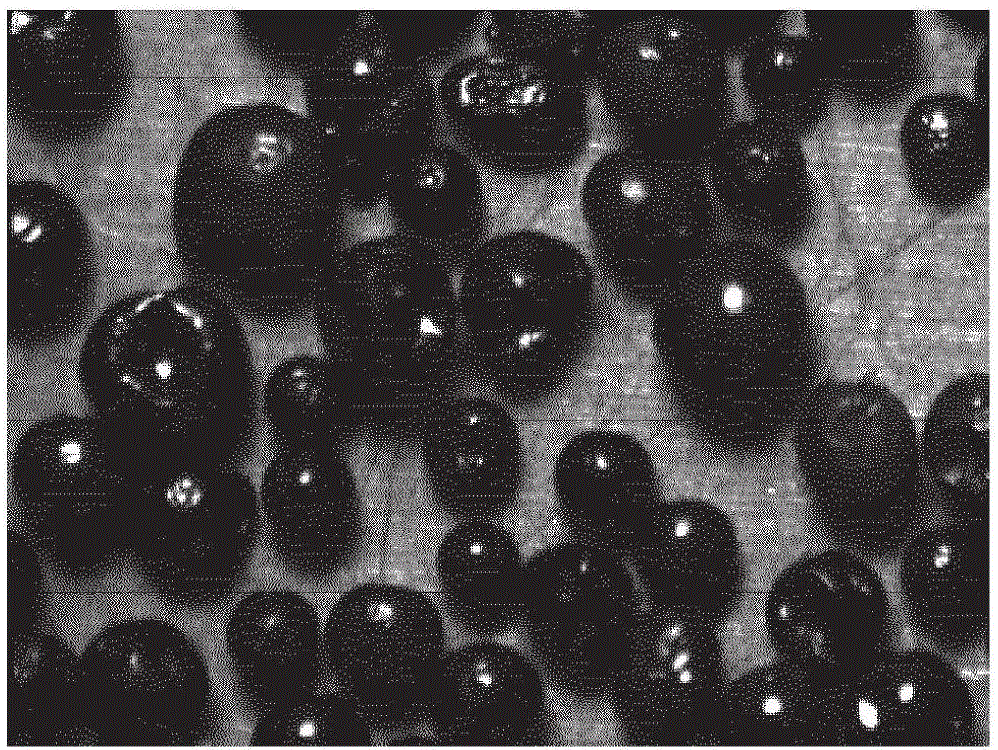
本申请要求2014年6月3日提交的美国临时专利申请第62/007,180号的优先权和权益,通过引用将该申请的内容纳入本文。
技术领域:
本公开涉及包括支撑剂、屋顶铺设粒料和催化剂载体的颗粒状炉渣产品及其制备方法。背景炉渣是冶金炉中进行金属生产工艺的副产物。虽然产生的炉渣的组成和量很大程度上取决于具体的工艺,炉渣通常包括金属氧化物与二氧化硅的混合物,产生的炉渣的量为所述工艺产生的金属量的大约10%至数倍。在金属生产过程中,炉渣以熔融形式存在于冶金炉中。炉渣的温度取决于所述工艺,但可以是约1500-1600℃量级。熔融炉渣周期性地从炉中排出(tapped),通常使其进行空气冷却和凝固,热量流失至环境。凝固的炉渣可以加工为一系列市售商品,如混凝土掺混物或纤维绝缘材料,但大量炉渣继续被丢弃为废物。近来对使用颗粒状炉渣作为油气生产中的支撑剂或作为屋顶铺设粒料产生兴趣。但是,运输、研磨和/或再熔融凝固的炉渣用于这种材料的生产涉及的费用使这些应用经济上不具吸引力。此外,用来将炉渣转化为产品如支撑剂或屋顶铺设粒料的方法整体上不令人满意,并且使这些材料不能满足一种或多种产品需求。例如,需要支撑剂具有特定的强度、尺寸、性质和组成性质。很难制备具有支撑剂所需的所有性质的炉渣颗粒,同时保持使用炉渣而不是其他原材料的经济利益。仍存在对将炉渣转化为商业可行的粒料产品的简单的经济上可行的方法以及对通过该方法制备的粒料产品如支撑剂和屋顶铺设粒料的需求。发明概述在一个实施方式中,提供一种用于从熔融炉渣组合物制备固体炉渣粒料的方法。所述方法包括:(a)提供所述熔融炉渣组合物;(b)在分散设备中将所述熔融炉渣组合物转化为固体炉渣粒料;以及(c)在分离器中根据形状对所述固体炉渣粒料进行分选,以制备具有不同球度的多个部分(fraction)。在另一个实施方式中,提供一种颗粒状炉渣产品,所述颗粒状炉渣产品包括由本文所述方法制备的固体炉渣粒料的一个或多个部分。所述颗粒状炉渣产品可包括支撑剂、屋顶铺设粒料、催化剂载体,可以是多孔或非多孔的,并且可以是涂覆或未涂覆的。在另一个实施方式中,所述分散设备包括雾化设备,所述将熔融炉渣组合物转化为固体炉渣粒料的步骤包括通过在所述分散设备中将所述熔融炉渣组合物与气体物流接触来雾化所述熔融炉渣组合物。在一些实施方式中,所述气体物流包括空气。在另一个实施方式中,所述雾化设备包括送风机,所述雾化熔融炉渣组合物包括使用所述送风机将所述气体物流吹入所述分散设备中所述熔融炉渣组合物的下降物流,从而将所述熔融炉渣组合物的下降物流分离成液滴,所述液滴凝固以形成所述固体炉渣粒料。在一些实施方式中,所述送风机适于产生小于约80英寸水压的最大总压力。在另一个实施方式中,所述固体炉渣粒料是非多孔性的。在另一个实施方式中,通过所述分选产生的所述部分中的至少一种由平均球度大于0.6的固体炉渣粒料组成。在一些实施方式中,所述固体炉渣粒料的平均球度和/或圆度为0.7至约0.9。在另一个实施方式中,通过所述分选产生的所述部分中的至少一种由平均球度小于0.6的固体炉渣粒料组成,所述固体炉渣粒料可包括伸长的粒料。