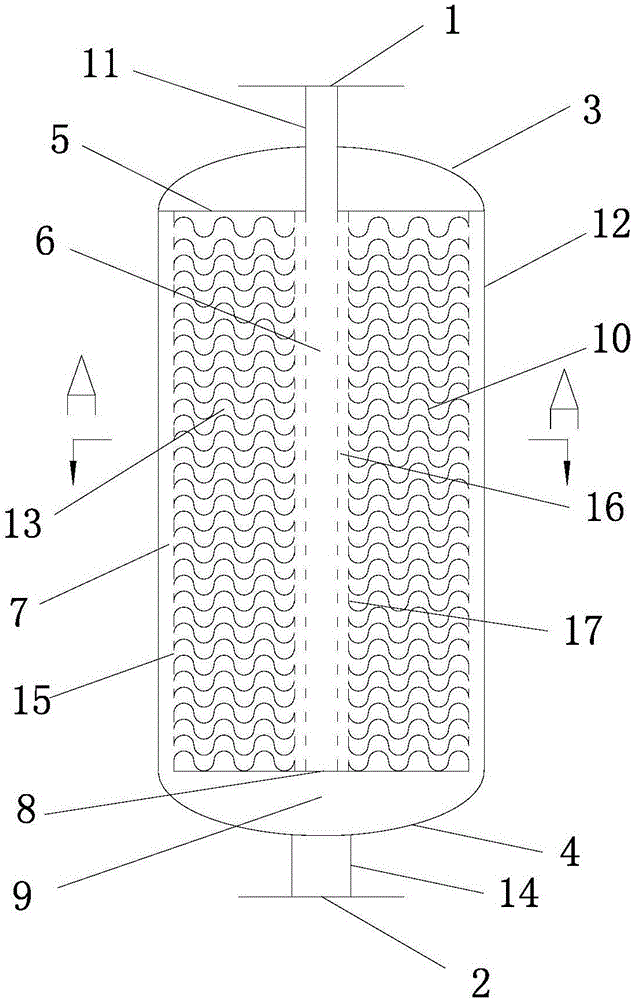
本公开涉及重整制氢领域,具体地,涉及一种重整制氢反应器、制氢转化炉及重整制氢方法。
背景技术:
:氢气不仅是重要的化工原料,也是一种清洁燃料。氢气在现代工业、尤其是石油化工工业、燃料电池等国民经济中扮演着越来越重要的角色。在全球原油不断重质化、劣质化趋势加剧以及人们对清洁油品数量需求不断增加、质量标准不断提升,环境法规不断严格的多重压力下,对氢气需求也越来越大,进而对制氢装置也提出了更高的要求。制氢工艺主要有水电解法、轻烃水蒸气转化法、部分氧化法和甲醇裂解法等,目前运用最广泛的是轻烃水蒸气转化法。轻烃水蒸气转化法制氢的原料以天然气、石脑油、炼厂气等含碳轻质烃类为主。其转化过程为:轻质烃类与水蒸汽在一定的温度、压力以及催化剂作用下发生反应,生成氢气及一氧化碳,一氧化碳再经过水煤气变换反应进一步生成氢气,进一步提高轻质烃类目的产物收率。制氢反应过程中发生的主要化学反应有:转化反应cnhm+nh2o→nco+(n+m/2)h2△h=206kj/mol变换反应co+h2o→co2+h2△h=-36kj/mol转化反应是一个强吸热反应,在传统的制氢炉中,通过燃料燃烧,将装填有转化催化剂的转化炉管加热到900~1000℃进行制氢反应。常见的重整制氢活性组分有pt、pd、ir、rh等第vш族过渡元素,由于其价格高,限制了工业应用。目前重整制氢工业应用最为广泛的活性组分是镍。催化剂活性高低与催化剂比表面轴向大小直接相关,相对而言,比表面越大,活性组分的分散度越好,活性中心数目越多,从而提高了催化剂的催化活性。现有的制氢转化炉在炉管中装填一定颗粒尺寸、形状的镍基催化剂,往往会出现装填不均匀,引起原料气偏流,造成原料转化率低,催化剂易积碳失活,降低装置的操作周期。另外,炉管中装填颗粒尺寸较小的催化剂,虽然可以提高催化剂的装填量,增加催化剂活性中心数目,在一定程度上提高原料的处理能力和转化率,不足之处在于催化剂尺寸越小,炉管压降越大,增加了原料气压缩机的能量消耗。技术实现要素:本公开的目的是提供一种重整制氢反应器、重整制氢转化炉及重整制氢反应方法,该重整制氢反应器及采用该重整制氢反应器的转化炉的压降低、无气体偏流和短路现象;采用该重整制氢转化炉的方法转化率高。为了实现上述目的,本公开第一方面提供一种重整制氢反应器,该反应器包括圆筒形密封承压壳体、进气口、出气口、从所述壳体顶部伸入到壳体内部的第一直管、从所述壳体底部伸入到壳体内部的第二直管和设置在所述壳体内所述第一直管下方所述第二直管上方的催化反应单元;所述进气口与所述第一直管连通,所述出气口与所述第二直管连通;所述催化反应单元的顶部和底部分别由顶部密封板和底部密封板密封,所述催化反应单元包括轴向设置的中心管,所述中心管穿过顶部密封板与第一直管流体连通;所述催化反应单元外侧壁与壳体的内壁之间形成有环隙;所述中心管和所述催化反应单元的侧壁分别形成有开孔,以使所述中心管通过所述开孔与所述环隙流体连通;所述底部密封板与所述壳体下部的内壁之间形成有与所述环隙流体连通的集气腔,所述环隙通过所述集气腔与所述第二直管连通;所述催化反应单元内设有微催化反应板,所述催化反应板的板面负载有重整制氢催化剂。可选地,所述微催化反应板沿轴向延伸且围绕所述中心管呈螺旋状分布,所述微催化反应板的顶端与所述顶部密封板密封连接,所述微催化反应板的底端与所述底部密封板密封连接。可选地,所述微催化反应板为一个或同轴设置的多个环状板,所述微催化反应板的内边缘与所述催化反应单元内侧壁密封固定连接,所述微催化反应板的外边缘与所述催化反应单元外侧壁密封固定连接。可选地,微催化反应板为选自平面板、齿形板、波纹板和波形板中的至少一种。本公开的第二方面提供一种重整制氢转化炉,包括进气管、出气管、烧嘴和燃烧室,该转化炉还包括本公开第一方面的重整制氢反应器,所述重整制氢反应器位于所述燃烧室内,所述重整制氢反应器的进气口与所述进气管连通,所述重整制氢反应器的出气口与所述出气管连通。本公开的第三方面提供采用本公开第二方面的重整制氢转化炉进行重整制氢反应的方法,该方法包括以下步骤:(1)使燃料气和空气经过所述烧嘴喷入所述燃烧室进行燃烧;(2)使原料气与水蒸气经所述转化炉的进气管进入所述重整制氢反应器,在所述催化反应单元内进行重整制氢反应,得到富含氢气的转化气。可选地,所述重整制氢反应的条件包括:反应温度为700~1100℃,反应压力为1.8~5.5mpag,水蒸气中的h2o与原料气中的碳原子的摩尔比为(2.5~5):1,空速为1000~100000h-1。可选地,所述原料气在所述催化反应单元内的平均流速为0.001~100m/s。可选地,所述原料气为天然气、液化石油气、炼厂气、重整氢提浓psa的解析气和石脑油中的至少一种。可选地,所述重整制氢反应催化剂包括重整制氢活性组分,所述重整制氢活性组分包括镍、钌、铂、钯、铱和铑中的至少一种。