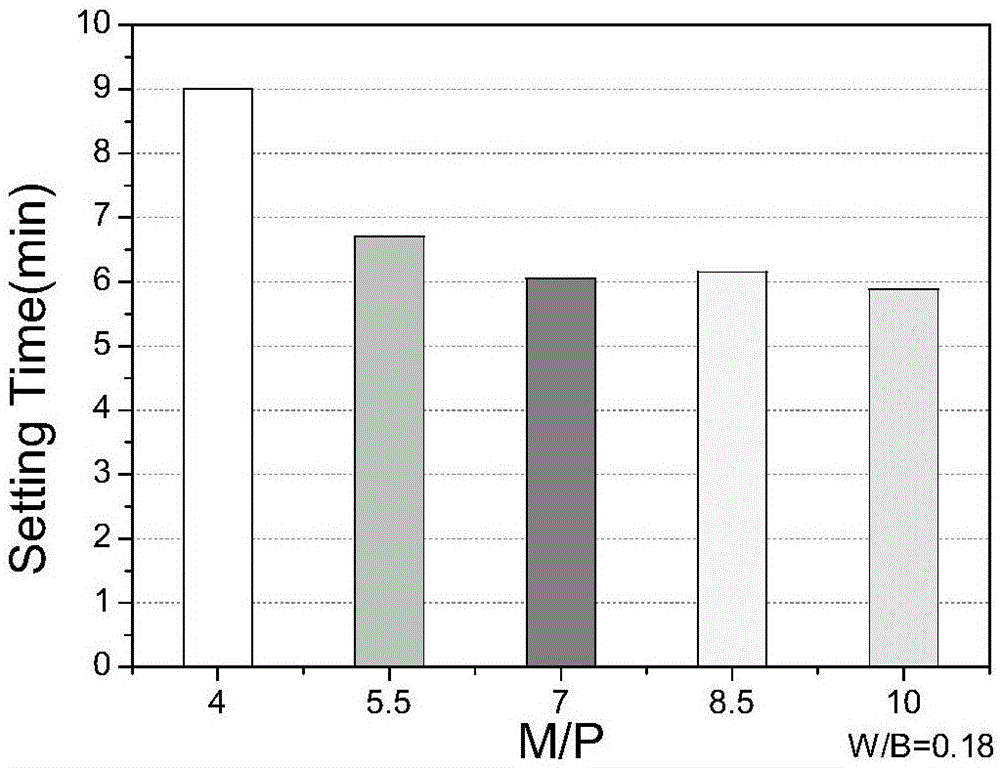
本发明属于混凝土
技术领域:
,涉及一种磷酸镁水泥。
背景技术:
:在混凝土作为建筑材料的160多年的历史中,混凝土与其他材料相比较有很多优点,钢筋混凝土结构在世界上仍然是使用最多的建筑材料。但是由于碳化,钢筋锈蚀等问题,混凝土结构耐久性降低。在公路工程中,交通量不断增加,机车载重增加,对公路造成严重的破坏。自然灾害频发,对于修补材料的研究越来越被重视。磷酸镁水泥在修补工程中有着独特的优势,被国内外诸多学者所关注。磷酸镁水泥是一种在常温下加水,氧化镁与可溶性磷酸盐之间发生酸-碱中和反应,形成具有一定粘结强度的新型气硬性无机胶凝材料。磷酸镁水泥与工程中常用的普通硅酸盐水泥等相比较,具有以下优点:凝结时间短;早期强度发展较快,而且强度较高;耐磨性好,收缩率低;新旧混凝土粘结强度高;低温硬化性能好;耐火耐高温性能好。磷酸镁水泥的影响因素主要有:原料、镁磷比(m/p)、水胶比(w/b)、缓凝剂和掺合料种类及其掺量等。目前困扰磷酸镁水泥应用的最主要原因是最优的配比无法确定,虽然国内外学者做了大量的试验研究,但是对于其最佳的原料搭配仍然没有一个定论,无法切实科学的指导工程应用。技术实现要素:基于现有磷酸镁水泥所存在的技术问题,本发明提出一种最优配比的磷酸镁水泥,使其适合于修补施工作业。为解决上述技术问题,本申请提供一种磷酸镁水泥,其包括:氧化镁、磷酸二氢钾、砂、硼砂、粉煤灰和水。其中,水泥的镁磷摩尔比为优选为7.0-8.5,进一步优选为7.0。其中,水胶比优选为0.18-0.21,进一步优选为0.21。其中,硼砂掺量为氧化镁质量的5%-10%。其中,粉煤灰替代磷酸镁水泥的质量百分比为15%,替代磷酸镁水泥的质量意思为,粉煤灰替代的是保持镁磷比的氧化镁和磷酸二氢钾的两种物质的质量和。本发明还提供上述磷酸镁水泥的制备方法,其包括:第一步,根据计算配比称量原料,将氧化镁、磷酸二氢钾、硼砂和砂加入砂浆搅拌锅,低速搅拌30s使干料混合均匀,然后加水低速搅拌30s使原料与水初步掺合,最后高速搅拌90s使磷酸镁水泥砂浆充分混合均匀;第二步,将充分搅拌后的磷酸镁水泥砂浆迅速浇筑到试模中,同时安放到振动台上,使磷酸镁水泥砂浆充分振捣密实,然后置于空气中自然养护,养护3h拆模;第三步,拆模后,将试块在空气中自然养护。有益的技术效果本发明提出一种最优配比的磷酸镁水泥,使其适合于修补施工作业。附图说明图1水胶比为0.18时,镁磷比对凝结时间的影响;图2水胶比为0.21时,镁磷比对凝结时间的影响;图3水胶比为0.18时,镁磷比对流动性的影响;图4水胶比为0.21时,镁磷比对流动性的影响;图5水胶比为0.18时,镁磷比对抗压强度的影响;图6水胶比为0.21时,镁磷比对抗压强度的影响;图7水胶比为0.21时,抗压强度随镁磷比的变化;图8镁磷比为7.0时,水胶比对凝结时间的影响;图9镁磷比为8.5时,水胶比对凝结时间的影响;图10镁磷比为7.0时,水胶比对流动性的影响;图11镁磷比为8.5时,水胶比对流动性的影响;图12镁磷比为5.5时,水胶比对抗压强度的影响;图13镁磷比为7.0时,水胶比对抗压强度的影响;图14镁磷比为8.5时,水胶比对凝结时间的影响;图15镁磷比和水胶比对抗折