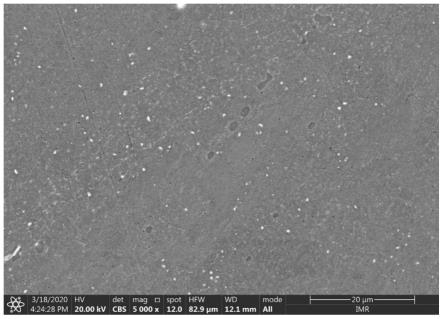
1.本发明涉及一种金属材料技术领域,特别是涉及一种高碳中高合金钢及其制备方法。
背景技术:2.对于大尺寸金属材料,传统的制备路线是先进行纯净化冶炼,模铸成锭或连铸成坯,然后进行锻轧和热处理制造成材,最后将材成形为构件等。该制备路线导致金属材料存在严重的尺寸效应,断面尺寸越大,心部冷却速度越慢,材料的偏析越严重,在非平衡凝固条件下,微观偏析将导致粗大析出相的形成。这些析出相在后续锻轧和热处理过程中虽然有所改善,但是难以达到令人满意的效果,特别是针对服役寿命有着极高要求或服役环境极其苛刻的情形。
3.为了解决这些粗大析出相的共性难题,国际上开发了粉末冶金技术。其中,粉末冶金工艺具体为:先将材料高压喷射成粉,然后采用热等静压等技术将粉末致密和烧结制成块体,再成形为各种构件。粉末冶金的优点是可以有效解决材料的偏析问题,使难成形的材料更均匀。
4.对于现有的高品质高碳中高合金钢的制备工艺,往往采用粉末冶金方法制备出碳化物细小的母材,以提高服役性能。粉末冶金方法主要广泛使用在工模具钢、高速钢等制备中。但是,由于制粉工序复杂,纯净度无法达到双真空熔炼水平,同时受限于热等静压装备的制造能力,生产效率低下,成本极高,制造周期长,很难制备高纯大尺寸母材,且材料利用率低,纯度、孔隙问题难以解决,工艺可控性较差。
5.综上,目前亟需研发一种可替代粉末冶金技术的低成本制备工艺,以实现大尺寸金属材料中粗大析出相有效减小甚至完全消除,经济上能够有效降低制造成本、减少工艺复杂度和缩短制造周期的技术效果。
技术实现要素:6.有鉴于此,本发明提供一种高碳中高合金钢及其制备方法,主要目的在于提供一种替代粉末冶金技术的低成本制备工艺,以有效减小高碳中高合金钢材料中的粗大析出相。
7.需要说明的是:本技术的高碳中高合金钢是碳含量为0.6%以上,合金元素总含量在5%以上的合金钢。
8.为达到上述目的,本发明主要提供如下技术方案:
9.一方面,本发明的实施例提供一种高碳中高合金钢的制备方法,其包括如下步骤:
10.步骤1):采用真空感应熔炼工艺、真空自耗熔炼工艺制备出自耗锭;其中,在所述自耗锭中:液析碳化物的最大等效直径小于100μm、全氧含量小于10ppm、夹杂物尺寸≤10μm、n含量小于40ppm;
11.步骤2):以所述自耗锭作为坯料,对所述坯料先进行保温处理,再进行至少一次高
温扩散及热变形处理,得到高碳中高合金钢;
12.其中,每一次所述高温扩散及热变形处理的步骤,包括:以设定升温速率将坯料的温度升温至高温扩散处理温度,进行高温扩散处理;然后再以设定降温速率将坯料的温度降温至热变形处理温度,进行热变形处理;
13.其中,所述设定降温速率为150-300℃/h;
14.其中,当坯料的温度低于1000℃时,则所述设定升温速率≤80℃/h,当坯料的温度大于等于1000℃时,则所述设定升温速率≥120℃/h。
15.优选的,在所述步骤1)中的真空自耗熔炼工艺中:
16.锭型的直径≤410mm;和/或
17.熔池的中心深度和自耗锭直径的比值为0.4-0.6;和/或
18.自耗锭的起弧段和补缩端的切除量≥100mm。
19.优选的,在所述步骤1)中的真空自耗熔炼工艺中:自耗锭中的碳化物最大等效直径小于100μm,优选不超过50μm。
20.优选的,在所述步骤2)中:
21.所述保温处理的温度为300-1000℃,且所述保温处理为多级保温处理;其中,后一级的保温处理温度高于前一级的保温处理温度;
22.优选的,在所述保温处理的步骤中:升温速率≤80℃/h,优选为50-80℃/h,进一步优选为80℃/h。
23.优选的,所述保温处理为两级保温处理,具体如下:
