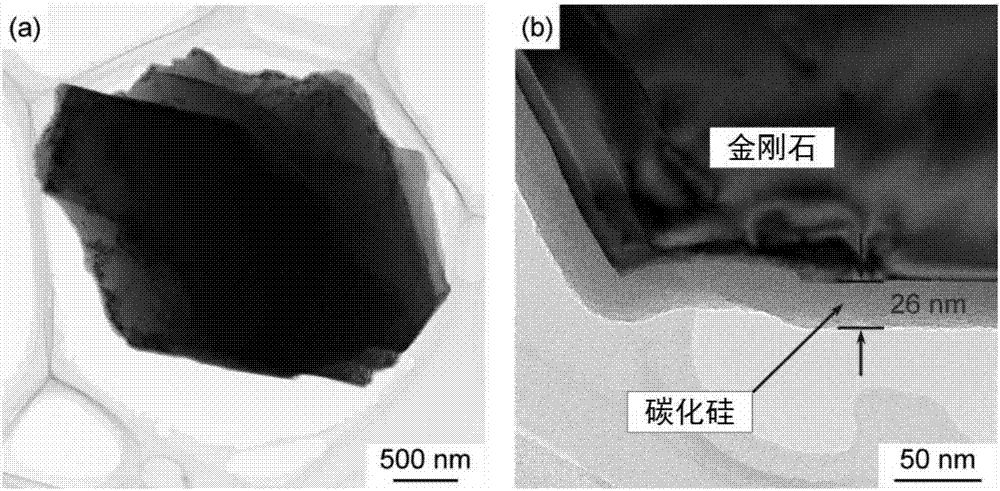
本发明涉及一种超硬材料,金刚石复合材料的制备方法。
背景技术:金刚石是自然界中硬度最高的材料,其被广泛应用于切割刀具,石油开采,精细加工等。天然金刚石由于其尺寸和数量的限制,成本极其高昂,聚晶金刚石的制备是工业上迫切的热点需求。金刚石的晶体结构中,每个碳原子都以SP3杂化轨道与另外4个碳原子形成共价键,构成正四面体。金刚石中的碳-碳共价键很强,从而决定了金刚石具有高熔点,低的扩散系数。金刚石的低扩散系数和高温下的石墨化相变,使得纯相金刚石的制备通常需要高温(1500摄氏度以上),超高压条件(10GPa以上)。高温,超高压的制备条件,不但大幅限制了大尺寸聚晶金刚石的合成,并且其高昂的成本更限制了其在相关领域的广泛应用。国内外为解决聚晶金刚石的烧结问题,主要采用添加烧结助剂和液相烧结的方法,常用的烧结助剂有Co,Ni,B,Si,Ti等,可以适度降低烧结压力,但现有的制备技术中,金刚石的烧结制备仍然需要5GPa以上的超高压力。金刚石的超高压制备条件需要进一步的改进,0.5GPa以下的金刚石合成制备工艺,是科学界和工业界的研究热点。放电等离子烧结(SparkPlasmaSintering,简称SPS)是一项制备材料的新技术,它具有升温速度快、烧结温度低,烧结时间短、抑制烧结体晶粒长大、节能环保等鲜明特点。为了降低金刚石制备工艺中的烧结压力,采用表面修饰完整包覆的保护涂层的方法,防止金刚石颗粒间的接触,添加合适的烧结助剂,并采用放电等离子烧结快速制备金刚石复合材料是一种可行的研究方向。通过对国内外专利与期刊的查新结果表明:还没有利用放电等离子烧结制备超高硬度金刚石复合材料的专利与报道。
技术实现要素:本发明的目的在于提供一种采用放电等离子烧结制备超高硬度金刚石复合材料的方法,该方法烧结压力低,100MPa烧结压力为常规金刚石制备压力(5GPa以上)的2%,该方法制备的金刚石复合材料致密度高、硬度高。为了实现上述目的,本发明的技术方案是:采用放电等离子烧结制备超高硬度金刚石复合材料的方法,其特征是它包括如下步骤:(1)粉体表面修饰:将金刚石粉体放入化学气相沉积设备内,化学气相沉积设备的背底真空为5Pa,化学气相沉积的前驱体为C6H18Si2(hexamethyldisilane:HMDS六甲基二硅烷),前驱体温度10~30℃,沉积温度690~740℃,沉积时间0.1~8小时,沉积气压200~800Pa;在金刚石粉体表面沉积包覆0.1~50纳米厚度的碳化硅薄膜(优选1~40纳米厚度),得到碳化硅包覆的金刚石复合粉体;(2)干燥:将步骤(1)得到的金刚石复合粉体放入干燥箱中,50~70℃干燥1~2小时,获得干燥后的金刚石复合粉体;(3)加入烧结助剂:将步骤(2)得到的干燥后的金刚石复合粉体与非晶态二氧化硅粉体按质量比为60~99.9:0.1~40混合(优选60~99:1~40)(混合物中非晶态二氧化硅的质量分数为0.1~40mass%),并采用刚玉研钵研磨混合0.5~1小时,得到复合粉体;(4)放电等离子烧结:将步骤(3)得到的复合粉体放入石墨模具中,在30~100MPa烧结压力下,温度1400~1700℃下,放电等离子烧结10~30分钟,得到复合材料;(5)脱模抛光:将(4)获得的复合材料进行脱模,表面抛光,获得超高硬度金刚石复合材料。