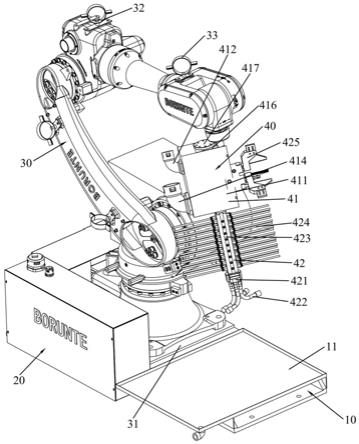
1.本发明涉及铸造生产领域技术,尤其是指一种可更换喷枪或铜管模块化压铸雾化治具的设备。
背景技术:2.铸造是将液体金属浇铸到与零件形状相适应的铸造空腔中,待其冷却凝固后,以获得零件或毛坯的方法。在铸造生产过程中,需要先将金属原料加热熔化,然后再将金属熔液浇铸到两片铸造模具形成的铸造空腔中。当金属熔液在浇铸腔内成型之后将铸造模具分开,将铸造成型的模具取出。在将刚刚铸造成型的元件从模具中取出后,常常会有残留的废液留在模具中,因此需要对模具的内部进行清理,同时为了便于模具中的铸造元件从模具中脱离,常常会在模具成型腔中喷涂脱模剂,因此传统的铸造设备会在取出模具中的铸造元件后,对模具上的空腔位置直接喷射脱模液,将铸造用的模具腔喷射干净,同时脱模液在模具腔中形成脱模层,使得铸造模具腔体内的液体原料固化成型后容易脱离。
3.现有的脱模剂喷涂系统喷头模块较为单一,并且无法更换,在面对特殊的模腔时无法采用适合的喷头,导致喷涂的质量较差,从而影响后续的铸造加工质量,并且现有的喷雾机一般包括有一控制器,导致喷雾机的重量较大,在使用工业机器人带动活动时,长期使用会使机器人单轴伺服过载老化,影响使用寿命,因此,有必要对现有的脱模剂喷涂系统作出进一步改进。
技术实现要素:4.有鉴于此,本发明针对现有技术存在之缺失,其主要目的是提供一种可更换喷枪或铜管模块化压铸雾化治具的设备,其通过喷头可拆卸地设置在安装架上并与雾化模组的输出端连通,增加了喷头模块的多样化,喷涂的效果更好,进一步保证了后续压铸产品的质量,同时减少了喷头的质量,增加了机器人的使用寿命。
5.为实现上述目的,本发明采用如下之技术方案:一种可更换喷枪或铜管模块化压铸雾化治具的设备,包括有安装座、控制柜、机器人以及雾化治具;该控制柜设置在安装座上;该机器人一端固定在安装座上并位于控制柜侧旁,机器人与控制柜连接;该雾化治具可拆换地安装在机器人的自由端,雾化治具包括有雾化模块,该雾化模块连接有喷枪模块和/或铜管模块,该雾化模块包括有安装架、控制回路波纹管、离型剂管道、执行回路波纹管以及雾化模组;该安装架可拆卸地安装在机器人的自由端,该控制回路波纹管设置在安装架上并与控制柜连接,该离型剂管道设置在安装架上并与控制回路波纹管的输出端连通,该雾化模组设置在安装座上并与离型剂管道的输出端连通,该执行回路波纹管设置在安装架上并与控制柜连接,且执行回路波纹管的输出端与雾化模组连通;该喷枪模块和/或铜管模块设置在安装架上并与雾化模组的输出端连通。
6.作为一种优选方案,所述机器人通过一隔热电木板安装在安装座上。
7.作为一种优选方案,所述安装座上还设置有一水槽板,该水槽板位于安装座上方
并位于机器人侧旁。
8.作为一种优选方案,所述机器人上设置有分别用于固定控制回路波纹管和执行回路波纹管的第一固定卡箍和第二固定卡箍。
9.作为一种优选方案,所述安装架通过一法兰安装架可拆卸地安装在机器人的自由端法兰上,且法兰安装架与机器人法兰之间夹设有一隔热电木盘。
10.作为一种优选方案,所述离型剂管道的输入端连接有一离型剂主进口以及多个诱导止回阀,对应的,离型剂管道也为多个,该离型剂主进口分别与控制回路波纹管的输出端以及多个诱导止回阀的输入端连通并与控制柜连接,每一诱导止回阀的输出端均与对应离型剂管道的输出端连通,且每一诱导止回阀上还设置有一用于调节脱模剂流量的调节旋钮。
11.作为一种优选方案,所述雾化模组上设置有多个进气口,该进气口的输入端与执行回路波纹管的输出端连通,进气口的输出端与雾化模组连通。
