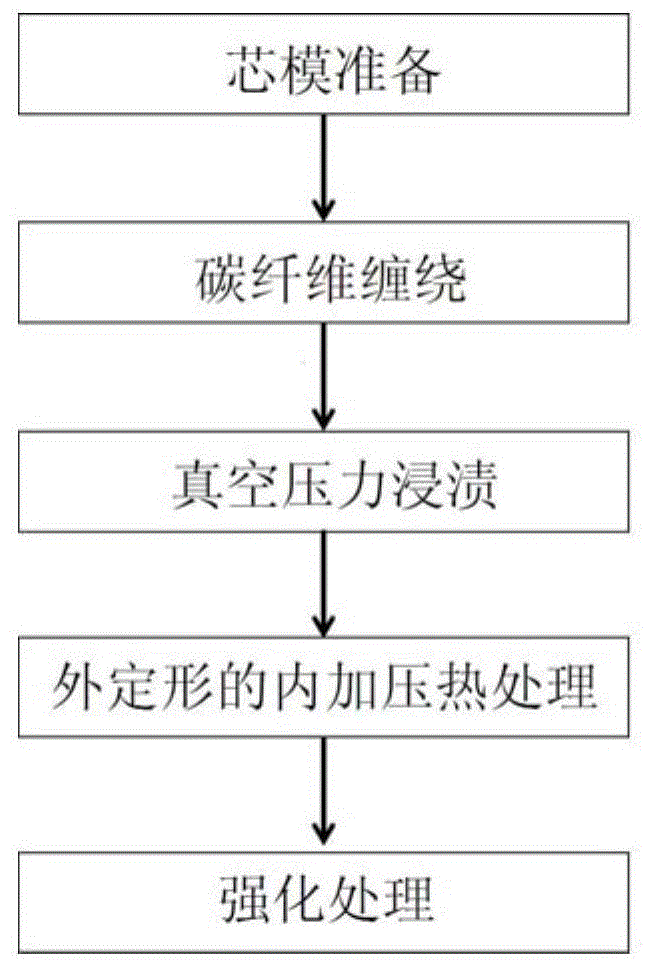
本发明属于复合材料制备技术领域,具体涉及回转体类炭/炭复合材料的制备方法。
背景技术:
炭/炭复合材料是炭纤维增强炭基体的复合材料,具有高强高模、比重轻、热膨胀系数小、抗腐蚀、抗热冲击、耐摩擦性能好、化学稳定性好等一系列优异性能,是一种新型的超高温复合材料。其中回转体类炭/炭复合材料已以炭/炭坩埚、炭/炭热压模具等产品形式广泛地应用于单晶硅提拉、先进陶瓷热压等民用领域。
尽管炭/炭复合材料具有众多优异的性能,但由于价格昂贵的原因,目前在民用领域主要应用在其它材料难以替代的苛刻工作环境下。炭/炭复合材料制造周期长、成本高的特点很大程度上限制了这种优秀材料在国民经济各领域的广泛应用。近十多年来,在兼顾结构性能的同时,缩短制造周期、降低成本、扩大应用范围成为炭/炭复合材料领域主攻的研究重点。
缠绕/卷绕成型工艺是将浸过树脂胶液的连续纤维(或布带、预浸纱)按照一定规律缠绕/卷绕到芯模上,然后经固化、脱模,获得产品。应用缠绕/卷绕成型工艺获得的炭/炭复合材料具有比强度高、结构可设计性好、生产效率和产品可靠性高、原料成本低的特点。申请号为200610104824.9的专利公开了一种c/c复合材料导电螺纹杆的制备方法,采用“轴向碳纤维棒+碳纤维缠绕/卷绕环向螺纹”预制体,通过化学气相沉积和液相浸渍/炭化等增密手段,最终得到高密度c/c复合材料导电螺纹杆。申请号为201280038583.6的专利公开了一种提高缠绕/卷绕成型复合材料层间结合强度的方法,通过不同层的缠绕/卷绕角度变化,使层间纤维发生镶嵌从而实现层间结合强度的提高。申请号为201310336558.2的专利公开了一种应用缠绕/卷绕成型技术的炭/炭坩埚制作方法,通过将炭纤维在芯模的的表面进行逐层缠绕/卷绕成型,制得坩埚预制体,然后对坩埚预制体进行坩埚固化及坩埚增密处理,最终制得密度≥1.70g/cm3的炭/炭坩埚成品。申请号为201510103863.6的专利涉及一种高强度轻质碳/碳复合材料的制备方法,通过对纤维的预处理和对树脂的混合改性,应用缠绕/卷绕成型工艺所获得的高强度轻质碳/碳复合材料拉伸强度达到800mpa以上,热导率为500w/(m·k)~530w/(m·k),热扩散率为4.4cm2/s。通过以上专利可以看出,缠绕/卷绕成型炭/炭复合材料能够获得优异的力学性能。同时,在保证性能的同时缩短制备周期进而实现高效制备方面,目前并没有完整的制备方法的相关研究。
技术实现要素:
本发明所要解决的技术问题在于针对上述现有技术的不足,提供一种回转体类炭/炭复合材料的制备方法。该方法制备厚度大于目标产物回转体类炭/炭复合材料厚度的缠绕体,然后引入沥青并采用外定形的内加压热处理工艺和强化处理达到目标产物厚度,从而增加了回转体类炭/炭复合材料中的炭纤维体积含量,提高了回转体类炭/炭复合材料的性能,缩短了后续工艺中的增密周期,进而提高了回转体类炭/炭复合材料的制备效率。
为解决上述技术问题,本发明采用的技术方案是:回转体类炭/炭复合材料的制备方法,其特征在于,该方法包括以下步骤:
