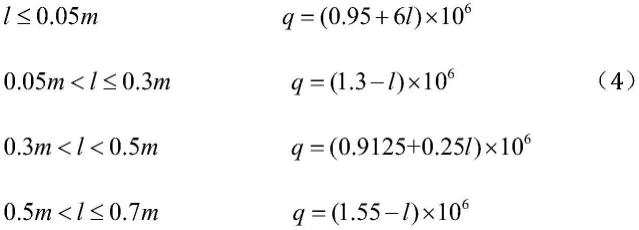
1.本发明属于冶金中圆坯连铸技术领域,涉及一种大直径尤其是φ1050mm~φ1350mm连铸圆坯生产工艺。
背景技术:2.随着世界连铸技术的不断发展,我国特殊钢弧形连铸技术更是成绩突出,从2006-2010年五年间,就打破了连铸坯断面长期以来一直不超过φ500mm的瓶颈,而且随着我国风电能源、工程机械等新兴领域用大型轴承、齿轮、法兰等环锻件的快速高质量的发展需要,倒逼冶金连铸技术进一步创新突破,连铸坯断面规格也就不断扩大,实现了φ500mm
→
φ600mm
→
φ800mm
→
φ900mm
→
φ1000mm的一次次突破和世界纪录的刷新,引领世界圆坯连铸技术的发展。然而,自2010年至今快11年了,由于受市场及技术的局限,连铸坯断面长期停留在φ1000mm关口,难以再突破扩大,或批量稳定生产,除去市场单品种批量少、连铸排产困难的因素外,技术层面的主要原因包括超大截面的连铸圆坯拉矫难、矫直难、中心疏松及裂纹的控制难、全截面成分均匀性控制难等等一系列问题。现随着减能耗减排放等政策的实施,风电领域用圆钢向高质量、大型化、轻量化、低成本、长寿命(20年以上)发展成为必然趋势,目前国内外风电主力机型为2-5mw,更大型风机基本仍处于少批量试验或样机阶段,所以未来5mw及以上大型风机将发展迅速,而大型风电的主轴、轴承、齿轮、法兰作为风电机组最关键核心部件,其对φ1050mm~φ1350mm甚至更大截面的坯料需求越来越大,而目前这种截面的坯料市场上只有传统模铸锭产品,可传统模铸锭存在纯净度差、效率低、成本高、质量不稳定的局限,很难满足行业的发展需要,更不适合降碳减排的“发展理念,所以,开发更大截面、更低消耗、更高质量、更高效率的新型坯料以满足大型风电机组之更大轴承、齿轮、法兰、主轴所需以及国之大器之大型工程机械、石油化工设备所需已是迫在眉睫。
技术实现要素:3.本发明的目的提供一种大直径高纯致密特殊钢连铸圆坯的生产方法,探索φ1050mm~φ1350mm连铸圆坯的生产。通过与国内外顶级连铸设计制作单位合作,引进高端连铸核心装备,开发新型连铸集成技术,优化连铸过程流场、温度场、磁场,实现三场合理匹配,结合钢水净化冶炼技术,获得高致密、高均质、高洁净度的φ1050mm~φ1350mm超大规格连铸圆坯,满足风电能源、工程机械、石油化工等新兴领域用超大型轴承、齿轮、法兰等环锻件及其它大型锻件的快速高质量发展的需要。
4.本发明所采用的技术方案为:一种大直径高纯致密特殊钢连铸圆坯生产方法,包括钢水冶炼、弧形圆坯连铸、切割、控制冷却、精整,所述弧形圆坯连铸是在弧形连铸机上浇注成型的,弧形圆坯连铸过程采用如下工艺中的一种或多种:
5.(1)弧形连铸机采用冶金智能凝固模型实时计算铸流凝固曲线,包括铸坯不同时段的表面温度、内部温度曲线,据此用于设置拉矫机的拉矫力,拉矫力的设置应遵循足够将
铸坯向前拉出且适度矫直,同时又能低于该区间铸坯温度对应的热模拟得出的热强度而不至于因拉矫力过大而将铸坯矫裂。
6.(2)结晶器液面控制采用放射性元素监控或涡流监控技术,以满足铸坯更低拉速和更低振动频率的需要,以此实现结晶器的液面波动范围控制在
±
(1~10)mm,相适应的拉速为0.01~0.15m/min的超低拉速。
7.(3)弧形连铸机采用多段电磁搅拌相结合:对结晶器内的钢水实施电磁搅拌,对连铸机二冷段的铸流实施电磁搅拌,对凝固末端铸坯的液芯实施电磁搅拌。这种搅拌组合相对传统的结晶器+末端搅拌组合更有利于大截面铸坯温度、成分、组织的均匀。