12.作为一种优选方案,所述喷枪模块和/或铜管模块包括有喷枪模块转接块以及喷雾喷枪,该喷枪模块转接块设置在安装架上并与雾化模组的输出端连通,该喷雾喷枪设置在喷枪模块转接块上并与喷枪模块转接块输出端连通。
13.作为一种优选方案,所述喷枪模块和/或铜管模块包括有雾化铜管安装架以及雾化铜管,该雾化铜管安装架设置在安装架上并与雾化模组的输出端连通,该雾化铜管设置在雾化铜管安装架上并与雾化铜管安装架输出端连通。
14.作为一种优选方案,所述喷枪模块和/或铜管模块包括有夹爪、雾化铜管安装架、雾化铜管、喷枪模块转接块以及雾化喷枪;该夹爪设置在安装架上并与控制柜连接,该雾化铜管安装架设置在安装架上并与雾化模块的输出端连通,该雾化铜管设置在雾化铜管安装架上并与雾化铜管安装架输出端连通,该喷枪模块转接块设置在雾化铜管安装架上并与雾化铜管安装架的输出端连通,该雾化喷枪设置在喷枪模块转接块上并与喷枪模块转接块的输出端连通。
15.本发明与现有技术相比具有明显的优点和有益效果,具体而言,由上述技术方案可知:第一、通过雾化治具可拆卸地设置在机器人的自由端,不仅使得喷头模块在使用过程中更加方便更换,而且增加了喷头模块的多样化,在面对不同的模腔时可以采用对应合适的雾化治具,喷涂的效果更好,进一步保证了后续压铸产品的质量,同时配合控制回路波纹管和执行回路波纹管均与控制柜连接,且控制柜位于机器人侧旁,使得雾化治具的控制器与机器人控制器合并在一起,取消了位于雾化治具上的控制器,大大减少了雾化治具的质量,有效防止了长时间使用造成的机器人单轴伺服过载老化,增加了机器人的使用寿命。
16.第二、通过离型剂管道的输入端连接有一离型剂主进口以及多个诱导止回阀,使得可以通过诱导止回阀控制离型剂主进口进行分流,并实现独立控制脱模剂的通断,起到及时阻断脱模剂的作用,避免高压吹气时液体残留影响产品质量,并配合雾化模组上设置有多个进气口,该进气口的输入端与执行回路波纹管的输出端连通,高压气体可通过进气口进入雾化模组中,并通过喷头喷出,使得可以通过高压气体进行模内清洁,吹除残留的脱模剂,以免影响后续产品的生产加工。
17.为更清楚地阐述本发明的结构特征和功效,下面结合附图与具体实施例来对本发明进行详细说明。
附图说明
18.图1是本发明之较佳实施例的立体结构示意图;图2是本发明之较佳实施例中雾化模块的局部组装示意图;图3是本发明之较佳实施例中雾化模块另一角度的局部组装示意图;图4是本发明之较佳实施例中雾化治具的立体结构示意图;图5是本发明之较佳实施例中另一雾化治具的立体结构示意图;图6是本发明之较佳实施例中又一雾化治具的立体结构示意图。
19.附图标识说明:10、安装座
ꢀꢀꢀꢀꢀꢀꢀꢀꢀꢀꢀꢀꢀꢀꢀꢀꢀꢀꢀꢀ
11、水槽板20、控制柜
ꢀꢀꢀꢀꢀꢀꢀꢀꢀꢀꢀꢀꢀꢀꢀꢀꢀꢀꢀꢀ
30、机器人31、隔热电木板
ꢀꢀꢀꢀꢀꢀꢀꢀꢀꢀꢀꢀꢀꢀꢀꢀ
32、第一固定卡箍33、第二固定卡箍
ꢀꢀꢀꢀꢀꢀꢀꢀꢀꢀꢀꢀꢀꢀ
40、雾化治具41、雾化模块
ꢀꢀꢀꢀꢀꢀꢀꢀꢀꢀꢀꢀꢀꢀꢀꢀꢀꢀ
411、安装架412、控制回路波纹管
ꢀꢀꢀꢀꢀꢀꢀꢀꢀꢀꢀ
413、离型剂管道414、执行回路波纹管
ꢀꢀꢀꢀꢀꢀꢀꢀꢀꢀꢀ
415、雾化模组416、法兰安装架
ꢀꢀꢀꢀꢀꢀꢀꢀꢀꢀꢀꢀꢀꢀꢀ
417、隔热电木盘418、雾化铜芯
ꢀꢀꢀꢀꢀꢀꢀꢀꢀꢀꢀꢀꢀꢀꢀꢀꢀ
42、喷枪模块和/或铜管模块421、喷枪模块转接块
ꢀꢀꢀꢀꢀꢀꢀꢀꢀꢀꢀ
422、喷雾喷枪423、雾化铜管安装架
ꢀꢀꢀꢀꢀꢀꢀꢀꢀꢀꢀ
424、雾化铜管425、夹爪