步骤一、芯模准备:采用清洗剂对芯模的外表面进行清洁,然后在清洁后的芯模的外表面铺放脱模布并在脱模布上刷涂脱模剂;
步骤二、碳纤维缠绕:采用缠绕机将连续炭纤维在步骤一中刷涂脱模剂的芯模上进行缠绕,并在芯模上形成缠绕件;所述缠绕件的厚度大于目标产物回转体类炭/炭复合材料的厚度;
步骤三、真空压力浸渍:将步骤二中得到的缠绕件连同芯模埋入沥青中,然后放置于真空压力浸渍炉进行真空压力浸渍,脱模后进行内外型面机加处理,得到浸渍件;
步骤四、内加压热处理:对步骤三中得到的浸渍件的外表面施加定型工装,并在浸渍件的内部放入或通入传压介质材料,然后通过传压介质材料对浸渍件及定型工装进行内加压热处理,使得浸渍件的内径和外径同时增大且外径的增大值小于内径的增大值,从而浸渍件的厚度减小,得到回转体类炭/炭复合材料坯体;所述内加压热处理的过程为:对浸渍件进行内部加压并对浸渍件及定型工装进行热处理,当热处理的温度升至浸渍件中沥青软化温度时,加大压力并保压,再在保压状态下升温依次进行炭化和石墨化;所述回转体类炭/炭复合材料坯体的厚度不小于目标产物回转体类炭/炭复合材料的厚度;
步骤五、强化处理:对步骤四中得到的回转体类炭/炭复合材料坯体进行强化,得到回转体类炭/炭复合材料;所述强化的方法为增密处理或/和制备涂层处理,所述增密处理采用树脂液相浸渍炭化或化学气相渗透,所述制备涂层处理采用化学气相沉积或刷涂。
本发明采用在芯模上缠绕成型的方法制备得到厚度大于目标产物回转体炭/炭复合材料的缠绕件,有利于避免纤维损失,提高纤维强度发挥率,然后进行真空压力浸渍引入沥青得到浸渍件,再在其外表面施加定型工装以限制变形,进行外定形的内加压热处理,使浸渍件的内、外径在同时增大的前提下,浸渍件外径增大值小于内径增大值,从而得到厚度发生减小、但不小于最终产品厚度的回转体类炭/炭复合材料坯体,在该内加压热处理过程中,当加热至沥青软化且成低粘度状态时进行内加压,沥青和炭纤维在内型面径向压力的作用下进行环向方向的流动/滑移及重新排布,由于浸渍件外径被定型工装限制而不能自由改变,因此浸渍件厚度变小,沥青对纤维的浸渍更为充分且分布更为均匀,纤维充分舒展且呈现拉应力状态,进一步提高了纤维强度发挥率;随着浸渍件的压缩,炭纤维体积含量增大,沥青的含量随之减小,由于沥青热处理过程中会产生缺陷,因此沥青体积含量的减少有利于后续热处理过程中缺陷数量的减少,从而提高纤维层间结合性能;当炭化和石墨化过程中进行内加压时,使得沥青在受压状态下发生相应结构转变,有利于提高回转体类炭/炭复合材料坯体中的残炭率,通过内加压热处理获得的炭化件和/或石墨件密度较高,避免或缩短了后续增密周期,由于定型工装的限制作用,本发明实现了净成型制造,有效缩减了机加工周期,从而提高了回转体类炭/炭复合材料的制备效率,同时有利于避免机加工工序对产品表面造成的损伤,有利于回转体类炭/炭复合材料性能的提升。
上述的回转体类炭/炭复合材料的制备方法,其特征在于,步骤一中所述芯模的外表面形状与目标产物回转体类炭/炭复合材料的内表面形状相同或类似。在芯模准备过程中,根据目标产物回转体类炭/炭复合材料的结构设计以及后续内加压热处理过程中纤维材料的形变规律设计制备芯模,因此,优选芯模的内表面形状与目标产物回转体类炭/炭复合材料的外表面形状相同或类似,有利于目标产物的快速成型及脱模,提高制备效率。