24.先将所述坯料加热至第一保温处理温度进行第一级保温处理,然后再加热至第二保温处理温度进行第二级保温处理;其中,所述第一级保温处理的温度为300-500℃,第二级保温处理的温度为800-900℃;优选的,所述第一级保温处理的时间大于等于5h;优选的,所述第二级保温处理的时间大于等于5h。
25.优选的,在所述高温扩散及热变形处理的步骤中:所述设定升温速率为150-400℃/h,优选为180-300℃/h。
26.优选的,在所述高温扩散及热变形处理的步骤中:
27.所述高温扩散处理的温度≥1200℃,优选为1200-1250℃;每次所述高温扩散处理的时间≥20h,优选为25-40h;和/或
28.所述热变形处理的温度≤1170℃,优选为1130-1170℃;和/或
29.所述热变形处理为锻造热变形处理。
30.优选的,在所述步骤2)中:进行高温扩散及热变形处理的次数为2-3次。
31.优选的,经步骤2)处理后,得到的高碳中高合金钢为块体或棒材。
32.另一方面,本发明实施例提供一种高碳中高合金钢,其中,所述高碳中高合金钢中的碳化物的最大等效直径≤8μm;优选的,所述高碳中高合金钢是由上述任一项所述的高碳中高合金钢的制备方法制备而成。
33.与现有技术相比,本发明的一种高碳中高合金钢及其制备方法至少具有下列有益效果:
34.本发明实施例提供一种高碳中高合金钢的制备方法,主要包括如下步骤:步骤1)采用真空感应熔炼工艺、真空自耗熔炼工艺制备出自耗锭;其中,在自耗锭中:液析碳化物
的最大等效直径小于100μm、全氧含量小于10ppm、夹杂物尺寸≤10μm、n含量小于40ppm;步骤2)以自耗锭作为坯料,对坯料先进行保温处理,再进行至少一次高温扩散及热变形处理(尤其是控制高温扩散处理前的升温速率、高温扩散处理后的降温速率),得到高碳中高合金钢。关于上述步骤说明如下:上述步骤1)主要是完成自耗锭的纯净度和原始碳化物尺寸控制,在此基础上,步骤2)为了防止碳化物在高温区升温时间过长,碳化物会发生球化及长大情况,选取快速升温,经过高温扩散回溶处理后,同样选取快速冷却的方法,防止后续降温过程中未完全回溶的碳化物长大,再结合后续的热变形处理,实现所制备的高碳中高合金钢中析出相小尺寸精准控制。另外,根据初始自耗锭的碳化物条件以及为达到高碳中高合金钢中的碳化物最大有效直径尺寸≤8μm的目的,可进行多次高温扩散及热处理,减少直至消除大尺寸析出相。本发明实施例所实施操作过程,不仅完成碳化物有效精准控制,而且避免高温合金变形开裂。
35.进一步地,本发明实施例通过选取真空感应熔炼及真空自耗熔炼工艺,将自耗锭的纯净度控制如下:全氧含量控制在10ppm以下、夹杂物尺寸≤10μm,n含量控制在40ppm以下。进一步地,在铸态凝固过程中选取适度规格真空自耗锭(如,选用锭型直径≤410mm),并选取合适凝固参数(通过浅熔池控制,熔池的深宽比控制为0.4-0.6),完成真空自耗锭铸态原始碳化物尺寸控制(即,自耗锭整个断面厚度的析出相最大等效直径小于100μm)。
36.相比于粉末冶金方法等的工艺复杂度和经济成本高昂,本发明实施例提供一种高碳中高合金钢的制备方法,是通过真空感应+真空自耗工艺制备出所需原坯料,然后经热加工工艺制备成目标构件,无需制粉环节,生产工艺远比粉末冶金方法简单,且不受热等静压装备能力限制,流程可控,成本更低。本发明利用现有的传统冶金装备进行制造,操作简单,不用研发制造新的装备,制备效率高,有利于工业化大批量生产。
37.本发明实施例提供一种高碳中高合金钢的制备方法为共性技术,应用范围广,适用于包括黑色金属和有色金属在内的金属材料,有利于控制大尺寸和超大尺寸金属材料的宏观和微观偏析,适用于各种大尺寸金属材料的高性能制备。