强度的影响;图16水胶比为0.18时,粉煤灰的引入对磷酸镁水泥凝结时间和流动性的影响;图17水胶比为0.21时,粉煤灰的引入对磷酸镁水泥凝结时间和流动性的影响;图18水胶比为0.18时,粉煤灰掺量对磷酸镁水泥抗压强度的影响;图19水胶比为0.21时,粉煤灰掺量对磷酸镁水泥抗压强度的影响;图20粉煤灰掺量对磷酸镁水泥抗折强度的影响;图21水胶比为0.18时,粉煤灰掺量对磷酸镁水泥28d抗压强度及其浸水7d后抗压强度的影响;图22水胶比为0.18时,粉煤灰掺加后流动性对软化系数的影响;图23水胶比为0.21时,粉煤灰掺量对磷酸镁水泥28d抗压强度及其浸水7d后抗压强度的影响;图24水胶比为0.21时,粉煤灰掺加后流动性对软化系数的影响;图25水胶比为0.24,镁磷比对软化系数的影响;图26粉煤灰掺加量对软化系数的影响。具体实施方式本申请提供一种磷酸镁水泥,其包括:氧化镁、磷酸二氢钾、砂、硼砂、粉煤灰和水。其中,水泥的镁磷摩尔比为优选为7.0-8.5,进一步优选为7.0。其中,水胶比优选为0.18-0.21,进一步优选为0.21。其中,硼砂掺量为氧化镁质量的5%-10%。其中,粉煤灰替代磷酸镁水泥的质量百分比为15%,替代磷酸镁水泥的质量意思为,粉煤灰替代的是保持镁磷比的氧化镁和磷酸二氢钾的两种物质的质量和。氧化镁和磷酸盐的理论摩尔比例为1∶1,但是,由于反应条件的限制,氧化镁无法全部参与反应,不能被全部消耗,剩余的未水化的氧化镁颗粒作为了磷酸镁水泥的基本骨架,因此对于该反应一定存在一个最佳的比例,使得磷酸镁水泥的性能最优。镁磷比是影响磷酸镁水泥性能的主要因素,由于氧化镁不会全部参与反应过程,大量剩余氧化镁颗粒作为骨架,以水化产物mgkpo4·6h2o作为粘结相,同时大量未水化的氧化镁颗粒可以提高基体的耐磨性能,镁磷比的确定对于磷酸镁水泥优化配合比设计至关重要,本发明经过测试,镁磷比在7.0时,磷酸镁水泥具有较高的强度、良好的工作性能以及优异的抗折性能。磷酸镁水泥对水较为敏感,因此水胶比对于其性能的影响较为显著,与镁磷比比相互作用,往往是影响磷酸镁水泥机械性能和工作性能的决定性因素。磷酸镁水泥工作性能受到水胶比影响较为明显,随着水胶比增加,凝结时间随之增加,流动性也随之增加,强度降低。水胶比还影响着磷酸镁水泥的收缩以及孔隙率和渗透率等性能,水胶比在0.21时,磷酸镁水泥具有较高的强度、良好的工作性能以及优异的抗折性能。由于磷酸镁水泥水化反应速度较快,除了通过调控原料活性、比表面积和配比之外,最有效的延长凝结时间的措施就是加入缓凝剂。目前最常用的缓凝剂有硼砂、硼酸、铵、三聚磷酸钠、碱金属盐,目前使用较多的是硼砂。通过验证,硼砂掺量宜在5%-10%范围内,硼砂可以抑制氧化镁颗粒的溶解,使得水化产物结晶形态不规则,从而影磷酸镁水泥早期抗压强度,当硼砂掺加过量时,磷酸镁水泥基体内会存在未水化的硼砂颗粒,但是由于硼砂颗粒表面光滑,降低了磷酸镁水泥基材之间的粘结效果,从而降低了材料整体的力学性能。硼砂对于磷酸镁水泥的收缩性能也有一定影响,随着硼砂掺量的增加,磷酸镁水泥砂浆的早期和后期收缩变形都有一定程度的增加,因此,硼砂掺量不宜过高。粉煤灰的掺加可以降低磷酸镁水泥的成本,另一方面可以改善磷酸镁水泥的外观颜色,使之更适用于修补工程,还可以提高磷酸镁水泥强度,填充内部孔隙使磷酸镁水泥更加致密,提高磷酸镁水泥的耐水性能。