上述的回转体类炭/炭复合材料的制备方法,其特征在于,步骤二中所述连续炭纤维为pan基炭纤维、沥青基炭纤维和黏胶基炭纤维的一种或两种以上。采用上述优选材质满足了不同用途的回转体类炭/炭复合材料的制备,包括结构件和功能件,而使用不同种类炭纤维的组合,有利于扩大本发明回转体类炭/炭复合材料的应用范围。
上述的回转体类炭/炭复合材料的制备方法,其特征在于,步骤二中所述缠绕的方式为螺旋缠绕或者环向螺旋交替缠绕,其中,环向缠绕的角度为85°~89°,螺旋缠绕的角度为20°~85°,所述环向螺旋交替缠绕过程中,通过缠绕机的控制主机对缠绕机的机头进行自动控制,在不割断连续炭纤维的条件下使连续炭纤维的缠绕方向由螺旋缠绕方向逐渐自动转换为环向缠绕方向,或者由环向缠绕方向逐渐自动转换为螺旋缠绕方向,以实现螺旋缠绕层与环向缠绕层之间的连续过渡。采用该优选缠绕方法、角度及缠绕操作要点所制备的炭/炭复合材料满足了对制备装置、制备效率和工艺成本的不同要求,有利于获得不同结构性能设计的炭/炭复合材料。
上述的回转体类炭/炭复合材料的制备方法,其特征在于,步骤二中所述缠绕件的厚度为步骤五中得到的回转体类炭/炭复合材料厚度的1.05~1.75倍。通过该优选厚度倍数,有利于使缠绕件通过内加压热处理工艺获得纤维强度发挥率高、制备周期短的回转体类炭/炭复合材料。
上述的回转体类炭/炭复合材料的制备方法,其特征在于,步骤四中所述回转体类炭/炭复合材料坯体中纤维体积含量平均值vf为65%以上或层数分布不小于50层/cm。通过内加压热处理工艺获得上述的回转体类炭/炭复合材料坯体中纤维充分舒展、均匀承力、强度发挥率高,且纤维缠绕层之间树脂热解炭均匀致密,缺陷较少,坯体材料呈现良好的层间结合性能。
上述的回转体类炭/炭复合材料的制备方法,其特征在于,步骤四中所述定型工装的内径大于浸渍件的外径,且定型工装与浸渍件的间隙尺寸为0.5mm~5mm。定型工装的内径大于浸渍件的外径保证了定型工装的定型作用;该优选间隙尺寸容纳了内加压热处理过程中的浸渍件的高温膨胀变形,同时实现了良好的定型作用。
上述的回转体类炭/炭复合材料的制备方法,其特征在于,步骤四中所述炭化和石墨化采用的传压介质材料为固相,所述固相的传压介质材料为石墨粉或炭化硅粉。该优选的传压介质材料能够承受炭化和石墨化温度,且自身不发生反应也不与浸渍件发生反应,有利于在内加压热处理过程中对浸渍件内型面的均匀施压,避免由于局部受压不够或过多导致的缺陷产生。
上述的回转体类炭/炭复合材料的制备方法,其特征在于,步骤四中所述内加压热处理在真空或惰性气氛保护下进行,所述炭化和石墨化均采用台阶式加热热处理工艺。根据沥青的粘温曲线和热解曲线制定炭化制度,根据炭化后得到的炭化件的结构转化规律制定石墨化制度,通过真空或惰性气氛保护有利于抑制浸渍件在热处理过程中与空气发生氧化反应导致坯体强度下降;通过台阶式加热热处理工艺,有利于抑制工艺过程中浸渍件的应力集中,从而获得性能更为优良的回转体类炭/炭复合材料。