所述伸长的粒料可包括哑铃-形状的粒料和/或断裂的哑铃-形状粒料。在另一个实施方式中,所述雾化设备还包括冲击板,至少一些固体炉渣粒料通过将液滴撞击所述冲击板制备,其中通过将液滴撞击所述冲击板制备的所述固体炉渣粒料的平均球度小于约0.6。在另一个实施方式中,所述方法还包括通过密度对所述固体炉渣粒料进行分选的步骤。在另一个实施方式中,所述方法还包括在分散设备中将熔融炉渣组合物转化为固体炉渣粒料的步骤之前和/或同时将熔融炉渣组合物与密度降低添加剂混合的步骤。根据本实施方式制备的固体炉渣粒料可以具有内部空穴。在一些实施方式中,将熔融炉渣组合物与密度降低添加剂混合的步骤包括将所述密度降低添加剂注入所述熔融炉渣组合物中。所述密度降低添加剂可选自下组:液态水、蒸汽、炭、碳酸金属盐及其任意两种或更多种的混合物。在一些实施方式中,将熔融炉渣组合物与密度降低添加剂混合的步骤包括在将熔融炉渣组合物转化为固体炉渣粒料之前通过向所述熔融炉渣组合物中注入水和/或蒸汽来使所述熔融炉渣组合物膨胀。在另一个实施方式中,所述方法还包括在涂覆设备中对至少一些所述固体炉渣粒料进行涂覆的步骤。在一些实施方式中,所述涂覆步骤包括用涂料组合物涂覆所述固体炉渣粒料,所述涂料组合物选自树脂组合物和陶瓷组合物。在通过所述分选制备的部分中的至少一种由平均球度大于0.6的固体炉渣组成,并且所述涂料组合物包括树脂组合物的一些实施方式中,所述涂覆步骤可以在通过形状对所述固体炉渣颗粒进行分选的步骤之后进行。在所述涂覆步骤包括将树脂组合物与所述固体炉渣粒料合并的一些实施方式中,对所述固体炉渣粒料加热至足以熔化所述树脂组合物的温度,所述方法还包括用所述树脂组合物对所述固体炉渣粒料进行滚转(tumbling),以制备聚合物涂覆的炉渣粒料。在所述涂覆步骤包括将树脂组合物与固体炉渣粒料合并的一些实施方式中,所述方法还可包括在所述涂覆步骤过程中或所述涂覆步骤之后对所述树脂组合物进行固化。所述固化步骤包括用交联活化剂对所述树脂组合物进行交联,其中所述交联活化剂包含在所述树脂组合物中。在通过所述分选制备的至少一个部分由平均球度大于0.6的所述固体炉渣粒料组成并且通过所述分选制备的至少一个部分由平均球度小于0.6的所述固体炉渣粒料组成的实施方式中,平均球度大于0.6的固体炉渣粒料与平均球度小于0.6的固体炉渣粒料之比可以通过调节以下一个或多个参数进行控制:(a)所述熔融炉渣组合物的温度;以及(b)气体物流和所述熔融炉渣组合物的下降物流之间的角度,其中所述分散设备包括雾化设备。在另一个实施方式中,所述熔融炉渣组合物包括游离铁,并且在所述熔融炉渣组合物的雾化过程中金属铁基本上完全被氧化,因此,所述固体炉渣粒料基本上是非磁性的。在另一个实施方式中,所述方法还包括以下步骤:(i)在冶金炉中提供所述熔融炉渣组合物;(ii)从所述冶金炉中回收所述熔融炉渣组合物;(iii)将所述熔融炉渣组合物保持在足够高的温度以防止其凝固的同时,将所述熔融炉渣组合物运送至所述分散设备。在一些实施方式中,在将所述熔融炉渣组合物从炉中回收之后直至其转化为所述固体炉渣粒料,所述熔融炉渣组合物的冶金组成保持恒定。