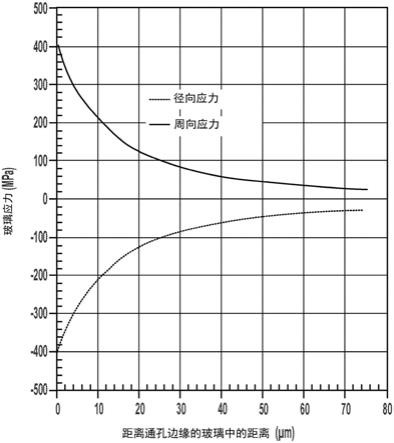
具有铜金属化贯穿孔的玻璃或玻璃陶瓷制品及其制造过程
1.本技术要求2019年2月21日提交的美国临时申请序号62/808,566的优先权权益,其内容通过参照全文的方式被引为依据并并入本文。
2.背景
技术领域
3.本说明书大体上涉及制造玻璃或玻璃陶瓷及具有铜金属化导电贯穿孔的玻璃或玻璃陶瓷制品的过程,且具体地涉及加热具有铜金属化贯穿孔的玻璃或玻璃陶瓷制品以减少径向开裂的过程。
背景技术:4.因为玻璃和玻璃陶瓷基材通常不与电子装置的其他部件反应,所以玻璃和玻璃陶瓷基材被用在电子装置的部件中。此可部分地是由于玻璃和玻璃陶瓷基材具有低介电常数,且由于玻璃和玻璃陶瓷基材是热稳定的。在许多电子装置中,玻璃和玻璃陶瓷基材具有贯穿孔,可通过将金属引入贯穿孔中而使贯穿孔具有导电性,例如中介层。为了将玻璃和玻璃陶瓷基材用于电子装置的部件,诸如中介层,将导电金属层施加于玻璃和玻璃陶瓷基材的一个或多个表面,且导电金属填充玻璃和玻璃陶瓷基材中的贯穿孔。通常用于填充玻璃和玻璃陶瓷基材中的贯穿孔的一种金属为铜(cu),这是由于其具有高的导电性。然而,当加热包含铜金属化贯穿孔的玻璃或玻璃陶瓷制品时,贯穿孔附近会形成径向裂痕,径向裂痕会使得包含铜金属化贯穿孔的玻璃或玻璃陶瓷制品变得低效率或不可使用。
5.因此,需要减少在加热期间包含铜金属化贯穿孔的玻璃和玻璃陶瓷制品中的径向裂痕的过程。
技术实现要素:6.根据第一条条款,方法包含将包含铜金属化贯穿孔的玻璃或玻璃陶瓷制品从第一温度加热至第二温度,其中第一温度大于或等于200℃且小于或等于300℃,及其中第二温度大于或等于350℃且小于或等于450℃,其中在包含铜金属化贯穿孔的玻璃或玻璃陶瓷制品从第一温度加热至第二温度期间的平均加热速率大于0.0℃/分钟且小于8.7℃/分钟。
7.第二条条款包括第一条条款的方法,其中将包含铜金属化贯穿孔的玻璃或玻璃陶瓷制品从第一温度加热至第二温度不在包含铜金属化贯穿孔的玻璃或玻璃陶瓷制品中造成径向裂痕。
8.第三条条款包括先前条款中任一者的方法,其进一步包含将包含铜金属化贯穿孔的玻璃或玻璃陶瓷制品从室温加热至第一温度。
9.第四条条款包括第三条条款的方法,其中在将包含铜金属化贯穿孔的玻璃或玻璃陶瓷制品从室温加热至第一温度期间的平均加热速率大于0.0℃/分钟且小于8.7℃/分钟。
10.第五条条款包括先前条款中任一者的方法,其中第一温度大于或等于225℃且小于或等于275℃。
11.第六条条款包括先前条款中任一者的方法,其中第二温度大于或等于375℃且小于或等于425℃。
12.第七条条款包括先前条款中任一者的方法,其中在将包含铜金属化贯穿孔的玻璃或玻璃陶瓷制品从第一温度加热至第二温度期间的平均加热速率大于或等于1.0℃/分钟且小于或等于6.5℃/分钟。
13.第八条条款包括先前条款中任一者的方法,其中在将包含铜金属化贯穿孔的玻璃或玻璃陶瓷制品从第一温度加热至第二温度期间的平均加热速率基本上恒定。