8.(4)连铸过程采用动态轻压下和重压下相结合的压下技术,拉矫机通过带有msr(机械轻压下)的模块,结合冶金智能凝固模型,根据模拟计算的铸坯温度来设计铸坯液芯凝固末端前沿拉矫机压下方式:铸坯液芯凝固末端高浓度液相挤压出去时实施重压下,钢液回流补缩时实施轻压下。使液芯高浓度溶质挤压到凝固更前沿进行均匀中和,有利于成分组织的均匀,减少偏析,同时又能让中和匀质的液相回流补缩,有利于组织的致密,从而改善超大断面铸坯中心偏析、疏松,提高铸坯均匀性和致密度,作出参考,压下量一般设计在2-3mm范围内,。
9.(5)采用一种通道式铸流加热方式,对铸坯表面进行均匀加热,让铸坯矫直前或开始矫直时温度保持在热脆性温度以上,而处于热塑性区,避免热脆性区矫直裂纹的产生,从而提高铸坯中心和表面质量。例如,某钢种热脆性区间在650℃-750℃,而根据现有拉速、铸坯温度预测过拉矫机时的温度正好落在该区间,那就要启动铸坯加热装置,让铸坯通过一加热通道将温度升到750℃以上,避开热脆性区,进入热塑性区矫直时就不易矫裂。
10.优选地,所述弧形连铸机的半径r=17m-20m,与之匹配的结晶器设计:横断面为圆形,直径为φ1100mm~φ1380mm,结晶器为倒锥形,锥度小于5
°
,高度或长度为500mm~800mm,适合更大弧形半径铸机,更有利于铸坯的振动滑脱。
11.具体地,工艺(1)和工艺(5)所述的冶金智能凝固模型基于如下条件或假设进行计算:
12.(1)沿着拉坯方向的传热很小,忽略不计,故温度只在二维方向即拉坯截面传导;
13.(2)钢的热物性参数只与温度有关,与位置无关;
14.(3)铸坯的物理特性是各向同性;
15.(4)在二冷区的同一冷却段为均匀冷却;
16.(5)铸坯表面的辐射传热、铸坯与托辊的接触传热以及二冷水的冷却传热,均用综合传热系数来计算;
17.(6)结晶器振动对于铸坯凝固传热的影响忽略不计。
18.(一)、基本方程:
19.取圆坯1/4横截面为研究对象,则凝固传热的二维非稳态传热方程为:
[0020][0021]
其中,ρ为钢水密度,kg/m3;c
p
为热容,j/(kg
·
℃);λ为导热系数,w/(m
·
℃);qv为内热源,j/(m3·
s);t为温度,℃;t为时间,s。
[0022]
(二)、初始条件满足:
[0023]
t(x,y)|
t=0
=t0ꢀꢀꢀꢀꢀꢀꢀꢀꢀꢀ
(2)
[0024]
其中t0为浇注温度,℃。
[0025]
(三)、边界条件:
[0026]
(1)结晶器内
[0027][0028][0029]
其中,l为距弯月面长度,m;q
结
为结晶器热流密度,w/m2。
[0030]
(2)二冷区
[0031]
q=h(t
b-tw)
ꢀꢀꢀꢀꢀꢀꢀꢀꢀꢀꢀꢀꢀꢀꢀꢀꢀꢀꢀꢀꢀꢀꢀꢀꢀꢀ
(5)
[0032]
其中,h为综合传热系数,tb为铸坯表面温度,℃;tw为环境温度,℃。
[0033]
二冷区一区和二区冷却系数为:
[0034]
h1=0.40w
0.289
ꢀꢀꢀꢀꢀꢀꢀꢀꢀꢀꢀ
(6)
[0035]
h2=0.31w
0.391
ꢀꢀꢀꢀꢀꢀꢀꢀꢀꢀꢀꢀꢀ
(7)
[0036]
其中,h1、h2分别为一区和二区的传热系数,kw/(m2·
℃);w为水流密度,l/(m2·
s)。
[0037]
(3)空冷区
[0038]
空冷区为空气散热,边界条件为:
[0039]
q=εσ[(tb+273)
4-(ta+273)4]
ꢀꢀꢀꢀꢀꢀꢀꢀꢀꢀꢀꢀꢀꢀꢀꢀꢀꢀꢀ
(8)
[0040]
其中,ε为辐射系数,钢铁为0.8;σ为玻尔兹曼常数,5.67
×
108;ta为空气温度,℃。
[0041]
总之,利用该模型用于指导拉矫力的设置,既能够足够将铸坯拉出且适度矫直,
[0042]
同时又能低于该区间铸坯温度对应的热强度(热模拟得出),不至于将铸坯矫裂。
