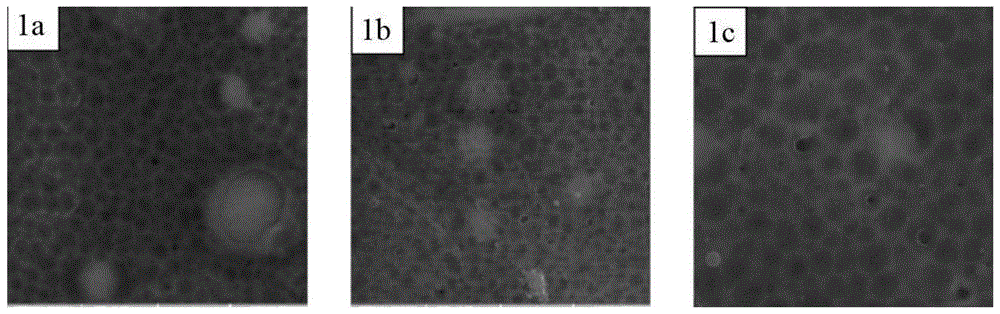
本发明属于复合膜材料
技术领域:
,具体涉及一种光催化膜水解产氢气的方法。
背景技术:
:氢能是一种无污染、热值高且储存和运输方便的可再生能源,是目前为止发现的最具应用前景的清洁能源之一,既能减少污染同时又可降低设备和运输方面的投资,利用太阳能作为驱动力光催化水分解制取氢气已经被广泛研究。g-c3n4具有合适的能带结构,有良好的可见光捕获能力以及物理化学稳定性,并且在层之间存在弱的范德华力。g-c3n4是推动光催化反应的重要因素且理论上与传统的光催化技术如tio2和zno相比,g-c3n4可以在可见光下将更多的光能转化为化学能。但是量子效率仍然有待提高,使其光催化制氢能力受到了一定程度的限制。铋系材料是一种性价比很高的材料,不仅拥有很高的表面能,且活性位点多。在整个铋系材料中被科学家们运用地最广泛的催化剂就是bi2moo6。bi2moo6已被用于与其他半导体构建异质结构,从而使电子-空穴对可以更快速的进行分离,并大幅度的提升其光催化性能。于是bi2moo6与g-c3n4相互结合作为光催化制氢的催化剂,并应用于制备氢能的领域中,但是目前基于光生电子与空穴的高复合率,会影响光催化剂的光催化性,催化活性没有达到人们最初预计的效果,从而使得单一催化剂产氢效率不高。技术实现要素:解决的技术问题:在催化产氢的过程中,如何获得一种光催化剂催化活性高、产氢速率高的方法。技术方案:为了解决上述问题,本发明所采用的技术方案如下:一种光催化膜水解产氢气的方法,在光照射条件下,利用bi2moo6/g-c3n4复合催化薄膜催化分解水产生氢气;所述bi2moo6/g-c3n4复合催化薄膜为将复合催化剂bi2moo6/g-c3n4投加到复合薄膜ppsu/pei(聚亚苯基砜树脂/聚醚酰亚胺)中获得。所述的光催化膜水解产氢气的方法,通过原位溶剂热法合成复合催化剂bi2moo6/g-c3n4,与复合薄膜ppsu/pei混合制备得到bi2moo6/g-c3n4复合催化薄膜;复合催化剂bi2moo6/g-c3n4为ppsu/pei复合薄膜质量的0.4%-3.2%。所述的光催化膜水解产氢气的方法,bi2moo6/g-c3n4复合催化薄膜由以下方法制备得到:(1)将ppsu、pei、nmp(n-甲基吡咯烷酮)和peg-200(聚乙二醇-200)加入到反应容器中,控温搅拌至反应物溶解,得到铸膜液;反应温度为60-70℃,转速为300-400rmp;ppsu、pei、nmp和peg-200的体积比为2∶1∶5-6∶1-2;(2)向步骤(1)铸膜液中加入复合催化剂bi2moo6/g-c3n4,继续搅拌溶解,至复合催化剂在铸膜液中分散均匀后停止加热;(3)将铸膜液在玻璃板上成膜,并置于恒温箱中,使溶剂挥发;然后用蒸馏水冲洗玻璃板直到薄膜完整脱落,将薄膜置于去离子水中浸泡6-10h,制得bi2moo6/g-c3n4复合催化薄膜。所述的光催化膜水解产氢气的方法,复合催化剂bi2moo6/g-c3n4的投加量为复合薄膜ppsu/pei质量的1.6%。所述的光催化膜水解产氢气的方法,复合催化剂bi2moo6/g-c3n4由以下方法获得:(1)将g-c3n4纳米片均匀分散在乙醇中,通过超声处理辅助1-2h,得到g-c3n4纳米片分散体;(2)将bi(no3)3·5h2o和na2moo4·2h2o溶解在乙二醇中,bi与mo的摩尔比为2∶1;(3)将g-c3n4纳米片分散体滴加到步骤(2)溶液中,在室温下剧烈搅拌3-4h后,将混合物转移到高压釜中并在150-160℃下保持5-6h;(4)通过离心收集沉淀物,洗涤,并在60-70℃下干燥20-24h,得到复合催化剂bi2moo6/g-c3n4。