本发明还提供上述磷酸镁水泥的制备方法,其包括:第一步,根据计算配比称量原料,将氧化镁、磷酸二氢钾、硼砂和砂加入砂浆搅拌锅,低速搅拌30s使干料混合均匀,然后加水低速搅拌30s使原料与水初步掺合,最后高速搅拌90s使磷酸镁水泥砂浆充分混合均匀;第二步,将充分搅拌后的磷酸镁水泥砂浆迅速浇筑到试模中,同时安放到振动台上,使磷酸镁水泥砂浆充分振捣密实,然后置于空气中自然养护,养护3h拆模;第三步,拆模后,将试块在空气中自然养护。以下采用实施例和附图来详细说明本发明的实施方式,借此对本发明如何应用技术手段来解决技术问题,并达成技术效果的实现过程能充分理解并据以实施。实验1、实验原料氧化镁是参与反应的主要原料之一,试验中采用重烧氧化镁(简写为m,相对原子质量40.3),是由山东济南鲁东耐火有限公司提供,将菱镁矿(mgco3)经过1700℃煅烧,破碎,球磨而成,其颜色为浅棕色,其化学组成见表1,主要粒径范围为60~85μm。表1氧化镁主要化学组成组成mgosio2caofe2o3al2o3其他含量96.80.71.190.40.30.61磷酸二氢钾(简写为p,相对原子质量136.09)也是参与mpc水化反应的主要原料之一,本试验中所用磷酸二氢钾为分析纯,含量大于99.5%,由上海埃彼化学试剂有限公司生产,ph值为4.2~4.5。硼砂(na2b4o7·10h2o,borax,简写为b,相对原子质量381.37)作为磷酸镁水泥反应体系中常用的缓凝剂,其为上海埃彼化学试剂有限公司生产,分析纯,含量99.5%。本试验中国实用的微中国iso标准砂(简写为s),由厦门艾思欧标准砂有限公司生产,每袋的重量约为1350g,级配良好的砂粒,符合gb/t14684-2001标准。粉煤灰(flyash,简写为fa)为一级粉煤灰,其主要化学成分如表2。表2粉煤灰主要化学组成化学组分caosio2mgoal2o3so3fe2o3k2o其他含量8.07521.1828.681.144.51.542.89水采用自来水。试验所用设备水泥胶砂搅拌机、维卡仪、水泥胶砂流动度测试仪、全自动压力试验机、300kn液压万能压力试验机和水泥胶砂振动台等。实验方法(1)确定配比,根据配比以及原材料纯度计算各种材料质量。配比主要根据国内外研究现状中诸多学者研究的材料配比范围确定。(2)根据计算配比称量原料,将氧化镁、磷酸二氢钾、硼砂和标准砂等加入砂浆搅拌锅,首先低速搅拌30s使干料混合均匀,然后加水低速搅拌30s使原料与水初步掺合,最后高速搅拌90s使mpc砂浆充分混合均匀。(3)将充分搅拌后的mpc砂浆迅速浇筑到试模中,同时安放到振动台上,使mpc砂浆充分振捣密实,然后置于空气中自然养护,养护3h拆模。(4)拆模后,将试块在空气中自然养护,养护至规定龄期,然后测定其性能,主要测试龄期为3h、1d、7d、28d。实验中抗压强度测试所用试模为70.7mm×70.7mm×70.7mm,抗折强度测试所用试模为40mm×40mm×160mm。凝结时间测试凝结时间测试主要按照国家标准gb/t1346-2001《水泥标准稠度用水量、凝结时间、安定性检测方法》中规定的标准流程进行测试,使用维卡仪,从拌合物加水开始计算凝结时间,由于mpc初凝时间和终凝时间相差较短,故以终凝时间作为mpc砂浆的凝结时间。