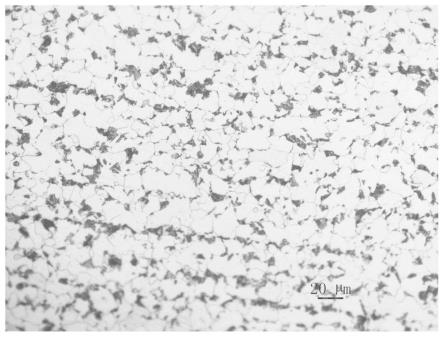
一种薄规格高韧性12cr1movr压力容器钢板的生产方法
技术领域
1.本发明涉及热轧领域,尤其涉及一种薄规格高韧性12cr1movr压力容器钢板的生产方法。
背景技术:2.12cr1movr是低合金压力容器钢板,主要用于石油石化行业、化工设备制造企业、电站建设、锅炉和压力容器制造等,用户对热强性和持久塑性提出更高要求,对现有工艺进行优化,提升钢板韧性,同时满足强度要求,以满足用户使用要求。
3.申请号cn 109112400 a的专利“一种容器用耐热12cr1movr钢板及其生产方法”提供了一种50~80mm厚的压力容器钢板生产方法,本方法提供10-40mm厚的压力容器钢板生产方法。
4.申请号cn 112442637 a的专利“一种新型合金容器用钢板12cr1movr的生产方法”,提供了一种新型合金容器用钢板12cr1movr的生产方法,采用控制轧制交货工艺,本方法提供一种正火+回火热处理工艺压力容器钢板,相比上述专利工艺稳定,利于控制,表面质量良好,韧性优良的钢板。
技术实现要素:5.本发明的目的是提供一种生产工艺稳定、性能优良、表面质量和冲击韧性薄规格高韧性12cr1movr压力容器钢板生产方法,采用正火+回火热处理工艺,采用窄成分控制,对轧制及热处理工艺进行精准控制,确保钢板性能优良,特别是韧性满足用户的高标准要求。
6.为解决上述技术问题,本发明采用如下技术方案:
7.本发明一种薄规格高韧性12cr1movr压力容器钢板的生产方法,包括:
8.1)、转炉出钢温度1630~1660℃,采用单渣工艺冶炼,采用低碳锰铁和硅铝铁合金脱氧合金化,转炉渣层厚度小于50mm;
9.2)、钢水进行rh炉处理,rh真空处理时间不少于20分钟,纯脱气时间不少于15分钟,最小真空度80-125pa,离位氢含量小于等于1.5ppm;
10.3)、连铸坯的厚度为300mm,钢水浇铸时过热度控制在15~28℃,换包时中包液位不小于30吨;连铸时采用轻压下,轻压下位置为凝固终端前三、四段,总压下量为8.0mm;连铸时采用电磁搅拌,电磁搅拌位置为4段、5段,电磁搅拌频率为5hz,电流为380a;结晶器宽侧水量4500l/min,窄侧水量370l/min,结晶器进水温度控制在36
±
2℃,结晶器进水温度控制在38
±
1℃,二冷水温度控制在22~25℃,水质指标要符合工艺要求;采用保护浇注,长水口密封氩气压力控制在≥0.3mpa,流量控制在130~160l/min;中间包浸入水口密封氩气压力0.2mpa,流量15~20l/min;浇铸时拉速需稳定在0.8m/min;铸坯矫直温度控制在950~1000℃,且铸坯沿宽度方向的温差不得超过50℃做好保护浇注,谨防钢水二次氧化和吸气增氮;
11.4)、切割后的铸坯立即放入缓冷区缓冷,缓冷区是将坯库的保温性能好的一块地
方四周用耐火砖砌墙围起来,墙的高度4米,热坯集中放入可以减缓铸坯降温,消除内部应力;将每垛坯子放到最高,坯垛集中摆放,缓冷时间72小时以上;
12.5)、加热工艺:板坯加热时采用三段式加热的步进式加热炉,第一加热段的加热温度1160~1200℃,加热时间40~50分钟;第二加热段的加热温度1200~1260℃,加热时间45~60分钟;总加热时间不少于220分钟;板坯出炉温度1210-1250℃;