ꢀꢀꢀꢀꢀꢀꢀꢀꢀꢀꢀꢀꢀꢀꢀꢀꢀꢀꢀꢀꢀ
43、离型剂主进口44、诱导止回阀
ꢀꢀꢀꢀꢀꢀꢀꢀꢀꢀꢀꢀꢀꢀꢀꢀ
441、调节旋钮45、进气口。
具体实施方式
20.请参照图1至图6所示,其显示出了本发明之较佳实施例的具体结构,其中包括有安装座10、控制柜20、机器人30以及雾化治具40。
21.该控制柜20设置在安装座10上;在本实施例中,所述安装座10上还设置有一水槽板11,该水槽板11位于安装座10上方。
22.该机器人30一端固定在安装座10上并位于控制柜20侧旁,机器人30与控制柜20连接;在本实施例中,所述机器人30通过一隔热电木板31安装在安装座10上,隔热电木板31起到隔热作用,避免压铸模具产生的高温传递给机器人,从而影响机器人30末端伺服电机正常工作;前述水槽板11位于机器人30侧旁,水槽板11用于雾化治具40待机时将多余的脱模剂进行排除。
23.该雾化治具40可拆换地安装在机器人30的自由端,用以针对不同的模腔采用不同的雾化治具,方便于对各种模腔进行快速清洁,雾化治具40包括有雾化模块41,该雾化模块连接有喷枪模块和/或铜管模块42,该雾化模块41包括有安装架411、控制回路波纹管412、
离型剂管道413、执行回路波纹管414以及雾化模组415,其中安装架411和雾化模组415均为铝材质,进一步降低了雾化治具40的质量。
24.前述机器人30上设置有分别用于固定控制回路波纹管412和执行回路波纹管的第一固定卡箍32和第二固定卡箍33;该安装架411可拆卸地安装在机器人30的自由端,其中,安装架411通过一法兰安装架416可拆卸地安装在机器人30的自由端法兰上,且法兰安装架416与机器人30法兰之间夹设有一隔热电木盘417,该控制回路波纹管412设置在安装架411上并与控制柜20连接,该离型剂管道413设置在安装架411上并与控制回路波纹管412的输出端连通,该雾化模组415设置在安装座411上并与离型剂管道413的输出端连通,雾化模组415通过雾化铜芯418以及雾化模组415之间的伯努利原理进行雾化,铜芯418位于雾化模组415中,该执行回路波纹管414设置在安装架411上并与控制柜20连接,且执行回路波纹管414的输出端与雾化模组415连通。
25.在本实施例中,所述离型剂管道413的输入端连接有一离型剂主进口43以及多个诱导止回阀44,对应的,离型剂管道413也为多个,该离型剂主进口43分别与控制回路波纹管412的输出端以及多个诱导止回阀44的输入端连通并与控制柜连接,每一诱导止回阀44的输出端均与对应离型剂管道413的输出端连通,诱导止回阀44与控制柜20连接,使得可通过控制柜20控制诱导止回阀44的通断,且每一诱导止回阀44上还对应设置有一用于调节脱模剂流量的调节旋钮441,脱模剂通过诱导止回阀44进行分流进入不同的离型剂管道413中,可以实现独立通断,起到及时阻断脱模剂的作用,避免高压吹气时液体残留影响产品质量,所述雾化模组415上设置有多个进气口45,该进气口45的输入端与执行回路波纹管414的输出端连通,进气口45的输出端与雾化模组415连通,进气口45与控制柜20连接,使得可通过控制柜20控制进气口45上高压气体的通断。
26.该喷枪模块和/或铜管模块42设置在安装架411上并与雾化模组415的输出端连通;在本实施例中,喷枪模块和/或铜管模块42如图4所示,包括有喷枪模块转接块421以及喷雾喷枪422,该喷枪模块转接块421设置在安装架411上并与雾化模组415的输出端连通,该喷雾喷枪422设置在喷枪模块转接块421上并与喷枪模块转接块421输出端连通。
