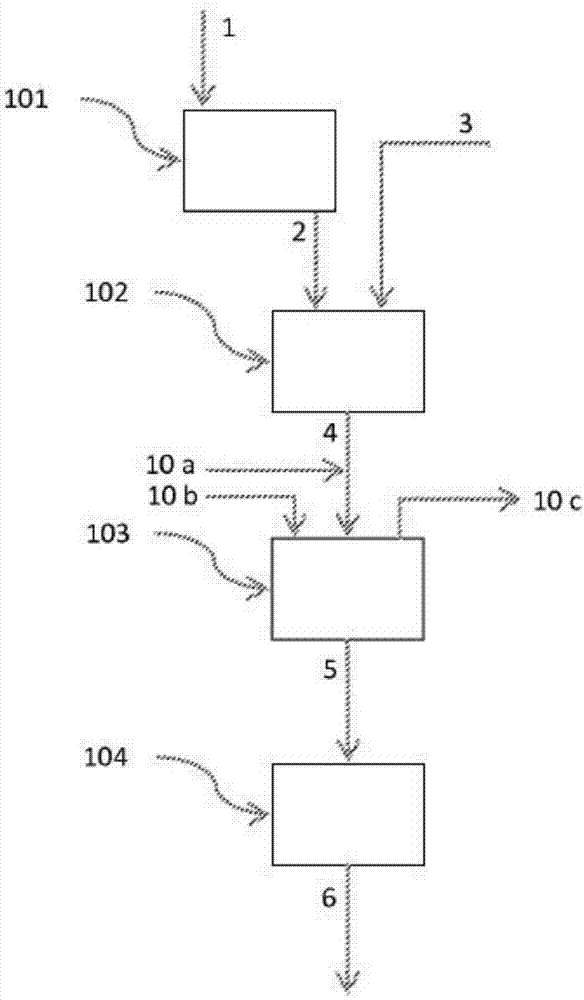
本发明涉及用于制备用于高密度电极生产的碳糊的方法,更准确地说,用于获得碳糊的有序混合方法,用于高密度电极生产,特别是用于铝电解的阳极,还涉及用于实施所述方法的装置。
背景技术:
众所周知,特别是根据fr992508和fr1073696,碳电极,尤其是用于铝电解的阳极,是由按照明确比例混合以下两方面物质所构成的糊剂制成的,一方面为固态干燥碳质颗粒状混合物,其中颗粒分布已知且受控,并且含有尺寸可达到10至30mm的集料,以及一定比例且尺寸一般小于100μm的亚毫米细粒(通常这些细粒含有按重量达18至22%的尺寸<74微米的细粒和12至18%的尺寸<32微米的细粒,尤其是在铝电解阳极生产时),另一方面为液态沥青粘合剂,其中所述术语“沥青粘合剂”表示源于石油工业、煤炭工业、尤其是煤焦油沥青,或者还有源于生物工业的重烃类残留物。
液态沥青粘合剂的使用,需要在高于软化点(以下简称sp)温度下使用,可采用不同标准方法表征,可参见iso5940-2梅特勒(mettler)方法。一方面,为了泵送和流速要求,另一方面,为了能够改进如下所述“涂布”和“渗透”性质而充分降低粘合剂的黏性,通常情况下,实施温度至少应比通过梅特勒方法获得的sp高30℃,通常情况下,最好比sp高60至70℃,在电解铝阳极生产领域的最新应用中,实施温度甚至比sp高90℃。
因此,沥青粘合剂采用固态冷藏方式交付,随后在使用现场融化,或直接采用热液态方式交付。在这两种情况下,都可将待用原料置于加热恒温罐中,保持粘合剂温度与其终端使用温度接近。
如图1a所示,可通过如下步骤确保均质糊剂的生产:预热颗粒状混合物1,向预热器101中供应,以确保粘合剂不会在集料冷表面上立即凝固,随后在混合机102中混合和揉合预热颗粒状混合物2,离开预热器101,与液态沥青粘合剂3一起投入混合机102中。离开混合机102时,可获得碳糊5,供应成型,压力机或振动压实机104中确保供应,在成型出料口输送电极块6。
碳糊同质,一方面,是指在颗粒状混合物的集料周围实现粘合剂均匀分布,即定义为粘合剂的“涂布”性质,和在粒间孔隙的均匀分布,即定义为粘合剂的“遮盖”性质,另一方面,是颗粒状混合物集料在孔隙中最大限度均匀填入,即定义为粘合剂的“渗透”性质。这两种性质共同有助于提高电极的密度,该参数是关键质量标准,与电极在电解过程中的耐久性和导电性直接相关。
可通过如下方式实施混合步骤:
-非连续地混合,采用配置水平轴的混合机,其中最著名的是“曲臂”混合机,或采用水平或倾斜旋转罐的混合机,其中,混合和揉合工具像混合机一样旋转,在这两种情况下,都需要向预热干颗粒状混合物原料上提供沥青粘合剂,
-或连续地混合,使用配置有横向螺钉的管式混合机,其往复轴向移动与螺钉的旋转移动叠加,其中,在螺钉一端上引入预热颗粒状混合物,随后是沥青粘合剂,混合物在螺钉叶片和装置主体之间、在被从装置另一端排放前的继续进行过程中,受到大量剪切循环,或使用配置倾斜旋转罐的混合机,其中混合和揉合工具像混合机一样旋转,沥青粘合剂在制备过程中在混合物上沉淀,即在干燥颗粒状混合物引入点的下游沉淀。