所述步骤(1)中的金刚石粉体为0.5~10μm(优选2~4μm)人造金刚石粉,质量纯度为99.0~99.99%。步骤(1)中所述的C6H18Si2(hexamethyldisilane:HMDS六甲基二硅烷)的质量纯度95~99%。所述步骤(1)中所获得的碳化硅包覆的金刚石粉体,碳化硅的质量分数为0.1~25mass%。所述步骤(3)中的非晶态二氧化硅粉体为类球形,平均粒径500纳米,质量纯度99.9%,二氧化硅的最佳质量分数为35mass%。所述步骤(4)中的石墨模具的尺寸为Φ10~20毫米,形状为圆柱形。所述步骤(4)中的放电等离子烧结工艺中,升温速率为100摄氏度/分钟,温度由红外设备测定。本发明具有以下优点:(1)本发明利用放电等离子烧结制备超高硬度金刚石复合材料的方法,制备压力100MPa,为常规金刚石制备压力(5GPa以上)的2%,低碳环保,制备周期短,一般在10小时以内;(2)所制备的金刚石复合材料,致密度高,硬度高,硬度最高可达36GPa;(3)金刚石粉体表面的碳化硅修饰,有效地阻隔金刚石粉体在烧结过程中的接触,从而阻止金刚石在高温下的石墨相变;(4)放电等离子烧结中,二氧化硅相充当了烧结助剂的作用,有效地促进了金刚石的烧结致密化,大大降低了金刚石的烧结合成压力。附图说明图1是本发明的工艺流程图。图2是本发明制备的碳化硅包覆层为26纳米的金刚石复合粉体图片。图3是本发明制备的金刚石复合材料的X射线衍射图谱。图4是本发明制备的金刚石复合材料的微观结构透射电镜图片。具体实施方式为了更好地理解本发明,以下结合实施例对本发明的技术方案作进一步描述,可以看出本发明的技术特征和优点。需要说明的是本发明的权限并不局限于所给出的实施例。下述实施例中:所述金刚石粉体为2~4μm人造金刚石粉,质量纯度为99.0~99.99%。所述的C6H18Si2(hexamethyldisilane:HMDS六甲基二硅烷)的质量纯度95~99%。所述非晶态二氧化硅粉体为类球形,平均粒径500纳米,质量纯度99.9%。所述石墨模具的尺寸为Φ10~20毫米,形状为圆柱形。实施例1:如图1所示,将4.5克金刚石粉体放入化学气相沉积设备(或称粉体化学气相沉积设备。以下相同)内,金刚石粉体粒径为2~4微米。化学气相沉积设备的背底真空为5Pa,化学气相沉积的前驱体为C6H18Si2(hexamethyldisilane:HMDS六甲基二硅烷),前驱体温度25℃,沉积温度720℃,沉积时间4小时,沉积气压400Pa。在金刚石粉体表面沉积包覆26纳米厚度的碳化硅薄膜,得到碳化硅包覆的金刚石复合粉体,其中碳化硅的质量分数为9mass%;将表面修饰后的金刚石复合粉体放入干燥箱中,50℃干燥1小时,获得金刚石复合粉体;将干燥后的金刚石复合粉体,按照质量比例65:35,与非晶态二氧化硅粉体混合,并采用刚玉研钵研磨混合0.5小时;将均匀混合的复合粉体放入石墨模具中,在100MPa烧结压力下,温度1600℃下,放电等离子烧结10分钟,升温速率100℃每分钟;将放电等离子烧结获得的复合材料进行脱模,表面抛光,获得超高硬度金刚石复合材料。对碳化硅表面修饰后的金刚石复合粉体进行微观形貌测试,对所获金刚石复合材料进行致密度,微观形貌,晶体结构,维氏硬度等测试。利用透射电子显微镜对碳化硅表面修饰后的金刚石粉体的微观形貌进行分析,如图2所示,结果表明:微米金刚石粉体表面被碳化硅薄膜均匀包覆,碳化硅薄膜的厚度为26纳米。