27.喷枪模块和/或铜管模块42也可以如图5所示,包括有雾化铜管安装架423以及雾化铜管424,该雾化铜管安装架423设置在安装架411上并与雾化模组415的输出端连通,该雾化铜管424设置在雾化铜管安装架423上并与雾化铜管安装架423输出端连通。
28.喷枪模块和/或铜管模块42还可以如图6所示,包括有夹爪425、雾化铜管安装架423、雾化铜管424、喷枪模块转接块421以及雾化喷枪422;该夹爪设425置在安装架411上并与控制柜20连接,夹爪425可以用来夹取模腔中加工完成的产品,该雾化铜管安装架423设置在安装架411上并与雾化模块415的输出端连通,该雾化铜管424设置在雾化铜管安装架423上并与雾化铜管安装架423输出端连通,该喷枪模块转接块421设置在雾化铜管安装架423上并与雾化铜管安装架423的输出端连通,该雾化喷枪422设置在喷枪模块转接块421上并与喷枪模块转接块421的输出端连通。
29.详述本实施例的工作原理如下:先通过安装座10将机器人30和控制柜20安装在压铸机上,并通过隔热电木板31隔绝压铸机传递给机器人30的热量,然后根据模腔选择合适的雾化治具40,当需要对特殊模腔进行点对点清洗雾化时,可以采用带有喷雾喷枪422的雾化治具40,当需要进行大面积模
腔清洗时,可以采用带有雾化铜管424的雾化治具40,也可以根据实际需要采用同时带有喷雾喷枪422和雾化铜管424的雾化治具40,接着由机器人30带动雾化治具40伸入模腔中,然后由控制柜20控制,使诱导止回阀44打开并对离型剂主进口43中的脱模剂进行分流,并可根据实际情况通过调节旋钮441调节脱模剂流量的大小,使得对模腔内完成脱模剂喷涂作业,喷涂完成后,由控制柜20控制关闭诱导止回阀44,进行快速关闭脱模剂,诱导止回阀44关闭后,由控制柜20控制进气口45打开,然后通过雾化治具40将高压气体喷出,将模腔内残留的脱模剂冲刷掉,实现对模内的清洁,避免残留的脱模剂对后续压铸产品造成影响,冲刷完成后,由控制柜20关闭进气口45,然后由机器人带动雾化治具40移出模腔,并回位到水槽板11的正上方,并将雾化治具40内残留的脱模剂排到水槽板11上,再通过水槽板11排出即可。
30.本发明的设计重点在于:首先,通过喷头可拆卸地设置在安装架上并与雾化模组的输出端连通,不仅使得喷头模块在使用过程中更加方便更换,而且增加了喷头模块的多样化,在面对不同的模腔时可以采用对应合适的喷头,喷涂的效果更好,进一步保证了后续压铸产品的质量,同时配合控制回路波纹管和执行回路波纹管均与控制柜连接,且控制柜位于机器人侧旁,使得喷枪模块的控制器与机器人控制器合并在一起,取消了位于喷头上的控制器,大大减少了喷头的质量,有效防止了长时间使用造成机器人单轴伺服过载老化,增加了机器人的使用寿命。其次,通过离型剂管道的输入端连接有一离型剂主进口以及多个诱导止回阀,使得可以通过诱导止回阀控制离型剂主进口进行分流,并实现独立控制脱模剂的通断,起到及时阻断脱模剂的作用,避免高压吹气时液体残留影响产品质量,并配合雾化模组上设置有多个进气口,该进气口的输入端与执行回路波纹管的输出端连通,高压气体可通过进气口进入雾化模组中,并通过喷头喷出,使得可以通过高压气体进行模内清洁,吹除残留的脱模剂,以免影响后续产品的生产加工。
31.以上所述,仅是本发明的较佳实施例而已,并非对本发明的技术范围作任何限制,故凡是依据本发明的技术实质对以上实施例所作的任何细微修改、等同变化与修饰,均仍属于本发明技术方案的范围内。