在某些最近连续过程应用中,例如:20世纪90年代以来的铝阳极生产,将水注入最终混合机-冷却器中,冷却糊剂的最后一步,有可能在下游步骤中将混合温度与电极成型温度分离。因此,有可能在比最高成型温度高的温度条件下混合,其中所述最高成型温度通常通过从模具上移除的电极的流动初始温度来定义,从而从沥青粘合剂的较低粘性中获益,以促进其渗透到集料的孔隙中。在用于铝电解的阳极的生产过程中,可将混合温度调节为高于成型温度25至30℃左右。不幸得是,注水和与热碳糊接触时的蒸发,会造成沥青粘合剂中较轻有机化合物的大量蒸发,必须对其进行收集并进行处理,以保护环境。
图1b示意性地描述了该方法,包括与图1a方法至混合机102的相同步骤。离开混合机102时,可将水10a注入使混合机102和混合机-冷却器103相连的导管,冷却供应至混合机-冷却器103的碳糊4,负载烃蒸气的冷却水流10c会从中逸出。作为一种变型,水10b直接注入混合机-冷却器103中。离开混合机-冷却器103时,通过压机或振动压实机104,可确保图1a中方法的碳糊5供应至成型位置,其中所述压机或振动压实机104在成型出料口处传送电极块6。
最近,专利申请wo2011/064461描述了一种具有水平轴的连续混合机的新设计,描述为能够在单个装置中实现混合步骤和冷却碳糊的步骤。
重要得是应注意,上述非连续或连续方法中,以及不同实施例中的混合步骤,总是涉及所有颗粒状混合物,没有对任何特定颗粒部分进行不同处理,还应注意:它使用同一种质量的粘合剂,且电极生产最终所需的所有粘合剂。同样,应注意:到目前为止,将原料引入混合机的顺序总是相同的,以避免混合机壁上粘附粘合剂:首先是单流中的颗粒状混合物,其次是单流中的液态沥青粘合剂。
此外,应注意,在目前已知的混合-冷却步骤中,糊剂的组成成分在冷却和较轻有机化合物部分除气后并没有明显变化,特别是没有新增任何干燥品、或任何粘合剂。
为了大致保持粘合剂的相同渗透率,而不必在高温下混合,并通过注水方式冷却糊剂,而仅仅通过在接近成型温度条件下简单混合,可以设想使用较低sp的沥青粘合剂(在铝电解用阳极生产情况下,通常情况下,而不是目前常用的),作为沿温度轴平移的温度函数的粘合剂黏性曲线,与sp变化值中的数值基本相同。但是,通常情况下sp的降低表示天然碳氢化合物焦油的真空蒸馏量较少,沥青粘合剂中中间型原油的含量增加。现在,这些油的c/h摩尔比通常比含有较重粘合剂的长链分子的c/h摩尔比低。因此,粘合剂中含有这些油,会导致在电极焙烧过程中粘合剂焦化值的下降,在焙烧工艺预热的含氢化合物除气过程中,会产生全新的微孔隙,甚至是微裂隙,最终可能会导致电极最终密度的退化,因此可能是导电性和耐久性方面退化,这当然是不合需要的。
fr992508描述了通过以电极生产所需数量,混合固态干燥颗粒状混合物和液态沥青粘合剂,制备碳糊的方法,所述碳糊用于铝电解用的电极生产,固态干燥颗粒状混合物是两部分成分的混合物,其中一部分是所谓的粗粒部分,包括集料,另一个部分是亚毫米细粒部分,包含至少两个连续混合步骤,第一个称为集料预浸步骤,包括将颗粒状混合物的粗粒部分与所述沥青粘合剂部分进行混合,数量至少足够涂布集料,至少部分可以填入所述集料的孔隙,随后实施第二个称为遮盖步骤,包括将源于第一个混合步骤且采用沥青粘合剂预浸渍的所述粗粒部分与电极生产所需的所述沥青粘合剂的剩余部分揉合,以及与所述颗粒状混合物的细粒部分揉合。
解决的技术问题
首先可通过低电阻率以及最长寿命来判断碳电极的质量。上述两个标准基本上取决于电极在其生产过程中的密化,更具体地说,取决于残留粒间孔隙和粘合剂未填入的孔隙。事实上,两者都会对电极的导电性,以及进入外部化合物的电极芯的接入路线产生不利影响,从而会有损电极寿命,例如:空气中的氧气、二氧化碳、电解酸盐等。因此,碳糊制备、成型、和电极焙烧的目标,是获得有几乎为零的内部孔隙率的焙烧阳极,通过最高密度对其进行量化。