利用X射线衍射仪对制得的金刚石复合材料进行分析,如图3所示,结果表明:放电等离子烧结后,金刚石没有发生石墨化相变,复合材料中的碳化硅为立方相。利用阿基米德排水法对制得的金刚石复合材料进行分析,结果表明:复合材料的相对致密度为95%。利用透射电子显微镜对制得的金刚石复合材料的微观形貌进行分析,如图4所示,结果表明:复合材料中,金刚石相被二氧化硅相隔开,复合材料致密度高。利用维氏硬度仪对制得的金刚石复合材料的硬度进行分析,结果表明:复合材料的硬度为36GPa。该方法所获得的金刚石复合材料,没有发生金刚石的石墨化相变,金刚石相被二氧化硅相隔开,致密度为95%,硬度为36GPa。实施例2:将4.5克金刚石粉体放入粉体化学气相沉积设备内,金刚石粉体粒径为2~4微米。粉体化学气相沉积设备的背底真空为5Pa,化学气相沉积的前驱体为C6H18Si2(hexamethyldisilane:HMDS六甲基二硅烷),前驱体温度25℃,沉积温度720℃,沉积时间4小时,沉积气压400Pa。在金刚石粉体表面沉积包覆26纳米厚度的碳化硅薄膜,得到碳化硅包覆的金刚石复合粉体,其中碳化硅的质量分数为9mass%;将表面修饰后的金刚石复合粉体放入干燥箱中,50℃干燥1小时,获得金刚石复合粉体;将干燥后的金刚石复合粉体,按照质量比例65:35,与非晶态二氧化硅粉体混合,并采用刚玉研钵研磨混合0.5小时;将均匀混合的复合粉体放入石墨模具中,在100MPa烧结压力下,温度1650℃下,放电等离子烧结10分钟,升温速率100℃每分钟;将放电等离子烧结获得的复合材料进行脱模,表面抛光,获得超高硬度金刚石复合材料。对碳化硅表面修饰后的金刚石复合粉体进行微观形貌测试,对所获金刚石复合材料进行致密度,微观形貌,晶体结构,维氏硬度等测试。所获得的金刚石复合材料,发生了金刚石的石墨化相变,金刚石相被二氧化硅相隔开,致密度为91%,硬度为18.5GPa。实施例3:将4.5克金刚石粉体放入粉体化学气相沉积设备内,金刚石粉体粒径为2~4微米。粉体化学气相沉积设备的背底真空为5Pa,化学气相沉积的前驱体为C6H18Si2(hexamethyldisilane:HMDS六甲基二硅烷),前驱体温度25℃,沉积温度720℃,沉积时间4小时,沉积气压400Pa。在金刚石粉体表面沉积包覆26纳米厚度的碳化硅薄膜,得到碳化硅包覆的金刚石复合粉体,其中碳化硅的质量分数为9mass%;将表面修饰后的金刚石复合粉体放入干燥箱中,50℃干燥1小时,获得金刚石复合粉体;将干燥后的金刚石复合粉体,按照质量比例65:35,与非晶态二氧化硅粉体混合,并采用刚玉研钵研磨混合0.5小时;将均匀混合的复合粉体放入石墨模具中,在100MPa烧结压力下,温度1550℃下,放电等离子烧结10分钟,升温速率100℃每分钟;将放电等离子烧结获得的复合材料进行脱模,表面抛光,获得超高硬度金刚石复合材料。对碳化硅表面修饰后的金刚石复合粉体进行微观形貌测试,对所获金刚石复合材料进行致密度,微观形貌,晶体结构,维氏硬度等测试。所获得的金刚石复合材料,没有发生金刚石的石墨化相变,金刚石相被二氧化硅相隔开,致密度为93%,硬度为31.2GPa。实施例4:将4.5克金刚石粉体放入粉体化学气相沉积设备内,金刚石粉体粒径为2~4微米。粉体化学气相沉积设备的背底真空为5Pa,化学气相沉积的前驱体为C6H18Si2(hexamethyldisilane:HMDS六甲基二硅烷),前驱体温度25℃,沉积温度720℃,沉积时间4小时,沉积气压400Pa。