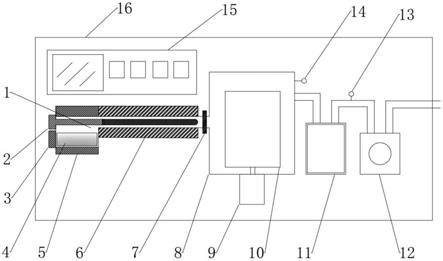
一种新型的parylene真空镀膜装置
技术领域
1.本实用新型属于真空镀膜技术领域,具体涉及到一种新型的parylene真空镀膜装置。
背景技术:2.parylene(中文名:聚对二甲苯)是一种保护性高分子聚合物材料的通常称呼,根据分子结构的不同,可分为n型、c型、d型、f型、ht型等多种类型。parylene膜层可在真空环境下通过气相沉积生成,parylene裂解后的活性分子具有良好穿透能力,能够在表面形状复杂的工件表面及其细小通孔等位置形成真正厚度均匀的无针孔覆型。parylene材料涂层具有很好的电气性能、热性能、化学稳定性和生物相容性,膜层可抵御酸碱、盐雾、霉菌、紫外及各种腐蚀性气件的侵害,被广泛应用于航空航天、电子工业、生物医疗、海洋环境和文物保护等方面。作为一种环保镀膜工艺,随着parylene材料的成本大幅度降低和工艺的日益成熟,近些年parylene镀膜的应用已经突破实验室和局部高端产品的应用阶段,逐渐转向大规模生产线和行业应用,其中电子行业尤为突出,同时也带动了生物医疗、海洋领域的积极应用,具有广泛的市场前景和巨大经济效益。
3.传统的parylene真空镀膜设备,由蒸发室、裂解室、镀膜室和低温冷阱系统以及真空获得系统5部分组成,蒸发室采用外部加热器方式紧扣在器壁上,满足器壁加热到150℃;裂解室采用外部加热炉将裂解管道加热到680℃以上;蒸发室和裂解室之间采用法兰连接,法兰及两端部分局部还需要做加热到150℃-200℃温控处理;裂解室和镀膜室之间采用法兰连接,连接段管路采用局部控温加热到150℃~200℃;经过裂解的单体分子在25℃左右的环境下涂敷成膜;真空室和低温冷阱系统连接,低温冷阱系统采用液氮制冷或者机械制冷机制冷满足制冷系统内部低于-70℃的温度,用于吸附未完成涂敷的单体材料;真空获得系统通过低温冷阱完成对真空容器大约10pa,裂解室大约65pa,蒸发室大约130pa的真空度指标建立。
4.由于传统方法采用蒸发室和裂解室两部分独立组成,导致两部分连接处需要增加保护连接法兰以及法兰两侧的温度区域的三组加热器,这种方法不仅增加了控制难度也增加了热能的消耗;其次对于裂解炉采用外部加热需要将外部炉体加热到680℃以上,受现有外置炉体结构的限制加热到680℃以上的有效裂解温区不足50%,为满足充分的裂解,需要增加裂解室的长度从而增加设备的整体长度,增加设备投入和运营占地成本;其次对于大气环境下应用的680℃的加热炉温度过高,不仅存在高温伤害危险,需要增加隔热层厚度,造成设备主体体积比较大,同时造成设备机柜内部温度比较高,不利于设备电子产品的工作;再次,由于裂解室在升温的过程中加热到680℃的时间较慢,能耗较高,也造成了整个作业流程时间过长,不利于批量生产和在行业或企业中广泛使用。
技术实现要素:5.为了解决目前传统parylene镀膜设备复杂庞大、耗能较高、裂解不充分、回收不完
全、作业时间长的难题,本实用新型提出了一种采用将蒸发室和裂解室一体化,并内置高温加热器进行充分快速裂解,采用低于-100℃低温冷阱提高收集效率的新型的parylene真空镀膜装置。
6.本实用新型解决技术问题所采用的技术方案如下:
7.一种新型的parylene真空镀膜装置,包括一体化蒸发裂解室、内置裂解加热器、温控进料门、物料舟、蒸发区温控器、裂解区保护温控器、连接法兰、镀膜室、电机机构、工件架、低温冷阱系统、真空系统、前级真空规、镀膜室真空规和测控系统;
8.所述一体化蒸发裂解室分为蒸发区和裂解区,所述蒸发区的外部设有用于对蒸发区进行温控的蒸发区温控器,所述裂解区的外部设有用于对裂解区的外部区域进行温度保护的裂解区保护温控器;
9.所述一体化蒸发裂解室靠近所述蒸发区的一端设有供所述物料舟进入所述蒸发区的温控进料门和供所述内置裂解加热器的加热部伸入所述一体化蒸发裂解室的通孔,所述内置裂解加热器的端部通过真空法兰和密封圈安装在所述通孔上,且所述内置裂解加热器的加热部包括与所述蒸发区对应的蒸发加热区和与所述裂解区对应的裂解加热区,所述裂解加热区为parylene材料的裂解提供所需的温度,所述蒸发加热区通过所述裂解加热区的热传导升温至所述蒸发区的工作温度范围;