有一套有助于最大化电极最终密度的措施:
-选择制备干燥颗粒状混合物的密度最高碳质材料:这些材料不可能总以足量、合理成本形式供应,由于全球整体趋势是供应源的质量退化,基本上是其原料天然碳氢化合物,通常是石油,质量退化的后果;因此,这种改进方式似乎不可持续,相比之下,会对生产碳质电极方法构成额外限制,这会在将来导致对原材料质量退化的耐受度增加;
-通过优选研磨受内孔隙或微裂隙削弱的集料,根据提供最佳颗粒混合物的方法,例如通过专利文档wo2001/38253中推荐的料层压缩的磨机操作,或者通过专利文档wo2008/083472中推荐的密度分离器,制备干燥颗粒状混合物,目前已有工业生产,当前尚无进一步改善。
-在糊剂揉合过程中优化需注入的沥青粘合剂数量,确保其足够涂布干颗粒状混合物,并能填充集料孔隙和粒间孔隙,而不是导致因为压实在电极的成型结束时出现粘合剂的渗出,渗出会导致在电极焙烧期间出现粘附问题:现代化控制系统可实现粘合剂配料优化的在线自动化,因此本身不再构成改良方式;
-通过改进fr992508已知方法,确保集料与沥青粘合剂的涂布和遮盖,在碳糊混合过程中,最大化沥青粘合剂渗透进入集料孔隙:这是本发明的主要目标,本规格中会进一步描述该发明的问题;
-然后,在电极-成型机中最大化碳糊的压实:该路线是过去几十年的发展要点,现有成型机(液压机或振动压实机)通常在真空下以优化循环和载荷方式运行,优化循环和载荷已使成型机具有卓越性能,在该领域中出现明显改善的程度较少;
-最后,通过最小化焙烧期间电极的重量损失,和密度损失方式实现目标,其中所述重量损失是因为在焦化前沥青粘合剂中含氢化合物蒸发导致,因为蒸发产生了新的微孔隙;可以实现:
ο一方面,最小化糊剂制备中所需粘合剂的百分比,使其限制为最大涂布、遮盖和渗透率所需的比例,该种操作已通过操作人员实施,尤其是可避免在压实过程中粘合剂的任何溢出,而导致焙烧过程中出现的粘附问题;
ο另一方面,通过使用高c/h摩尔比的沥青粘合剂,通过真空分馏,甚至可以通过重整方式可以耗尽中间型原油,因此具有最高可能的sp(通常最小sp=130℃,或者甚至是150至170℃,而不是铝电解用阳极生产情况下常规使用的sp=110至115℃);但是,不会导致涂布、遮盖和渗透质量下降的高sp粘合剂的使用,需要在整个粘合剂的搬运、存储和利用链条中,采用较高温度进行操作,而且现在遇到需要克服,尤其是混合设备层面的技术限制;但是,如解决该等技术限制,高sp粘合剂的使用可能会导致焙烧后电极密度增加,但是,没有对“原”电极密度有明显改善(焙烧前),因为粘合剂的黏性与现有粘合剂的黏性基本相同,因此,没有对涂布、遮盖和渗透性质有明显改善;基本问题仍然保持不变,本发明的优点仍然存在。
申请者在其研究方案中,在偏振光下对各种混合机的碳糊进行显微观察,结果清楚地表明,在目前已知的方法中,采用沥青粘合剂对集料实施良好均匀涂布,以及在压实结束时在残留粒间孔隙的良好填充仍不完善,虽然引入混合机的液态沥青粘合剂量足够,即使略过量,也能遮盖集料的扩展表面,在压实结束时填入残留颗粒孔隙,虽然混合装置可以确保混合物的充分混合,而不会有一种或其它成分旁通的现象。
