率。
6.优选地,所述模芯和所述镶件的镶柱上设置有多个点冷孔。这样,在压铸过程中,可向点冷孔中注入冷却液对模芯、镶件及压铸形成的薄壁壳体进行冷却,保持热平衡,使压铸形成的薄壁壳体均匀收缩,避免压铸形成的薄壁壳体因收缩不均匀而产生变形。进一步地,所述模芯上的点冷孔的深度为50mm,所述点冷孔与所述模腔之间的间距为18mm。这样,可进一步提高本实用新型薄壁壳体用压铸模具在压铸过程中的热平衡。
7.优选地,所述压铸模具中设置有两个所述模腔,且该两个所述模腔在所述模芯中呈对称设置。这样,在使用本实用新型薄壁壳体用压铸模型压铸形成薄壁壳体时,可同时压铸形成两个薄壁壳体,有效提高了薄壁壳体的压铸效率。进一步地,所述压铸模具中,定模板和动模板扣合连接,且所述定模板和所述动模板的扣合面上设置有容纳所述模芯的模槽;所述定模板上设置有浇注用的分流锥,两个所述模腔在所述分流锥两侧呈对称设置并通过浇注流道与所述分流锥连通;所述排气块在所述定模板的两端并在所述分流锥的两侧呈对称设置。这样,可使用同一个分流锥同时向两个模腔中注入压铸用金属液,保证压铸用金属液能够在两个模腔中同步流动填充,且压铸金属液在填充模腔的过程中,可同步将模腔中的渣质及气体排出,从而可保证压铸形成的两个薄壁壳体的质量相同,进而可提高本实用新型薄壁壳体用压铸模具同时压铸形成的两个薄壁壳体的质量稳定性。
附图说明
8.图1为新能源智能驾驶辅助驱动马达的机壳的结构示意图;
9.图2为本实用新型薄壁壳体用压铸模具的结构示意图;
10.图3为图2所示的薄壁壳体用压铸模具拆除定模板及一个定模芯时的结构示意图;
11.图4为图3中的a-a剖视结构示意图;
12.图5为图3中的b-b剖视结构示意图;
13.图6为图3中的c-c剖视结构示意图。
具体实施方式
14.下面,结合图2-6,对本实用新型薄壁壳体用压铸模具进行详细说明。
15.如图2-4所示,本实用新型薄壁壳体用压铸模具包括定模板1、动模板2、模芯和镶件。其中,定模板1和动模板2扣合连接,且定模板1和动模板2的扣合面上设置有容纳模芯的模槽。模芯包括定模芯31和动模芯32,定模芯31安装在定模板1上的定模槽(图中未示出)中,动模芯32安装在动模板2上的动模槽(图中未示出)中。模芯中设置有模腔301,镶件位于模腔301中,且模腔301的内壁和镶件的外表面上设置有烂纹(图中未示出)。这样,在采用本实用新型薄壁壳体用压铸模具压铸形成薄壁壳体(图中未示出)时,由于模腔301的内壁和镶件的外表面上设置有烂纹,可有效增加压铸形成的薄壁壳体的表面积及结构紧密度,从而可最大程度地降低薄壁壳体上产生气孔的概率;可有效增加压铸形成的薄壁壳体的表面
粗糙度及表面强度,从而可在后期表面处理时减少起皮等不良现象的发生;可使压铸形成的薄壁壳体的表面与模腔的表面之间存留少量空气,避免薄壁壳体形成真空吸附,从而可有效减少粘模现象发生,方便脱模,进而可避免薄壁壳体在脱模时发生变形。优选地,模芯中设置有渣包槽302,且模腔301通过渣包槽302与排气块5中的排气通道(图中未示出)连通。这样,在压铸过程中,可利用渣包槽302和排气块5来满足本实用新型薄壁壳体用压铸模具的排渣排气需求,避免压铸形成的薄壁壳体出现气孔、涡流孔及冷隔等现象,从而避免压铸形成的薄壁壳体在冷却收缩过程中受到阻力而产生变形。在实施本实用新型薄壁壳体用压铸模具时,可采用药水或激光方式加工出烂纹。