同时由于该材料凝结较快,故凝结时间测试间隔要短,初期每隔30s测试一次,初凝后每隔10s测试一次,接近终凝减小测试间隔。流动度测试磷酸镁水泥砂浆流动度按照国家标准gb/t2419-2005《水泥胶砂流动度测定方法》进行测试,即跳桌法。抗压抗折力学性能测试测试砂浆试件预定龄期(3h、1d、7d、28d)的抗折强度,按照gb17671-1999《水泥胶砂强度检验方法》进行检验测试,抗压强度利用70.7mm×70.7mm×70.7mm试块在万能压力试验机上测试,按照《建筑砂浆基本性能试验方法》(jgj/t70-2009)规定方法进行测试,每组取三个试块,当三个试块的测试值中的一个最大或者最小值与中间值得差值超过中间值15%的时候,去中间值为有效抗压强度,如果最大最小值都超过中间值得15%,则认为本组试块数据无效。耐水性评价对于mpc耐水性评价常用的方法为软化系数,由于mpc在浸水状态下,其强度容易发生倒缩现象,原因主要是未参与水化的磷酸二氢钾会发生部分溶解,所以定义了软化系数来评价mpc的耐水性,用r表示,其计算方式为:f-浸水后无侧限抗压强度,mpa;f-自然养护状态下无侧限抗压强度,mpa;r-软化系数。镁磷比(m/p)对凝结时间的影响,结果见图1和图2。磷酸盐易溶于水,其水化速率主要取决于mgo的溶解速率,mgo的溶解速度越快,其反应速率越快,凝结时间越短,因此氧化镁的细度,活性等都影响着反应速率即也影响着凝结时间。在氧化镁细度以及活性(煅烧温度对其活性影响较大)一定的情况下,氧化镁的溶解量就影响着早期反应速率,因此,不同的镁磷比可能会导致凝结时间改变。实验中分别限定水胶比为0.18和0.21时,镁磷比对凝结时间的影响。从图1和图2可以看出,随着镁磷比的减小,凝结时间呈下降趋势,在镁磷比比4~5.5范围内凝结时间随镁磷比变化较为明显,镁磷比>5.5后变化较为平缓。水胶比为0.21,凝结时间从17分钟缩短到13分钟,主要原因为,镁磷比较小的时候,氧化镁含量相对较少,其溶解量少成为控制整个反应进行的主要因素。同时,水化产物生成量少,形成具有一定强度的粘结整体所需时间长。另一方面氧化镁含量少,硼砂溶解于水中形成的b4o72-,与氧化镁溶解形成的mg2+络合物mgb4o7对氧化镁颗粒的吸附包裹效果较好,起到了保护膜作用,对阻碍mg2+和磷酸盐互相接触的效果较好,缓凝效果明显。从反应温度方面考虑,是由于前期水化产物生成量相对较少,水化过程中产生的热量相对较少,对反应的促进效果相对于其他组较弱。在以上种种因素影响下,镁磷比小时,凝结时间延长。随着镁磷比值的变大,氧化镁溶解增加,缓凝剂硼砂形成保护膜的有效数量减少,反应放热增多,体系温度升高,水化速率升高,水化产物生成量逐渐增多,其互相连接形成空间硬化体系的速度加快,因此凝结时间逐渐缩短。镁磷比对流动性的影响,结果见图3和图4。反应过程中凝结时间会随着m/p值的变化而变化,主要是反应速率对水化过程影响较大,水化速率高,相应的水化产物生成量就会增多,mpc浆体水化硬化过程就会相应缩短,从而表现出流动性降低。同时氧化镁比表面积也会影响mpc水化过程,比表面积增加,包裹氧化镁的用水量就会增加。