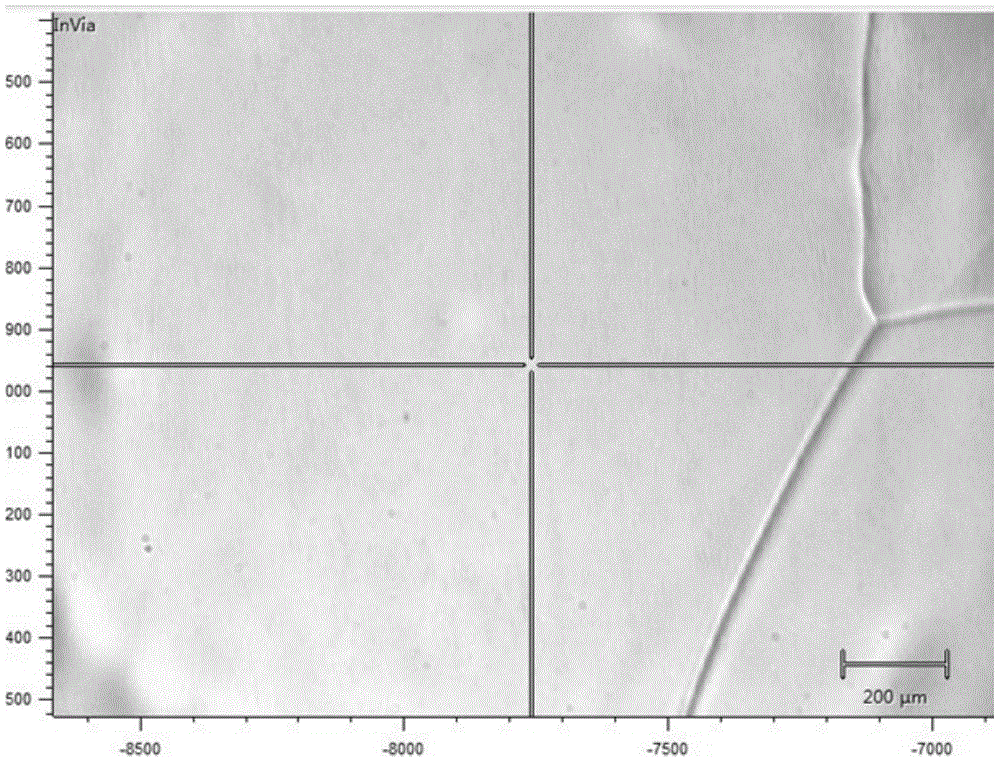
本发明涉及一种生长大面积石墨烯的装置、方法以及由此得到的石墨烯。
背景技术:随着2010年诺贝尔物理学奖得主的揭晓,石墨烯(Graphene)也成为大家讨论的焦点。2004年,英国曼彻斯特大学的安德烈·海姆和康斯坦丁·诺沃肖洛夫利用普通胶带成功地从石墨中剥离出石墨烯,这种材料仅有一个碳原子厚,是目前已知的最薄的材料。它不仅是已知材料中最薄的一种,还非常牢固而柔软;作为单质,它在室温下传递电子的速度比已知导体都快。石墨烯可以应用于晶体管、触摸屏、基因测序的领域,同时有望帮助物理学家在量子物理学研究领域取得新突破,它的问世引起了全世界的研究热潮。鉴于石墨烯具有诸多优于常规材料的性质,在理论基础研究和纳米电子学具有广阔的应用前景,因此制备大面积、高质量、低缺陷的石墨烯是一项亟待解决的首要问题。目前,石墨烯的制备方法主要有以下四种:1、微机械剥离石墨法:因为石墨晶体是片层结构,各层之间是以范德瓦尔斯力微弱的结合,因此微机械剥离石墨法主要使用微机械外力从石墨晶体表面剥离出石墨烯片层结构。该方法具有成本低,样品质量高,且片层数可控的优点,缺点是很难精确控制大小,重复性较差,产量低,效率低,难以实现石墨烯的大面积和规模化制备,且耗费时间较长,尺寸较小,即只有0.1mm左右,故而仅限于作为实验室的基础理论研究方面的应用。2、氧化石墨还原法:氧化石墨还原法是在一定的化学条件下,利用氧化反应,将环氧基、羟基、羰基和羧基等亲水性基团引入石墨结构中,得到氧化石墨,再利用还原剂还原或热处理等方法,还原氧化石墨获得石墨烯的方法。氧化石墨还原法由于其稳定性而被广泛采用。然而,氧化过程会导致大量的结构缺陷,这些缺陷即使经1100℃退火也不能完全被消除,仍有许多羟基、环氧基、羰基、羧基的残留。缺陷导致的电子结构变化使石墨烯由导体转为半导体,严重影响石墨烯的电学性能,制约了它的应用。3、在碳化硅衬底上外延生长石墨烯:该方法的核心是在对SiC衬底完成表面预处理后,利用Si具有比C更高的饱和蒸汽压的性质,在大于1100℃高温和小于10-6Pa的超高真空条件下,Si原子率先从衬底表面升华,剩余的C原子重构成石墨烯层。外延生长法制备的石墨烯表现出较高的载流子迁移率等特性,因而表现出杰出的电学性质,但由于SiC晶体表面结构较为复杂,难以获得大面积、厚度均一的石墨烯。4、金属衬底的化学气相沉积法:该方法制备石墨烯材料的机理是,在800~1200℃的高温气态条件下,气态碳氢化合物等经过具有催化活性的过渡金属表面时,在金属表面脱氢,剩余游离态的碳原子吸附在金属表面,冷却时以sp2键合形成石墨烯结构。该方法是近年来制备较大面积、高质量石墨烯比较有效的方法之一,并且可以与现有的半导体制造工艺兼容。但该种方法在目前常用的工艺下仍存在以下缺陷:(1)、生长的石墨烯面积较小,一般是2-12英寸;(2)、生产的较大面积的石墨烯样则层数不均匀,一般1~10层都有;(3)、虽然生产小面积石墨烯由于沉积比较均匀,方阻和透过率都在较高的水平。然而石墨烯样面积做的越大,由于气体和温度的差异,导致方阻和透过率表面各处差异就越大,不利于批量生产;(4)、较大面积铜箔衬底在装样和取样上都比较困难,退火后铜箔硬度会急剧下降,装配中如不能很好贴合,铜箔会发生褶皱变形,这会对之后的转片等工艺带来严重的影响,极大地影响石墨烯产品的质量。