13.6)、轧制及冷却工艺:板坯加热好之后进行两阶段控制轧制,第一阶段轧制在粗轧机上完成,第一阶段开轧厚度为板坯厚度,第一阶段开轧温度不小于1200℃,第一阶段轧制时设定扭矩为2400knm,设定压下量为38mm,轧制速度为2.1~3.4m/s,高温延伸阶段的单道次压下率不小于18%,第一阶段终轧温度≥1050℃,第一阶段轧制到第二阶段的开轧厚度为止;第二阶段轧制在精轧机上完成,第二阶段开轧温度为940~980℃,第二阶段的开轧厚度为57~125mm,第二阶段终轧温度为870~920℃,第二阶段轧制时设定扭矩为2200knm、设定轧制力为85mn、设定压下量为20mm,末道次压下率5%~10%,以保证板形;钢板轧完后进行层流冷却,acc水温为17~20℃,冷却速度为15~22℃/s,终冷温度为620~660℃,一般头部遮蔽0-2.0m,尾部遮蔽0-2.5m,边部遮挡0-2.0m,控制钢板返红后整体温度差≤50℃;
14.7)、采用正火+回火热处理工艺,正火炉保温温度880~960℃,保温时间>3分钟,在炉时间10~30min,回火保温温度680~760℃,保温时间>10分钟,在炉时间20~40min;出炉空冷,平铺冷却到200℃后采用堆垛缓冷,缓冷时间大于6小时。
15.进一步的,为保证一定的压缩比板坯质量,选用300mm厚的连铸坯,铸坯中心偏析不大于c2.5,中心疏松不大于2.5级,中间裂纹不大于1.0级。
16.进一步的,所述钢板包含的质量百分比的化学成分为:c:0.12~0.14%、si:0.25~0.35%、mn:0.50~0.65%、p:≤0.015%、s:≤0.005%、nb:0.025~0.035%、v:0.15~0.30%,cr:0.90~1.20%,mo:0.25~0.35%,als:0.15~0.32%,h≤1.7ppm;o:≤0.0036%;n:≤0.0044%;其余为铁和不可避免杂质。
17.进一步的,其化学成分的质量百分含量为:c 0.12%、si 0.28%、mn 0.57%、p 0.013%、s 0.004%、als 0.024%、nb 0.025%、v 0.18%、cr 0.88%,mo 0.26%,h 0.6ppm;o:0.0030%;n:0.0040%;余量为fe和不可避免的杂质。
18.进一步的,其化学成分的质量百分含量为:c 0.14%、si 0.28%、mn 0.60%、p 0.010%、s 0.003%、als 0.027%、nb 0.030%、v 0.20%、cr 1.0%,mo 0.25%,h 0.5ppm;o:0.0025%;n:0.0038%,余量为fe和不可避免的杂质。
19.进一步的,其化学成分的质量百分含量为:c 0.12%、si 0.34%、mn 0.55%、p 0.0015%、s 0.005%、als 0.020%、nb 0.025%、v 0.16%、cr 0.90%、mo 0.28%,h 0.9ppm;o:0.0035%;n:0.0045%余量为fe和不可避免的杂质。
20.进一步的,其化学成分的质量百分含量为:c 0.12%、si 0.25%、mn 0.62%、p 0.008%、s 0.003%、als 0.030%、nb 0.030%、v 0.25%、cr 1.10%、mo 0.30%,h 0.50ppm;o:0.0025%;n:0.0025%,余量为fe和不可避免的杂质。
21.与现有技术相比,本发明的有益技术效果:
22.(1)钢板厚度为10mm-40mm;
23.(2)对钢板进行适度的合金化,在保证钢板性能的前提下降低了合金成本;
24.(3)轧制过程采用正火+回火工艺保证钢板轧态组织为f+p;
25.(4)合适的调质工艺,促进钢板具有良好的强韧力学性能。
26.本发明的突出优点是基于正火+回火处理工艺,稳定生产10mm-40mm高韧性钢板。经实际生产并检验,其力学性能优异,各实施例的钢板强度符合标准要求,延伸率大于22%,钢板20℃冲击功可达150j以上。