在比表面积一定的情况下,氧化镁掺量增加,同样会使得用水量增加,所以,m/p不同,mpc流动性也会受到相应的影响。由于mpc水化硬化反应过程较快,凝结时间较短,因此其流动性测试要在搅拌完成后在尽量短的时间内完成测试,以免流动性过多损失。实验中分别限定水胶比为0.18和0.21时,镁磷比对流动性的影响。从图3和图4可以看出,在水胶比为0.18时,mpc砂浆流动性随着m/p的增加而减小,但是当水胶比增大至0.21时其流动性变化分成了两个阶段,随着m/p增加,其流动性先增加后减小。当m/p从8.5增加到10的时候流动性急剧减小,从220mm下降到140mm左右。在流动性变化的前段,m/p增加流动性增大,主要由于当m/p较小时,mgo相对于磷酸盐溶解量较少,其溶解速度限制了反应的进行,因此水化产物生成量稍少,自由水含量高,对mpc砂浆流动性具有较大贡献。随着m/p增加,mgo掺量增加,溶解增量增加,与磷酸盐反应的mg2+增多,水化产物生成量增加,故其流动性程下降趋势。另一方面,m/p值增加,大量的自由水用来包裹mgo颗粒表面,为mpc砂浆提供流动性,但是在用水量一定的情况下,当自由水参与水化反应过程比率增加,自由水不足以润湿mgo颗粒,流动性明显降低。镁磷比对抗压强度的影响,见图5和图6。因为重烧氧化镁溶解速度较低,并不是所有的氧化镁都会参与反应,未水化的氧化镁颗粒充当骨架,水化产物mgkpo4·6h2o会作为粘结相,形成具有一定强度的硬化体,其强度与水化产物形成的粘结相的空间结构密切相关。不同的m/p值影响着水化产物的生成量,无论是哪一种组分过量都会明显影响mpc砂浆的整体强度。实验中分别限定水胶比为0.18和0.21时,镁磷比对抗压强度的影响。随着龄期的增长,各配比试样强度都有明显的增长,尤其是前期强度,3h强度基本都达到了30mpa以上,能达到28d强度的50%,1d强度能达到28d强度的70%。研究显示,虽然mpc砂浆性能会随着m/p变化而变化,水化产物的生成量发生变化,但是其类别不会发生改变。m/p值偏大或偏小都会影响水化产物的生成量,进而影响水化产物形成空间网络的完整性,导致整体强度性能下降。从图5和6可以得出,m/p值为8.5和7时,其强度性能达到最优。图7为不同龄期强度随m/p值的变化关系,以w/b为0.21为例,随着m/p的增加,mpc砂浆强度呈先增加后减小变化,其主要原因为,当m/p值较小的时候,磷酸盐相对过量,氧化镁溶解量有限,制约了水化产物的生成量,从而影响了mgkpo4·6h2o形成空间网络的完整性,进而导致该m/p值下,强度稍小。当m/p值较大的时候,mgo相对过量,磷酸盐的含量制约了水化产物的生成量,因此,强度也表现的较低。故而在较大和较小的m/p值之间存在最优的氧化镁和磷酸盐配比。水胶比(w/b)对凝结时间的影响,结果见图8和图9。水既作为反应原料之一,又作为溶剂存在,其对于mpc体系的至关重要。工程要求修补材料能满足施工时间,在能满足强度要求的前提下,可以通过w/b调节mpc凝结时间。图8和图9为凝结时间和水胶比之间的变化关系。实验中分别限定镁磷比为7.0和8.5时,水胶比对流动性的影响。通过图8和图9可以明显看出,随水胶比增加,mpc砂浆凝结时间逐渐延长。