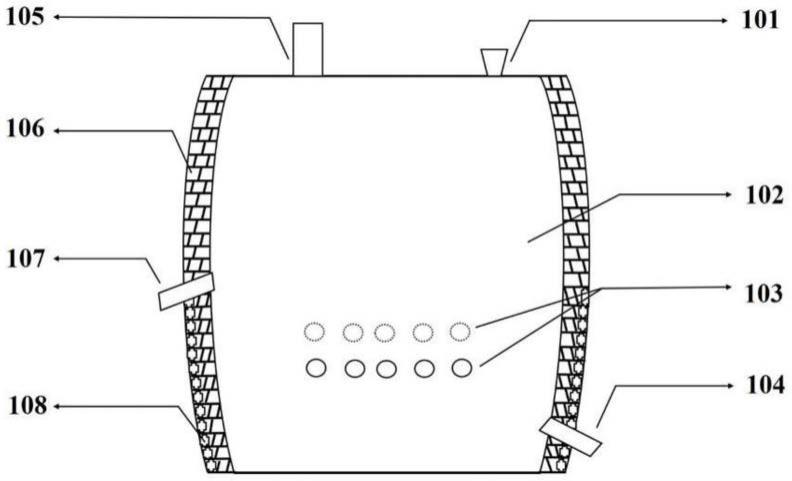
一种侧吹熔炼回收冶炼废弃渣中铅锌铜的方法
一、技术领域:
1.本发明属于铜冶炼生产技术领域,具体涉及一种侧吹熔炼回收冶炼废弃渣中铅锌铜的方法。
二、
背景技术:2.在铜冶炼过程中会产生大量的铜冶炼渣,主要包括铜精矿熔炼过程产生的熔炼渣、铜锍吹炼过程产生的吹炼渣以及粗铜精炼过程产生的精炼渣,该类废料中含有pb、zn、cu等有价金属。其中,熔炼渣中pb、zn、cu的含量分别为0.30~2.0%、3.0~8.0%、1.0~5.0%;吹炼渣中pb、zn、cu的含量分别为4~12%、1.0~4.0%、5~15%;精炼渣中pb、zn、cu的含量分别为10~20%、0.5~1.0%、18~30%。
3.目前,冶炼行业大都采用渣选矿的方式回收熔炼渣中的铜,但渣选工艺存在部分缺陷:工艺流程长、占地面积大和投资高;无法回收渣中锌等有价金属,损失了大量的潜在价值;噪声污染与作业环境对作业人员身心健康存在潜在危害等。少数企业采用传统电炉贫化工艺降低尾渣中的含铜量,但由于其工艺局限性,存在尾渣含铜较高的弊端。现有处置技术均未考虑铅锌等其他金属的回收利用。
4.发明专利cn 106367605 b公开了一种侧吹贫化铜冶炼渣的生产方法,该方法采用侧吹贫化铜冶炼渣的生产方法降低冶炼渣中的铜,从而回收金属铜。但该方法未考虑铅锌的回收利用,造成一定的资源损失。
5.发明专利cn 112322902 b公开了一种铜冶炼渣的资源化回收方法,该方法介绍了一种铜冶炼渣的资源化回收方法,有效地回收铜熔炼渣和铜吹炼渣中的铅锌铜等有价元素,但该技术流程较长,需要两台还原炉才能实现,同时需要加入石英对渣型进行调整。
三、
技术实现要素:6.本发明要解决的技术问题是:为了克服上述现有铜冶炼渣回收处理方法中存在的技术问题,本发明提供一种侧吹熔炼回收冶炼废弃渣中铅锌铜的方法。本发明方法操作简便、流程短,并且能够从铜冶炼渣中有效回收多种有价金属。
7.为了解决上述问题,本发明采取的技术方案是:
8.本发明提供一种侧吹熔炼回收冶炼废弃渣中铅锌铜的方法,所述回收方法包括以下步骤:
9.a、以铜熔炼渣、吹炼渣和精炼渣中至少两种为原料,粉煤或还原煤为助剂;
10.b、将铜熔炼渣、吹炼渣和精炼渣中至少两种进行混合,混合后加入侧吹炉,并加入粉煤或还原煤,然后经侧吹炉侧吹口将燃料通入炉内进行加热、搅拌,当侧吹炉内熔池深度达到1000~2000mm、温度为1200~1400℃时进行熔炼反应,反应时间为3~4.5h;
11.c、熔炼反应后,产生的铜锍和尾渣分别经侧吹炉铜锍口和放渣口排出;产生的烟气由烟道口排出,经收尘系统回收烟尘。
12.根据上述的侧吹熔炼回收冶炼废弃渣中铅锌铜的方法,步骤a所述铜熔炼渣中的
主要成分及其重量百分含量分别为pb 0.3~2.0%、zn 3.0~8.0%、cu 1.0~5.0%、fe 36~40%和sio
2 20~22%;所述吹炼渣中的主要成分及其重量百分含量分别为pb 4~12%、zn 1.0~4.0%、cu 5~15%、fe 15~20%和sio
2 15~17%;所述精炼渣中的主要成分及其重量百分含量分别为pb 10~20%、zn 0.5~1.0%、cu 18~30%、fe 3~5%和sio
2 30~50%。
13.根据上述的侧吹熔炼回收冶炼废弃渣中铅锌铜的方法,步骤a中所述原料为铜熔炼渣和吹炼渣时,二者之间的混合质量配比为0.25~3.5:1;所述原料为铜熔炼渣和精炼渣时,二者之间的混合质量配比为4~24:1;所述原料为铜熔炼渣、吹炼渣和精炼渣时,三者之间的混合质量配比为4.25~27.5:1:1;所述原料混合后所得混合料中,铁硅之间的质量比为1.2~1.8:1。