在另一个实施方式中,通过形状分离所述粒料的装置包括螺旋分离器。在另一个实施方式中,所述熔融炉渣组合物基本上不含石灰。在另一个实施方式中,所述熔融炉渣组合物是有色金属类炉渣。在另一个实施方式中,提供一种颗粒状炉渣产品,所述颗粒状炉渣产品包括由本文所述方法制备的固体炉渣粒料的一个或多个部分,所述方法可包括熔融炉渣组合物的气体雾化。所述颗粒状炉渣产品可包括屋顶铺设粒料,非多孔支撑剂,多孔颗粒状炉渣产品,催化剂载体和/或涂覆的支撑剂。所述颗粒状炉渣产品可包括平均球度大于0.6的固体炉渣粒料;被任选地固化或部分固化的树脂组合物涂覆的固体炉渣粒料;和/或平均球度小于0.6的固体炉渣粒料。附图的简要说明现将参照附图仅以示例的方式描述本发明,附图中:图1是本文所述的方法的一个实施方式的示意图;图2A-2D是通过本文所述方法制备的涂覆或未涂覆的炉渣粒料在粉碎之前和之后的照片,其中图2A显示未涂覆的20/40炉渣粒料;图2B显示树脂涂覆的20/40炉渣粒料;图2C显示在10,000psi条件下粉碎的树脂涂覆的20/40炉渣粒料;图2D显示在10,000psi条件下粉碎的未涂覆的炉渣粒料(图2D);图3显示树脂涂覆的炉渣粒料的截面扫描电子显微镜照片;以及图4A和4B显示将常规陶瓷支撑剂颗粒(图4A)与根据本文所述方法制备的炉渣颗粒(图4B)的光滑度、球度和圆度进行比较的截面扫描电子显微镜照片。发明详述以下是对由冶金工艺生产的炉渣组合物制备市售颗粒产品的方法的详细描述。本文描述的三种颗粒产品为:用于油气回收的支撑剂、屋顶铺设粒料和催化剂载体。支撑剂是注入油田或气田周围区域中诱导产生的水力压裂的颗粒,以防止压裂闭合并提供油或气可通过其中进入井内的多孔通路。支撑剂需要具有多种性质,包括高压缩强度、耐酸溶解性、耐浸提性和球形形状。屋顶铺设粒料是施用于沥青屋面板和壁板的颗粒,其向这些建筑材料提供特征性质地和外观。屋顶铺设粒料通常设置有陶瓷涂料和颜料,其在窑内施用。炉渣粒料可用作多种类型催化剂的催化剂载体,可以用催化剂颗粒涂覆用于该目的。或者,所述颗粒本身可用作催化剂,这取决于其组成。当催化剂为颗粒多孔床的形式时,用于该目的的炉渣粒料的重要性质是球度和粒度分布。颗粒的孔隙率也是重要的。虽然对支撑剂、屋顶铺设粒料和催化剂载体的制备进行以下描述,但应理解本文所述方法可应用于制备宽泛的多种颗粒产品,包括磨料。本文所述的方法中使用的起始材料是炉渣组合物。通常这些炉渣组合物是金属制备工艺的副产物。用于本文所述方法的炉渣组合物可具有多种组成,这取决于它们来源的工艺。本文使用的炉渣组合物可以是铁类的或有色金属类的。铁类炉渣在钢生产过程中产生,通常包含石灰、二氧化硅、氧化铝和氧化镁,并且还可包含游离铁。有色金属类炉渣在用于制备有色金属如铜、镍和铅的冶炼工艺中产生。有色金属类炉渣可包括不同量的二氧化硅、氧化铁、氧化镁和石灰。当本文所述的炉渣粒料用作屋顶铺设粒料时,由于石灰与水结合产生氢氧化钙,氢氧化钙能降低其中使用炉渣粒料的屋顶或壁板的耐候特征,因此,希望避免包含大量石灰的铁类炉渣。