与现有技术相比,本发明的有益效果为:(1)重整制氢反应器的催化反应单元为由微催化反应板构成的径向反应区,反应板上负载有制氢反应的催化剂,反应气体从气相主体扩散至催化活性中心的距离缩短,大大降低了传质阻力(扩散阻力几乎为零),同时生成的产物能够很快扩散到流体主体,产物在反应器中停留时间较短,从根本上提高了制氢反应的转化效率,达到提高单位催化剂产品时空产率的目的。(2)反应气体从中心管均匀分布进入径向反应区且由内向外流动,流道面积逐渐增大,有利于体积增加的制氢反应向产物方向移动。另外,随着反应物流由内向外流动,外层微催化反应板的温度高于内层微催化反应板,处于环隙处的微催化反应板的温度最高,由于制氢反应是一个吸热反应,因此,有利于制氢反应的进行。(3)与装填颗粒状的重整制氢反应器相比,采用微催化反应板,反应器所用的活性金属总量明显减少、压降低。在相同处理规模条件下,本公开的重整制氢反应器及由其构成的转化炉设备尺寸较传统小5%~30%,压降低3%~55%。(4)与装填颗粒状的重整制氢反应器相比,本公开的重整制氢反应器的微催化反应板不易积碳失活,使用寿命长,压降低,床层压降较同处理量的反应器低(15%~90%);(5)催化反应单元由微催化反应板组成,增加了活性中心数量、提高了反应气体在催化反应活性中心的均匀度,避免出现反应死区和气体偏流现象,能够充分保证整个运行周期内的平稳运行。(6)作为重整制氢转化炉管能够适用于不同类型的转化炉,使用范围广,且可以根据实际的工业生产要求通过具有功能化的套筒的集成方式以及数量的增减达到控制和调节生产,有利于实现设备的最大利用效率,无明显放大效应,同时缩短设备的加工时间,进一步降低反应器生产成本。本公开的其他特征和优点将在随后的具体实施方式部分予以详细说明。附图说明附图是用来提供对本公开的进一步理解,并且构成说明书的一部分,与下面的具体实施方式一起用于解释本公开,但并不构成对本公开的限制。在附图中:图1是本公开的重整制氢反应器的一种具体实施方式的结构示意图;图2是本公开的重整制氢反应器的一种具体实施方式的剖视图(即图1中a-a面的剖视图);图3是本公开的重整制氢反应器的一种具体实施方式的催化反应单元侧壁示意图;图4是本公开的重整制氢反应器的一种具体实施方式的顶部密封板的示意图;图5是本公开的重整制氢反应器的第二种具体实施方式的结构示意图;图6是本公开的重整制氢反应器的第二种具体实施方式的剖视图(即图5中a-a面的剖视图);图7是本公开的重整制氢反应器的一种具体实施方式的构成反应器催化反应单元侧壁所用三棱柱形组件结构示意图;图8是本公开的重整制氢反应器的一种具体实施方式的构成反应器催化反应单元侧壁所用圆柱形组件结构示意图;图9是本公开的重整制氢反应器的第三种具体实施方式的结构示意图;图10是本公开的重整制氢反应器的第三种具体实施方式的剖视图(即图9中a-a面的剖视图);图11是本公开的重整制氢反应器的第四种具体实施方式的结构示意图;图12是本公开的重整制氢反应器的第四种具体实施方式的剖视图(即图11中a-a面的剖视图);图13是本公开的重整制氢反应器的一种具体实施方式的齿形微催化反应板的结构示意图;图14是本公开的重整制氢反应器的一种具体实施方式的波纹微催化反应板的结构示意图;图15是本公开的重整制氢反应器的一种具体实施方式的波形微催化反应板的结构示意图;图16是本公开的重整制氢转化炉的一种具体实施方式的结构示意图;图17是本公开的重整制氢转化炉的另一种具体实施方式的结构示意图;图18是本公开的重整制氢反应器的第五种具体实施方式的结构示意图;图19是本公开的重整制氢反应器的第五种具体实施方式的剖视图(即图18中a-a面的剖视图);图20是本公开的重整制氢反应器的第六种具体实施方式的剖视图;图21是本公开的重整制氢反应器的第七种具体实施方式的剖视图;图22是本公开的重整制氢反应器的第八种具体实施方式的结构示意图;图23是本公开的重整制氢反应器的第九种具体实施方式的结构示意图;图24是本公开的重整制氢反应器的第十种具体实施方式的结构示意图;图25是本公开的重整制氢反应器的第十一种具体实施方式的示意图;图26是本公开的重整制氢反应器的一种具体实施方式的中心管示意图;图27是本公开的重整制氢反应器另一种具体实施方式的中心管示意图。附图标记说明1-进气口2-出气口3-上封头4-下封头5-顶部密封板6-中心管7-环隙8-底部密封板9-集气腔10-微催化反应板11-第一直管12-壳体14-第二直管15-催化反应单元外侧壁16-缓冲腔17-催化反应单元内侧壁20-重整制氢转化炉21-重整制氢反应器22-燃烧室23-烧嘴24-进气管25-出气管。具体实施方式以下结合附图对本公开的具体实施方式进行详细说明。应当理解的是,此处所描述的具体实施方式仅用于说明和解释本公开,并不用于限制本公开。在本公开中,在未作相反说明的情况下,使用的方位词如“上、下、顶部、底部”通常是指装置在正常使用状态下的上和下、顶部和底部,具体可以参考图1的图面方向。“内、外”是针对装置本身的轮廓而言的。此外,术语“第一”、“第二”仅用于描述目的,而不能理解为指示或暗示相对重要性或者隐含指明所指示的技术特征的数量。由此,限定有“第一”、“第二”的特征可以明示或者隐含地包括一个或者更多个该特征。