所述的光催化膜水解产氢气的方法,bi2moo6的掺杂量为复合催化剂质量的30wt.%。所述的光催化膜水解产氢气的方法,复合催化剂bi2moo6/g-c3n4中bi2moo6的掺杂量为复合催化剂质量的10wt.%-40wt.%。所述的光催化膜水解产氢气的方法,复合催化剂bi2moo6/g-c3n4中g-c3n4的制备:将尿素置于马弗炉中进行煅烧,在500-600℃的空气氛围下煅烧3h,得到g-c3n4;所述g-c3n4与浓硝酸混合搅拌,对悬浮液离心处理并洗涤至中性,干燥;加入乙醇进行分散处理,加热得到已剥离的g-c3n4纳米片。所述的光催化膜水解产氢气的方法,复合催化剂bi2moo6/g-c3n4中g-c3n4的制备过程中尿素的煅烧温度为550℃。所述的光催化膜水解产氢气的方法,所述bi2moo6/g-c3n4复合催化薄膜中g-c3n4的制备过程中尿素的煅烧温度为550℃,bi2moo6的掺杂量为复合催化剂质量的30wt.%,复合催化剂bi2moo6/g-c3n4的投加量为复合薄膜ppsu/pei质量的1.6%。有益效果:与现有的技术相比,本发明的优点包括:(1)本发明通过将复合催化剂bi2moo6/g-c3n4投加于复合薄膜ppsu/pei中,在紫外光照射下分解水产氢气,表现出了更优异的光催化性能,大大提高了光降解效率。(2)钼酸铋附着在g-c3n4纳米片上,提高了其表面能与热稳定性降低了光生电子-空穴的复合速度,从而提高了光催化性能,将其投加共混体系中,通过相转换法并在平板玻璃上成膜,复合催化剂较均匀的分散其中,水蒸汽分布在薄膜上,通过紫外光照射,光催化剂分解水产生氢气。(3)本发明所使用的复合催化剂bi2moo6/g-c3n4具有廉价易得、无毒环保和化学性质稳定等优点。(4)本发明利用bi2moo6/g-c3n4复合催化薄膜,光解产生氢气效率较高,产氢速率接近1600μmol/(hr·m3·kpa)。附图说明图1为复合催化薄膜m1、m2和m3的sem扫描图,其中,图1a为膜m1的sem扫描图,图1b为膜m2的sem扫描图,图1c为膜m3的sem扫描图;图2为复合催化薄膜m2、m4、m5和m6的sem扫描图,其中,图2a为膜m4的sem扫描图,图2b为膜m5的sem扫描图,图2c为膜m2的sem扫描图,图2d为膜m6的sem扫描图;图3为复合催化薄膜m2、m7、m8和m9的sem扫描图,其中,图3a为膜m7的sem扫描图,图3b为膜m2的sem扫描图,图3c为膜m8的sem扫描图,图3d为膜m9的sem扫描图;图4为复合催化薄膜m1、m2和m3的紫外光谱图;图5为复合催化薄膜m2、m4、m5和m6的紫外光谱图;图6为复合催化薄膜m2、m7、m8和m9的紫外光谱图;图7为复合催化薄膜m1、m2和m3的红外光谱图;图8为复合催化薄膜m2、m4、m5和m6的红外光谱图;图9为复合催化薄膜m2、m7、m8和m9的红外光谱图;图10为利用复合催化薄膜进行产氢的装置结构示意图;图11为氢气浓度标准曲线图。具体实施方式为使本发明的上述目的、特征和优点能够更加明显易懂,下面结合具体实施例对本发明的具体实施方式做详细的说明。