粘合剂在集料孔隙内的均匀渗透是较为复杂且困难的操作,因为需要粘合剂能自由进入这些空间,且液流学特性提供其足够的润湿性质。
在理论上,如获得较好的集料均匀涂布,粘合剂进入孔隙的可能性将达到最佳状态。但是,干颗粒状混合物中存在细粒,可以至少部分地阻止粘合剂进入孔隙。同样,粘合剂中存在大分子(例如:源于重分子聚结的煤焦油沥青中的中间相,尤其是在重成型操作期间,或者例如原油沥青粘合剂中的链烷烃)可以至少部分地阻止进入孔隙,通过毛细作用减慢粘合剂的渗透。
图2a示意性地示出了根据现有技术方法实施所获得的涂布沥青粘合剂203和细粒202的集料201,有不当涂布区域210,未填充粘合剂的孔隙,例如孔隙空间211,和堵塞进入集料201中孔隙的细粒和/或大分子212。
最后,即使粘合剂能完全自由地进入孔隙,仍有必要通过毛细作用进行基本提升,最大程度填充相应空隙。文献中已经广泛确定,毛细作用的提升率与粘合剂湿润集料表面的能力直接相关,直接取决于粘合剂的黏性,在其他方面相同的情况下。现在,如上所述,指定操作温度下沥青粘合剂的黏性是其sp的直接函数。因此,为便于说明,尤其是在铝电解用阳极生产的具体情况下,
-具有130℃sp的煤焦沥青具有的黏性和毛细作用渗透率与具有110℃sp的煤焦沥青的相同,只要sp间差异会增加混合温度,即如为+20℃,相反地,具有sp90℃的沥青可与比具有110℃sp的沥青低20℃的温度混合,而孔隙中渗透率无任何实质变化;
-如果保持在比sp高10或20度的温度中,在几十小时后,可达到毛细作用渗透到给定直径孔隙中的相同程度(因此,现有工业方法无法达到),因此,具有极高的粘合剂黏性,而如果采用流动性极高的粘合剂,在比sp高80-90℃的条件下操作时,仅需几分钟。
在该等情况下,申请者在来自各种混合机的碳糊上实施其研究方案的情况下,在偏振光条件下实施显微观察,已清楚地表明,粘合剂进入孔隙以及通过毛细作用形成提升率的双重问题,已成为实现电极最高密化的障碍,大量孔隙仍然保持为空或仅有部分填入。即使在铝工业阴极块生产或者电冶金电极生产中,该双重问题仍然存在,其中在第一个焙烧步骤中,焙烧预制碳质块,随后在第二个焙烧步骤前,采用沥青粘合剂再浸渍(通常在真空下)。事实上,在真空条件下再浸渍通常只是部分再浸渍,不可能进入碳质块核心中的所有孔隙。
本发明提出了一种能够消除障碍,进一步提高电极密化限制的方法。
技术实现要素:
本发明是一种通过混合fr992508中已知类型的固态干燥颗粒状混合物和液态沥青粘合剂,制备用于高密度电极生产的碳糊的方法,包含至少如上所述两个连续混合步骤,其特征在于,第一个混合步骤中使用的沥青粘合剂,与第二个混合步骤中使用的沥青粘合剂的粒级不同,在第一个混合步骤中所用的沥青粘合剂的软化点比在第二个混合步骤中所用的沥青粘合剂的软化点低。
有利得是,本发明方法也有如下一种或多种特征:
-在第二个混合步骤中,在引入来自第一个混合步骤的预浸渍粗粒部分的同时或之后,引入沥青粘合剂的剩余部分,在引入沥青粘合剂的剩余部分的同时或之后,引入细粒部分;
-在引入第二个混合步骤获得的预混合物之前,将干燥颗粒状混合物的细粒与沥青粘合剂的所有或部分剩余部分预混合;
-通过分馏操作,随后从用于碳糊制备的单粒级沥青粘合剂开始软化,获得具有不同软化点的两种沥青粘合剂品质。