10.所述一体化蒸发裂解室靠近所述裂解区的一端通过所述连接法兰与所述镀膜室连通,所述电机机构安装固定在所述镀膜室上,位于所述镀膜室内的工件架与所述电机机构的驱动端固定连接,所述镀膜室通过真空管道依次与所述低温冷阱系统、所述真空系统连接,所述前级真空规设置在所述低温冷阱系统与所述真空系统之间的真空管道上,所述镀膜室真空规设置在所述镀膜室上;
11.所述测控系统用于采集所述前级真空规和所述镀膜室真空规的真空度数据并控制所述真空系统的工作状态,还用于控制所述内置裂解加热器、所述温控进料门、所述蒸发区温控器、所述裂解区保护温控器的工作温度、所述低温冷阱系统的制冷温度以及所述电机机构的运动。
12.本实用新型具有以下有益效果:
13.(1)本实用新型将蒸发室和裂解室制作成一个整体,去掉传统的用于连接蒸发室和裂解室的法兰连接组件以及对应的温控补偿器等冗余部分,形成一体化蒸发裂解室,便于进行整体温控的同时,有效降低了设备总长度,解决了传统parylene镀膜设备连接复杂、总体体积庞大的问题;
14.(2)本实用新型采用新型的内置裂解加热器安装到一体化蒸发裂解室内,用于满足parylene裂解所需的温度,由于内置裂解加热器自身热负载较小,且在真空环境下更容易快速加热,因此减少了设备加热过程的耗时,有效缩短了镀膜作业时间,同时内置裂解加热器更有利于parylene的充分裂解;
15.(3)本实用新型通过在裂解区的外部设置裂解区保护温控器,将传统parylene镀膜设备的裂解炉需加热至680℃以上改为满足parylene活性小分子的裂解保温区间,并且经过实验验证,该裂解保温区间完全能够满足经过加热裂解后的parylene活性小分子顺利到达镀膜室,保证parylene镀膜过程的顺利进行;同时,由于裂解区的温度大幅度降低,因此也有效降低了一体化蒸发裂解室的体积和加热功耗。
附图说明
16.图1为本实用新型所述的一种新型的parylene真空镀膜装置的结构示意图;
17.图1中:1为一体化蒸发裂解室,2为内置裂解加热器,3为温控进料门,4为parylene物料舟,5为蒸发区温控器,6为裂解区保护温控器,7为连接法兰,8为镀膜室,9为电机机构,10为工件架,11为低温冷阱,12为真空获得设备,13为前级真空规,14为镀膜室真空规,15为测控系统,16为设备机柜;
18.图2为图1中内置裂解加热器的剖视图;
19.图2中:端部2-1,温控传感器连接线2-2,加热棒连接线2-3,气体冷却管2-4,隔离块2-5,裂解器加热棒2-6,绝缘导热填充料2-7,温控传感器2-8,内置裂解加热器壳体2-9,密封圈2-10;
20.图3为图1中裂解区的横截面示意图;
21.图4为测控系统的控制原理逻辑示意图。
具体实施方式
22.下面将结合附图及较佳实施例对本实用新型的技术方案进行详细描述。
23.本实用新型提出一种新型的parylene真空镀膜装置,如图1所示,该装置包括一体化蒸发裂解室1、内置裂解加热器2、温控进料门3、物料舟4、蒸发区温控器5、裂解区保护温控器6、连接法兰7、镀膜室8、电机机构9、工件架10、低温冷阱系统11、真空系统12、前级真空规13、镀膜室真空规14和测控系统15。
24.本实用新型的parylene真空镀膜装置将蒸发室和裂解室制作成一个整体,去掉传统的用于连接蒸发室和裂解室的法兰连接组件以及对应的温控补偿器等冗余部分,形成一体化蒸发裂解室1,便于进行整体温控的同时,有效降低了设备总长度,缩小设备体积。具体地,仍参见图1,一体化蒸发裂解室1分为蒸发区和裂解区,蒸发区的外部设有蒸发区温控器5,蒸发区温控器5通过温控可满足150℃~180℃温度范围,以实现对蒸发区的温控;裂解区的外部设有裂解区保护温控器6,裂解区保护温控器6的工作温度范围为180℃~200℃,主要用来实现对裂解区的外部区域进行180℃~200℃的温度保护作用,使得经过内置加热裂解器2裂解后的parylene活性小分子可以在180℃~200℃的温度保护下顺利到达镀膜室8。由于经过加热裂解后的parylene活性小分子可以在180℃~200℃的温度保护下顺利到达镀膜室8,因此本实用新型将原来传统parylene镀膜设备的680℃的裂解炉区间改为满足parylene活性小分子180-200℃的裂解保温区间,并且经过实验验证,该裂解保温区间完全能够满足经过加热裂解后的parylene活性小分子顺利到达镀膜室,保证parylene镀膜过程的顺利进行;同时,由于裂解区的温度大幅度降低,因此也有效降低了一体化蒸发裂解室的体积和加热功耗。