主要是由于w/b增加,mpc砂浆体系中自由水增多,增加了mgo颗粒表面的润湿程度,大量的自由水使得mgkpo4·6h2o不易互相搭接形成具有一定强度的空间网状结构。水的比热容较大,水含量的增加,吸收了大量的反应热,降低了体系温度,降低了反应速率,进而也起到了延长凝结时间的作用。w/b对流动性的影响,结果见图10和图11。水胶比的改变不仅影响着凝结时间的变化,同时还导致流动性明显的改变,流动性也是施工所考虑的重要条件之一。流动性影响着结构的密实性,流动性太低,会导致不易振捣密实,从而影响基体的强度性能。实验中分别限定镁磷比为7.0和8.5时,水胶比对流动性的影响。如图10和图11所示,随水胶比增加,流动性明显改善,与凝结时间表现出相似的规律。流动性改善的具体原因是,w/b增大,体系内自由水含量增加,mgo颗粒表面被充分润湿,削弱了颗粒之间的相互作用。从图中也可以看出,w/b对mpc基体的流动性影响较大,w/b增长0.3,流动性增长了100mm左右。w/b对mpc强度的影响,结果见图12和图13。水胶比增大,体系内自由水含量增加,体系内自由水的含量会影响mpc砂浆基体的孔结构分布,w/b越高孔隙结构越粗糙,孔隙连通性更大,从而对于mpc砂浆的强度影响就越大。实验中分别限定镁磷比为7.0和5.5时,水胶比对抗压强度的影响。从图12和图13中可以发现,m/p小于7,w/b值过大或过小都使得mpc砂浆强度降低,其主要原因是,m/p一定,水胶比较大时,体系内自由水含量增多,大量的自由水在体系内部无法排除,导致其内部有害孔数量增多,从而影响其强度特性,使其强度降低。而w/b值较小时,大部分水都参与水化过程,体系中自由水不能将mgo颗粒完全包裹,同时水化过程较快,导致流动性较低,因此,mpc砂浆不易振捣密实,内部孔隙率升高,导致强度降低。如图14所示,m/p值大于7,随水胶比增加,mpc砂浆强度呈下降趋势。从前所述随m/p值增大,mpc砂浆流动性降低,凝结时间缩短,同时氧化镁相对过量,水化反应用水量减少,过量的自由水被滞留在体系中无法排出,导致体系孔隙率升高,强度降低,故w/b增大,强度呈下降趋势。m/p和w/b对抗折强度的影响,结果见图15。在普通硅酸盐混凝土中,其基体抗折强度与其抗压强度成正比,mpc水泥砂浆也表现出同样的规律,通过图15可以看出,随着m/p的增加,抗折强度先升高后降低,在m/p值为7时,抗折强度最高达到了8.5mpa。在保持m/p不变,发现,随w/b值增加,其抗折强度亦是先增大后减小,且在w/b为0.21时表现出较为优异的抗折性能。从上面的实验可以看出,在w/b一定时,随着m/p值的增加,mpc砂浆凝结时间随之缩短,但mpc砂浆的流动并不是m/p值的单调函数,在w/b较小时,其流动性呈下降趋势,但是当w/b在0.21附近时,其流动性变化趋势为先增加后减少。抗压强度在m/p值7.0~8.5时达到最高,但是同时考虑凝结时间和流动性等因素,m/p值为7.0时的性能表现能够满足通常抢修抢建工程对材料的需求,具有较高的强度和良好的工作性能。mpc砂浆性能对w/b的变化较为敏感,其凝结时间随w/b值的增加而延长,流动性随之增加。w/b在影响mpc砂浆流动性的同时会影响其基体的浇筑质量,其值较小时,试样不易浇筑密实,进而影响其整体强度,因此w/b不宜过小。