上述的回转体类炭/炭复合材料的制备方法,其特征在于,步骤四中所述内加压热处理的制度为:(1)先在4mpa~8mpa的压力下,以20℃/min~35℃/min的速率升温至沥青软化温度;(2)然后在4mpa~8mpa的压力下,以10℃/min~35℃/min的速率升温至沥青粘度最低值的温度并保温1h~3h;(3)继续在4mpa~8mpa的压力下,以5℃/min~10℃/min的速率升温至400℃并保温0.5h~2h;(4)继续在4mpa~8mpa的压力下,以1℃/min~3℃/min的速率升温至550℃并保温0.5h~2h;(5)继续在4mpa~8mpa的压力下,以5℃/min~10℃/min的速率升温至900℃并保温1h~2h完成炭化;(6)再在2mpa~5mpa的压力下,以5℃/min~50℃/min的速率升温至2600℃并保温1h~2h完成石墨化,然后随炉冷却至室温。通过该优选内加压热处理制度,有利于使浸渍件内沥青和纤维在内型面径向压力的作用下进行环向方向的流动/滑移及重新排布,坯体纤维体积更高,沥青对纤维的浸渍充分且分布更为均匀,纤维充分舒展且呈现拉应力状态,进一步提高了纤维强度发挥率及缠绕成型炭/炭复合材料性能。
上述的回转体类炭/炭复合材料的制备方法,其特征在于,步骤五中所述化学气相渗透强化的具体过程为:对化学气相渗透炉抽真空,然后以100℃/h~300℃/h的速率升温至950℃~1300℃并保持化学气相渗透炉中的真空度低于2000pa,再将惰性气体与碳氢气体按照2:1的体积比通入化学气相渗透炉中进行化学气相渗透10h~60h。通过该优选的增密强化过程,有利于修复制备过程中产生的表面积内部缺陷,从而进一步提升缠绕成型炭/炭复合材料性能。
本发明与现有技术相比具有以下优点:
1、本发明首先制备厚度大于目标产物回转体类炭/炭复合材料厚度的缠绕体,然后引入沥青并采用外定形的内加压热处理工艺和强化工艺至其达到目标产物厚度,从而增加了目标产物回转体类炭/炭复合材料中的炭纤维体积含量,改善了回转体类炭/炭复合材料结构,提高了回转体类炭/炭复合材料的性能,缩短了后续工艺中的增密周期,进而提高了回转体类炭/炭复合材料的制备效率。
2、本发明通过引入沥青并采用外定形的内加压热处理工艺,克服了缠绕过程中因张力递减导致平均张力值较低的缺点,提高了缠绕效果,同时在内加压热处理过程中,通过纤维滑移和沥青迁移,浸渍件的层间间距减小且沥青分布均匀、渗透充分,有效抑制了层间和层内缺陷的产生,提高了回转体类炭/炭复合材料的质量。
3、本发明在内加压状态下进行热处理,提高了沥青的残炭率,同时有利于沥青热解炭强度的提高以及改善其与纤维的紧密结合程度,提高了回转体类炭/炭复合材料层间的结合性能,进而改善了回转体类炭/炭复合材料的力学和热学性能,使其满足了大部分结构件应用需求,扩大了回转体类炭/炭复合材料的应用范围。
4、本发明通过在外定形内加压条件下进行渐进式梯度加压的炭化和石墨化,解决了常规缠绕成型的炭/炭复合材料随温度升高产生滑移、变形等问题,同时有利于抑制回转体类炭/炭复合材料在炭化和石墨化过程中由于材料各组分的不均匀变化所导致的椭圆变形,确保了产品结构尺寸的稳定性,实现了近净尺寸制造,减少了后续机加工工艺,进一步提高了回转体类炭/炭复合材料的制备效率。