25.一体化蒸发裂解室1靠近蒸发区的一端设有温控进料门3和通孔,盛有parylene的物料舟4通过温控进料门3放置到一体化蒸发裂解室1对应的蒸发区内,通孔则用于供内置裂解加热器2的加热部伸入一体化蒸发裂解室1的内部,并且内置裂解加热器2的端部通过真空法兰(例如cf真空法兰)和密封圈2-10(例如无氧铜密封圈)安装在通孔上,实现对通孔的密封。内置裂解加热器2的加热部位于一体化蒸发裂解室1内,加热部包括与蒸发区对应的蒸发加热区和与裂解区对应的裂解加热区,裂解加热区为parylene材料的裂解提供所需
的温度,蒸发加热区通过裂解加热区的热传导升温,可满足达到蒸发区的150℃~180℃工作温度范围,从而保证parylene物料的有效蒸发。
26.进一步地,如图2所示,内置裂解加热器2包括端部2-1和与端部2-1一体化连接的加热部,加热部具体包括壳体2-9、裂解加热棒2-6、温度传感器2-8和气体冷却管2-4。
27.壳体2-9内的隔离块2-5将加热部分成蒸发加热区(图2中的a区)和裂解加热区(图2中的b区)两个区域,其中蒸发加热区是靠近端部2-1的区域,其工作温度范围为150℃~180℃,裂解加热区是远离端部2-1的区域,其工作温度范围为650℃~800℃,并且裂解加热棒2-6和温度传感器2-8均设置在裂解加热区的内部,同时裂解加热区的内部填充绝缘导热材料2-7,裂解加热棒2-6的连接线2-3和温度传感器2-8的连接线2-2通过蒸发加热区和端部2-1后与测控系统15连接,通过测控系统15为裂解区对应的壳体2-9部分实现650℃~800℃的控温,满足不同分子结构的parylene材料高温裂解需求;蒸发加热区的内部设有气体冷却管2-4,气体冷却管2-4通过端部2-1后与外部连通,气体冷却管2-4在测控系统15的控制下向蒸发加热区充入空气,从而加速内置裂解加热器2的降温。该内置裂解加热器2安装到一体化蒸发裂解室1内,用于满足parylene裂解所需的温度,由于内置裂解加热器2自身热负载较小,且在真空环境下更容易快速加热,因此减少了设备加热过程的耗时,有效缩短了镀膜作业时间。
28.内置裂解加热器2的壳体2-9采用外径和原来裂解炉内径相同、长度和同型号裂解炉有效加热区域相同的310s牌号不锈钢材料制作,新的裂解区内径和内置裂解加热器2的壳体2-9外径为同心圆环或带多翅片的同心圆环(壳体2-9的外壁沿圆周设有若干个翅片,如图3所示),制作成可满足800℃高温的热控内置裂解加热器2。在满足蒸发区的真空度为120pa~140pa范围以内,裂解区的真空度为60pa~70pa范围以内以下和镀膜室8的真空度为1pa~10pa范围以内的真空需求情况下,综合考虑稀薄气体的流态,图3所示的这种管道间隙更利于提高粘滞流-分子流状态的稀薄气体分子与高温器壁的撞击次数,更容易获取促使parylene分子裂解成单体所需的能量,从而使裂解更加充分。
29.一体化蒸发裂解室1靠近裂解区的一端通过连接法兰7与镀膜室8连通,电机机构9安装固定在镀膜室8上,工件架10位于镀膜室8的内部,并且工件架10与电机机构9的驱动端固定连接,电机机构9驱动工件架10在镀膜过程中旋转;低温冷阱系统11可满足低于-100℃的低温性能,其通过真空管道分别与镀膜室8、真空系统12连接,用于吸附镀膜过程中没有完全沉积的parylene单体分子,避免其进入真空系统12内部造成设备损毁;前级真空规13设置在低温冷阱系统11与真空系统12之间的真空管道上,用于监测真空系统12的本地真空和抽气性能;镀膜室真空规14设置在镀膜室8上,用于监测镀膜室8内部的工作真空度。可选地,本实用新型中的低温冷阱系统11采用低于-100℃的机械制冷机系统,相比液氮系统避免了大量的外围设备投入和每次都要一次性消耗液氮的不足,相比常用的-70℃的低温冷阱又提高了未完成涂敷的parylene单体的收集效率,使parylene单体回收更完全。