在金刚石粉体表面沉积包覆25纳米厚度的碳化硅薄膜,得到碳化硅包覆的金刚石复合粉体,其中碳化硅的质量分数为8mass%;将表面修饰后的金刚石复合粉体放入干燥箱中,50℃干燥1小时,获得金刚石复合粉体;将干燥后的金刚石复合粉体,按照质量比例60:40,与非晶态二氧化硅粉体混合,并采用刚玉研钵研磨混合0.5小时;将均匀混合的复合粉体放入石墨模具中,在100MPa烧结压力下,温度1600℃下,放电等离子烧结10分钟,升温速率100℃每分钟;将放电等离子烧结获得的复合材料进行脱模,表面抛光,获得超高硬度金刚石复合材料。对碳化硅表面修饰后的金刚石复合粉体进行微观形貌测试,对所获金刚石复合材料进行致密度,微观形貌,晶体结构,维氏硬度等测试。所获得的金刚石复合材料,没有发生金刚石的石墨化相变,金刚石相被二氧化硅相隔开,致密度为97%,硬度为26.5GPa。实施例5:将4.5克金刚石粉体放入粉体化学气相沉积设备内,金刚石粉体粒径为2~4微米。粉体化学气相沉积设备的背底真空为5Pa,化学气相沉积的前驱体为C6H18Si2(hexamethyldisilane:HMDS六甲基二硅烷),前驱体温度25℃,沉积温度720℃,沉积时间4小时,沉积气压400Pa。在金刚石粉体表面沉积包覆25纳米厚度的碳化硅薄膜,得到碳化硅包覆的金刚石复合粉体,其中碳化硅的质量分数为8mass%;将表面修饰后的金刚石复合粉体放入干燥箱中,50℃干燥1小时,获得金刚石复合粉体;将干燥后的金刚石复合粉体,按照质量比例70:30,与非晶态二氧化硅粉体混合,并采用刚玉研钵研磨混合0.5小时;将均匀混合的复合粉体放入石墨模具中,在100MPa烧结压力下,温度1600℃下,放电等离子烧结10分钟,升温速率100℃每分钟;将放电等离子烧结获得的复合材料进行脱模,表面抛光,获得超高硬度金刚石复合材料。对碳化硅表面修饰后的金刚石复合粉体进行微观形貌测试,对所获金刚石复合材料进行致密度,微观形貌,晶体结构,维氏硬度等测试。所获得的金刚石复合材料,没有发生金刚石的石墨化相变,金刚石相被二氧化硅相隔开,致密度为92%,硬度为17.4GPa。实施例6:将4.5克金刚石粉体放入粉体化学气相沉积设备内,金刚石粉体粒径为2~4微米。粉体化学气相沉积设备的背底真空为5Pa,化学气相沉积的前驱体为C6H18Si2(hexamethyldisilane:HMDS六甲基二硅烷),前驱体温度25℃,沉积温度720℃,沉积时间4小时,沉积气压400Pa。在金刚石粉体表面沉积包覆25纳米厚度的碳化硅薄膜,得到碳化硅包覆的金刚石复合粉体,其中碳化硅的质量分数为8mass%;将表面修饰后的金刚石复合粉体放入干燥箱中,50℃干燥1小时,获得金刚石复合粉体;将干燥后的金刚石复合粉体,按照质量比例75:25,与非晶态二氧化硅粉体混合,并采用刚玉研钵研磨混合0.5小时;将均匀混合的复合粉体放入石墨模具中,在100MPa烧结压力下,温度1600℃下,放电等离子烧结10分钟,升温速率100℃每分钟;将放电等离子烧结获得的复合材料进行脱模,表面抛光,获得超高硬度金刚石复合材料。对碳化硅表面修饰后的金刚石复合粉体进行微观形貌测试,对所获金刚石复合材料进行致密度,微观形貌,晶体结构,维氏硬度等测试。所获得的金刚石复合材料,没有发生金刚石的石墨化相变,金刚石相被二氧化硅相隔开,致密度为83%,硬度为11.6GPa。