38.本发明实施例提供一种高碳中高合金钢的制备方法,通过对铸锭的凝固偏析控制和特殊的减少碳化物的热加工方式,解决了粉末冶金不能解决的纯净度不足和存在微小缺陷的问题。另外,本发明还能实现采用以小制大的技术路线(例如,通过制备出纯净度高且偏析小甚至无偏析的小块体;而多个小块体可以构筑制备出低偏析大尺寸金属材料),克服了粉末冶金受限于热等静压装备的规模限制,且能够同时减轻或消除宏观偏析和微观偏析以及大尺寸第二相控制。
39.上述说明仅是本发明技术方案的概述,为了能够更清楚了解本发明的技术手段,并可依照说明书的内容予以实施,以下以本发明的较佳实施例并配合附图详细说明如后。
附图说明
40.图1a为有效控制粗大析出相而选择的适宜尺寸自耗锭的示意图;
41.图1b为将图1a的自耗锭经多次高温扩散-热变形处理后得到的块体示意图;
42.图2为实施例1中制备的m50轴承钢棒材的微观结构图;
43.图3为采用传统铸锻方法制造的m50轴承钢棒材的微观结构图;
44.图4为采用传统铸锻方法制造的v4e模具钢棒材的微观结构图;
45.图5为实施例2制备的v4e模具钢棒材的微观结构图;
46.图6为采用粉末冶金方法制造的v4e模具钢棒材的微观结构图;
47.图7为实施例3制备的caldie模具钢棒材的微观结构图;
48.图8为采用传统铸锻方法制备的caldie模具钢棒材的微观结构图;
49.图9是对比例5制备的m50轴承钢棒材的微观结构图;
50.图10是对比例6制备的m50轴承钢棒材的微观结构图。
具体实施方式
51.为更进一步阐述本发明为达成预定发明目的所采取的技术手段及功效,以下结合附图及较佳实施例,对依据本发明申请的具体实施方式、结构、特征及其功效,详细说明如后。在下述说明中,不同的“一实施例”或“实施例”指的不一定是同一实施例。此外,一或多个实施例中的特定特征、结构、或特点可由任何合适形式组合。
52.本发明提供一种高碳中高合金钢及其制备方法,具体地是一种通过对自耗锭的纯净度及成分偏析进行控制(参见步骤1)、关键共晶碳化物溶解及热变形控制(参见步骤2),将铸态自耗锭制备成碳化物≤8μm的高碳中高合金钢。解决的是粉末冶金出现的问题,如纯净度不足和存在微缺陷,工艺复杂,成本高,以及传统冶金工艺中大尺寸析出相难以控制的问题,以块体冶金方法代替了传统的粉末冶金方法等,实现氧含量≤10ppm、夹杂物尺寸≤10μm,碳化物≤8μm的高碳中高合金钢块体的制备,推动冶金学科发展和技术变革。
53.具体地,本发明的方案如下:
54.步骤1),采用真空感应熔炼工艺、真空自耗熔炼工艺制备出自耗锭;其中,在所述自耗锭中:液析碳化物的最大等效直径小于100μm、全氧含量小于10ppm、夹杂物尺寸≤10μm、n含量小于40ppm。
55.其中,在该步骤中,利用锭型尺寸及控制熔炼工艺实现自耗锭初的始碳化物尺寸及纯净度的控制。
56.具体地,对高碳中高合金钢进行双真空冶炼(真空感应+真空自耗),确保其高的纯净度,将钢中全氧含量控制到10ppm以下,夹杂物尺寸≤10μm,n控制到40ppm以下。其中,在真空自耗熔炼过程中,根据自耗锭凝固偏析控制要求,采用适宜自耗锭尺寸,选用锭型的直径≤410mm,将稳态熔炼阶段熔池的深宽比控制在0.4-0.6,以实现最佳熔池控制,其中熔池深是熔池中心深度,熔池宽是自耗锭直径。自耗锭整个断面厚度的析出相(液析碳化物)最大等效直径小于100μm(在此需要说明的是,本技术的术语“等效直径”:(a+b)/2,其中,a是碳化物长轴长度,b是碳化物短轴长度);同时增加结晶器冷却强度,确保自耗锭凝固析出的碳化物最大等效直径小于100μm。控制自耗锭起弧端与补缩端切除量,优选切除量≥100mm,使剩下自耗锭成分更加均匀。更优的,为保证锻造不开裂,可以进一步将表面进行机加工,不得残留黑皮及表面质量缺陷。
