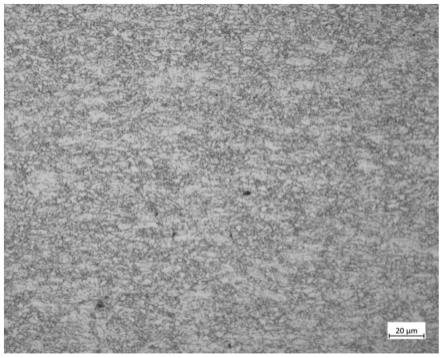
一种抗拉强度900mpa级热轧双相高耐蚀钢板及其制造方法
技术领域
1.本发明属于耐候钢板技术领域,具体涉及一种抗拉强度900mpa级热轧双相高耐蚀钢板及其制造方法。
背景技术:2.耐候钢又称为耐大气腐蚀钢,相对于普通碳钢具有良好的耐大气腐蚀性能,广泛应用于铁道车辆、集装箱、桥梁、建筑、塔架等户外长期暴露在大气中的钢结构及装备制造,延长服役寿命。耐候钢作为低碳绿色钢铁材料,可降低全生命周期对铁矿石、能源等的消耗,减少碳排放,具有广阔的推广应用前景。近年来,随着铁道车辆、集装箱等结构件向着长寿命、重载、轻量化等方向发展,耐候钢材料也向着高耐蚀、高强度发展。
3.目前,国内关于高强度热轧高耐蚀钢已申请多项专利。
4.cn101376953a公开了一种高耐蚀高强度耐候钢及其制造方法,c含量0.002%~0.005%,mn含量:0.01%~0.05%,屈服强度》700mpa,根据实施例可知其抗拉强度》800mpa,屈强比》0.85,其屈强比较高,不利于下游用户成形加工。
5.cn111349850a公开了一种高耐蚀耐候钢及其制造方法,其化学成分质量百分比含量(wt%)为:c:0.03-0.05%,si:0.03-0.05%,mn:0.8-1.2%,cu:0.1-0.2%,cr:6.8-8.2%,ni:0.05-0.15%,mo:0.15-0.25%,al:0.03-0.05%,屈服强度≥700mpa,抗拉强度≥900mpa,延伸率10-14%。其成分中cr含量较高,增加了材料的焊接难度和制造成本;另一方面,含有贵重合金mo,显著提高制造成本。
技术实现要素:6.本发明的目的在于提供一种抗拉强度900mpa级热轧双相高耐蚀钢板及其制造方法,该高耐蚀钢板具有优异的耐大气腐蚀性能、高强度和低屈强比,易成形。
7.为实现上述目的,本发明采取的技术方案如下:
8.一种抗拉强度900mpa级热轧双相高耐蚀钢板,包括以下质量百分比的化学成分:c:0.015%~0.040%、si:0.40%~0.70%、mn:0.30%~0.60%、p:0.015%~0.030%、s:≤0.002%、cr:3.00%~5.00%、ni:≤0.15%、cu:0.15%~0.30%、als:0.020%~0.050%、ti:0.010%~0.025%、h≤1.5ppm,其余为fe和不可避免的杂质元素。
9.所述抗拉强度900mpa级热轧双相高耐蚀钢板的金相组织为准多边形铁素体和粒状贝氏体的双相组织,晶粒度12~13级。
10.所述抗拉强度900mpa级热轧双相高耐蚀钢板的屈服强度r
el
≥600mpa,抗拉强度rm≥900mpa,r
el
/rm《0.80,延伸率a≥14%。
11.本发明提供的所述抗拉强度900mpa级热轧双相高耐蚀钢板的制造方法,包括以下步骤:铁水预处理深脱硫
→
转炉顶底复合吹炼
→
炉外精炼
→
连铸
→
加热
→
轧制
→
层流冷却
→
卷取。
12.所述炉外精炼步骤中,采用lf精炼+rh精炼处理,rh真空脱碳时间≥5min,控制h含
量≤1.5ppm。
13.所述连铸步骤中,钢水浇铸中包温度控制在1530℃~1550℃,采用保护渣进行保护浇铸,浇铸时液面波动≤
±
5mm,连铸坯拉速控制在1.0~1.5m/min,投用动态轻压下提高连铸坯内部质量。所述连铸板坯的厚度为230mm。
14.铸坯切割完成后直接装炉,入加热炉温度≥500℃。
15.所述加热步骤中,加热温度1200℃~1250℃,在炉时间150~200min,二加+均热时间≤100min;促进奥氏体均匀化和合金元素在奥氏体中充分固溶;同时避免加热时间过长,低熔点cu元素在奥氏体晶界富集,导致热轧卷边部产生裂纹缺陷。
16.所述轧制步骤中,粗轧阶段轧制温度控制在1050℃以上,累计压下率≥80%,在高温下进行8道次大变形,促进形变奥氏体晶粒回复再结晶,细化奥氏体细化晶粒尺寸;精轧阶段采用7机架连轧,精轧开轧温度≤1030℃,精轧终轧温度为820~880℃,累计变形量≥85%,通过累计大变形,增加形变奥氏体内的形变带和位错密度,增加铁素体相变形核点,细化相变后铁素体晶粒。
17.所述层流冷却和卷取步骤中,控制冷却速度为20~40℃/s,冷却至700~750℃进行空冷,然后以20~40℃/s冷却至550~600℃进行卷取,采用分段的冷却方式可以获得均匀细小的准多边形铁素体+粒状贝氏体双相组织。卷取后自然冷却至室温。