实施例1bi2moo6/g-c3n4复合催化薄膜的制备方法,包括以下步骤:g-c3n4的制备:将尿素置于80℃的烘箱中干燥8h,取5g干燥好的尿素置于马弗炉中进行煅烧,马弗炉的升温速率为5℃/min,在500℃的空气氛围下煅烧3h,待其冷却至室温后,取出坩埚收集黄色粉末为g-c3n4;将g-c3n4与浓硝酸混合搅拌,对悬浮液离心处理并洗涤至中性,60℃下干燥12h;将0.2g上述获得的粉末在室温下分散在100ml乙醇中并进行超声剥离8h;再以3000rpm离心20min的方式处理悬浮液,目的是为了去除残留在悬浮液中未剥离的g-c3n4;在磁力搅拌的作用下将已剥离的g-c3n4纳米片分散体在60℃下加热以除去乙醇,制备得到焙烧温度为500℃的g-c3n4纳米片。bi2moo6掺杂量为30wt.%的bi2moo6/g-c3n4复合催化剂的制备:(1)将0.1g焙烧温度为500℃的g-c3n4纳米片均匀分散在60ml乙醇中,通过超声辅助处理1h,得到g-c3n4纳米片分散体;(2)将0.0929g的bi(no3)3·5h2o和0.0504g的na2moo4·2h2o(bi与mo的摩尔比为2∶1)溶解在20ml乙二醇中;(3)将g-c3n4纳米片分散体滴加到步骤(2)溶液中,在室温下剧烈搅拌4h后,将混合物转移到100ml的高压釜中并在160℃下保持5h;(4)通过离心收集黄色沉淀物,洗涤数次并在60℃下干燥过夜得到bi2moo6/g-c3n4复合催化剂。bi2moo6/g-c3n4复合催化薄膜的制备:(1)将4mlppsu、2mlpei、11.2mlnmp和2.8mlpeg-200加入到小烧杯中,加入磁石,盖上锡箔纸后放入集热式恒温加热磁力搅拌器中,控制温度为70℃、转速控制在300rmp搅拌至反应物溶解,得到铸膜液;(2)向铸膜液中加入0.05gbi2moo6/g-c3n4复合催化剂,继续搅拌溶解,至复合催化剂在铸膜液中分散均匀后停止加热;(3)将铸膜液在玻璃板上成膜,并置于恒温箱中静置8h,使溶剂挥发;然后用蒸馏水冲洗玻璃板直到薄膜完整脱落,将薄膜置于去离子水中浸泡8h,制得bi2moo6/g-c3n4复合催化薄膜。制备得到的复合催化剂为500℃-30wt.%-bi2moo6/g-c3n4,表示的是g-c3n4的煅烧温度为500℃,bi2moo6的掺杂量为30wt.%;bi2moo6/g-c3n4复合催化薄膜(膜标号为m1)中该复合催化剂的投加量为0.05g。实施例2g-c3n4的制备方法同实施例1,其中,g-c3n4的煅烧温度为550℃;bi2moo6/g-c3n4复合催化剂的制备方法同实施例1,制备得到的复合催化剂为550℃-30wt.%-bi2moo6/g-c3n4;bi2moo6/g-c3n4复合催化薄膜(膜标号为m2)的制备方法同实施例1,其中,该复合催化剂的投加量为0.05g。实施例3g-c3n4的制备方法同实施例1,其中,g-c3n4的煅烧温度为600℃;bi2moo6/g-c3n4复合催化剂的制备方法同实施例1,制备得到的复合催化剂为600℃-30wt.%-bi2moo6/g-c3n4;bi2moo6/g-c3n4复合催化薄膜(膜标号为m3)的制备方法同实施例1,其中,该复合催化剂的添加量为0.05g。实施例4g-c3n4的制备方法同实施例1,其中,g-c3n4的煅烧温度为550℃;bi2moo6/g-c3n4复合催化剂的制备方法同实施例1,其中bi2moo6的掺杂量为10wt.%,制备得到的复合催化剂为550℃-10wt.%-bi2moo6/g-c3n4;bi2moo6/g-c3n4复合催化薄膜(膜标号为m4)的制备方法同实施例1,其中,该复合催化剂的添加量为0.05g。实施例5g-c3n4的制备方法同实施例1,其中,g-c3n4的煅烧温度为550℃;bi2moo6/g-c3n4复合催化剂的制备方法同实施例1,其中bi2moo6的掺杂量为20wt.%,制备得到的复合催化剂为550℃-20wt.