本发明的主题还是用于实施上述本发明方法的设施,其包括连续或非连续模式的两个混合机步骤,其中第一个混合机步骤用于本方法第一个步骤的实施,具有至少一个能够接收集料固态干燥颗粒流和液态沥青粘合剂的进料口,以及能够输送第一个混合步骤的糊状混合物的出料口,其中第二个混合机步骤用于第二个称为涂布混合步骤的实施,包括能够接收来自第一个混合机步骤的糊状混合物的进料口,和至少另一个能够接收细粒固态干燥颗粒流和沥青粘合剂补充流的进料口,第二个混合机步骤也具有能够输送已制备碳糊的出料口,适合电极成型,该装置能够将不同粒级的两种粘合剂分别存储在有储罐和循环的两个装置中,分别向第一个混合机步骤和第二个混合机步骤供料,还有用于对分别向第一个混合机步骤和第二个混合机步骤供应的两种粒级的沥青粘合剂中各粒级沥青粘合剂(3a,3b)进行配料的装置。
有利得是,本发明的设施还可具有以下一种或多种特征:
此外,它还包含用于对干燥颗粒状混合物中的集料部分和细粒部分进行单独预热的装置,以及单独处理设备,其中之一可能够确保在第一个混合机步骤中供应集料部分,另一个确保在第二个混合机步骤中供应细粒部分;以及
还另外包括至少一个分馏单元,能够从中等粒级的同一沥青粘合剂中生产出不同粒级的两种沥青粘合剂。
附图说明
参考附图,通过下文中非限制性实施例方式给出的说明,本发明的其他特征和优点将显而易见,其中所述附图中,相同参考号表示相同或相似和对应的元件。在该等附图中:
-图1a和1b示意性地且分别示出了通过背景技术中所记载的现有技术已知的用于制备碳糊的两种方法;
-图2a,如上所述,示意性地示出了通过现有技术方法实施获得,涂布有粘合剂和细粒的集料;
-图2b类似于图2a,展示了根据本发明方法,在第一个混合步骤后,集料具有用于预涂布并渗透到集料孔隙中的沥青粘合剂,以及在第二个混合步骤后,集料具有用于遮盖的沥青粘合剂;
-图3a和3b是与图1a和1b类似的两个示意图,分别示出了根据本发明方法的两个实施例和相应的设施。
具体实施方式
本发明是以可进入粘合剂的大部分孔隙均集中在干燥颗粒混合物的粗粒部分的观察为基础,因为细粒基本上来自本发明方法上游步骤中的磨损或研磨现象,细粒具有更少且尺寸更小的孔隙。
根据本发明,提出将现有技术的混合步骤分解为本发明的两个步骤,如图3a所示。
第一个,称为“预浸”混合步骤,仅涉及干燥颗粒状混合物的粗颗粒部分,细粒除外。粗粒部分1a首先供应至预热器101a,以预热状态2a从预热器101a中流出,以便供应至第一个混合步骤102a,其中预热的粗粒部分2a与电极生产所需的沥青粘合剂的一部分3a混合,随后供至第一个混合步骤102a。第一个混合步骤旨在促进沥青粘合剂进入和渗透入干颗粒状混合物的粗粒部分的孔隙中,在缺乏干燥颗粒状混合物的细粒的情况下,有利于结料在集料周围分布,提高均质涂布。第一步骤根据与现有技术混合机相同的原理提供,即,在预热粗颗粒部分2a同时或之后将沥青粘合剂的部分3a引入第一个混合步骤102a中,以避免混合机壁上粘上粘合剂。
第二个,称为“遮盖”混合步骤,在该步骤中,将干燥颗粒状混合物的剩余部分,即细粒(细粒或超细粒)部分,以及电极生产所需附加粘合剂添加到离开第一步骤的产品中。为此,将预先涂布沥青粘合剂,且离开第一个混合步骤102a的粗粒部分4a,供应至第二个混合步骤102b中,一方面,也供应离开第二个预热器101b的预热细粒部分2b,也供应细粒部分1b,另一方面,供应所需沥青粘合剂3b的剩余部分。第二个混合步骤主要是为了能够均匀地涂布所有颗粒状混合物,特别是形成最大比表面积的细粒,而且还旨在分布这些细粒,尽可能在预浸渍和预涂布集料之间均匀涂布,以最佳可能方式填充粒间孔隙,如图2b所示。在图2b中,集料201涂布有预涂布沥青粘合剂203a,此外,通过第一个混合步骤的影响,如孔隙213所示,填入集料201的孔隙中,这一层预涂布粘合剂203a本身遮盖有沥青遮盖粘合剂203b,供应至第二个混合步骤102b,其中细粒202供应至第二个混合步骤102b,基本上均匀分布。
