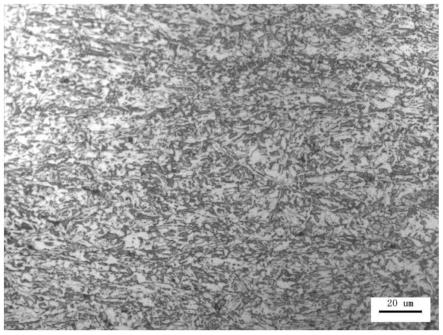
一种460mpa级高韧性特厚板及其制造方法
技术领域
1.本发明涉及钢板生产技术领域,尤其涉及一种460mpa级高韧性特厚板及其制造方法。
背景技术:2.钢板经正火后可以获得较高的综合力学性能和较好的机加工性能,是提高钢板组织均匀性、韧性的重要热处理手段。正火钢板广泛应用于压力容器、高层建筑、桥梁、工程机械等领域,特别是一些风电、容器项目,在项目设计时就强制要求使用正火钢板。
3.常规正火采用空冷方式,因冷却速度慢会导致相变温度高,虽然可以得到细化的珠光体组织,使冲击功和延伸率得到提高,但提高韧性的同时,铁素体晶粒仍会长大,导致钢板的强度有所降低;铌微合金化钢正火后因铌的碳氮化物长大,其沉淀强化效果降低,因此钢板经正火后强度会有较大幅度降低,特别是控轧控冷钢板常会因强度损失过大而产生不合格品。
4.为防止钢板正火后强度大幅降低,国内各钢厂先后开发了正火控冷工艺(ncc):钢板正火后采用水冷手段,通过控制冷却速度和终冷温度来降低钢板的相变温度,抑制微合金碳氮化物长大,同时通过降低相变温度降低原子扩散能力,得到珠光体片层间距较小的细化珠光体组织,使钢板应力、硬度增大,强度提高,伸长率和冲击韧性大幅提高。其强度指标虽然同正火空冷相比得到显著改善,但与tmcp钢板强度指标相比仍然有较大差距。tmcp态交货钢板虽然省去了热处理环节,但为了保证低温韧性添加了较多的合金,且容易因组织不均匀而造成性能波动,生产难度较大,并且不能真正达到节能降本的目的。
5.公告号为cn101343685b的中国发明专利公开了“一种屈服强度为420mpa级高强度建筑用钢板的热处理方法”,连铸坯经过控轧控冷后得到45mm厚钢板,加热到正火的温度890~950℃,保温10~30分钟,保温后以2~6℃/s的速度降温,终冷温度为600~750℃;矫直;在冷床空冷,获得高性能建筑用钢板;但其要求nb含量达到0.03%以上才满足相应的力学性能,其目的是通过高nb来扩大未再结晶区温度,提高精轧终轧温度的目的。此方法利于控制钢板板形,但终轧温度提高以后,会减弱超快冷效果,不利于钢板心部快速通过奥氏体区到达相变区,从而不利于钢板心部nb在相变过程中的析出,因此钢板心部强度较低。
6.公告号为cn104962814b的中国发明专利公开了“一种正火高强韧性150mm特厚板及其生产方法”,采用轧后堆垛缓冷的控冷方式,由于缓冷过程中形变储能大量释放,导致位错密度降低,减少了铁素体的形核质点,并且冷速较低导致相变点温度较高,会造成铁素体晶粒长大,减小了轧态钢板强度富余量,不利于提升钢板综合力学性能。
7.公告号为cn102115806b的中国发明专利公开了“一种提高特厚板低温韧性的热处理工艺”,采用亚温正火,同时冷却方式采用空冷,其微观组织一般会含有20%左右的未溶铁素体,会造成正火后组织不均匀,导致应力集中,主要是对冲击韧性会产生波动;同时对于厚规格钢板,空冷冷速慢,奥氏体向铁素体转变时铁素体形核率低,导致部分铁素体晶粒粗大,对钢板强度造成波动。
8.公告号为cn102061373b的中国发明专利公开了“一种提高高强度特厚板力学性能的热处理工艺”,在特厚板的正火过程中增加水冷工序,用水冷代替空冷进行正火,但其采用淬火水槽来进行控冷,钢板在水中很难准确测定目标出水温度,实际操作难度大,并且对于大部分中厚板产线,受场地空间限制很难配备大型淬火槽。
9.公开号为cn105154631a的中国专利申请公开了“一种提高厚度≥50mm规格正火钢板强度的淬火机加速冷却方法”,正火钢板出淬火炉后随淬火机辊道进入淬火机开始水冷,但其主要涉及淬火机设备参数,包括低压段开口度、上下开口度比例、辊道速度以及水量控制角度等,以保证正火控冷后温度的精准命中,没有从工艺角度研究正火温度、保温时间、冷速等对钢板性能的影响。
10.与上述技术方案不同,本发明在gb/t 1591-2018标准中q460钢成分基础上,通过降低碳含量、结合“二阶段控轧、轧后三阶段超快冷以及离线正火弱水冷”工艺,实现460mpa级高韧性特厚板高强度及低温韧性的匹配。