附图说明
27.下面结合附图说明对本发明作进一步说明。
28.图1为本发明实施例3轧态的金相照片,组织为f+p;
29.图2为本发明实施例3正火态的金相照片,组织为f+p;
30.图3为本发明实施例3正火+回火态的金相照片,组织为f+p。
具体实施方式
31.本发明的目的是提供一种生产工艺稳定、性能优良、表面质量和冲击韧性薄规格高韧性12cr1movr压力容器钢板生产方法,所述钢板包含的质量百分比的化学成分(单位,wt%)为:c:0.12~0.14、si:0.25~0.35、mn:0.50~0.65、p:≤0.015、s:≤0.005、nb:0.025~0.035、v:0.15~0.30,cr:0.90~1.20,mo:0.25~0.35,als:0.15~0.32,h≤1.7ppm;o:≤0.0036%;n:≤0.0044%;其余为铁和不可避免杂质;所述钢板的生产方法包括kr脱硫
→
转炉冶炼
→
lf精炼
→
rh精炼
→
连铸
→
保温坑缓冷
→
加热
→
轧制
→
冷却
→
热矫
→
剪切
→
探伤
→
正火
→
回火。
32.上述一种10mm~40mm厚规格12cr1movr压力容器钢板生产方法,具体包括:
33.1)、转炉出钢温度1630~1660℃,采用单渣工艺冶炼,采用低碳锰铁和硅铝铁合金脱氧合金化,转炉渣层厚度小于50mm。
34.2)、钢水进行rh炉处理,rh真空处理时间不少于20分钟,纯脱气时间不少于15分钟,最小真空度80-125pa,离位氢含量小于等于1.5ppm。
35.3)、连铸坯的厚度为300mm,钢水浇铸时过热度控制在15~28℃,换包时中包液位不小于30吨;连铸时采用轻压下,轻压下位置为凝固终端前三、四段,总压下量为8.0mm;连铸时采用电磁搅拌,电磁搅拌位置为4段、5段,电磁搅拌频率为5hz,电流为380a;结晶器宽侧水量4500l/min,窄侧水量370l/min,结晶器进水温度控制在36
±
2℃,结晶器进水温度控制在38
±
1℃,二冷水温度控制在22~25℃,水质指标要符合工艺要求;采用保护浇注,长水口密封氩气压力控制在≥0.3mpa,流量控制在130~160l/min;中间包浸入水口密封氩气压力0.2mpa,流量15~20l/min;浇铸时拉速需稳定在0.8m/min。铸坯矫直温度控制在950~1000℃,且铸坯沿宽度方向的温差不得超过50℃做好保护浇注,谨防钢水二次氧化和吸气增氮。
36.4)、切割后的铸坯立即放入缓冷区缓冷,缓冷区是将坯库的保温性能好的一块地方四周用耐火砖砌墙围起来,墙的高度4米,热坯集中放入可以减缓铸坯降温,消除内部应力。将每垛坯子放到最高,坯垛集中摆放,缓冷时间72小时以上。
37.5)、加热工艺:板坯加热时采用三段式加热的步进式加热炉,第一加热段的加热温度1160~1200℃,加热时间40~50分钟;第二加热段的加热温度1200~1260℃,加热时间45~60分钟;总加热时间不少于220分钟;板坯出炉温度1210-1250℃。
38.6)、轧制及冷却工艺:板坯加热好之后进行两阶段控制轧制,第一阶段轧制在粗轧机上完成,第一阶段开轧厚度为板坯厚度,第一阶段开轧温度不小于1200℃,第一阶段轧制时设定扭矩为2400knm,设定压下量为38mm,轧制速度为2.1~3.4m/s,高温延伸阶段的单道次压下率不小于18%,第一阶段终轧温度≥1050℃,第一阶段轧制到第二阶段的开轧厚度为止。第二阶段轧制在精轧机上完成,第二阶段开轧温度为940~980℃,第二阶段的开轧厚度为57~125mm,第二阶段终轧温度为870~920℃,第二阶段轧制时设定扭矩为2200knm、设定轧制力为85mn、设定压下量为20mm,末道次压下率5%~10%,以保证板形。钢板轧完后进行层流冷却,acc水温为17~20℃,冷却速度为15~22℃/s,终冷温度为620~660℃,一般头部遮蔽0-2.0m,尾部遮蔽0-2.5m,边部遮挡0-2.0m,控制钢板返红后整体温度差≤50℃。