%-bi2moo6/g-c3n4;bi2moo6/g-c3n4复合催化薄膜(膜标号为m5)的制备方法同实施例1,其中,该复合催化剂的添加量为0.05g。实施例6g-c3n4的制备方法同实施例1,其中,g-c3n4的煅烧温度为550℃;bi2moo6/g-c3n4复合催化剂的制备方法同实施例1,其中bi2moo6的掺杂量为40wt.%,制备得到的复合催化剂为550℃-40wt.%-bi2moo6/g-c3n4;bi2moo6/g-c3n4复合催化薄膜(膜标号为m6)的制备方法同实施例1,其中,该复合催化剂的添加量为0.05g。实施例7g-c3n4的制备方法同实施例1,其中,g-c3n4的煅烧温度为550℃;bi2moo6/g-c3n4复合催化剂的制备方法同实施例1,其中bi2moo6的掺杂量为30wt.%,制备得到的复合催化剂为550℃-30wt.%-bi2moo6/g-c3n4;bi2moo6/g-c3n4复合催化薄膜(膜标号为m7)的制备方法同实施例1,其中,该复合催化剂的添加量为0.025g。实施例8g-c3n4的制备方法同实施例1,其中,g-c3n4的煅烧温度为550℃;bi2moo6/g-c3n4复合催化剂的制备方法同实施例1,其中bi2moo6的掺杂量为30wt.%,制备得到的复合催化剂为550℃-30wt.%-bi2moo6/g-c3n4;bi2moo6/g-c3n4复合催化薄膜(膜标号为m8)的制备方法同实施例1,其中,该复合催化剂的添加量为0.1g。实施例9g-c3n4的制备方法同实施例1,其中,g-c3n4的煅烧温度为550℃;bi2moo6/g-c3n4复合催化剂的制备方法同实施例1,其中bi2moo6的掺杂量为30wt.%,制备得到的复合催化剂为550℃-30wt.%-bi2moo6/g-c3n4;bi2moo6/g-c3n4复合催化薄膜(膜标号为m8)的制备方法同实施例1,其中,该复合催化剂的添加量为0.2g。对实施例1-9制备的复合催化膜进行扫描电镜(sem)扫描电镜分析,分析结果如下:图1为膜m1、m2、m3的sem扫描图,其中,图1a为膜m1的sem扫描图,图1b为膜m2的sem扫描图,图1c为膜m3的sem扫描图。由图1可知,复合催化薄膜的膜孔随着煅烧温度的增加逐渐变大,但是m1和m3的sem扫描图并不能很明显的看出复合催化剂bi2moo6/g-c3n4的负载情况,虽然m2上催化剂负载量并不多,但是负载效果明显。图2为膜m4、m5、m2和m6的sem扫描图,其中,图2a为膜m4的sem扫描图,图2b为膜m5的sem扫描图,图2c为膜m2的sem扫描图,图2d为膜m6的sem扫描图;由图2可以看出当bi2moo6的掺杂量为20%时,能看出复合催化薄膜上有负载着复合催化剂,但是孔洞较m2大,m1与m6均无明显的复合催化剂负载现象且m6孔洞较大。图3为膜m7、m2、m8和m9的sem扫描图,其中,图3a为膜m7的sem扫描图,图3b为膜m2的sem扫描图,图3c为膜m8的sem扫描图,图3d为膜m9的sem扫描图。由图3可知,m2与m8相比,m8的复合催化剂负载情况较好;m7中几乎观察不到负载的复合催化剂,说明当复合催化剂的投加量过少时效果并不理想,投加量增加到一定程度时催化剂并不能很好的与铸膜液混合均匀,导致出现团聚现象;比较m8与m9易发现m9的空洞明显小于m8,说明投加量过大也有可能会造成一定程度的膜孔堵塞。对实施例1-9制备得到的复合催化膜进行紫外光谱分析,分析结果如下:如图4为膜m1、m2和m3的紫外光谱图。