技术实现要素:11.本发明提供了一种460mpa级高韧性特厚板及其制造方法,优化了化学成分及生产工艺,在不增加合金元素前提下,通过二阶段控轧、轧后三阶段超快冷以及离线正火弱水冷等工艺,得到以板条贝氏体为主的组织,占比大于70%,晶内分布大量小角度晶界和大角度晶界,上述晶界有利于阻止裂纹扩展,从而得到优异的低温韧性;成品钢板具有大厚度、高强度、高低温韧性、厚度方向组织及性能均匀、合金成本低等特点。
12.为了达到上述目的,本发明采用以下技术方案实现:
13.一种460mpa级高韧性特厚板,钢板化学成分按重量百分比计为c:0.04%~0.06%,si:0.25%~0.45%,mn:1.50%~1.70%,nb:0.02%~0.03%,ti:0.01%~0.02%,p<0.020%,s<0.005%,其余为fe及不可避免的夹杂;钢板组织以板条贝氏体为主,体积比大于70%;晶内分布位向差为3~15
°
的小角度晶界及位向差大于15
°
的大角度晶界。
14.成品钢板的力学性能为:
15.屈服强度:钢板厚度1/2处460~490mpa,钢板厚度1/4处500~540mpa,钢板近表面处520~560mpa;
16.抗拉强度:钢板厚度1/2处640~670mpa,钢板厚度1/4处660~700mpa,钢板近表面处650~690mpa;
[0017]-40℃冲击功:钢板厚度1/2处280~320j,钢板厚度1/4处325~360j,钢板近表面处340~370j。
[0018]
成品钢板65≤厚度≤100mm。
[0019]
一种460mpa级高韧性特厚板的制造方法,包括如下步骤:
[0020]
1)钢坯加热;均热温度1160~1200℃,总在炉时间4~6小时;
[0021]
2)采用二阶段控轧;再结晶区开轧温度为1100~1200℃,未再结晶区开轧温度为880~920℃,终轧温度为780~820℃;
[0022]
3)轧后超快冷;以35~40℃/s的冷速冷至600~640℃,随后空冷20~25s,再以15~20℃/s的冷速冷至300~340℃;
[0023]
4)热轧态钢板进行离线正火+控冷热处理;正火温度900~920℃,净保温时间为10~20min;空冷至600~640℃;
[0024]
5)采用弱水冷方式进行冷却,终冷温度380~420℃,冷速8~12℃/s。
[0025]
所述钢坯采用连铸钢坯或模铸开坯钢坯,钢坯厚度
÷
钢板终轧厚度≥3.5。
[0026]
再结晶区轧制后,待温厚度为成品钢板厚度的2~2.5倍。
[0027]
与现有技术相比,本发明的有益效果是:
[0028]
1)通过降低碳含量,确保不会由于贝氏体相变不完全而形成过多的马氏体,同时保证碳含量足以与微合金元素反应;而且在此碳含量范围内使得马氏体体积分数减少,改善了钢板的韧性且不会造成强度过大损失;
[0029]
2)结合轧后三阶段冷却工艺,使轧后钢板快速冷却至相变温度,通过空冷过程中得到针状铁素体,再在随后的快冷过程中得到强度更高的粒状贝氏体和m/a岛;
[0030]
3)正火后二阶段控冷,首先空冷至600~640℃粒状贝氏体转变区,再次形成的粒状贝氏体是由马氏体板条束为主的团絮状m/a岛及少量孤立分布在多边形铁素体晶界上的块状m/a岛组成,相当于增加了基体中的界面,可使晶粒细化;在板条晶界上析出的碳化物发生球化,因此板条束铁素体晶界上的碳化物不连续,裂纹不易扩展,使钢板具有高强度兼具稳定的高冲击韧性;
[0031]
4)最终成品钢板力学性能为屈服强度:钢板厚度1/2处460~490mpa,钢板厚度1/4处500~540mpa,钢板近表面处520~560mpa;抗拉强度:钢板厚度1/2处640~670mpa,钢板厚度1/4处660~700mpa,钢板近表面处650~690mpa;-40℃冲击功:钢板厚度1/2处280~320j,钢板厚度1/4处325~360j,钢板近表面处340~370j。
附图说明
[0032]
图1是本发明实施例1正火态特厚板的金相组织照片。
[0033]
图2是本发明实施例2正火态特厚板的金相组织照片。