39.7)、采用正火+回火热处理工艺,正火炉保温温度880~960℃,保温时间>3分钟,在炉时间10~30min,回火保温温度680~760℃,保温时间>10分钟,在炉时间20~40min。出炉空冷,平铺冷却到200℃后采用堆垛缓冷,缓冷时间大于6小时。
40.为保证一定的压缩比板坯质量,选用300mm厚的连铸坯,铸坯中心偏析不大于c2.5,中心疏松不大于2.5级,中间裂纹不大于1.0级。
41.以下结合实施例对本发明作进一步的描述。
42.实施例1
43.将冶炼、连铸后的拟轧制的板坯放入加热炉,加热时间为260分钟,均热时间为45分钟。板坯的化学成分的质量百分含量为:c 0.12%、si 0.28%、mn 0.57%、p 0.013%、s 0.004%、als 0.024%、nb 0.025%、v 0.18%、cr 0.88%,mo 0.26%,h 0.6ppm;o:0.0030%;n:0.0040%;余量为fe和不可避免的杂质。轧制成厚度为10mm的钢板,详细的轧制及热处理工艺见表1,其力学性能见表2。
44.实施例2
45.将冶炼、连铸后的拟轧制的板坯放入加热炉,加热时间为250分钟,均热时间为40分钟。板坯的化学成分的质量百分含量为:c 0.14%、si 0.28%、mn 0.60%、p 0.010%、s 0.003%、als 0.027%、nb 0.030%、v 0.20%、cr 1.0%,mo 0.25%,h 0.5ppm;o:0.0025%;n:0.0038%,余量为fe和不可避免的杂质。轧制成厚度为20mm的钢板,详细的轧制及热处理工艺见表1,其力学性能见表2。
46.实施例3
47.将冶炼、连铸后的拟轧制的板坯放入加热炉,加热时间300分钟,均热时间为50分钟。板坯的化学成分的质量百分含量为:c 0.12%、si 0.34%、mn 0.55%、p 0.0015%、s 0.005%、als 0.020%、nb 0.025%、v 0.16%、cr 0.90%、mo 0.28%,h 0.9ppm;o:0.0035%;n:0.0045%余量为fe和不可避免的杂质。轧制成厚度为30mm的钢板,详细的轧制及热处理工艺见表1,其力学性能见表2。
48.实施例4
49.将冶炼、连铸后的拟轧制的板坯放入加热炉,加热时间280分钟,均热时间为50分钟。板坯的化学成分的质量百分含量为:c 0.12%、si 0.25%、mn 0.62%、p 0.008%、s 0.003%、als 0.030%、nb 0.030%、v 0.25%、cr 1.10%、mo 0.30%,h 0.50ppm;o:0.0025%;n:0.0025%,余量为fe和不可避免的杂质。轧制成厚度为40mm的钢板,详细的轧制及热处理工艺见表1,其力学性能见表2。
50.表1实施例1~4的工艺参数
[0051][0052]
表2实施例1~4的力学性能
[0053][0054]
表3 12cr1movr钢板高温拉伸性能
[0055][0056][0057]
以上所述的实施例仅是对本发明的优选方式进行描述,并非对本发明的范围进行限定,在不脱离本发明设计精神的前提下,本领域普通技术人员对本发明的技术方案做出的各种变形和改进,均应落入本发明权利要求书确定的保护范围内。