因此,当炉渣粒料用作屋顶铺设粒料时,有色金属类炉渣和/或基本上不含石灰的炉渣是优选的。为了使本文所述的粒料产品的制备效率最大化,希望避免对之前已冷却和凝固的炉渣进行粉碎和/或熔融。因此,在本文所述的实施方式中,金属生产过程中产生的熔融炉渣组合物从冶金炉中回收,并在其从所述炉转移至分散设备时保持在熔融状态。以这种方式,所述方法保存熔融炉渣的热量并降低或减少增加热能将熔融炉渣转化为固体颗粒的需求,同时消除机械研磨所述炉渣的需求。但是,应理解,本文所述方法的很多优点不在于保存熔融炉渣的热量,无论熔融炉渣的热量是否得到保存或者在再熔融和转化为固体粒料之前是否允许炉渣冷却和凝固都能实现这些优点。图1是描述制备支撑剂、屋顶铺设粒料和/或催化剂载体的方法的示意图。炉内的炉渣在略高于其熔化温度的温度条件下保持在熔融状态。熔融炉渣的温度取决于具体工艺,在炼钢工艺中温度范围为约1500-1600℃,炉渣被过热,高于其熔化温度约40-150℃。对于有色金属类炉渣,熔融炉渣的温度范围为约1000-1700℃。但是,应理解炉渣温度不限于本文提到的范围,取决于产生炉渣的方法。熔融炉渣周期性地从炉中排出,直接排入可移动炉渣容器或炉渣流槽或浇道,熔融炉渣从中运送至工厂的另一区域。运送过程中,炉渣保持在熔融状态。炉渣通常以间歇基准排出。在一个实施方式中,熔融炉渣从炉渣容器转移至分散设备,在分散设备中熔融炉渣转化为固体炉渣颗粒。分散设备可包括如美国专利第3,584,142号和5,944,861号所述的包括转鼓的成丸设备,或雾化设备。但是,成丸设备通常产生直径为约0.15-13mm的炉渣粒料,大部分颗粒的直径在1.5-10mm范围内。具有该直径的颗粒更适于用作混凝土骨料。以下描述关注于分散设备为雾化设备的实施方式,其中熔融炉渣被气体物流雾化,所述气体物流可包括空气。与成丸机产生的炉渣粒料相比,雾化产生具有较小粒径和较窄粒径分布的炉渣粒料,雾化颗粒更适用于作为支撑剂和屋顶铺设粒料。雾化设备可包括紧邻冶金炉的气体雾化车间(plant),从而可以在将炉渣从炉转移至气体雾化车间时将炉渣保持在熔融状态。例如,所述气体雾化车间和所述炉的分隔间距小于约1km。在本实施方式中,熔融炉渣直接从所述炉转移至雾化设备,从而使熔融炉渣的热量损失和凝固最小化。在一些实施方式中,熔融炉渣不进行任何中间加工,例如添加添加剂以改变熔融炉渣的组成或性质。但是,在其他实施方式中,在雾化设备内部将熔融炉渣转化为固体炉渣粒料之前和/或同时可以将熔融炉渣与密度降低添加剂混合。例如,在一些实施方式中,密度降低添加剂可以注入熔融炉渣组合物中,并且可以选自液态水、蒸汽、炭或碳酸金属盐中的一种或多种。将熔融炉渣与密度降低添加剂混合使熔融炉渣膨胀,在雾化设备中对膨胀炉渣的雾化产生具有内部空穴的固体炉渣粒料,因此与不采用密度降低添加剂制备的固体炉渣粒料相比密度更低,孔隙率更高。添加水通常得到具有内部空穴和非多孔外表面的粒料,而添加炭或金属氧化物通常得到具有内部空穴和多孔外表面的粒料。在制备支撑剂和催化剂载体时,提供调节的密度和孔隙率的能力是有利的。例如,在雾化设备中,密度降低添加剂如蒸汽和液态水可以结合到气体物流中,以调节固体炉渣粒料的性质和/或组成。