57.步骤2)以所述自耗锭作为坯料,对所述坯料先进行保温处理,再进行至少一次高温扩散及热变形处理,得到高碳中高合金钢;其中,每一次所述高温扩散及热变形处理的步骤,包括:以设定升温速率将坯料的温度升温至高温扩散处理温度,进行高温扩散处理;然后再以设定降温速率将坯料的温度降温至热变形处理温度,进行热变形处理;其中,设定降温速率为150-300℃/h;其中,当坯料的温度低于1000℃时,则所述设定升温速率≤80℃/h,
当坯料的温度大于等于1000℃时,则所述设定升温速率≥120℃/h。
58.该步骤主要是根据碳化物高温长大与回溶特性及结合锻造热变形处理,制备出单块均质块体(块体中的碳化物≤8μm),优选的,可以根据最终材料需要,制备所需规格棒材(棒材中的碳化物≤8μm)。
59.关于该步骤,详细说明如下:
60.1)关于保温处理:为了防止自耗锭在加热初期由于应力过大开裂,将自耗锭放入加热炉,在多个保温段进行多级保温处理,保温段的温度设置范围在300-1000℃,一种优选方式为分别在300-500℃以及800-900℃两个保温段进行保温处理,保温时间均大于等于5h。控制自耗锭在1000℃以下时的升温速率(加热速度),使自耗锭升温均匀,加热速度设置为80℃/h以下,优选加热速度设置为50-80℃/h,进一步优选控制在80℃/h。
61.2)利用高碳中高合金钢中共晶碳化物高温转变与长大特征和回溶特性,在高温加热阶段(即1000℃以上的高温区)开展快速升温及适时高温扩散,实现铸态碳化物快速回溶,在高温扩散后,同样采用快速降温方法,快速降温至1130-1170℃范围进行热变形工艺。快速升温-高温扩散-快速降温-热变形处理的循环操作可进行两次以上。其中,在高温区,快速加热和快速冷却操作主要为了防止局部碳化物球化长大,而高温扩散主要是控制碳化物回溶,尺寸变小。最终通过“快速升温-高温扩散-快速降温-热变形工艺”操作,制备出高均质小尺寸块体(或棒材)。
62.3)在该步骤的操作过程中,在≥1000℃的高温区段,防止碳化物长大及转化,控制快速升温的加热速度(升温速率)大于等于120℃/h,优选控制在150-400℃/h,进一步优选控制在180-300℃/h。快速升温后进行高温保温扩散处理,该高温扩散处理的温度优选为1200-1250℃,进一步优选为1210
±
10℃,高温扩散处理的时间控制在≥20h,优选为25-40h,然后在高温扩散温度以下,进行快速降温,快速降温速率优选150-300℃/h,快速降温到小于等于1170℃,优选降温至1130-1170℃;之后进行锻造热变形处理(即第一次热变形处理),锻造热变形处理同样起到防止碳化物长大的作用。然后可以将第一次热变形处理后坯料重回加热炉,再次快速升温到高温扩散温度处理温度进行高温保温扩散处理,控制高温扩散时间,高温扩散后再次重复锻造热变形处理,重复次数依据碳化物细化尺寸设定,优选2-3次,经热变形后形成的块体中的碳化物最大等效直径≤8μm。
63.其中,关于本发明实施例的上述制备工艺,步骤1)制备的自耗锭的示意图参见图1a所示;步骤2)制备的高碳中高合金钢块体的示意图参见图1b所示;当然步骤2)也可以制备成棒材。
64.为了使本发明的技术方案和有益效果更加清楚,下面通过实验实施例进一步对本发明说明如下:
65.实施例1
66.本实施例制备一种m50轴承钢,主要步骤如下:
67.步骤1)采用双真空工艺(真空感应+真空自耗)制备自耗锭。
68.其中,选取的锭型的直径为ф350mm。在真空自耗熔炼过程中,根据成分偏析控制,将稳态熔炼阶段的熔池深宽比控制在0.4-0.6范围内,同时增加结晶器冷却强度,使最终自耗锭中的碳化物最大等效直径为50μm。自耗锭的起弧端与补缩端切除量≥100mm,使剩下自耗锭成分更加均匀。最终使得自耗锭中的氧含量为6ppm、氮含量为20ppm。进一步,为保证锻