14.根据上述的侧吹熔炼回收冶炼废弃渣中铅锌铜的方法,步骤a中所述粉煤或还原煤的加入量为原料总重量的2~6%。
15.根据上述的侧吹熔炼回收冶炼废弃渣中铅锌铜的方法,步骤a中所述还原煤中含碳量>60%,粒径为4~10mm;所述粉煤中含碳量>50%,粒径<100目。
16.根据上述的侧吹熔炼回收冶炼废弃渣中铅锌铜的方法,步骤b中所述燃料为压缩空气或富氧空气,所述燃料通入熔炼炉时控制压力为0.1~0.4mpa。
17.根据上述的侧吹熔炼回收冶炼废弃渣中铅锌铜的方法,步骤b中所述侧吹炉为竖直炉,由进料口、炉缸、侧吹口、铜锍口、烟道口、耐火材料和放渣口构成,外部设置有铜水套;进料口和烟道口位于炉体顶部;放渣口布置在炉体中部,放渣口距炉底1450~1500mm;侧吹口布置在炉体中部,与炉底距离为700~920mm;铜锍口布置在炉体下部,距炉底400~600mm。
18.根据上述的侧吹熔炼回收冶炼废弃渣中铅锌铜的方法,步骤c中所得铜锍的品位为30~60%;所得尾渣中含cu 0.3~0.4%、pb 0.1~0.2%、zn 0.7~1.1%。
19.根据上述的侧吹熔炼回收冶炼废弃渣中铅锌铜的方法,步骤c中所述回收的烟尘为富锌烟尘,富锌烟尘中含zn 60~70%。
20.本发明技术方案中,采用的铜熔炼渣中fe含量较高,铁硅比较高;吹炼渣中铁硅适中;精炼渣中si含量较高,铁硅比较低,将三种渣料进行混合,搭配出合适的铁硅比,通过协同作用,有效处理铜冶炼渣。其反应原理如下:
21.fe3o4+c=3feo+co
22.2feo+sio2=fe2sio423.feo+c=fe+co
24.zno+c=zn+co
25.pbo+c=pb+co
26.cu2o+c=2cu+co
27.zn2sio4+2c=2co+2zn+sio228.znfe2o4+c=co+zn+2feo
29.pbsio3+c=co+pb+sio230.本发明的积极有益效果:
31.1、本发明技术方案将铜熔炼渣、吹炼渣和精炼渣进行搭配使用,调至合适的铁硅
6.8%,fe 36.0%和sio
2 22.0%;吹炼渣中的化学成分及其重量百分含量分别为cu 8.5%、pb 10.5%、zn 3.0%、fe 20.0%和sio
2 15.0%;
51.b、将铜熔炼渣4.0t和吹炼渣5.0t进行混合,混合后通过加料口加入侧吹炉中,同时加入439kg粉煤,然后经侧吹炉侧吹口设有的喷枪将燃料富氧空气通入炉内熔池进行加热、搅拌,富氧空气的喷吹压力为0.1~0.4mpa,当侧吹炉内熔池深度达到1500~2000mm、温度为1320~1350℃时进行熔炼反应,反应时间为4.2h;
52.c、熔炼反应后,产生的铜锍和尾渣分别经侧吹炉铜锍口和放渣口排出;产生的烟气由烟道口排出,经收尘系统回收烟尘。
53.本实施例在放渣口和铜锍口取样检测,经化验检测,所得尾渣中含cu 0.39%、pb 0.20%、zn 1.05%;铜锍口得到的冰铜品位为40%;回收的烟尘中含zn 65.7%。
54.实施例3:
55.参见附图1,本发明侧吹熔炼回收冶炼废弃渣中铅锌铜的方法,该回收方法的详细步骤如下:
56.a、以铜熔炼渣和铜精炼渣为原料,熔炼渣和精炼渣二者之间的质量配比比例为4:1,还原煤为助剂;
57.所述铜熔炼渣中的化学成分及其重量百分含量分别为cu 3.0%、pb 0.8%、zn 4.0%,fe 40.0%和sio
2 20.0%;精炼渣中的化学成分及其重量百分含量分别为cu 25.0%、pb 18.0%、zn 0.8%、fe 5.0%和sio