其他可能的添加剂包括炭和碳酸金属盐,以改变固体炉渣粒料的密度、孔隙率和/或组成。同样,可以向气体物流加入金属氧化物以改变炉渣粒料的组成。在一些实施方式中,制备低孔隙率固体炉渣粒料用作支撑剂、屋顶铺设粒料和/或催化剂载体是有利的。例如,本发明人发现气体-雾化的炉渣粒料,特别是由非膨胀熔融炉渣组合物产生的那些炉渣粒料具有低孔隙率。在粒料随后进行涂覆的情况下,在屋顶铺设粒料(陶瓷的并在窑中涂覆颜料)和催化剂载体的情况下,或在涂覆的支撑剂的情况下是有利的,以下将进一步讨论。由于希望降低需要的涂覆材料的量以提供均匀涂层,低孔隙率是有利的。此外,发明人发现用含氧气的气体如空气进行气体雾化趋向于氧化炉渣中的任意游离金属,如铁。减少或消除炉渣粒料中的游离铁是有利的,这降低了粒料的磁性,并降低颗粒生锈的趋势。这对于支撑剂和屋顶铺设粒料来说都是希望的。在气体雾化车间内,从炉渣容器或流槽倾倒熔融炉渣,使其通过雾化室下降,向该雾化室中吹入来自送风机的气体物流。当气体物流接触下降炉渣的熔融物流时,炉渣同时分离成液滴并冷却至固态,从而形成固体炉渣粒料,该固体炉渣粒料降落至所述室底部。向送风机输入的气体可包括常压气体,而非现有技术空气雾化工艺中通常使用的压缩气体。使用常压气体使得雾化设备能使用常规送风机,而非相对复杂的成本更高的压缩气体注入系统。送风机可以是能产生小于约80英寸水压,或约20kPa的最大总压力的类型。需要支撑剂颗粒为球形,球度大于约0.60。可以对本方法进行优化,从而主要产生具有高球度的适于用作支撑剂的固体炉渣颗粒。可以对参数进行调节以优化球形颗粒的制备,所述参数包括进入雾化室的熔融炉渣的温度;雾化室中气体物流相对于熔融炉渣下降物流的角度;流槽的宽度相对于送风机气体喷嘴的宽度;以及气体/炉渣比。对通过雾化设备产生的固体炉渣粒料进行回收,进一步加工为市售产品。低压雾化设备将产生一部分球形粒料(如本文所述球度大于0.60)和一部分非球形粒料(如本文所述球度小于0.60)。为了最大化适合用作支撑剂的球形粒料的制备,本实施方式采用形状分离步骤,其将固体炉渣粒料分成至少两种分离的部分。这些部分中的一种主要包含球形炉渣粒料,另一部分主要包含非球形炉渣粒料。本发明人发现该形状分离能制备包含一部分高球度炉渣粒料的颗粒状炉渣产品。例如,支撑剂颗粒推荐的球度和圆度为0.6,对于高强度支撑剂为0.7。发明人发现根据本方法产生的球度固体炉渣粒料具有高达约0.90的球度和/或圆度,根据Krumbein和Sloss图表所定义,如题为“水力压裂和砾石填充操作中使用的支撑剂的性质测量(MeasurementofPropertiesofProppantsUsedinHydraulicFracturingandGravel-PackingOperations)”,2008年5月,第一版,ANSI/API推荐的做法(RecommendedPractice)19C所示。球度与颗粒接近球体形状的程度,即,颗粒表面积接近对应的球体表面积的程度有关。圆度是颗粒边缘形状的度量,而不考虑颗粒的形状。