造不开裂,将自耗锭的表面进行机加工,不得残留黑皮及表面质量缺陷。
69.步骤2)以自耗锭为坯料,放入加热炉,先进行两级保温处理(以80℃/h的升温速率加热到300-500℃,在该温度段下保温5h,以进行第一级保温处理;然后再加热至800-900℃,在该温度段保温段进行保温8h,以进行第二级保温处理),然后进行两次高温扩散及热变形处理,得到m50轴承钢棒材。
70.其中,该两次高温扩散及热处理的步骤,包括:除900℃以下保温处理外,坯料在1000℃以下时,加热速度控制在80℃/h(即,在保温处理后,将坯料从保温处理的温度加热至1000℃,采用的加热速率为80℃/h),当坯料的温度在≥1000℃时,选取150℃/h的升温速率,快速升温到1200℃进行第一次高温扩散处理,第一次高温扩散处理的时间为25h;然后空冷快速降温至1130℃(其中,降温速率为300℃/h),进行第一次热变形处理(锻造)。再将第一次热变形处理后坯料重回加热炉,选取150℃/h的升温速率再次快速升温到1200℃进行第二次高温扩散处理,其中,第二次高温扩散处理的时间为20h,高温扩散处理后再次空冷快速降温至1130℃(其中,降温速率为250℃/h),进行第二次锻造热变形处理。经第二次热变形处理后,得到m50轴承钢棒材。
71.本实施例制备的m50轴承钢棒材的微观结构参见图2所示;其中,碳化物尺寸(最大等效直径)≤8μm。
72.对比例1
73.对比例1选用传统工业化m50轴承钢棒材制造工艺,具体地,先经过双真空熔炼制备成自耗锭,然后经一次高温扩散处理(其中,高温扩散处理的温度为1170℃、时间为15h),在高温扩散加热及炉冷到锻造温度过程中,冷却或加热速度>120℃/h,之后再经锻造、轧制等热变形方法制备m50轴承钢棒材。
74.其中,对比例1采用传统工业化m50轴承钢棒材制造工艺制备的棒材的显微组织参见图3所示。
75.通过对比图2和图3,可以明显看出:采用本发明实施例的方法制备的m50轴承钢中的碳化物尺寸较小(≤8μm)。而采用对比例1中的传统工业化m50轴承钢棒材制造工艺制备的m50轴承钢中具有尺寸较大的析出相(碳化物析出相)。
76.实施例2
77.本实施例制备一种合金含量高的vanadis 4extra(v4e)冷作模具钢,具体步骤如下:
78.步骤1)利用真空感应及真空自耗冶炼方法制备高纯净v4e模具钢自耗锭,利用锭型尺寸及控制熔炼工艺改善铸锭的均质性,其中,钢锭截面尺寸为ф150mm,自耗锭中碳化物最大等效直径为19.3μm,全氧含量为6ppm、氮含量为25ppm。
79.步骤2)以自耗锭为坯料,放入加热炉,先进行两级保温处理(以80℃/h的升温速率加热到300-500℃,在该温度段下保温5h,以进行第一级保温处理;然后再加热至800-900℃,在该温度段保温段进行保温6h,以进行二级保温处理)。然后,进行两次高温扩散及热变形处理,得到v4e模具钢棒材。
80.其中,该两次高温扩散及热处理的步骤,包括:除900℃以下保温段外,坯料在1000℃以下的温度时,加热速度控制在80℃/h(即,在保温处理后,将坯料从保温处理的温度加热至1000℃,采用的加热速率为80℃/h);当坯料的温度在≥1000℃时,选取150℃/h的升温
速率,快速升温至1220℃进行第一次高温扩散处理,第一次高温扩散处理的时间为20h,然后空冷快速降温至1130℃(其中,降温速率为300℃/h),进行第一次锻造热变形处理。将第一次热变形处理后坯料重回加热炉,以150℃/h的升温速率快速升温至1220℃进行第二次高温保温扩散处理,其中,第二次高温扩散处理的时间为15h。然后再空冷快速降温至1130℃(其中,降温速率为250℃/h),进行第二次锻造热变形处理。控制单道次变形量大于50%。经热变形后形成的v4e钢棒材。