实施例7:将4.5克金刚石粉体放入粉体化学气相沉积设备内,金刚石粉体粒径为2~4微米。粉体化学气相沉积设备的背底真空为5Pa,化学气相沉积的前驱体为C6H18Si2(hexamethyldisilane:HMDS六甲基二硅烷),前驱体温度25℃,沉积温度720℃,沉积时间0.1小时,沉积气压400Pa。在金刚石粉体表面沉积包覆1纳米厚度的碳化硅薄膜,得到碳化硅包覆的金刚石复合粉体,其中碳化硅的质量分数为1mass%;将表面修饰后的金刚石复合粉体放入干燥箱中,50℃干燥1小时,获得金刚石复合粉体;将干燥后的金刚石复合粉体,按照质量比例65:35,与非晶态二氧化硅粉体混合,并采用刚玉研钵研磨混合0.5小时;将均匀混合的复合粉体放入石墨模具中,在100MPa烧结压力下,温度1600℃下,放电等离子烧结10分钟,升温速率100℃每分钟;将放电等离子烧结获得的复合材料进行脱模,表面抛光,获得超高硬度金刚石复合材料。对碳化硅表面修饰后的金刚石复合粉体进行微观形貌测试,对所获金刚石复合材料进行致密度,微观形貌,晶体结构,维氏硬度等测试。所获得的金刚石复合材料,没有发生金刚石的石墨化相变,部分金刚石相被二氧化硅相隔开,致密度为82%,硬度为18.5GPa。实施例8:将4.5克金刚石粉体放入粉体化学气相沉积设备内,金刚石粉体粒径为2~4微米。粉体化学气相沉积设备的背底真空为5Pa,化学气相沉积的前驱体为C6H18Si2(hexamethyldisilane:HMDS六甲基二硅烷),前驱体温度25℃,沉积温度720℃,沉积时间0.1小时,沉积气压400Pa。在金刚石粉体表面沉积包覆1纳米厚度的碳化硅薄膜,得到碳化硅包覆的金刚石复合粉体,其中碳化硅的质量分数为1mass%;将表面修饰后的金刚石复合粉体放入干燥箱中,50℃干燥1小时,获得金刚石复合粉体;将干燥后的金刚石复合粉体,按照质量比例65:35,与非晶态二氧化硅粉体混合,并采用刚玉研钵研磨混合0.5小时;将均匀混合的复合粉体放入石墨模具中,在100MPa烧结压力下,温度1650℃下,放电等离子烧结10分钟,升温速率100℃每分钟;将放电等离子烧结获得的复合材料进行脱模,表面抛光,获得超高硬度金刚石复合材料。对碳化硅表面修饰后的金刚石复合粉体进行微观形貌测试,对所获金刚石复合材料进行致密度,微观形貌,晶体结构,维氏硬度等测试。所获得的金刚石复合材料,发生了金刚石的石墨化相变,部分金刚石相被二氧化硅相隔开,致密度为80%,硬度为13.4GPa。实施例9:将4.5克金刚石粉体放入粉体化学气相沉积设备内,金刚石粉体粒径为2~4微米。粉体化学气相沉积设备的背底真空为5Pa,化学气相沉积的前驱体为C6H18Si2(hexamethyldisilane:HMDS六甲基二硅烷),前驱体温度25℃,沉积温度720℃,沉积时间0.1小时,沉积气压400Pa。在金刚石粉体表面沉积包覆1纳米厚度的碳化硅薄膜,得到碳化硅包覆的金刚石复合粉体,其中碳化硅的质量分数为1mass%;将表面修饰后的金刚石复合粉体放入干燥箱中,50℃干燥1小时,获得金刚石复合粉体;将干燥后的金刚石复合粉体,按照质量比例65:35,与非晶态二氧化硅粉体混合,并采用刚玉研钵研磨混合0.5小时;将均匀混合的复合粉体放入石墨模具中,在100MPa烧结压力下,温度1550℃下,放电等离子烧结10分钟,升温速率100℃每分钟;将放电等离子烧结获得的复合材料进行脱模,表面抛光,获得超高硬度金刚石复合材料。