5、本发明优选通过台阶式的外定形内加压热处理工艺及参数,克服了浸渍沥青后的浸渍件炭化过程中内部出现局部分层、以及高温处理中体积收缩造成分层或开裂的缺陷,同时消除了后续增密强化过程中形成的内部残余应力,有效保证了回转体类炭/炭材料制品内部质量和综合性能。
6、本发明通过后续的增密强化处理,进一步提高了炭/炭复合材料的密度,弥合了炭/炭复合材料材料表面损伤和内部微裂纹,进一步改善了炭/炭复合材料的使用性能。
7、本发明制备的回转体类炭/炭复合材料的环向拉伸强度大于120mpa,弯曲强度大于150mpa,层间剪切强度大于15mpa,热膨胀系数(1000℃)小于3.0×10-6/k,且回转体类炭/炭复合材料的总体力学、热物理性能高,尺寸稳定性好,同时实现近净尺寸制造,制备原料损耗降低30%以上,将密度为1.40g/cm3的炭/炭材料制备周期缩短至35天以内。
下面通过附图和实施例对本发明的技术方案作进一步的详细描述。
附图说明
图1为本发明制备方法的流程框图。
图2为本发明内加压热处理采用的热压装置的结构示意图。
附图标记说明
1—浸渍件;2—传压介质材料;3—热压辅助环;
4—热压模具;5—发热体;6—热压压头。
具体实施方式
如图1所示,本发明制备方法的过程为:首先进行芯模准备,然后将碳纤维缠绕在准备好的芯模上成型,进行真空压力浸渍,再进行外定形的内加压热处理,最后经强化处理得到回转体类炭/炭复合材料。
如图2所示,本发明采用的内加压热处理装置包括盛放有浸渍件1的热压模具4,以及设置在热压模具4外侧的发热体5,所述热压模具4中浸渍件1的内部分布着传压介质材料2,且热压模具4中浸渍件1的上端装配有热压辅助环3,所述热压辅助环3与热压压头6配合。
实施例1
本实施例的制备方法包括以下步骤:
步骤一、芯模准备:确定目标产物圆筒形状炭/炭复合材料的内径660mm,外径690mm,壁厚30mm,长度500mm,高温椭圆变形量不超过3mm,密度不小于1.65g/cm3,环向拉伸强度不小于190mpa,层间剪切强度不小于25mpa,根据目标产物圆筒形状炭/炭复合材料以及采用的连续炭纤维的热处理变形规律,设计外表面形状与目标产物圆筒形状炭/炭复合材料的内表面形状相同、长度为600mm、外径为586mm的金属芯模,采用清洗剂对该金属芯模的外表面进行清洁,然后在清洁后的金属芯模的外表面铺放聚四氟乙烯脱模布并在聚四氟乙烯脱模布上刷涂硅脂作为脱模剂;
步骤二、碳纤维缠绕:采用缠绕机将12k的pan基连续炭纤维的4团纱按照环向螺旋交替缠绕的方式在步骤一中刷涂硅脂脱模剂的金属芯模上进行缠绕,其中,螺旋缠绕的角度为20°,环向缠绕的角度为85°,并在金属芯模上形成缠绕件;所述环向螺旋交替缠绕过程中,通过缠绕机的控制主机对缠绕机的机头进行自动控制,在不割断连续炭纤维的条件下使连续炭纤维的缠绕方向由螺旋缠绕方向逐渐自动转换为环向缠绕方向,或者由环向缠绕方向逐渐自动转换为螺旋缠绕方向,以实现螺旋缠绕层与环向缠绕层之间的连续过渡;所述缠绕采用等张力缠绕方式,张力42n;所述缠绕件的尺寸为:内径586mm,外径691mm,厚度为52.5mm,高度为520mm,缠绕件中纤维体积含量vf为55%;