[0043]
具体地,弧形圆坯连铸过程中,结晶器与二冷段总的冷却采用比水量0.01~0.3l/kg,二冷段采用气雾冷却的方式,能起到均匀温和的冷却效果,相对水直接喷淋冷却不易产生应力裂纹。
[0044]
具体地,工艺(2)中,放射性元素监控技术是利用放射性元素的放射性通过钢液和渣液的强度不一从而感知结晶器中钢水液面的位置,然后将信号传到计算机形成结晶器液面的波动曲线,根据曲线及时调整结晶器的液面高度);涡流监控技术是利用涡流传感器的电磁信号在钢水表面产生涡电流,涡电流的大小随钢水液面到传感器的距离而变化,该变化信号传递到监控系统,根据信号及时调整结晶器的液面高度,从而达到控制结晶器液面波动的目的。
[0045]
具体地,工艺(3)中,结晶器电磁搅拌:频率为0.5~10hz、电流为0~350a,二冷段电磁搅拌:频率为0.5~10hz、电流为0~350a,末端电磁搅拌:频率为1~15hz、电流为0~
500a。多段搅拌不但有利于夹杂物上浮、也有利于组织及成分的均匀,也增加低倍组织致密性。与≤φ1000mm连铸圆坯的组合电磁搅拌技术相比,本技术电磁搅拌技术增加了二冷段的搅拌,而且搅拌能力更强,可调范围更宽。
[0046]
优选地,工艺(5)是通过可燃气与空气进行燃烧,以此实现对铸坯表面的加热。
[0047]
进一步地,弧形圆坯连铸过程进一步采用如下工艺中的一种或多种:
[0048]
(6)大包下渣检测:大包浇注后期,由于钢水顶部渣层离大包水口越来越近,偶尔会有渣子随钢流卷入到中间包影响铸流纯净度,通过在大包水口附近安装传感器,感知钢水液面覆盖的渣层的渣子偶尔随钢流卷入到中间包,然后将此信号传递到监控系统,操作人员就可通过水口闸门的开启度进行控制,确保进入中间包的钢水少渣或无渣,达到提高钢水纯净度的目的。
[0049]
(7)中间包连续测温:在线随时感知中间包钢水温度,也就随时感知浇注钢水的过热度,然后通过浇注速度进行调控,同时可预警下一炉的温度合理控制,确保浇注质量的平稳,因过热度过高或过低都会影响钢坯质量或生产的顺行。
[0050]
(8)全保护浇铸:全保护浇注是让整个连铸过程钢水始终与空气隔绝,减少或避免钢水的二次氧化和吸气。且优选采用自动全保护浇铸,计算机自动化控制的浇铸技术能避免人为因素的波动,生产更平稳,过程参数易监控。
[0051]
再来,由于铸坯截面积越大,在由弧形矫直过程中所受到的变形抗力越大,传统的单辊多点矫直很难平稳有效,甚至出现时而矫不直,时而矫裂现象,为了获得稳定和更高强度的拉矫力,拉矫机采用多组密排矫直方式,让连续布置的拉矫机两个以上矫直机构成一组、同框架前后密集排布。相对单辊多点矫直本技术的矫直是单台矫直机的能力变强,矫直辊变多,而且每台矫直机之间间距小,整体效果就更接近连续矫直,相对间断的多点矫直效果好得多。
[0052]
具体地,所述钢水冶炼采用先后进行的电炉或转炉冶炼、炉外精炼、真空脱气处理。
[0053]
由于大直径连铸圆坯的截面越大,因此优选火焰切割方式,火焰切割的火焰长度越长、威力越大,同时切割产生的氧化铁也越多,本技术所述的切割是采用氧炔火焰切割,切割过程中添加铁粉,利用铁粉的氧化生热提高切割效率,并进一步使用高压气流在切割过程中辅助吹渣,保证铸坯质量。
[0054]
优选地,所述控制冷却,是将切割后的一段段圆坯转移到地坑或堆垛后用保护罩保护起来或转移到炉膛进行冷却,避免冷却过快产生应力裂纹等表面缺陷。
[0055]
优选地,所述精整,是将冷却好的铸坯进行表面、端部及尺寸的检查,对缺陷进行清理,使其符合生产标准。
[0056]
基于上述连铸方法,能够适用于生产φ1050mm~φ1350mm规格的连铸圆坯。
[0057]