30.测控系统15用于采集前级真空规13和镀膜室真空规14的真空度数据以及控制真空系统12的工作状态(例如系统的启动、停止、工作时长等),还用于控制内置裂解加热器2、温控进料门3、蒸发区温控器5、裂解区保护温控器6的工作温度、低温冷阱系统11的制冷温度以及启动和关闭电机机构9,使一体化蒸发裂解室1、电机机构9、低温冷阱系统11和真空系统12有序工作,实现parylene镀膜过程。
31.进一步地,如图4所示,测控系统15包括plc控制器、触摸显示屏和温度控制器,其中触摸显示屏和温度控制器分别与plc控制器连接,plc控制器还分别与电机机构9、真空系统12、前级真空规13和镀膜室真空规14连接;plc控制器用于控制触摸显示屏显示温度数据、真空度数据以及电机机构9的运动状态,以及接收通过触摸显示屏输入的镀膜材料参数和膜厚参数等;plc控制器还用于通过温度控制器分别控制内置裂解加热器2、蒸发区温控器5、裂解区保护温控器6、低温冷阱系统11以及温控进料门3的温度,温度控制器包括与内置裂解加热器2连接的加热器温度控制器、与蒸发区温控器5连接的蒸发温度控制器、与裂解区保护温控器6连接的裂解温度控制器、与低温冷阱系统11连接的冷阱温度控制器以及与温控进料门3连接的进料门温度控制器,通过加热器温度控制器、蒸发温度控制器、裂解温度控制器、冷阱温度控制器以及进料门温度控制器实现对相应组件的温度控制。
32.仍参见图1,本实用新型的一种新型的parylene真空镀膜装置还包括设备机柜16,设备机柜16是整个装置的安装和固定基础,一体化蒸发裂解室1、镀膜室8、低温冷阱系统11、真空系统12和测控系统15均集成在设备机柜16内。
33.下面以parylenec材料为例,对本实用新型的parylene真空镀膜装置的测试步骤进行如下说明:
34.1.设备供电,测控系统15,系统上电开机,开始系统状态检查2-3分钟;
35.2.测控系统15的触摸显示屏上开始显示并记录温度曲线、真空度曲线、镀膜参数、运动状况等数据,可开始操作;
36.3.在测控系统15选择对应分子结构的镀膜材料,并输入膜厚参数;
37.4.将放置好工件的工件架10安装在镀膜室8内并和电机机构9连接;
38.5.打开温控进料门3,将放置好物料的parylene物料舟4放置到一体化蒸发裂解室1对应的蒸发室内,并关闭温控进料门3;
39.6.启动真空系统12,并观察前级真空规13真空度优于100pa时,启动低温冷阱系统11开始制冷;
40.7.将裂解区保护温控器6控温到180℃~200℃;
41.8.将温控进料门3和蒸发区温控器5控温到70℃;
42.9.当低温冷阱系统11预冷到-70℃后,将内置裂解加热器2加热到650℃~750℃对应不同型号材料的裂解温度需求下,启动电机机构9开始运动;
43.10.当低温冷阱系统11预冷温度低于-100℃时,将温控进料门3和蒸发区温控器5从70℃升温到140℃,parylene单体分子开始在镀膜室沉积;
44.11.镀膜完成后关闭温控进料门3和蒸发区温控器5,并打开风扇对蒸发区温控器5降温到45℃以下;
45.12.然后关闭内置裂解加热器2、并通过气体冷却管2-4给内置裂解加热器2充入空气加速其降温;
46.13.关闭裂解区保护温控器6;
47.14.关闭电机机构9,关闭低温冷阱系统11,关闭真空系统12;
48.15.通过一体化蒸发裂解室1上的真空放气阀门给系统充入干燥大气,并取出工件架10;
49.16关闭系统。
50.以上所述实施例的各技术特征可以进行任意的组合,为使描述简洁,未对上述实施例中的各个技术特征所有可能的组合都进行描述,然而,只要这些技术特征的组合不存在矛盾,都应当认为是本说明书记载的范围。
51.以上所述实施例仅表达了本实用新型的几种实施方式,其描述较为具体和详细,但并不能因此而理解为对实用新型专利范围的限制。应当指出的是,对于本领域的普通技术人员来说,在不脱离本实用新型构思的前提下,还可以做出若干变形和改进,这些都属于本实用新型的保护范围。因此,本实用新型专利的保护范围应以所附权利要求为准。