w/b值过大,mpc砂浆凝结时间较短,大量的自由水不易被排出,体系孔隙率升高,亦会导致mpc砂浆强度降低,故在考虑诸多因素影响下,w/b宜在0.21附近,表现出较好的工作性能和强度特性。抗折强度与抗压强度表现出一致的变化规律,在w/b值为0.21,m/p值为7.0时表现出较为优异的抗折性能。成本问题是影响磷酸镁水泥推广的一项重要因素,在普通混凝土中掺加粉煤灰会改善其基础性能,故将粉煤灰引入磷酸镁水泥的改性研究中。粉煤灰的引入对凝结时间和流动性的影响,结果见图16和图17。实验中磷酸镁水泥的水胶比分别为0.18和0.21。从图16和图17中可以明显看出,粉煤灰对mpc砂浆工作性能具有明显的改善作用,粉煤灰掺量增加,磷酸镁水泥的凝结时间延长,流动性提高,但是在粉煤灰掺量较小(小于10%)时,对于凝结时间的延长效果很微弱。凝结时间延长的原因是,粉煤灰替代mpc后其反应原料减少,水化产物生成量减少,使mgo颗粒和粉煤灰颗粒之间的由水化产物相互搭接形成空间网状结构的机会减少,另一方面,由于粉煤灰通常被视为惰性填料,基本上不参与水化反应,反应物减少,水化过程产生的热量降低,mpc砂浆体系温度降低,此外粉煤灰还可以吸附po43-离子,减少mgkpo4·6h2o的形成,从而延长凝结时间。对于流动性的改善较为明显,粉煤灰掺量从0%~30%增加,mpc砂浆流动度增加了50mm左右,因此,粉煤灰的掺加可以明显改善mpc砂浆的流动性。其对流动性改善的主要原因是,粉煤灰的微集料效应,粉煤灰微观结构大多为球形颗粒,在体系中充当滚轴作用,减小了颗粒之间的阻力,从而提高了mpc基体的流动性。流动性提高,另一方面也由于水化产物生成量减少的原因。掺杂粉煤灰对mpc抗压强度的影响,结果见图18和图19。掺加粉煤灰可以改善mpc强度性能,通过预实验也发现其掺量在15%左右对mpc强度有改善效果,同时对流动性,凝结时间等都有提高,然而砂浆流动性及其凝结时间影响着基体的浇筑质量,从而也影响着强度性能,故在试验中研究了不同水胶比和不同粉煤灰掺量对于mpc砂浆强度的影响。实验中,磷酸镁水泥的水胶比分别为0.18和0.21。如图18和图19所示,随着粉煤灰掺量的增加,在水胶比较小时,掺加粉煤灰后,其强度有所改善,在粉煤灰掺量为15%龄期为28d时,表现出优异的强度性能,相较于未掺加粉煤灰试样,强度提高。然而当水胶比增大后,随粉煤灰掺量的增加,mpc砂浆强度呈下降趋势。可见粉煤灰对于mpc基体不同的水胶比状态下具有不同效果,在未掺加粉煤灰状态下,w/b值较小时,mpc砂浆流动性相对稍低,凝结时间较短,在成型过程中内部气泡不易排出,滞留在体系内使构件不易浇筑密实,影响了mpc砂浆的强度性能。粉煤灰掺加后,其流动性有所改善,凝结时间延长,使得mpc更易浇筑密实,此外,粉煤灰的微集料效应作用下,其填充了mpc反应过程中产生的孔隙,增加了基体的密实性,从而使得强度得以提高。但是随水胶比增大,mpc本身流动性提升,凝结时间能保证其浇筑质量,此时,粉煤灰掺加后,其作为惰性填料,本身基本不与mpc发生反应,同时在反应过程中还会吸附缓凝剂、po43-离子,降低体系的ph值,其本身含有的杂质等都会影响mgkpo4·6h2o空间网状结构的完整性,进而影响mpc基体的整体强度。