优选地,模芯中,靠近模腔301中的耳部结构腔(图中未示出)处设置有与模腔301连通的渣包303。这样,在靠近模腔301中的耳部结构腔即压铸形成薄壁壳体上的耳部结构的部位设置渣包303,可使压铸金属液能够快速顺利填充模腔中的耳部结构腔,从而避免薄壁壳体在冷却收缩过程中因收缩不均匀而出现变形,提高薄壁壳体的生产合格率。优选地,模芯中设置有多个点冷孔304,这样,在压铸过程中,可向点冷孔304中注入冷却液对模芯及压铸形成的薄壁壳体进行冷却,保持热平衡,使压铸形成的薄壁壳体均匀收缩,避免压铸形成的薄壁壳体因收缩不均匀而产生变形。优选地,模芯上的点冷孔304的深度为50mm,且点冷孔304与模腔301之间的间距为18mm。这样,可进一步提高本实用新型薄壁壳体用压铸模具在压铸过程中的热平衡。优选地,模芯上设置有呈均匀分布12路点冷孔,可有效提高模芯及压铸形成的薄壁壳体的热平衡性。
16.如图3-6所示,镶件包括镶柱41和连接块42,镶柱41与连接块42连接,且镶柱41插装在模腔301中,连接块42在模腔301的外部与抽芯滑块6连接。这样,在开模时,抽芯滑块6可通过连接块42带动镶柱移动,从而使镶柱41与压铸形成的薄壁壳体(图中未示出)分离,快速完成脱模,提高薄壁壳体的生产效率。优选地,镶件中的镶柱41上设置有多个点冷孔411。这样,在压铸过程中,可向点冷孔411中注入冷却液对镶件及压铸形成的薄壁壳体进行冷却,保持热平衡,使压铸形成的薄壁壳体均匀收缩,避免压铸形成的薄壁壳体因收缩不均匀而产生变形。在具体实施本实用新型薄壁壳体用压铸模具时,镶柱41中可设置5路点冷孔或2路点冷孔。优选地,抽芯滑块6安装在压铸模具中的滑槽(图中未示出)中并与镶件中的连接块42连接。这样,在开模时,抽芯滑块6可沿滑槽滑动,避免抽芯滑块6在滑动过程中发生晃动或错位,提高开模稳定性,进而避免压铸形成的薄壁壳体在脱模时因镶件移动方向不稳定而发生变形,提高薄壁壳体的生产合格率。优选地,抽芯滑块6与固定在动模板2上的驱动件7连接并在驱动件7的驱动下滑动。这样,在开模及合模时,本实用新型薄壁壳体用压铸模具可通过驱动件7驱动抽芯滑块6在滑槽中滑动,既方便控制开模合模速度,又可以减小开模合模时的工作量,提高薄壁壳体的生产效率。优选地,驱动件7可采用气缸,选材及控制方便。
17.如图3所示,本实用新型薄壁壳体用压铸模具中设置有两个模腔301,且该两个模腔301在压铸模具中呈对称设置。这样,在使用本实用新型薄壁壳体用压铸模型压铸形成薄壁壳体时,可同时压铸形成两个薄壁壳体,有效提高了薄壁壳体的压铸效率。优选地,定模板1上设置有浇注用的分流锥8,两个模腔301在分流锥8两侧呈对称设置并通过浇注流道9与分流锥8连通;排气块5在定模板1的两端并在分流锥8的两侧呈对称设置。这样,可使用同一个分流锥8同时向两个模腔301中注入压铸用金属液,保证压铸用金属液能够在两个模腔301中同步流动填充,且压铸金属液在填充模腔301的过程中,可同步将模腔301中的渣质及
气体排出,从而可保证压铸形成的两个薄壁壳体的质量相同,进而可提高本实用新型薄壁壳体用压铸模具同时压铸形成的两个薄壁壳体的质量稳定性。
18.经实际生产使用发现,采用本实用新型薄壁壳体用压铸模具压铸形成薄壁壳体时,不良品率降低到1%左右,大大提高了压铸形成的薄壁壳体的生产合格率。综上可见,采用本实用新型薄壁壳体用压铸模具压铸形成薄壁壳体时,可减少气孔的产生概率,减少薄壁壳体脱模变形的发生概率,提高薄壁壳体的生产合格率。