在本公开的描述中,“多个”的含义是两个或两个以上,除非另有明确具体的限定。本公开的第一方面提供一种重整制氢反应器,该反应器包括圆筒形密封承压壳体12、进气口1、出气口2、从壳体12顶部伸入到壳体内部的第一直管11、从壳体12底部伸入到壳体内部的第二直管14和设置在壳体12内第一直管11下方第二直管14上方的催化反应单元13;进气口与第一直管11连通,出气口2与第二直管14连通;催化反应单元13的顶部和底部分别由顶部密封板5和底部密封板8密封,催化反应单元13包括轴向设置的中心管6,中心管6穿过顶部密封板5与第一直管11流体连通;催化反应单元外侧壁15与壳体12的内壁之间形成有环隙7;中心管6和催化反应单元13的侧壁分别形成有开孔,以使中心管6通过开孔与环隙7流体连通;底部密封板8与壳体12下部的内壁之间形成有与环隙7流体连通的集气腔9,环隙7通过集气腔9与第二直管14连通;催化反应单元13内设有微催化反应板10,催化反应板的板面负载有重整制氢催化剂。本公开的重整制氢反应器采用微催化反应板,反应板上负载有制氢反应所需的活性组分,减少了催化活性金属用量且催化剂不易积碳失活、缩短了反应气体扩散至催化活性中心的距离,降低了传质阻力和反应器压降,提高了制氢反应转化率;反应气体在反应器中由中心向外流动,流道面积逐渐增大、反应板温度逐渐升高,有利于作为体积增加和吸热反应的制氢反应转化率的提升;该重整制氢反应器使用范围广,作为制氢转化炉的炉管可以适用于不同种类的转化炉。本公开所指的重整制氢反应器,通常在工业生产中也称为制氢转化炉管或转化炉管,在无特别说明情况下,以上三种称呼均表示相同的装置。根据本公开,微催化反应板可以在任选的一个板面负载有重整制氢催化剂,也可以在微催化反应板的两个板面均负载有重整制氢催化剂,优选为两个板面均负载催化剂,以进一步提高反应器进行制氢反应的转化率。重整制氢催化剂可以采用本领域技术人员所熟知的催化活性组分,例如负载的活性组分可以是具有重整制氢反应活性的镍、钌、铂、钯、铱和铑等金属;所述的负载是指可以通过浸渍、离子溅射、涂覆或装填等方法将含有活性组分的催化剂或直接将活性组分负载到微催化反应板上。其中,活性金属组分涂覆负载过程可以采用本领域技术人员所熟知的包括金属基体的预处理和催化剂沉积两个阶段的涂覆方法。根据本公开,微催化反应板10可以沿反应器轴向或径向延伸,或者微催化反应板10的延伸方向与水平方向呈夹角θ,0°<θ<90°。催化反应单元13内可以包括一个或多个微催化反应板10,多个微催化反应板10在催化反应单元13内可以按本领域的常规方式排布,只要保证反应原料气在催化反应单元13从中心向四周径向运动即可。为了进一步增强反应原料气与微催化反应板10上催化剂的接触,在本公开的一种具体实施方式中,如图18-21所示,催化反应单元13内的微催化反应板10可以沿轴向延伸且围绕中心管6呈螺旋状分布,微催化反应板10的顶端可以与顶部密封板5密封连接,微催化反应板10的底端可以与底部密封板8密封连接。在另一种具体实施方式中,如图1-2所示,为了进一步降低反应器压降、适应制氢反应体积增加的特点,微催化反应板10为一个或同轴设置的多个环状板,微催化反应板10的内边缘可以与催化反应单元内侧壁17密封固定连接,微催化反应板10的外边缘可以与催化反应单元外侧壁15密封固定连接,环状的微催化反应板10与水平方向的夹角θ优选为0°~45°,此时环状的微催化反应板10优选沿径向延伸,即夹角θ为0°。根据本公开,重整制氢反应器采用负载有重整制氢催化剂的微催化反应板10可以减少反应器内催化活性金属的总用量、减小反应器尺寸、降低反应器压降,其中微催化反应板10可以为本领域常规种类。为了进一步增加反应器内催化活性中心数目,优选地,微催化反应板10可以为选自平面板、齿形板、波纹板和波形板中的至少一种,如图19、图20、图21、图13、图14、图15所示,更优选为齿形板、波纹板和波形板中的至少一种。其中齿形板、波纹板和波形板的结构和尺寸不做限制,只要满足负载活性组分、满足制氢工艺条件要求即可。为了提高催化反应单元内装填微催化反应板数目,在反应器内优选同一种类型微催化反应板。进一步地,为了便于生产、安装为反应板,同时均匀分布原料气,每一块微催化反应板的齿形波形大小、类型、疏密程度等应完全一致,本发明对齿形波形大小、类型、疏密程度不做具体限制,只要满足制氢反应工艺条件即可。根据本公开,在相同的反应条件和反应器直径下,催化反应单元13的数量可以增加反应气体与催化剂的接触几率,提高转化率的作用。可以根据实际反应情况来调整催化反应单元13的数量,例如催化反应单元13的数量可以为1~500个,优选为1~300个。为了提高反应原料分布均匀度,优选地,催化反应单元13、中心管6与壳体12呈同轴方式布置,多个催化反应单元可以同轴设置。在这种情况下,催化反应单元内侧壁17与中心管6的管壁之间以及相邻的两个催化反应单元13的筒壁之间可以形成有缓冲腔16,以便于反应原料气在缓冲腔内进一步均匀分配。在本公开的一种具体实施方式中,如图9所示,催化反应单元可以包括同轴套设的多个催化反应单元13;在其他实施方式中,多个催化反应单元13同轴上下排列。根据本公开,为了延长微反应板的使用寿命,中心管6、微催化反应板可以采用金属材质、陶瓷材质,优选采用不与反应系统中的气体发生反应的金属材质。为了延长使用寿命,顶部密封板5、底部密封板8可以设有膨胀节,如图4所示。根据本公开,催化反应单元13和中心管6的相对尺寸可以在较大范围内变化,本公开不做特殊要求。催化反应单元13的侧壁和中心管6的管壁可以为约翰逊网、开孔板、棱柱形或圆柱形构成壁面中的至少一种,约翰逊网是本