步骤三、真空压力浸渍:将步骤二中得到的缠绕件连同金属芯模埋入中温沥青中,然后放置于真空压力浸渍炉的包套筒中进行真空压力浸渍,脱模后进行内外型面机加处理,得到外径为690mm的浸渍件;所述真空压力浸渍的过程为:在氮气气氛条件下,在80min内升温至320℃后抽真空至0.092mpa并保持2h,再通入氮气加压至2mpa并保持2h;
步骤四、内加压热处理:将步骤三中得到的浸渍件放置于热压装置的热压模具1中,并在其外表面施加定型工装(即热压辅助环3),并在浸渍件的内部放入传压介质材料2,然后在氮气气氛条件下通过热压压头6对作为传压介质材料2的石墨粉进行加压,并通过发热体5进行加热升温,对浸渍件及热压辅助环3进行内加压热处理,使得浸渍件的内径和外径同时增大且外径的增大值小于内径的增大值,从而浸渍件的厚度减小,得到圆筒形状炭/炭复合材料坯体;所述热压模具1的内径为691mm;所述内加压热处理的过程为:(1)先在4mpa~8mpa的压力下,以20℃/min~35℃/min的速率升温至150℃;(2)然后在4mpa~8mpa的压力下,以10℃/min~35℃/min的速率升温至320℃并保温3h;(3)继续在4mpa~8mpa的压力下,以5℃/min~10℃/min的速率升温至400℃并保温0.5h;(4)继续在4mpa~8mpa的压力下,以1℃/min~3℃/min的速率升温至550℃并保温0.5h;(5)继续在4mpa~8mpa的压力下,以5℃/min~10℃/min的速率升温至900℃并保温1h完成炭化;所述炭化后浸渍件的尺寸为:内径658mm,外径690.5mm,厚度16.25mm,高度520mm,炭化后浸渍件中纤维体积含量vf为65%;(6)在石墨化炉中,在2mpa的压力下,使用石墨粉作为内加压石墨化处理的压力传递介质,以50℃/min的速率升温至2600℃并保温1h完成石墨化,然后随炉冷却至室温;所述圆筒形状炭/炭复合材料坯体的厚度为30mm,纤维体积含量平均值vf为75%,层数分布为65层/cm,密度为1.45g/cm3,无明显分层等缺陷;
步骤五、强化处理:对步骤四中得到的圆筒形状炭/炭复合材料坯体进行机械加工,然后放置于化学气相渗透炉中并抽真空至500pa,以100℃/h~300℃/h的速率升温至950℃并保持化学气相渗透炉中的真空度低于2000pa,再将氩气与天然气按照2:1的体积比通入化学气相渗透炉中进行化学气相渗透10h进行强化,得到圆筒形状炭/炭复合材料。
经检测,本实施例制备的圆筒形状炭/炭复合材料的密度为1.66g/cm3,高温椭圆变形量不超过2mm,机加性能较好,且环向拉伸强度为200mpa,层间剪切强度为27mpa,圆筒形状炭/炭复合材料无分层等明显缺陷。
本实施例步骤二中的连续碳纤维还可为除了pan基连续炭纤维以外的pan基炭纤维、沥青基炭纤维和黏胶基炭纤维的一种或两种以上。
本实施例步骤五中的强化处理的方法还可采用树脂液相浸渍炭化、化学气相沉积或刷涂。
实施例2