对碳化硅表面修饰后的金刚石复合粉体进行微观形貌测试,对所获金刚石复合材料进行致密度,微观形貌,晶体结构,维氏硬度等测试。所获得的金刚石复合材料,没有发生金刚石的石墨化相变,部分金刚石相被二氧化硅相隔开,致密度为81%,硬度为14.2GPa。实施例10:将4.5克金刚石粉体放入粉体化学气相沉积设备内,金刚石粉体粒径为2~4微米。粉体化学气相沉积设备的背底真空为5Pa,化学气相沉积的前驱体为C6H18Si2(hexamethyldisilane:HMDS六甲基二硅烷),前驱体温度25℃,沉积温度720℃,沉积时间4小时,沉积气压200Pa。在金刚石粉体表面沉积包覆22纳米厚度的碳化硅薄膜,得到碳化硅包覆的金刚石复合粉体,其中碳化硅的质量分数为8mass%;将表面修饰后的金刚石复合粉体放入干燥箱中,50℃干燥1小时,获得金刚石复合粉体;将干燥后的金刚石复合粉体,按照质量比例65:35,与非晶态二氧化硅粉体混合,并采用刚玉研钵研磨混合0.5小时;将均匀混合的复合粉体放入石墨模具中,在100MPa烧结压力下,温度1650℃下,放电等离子烧结10分钟,升温速率100℃每分钟;将放电等离子烧结获得的复合材料进行脱模,表面抛光,获得超高硬度金刚石复合材料。对碳化硅表面修饰后的金刚石复合粉体进行微观形貌测试,对所获金刚石复合材料进行致密度,微观形貌,晶体结构,维氏硬度等测试。所获得的金刚石复合材料,没有发生金刚石的石墨化相变,金刚石相被二氧化硅相隔开,致密度为94%,硬度为34.1GPa。实施例11:将4.5克金刚石粉体放入粉体化学气相沉积设备内,金刚石粉体粒径为2~4微米。粉体化学气相沉积设备的背底真空为5Pa,化学气相沉积的前驱体为C6H18Si2(hexamethyldisilane:HMDS六甲基二硅烷),前驱体温度25℃,沉积温度720℃,沉积时间4小时,沉积气压800Pa。在金刚石粉体表面沉积包覆30纳米厚度的碳化硅薄膜,得到碳化硅包覆的金刚石复合粉体,其中碳化硅的质量分数为10mass%;将表面修饰后的金刚石复合粉体放入干燥箱中,50℃干燥1小时,获得金刚石复合粉体;将干燥后的金刚石复合粉体,按照质量比例65:35,与非晶态二氧化硅粉体混合,并采用刚玉研钵研磨混合0.5小时;将均匀混合的复合粉体放入石墨模具中,在100MPa烧结压力下,温度1650℃下,放电等离子烧结10分钟,升温速率100℃每分钟;将放电等离子烧结获得的复合材料进行脱模,表面抛光,获得超高硬度金刚石复合材料。对碳化硅表面修饰后的金刚石复合粉体进行微观形貌测试,对所获金刚石复合材料进行致密度,微观形貌,晶体结构,维氏硬度等测试。所获得的金刚石复合材料,没有发生金刚石的石墨化相变,金刚石相被二氧化硅相隔开,致密度为95%,硬度为35.3GPa。实施例12:将4.5克金刚石粉体放入粉体化学气相沉积设备内,金刚石粉体粒径为2~4微米。粉体化学气相沉积设备的背底真空为5Pa,化学气相沉积的前驱体为C6H18Si2(hexamethyldisilane:HMDS六甲基二硅烷),前驱体温度25℃,沉积温度720℃,沉积时间4小时,沉积气压400Pa。在金刚石粉体表面沉积包覆26纳米厚度的碳化硅薄膜,得到碳化硅包覆的金刚石复合粉体,其中碳化硅的质量分数为9mass%;将表面修饰后的金刚石复合粉体放入干燥箱中,50℃干燥1小时,获得金刚石复合粉体;将干燥后的金刚石复合粉体,按照质量比例65:35,与非晶态二氧化硅粉体混合,并采用刚玉研钵研磨混合0.5小时;将均匀混合的复合粉体放入石墨模具中,在30MPa烧结压力下,温度1650℃下,放电等离子烧结10分钟,升温速率100℃每分钟;将放电等离子烧结获得的复合材料进行脱模,表面抛光,获得超高硬度金刚石复合材料。