具体实施方式
[0034]
本发明所述一种460mpa级高韧性特厚板,钢板化学成分按重量百分比计为c:0.04%~0.06%,si:0.25%~0.45%,mn:1.50%~1.70%,nb:0.02%~0.03%,ti:0.01%~0.02%,p<0.020%,s<0.005%,其余为fe及不可避免的夹杂;钢板组织以板条贝氏体为主,体积比大于70%;晶内分布位向差为3~15
°
的小角度晶界及位向差大于15
°
的大角度晶界。
[0035]
成品钢板的力学性能为:
[0036]
屈服强度:钢板厚度1/2处460~490mpa,钢板厚度1/4处500~540mpa,钢板近表面处520~560mpa;
[0037]
抗拉强度:钢板厚度1/2处640~670mpa,钢板厚度1/4处660~700mpa,钢板近表面处650~690mpa;
[0038]-40℃冲击功:钢板厚度1/2处280~320j,钢板厚度1/4处325~360j,钢板近表面处340~370j。
[0039]
成品钢板65≤厚度≤100mm。
[0040]
一种460mpa级高韧性特厚板的制造方法,包括如下步骤:
[0041]
1)钢坯加热;均热温度1160~1200℃,总在炉时间4~6小时;
[0042]
2)采用二阶段控轧;再结晶区开轧温度为1100~1200℃,未再结晶区开轧温度为880~920℃,终轧温度为780~820℃;
[0043]
3)轧后超快冷;以35~40℃/s的冷速冷至600~640℃,随后空冷20~25s,再以15~20℃/s的冷速冷至300~340℃;
[0044]
4)热轧态钢板进行离线正火+控冷热处理;正火温度900~920℃,净保温时间为10~20min;空冷至600~640℃;
[0045]
5)采用弱水冷方式进行冷却,终冷温度380~420℃,冷速8~12℃/s。
[0046]
所述钢坯采用连铸钢坯或模铸开坯钢坯,钢坯厚度
÷
钢板终轧厚度≥3.5。
[0047]
再结晶区轧制后,待温厚度为成品钢板厚度的2~2.5倍。
[0048]
本发明所述一种460mpa级高韧性特厚板的化学成分设计原理如下:
[0049]
1、碳的主要作用是在正火后控冷过程中形成大量的(nb,ti)(c,n),起析出强化的作用,另外一部分碳用于固溶强化,能够有效减少强度性能损失;本发明将c含量控制在0.04%~0.06%,目的是确保不会由于贝氏体相变不完全而形成过多的马氏体,同时该碳含量足以与nb反应生成(nb,ti)(c,n),由于碳含量控制较低,使得马氏体体积分数减少,可以改善钢材韧性,而不会造成强度损失。
[0050]
2、硅的作用是降低碳的石墨化倾向,通过固溶强化起到一定的提高强度的作用,但硅含量不宜过高,否则会加剧杂质元素在晶界的偏聚,降低正火后韧性。因此本发明控制si含量为0.25%~0.45%。
[0051]
3、锰能够提高正火态钢珠光体强度,还可以提高铌、钒在钢中的溶解度,但锰含量偏高会促使晶粒有长大倾向;因此,本发明控制mn含量为1.50%~1.70%。
[0052]
4、铌的作用主要是在铁素体相变过程中发生沉淀析出,同时通过晶粒细化提高强度,但铌含量偏高会影响再结晶温度,抑制奥氏体再结晶,使得未再结晶终轧温度较高,控冷时容易导致相变析出形成多边形铁素体,因此本发明将铌含量控制在0.02%~0.03%。
[0053]
5、钛主要与铌共同作用形成(nb,ti)(c,n),正火温度下阻碍位错移动,但过多钛会导致(nb,ti)(c,n)聚合粗化,正火温度下起不到抑制奥氏体晶粒长大的作用;因此本发明控制钛含量为0.01%~0.02%。
[0054]
本发明所述一种460mpa级高韧性特厚板的工艺路线设计原理如下:
[0055]
1、钢坯厚度;当总压缩比小于3.5时,单纯提高粗轧或精轧阶段的总压缩比、单道次压下量很难改善钢板的低温韧性,当总压缩比大于3.5时,变形分配到粗轧或精轧阶段都可以使低温韧性大幅提升;因此本发明限定钢坯厚度
÷
钢板终轧厚度≥3.5。
[0056]