技术实现要素:本发明的第一个目的是提供一种用于生长大面积石墨烯的装置。实现本发明第一个目的的技术方案是:一种生长大面积石墨烯的装置,包括金属衬底、卷形石英舟、固定装置和扩散炉;金属衬底的两边各设置有至少一个小孔;所述固定装置包括固定丝,所述固定丝穿过两边小孔将金属衬底固定在卷形石英舟上。所述固定装置还包括用于将金属衬底两端与卷形石英舟固定的绑条。所述生长大面积石墨烯的装置还包括进气管;所述进气管上均匀分布有出气孔;所述进气管为直管或者环绕卷形石英舟设置。本发明的第二个目的是提供一种易于实施的能生长出大面积、厚度均一、性能好的生长大面积石墨烯的方法。实现本发明第二个目的的技术方案是一种生长大面积石墨烯的方法,包括以下步骤:步骤一:准备金属衬底;用去离子水和纯度不小于99.7%的丙酮对铜箔表面进行全面的擦洗,并晾干;所述步骤二中的固定丝为无氧铜丝。步骤二:将金属衬底装样于卷形石英舟的外表面上;在金属衬底两边各打至少一个小孔,用固定丝穿过两边小孔将金属衬底固定在卷形石英舟上,用固定丝固定后,再在金属衬底两端绑上绑条。步骤三:将步骤二的包含金属衬底的卷形石英舟放入扩散炉内进行沉积;在此可以采用两种方式,一种是两步沉积法:a、将扩撒炉内压力抽到100pa以下,保压30分钟,确保扩散炉真空系统稳定后,向扩散炉内通氩气至常压;此过程重复两次,氩气流量为1000sccm;b、将扩散炉升温至950~1050℃,升温过程中采用氩气和氢气保护,该过程中通氩气和氢气的流量分别为500~2000sccm和500~1000sccm,达到目标温度后,关闭氩气和氢气;c、将扩散炉真空抽到1~100pa,然后向扩散炉内通入氢气和烃类气体或液体碳源,在该温度和压力下沉积10~20min;d、关闭氢气和烃类气体或液体碳源,将扩散炉真空抽到1~100pa,然后关闭抽气泵;向扩散炉内通入氢气和烃类气体或液体碳源,直到压力升高到1.1~1.5Kpa后关闭所有气体;在该温度和压力下沉积3~10min;e、沉积过程结束后,立即抽去扩散炉内反应后的残留气体,降温冷却,在氩气和氢气保护下降温,氩气流量1000sccm,氢气流量为100~200sccm。c步和d步中的氢气和烃类气体或液体碳源的纯度为99.999%;c步中烃类气体或液体碳源的流量为400~600sccm,氢气流量为20~40sccm;d步中烃类气体或液体碳源的流量为100~200sccm,氢气流量为100~200sccm。另一种是三步沉积法:a、将扩撒炉内压力抽到100pa以下,保压30分钟,确保扩散炉真空系统稳定后,向扩散炉内通氩气至常压;此过程重复两次,氩气流量为1000sccm;;b、将扩散炉升温至950~1050℃,升温过程中采用氩气和氢气保护,该过程中通氩气和氢气的流量分别为500~2000sccm和500~1000sccm,达到目标温度后,关闭氩气和氢气;c、将扩散炉真空抽到1~100pa,然后向扩散炉内通入氢气和烃类气体或液体碳源,在该温度和压力下沉积10~20min;d、将扩散炉真空抽到1~100pa,然后向