81.其中,本实施例制备的冷作模具钢v4e棒材的微观结构参见图5所示,其中,碳化物尺寸(最大等效直径)≤8μm。
82.对比例2
83.对比例2采用传统工业化v4e模具钢制造工艺,具体地,双真空熔炼制备成冷作模具钢v4e自耗锭,经1160℃保温15h后,进行锻造轧制等热变形方法制备棒材,其中,加热速度范围是120-200℃/h。
84.其中,对比例2采用传统工业化v4e模具钢制造工艺制备的棒材显微组织参见图4所示。通过对比图4和图5,可以明显看出:采用本发明实施例的方法制备的v4e钢中的碳化物尺寸较小(≤8μm),而采用对比例2中的传统铸锻方法制备的钢中具有尺寸较大的析出相(共晶碳化物)。
85.对比例3
86.对比例3采用粉末冶金方法制备一种v4e模具钢,其中,其微观结构参见图6所示。
87.利用gb/t 14979-1994检测对实施例2、对比例2、对比例3所制备冷作模具钢v4e中共晶碳化物的不均匀度进行检测,数据如表1所示。
88.表1为v4e模具钢中的共晶碳化物不均匀度
[0089][0090]
另外,通过对比图5和图6、以及表1,可以看出:采用本发明实施例的方法制备的v4e钢中的碳化物尺寸较小(≤8μm),与粉末冶金棒材中的碳化物水平相当。
[0091]
实施例3
[0092]
本实施例制备一种合金含量高的caldie模具钢,具体步骤如下:
[0093]
步骤1)利用真空感应及真空自耗冶炼方法制备出高纯净自耗锭;其中,利用锭型尺寸及控制熔炼工艺改善自耗锭的均质性,控制全氧含量为8ppm,氮含量为15ppm,钢锭截面尺寸为ф190mm,自耗锭中碳化物最大等效直径为18μm。
[0094]
步骤2)以自耗锭为坯料,放入加热炉,先进行两级保温处理(以80℃/h的升温速率加热到300-500℃,在该温度段下保温5h,以进行一级保温处理;然后,再加热至800-900℃,在该温度段保温段进行保温5h,以进行二级保温处理)。然后,进行两次高温扩散及热变形处理,得到caldie模具钢棒材。
[0095]
其中,该两次高温扩散及热处理的步骤,包括:除900℃以下保温段外,当坯料在1000℃以下的温度时,加热速度控制为80℃/h(即,在保温处理后,将坯料从保温处理的温
度加热至1000℃,采用的加热速率为80℃/h),在≥1000℃的温度时选取150℃/h快速升温到1200℃,进行第一次高温扩散处理,第一次高温扩散处理的时间为24h;然后空冷快速降温至1120℃(降温速率为300℃/h),进行第一次锻造热变形处理。第一次热变形处理后坯料重回加热炉,选取150℃/h的升温速率再次快速升温到1250℃,进行第二次高温扩散处理,第二次高温扩散处理的时间为18h;然后,再次快速降温至1120℃(降温速率为250℃/h),以进行第二次锻造热变形处理。控制单道次变形量大于50%。经热变形后形成的caldie模具钢棒材中的碳化物尺寸(最大等效直径)为≤8μm。
[0096]
本实施例制备的caldie模具钢棒材的微观结构参见图7所示。
[0097]
对比例4
[0098]
对比例4采用气密保护电渣工艺制备caldie模具钢,具体地,经1160℃保温12h后,进行锻造轧制等热变形方法制备棒材,其中,加热速度范围是120-200℃/h。
[0099]
其中,对比例4采用传统工业化caldie模具钢制造工艺制备的棒材的显微组织参见图8所示。
[0100]
通过对比图7和图8,可以明显看出:采用本发明实施例的方法制备的caldie模具钢中的碳化物尺寸较小(≤8μm),而采用对比例4中的传统铸锻方法制备的caldie模具钢中具有尺寸较大的析出相(共晶碳化物)。
[0101]
对比例5
[0102]