发明人还发现通过本方法产生的固体炉渣粒料具有高圆度和高表面光滑度/低表面粗糙度。表面粗糙度可定义为算术平均表面粗糙度(Ra),它是距离表面轮廓的平均海拔的单个深度/高度的平均值。从图4A和4B可以看出,本方法制备的炉渣粒料(图4B)与常规陶瓷支撑剂颗粒(图4A)相比,具有改进的光滑度、球度和圆度。当炉渣粒料用作支撑剂或催化剂载体时,预期这些改进的形状是特别有利的,这是因为预期它们能提供改进的压缩强度并改进这种颗粒床的孔隙率。同时,预期这种颗粒的涂层消耗较少量的涂覆材料。当炉渣粒料用作屋顶铺设粒料时,改进的圆度也是有利的,这是因为在安装涂覆有该粒料的屋顶板时,其减少了颗粒的尖锐边缘伤害屋面工的可能性。形状分离步骤可以通过螺旋分离器进行,螺旋分离器可包括用于将球形颗粒与非球形颗粒分离的常规干燥螺旋分离器。螺旋分离器是简单的设备,其包括塔,在塔周围缠绕有在其内边缘处具有开口的向内包括的螺旋槽和在其外边缘处的收集槽。与非球形颗粒相比,球形颗粒加速至更高的速度。球形颗粒在螺旋的外边缘上滚动并且被捕获在外收集槽中。非球形颗粒朝向内边缘滚动并通过狭缝落下以收集在分离器的底部。除了形状分离步骤,希望进行额外的分离,以使粒料产品的其他性质最大化。例如,除了形状分离,希望基于尺寸分离固体炉渣粒料。尺寸分离可以产生具有预定粒径分布的固体炉渣粒料部分,这是一些应用所需的。除了形状分离,希望基于密度分离固体炉渣粒料。这可以例如通过使用螺旋分离器(可以是与形状分离使用的相同的分离器)完成。或者,密度分离可以以雾化过程中颗粒行进的距离为基础通过分离不同的炉渣粒料部分进行。如上所示,来自送风机的气体物流将导致熔融炉渣形成液滴,液滴凝固并降至雾化室的底板。气体物流相对于熔融炉渣的下降物流成一定角度,因此,炉渣粒料在降落至所述室底板之前发生水平位移。较重或密度较大的颗粒趋向于降落至接近送风机,而较轻、密度较小的颗粒水平位于距送风机的距离较大的位置。该密度分离步骤可用于制备某些产品,如支撑剂。例如,可以使用密度分离以排除密度太大不能用作支撑剂的高密度颗粒。同样,高密度粒料通常在组成上与较低密度粒料不同,与较低密度粒料相比具有较高的金属含量。因此,密度分离步骤可用于分离出化学组成不适合用作支撑剂的粒料,例如,考虑耐浸提性、压缩强度等。对于屋顶铺设粒料,希望排除含游离铁的较高密度的粒料,这是由于粒料中包含的任意游离铁会生锈并导致屋顶铺设粒料褪色,同时还因为游离铁的磁性可能导致含铁粒料粘附于制备屋顶铺设粒料时使用的设备。如上所述,熔融炉渣的气体雾化产生非球形的固体炉渣粒料的至少一部分。非球形粒料特别适合用作屋顶铺设粒料。甚至对气体雾化方法进行优化用于制备球形炉渣粒料时,一部分炉渣粒料将是非球形的,适合用作屋顶铺设粒料。例如,一些液滴在成为球形之前凝固,具有伸长的形状。同样,液滴可能粘着在一起形成非球形粒料,或者通过不完全凝固的粒料的变形形成哑铃形状的伸长粒料。可以对上述气体雾化的条件进行调节,以使非球形颗粒的生产最大化。此外,可以将冲击板放置在雾化室中,放置在气体雾化产生的液滴的通路上。液体或部分凝固的液滴将撞击所述板,导致它们变形和/或破裂成为适合用作屋顶铺设粒料的非球形形状。