2 30.0%;
58.b、将铜熔炼渣6.0t和精炼渣1.5t进行混合,混合后通过加料口加入侧吹炉中,同时加入240kg还原煤,然后经侧吹炉侧吹口设有的喷枪将燃料压缩空气通入炉内熔池进行加热、搅拌,压缩空气的喷吹压力为0.1~0.4mpa,当侧吹炉内熔池深度达到1200~1800mm、温度为1300~1350℃时进行熔炼反应,反应时间为4.5h;
59.c、熔炼反应后,产生的铜锍和尾渣分别经侧吹炉铜锍口和放渣口排出;产生的烟气由烟道口排出,经收尘系统回收烟尘。
60.本实施例在放渣口和铜锍口取样检测,经化验检测,所得尾渣中含cu0.40%、pb 0.17%、zn 0.90%;铜锍口得到的冰铜品位为38%;回收的烟尘中含zn 68.8%。
61.实施例4:
62.参见附图1,本发明侧吹熔炼回收冶炼废弃渣中铅锌铜的方法,该回收方法的详细步骤如下:
63.a、以铜熔炼渣和精炼渣为原料,熔炼渣和精炼渣二者之间的质量配比比例为13:1,还原煤为助剂;
64.所述铜熔炼渣中的化学成分及其重量百分含量分别为cu 2.0%、pb 0.5%、zn 7.0%,fe 36.0%和sio
2 22.0%;精炼渣中的化学成分及其重量百分含量分别为cu 28.0%、pb 12.5%、zn1.0%、fe 5.0%和sio
2 30.0%;
65.b、将铜熔炼渣6.5t和精炼渣0.5t进行混合,混合后通过加料口加入侧吹炉中,同时加入267kg还原煤,然后经侧吹炉侧吹口设有的喷枪将燃料压缩空气通入炉内熔池进行加热、搅拌,压缩空气的喷吹压力为0.1~0.4mpa,当侧吹炉内熔池深度达到1200~1800mm、温度为1300~1400℃时进行熔炼反应,反应时间为4.0h;
66.c、熔炼反应后,产生的铜锍和尾渣分别经侧吹炉铜锍口和放渣口排出;产生的烟
气由烟道口排出,经收尘系统回收烟尘。
67.本实施例在放渣口和铜锍口取样检测,经化验检测,所得尾渣中含cu 0.38%、pb 0.15%、zn 1.08%;铜锍口得到的冰铜品位为41%;回收的烟尘中含zn 67.4%。
68.实施例5:
69.参见附图1,本发明侧吹熔炼回收冶炼废弃渣中铅锌铜的方法,该回收方法的详细步骤如下:
70.a、以铜熔炼渣、吹炼渣和精炼渣为原料,熔炼渣、吹炼渣和精炼渣三者之间的质量配比比例为4.25:1:1,粉煤为助剂;
71.所述铜熔炼渣中的化学成分及其重量百分含量分别为cu 3.0%、pb 0.9%、zn 4.2%,fe 40.0%和sio
2 20.0%;冶炼渣中的化学成分及其重量百分含量为cu 9.2%、pb 9.8%、zn 2.4%、fe 20%、sio
2 15%;精炼渣中的化学成分及其重量百分含量分别为cu 22.5%、pb 17.5%、zn 1.0%、fe 5.0%和sio
2 30.0%;
72.b、将铜熔炼渣4.25t、冶炼渣1.0t和精炼渣1.0t进行混合,混合后通过加料口加入侧吹炉中,同时加入296kg粉煤,然后经侧吹炉侧吹口设有的喷枪将燃料富氧空气通入炉内熔池进行加热、搅拌,富氧空气的喷吹压力为0.1~0.4mpa,当侧吹炉内熔池深度达到1200~1500mm、温度为1300~1400℃时进行熔炼反应,反应时间为4.0h;
73.c、熔炼反应后,产生的铜锍和尾渣分别经侧吹炉铜锍口和放渣口排出;产生的烟气由烟道口排出,经收尘系统回收烟尘。
74.本实施例在放渣口和铜锍口取样检测,经化验检测,所得尾渣中含cu0.37%、pb 0.20%、zn 1.1%;铜锍口得到的冰铜品位为43%;回收的烟尘中含zn 63%。