对比例5制备一种m50轴承钢,主要步骤如下:
[0103]
步骤1)采用双真空工艺(真空感应+真空自耗)制备自耗锭。
[0104]
其中,选取的锭型直径为ф350mm。在真空自耗熔炼过程中,将稳态熔炼阶段的熔池深宽比控制在0.65-0.75,自耗锭的起弧端与补缩端切除量80mm,最终使得自耗锭中的全氧含量为7ppm、氮含量为20ppm,碳化物最大等效直径为160μm。
[0105]
步骤2)与实施例1的步骤完全一致,最终形成的m50轴承钢棒材的碳化物尺寸(最大等效直径)为15μm。
[0106]
对比例5制备的m50轴承钢棒材的微观结构参见图9所示。从图9可以明显看出:对比例5制备的m50轴承钢棒材中的碳化物尺寸较大。
[0107]
对比例6
[0108]
对比例6制备一种m50轴承钢,主要步骤如下:
[0109]
步骤1)采用双真空工艺(真空感应+真空自耗)制备自耗锭。步骤和实施例1完全一致,最终使得自耗锭中的全氧含量为5ppm、氮含量为18ppm,最终自耗锭中的碳化物最大等效直径为47μm。进一步,为保证锻造不开裂,将自耗锭的表面进行机加工,不得残留黑皮及表面质量缺陷。
[0110]
步骤2)以自耗锭为坯料,放入加热炉,先进行保温处理(以80℃/h的升温速率加热到300-500℃,在该温度段下保温5h再加热至800-900℃,在该温度段保温段进行保温3h),然后进行两次高温扩散及热变形处理,得到m50轴承钢棒材。
[0111]
其中,该两次高温扩散及热处理的步骤,包括:除900℃以下保温处理外,坯料在1000℃以下时,加热速度控制在30℃/h(即,在保温处理后,将坯料从保温处理的温度加热至1000℃,采用的加热速率为30℃/h),当坯料的温度在≥1000℃时,选取90℃/h的升温速率,缓慢升温到1200℃进行第一次高温扩散处理,第一次高温扩散处理的时间为15h;然后
炉冷降温至1130℃(降温速率为100℃/h),进行第一次热变形处理(锻造)。再将第一次热变形处理后坯料重回加热炉,选取90℃/h的升温速率再次缓慢升温到1200℃进行第二次高温扩散处理,高温扩散处理的时间为15h,高温扩散处理后再次炉冷降温至1130℃(其中,降温速率为100℃/h),进行第二次锻造热变形处理。经第二次热变形处理后形成的m50轴承钢棒材中的碳化物尺寸(最大等效直径)为21μm。
[0112]
对比例6制备的m50轴承钢棒材的微观结构参见图10所示。从图10可以明显看出:对比例6制备的m50轴承钢棒材中的碳化物尺寸较大。
[0113]
需要说明的是:对比例5、和对比例6并非是现有技术手段,而是作为对比实验,以证明本发明的步骤1)和步骤2)的协同作用,仅有步骤1)和步骤2)一起协同作用,才能实现达到“高碳中高合金钢中碳化物的最大有效直径尺寸≤8μm”的效果。
[0114]
综上,本发明实施例提供的高碳中高合金钢及其制备方法,具体地是一种通过对自耗锭的纯净度及成分偏析进行控制(参见步骤1)、关键共晶碳化物溶解及热变形控制(参见步骤2),将铸态自耗锭制备成碳化物≤8μm的均质小尺寸构件(如,块体或棒材)的制造方法。另外,采用多个本发明实施例制备的小体积的高纯净、高均质构件,可以构筑制备低偏析大尺寸金属材料,从而显著减小直至消除了粗大析出相,有效提升了材料的均质性及制备效率、减少制备成本,并大幅提升以高合金工模具钢、刀具钢及航空轴承钢为例的材料使用寿命。本发明解决了传统冶金工艺中大尺寸的析出相难以控制的问题,以块体冶金代替了传统的粉末冶金方法等,将推动冶金学科发展和技术变革。
[0115]
以上所述,仅是本发明的较佳实施例而已,并非对本发明作任何形式上的限制,依据本发明的技术实质对以上实施例所作的任何简单修改、等同变化与修饰,均仍属于本发明技术方案的范围内。