由图4可知,在相同波长的前提下m1的吸光度明显低于m2与m3;且所有的复合催化薄膜均能吸收小于450nm的光,说明不同的煅烧温度对其光吸收能力影响不大;半导体禁带宽度计算公式如式(1)所示:eg=1240/λg(1)式中,eg为禁带宽度值(ev);λg为利用截线法做出吸收波长阙值(nm)。由公式(1)计算可得,m1-m3的光响应边的禁带宽度分别为2.93、3.12、2.75ev,m2的光响应边的禁带宽度稍大,其主要表现为最低能量光响应边增大,说明当投加了煅烧温度为550℃的复合催化剂时,增加了复合催化薄膜的利用空间跟光催化能力。图5为膜m2、m4、m5和m6的紫外光谱图。从图5中可以看出,在相同波长的条件下,当bi2moo6的掺杂量为复合催化剂质量的30wt.%时,复合催化薄膜的吸光度略低于其他掺杂量,且所有的复合催化薄膜均能吸收小于450nm的光,说明不同的掺杂比对其光吸收能力影响不大,但经由半导体禁带宽度计算公式(1)可得,m4、m5、m6的光响应边的禁带宽度分别为2.91、2.94、2.89ev均低于m2的禁带宽度。图6为膜m2、m7、m8和m9的紫外光谱图。由图6可知,当复合催化剂的投加量不同时,复合催化薄膜的紫外光谱变化有相同的趋势,当波长相同时,m7的吸光度始终高于其他投加量的薄膜,由计算可得m7-m9的禁带宽度分别为3.02、2.86和2.92ev。对实施例1-9制备得到的复合催化膜进行接触角分析,分析结果如下:利用接触角仪对不同复合催化薄膜进行亲水性和疏水性分析,结果如表1所示。由表1可知,m1到m3可以看出,随着复合催化剂中g-c3n4煅烧温度的增加,复合催化薄膜接触角先增大后减小;改变复合催化剂的bi2moo6的掺杂比,由m4、m5、m2、与m6可以看出,随着掺杂比的增加,复合催化薄膜接触角先减小后增大,当掺杂比为40wt.%时,表现为较高的疏水性,会影响到水的通过;由膜m2、m7、m8和m9的接触角测试结果可知,当复合催化剂的投加量为0.2g时,与其他投加量相比,接触角较小,表示亲水性越好。表1不同薄膜的接触角膜编号m1m2m3m4m5m6m7m8m9接触角(°)60.766.953.561.960.166.260.761.852.2对实施例1-9制备得到的复合催化膜进行ft-ir红外光谱分析,分析结果如下:图7为投加500℃-30wt.%-bi2moo6/g-c3n4、550℃-30wt.%-bi2moo6/g-c3n4与600℃-30wt.%-bi2moo6/g-c3n4复合催化剂的复合催化薄膜的ft-ir红外光谱分析图。由图7可知,三种复合催化薄膜的特征峰主要出现在1191.2cm-1到1283.5cm-1之间;1000-1700cm-1区域的一系列峰来自cn或cnn的拉伸模式;825.13cm-1和803.5cm-1的带对应mo-o键的伸缩振动峰;另外的出现在600-400cm-1范围内的带518.58cm-1处的峰为bi-o的伸缩振动模式。图8为投加550℃煅烧温度下不同投加量的bi2moo6/g-c3n4复合催化剂的复合催化薄膜的的傅里叶红外光谱分析图。由图8可知,1584.43cm-1为结晶水h2o变角的特征峰;薄膜在1353.20cm-1、1235.31cm-1、1238.38cm-1、1239.28cm-1为r1-so2-r2的so2反对称收缩的特征峰;在1169.07cm-1、1149.67cm-1为r1-so2-r2的so2对称收缩的特征峰;1000-1700cm-1区域的一系列峰来自cn或cnn的拉伸模式;在1102.44cm-1、1104.86cm-1为伯胺r-nh2的c-n伸缩。由此可见pei于ppsu之间存在相互作用力,使特征吸收峰移动。