在本第二个混合步骤中,为了避免在添加预热细粒2b时第一个步骤中糊剂4a的“干燥”,在峰值功率和固有堵塞混合机风险的情况下,可以确保所需沥青粘合剂3b的剩余部分在第一个混合步骤糊剂4a引入的同时或之后引入,但在干燥颗粒状混合物剩余部分引入的同时或之前引入,即:离开用于粗细粒部分单独预热装置的第二个预热器101b的预热细粒部分2b,也包含粗粒部分的第一个预热器101a,相对于现有技术,有多项是新颖的。
随后,离开第二个混合步骤102b的碳糊5,准备提供给在压力机或振动压实机104中,已实施的成型,从压力机或振动压实机104中,电极块6离开,准备焙烧。
可计算在两个混合步骤的每一个混合步骤时需注入的粘合剂3a、3b的分布:
-或者离开各步骤的产品,具有与生产原料电极(rawelectrode)用的最终糊剂5所需的相同重量的粘合剂;
-或者,最低限度,通过在第一步骤中注入涂布集料和填入孔隙所必须的粘合剂3a的量,通过在第二步骤中注入粘合剂3b剩余量部分,以便于获得生产原料电极用的最终糊剂5中按重量所需含量;根据相对于所有干燥颗粒状混合物延伸表面的待涂布集料表面积,按比例对第一步骤中涂布集料所需的粘合剂3a部分进行评估;
-或者介于前述两项且任意选择的任何其他分布。
根据如下基本数据,本发明的一个实施例描述如下:
-生产率:每小时50吨(t/h)碳糊
-原料电极中粘合剂的含量:按重量15%,即:7.5t/h粘合剂和42.5t/h干燥颗粒状混合物
-干颗粒状混合物的组成:
ο干燥颗粒状混合物的布莱恩(blaine)比表面积:3500cm2/g
ο80%粗粒部分,即34t/h
ο20%细粒部分,即8.5t/h
-粗粒部分特征:
ο仅粗粒部分的blaine比表面积:约350cm2/g
ο密度:2.0kg/dm3,
ο按孔隙体积%:估计为10%
-粘合剂密度:1.3kg/dm3
结果:
-对于通过两个步骤的等量粘合剂(按重量):
ο离开第一步的糊剂的流速:42.5x0.80/(1-0.15)=40t/h
ο注入第一步中的粘合剂的流速:40x0.15=6.0t/h
ο注入第二步中的粘合剂的流速:7.5-6.0=1.5t/h
-最低限度:
ο注入第一步中用于涂布粗粒部分的粘合剂的流速:7.5x(350x40)/(3500x42.5)=0.7t/h
ο第一步中所需用于填充孔隙的粘合剂的流速:(42.5x0.80/2.0)x0.10x1.3=2.2t/h
ο注入第一步中的粘合剂的总流速:0.7+2.2=2.9t/h
ο注入第二步中的粘合剂的流速:7.5-2.9=4.6t/h
-中间选择:
ο示例:两个步骤之间50/50平均分配
ο注入各步骤中的粘合剂的流速:7.5/2=3.75t/h
在第二步中细粒2b部分的添加和沥青粘合剂3b的补充,可通过两种不同方式进行:对其中每一部分,单独直接添加和补充到混合装置中,确保第二个混合步骤102a的实施(参见图3a),或相反地,在前一个旨在提高遮盖粘合剂203b中细粒202分散度,从而确保能在来自第一个混合步骤102a的预浸渍集料201周围更均匀分布的预混合步骤后单独同步实施,如图3b所示。