扩散炉内通入氢气和烃类气体或液体碳源,在该温度和压力下沉积5~10min;e、关闭氢气和烃类气体或液体碳源,将扩散炉真空抽到1~100pa,然后关闭抽气泵;向扩散炉内通入氢气和烃类气体或液体碳源,直到压力升高到1.1~1.5Kpa后关闭所有气体;在该温度和压力下沉积3~10min;f、沉积过程结束后,立即抽去扩散炉内反应后的残留气体,在氩气和氢气保护下降温,氩气流量1000sccm,氢气流量为100~200sccm;c步和d步和e步中的氢气和烃类气体或液体碳源的纯度为99.999%;c步中烃类气体或液体碳源的流量为400~600sccm,氢气流量为20~40sccm;d步中烃类气体或液体碳源的流量为40~60sccm,氢气流量为20~40sccm;e步中烃类气体或液体碳源的流量为100~200sccm,氢气流量为100~200sccm。步骤四:冷却,取样。冷却后,裁断绑条和固定丝,拖住裁断的绑条沿切线方向将生长石墨烯的金属衬底转移到亚克力板上。本发明的第三个目的是提供一种无褶皱、层数均匀的石墨烯。实现本发明的第三个目的的技术方案是,采用前述的装置和制备方法,从而得到无这周、层数均匀的大面积的石墨烯。本发明得以实现的原理在于:一般石英管尺寸不会很大,其他形状石英器件不利于装配大面积石墨烯薄膜。而卷形石英舟因为其卷形结构,一方面不会造成铜箔的褶皱,另一方面也使得装配大面积铜箔成为可能。例如同样粗细的石英管中,平板结构能装配的铜箔面积远小于卷形石英舟;而普通石英舟在装配大面积的铜箔时,铜箔中部没有支撑,就容易下沉产生褶皱,最终影响石墨烯的品质。本发明所使用的装置以及装样和取样方法,卷形石英舟可以给铜箔一个很好的支撑,装样时在确保铜箔固定不会脱落的情况下,尽可能大的保证了石墨烯沉积基底铜箔的有效面积。取样时,由于生长石墨烯薄膜的铜箔面积大,不像小面积铜箔那么容易取出不产生褶皱划痕。采用了上述技术方案后,本发明具有以下有益的效果:(1)本发明创新地利用卷型石英舟来作为铜箔承载装置,将铜箔装配在卷形石英舟外表面,然后仅用固定丝固定,能最大面积的装配铜箔和沉积石墨烯,而且由于铜箔始终有卷形石英舟给予支撑,在装样、沉积、取样时都不会产生褶皱,因此不仅面积较工业化生产和实验室实验样品大很多(可以做到大于0.5m2)、层数均匀(1~3层)、方阻和透过率均匀,而且如此大面积石墨烯转样后表面光滑平整无褶皱,由此同时解决了现有技术中石墨烯制备装置无法生产层数一致、方阻和透过率均匀的大面积石墨烯样的问题和现有技术对于生产大面积石墨烯在装样、取样、转压过程中易产生褶皱的问题。(2)本发明的装置里的进气管上设置小的气孔,这样能更加确保在扩散炉内气压均匀,进一步提高了石墨烯的品质。而且进气管可以环绕卷形石英舟设置,气孔均匀分布,这样效果更好。(3)本发明的装样方法在确保铜箔固定不会脱落的情况下,尽可能大的保证了石墨烯沉积基底铜箔的有效面积,而取样方法能最大程度的保证在如此大面积的铜箔从卷形石英舟上转移下来时不产生褶皱。(4)采用现有的CVD工艺参数来制备大面积石墨烯薄膜时会导致石墨烯样层数不均匀,方阻透过率不均匀,而本发明CVD法所选择的工艺参数能进一步确保制备出来的石墨烯薄膜层数均匀,方阻透光率良好。