图9是投加量分别为0.025g、0.05g、0.1g和0.2g的550℃-30%-bi2moo6/g-c3n4复合催化剂的复合催化薄膜的傅里叶红外光谱分析图。由图9可知,四种不同组分复合薄膜的最高峰均出现在1200cm-1到1280cm-1之间,1000-1700cm-1区域的一系列峰来自cn或cnn的拉伸模式;825.13cm-1和803.5cm-1的吸收带对应mo-o键的伸缩振动峰;另外的出现在600-400cm-1范围内的吸收带518.58cm-1处的峰为bi-o的伸缩振动模式。实施例10膜水气通量的分析:(1)把测试膜水气通量的设备(如图10)搭接好,打开氮气罐的阀门清洗装置约3min;(2)将不同组分的复合催化薄膜均剪成长为120mm、宽为50mm的长方形薄膜,放进透明平板滤池中,检查设备情况后将透明平板滤池的盖子盖上,依次拧好6枚螺丝钉;(3)待压力和流量稳定后记录皂泡流量计上的读数,然后按照下式计算膜水气通量:式中,c-膜的水气通量,l/m2·h;v-每分钟通过的气体,l;a-薄膜面积,m2;t-反应时间,h。膜含水量的分析:(1)把备用的实施例1-9制备得到的共9片复合催化薄膜均裁剪为大小相等的正方形(4cm×4cm),将其放在蒸馏水中浸泡24h;(2)取出浸泡好的复合催化薄膜,用吸水纸将复合催化薄膜擦干,用电子天平称重后记录数据;(3)把称重后的复合催化薄膜在烘箱中进行干燥,温度设置在60℃,经过48h的干燥处理后,再取出进行称重,记录数据,水的平衡含水率百分比公式如式(3)所示:式中:ewc-平衡含水率;ww-湿样重量,g;wd-干样品重量,g。制作氢气浓度标准曲线:准备两个密闭性良好的fep特氟龙集气袋,先后用空气和氮气清洗后将集气袋抽真空后分别装上适量的纯氢气和纯氮气。再准备五个带有聚丙烯阀门的密闭性良好的集气袋,清洗干净后抽真空,取一个集气袋注入1ml的h2和9ml的n2,配制成含氢气10%的样品;再从含氢气10%的集气袋样品中抽1ml的气体注入另一个集气袋中,同时再抽取9ml的n2注入集气袋中稀释样品,配制成含氢气1%的样品后做好标记;以此方法分别配制氢气浓度为1000ppm,5000ppm,10000ppm,50000ppm和100000ppm的样品。待氢气混匀后,用5ml的气体注射器分别抽五袋配制好的气体,每次抽取2ml,每个气袋抽取3次,分别注入气相色谱仪中进行分析,取其平均峰面积以减少实验误差,将实验结果绘制成图,如图11所示,得到的标准曲线方程为:y=22.669x+14921,其中y表示平均峰面积,x表示氢气浓度。氢气采集装置如图10所示。该装置包括不锈钢三口烧瓶1、透明平板滤池5和集气袋7;不锈钢三口烧瓶1上设有调温电热套;不锈钢三口烧瓶1的一个口与无氧水瓶3连接,还有个口与高纯氮气瓶4连接;透明平板滤池5的另一端与集气袋7连接;不锈钢三口烧瓶1与无氧水瓶3之间设有蠕动泵2,不锈钢三口烧瓶1与高纯氮气瓶4之间设有氮气质量流量计9;透明平板滤池5与集气袋7之间设有干燥瓶6;集气袋7和干燥瓶6上连接皂泡流量计10;透明平板滤池5上设有复合薄膜12,复合薄膜12与不锈钢三口烧瓶1中另一个口连接,并且之间设有压力计11和加热线圈,复合薄膜12上设有紫外光灯8。