根据图3b的方法,与根据图3a的方法不同之处在于,离开预热器101b的预热细粒部分2b和所需沥青粘合剂3b的剩余部分,直接供应预混合机105,将离开预混合机105,经预混合产生的糊剂4b供应至第二个混合步骤102b,像离开第一个混合步骤102a的糊剂4a一样,通过该步骤后,在前述条件下获得供应成型104的碳糊5,以获得模块化电极块6。
前述基本方法的发展包括,各步骤添加的粘合剂粒级之间的差异,以考虑各自的具体目标:
-因此,在第一步或预浸步骤中,目的主要是确保集料201的良好涂布,以及孔隙213的良好填充。因此,目的是尽可能使用流动性最高的粘合剂,如有可能,尽量保持接近电极成型的温度,从而避免冷却糊剂的额外步骤,因为该步骤会导致产生轻芳烃化合物的排放。因此,选择具有低sp的粘合剂,其sp通常比成型温度低至少50℃,最好是80℃(例如:如成型温度为160至170℃,sp为的粘合剂合适使用)。
-在第二步或遮盖步骤中,目的是用细粒202涂布集料201并填充粒间孔隙,细粒202本身涂布有遮盖粘合剂203b,且分布均匀,但没有任何孔隙浸渍的需要,因为集料201已经预浸渍处理,细粒202本质上不是多孔型。如前所述,一旦温度比粘合剂sp高30℃或以上,该步骤需要很小的功率系数。因此,可以选择接近成型温度满足该条件的较高sp值的粘合剂(例如:对于成型温度为sp为的粘合剂适合使用)。第二个步骤选择使用较高sp的粘合剂的优点在于,补偿第一个称为预浸步骤低sp粘合剂选择的需要,以尽可能保持粘合剂混合物的焦化值,最后,避免在电极6的焙烧期间,失去因集料201更好地浸渍所得密度增益。
在图2b中,如使用两种不同粒级的粘合剂或者两种粘合剂的sp不同时,用于预涂布和预渗入孔隙213的沥青粘合剂203a是低sp粘合剂,反之沥青遮盖粘合剂203b是高sp粘合剂。
在该阶段,因此假定向操作员提供了两种不同粒级的粘合剂,和专门的存储设施,可以代表主要的障碍。此外,为了克服该障碍,为此方法提出的另一项开发允许操作人员在不更改当前供应物流,通过添加第二日专用储罐来减少对存储设施影响的方式实施本发明:实际上是在主要存储装置和日用储罐之间,插入小分馏单元,能够从平均sp的粗粘合剂部分产生高sp的粘合剂203b。该操作中回收的轻油,与平均sp的粘合剂原料剩余部分熔融,以产生具有低sp的粘合剂203a。因此,例如,采用sp110℃的粘合剂,且假定两个步骤之间粘合剂50/50分布,可以设想获得sp130℃的结合物203b和sp90℃的粘合剂203a。通过该操作,可以获得用于实施本发明的两种粒级粘合剂203a,203b,而不产生影响操作人员的新供应限制,也没有再处理任何剩余流量。
本发明方法的实施,结合单种粒级粘合剂或两种不同粒级粘合剂,可通过在非连续模式和连续模式中,通过结合2个常规混合机步骤轻松实施,与采用混合机-冷却器103的现有技术类似(参见图1b)。装置和现有技术之间的极少数操作差异,仅需小幅更改:
-第一个混合机阶段102a,用于第一个称为预浸步骤的实施,在接近现有技术的混合温度下实施,在该情况下使用单种粒级的粘合剂,或在接近成型温度下(不高于30℃)实施,在该情况下使用两种不同粒级的粘合剂,将较低sp粘合剂203a注入第一个混合阶段102a的3a中。此外,第一个阶段102a在进料口处接收与当前现有技术相同的颗粒流和粘合剂液流,以便在出料口处产生比传统方法颗粒大但黏性小的糊剂:不如说,所有运行条件都以有利方向发展。