凝固的非球形颗粒可以从雾化室中回收,可以进行任意上述形状分离、尺寸分离或密度分离,以使非球形固体炉渣粒料的某些性质最大化。例如,可以使用形状分离,以使产品中存在的非球形粒料的比例最大化。当非球形炉渣粒料包括显著比例的伸长炉渣粒料(如哑铃形状粒料)时,所述方法可包括轻质粉碎(lightcrushing)步骤以使这些颗粒破裂。在将粒料用作屋顶铺设粒料时,颗粒破裂以产生裂开的边缘是希望的。应理解,大量热从熔融炉渣转移至雾化所述炉渣使用的气体。因此,气体雾化步骤产生高温气流。该加热的气体可以在金属生产工艺的他处使用,或者热量可从加热的气体中提取。这样,所述方法还可包括将该加热的气体从所述雾化设备传输通过热交换器,以回收雾化步骤中熔融炉渣损失的至少部分热量。当用作屋顶铺设粒料时,非球形炉渣粒料将在制备沥青基屋面材料或壁板材料过程中进行进一步加工。这些进一步加工步骤包括在窑中对固体炉渣粒径进行陶瓷和/或颜料涂覆。从雾化设备中回收和任选地分离之后,可以对用作支撑剂的球形炉渣粒料提供由树脂材料或陶瓷材料构成的涂层。球形炉渣粒料的涂覆在涂覆车间进行,通常涉及在翻转或混合设备中将该球形炉渣粒料与涂覆材料混合,从而提供具有均匀的涂覆材料层的粒料。图3显示树脂涂覆的炉渣粒料的截面扫描电子显微镜照片。在树脂涂料的情况下,在涂覆设备(如涂覆车间)中将树脂组合物与炉渣粒料合并,粒料被加热,以使树脂熔融并使其涂覆所述粒料。树脂组合物包含树脂,该树脂可包括聚合物、预聚物、单体和/或低聚物。在一些实施方式中,在气体雾化步骤之后将粒料冷却至室温,然后在涂覆设备中再加热。为了进一步减少能量消耗,所述方法的一些实施方式可以利用从雾化设备回收的凝固的炉渣粒料的残余热量。希望利用凝固的炉渣粒料的残余热量时,涂覆设备可以紧邻所述雾化设备,以使固体炉渣粒料可以在残余热量消散至周围环境之前从雾化设备运送至涂覆设备。如果需要的话,树脂涂料可以在其施用于固体炉渣粒料之后进行交联,例如通过在涂覆设备中将交联活化剂或交联剂与树脂组合物和炉渣粒料混合。炉渣粒料的树脂涂层用于多种目的。如上所述,支撑剂需要具有一定的耐浸提性,特别是在酸性环境中。树脂涂层可施用于固体炉渣粒料,以增加其耐酸溶解性。也可使用树脂涂层来改变和调节固体炉渣粒料的密度以用于具体应用,通常将减小炉渣粒料的密度。本发明人还发现炉渣粒料的树脂涂层能增加其压缩强度,并减少其被压缩至断裂点时产生细粒的趋势。产生细粒是支撑剂颗粒不希望的性质,这是由于细粒容易填充支撑剂颗粒之间的间隔,损坏支撑剂占据的破裂处的孔隙率并降低支撑剂包装(pack)的传导性。根据人造支撑剂的工业可接受的推荐做法(APIRP19C和ISO13503-2),指定尺寸范围的支撑剂在指定压缩应力下产生的细粒应当小于指定百分数。APIRP19C和ISO13503-2所定义的细粒是尺寸小于支撑剂规格的最小目数的颗粒。例如,对于20/40目支撑剂(0.425-0.850mm),细粒为通过40目(<0.425mm)的颗粒。当通过本发明方法产生的聚合物涂覆的炉渣粒料压缩至断裂点时,发明人发现产生的细粒水平小于工业推荐的细粒水平,与等量的未涂覆炉渣粒料相比,涂覆的粒料产生更少更大的断裂产物。