粉煤灰掺加后,抗折强度有明显的提高,相较于未掺加粉煤灰的对照组,当粉煤灰掺加量为10%左右时,抗折强度最高达到7.3mpa,如图20所示。粉煤灰的加入对mpc耐水性的影响。mpc体系长期遇水强度发生倒缩现象,软化系数是评价其倒缩性能重要指标。矿物掺合料粉煤灰,改善了磷酸镁水泥的强度性能、工作性能和粘结性能等,同时其对于磷酸镁水泥的耐水性能也有影响,在未掺加粉煤灰时,其在空气中养护28d,后浸水7d后强度(用r表示)变化如图21和图23所示(水胶比为0.18)。由公式计算其软化系数,通过两图可明显看出,浸水后mpc砂浆强度明显下降,浸水后强度变化趋势基本与28d强度变化一致,当w/b较小时,其耐水性主要由流动性控制,如图22和图24,流动性小时其软化系数相对较小,随流动性增加,耐水性提高。主要原因是,流动性增加,其结构愈密实,kh2po4只是在表面附近被溶解,内部短期不易被水分子侵蚀。浸水7d后其强度总体降低大约在10%左右,在水胶比较大时,其软化系数随m/p值的增大,其呈升高趋势,如图25。主要原因为,kh2po4易溶于水,进而会导致mpc砂浆体系中孔隙率升高,内部更易受到侵蚀,但是,随m/p值的增加,虽然流动降低,但mpc基体中未水化的kh2po4含量逐渐减少,降低了浸水后mpc由于kh2po4溶解而导致的孔隙率升高的发生概率,故其软化系数随m/p值增加而增加。掺加粉煤灰后,见图26,在w/b为0.18情况下,mpc砂浆流动性得到改善,同时由于粉煤灰的微集料效应,填充了mpc中的大量孔隙,使mpc基体密实度增加,故其耐水性能相较于未掺加粉煤灰mpc砂浆有所提高。m/p为7.0,w/b为0.18时,mpc砂浆软化系数只有0.9,而在粉煤灰掺加量为15%时最高达到了0.95。从上面的分析可以看出,掺加粉煤炭后,由于粉煤灰的微集料效应,mpc砂浆流动性有了明显的改善,随着粉煤灰掺量的增加,不同w/b状态下其流动性和凝结时间都呈增长趋势,但是当粉煤灰掺量较少(少于10%)时,凝结时间延长较少。在w/b值较小时,掺加粉煤灰后mpc砂浆强度相较于为掺加组强度有所提高,主要由于流动性的改善,提高了浇筑质量,以及粉煤灰的微集料效应,填充了内部孔隙,使内部结构更加致密,强度提高。随着w/b增加,掺加粉煤灰后,mpc砂浆强度呈下降趋势,主要由于粉煤灰被视为惰性填料,不与mpc砂浆基体发生反应,粉煤灰自身杂质影响了mpc基体的完整性,强度降低。耐水性与流动性有较为密切的联系,流动性较好时,其内部结构越密实,短期内未参与水化的kh2po4不易溶解到水中,减小了内部孔隙率的升高,表现出较好的耐水性。w/b为0.18,粉煤灰掺量为15%时,其软化系数达到了0.95。所有上述的首要实施这一知识产权,并没有设定限制其他形式的实施这种新产品和/或新方法。本领域技术人员将利用这一重要信息,上述内容修改,以实现类似的执行情况。但是,所有修改或改造基于本发明新产品属于保留的权利。以上所述,仅是本发明的较佳实施例而已,并非是对本发明作其它形式的限制,任何熟悉本专业的技术人员可能利用上述揭示的技术内容加以变更或改型为等同变化的等效实施例。但是凡是未脱离本发明技术方案内容,依据本发明的技术实质对以上实施例所作的任何简单修改、等同变化与改型,仍属于本发明技术方案的保护范围。当前第1页12