18.所述空冷的时间为3~6s。如果空冷时间《3s,则生成的铁素体组织少,材料强度高,延伸率低;如果空冷时间大于6s,则生成大量铁素体组织并粗化,使得材料的强度降低。
19.本发明提供的抗拉强度超过900mpa的热轧双相高耐蚀钢板中的各合金元素及其质量百分比设计原理如下:
20.c(碳):c是提高钢材强度最经济的元素,但是c含量过高会恶化钢材的焊接性能,降低塑性。因此,本发明将c含量设计为0.015%~0.040%。
21.si(硅):si能增加钢中铁素体体积分数,固溶强化提高材料强度。此外,si还有利于细化腐蚀产物,促进钢材表面形成致密的保护性锈层从而提高耐大气腐蚀性能。但是si含量过高会恶化钢材的焊接性能和表面质量。因此本发明将si含量设计为0.40~0.70%。
22.mn(锰):mn是钢中重要的固溶强化元素之一,也是炼钢过程中的重要脱氧元素。mn还能提高奥氏体稳定性,扩大奥氏体相区,促进贝氏体组织转变。但是mn含量过高不但会提高高耐蚀钢的制造成本,还会恶化钢材的焊接性能。因此,将其含量设计为0.30~0.60%。
23.als(铝):al是钢中加入的主要脱氧元素,还能与n结合在高温析出aln,细化奥氏体晶粒尺寸。但过高的al会导致钢中氧化物夹杂增加,降低钢材的低温韧性和耐大气腐蚀性能。因此,将其含量设计为0.020~0.050%。
24.cr(铬):cr是提高钢材耐大气腐蚀性能重要的合金元素,能够在钢材表面富集促进致密的与基体粘附性好的保护性锈层生成,阻止氧气、水等腐蚀性介质向集体扩散。cr还能提高材料淬透性,促进贝氏体组织生成。cr含量过高会恶化钢材的焊接性能,提高制造成本,因此将cr含量设计为3.00~5.00%。
25.cu(铜):cu能显著提高材料的耐大气腐蚀性能,与cr复合作用时提高耐大气腐蚀性能效果更佳。但是cu的熔点较低,只有1083℃,含量过高容易导致连铸漏钢,热轧过程中产生边部裂纹,因此将cu含量设计为0.15~0.30%。
26.ni(镍):ni能提高材料的自腐蚀电位,降低腐蚀倾向,提高耐大气腐蚀性能;还能
与cu反应生成高熔点的cu-ni二元合金相,有效阻止cu引起的铜脆;但ni是贵重金属元素,含量过高显著增加钢材制造成本,因此将ni含量控制在≤0.15%。
27.ti(钛):ti是强氮化物形成元素,在焊接过程中tin能抑制粗晶区奥氏体晶粒粗化,提高高耐蚀钢焊接热影响区的低温韧性。将其含量控制在0.010%~0.025%。
28.p(磷):p是提高钢材耐大气腐蚀性能最经济的元素,但是p含量过高容易在晶界偏析降低钢材的低温韧性,增加焊接裂纹敏感性。因此将p含量设计为0.015~0.030%;
29.s(硫):s是钢中的有害残余元素,易于mn反应生成mns非金属夹杂,恶化钢材的耐大气腐蚀性能和塑韧性。因此本发明将s含量设计为≤0.002%
30.h(氢):h扩散聚集易导致高强钢延迟断裂,因此本发明严格控制钢中h含量≤1.5ppm。
31.本发明采用高cr含量设计,同时添加适量的si、p、cu、ni,通过五种元素的协同作用,促进致密的α-feooh生成,降低材料的腐蚀倾向,提高耐大气腐蚀性能,实现贵重合金cu、ni的减量化,从而降低高耐蚀钢制造成本,成分中i=26.01(%cu)+3.88(%ni)+1.20(%cr)+1.49(%si)+17.28(%p)-7.29(%cu)
×
(%ni)-9.10(%ni)
×
(%p)-33.39(%cu)2≥10.0,成分中未添加微合金元素nb来提高强度,而是结合控制轧制和分段冷却工艺得到细晶准多边形铁素体+粒状贝氏体双相组织,通过细晶强化、相变强化和固溶强化综合作用,实现高强度和低屈强比控制,降低高耐蚀钢的制造成本。
32.有现有技术相比,本发明提供的抗拉强度900mpa级热轧双相高耐蚀钢板具有如下优点:
33.1)本发明钢板的力学性能:屈服强度r
el
≥600mpa,抗拉强度rm≥900mpa,r
el
/rm《0.80,延伸率a≥14%,具体为:r
el 630~750mpa,抗拉强度r
m 920~960mpa,r
el
/r
m 0.65~0.79,延伸率a15~18.5%,在具有高强度的同时,具有低屈强比。
34.2)经过180
°
冷弯d=a和双倍冷弯试样外侧面没有裂纹出现,具有良好的冷弯成形性能,便于下游用户制造加工。