技术领域:
人员所熟知的,本发明在此不再赘述。优选地,催化反应单元13的侧壁和中心管6的管壁可以为开孔板,开孔板的开孔形式可以是如图26所示的圆孔型或如图27所示的槽型,开孔的形状、开孔大小、开孔多少(开孔率)本发明不做限制,只要满足重整制氢工艺条件即可。根据本公开,重整制氢反应器的壳体、上下封头采用的材质可以与常规重整制氢炉管选择的材质相同,例如:hp-40nb,重整制氢反应器壳体材质是本领域技术人员所熟知的,本发明不再赘述。重整制氢反应器的具体尺寸也可以在较大范围内变化。进一步地,为了适应新建制氢转化炉装置规模或现有制氢转化炉装置改造升级,本公开的重整制氢反应器的反应器内径可以为30~1000mm,优选为50~300mm;反应器中催化反应单元长度可以为1000mm~30000mm,优选为3000mm~15000mm。如图1所示,反应原料气在本公开的重整制氢反应器中的流动情况可以包括:反应原料气从反应器进气口1经第一直管11进入催化反应单元13的中心管6,经中心管壁开孔进入缓冲腔16汇集,在缓冲腔16的进一步缓冲、再分配作用下,反应物流继续向外流动,均匀径向进入催化反应单元13,并径向向外流动,反应原料气在向外流动的同时在微催化反应板10表面负载的催化剂活性中心发生反应,反应物流继续向外流动,穿过催化反应单元13的筒壁开孔向外流动至环隙7汇集,进入集气腔9,通过第二直管14、出气口2离开重整制氢反应器。如图16-17所示,本公开的第二方面提供一种重整制氢转化炉,包括进气管24、出气管25、烧嘴23和燃烧室22,该转化炉还包括本公开第一方面的重整制氢反应器21,重整制氢反应器21位于燃烧室22内,重整制氢反应器21的进气口1与进气管24连通,重整制氢反应器的出气口2与出气管25连通。根据本公开,重整制氢转化炉可以为本领域常规种类,例如可以为顶烧炉、侧烧炉、底烧炉和梯形炉中的至少一种,优选为如图16所示的顶烧炉和/或如图17所示的侧烧炉。转化炉中烧嘴、燃料种类等不做特殊限制,只要能够满足重整制氢所需能量即可。另外,本公开对安装在转化炉进气管、出气管之间的反应器数量以及排列方式等不做特别限制,只要满足重整制氢工艺条件要求即可。本公开的重整制氢转化炉炉管压降低、炉管内单位体积催化剂的产品时空产率高,且转化炉整体尺寸小,降低了设备投资和能耗。本公开的第三方面提供采用本公开第二方面的重整制氢转化炉进行重整制氢反应的方法,该方法包括以下步骤:(1)使燃料气和空气经过烧嘴喷入燃烧室进行燃烧;(2)使原料气与水蒸气经转化炉的进气管进入重整制氢反应器,在催化反应单元13内进行重整制氢反应,得到富含氢气的转化气。本公开的重整制氢反应方法转化炉管内压降低、原料气转化率高,能够满足制氢反应要求。在根据本公开的重整制氢反应方法中,重整制氢反应的条件可以在较大范围内变化,优选地,重整制氢反应器内的反应温度可以为700~1100℃,优选为800~950℃;反应压力可以为1.8~5.5mpag,优选为1.8~3.5mpag,水蒸气中的h2o与原料气中的碳原子的摩尔比可以为(2.5~5):1,优选为(2.5~4):1。上述优选的反应条件下,本公开的重整制氢反应转化率更高。进一步地,为了提高原料气转化率,原料气空速可以为1000~100000h-1,进一步优选3000~90000h-1,最优选为8000~70000h-1。为了提高原料气转化率,原料气在催化反应单元内的平均流速可以为0.3~90m/s。进一步地,在微催化反应板沿轴向延伸且围绕中心管6呈螺旋状分布的实施方式中,原料气通过微催化反应板的螺旋状结构的平均流速可以为0.003~90m/s,优选为0.1~75m/s;在多个环状的微催化反应板10沿轴向间隔设置的实施方式中,原料气通过的平均流速可以为0.001~100m/s,优选为0.3~90m/s。在根据本公开的重整制氢反应方法中,反应原料气可以为天然气、液化石油气、炼厂气、重整氢提浓psa的解析气和石脑油中的至少一种。其中,天然气主要成为甲烷,并含有少量的乙烷等小分子烃类、二氧化碳和氮气等,天然气中的硫含量低,且主要为硫化氢、硫醇、羟基硫等,容易通过简单的加氢处理就能将其脱除掉;炼厂气主要是指原油蒸馏装置的不凝气、催化干气、焦化干气、加氢干气和重整干气等;液化石油气主要组分为丙烷、丙烯、丁烷、丁烯,可以是一种或几种上述烃的混合物,并含有少量戊烷、戊烯和微量硫化物杂质,其中氧硫化碳用醇胺吸收塔脱除,并用碱洗法去除硫化物;重整氢提浓psa的解析气中含有约大量的氢气及一些小分子烃类;石脑油的择优顺序为:干点70℃的直溜轻石脑油(重整拔头油)、炼厂窄馏分重整抽余油、干点146℃的全馏分直溜汽油、单程加氢裂化石脑油。