2、钢坯均热温度;当钢坯均热温度超过1200℃时,nb(c,n)粒子会快速回溶,粗晶区晶粒迅速长大,为确保轧态组织钢板有较高的强度富余量,确保原始晶粒细化,故采用较低的钢坯加热温度,将均热温度控制在1160~1200℃,加热时间4~6h。
[0057]
3、二阶段控轧;传统工艺采用奥氏体再结晶区控轧,终轧温度较高,奥氏体晶粒粗大,由于遗传效应导致铁素体晶粒亦粗大;本发明采用二阶段控轧工艺,奥氏体组织在再结晶区变形再结晶使晶粒细化,未再结晶区变形时,奥氏体沿轧制方向被压扁拉长,在晶粒内产生变形带,使铁素体的形核点位增加,促进了铁素体晶粒的细化;
[0058]
控制再结晶区轧后待温厚度,目的是减少精轧阶段变形量,从而减少低温形变对厚度方向组织不均匀的影响。
[0059]
考虑屈服强度会随着开轧温度升高、终轧温度降低、终冷温度降低、冷速的增大而升高,延伸率随开轧温度降低、终轧温度降低、终冷温度降低、冷却速度的增大而升高,随终冷温度的降低,粒状贝氏体、针状铁素体明显增加,并且m/a岛更加分散。最终确定再结晶区开轧温度为1100~1200℃,未再结晶区开轧温度为880~920℃,终轧温度为780~820℃。
[0060]
4、轧后三阶段超快冷;终轧结束后先以35~40℃/s的冷速快速冷却,在这一冷速下基本不产生先共析铁素体,并且冷至600~640℃范围内进入贝氏体相变开始点,继而可在较大的冷却温度范围内不发生相变,便于空冷时驰豫过程的进行,同时可确保不同厚度的钢板或同一块钢板不同部位均可得到相似的贝氏体复合组织。驰豫过程中温转变(600~640℃),空冷20~25s,产物主要为板条贝氏体及少量粒状贝氏体或针状铁素体,再经过15~20℃/s冷速冷至300~340℃,得到细化的贝氏体板条束组织,轧态下强度富余量大为提升。
[0061]
5、正火后弱水冷;正火后先空冷,其目的是使沿晶界析出的碳化物有充足的时间进行扩散,达到均匀状态;空冷至600~640℃,钢板在此温度下进入贝氏体转变温度区域;再以8~12℃/s冷速冷却至380~420℃,目的是充分形成粒状贝氏体,其由马氏体板条束为主的团絮状m/a岛及少量孤立分布在多边形铁素体晶界上的块状m/a岛组成;
[0062]
采取以上措施可极大地提高钢板低温韧性并且强度保持不变。
[0063]
以下实施例在以本发明技术方案为前提下进行实施,给出了详细的实施方式和具体的操作过程,但本发明的保护范围不限于下述的实施例。
[0064]
【实施例】
[0065]
各实施例的钢坯化学成分见表1,钢坯加热工艺参数见表2,钢坯控轧控冷工艺参数见表3,钢板正火控冷工艺参数见表4,成品钢板的规格及性能见表5,成品钢板规格及性能(钢板厚度1/2处)见表6,成品钢板规格及性能(钢板近表面)见表7。
[0066]
实施例1、实施例2的正火态特厚板的金相组织照片如图1、图2所示。
[0067]
表1各实施例钢坯化学成分(wt%)
[0068]
实施例csimnpsnbti10.040.331.620.0170.0020.0260.01420.050.351.690.0150.0020.0220.01930.040.301.570.0150.0030.0270.01740.060.341.610.0160.0030.0250.01850.050.321.620.0160.0030.0240.01760.050.361.680.0150.0030.0250.016
[0069]
表2各实施例钢坯加热工艺参数
[0070][0071]
表3各实施例钢坯控轧控冷工艺参数
[0072][0073]
表4各实施例钢板正火控冷工艺参数
[0074][0075]
表5各实施例成品钢板规格及性能(钢板厚度1/4处)
[0076][0077]
表6各实施例成品钢板规格及性能(钢板厚度1/2处)
[0078][0079]
表7各实施例成品钢板规格及性能(钢板近表面)
[0080][0081]
以上所述,仅为本发明较佳的具体实施方式,但本发明的保护范围并不局限于此,任何熟悉本技术领域的技术人员在本发明揭露的技术范围内,根据本发明的技术方案及其发明构思加以等同替换或改变,都应涵盖在本发明的保护范围之内。