因此,由本发明方法产生的树脂涂覆的炉渣粒料更耐断裂,当压缩至断裂点时,更容易保持其中插入炉渣粒料的破裂处的孔隙率。实施例基于ISO13503-2或APIRP19C,根据工业可接受的推荐做法,对根据本发明方法产生的树脂涂覆的球形炉渣粒料的多种性质进行测试,以确定该粒料用作支撑剂的适用性。对根据本发明方法产生的球形炉渣粒料进行加热并用酚醛树脂进行树脂涂覆,酚醛树脂与炉渣粒料之比为3.3重量%。使用六亚甲基四胺(HEXA)对树脂涂层进行交联,HEXA与炉渣粒料之比为1.6重量%。根据APIRP19C的涂覆的炉渣粒料的筛网测试显示涂覆的粒料满足“20/40”支撑剂需求,最少90%的测试样品具有目数20至目数40之间的筛网尺寸,即为422微米至853微米。超过98%的根据本发明方法的涂覆颗粒的筛网尺寸在此范围之内。根据APIRP19C对涂覆的炉渣粒料进行粉碎分析,以评估压缩条件下产生的细粒。在测试压缩应力水平为7,500,10,000,12,500和15,000psi时,建议的20/40支撑剂的可允许细粒最大量为10%。如以下表1所示,根据本发明方法的涂覆的炉渣粒料在各压缩应力水平下产生小于10%的细粒。表1负载应力(psi)细粒百分数(%)7,5002.110,0002.512,5005.815,0009.2根据APIRP19C,在10,000psi条件下还通过粉碎分析对未涂覆的炉渣粒料进行测试,发现产生30.2%的细粒,而作为比较,树脂涂覆的粒料的结果为2.5%。除了减少细粒的产生之外,发明人发现粉碎树脂涂覆的炉渣粒料产生的片段比粉碎未涂覆的炉渣粒料产生的那些更大。这可以从图2A-2D看出,其显示未涂覆的20/40炉渣粒料(图2A),树脂涂覆的20/40炉渣粒料(图2B),在10,000psi条件下粉碎的树脂涂覆的20/40炉渣粒料(图2C)以及在10,000psi条件下粉碎的未涂覆的炉渣粒料(图2D)。预期通过粉碎涂覆的炉渣粒料产生的片段的量减少并且尺寸增加,这对于保持被本发明方法产生的树脂涂覆的炉渣粒料撑开的破裂处的孔隙率和传导性具有有益效果。对于陶瓷支撑剂和树脂涂覆的支撑剂推荐的最大酸溶解性为7%。根据APIRP19C对未涂覆的炉渣粒料和本发明方法的涂覆的炉渣粒料的酸溶解性进行测试,采用12:3HCl:HF在150华氏度进行30分钟。未涂覆的炉渣粒料的酸溶解性约为14.3%,而涂覆的炉渣粒料的酸溶解性约为7.7%,这是工业上可接受的。如上所述,对于支撑剂推荐的球度和圆度为大于或等于0.6,对于高强度支撑剂为大于或等于0.7。根据本发明方法的树脂涂覆的炉渣粒料的球度和圆度为0.9,根据APIRP19C测定。根据APIRP19C,在树脂涂覆之前和之后测试炉渣粒料的浊度。未涂覆的炉渣粒料的浊度为550FTU,而涂覆的粒料的浊度为110FTU。建议的最大支撑剂浊度小于或等于250FTU。尽管本发明已结合某些具体实施方式来进行描述,但本发明不限于这些具体实施方式。相反,本发明包括可能落入所附权利要求书的范围内的所有实施例。当前第1页1 2 3