特别是采用三步沉积的工艺及工艺参数的选择使得制备后铜箔软硬程度以及制备过程中工艺原因使得铜箔所发生的形变不同与卷形石英舟的装片卸片手法共同影响则可以做到外观更加平整,品质更好。附图说明为了使本发明的内容更容易被清楚地理解,下面根据具体实施例并结合附图,对本发明作进一步详细的说明,其中图1为本发明沉积前将铜箔与卷形石英舟固定的示意图。图2为本发明应用例2沉积的大面积石墨烯的表面形貌(200倍)。从该图看出铜箔表面沉积的石墨烯连续、平整光滑、无缺陷。图3为本发明引用例2沉积的石墨烯的拉曼光谱。附图中标号为:金属衬底1、小孔11、卷形石英舟2、固定丝3、绑条4。具体实施方式见图1,本实施例的生长大面积石墨烯的装置包括金属衬底1、卷形石英舟2、固定装置、进气管和扩散炉;金属衬底1的两边各设置有至少一个小孔11;卷形石英舟2由两个支撑角支撑放置在扩散炉内。固定装置包括固定丝3和绑条4,固定丝3穿过两边小孔11将金属衬底1固定在卷形石英舟2上。绑条4将金属衬底1两端与卷形石英舟2固定。进气管上均匀分布有出气孔。采用前述的装置生长大面积石墨烯的方法包括以下步骤:步骤一:准备金属衬底1;采用铜箔作为金属衬底1,用去离子水和纯度不小于99.7%的丙酮对铜箔表面进行全面的擦洗,并晾干;步骤二:将金属衬底1装样于卷形石英舟2的外表面上;固定丝3为无氧铜丝;在金属衬底1两边各打至少一个小孔11,用固定丝3穿过两边小孔11将金属衬底1固定在卷形石英舟2上;再在金属衬底1两端绑上绑条4,如图1所示。步骤三:将步骤二的包含金属衬底1的卷形石英舟2放入扩散炉内进行沉积;a、将扩撒炉内压力抽到100pa以下,保压30分钟,确保扩散炉真空系统稳定后,向扩散炉内通氩气至常压;a步过程重复两次,氩气流量为1000sccm;b、将扩散炉升温至950~1050℃;升温过程中采用氩气和氢气保护,该过程中通氩气和氢气的流量分别为500~2000sccm和500~1000sccm,达到目标温度后,关闭氩气和氢气;c、将扩散炉真空抽到1~100pa,然后向扩散炉内通入氢气和烃类气体或液体碳源,在该温度和压力下沉积10~20min;氢气和烃类气体或液体碳源的纯度为99.999%;烃类气体或液体碳源的流量为400~600sccm,氢气流量为20~40sccm;d、关闭氢气和烃类气体或液体碳源,将扩散炉真空抽到1~100pa,然后关闭抽气泵;向扩散炉内通入氢气和烃类气体或液体碳源,直到压力升高到1.1~1.5Kpa后关闭所有气体;在该温度和压力下沉积3~10min;氢气和烃类气体或液体碳源的纯度为99.999%;烃类气体或液体碳源的流量为100~200sccm,氢气流量为100~200sccm;e、沉积过程结束后,立即抽去扩散炉内反应后的残留气体,在氩气和氢气保护下降温冷却,氩气流量1000sccm,氢气流量为100~200sccm。步骤四:冷却,取样:冷却后,裁断绑条4和固定丝3,拖住裁断的绑条4沿切线方向将生长石墨烯的金属衬底1转移到亚克力板上。