与现有技术相比,本发明的优点在于:
[0058]
(1)钢材纯净度大大提高,锻后用φ2mm当量的高频探伤合格率达99.5%,比传统模铸产品同工艺同级别探伤合格率提高10%以上。
[0059]
(2)与传统模铸单炉生产相比,可实现多炉连续生产,而且计算机自动控制,生产效率高,成坯率高,节材降耗10%以上,更好更充分满足市场快速增长的需要。
[0060]
(3)采用弧形连铸浇注成圆柱形钢坯,相对模铸的锥形钢更接近于最终锻件毛坯
的形状,锻造工艺更省,效率更高,锻造成本也更低。
[0061]
(4)与≤φ1000mm连铸圆坯相比,搅拌技术、矫直技术更先进,能满足更大直径锻件使用,品种更大型化、质量更高端化。同时推动世界连铸技术向更高水平发展。
具体实施方式
[0062]
以下结合实施例对本发明作进一步详细描述,所述实施例是示例性的,旨在用于解释本发明,而不能理解为对本发明的限制。
[0063]
一种φ1050mm~φ1350mm高纯致密特殊钢连铸圆坯生产工艺工艺流程为:钢水经转炉或电炉冶炼
→
炉外精炼
→
真空脱气
→
(r17m~r20m)弧形圆坯连铸机浇注
→
高效火焰切割
→
控制冷却
→
精整
→
检验判定。
[0064]
采用创新弧形连铸机浇注成形,弧形连铸机半径r在17m~20m之间,结晶器断面为圆形,直径为φ1100mm~φ1380mm,倒锥形,结晶器长度为500mm~800mm,适合更大弧形半径铸机,更有利于铸坯的振动滑脱。
[0065]
结晶器液面控制采用更精确的放射性元素监控或涡流监控技术,结晶器液面波动控制在
±
(1~10)mm,拉速为0.01~0.15m/min,以满足超大截面铸坯更低拉速和更低振动频率的需要。
[0066]
弧形连铸机采用新型多段电磁搅拌技术相结合:结晶器电磁搅拌:频率为(0.5-10)hz、电流为(0-350)a+二冷段电磁搅拌:频率为(0.5-10)hz、电流为(0-350)a+末端电磁搅拌:频率为(0.5-10)hz、电流为(0-350)a。
[0067]
弧形连铸机的拉矫机采用多组单台双辊拉矫机,矫直采用多组密排矫直方式。由于铸坯截面积越大,拉矫力也越大,需要对拉矫机的排列方式重新设计改善,以提高单台拉矫机的拉矫力,同时获得更接近连续矫直的作用。
[0068]
弧形连铸机采用轻压下技术,利用多组多辊拉矫机分级压下,改善铸坯中心区的疏松与偏析。
[0069]
弧形连铸机采用铸坯加热技术,利用天然气和空气燃烧的加热技术,对铸流均匀加热,确保不同钢种铸坯的矫直温度在合理区间,避免热脆性区矫直裂纹的产生。
[0070]
弧形连铸机的铸坯切割采用氧炔火焰切割辅助铁粉添加及高压吹渣技术,这样更有利于超大截面超厚度的顺利切割与排渣。
[0071]
具体实施结果参见表1
[0072]
表1 φ1050mm~φ1350mm连铸圆坯
[0073][0074][0075]
实施例1、2、3都是按工艺路径“转炉或电炉冶炼
→
炉外精炼
→
真空脱气
→
弧形圆坯连铸
→
火焰切割
→
控制冷却
→
精整
→
检验判定”生产出三炉号的φ1200mmq345或s355nl钢连铸圆坯,然后供下游锻造用户锻造成风力发电机组用直径5000mm塔筒法兰毛坯,整体热处理后再取样、车加工、检测;国内传统4、5是江阴一锻造厂采购张家港及常州二家不同模铸厂的q345e模铸锭,按本发明案例同样的加工方法进行锻造、热处理,然后取样、车加工、检测;从检测结果看,实施例产品与传统产品的机械性能差别不大,都满足材料标准要求,且有较大富余,但从纯净度及ut结果来看,实施例产品优于传统产品,而且成坯率提高了10%~13%,实现了多炉连续自动化高效率的生产目的,方法是非常成功的。