本实施例的制备方法包括以下步骤:
本实施例与实施例1的不同之处为:步骤一中目标产物炭/炭埚帮的设计密度为不小于1.45g/cm3,层间结合强度为不小于15mpa,环向拉伸强度指标不小于120mpa,芯模材质为电极石墨,芯模的外径为597mm;步骤二中螺旋缠绕角度为85°,环向缠绕角度为87°,缠绕件内径597mm,外径660mm,厚度为31.5mm;步骤四中热压模具的内径为670mm,与缠绕件间隙为5mm,所述内加压热处理的过程为:(1)先在4mpa~8mpa的压力下,以20℃/min~35℃/min的速率升温至150℃;(2)然后在4mpa~8mpa的压力下,以10℃/min~35℃/min的速率升温至320℃并保温1h;(3)继续在4mpa~8mpa的压力下,以5℃/min~10℃/min的速率升温至400℃并保温2h;(4)继续在4mpa~8mpa的压力下,以1℃/min~3℃/min的速率升温至550℃并保温2h;所述炭/炭埚帮坯体的厚度为30mm,纤维体积含量平均值vf为68%,层数分布为50层/cm,密度为1.45g/cm3,无明显分层等缺陷;步骤五中化学气相渗透温度为1300℃,化学气相渗透时间为60h,得到炭/炭埚帮坯体。
经检测,本实施例制备的炭/炭埚帮的密度为1.57g/cm3,高温椭圆变形量不超过2mm,机加性能较好,且环向拉伸强度为178mpa,层间剪切强度为25mpa,炭/炭埚帮无分层等明显缺陷。
实施例3
本实施例的制备方法包括以下步骤:
本实施例与实施例1的不同之处为:步骤一中目标产物炭/炭埚帮的设计密度为不小于1.55g/cm3,层间结合强度为不小于22mpa,环向拉伸强度指标不小于170mpa,芯模材质为电极石墨,芯模的外径为609mm;步骤二中螺旋缠绕角度为55°,环向缠绕角度为89°,缠绕件内径609mm,外径690mm,厚度为40.5mm;步骤四中热压模具的内径为696mm,与缠绕件间隙为3mm,所述内加压热处理的过程为:(1)先在4mpa~8mpa的压力下,以20℃/min~35℃/min的速率升温至150℃;(2)然后在4mpa~8mpa的压力下,以10℃/min~35℃/min的速率升温至320℃并保温2h;(3)继续在4mpa~8mpa的压力下,以5℃/min~10℃/min的速率升温至400℃并保温1.2h;(4)继续在4mpa~8mpa的压力下,以1℃/min~3℃/min的速率升温至550℃并保温1.2h;所述圆筒形状炭/炭复合材料坯体的厚度为30mm,纤维体积含量平均值vf为70%,层数分布为55层/cm,密度为1.55g/cm3,无明显分层等缺陷;步骤五中化学气相渗透温度为1130℃,化学气相渗透时间为35h,得到炭/炭埚帮。
经检测,本实施例制备的炭/炭埚帮的密度为1.57g/cm3,高温椭圆变形量不超过2mm,机加性能较好,且环向拉伸强度为178mpa,层间剪切强度为25mpa,炭/炭埚帮无分层等明显缺陷。
以上所述,仅是本发明的较佳实施例,并非对本发明作任何限制。凡是根据发明技术实质对以上实施例所作的任何简单修改、变更以及等效变化,均仍属于本发明技术方案的保护范围内。