下面进行六个应用例,表一为采用两步沉积法的三个应用例的具体工艺参数:表一应用例1应用例2应用例3铜箔尺寸400x1000mm500x1000mm600x1200mmb步升温目标温度950℃1000℃1050℃b步氩气流量500sccm1500sccm2000sccmb步氢气流量500sccm750sccm1000sccmc步扩散炉压力1pa50pa100pac步沉积时间10min15min20minc步烃类或碳源流量甲烷400sccm甲苯500sccm乙醇600sccmc步氢气流量20sccm30sccm40sccmd步扩散炉压力1pa50pa100pad步升压目标压力1.1Kpa1.3Kpa1.5Kpad步沉积时间3min7min10mind步烃类或碳源流量甲烷100sccm甲苯150sccm乙醇200sccmd步氢气流量100sccm150sccm200sccme步氢气流量100sccm150sccm200sccm表二为采用三步沉积法的三个应用例的具体工艺参数:表二:应用例1应用例2应用例3铜箔尺寸400x1000mm500x1000mm600x1200mmb步升温目标温度950℃1000℃1050℃b步氩气流量500sccm1500sccm2000sccmb步氢气流量500sccm750sccm1000sccmc步扩散炉压力1pa50pa100pac步沉积时间5min8min10minc步烃类或碳源流量甲烷400sccm甲苯500sccm乙醇600sccmc步氢气流量20sccm30sccm40sccmd步扩散炉压力1pa50pa100pad步沉积时间5min7min10mind步烃类或碳源流量甲烷40sccm甲苯50sccm乙醇60sccmd步氢气流量20sccm30sccm40sccme步扩散炉压力1pa50pa100pae步升压目标压力1.1Kpa1.3Kpa1.5Kpae步沉积时间3min7min10mine步烃类或碳源流量甲烷100sccm甲苯150sccm乙醇200sccme步氢气流量100sccm150sccm200sccmf步氢气流量100sccm150sccm200sccm为便于对比,在此以现有的气相沉积法做三个对比例:对比例1:卷形石英舟,一步沉积;对比例2:卷形石英舟,两步沉积,参数不同;对比例3:石英斜板,两步沉积;表三:对例1对比例2对比例3铜箔尺寸70x150mm140x150mm100x200mmb步升温目标温度1000℃1000℃1000℃b步氩气流量2000sccm1500sccm2000sccmb步氢气流量700sccm750sccm750sccmc步扩散炉压力5pa5pa5pac步沉积时间5min10min12minc步烃类或碳源流量甲烷50sccm甲烷100sccm甲烷150sccmc步氢气流量10sccm15sccm20sccme步氢气流量100sccm100sccm100sccm对以上六个应用例和三个对比例进行检测,各检测结果如下表四:表四由表二的对比可知,本发明的方法制备的大面积石墨烯样品大、层数均匀、方阻和透过率均匀,转样后表面光滑平整无褶皱(如图2和图3,应用例2的显微镜图片和拉曼光谱可进一步印证。以上所述的具体实施例,对本发明的目的、技术方案和有益效果进行了进一步详细说明,所应理解的是,以上所述仅为本发明的具体实施例而已,并不用于限制本发明,凡在本发明的精神和原则之内,所做的任何修改、等同替换、改进等,均应包含在本发明的保护范围之内。