35.3)本发明采用低c、低mn,高cr和cu、si、p、ni的少量多元复合成分设计,未添加微合金元素nb,通过控制轧制和分段冷却工艺,固溶强化、细晶强化和相变强化提高材料的强度,同时具有优异的耐大气腐蚀性能。
36.4)本发明采用热装轧制工艺,降低加热炉能耗和铸坯氧化烧损,提高生产效率和成材率,降低制造成本。
附图说明
37.图1为实施例2中的900mpa级热轧双相高耐蚀钢板的金相组织图;
38.图2为实施例2中的900mpa级热轧双相高耐蚀钢板双倍冷弯图。
具体实施方式
39.本发明提供的一种抗拉强度900mpa级热轧双相高耐蚀钢板,其化学成分及质量百分比为:c:0.015%~0.045%、si:0.40%~0.70%、mn:0.30%~0.60%、p:0.015%~0.030%、s:≤0.002%、cr:3.00%~5.00%、ni:≤0.15%、cu:0.15%~0.30%、als:0.020%~0.050%、ti:0.010%~0.025%、h≤1.5ppm,其余为fe和不可避免的杂质元素。
40.所述抗拉强度900mpa级热轧双相高耐蚀钢板的制造方法包括:铁水预处理深脱硫
→
转炉顶底复合吹炼
→
炉外精炼
→
连铸
→
加热
→
轧制
→
层流冷却
→
卷取,自然冷却至室温。按照上述化学成分进行钢水冶炼;
41.精炼采用“lf+rh”双联工艺处理,rh真空脱碳时间≥5min,控制h含量≤1.5ppm,钢水浇铸中包温度控制在1530℃~1550℃,采用保护渣进行保护浇铸,液面波动≤
±
5mm,连铸坯拉速控制在1.0~1.5m/min,投用动态轻压下提高连铸坯内部质量,得到的连铸板坯的厚度为230mm;
42.铸坯切割完成后直接装入加热炉,入加热炉时铸坯温度≥500℃,在加热炉内对铸坯进行加热,加热温度1200℃~1250℃,在炉时间150~200min,二加+均热时间≤100min;
43.轧制分粗轧和精轧两个阶段进行,粗轧阶段轧制温度控制在1050℃以上,累计压下率≥80%,精轧阶段采用7机架连轧,精轧开轧温度≤1030℃,精轧终轧温度为820~880℃,累计变形量≥85%;
44.精轧结束后进行层流冷却,控制冷却速度为20~40℃/s,冷却至700~750℃进行空冷,空冷时间3~6s,然后以20~40℃/s冷却至550~600℃进行卷取,卷取后自然冷却至室温。
45.各实施例及对比例中的双相钢的化学成分及质量百分比如表1所示,余量为fe和不可避免的杂质元素。
46.表1实施例及对比例化学成分
[0047][0048]
采用传统热连轧板带流程进行轧制,工艺流程包括:加热
→
轧制
→
层流冷却
→
卷取。各实施例及比较例中的主要工艺参数如表2所示。
[0049]
表2轧制及冷却工序主要工艺参数
[0050][0051]
实施例及比较例生产得到的双相钢板的力学性能如表3所示,其中,力学性能拉伸性能测试根据gb/t 228.1-2010《金属材料拉伸试验第1部分:室温试验方法》进行,冷弯性能测试根据gb/t 232-2010《金属材料弯曲试验方法》进行。
[0052]
表3力学性能
[0053][0054]
按照tb/t 2375进行72h周期浸润腐蚀试验,式样尺寸:长
×
宽
×
厚=60mm
×
40mm
×
2mm,以q345b低合金钢和q450nqr1普通耐候钢作为对比试样,试验结果如表4所示。实施例中的高耐蚀钢腐蚀失重速率相对于q450nqr1普通耐候钢降低了近1倍,具有良好的耐大气腐蚀性能。
[0055]
表4各实施例及对比试样耐大气腐蚀性能
[0056] 平均腐蚀失重速率,(g/(m2·
h))相对腐蚀率,%实施例1//实施例21.2328实施例31.1727实施例41.2128
q450nqr12.3354q345b4.32100对比例12.6862对比例21.2629对比例31.2930
[0057]
综上所述,按本发明技术方案制造的高耐蚀钢板屈服强度≥600mp,抗拉强度≥900mpa,延伸率≥14%以上,屈强比《0.80,具有优异的耐大气腐蚀性能和成形性能,制造成本较低。可应用于集装箱、铁道车辆、建筑、桥梁等户外装备和构件制造,满足长寿命要求。
[0058]
上述参照实施例对一种抗拉强度900mpa级热轧双相高耐蚀钢板及其制造方法进行的详细描述,是说明性的而不是限定性的,可按照所限定范围列举出若干个实施例,因此在不脱离本发明总体构思下的变化和修改,应属本发明的保护范围之内。