对碳化硅表面修饰后的金刚石复合粉体进行微观形貌测试,对所获金刚石复合材料进行致密度,微观形貌,晶体结构,维氏硬度等测试。所获得的金刚石复合材料,没有发生金刚石的石墨化相变,金刚石相被二氧化硅相隔开,致密度为90%,硬度为26.4GPa。实施例13:将4.5克金刚石粉体放入粉体化学气相沉积设备内,金刚石粉体粒径为0.5~2微米。粉体化学气相沉积设备的背底真空为5Pa,化学气相沉积的前驱体为C6H18Si2(hexamethyldisilane:HMDS六甲基二硅烷),前驱体温度25℃,沉积温度720℃,沉积时间4小时,沉积气压400Pa。在金刚石粉体表面沉积包覆30纳米厚度的碳化硅薄膜,得到碳化硅包覆的金刚石复合粉体,其中碳化硅的质量分数为17mass%;将表面修饰后的金刚石复合粉体放入干燥箱中,50℃干燥1小时,获得金刚石复合粉体;将干燥后的金刚石复合粉体,按照质量比例65:35,与非晶态二氧化硅粉体混合,并采用刚玉研钵研磨混合0.5小时;将均匀混合的复合粉体放入石墨模具中,在30MPa烧结压力下,温度1650℃下,放电等离子烧结30分钟,升温速率100℃每分钟;将放电等离子烧结获得的复合材料进行脱模,表面抛光,获得超高硬度金刚石复合材料。对碳化硅表面修饰后的金刚石复合粉体进行微观形貌测试,对所获金刚石复合材料进行致密度,微观形貌,晶体结构,维氏硬度等测试。所获得的金刚石复合材料,没有发生金刚石的石墨化相变,金刚石相被二氧化硅相隔开,致密度为85%,硬度为15.7GPa。实施例14:将4.5克金刚石粉体放入粉体化学气相沉积设备内,金刚石粉体粒径为4~10微米。粉体化学气相沉积设备的背底真空为5Pa,化学气相沉积的前驱体为C6H18Si2(hexamethyldisilane:HMDS六甲基二硅烷),前驱体温度25℃,沉积温度720℃,沉积时间4小时,沉积气压400Pa。在金刚石粉体表面沉积包覆20纳米厚度的碳化硅薄膜,得到碳化硅包覆的金刚石复合粉体,其中碳化硅的质量分数为6mass%;将表面修饰后的金刚石复合粉体放入干燥箱中,50℃干燥1小时,获得金刚石复合粉体;将干燥后的金刚石复合粉体,按照质量比例65:35,与非晶态二氧化硅粉体混合,并采用刚玉研钵研磨混合0.5小时;将均匀混合的复合粉体放入石墨模具中,在100MPa烧结压力下,温度1650℃下,放电等离子烧结30分钟,升温速率100℃每分钟;将放电等离子烧结获得的复合材料进行脱模,表面抛光,获得超高硬度金刚石复合材料。对碳化硅表面修饰后的金刚石复合粉体进行微观形貌测试,对所获金刚石复合材料进行致密度,微观形貌,晶体结构,维氏硬度等测试。所获得的金刚石复合材料,发生金刚石的石墨化相变,金刚石相被二氧化硅相隔开,致密度为87%,硬度为13.7GPa。实施例15:将4.5克金刚石粉体放入粉体化学气相沉积设备内,金刚石粉体粒径为2~4微米。粉体化学气相沉积设备的背底真空为5Pa,化学气相沉积的前驱体为C6H18Si2(hexamethyldisilane:HMDS六甲基二硅烷),前驱体温度25℃,沉积温度720℃,沉积时间8小时,沉积气压400Pa。