在根据本公开的重整制氢反应方法中,蒸汽指中压蒸汽,其温度可以为420℃左右、压力可以为3.5mpa左右,在实际配气过程中蒸汽的温度、压力可能会出现波动,本公开不做具体限制,只要满足制氢工艺需条件即可。在根据本公开的重整制氢反应方法中,重整制氢反应催化剂可以为本领域常规种类,例如,重整制氢反应催化剂可以包括重整制氢活性组分,重整制氢活性组分可以包括镍、钌、铂、钯、铱和铑中的至少一种。下面将结合附图通过实施例来进一步说明本发明,但是本公开并不因此而受到任何限制。实施例1如图1、图2、图3、图4、图15所示,本实施例所采用的重整制氢反应器包括含有上端设有第一直管11、下端设有第二直管14的承压壳体12,壳体内设有筒状催化反应单元13,催化反应单元13包括轴向设置的中心管6,第一直管11的上部设置有进气口1,第二直管14下部设置有出气口2。催化反应单元由水平平行设置的波形催化反应板构成,中心管6、筒状催化反应单元13与壳体12呈同轴方式布置;催化反应单元13的微催化反应板10与催化反应单元外侧壁15、催化反应单元内侧壁17连接固定;催化反应单元外侧壁15、催化反应单元内侧壁17分别与顶部密封板5、底部密封板8连接固定;中心管6采用圆形开孔,开孔率16.8%,微催化反应板10两侧负载有重整制氢反应所需催化活性组分nio。重整制氢反应器的内径为130mm,切线长度11500mm,中心管内径为25mm,径向催化反应单元高度9500mm,催化反应单元13的相邻两微催化反应板在催化反应单元13直径二分之一处间距为1mm,环隙距离为5mm,催化反应单元13相邻微反应板之间的平均流速为0.02m/s。反应器壳体材质采用hp40-nb(含有cr、ni、nb、w、mo、ti等元素),微催化反应板10采用fe-cr-al/al2o3材质材料为催化负载基板,且为波形基板,波峰与波谷距离为2.5mm,同一微催化反应板上两相邻波峰或相邻波谷之间的距离为5mm,基板两侧负载活性金属为nio,含量为17.5%。本实施例的重整制氢转化炉如图16所示,包括上述重整制氢反应器21、进气管24、出气管25、烧嘴23和燃烧室22,重整制氢反应器21位于燃烧室22内,重整制氢反应器21的进气口1与进气管24连通,重整制氢反应器的出气口2与出气管25连通。将本实施例的重整制氢反应器和转化炉应用于天然气蒸汽重整制氢反应,主要步骤包括:1)使燃料气和空气经转化炉的烧嘴23喷入燃烧室22,使燃料在转化炉的燃烧室中燃烧提供制氢反应所需热量,反应器温度为910℃;2)使水蒸汽与ch4摩尔比为3.1的混合气体(温度500℃,压力3.0mpag),流量为30kmol/h,空速42300h-1,充分混合后进入转化炉进气管,通过反应器第一直管11,然后依次进入中心管6、缓冲腔16、套筒15的微催化反应板上进行重整制氢反应,发生反应后的转化气通过环隙7、集气腔9、第二直管14离开反应器,进入转化炉出气管25,将富含氢气的转化气排出至转化炉外部。经检测,出口甲烷含量(不含水蒸汽)为0.2%。表1中给出的是本实施例的重整制氢反应器与现有技术中相同反应器尺寸及相同催化反应单元尺寸的制氢反应器对比情况。从反应器床层压降、ch4转化率、空速三个指标可以看出,本实施例的反应器都表现出了优异的性能,尤其是在降低反应器压降,提高反应器空速方面的优势尤为突出。表1本实施例的重整反应器与常规制氢反应器对比反应器类型压降,mpach4转化率/(%)空速,h-1常规反应器0.33953400本实施例的反应器0.06≥9942300实施例2如图2、图3、图4、图5所示,本实施例的重整制氢反应器和转化炉与实施例1的反应器尺寸、相邻两催化反应板间距、环隙距离、微反应板的基体材质和单位面积活性组分nio负载量参数相同。与实施例1不同之处在于,本实施例中微催化反应板为平面微反应板。同理将本实施例的反应器和转化炉应用于天然气蒸汽重整制氢反应。制氢工艺条件与实施例1相同,经检测,出口甲烷含量(不含水蒸汽)为1.3%。表2中给出的是本实施例的重整制氢反应器与现有技术中相同反应器尺寸及相同催化反应单元尺寸的制氢反应器对比情况。从反应器床层压降、ch4转化率、空速三个指标可以看出,本实施例的反应器都表现出了优异的性能,尤其是在降低反应器压降,提高反应器空速方面的优势尤为突出。表2本实施例的重整反应器与常规制氢反应器对比反应器类型压降,mpach4转化率/(%)空速,h-1常规反应器0.33953400本实施例的反应器0.05≥9742300实施例3如图5、图6、图7所示,本实施例的重整制氢反应器和转化炉与实施例2的反应器尺寸、相邻两催化反应板间距、环隙距离、微反应板的基体材质和单位面积活性组分nio负载量参数相同。与实施例2不同之处在于,本实施例中催化反应单元内侧壁17和催化反应单元外侧壁15由正三棱柱形hp40-nb材质构成,三棱柱边长9.5mm,相邻三棱柱构成的缝隙间距为1.5mm。同理将本实施例的反应器和转化炉应用于天然气蒸汽重整制氢反应。