-第二个混合机阶段102b,旨在实施第二个称为遮盖步骤,采用与现有技术混合机-冷却器相同方式,在接近成型温度条件下操作,但一方面在接口处接收第一阶段102a排放的颗粒状糊剂4a,另一方面在进料口处接收细粒2b和补充粘合剂3b,这是两种粒级粘合剂使用时具有较高sp的粘合剂,优先在105中混合,而不是将冷却水注入到现有技术中所用上述混合机-冷却器中,以便最终产生比现有技术产生的糊剂密度高但温度几乎相同的糊剂5。
作为选择,可以设想采用单个混合设备来实施本发明方法,该种解决方法在设施和资本支出成本方面具有明显的优势:
-可通过非连续混合,按序引入专用于本发明的上述材料,以便在装置循环过程中,具有采用低sp(3a)粘合剂预浸(102a)集料(2a)的阶段,随后通过添加高sp(3b)粘合剂和细粒(2b),或者作为选择可以通过添加(在105中)预混合的细粒和高sp(3b)粘合剂遮盖(102b)预浸渍集料(4a)的阶段。
-或通过连续混合,将材料按序引入专用于本发明的如上所述混合机中,以便在混合机内通过低sp(3a)粘合剂产生一个称为集料(2a)预浸区的上游,随后是预浸渍高sp(3b)粘合剂和细粒(2b)的称为集料遮盖区的下游,或者作为选择通过添加预混合细粒(2b)和高sp(3b)粘合剂。
ο因此,例如,可以设想,在水平管式混合机的上游端引入集料(2a),随后立即引入低sp(3a)粘合剂,在足够预浸集料的长时间后,通常是在混合区域半途,引入高sp(3b)粘合剂,随后立即引入细粒(2b),在采用细粒(2b)和高sp(3b)粘合剂的混合物的集料均匀遮盖足够长时间后,在水平混合机下游末端排放碳质最终糊剂(5)。作为选择,可以沿混合机半途引入细粒(2b)和高sp(3b)粘合剂的混合物。
ο同样,可以设想,例如,如专利文献wo2011/064461中所述连续混合机的使用,其中对其上游区域实施了更改,以分为两个区域:上游,接收集料(2a)和低sp(3a)的预浸渍区,随后是按序供应高sp(3b)粘合剂和细粒(2b)或两者混合物的装置,随后是下游遮盖区,去除了专利文献wo2011/064461中所述的冷却糊剂区域。在该配置中,压力辊以及解聚装置和分配挡板配置装置的整个有用长度。
ο或者,任何其他混合机配置,允许按序引入本发明中所述材料,以提供后接遮盖区的预浸渍集料区域。
在任何情况下,无论是采用单个混合机,还是采用两台串联混合机实施本发明,都需要对传统处理设施的上游部分实施更改,以便纳入新方法供应所需的其他设备,即:
-对干燥颗粒状混合物中的集料(1a)和细粒(1b)进行单独预热(101a,101b),以及注入一台或另一台混合机点的单独处理设备;
-可选地,至于在预浸区域和步骤,以及在遮盖区域和步骤,不同粒级粘合剂的使用:
ο在两种粒级粘合剂单独供应的情况下,需要有接收第二种粒级粘合剂的供应的第二个储罐,以及其独立的再加热装卸装置;
ο或者,在仅保持中等粒级粘合剂单独供应的情况下,需要有根据现有单个存储单元的两种粒级粘合剂生产用单元;
ο在这两种情况下,都需要有第二日专用储罐,以及供应和配料第二种粒级粘合剂的循环装置;
-可选地有,用于预混合(105)细粒(2b)和高sp(3b)粘合剂的搅拌槽,其配置有专用提取/配料系统,用于直接向遮盖区进料口提供预混合物。