在金刚石粉体表面沉积包覆50纳米厚度的碳化硅薄膜,得到碳化硅包覆的金刚石复合粉体,其中碳化硅的质量分数为25mass%;将表面修饰后的金刚石复合粉体放入干燥箱中,50℃干燥1小时,获得金刚石复合粉体;将干燥后的金刚石复合粉体,按照质量比例65:35,与非晶态二氧化硅粉体混合,并采用刚玉研钵研磨混合0.5小时;将均匀混合的复合粉体放入石墨模具中,在100MPa烧结压力下,温度1650℃下,放电等离子烧结10分钟,升温速率100℃每分钟;将放电等离子烧结获得的复合材料进行脱模,表面抛光,获得超高硬度金刚石复合材料。对碳化硅表面修饰后的金刚石复合粉体进行微观形貌测试,对所获金刚石复合材料进行致密度,微观形貌,晶体结构,维氏硬度等测试。所获得的金刚石复合材料,没有发生金刚石的石墨化相变,金刚石相被二氧化硅相隔开,致密度为94%,硬度为31.6GPa。实施例16:将4.5克金刚石粉体放入化学气相沉积设备内,金刚石粉体粒径为2~4微米。化学气相沉积设备的背底真空为5Pa,化学气相沉积的前驱体为C6H18Si2(hexamethyldisilane:HMDS六甲基二硅烷),前驱体温度10℃,沉积温度690℃,沉积时间4小时,沉积气压400Pa。在金刚石粉体表面沉积包覆5纳米厚度的碳化硅薄膜,得到碳化硅包覆的金刚石复合粉体,其中碳化硅的质量分数为3mass%;将表面修饰后的金刚石复合粉体放入干燥箱中,70℃干燥1小时,获得金刚石复合粉体;将干燥后的金刚石复合粉体,按照质量比例65:35,与非晶态二氧化硅粉体混合,并采用刚玉研钵研磨混合1小时;将均匀混合的复合粉体放入石墨模具中,在100MPa烧结压力下,温度1400℃下,放电等离子烧结10分钟,升温速率100℃每分钟;将放电等离子烧结获得的复合材料进行脱模,表面抛光,获得超高硬度金刚石复合材料。对碳化硅表面修饰后的金刚石复合粉体进行微观形貌测试,对所获金刚石复合材料进行致密度,微观形貌,晶体结构,维氏硬度等测试。所获得的金刚石复合材料,没有发生金刚石的石墨化相变,金刚石相被二氧化硅相隔开,致密度为82%,硬度为14.6GPa。实施例17:将4.5克金刚石粉体放入化学气相沉积设备内,金刚石粉体粒径为2~4微米。化学气相沉积设备的背底真空为5Pa,化学气相沉积的前驱体为C6H18Si2(hexamethyldisilane:HMDS六甲基二硅烷),前驱体温度30℃,沉积温度740℃,沉积时间4小时,沉积气压400Pa。在金刚石粉体表面沉积包覆40纳米厚度的碳化硅薄膜,得到碳化硅包覆的金刚石复合粉体,其中碳化硅的质量分数为20mass%;将表面修饰后的金刚石复合粉体放入干燥箱中,70℃干燥2小时,获得金刚石复合粉体;将干燥后的金刚石复合粉体,按照质量比例65:35,与非晶态二氧化硅粉体混合,并采用刚玉研钵研磨混合1小时;将均匀混合的复合粉体放入石墨模具中,在100MPa烧结压力下,温度1700℃下,放电等离子烧结30分钟,升温速率100℃每分钟;将放电等离子烧结获得的复合材料进行脱模,表面抛光,获得超高硬度金刚石复合材料。对碳化硅表面修饰后的金刚石复合粉体进行微观形貌测试,对所获金刚石复合材料进行致密度,微观形貌,晶体结构,维氏硬度等测试。所获得的金刚石复合材料,没有发生金刚石的石墨化相变,金刚石相被二氧化硅相隔开,致密度为93%,硬度为30.1GPa。本发明所列举的工艺参数(如质量分数、烧结压力、温度、时间等)的上下限、区间取值都能实现本发明,在此不一一列举实施例。