制氢工艺条件与实施例1相同,经检测,出口甲烷含量(不含水蒸汽)为1.5%。表3中给出的是本实施例的重整制氢反应器与现有技术中相同反应器尺寸及相同催化反应单元尺寸的制氢反应器对比情况。从反应器床层压降、ch4转化率、空速三个指标可以看出,本实施例的反应器都表现出了优异的性能,尤其是在降低反应器压降,提高反应器空速方面的优势尤为突出。表3本实施例的重整反应器与常规制氢反应器对比反应器类型压降,mpach4转化率/(%)空速,h-1常规反应器0.33953400本实施例的反应器0.04≥97.542300实施例4如图9、图10所示,本实施例的重整制氢反应器和转化炉、制氢工艺条件等与实施例2数相同。与实施例2不同之处在于,本实施例采用两个套筒构成的径向催化反应单元,两个套筒的径向尺寸相同,套筒的其他参数与实施例2相同。制氢工艺条件与实施例1相同,经检测,出口甲烷含量(不含水蒸汽)为1.0%。表4中给出的是本实施例的重整制氢反应器与现有技术中相同反应器尺寸及相同催化反应单元尺寸的制氢反应器对比情况。从反应器床层压降、ch4转化率、空速三个指标可以看出,本实施例的反应器都表现出了优异的性能,尤其是在降低反应器压降,提高反应器空速方面的优势尤为突出。表4本实施例的重整反应器与常规制氢反应器对比反应器类型压降,mpach4转化率/(%)空速,h-1常规反应器0.33953400本实施例的反应器0.07≥9842300实施例5如图11、图12示,本实施例的重整制氢反应器和转化炉、制氢工艺条件等与实施例1数相同。与实施例1不同之处在于,本实施例套筒13的微催化反应板内侧直接与中心管6外壁连接固定,省却了缓冲腔16、催化反应单元内侧壁17。同理将本实施例的重整制氢反应器和转化炉应用于天然气蒸汽重整制氢反应。制氢工艺条件除空速与实施例1不同外,其余工艺条件均相同,本实施例的空速为48600。经检测,出口甲烷含量(不含水蒸汽)为1.2%。表5中给出的是本实施例的重整制氢反应器与现有技术中相同反应器尺寸及相同催化反应单元尺寸的制氢反应器对比情况。从反应器床层压降、ch4转化率、空速三个指标可以看出,本实施例的反应器都表现出了优异的性能,尤其是在降低反应器压降,提高反应器空速方面的优势尤为突出。表5本实施例的重整反应器与常规制氢反应器对比反应器类型压降,mpach4转化率/(%)空速,h-1常规反应器0.33953400本实施例的反应器0.1≥9848600实施例6如图11、图12所示,本实施例的重整制氢反应器和转化炉与实施例5相同。与实施例5不同之处在于,本实施例采用重整氢提浓psa解析气作为反应原料,解析气组见表6。燃料在转化炉的燃烧室中燃烧提供制氢反应所需热量,反应器温度为905℃。水蒸汽与ch4摩尔比为2.5的混合气体(温度500℃,压力3.05mpag),流量为35kmol/h,空速49300h-1,充分混合后进入转化炉进气管,通过反应器第一直管11、进入催化反应单元进行重整制氢反应,发生反应后的转化气通过环隙7、集气腔9、第二直管14离开反应器,进入转化炉出气管,将富含氢气的转化气排出至转化炉外部。经检测,出口甲烷含量(不含水蒸汽)为0.75%。采用实施例5中提供的反应器,反应原料、工艺条件与实施例不同,得到的反应结果与常规反应器在相同反应原料与工艺条件得到的反应结果对比情况见表7。从反应器床层压降、ch4转化率、空速三个指标可以看出,本实施例的反应器都表现出了优异的性能,尤其是在降低反应器压降,提高反应器空速方面的优势尤为突出。表6重整氢提浓psa解析气组成表7本实施例的制氢方法反应器与常规制氢反应器对比反应器类型压降,mpach4转化率/(%)空速,h-1常规反应器0.38974400本实施例的反应器0.13≥9949300实施例7如图18、图19所示,本实施例所采用的重整制氢反应器包括上端设有第一直管11、下端设有第二直管14的承压壳体12,壳体内设有一个含有中心管6的催化反应单元13,所述第一直管11的上部设置有进气口1,第二直管14下部设置有出气口2。催化反应单元13由微催化反应板10绕中心管6呈螺旋形布置构成,中心管6与壳体12呈同轴方式布置;微催化反应板10上边缘与催化反应单元顶部密封板5密封固定,微催化反应板10下边缘与催化反应单元底部密封板8密封固定;微催化反应板10两侧负载有重整制氢反应所需催化活性组分nio。重整制氢反应器的内径为110mm,切线长度12500mm,中心管内径为30mm,微催化反应板10的长度为10000mm,中心管采用圆形开孔,孔径大小为均匀开孔,开孔率为17.5%,相邻两催化反应板间距为1mm,最外层微催化反应板与壳体内壁的环隙距离为3mm,微反应板之间的平均流速为1.3m/s。反应器壳体材质采用hp40-nb(含有cr、ni、nb、w、mo、ti等元素),微催化反应板10采用fe-cr-al/al2o3材质材料为催化负载基板,且为平面基板,基板两侧负载活性金属为nio,含量为13.5%。