氢气采集装置的工作过程为:把复合薄膜12放进透明平板滤池5中;反应前将曝气完的去离子水装满无氧水瓶3,连接蠕动泵2;开启高纯氮气瓶4,使氮气在整套反应装置里顺畅流通;开启加热线圈,待加热线圈加热到110℃时开启调温电热套,调温至100℃;待不锈钢三口烧瓶1完全预热时开启恒流泵,调节流速至理想状态后开始用虹吸的方法注入无氧去离子水的混合液,开始反应;混合液在100℃的不锈钢三口烧瓶1里气化成水蒸气,经载气n2的推动,水蒸气通过加热线圈的保温后进入透明平板滤池5的上半部分,在紫外光灯8的照射下结合复合催化薄膜上的复合催化剂催化水蒸气产生氢气,氢气从透明平板滤池5的下半部分出来;氢气从透明平板滤池5出来后,随后进入干燥瓶6,干燥后进入皂泡流量计10测出气体流速;待皂泡流量计10的示数稳定后,以10min为一个反应时间,打开阀门2开始采集气体,采集3min后关闭集气袋7,共反应3次,完成采气。表2为膜m1、m2和m3的水气通量、含水率和产氢速率测试结果。由表2可知,在m1-m3中,复合催化薄膜的含水率无明显的变化趋势;复合催化薄膜的单位面积水气通量的变化趋势跟产氢速率的变化趋势相反,水气通量越大,表示气体与薄膜接触的时间越短,则反应时间越短,从而导致产氢速率最低;其中m1的单位面积水气通量为1013.00l/m2·h明显高于其他两片膜,这与复合催化剂是否与铸膜液混合均匀、复合催化剂的粒径有着直接的关系,光催化活性较低也会导致产氢速率低,m2的产氢速率最快,达到1347.953μmol/(hr·m3·kpa),综合考虑,选择550℃为最佳煅烧温度。表2膜m1、m2和m3的水气通量、含水率和产氢速率测试结果注:表中数值为平均值±标准偏差,每个样品分析5次的平均值和标准偏差。表3为膜m4、m5、m2和m6的水气通量、含水率和产氢速率测试结果。由表3可知,复合催化薄膜的含水率无明显的变化趋势;复合催化薄膜的单位面积水气通量的变化趋势跟产氢速率的变化趋势相反;复合催化薄膜的产氢速率先增大后减小,说明bi2moo6的掺杂量有一个最佳值,当bi2moo6的掺杂比为10wt.%与40wt.%时产氢速率明显偏低,说明当bi2moo6的掺杂比为10wt.%时,bi2moo6对g-c3n4的负载量不够,不能很好的提高光催化活性,而掺杂比为40wt.%时虽然提高了bi2moo6对g-c3n4的负载量,但是高浓度的掺杂比并不利于反应的进行,说明过量的bi2moo6覆盖了g-c3n4上的表面活性位点;其中m2的产氢速率最快,达到1347.953μmol/(hr·m3·kpa),综合考虑,选择30wt.%为最佳掺杂比。表3膜m4、m5、m2和m6的水气通量、含水率和产氢速率测试结果膜编号单位面积水气通量(l/m2·h)含水率ewc(%)产氢速率(μmol/(hr·m3·kpa))m4678.73±136.2662733.473±175.669m5617.53±85.43641031.817±171.152m2597.38±145.30601347.953±167.876m6990.10±278.1268598.959±171.019注:表中数值为平均值±标准偏差,每个样品分析5次的平均值和标准偏差。表4为膜m7、m2、m8和m9的水气通量、含水率和产氢速率测试结果。如表4所示,复合催化薄膜的含水率并无明显的变化趋势;水气通量越大,产氢速率越小,从理论上说水气通量越大,气体与薄膜接触的时间越短,则反应时间越短,从而导致产氢速率最低;但m9的水气通量最低而产氢速率却不是最高的,说明复合催化剂的投加量有一个最适值,超过这一最适值后会导致复合催化剂与铸膜液混合不均匀,复合催化剂聚集在一起会堵塞膜孔;m8的产氢速率最快,达到1581.396μmol/(hr·m3·kpa),综合考虑,选择0.1g为最佳投加量。表4膜m7、m2、m8和m9的水气通量、含水率和产氢速率测试结果注:表中数值为平均值±标准偏差,每个样品分析5次的平均值和标准偏差。当前第1页12