本实施例的重整制氢转化炉如图16所示,包括上述重整制氢反应器21、进气管24、出气管25、烧嘴23和燃烧室22,重整制氢反应器21位于燃烧室22内,重整制氢反应器21的进气口1与进气管24连通,重整制氢反应器的出气口2与出气管25连通。将本实施例的重整制氢反应器和转化炉应用于天然气蒸汽重整制氢反应,主要步骤包括:1)使燃料气和空气经转化炉的烧嘴23喷入燃烧室22,使燃料在转化炉的燃烧室中燃烧提供制氢反应所需热量,反应器温度为950℃;2)使水蒸汽与ch4摩尔比为3.2的混合气体(温度500℃,压力3.2mpag),流量为44.91kmol/h,空速63230h-1,充分混合后进入转化炉进气管,通过反应器第一直管11、中心管6进入微催化反应板上进行重整制氢反应,发生反应后的转化气通过催化反应单元出气口15、环隙7、集气腔9、第二直管14离开反应器,进入转化炉出气管,将富含氢气的转化气排出至转化炉外部。经检测,出口甲烷含量(不含水蒸汽)为1.45%。表8中给出的是本实施例的重整制氢反应器与现有技术中相同反应器尺寸及相同催化反应单元尺寸的制氢反应器对比情况。从反应器床层压降、ch4转化率、空速三个指标可以看出,本实施例的反应器都表现出了优异的性能,尤其是在降低反应器压降,提高反应器空速方面的优势尤为突出。表8本实施例的一种重整反应器与常规制氢反应器对比反应器类型压降,mpach4转化率/(%)空速,h-1常规反应器0.33953400本实施例的反应器0.05≥95.563230实施例8如图18、图20、图13所示,本实施例的重整制氢反应器和转化炉与实施例7的反应器尺寸、相邻两催化反应板间距、最外层微催化反应板与壳体内壁的环隙距离、微反应板的基体材质和单位面积活性组分nio负载量参数相同。与实施例7不同之处在于,本实施例中微催化反应板为齿形微反应板,其齿形方向可以为沿反应器径向方向。对于齿形板而言,波峰与波谷距离为4mm,同一微形板两相邻波峰或相邻波谷之间的距离为6.5mm。同理将本实施例的重整制氢反应器和转化炉应用于天然气蒸汽重整制氢反应。制氢工艺条件与实施例7相同,经检测,出口甲烷含量(不含水蒸汽)为1.2%。表9中给出的是本实施例的重整制氢反应器与现有技术中相同反应器尺寸及相同催化反应单元尺寸的制氢反应器对比情况。从反应器床层压降、ch4转化率、空速三个指标可以看出,本实施例的反应器都表现出了优异的性能,尤其是在降低反应器压降,提高反应器空速方面的优势尤为突出。表9本实施例的另一种重整反应器与常规制氢反应器对比反应器类型压降,mpach4转化率/(%)空速,h-1常规反应器0.33953400本实施例的反应器0.062≥9663230实施例9如图18、图21、图15所示,本实施例的重整制氢反应器和转化炉与实施例8的反应器尺寸、相邻两催化反应板间距、最外层微催化反应板与壳体内壁的环隙距离、微反应板的基体材质和单位面积活性组分nio负载量参数相同。与实施例8不同之处在于,本实施例中微催化反应板为波形微反应板,其波形方向为沿反应器径向方向。对于波形板而言,波峰与波谷距离为4mm,同一微形板两相邻波峰或相邻波谷之间的距离为6.5mm。同理将本实施例的反应器应用于天然气蒸汽重整制氢反应。制氢工艺条件与实施例7相同,经检测,出口甲烷含量(不含水蒸汽)为1.30%。表10中给出的是本实施例的重整制氢反应器与现有技术中相同反应器尺寸及相同催化反应单元尺寸的制氢反应器对比情况。从反应器床层压降、ch4转化率、空速三个指标可以看出,本实施例的反应器都表现出了优异的性能,尤其是在降低反应器压降,提高反应器空速方面的优势尤为突出。表10本实施例的重整反应器与常规制氢反应器对比反应器类型压降,mpach4转化率/(%)空速,h-1常规反应器0.33953400本实施例的反应器0.06≥9663230实施例10如图19、图22所示,本实施例的重整制氢反应器和转化炉、制氢工艺条件等与实施例9参数相同。与实施例9不同之处在于,本实施例中微催化反应板波形方向为沿反应器轴向方向,且为波形板。同理将本实施例的重整制氢反应器和转化炉应用于天然气蒸汽重整制氢反应。制氢工艺条件与实施例7相同,经检测,出口甲烷含量(不含水蒸汽)为0.05%。表11中给出的是本实施例的重整制氢反应器与现有技术中相同反应器尺寸及相同催化反应单元尺寸的制氢反应器对比情况。从反应器床层压降、ch4转化率、空速三个指标可以看出,本实施例的反应器都表现出了优异的性能,尤其是在降低反应器压降,提高反应器空速方面的优势尤为突出。表11本实施例的重整反应器与常规制氢反应器对比反应器类型压降,mpach4转化率/(%)空速,h-1常规反应器0.33953400本实施例的反应器0.05≥9963230实施例11如图19、图23、图14所示,本实施例的重整制氢反应器和转化炉、制氢工艺条件、微催化反应板波形方向及结构参数等与实施例10参数相同。与实施例10不同之处在于,本实施例中微反应板为波纹板。同理将本实施例的重整制氢反应器和转化炉应用于天然气蒸汽重整制氢反应。制氢工艺条件与实施例10相同,经检测,出口甲烷含量(不含水蒸汽)为0.05%。表12中给出的是本实施例的重整制氢反应器与现有技术中相同反应器尺寸及相同催化反应单元尺寸的制氢反应器对比情况。从反应器床层压降、ch4转化率、空速三个指标可以看出,本实施例的反应器都表现出了优异的性能,尤其是在降低反应器压降,提高反应器空速方面的优势尤为突出。表12本实施例的重整反应器与常规制氢反应器对比反应器类型压降,mpach4转化率/(%)空速,h-1常规反应器0.33953400本实施例的反应器0.05≥99.363230实施例12如图19、图24、图13所示,本实施例的重整制氢反应器和转化炉、制氢工艺条件、微催化反应板波形方向及结构参数等与实施例10参数相同。与实施例10不同之处在于,本实施例中微反应板为齿形板。同理将本实施例的重整制氢反应器和转化炉应用于天然气蒸汽重整制氢反应。制氢工艺条件与实施例10相同,经检测,出口甲烷含量(不含水蒸汽)为0.08%。表13中给出的是本实施例的重整制氢反应器与现有技术中相同反应器尺寸及相同催化反应单元尺寸的制氢反应器对比情况。从反应器床层压降、ch4转化率、空速三个指标可以看出,本实施例的反应器都表现出了优异的性能,尤其是在降低反应器压降,提高反应器空速方面的优势尤为突出。表13本实施例的重整反应器与常规制氢反应器对比反应器类型压降,mpach4转化率/(%)空速,h-1常规反应器0.33953400本实施例的反应器0.055≥9963230实施例13如图19、图25所示,本实施例的重整制氢反应器、制氢工艺条件等与实施例7参数相同。与实施例7不同之处在于,本实施例中包含同轴设置的五个结构尺寸相同的微催化反应单元,催化反应单元高2000mm。除最上部、最下部催化反应单元外,相邻催化反应单元的顶部密封板5与底部密封板8密封固定,中心管6连接固定且连通。本实施例的重整制氢转化炉如图17所示,为侧烧炉,包括上述重整制氢反应器21、进气管24、出气管25、烧嘴23和燃烧室22,重整制氢反应器21位于燃烧室22内,重整制氢反应器21的进气口1与进气管24连通,重整制氢反应器的出气口2与出气管25连通。将本实施例重整制氢反应器和转化炉应用于天然气蒸汽重整制氢反应。制氢工艺条件与实施例7相同。经检测,出口甲烷含量(不含水蒸汽)为1.2%。表14中给出的是本实施例的重整制氢反应器与现有技术中相同反应器尺寸及相同催化反应单元尺寸的制氢反应器对比情况。从反应器床层压降、ch4转化率、空速三个指标可以看出,本实施例的反应器都表现出了优异的性能,尤其是在降低反应器压降,提高反应器空速方面的优势尤为突出。表14本实施例的重整反应器与常规制氢反应器对比反应器类型压降,mpach4转化率/(%)空速,h-1常规反应器0.33953400本实施例的反应器0.075≥97.563230实施例14如图18、图19所示,本实施例的重整制氢反应器和转化炉与实施例7参数相同。与实施例7不同之处在于,本实施例采用重整氢提浓psa解析气作为反应原料,解析气组见表15燃料在转化炉的燃烧室中燃烧提供制氢反应所需热量,反应器温度为930℃。水蒸汽与ch4摩尔比为2.8的混合气体(温度500℃,压力3mpag),流量为48.52kmol/h,空速68310h-1,充分混合后进入转化炉进气管,通过反应器第一直管11、中心管6进入微催化反应板上进行重整制氢反应,发生反应后的转化气通过环隙7、集气腔9、第二直管14离开反应器,进入转化炉出气管,将富含氢气的转化气排出至转化炉外部。经检测,出口甲烷含量(不含水蒸汽)为0.08%。采用实施例7中提供的反应器,反应原料、工艺条件与实施例不同,得到的反应结果与常规反应器在相同反应原料与工艺条件得到的反应结果对比情况见表16。从反应器床层压降、ch4转化率、空速三个指标可以看出,本实施例的反应器都表现出了优异的性能,尤其是在降低反应器压降,提高反应器空速方面的优势尤为突出。表15重整氢提浓psa解析气组成表16本实施例的重整反应器与常规制氢反应器对比反应器类型压降,mpach4转化率/(%)空速,h-1常规反应器0.38974400本实施例的反应器0.1≥9968310本公开提供的重整制氢反应器和转化炉结构紧凑、活性金属用量少;采用该反应器进行重整制氢反应时,床层压降小、单位体积催化剂生产强度大、反应物扩散路径较短、原料转化率高,无气体偏流和短路现象,能够满足现行水蒸汽重整制氢的生产过程。从实施例1-14的数据可以看出,从反应器床层压降、ch4转化率、空速三个指标可以看出,本公开的重整制氢反应器和转化炉表现出了优异的性能,尤其是在降低反应器压降,提高反应器空速方面的优势尤为突出。以上结合附图详细描述了本公开的优选实施方式,但是,本公开并不限于上述实施方式中的具体细节,在本公开的技术构思范围内,可以对本公开的技术方案进行多种简单变型,这些简单变型均属于本公开的保护范围。另外需要说明的是,在上述具体实施方式中所描述的各个具体技术特征,在不矛盾的情况下,可以通过任何合适的方式进行组合。为了避免不必要的重复,本公开对各种可能的组合方式不再另行说明。此外,本公开的各种不同的实施方式之间也可以进行任意组合,只要其不违背本公开的思想,其同样应当视为本公开所公开的内容。当前第1页12