14.第九条条款包括先前条款中任一者的方法,其中在将包含铜金属化贯穿孔的玻璃或玻璃陶瓷制品从第一温度加热至第二温度期间的平均加热速率是可变的。
15.第十条条款包括先前条款中任一者的方法,其中,所述方法进一步包括:将包含铜金属化贯穿孔的玻璃或玻璃陶瓷制品保持在第一温度持续大于或等于10分钟且小于或等于1小时的时段。
16.第十一条条款包括先前条款中任一者的方法,其中,方法进一步包括:将包含铜金属化贯穿孔的玻璃或玻璃陶瓷制品保持在第二温度持续大于或等于10分钟且小于或等于1小时的时段。
17.第十二条条款包括先前条款中任一者的方法,其中,将包含铜金属化贯穿孔的玻璃或玻璃陶瓷制品从第一温度加热至第二温度包括:将包含铜金属化贯穿孔的玻璃或玻璃陶瓷制品保持在恒定温度持续大于或等于10分钟且小于或等于45分钟的时段。
18.第十三条条款包括先前条款中任一者的方法,其中包含铜金属化贯穿孔的玻璃或玻璃陶瓷制品中的贯穿孔的直径大于或等于25μm且小于或等于75μm。
19.第十四条条款包括先前条款中任一者的方法,其中包含铜金属化贯穿孔的玻璃或玻璃陶瓷制品中的贯穿孔的节距大于或等于60μm且小于或等于800μm。
20.第十五条条款包括先前条款中任一者的方法,其中包含铜金属化贯穿孔的玻璃或玻璃陶瓷制品中的贯穿孔的深度大于或等于50μm且小于或等于600μm。
21.第十六条条款包括先前条款中任一者的方法,其中玻璃或玻璃陶瓷制品包含至少90重量%的二氧化硅。
22.第十七条条款包括一种方法,其包括:将包含铜金属化贯穿孔的玻璃或玻璃陶瓷制品从第一温度加热至第二温度,其中第一温度大于或等于240℃且小于或等于260℃,及其中第二温度大于或等于400℃且小于或等于450℃,其中在包含铜金属化贯穿孔的玻璃或玻璃陶瓷制品从第一温度加热至第二温度期间的平均加热速率大于0.0℃/分钟且小于或等于6.5℃/分钟。
23.第十八条条款包括一种玻璃或玻璃陶瓷制品,其包含:包含至少一个贯穿孔的玻璃或玻璃陶瓷基材,所述至少一个贯穿孔在厚度方向上穿透玻璃或玻璃陶瓷基材;以及存在于所述至少一个贯穿孔中的铜,其中玻璃或玻璃陶瓷制品在退火到≤450℃后不包含径向裂痕。
24.第十九条条款包括第十八条条款的玻璃或玻璃陶瓷制品,其中玻璃或玻璃陶瓷基材包含至少90重量%的二氧化硅。
25.第二十条条款包括第十八或十九条条款的玻璃或玻璃陶瓷制品,其中玻璃或玻璃陶瓷基材中的所述至少一个贯穿孔的直径大于或等于25μm且小于或等于75μm。
26.第二十一条条款包括第十八至二十条条款中任一者的玻璃或玻璃陶瓷制品,其中玻璃或玻璃陶瓷制品中的所述至少一个贯穿孔的节距大于或等于60μm且小于或等于800μm。
27.第二十二条条款包括第十八至二十一条条款中任一者的玻璃或玻璃陶瓷制品,其中玻璃或玻璃陶瓷基材中的所述至少一个贯穿孔的深度大于或等于50μm且小于或等于600μm。
28.在以下的详细描述中提出了要求保护的主题的另外的特征和优点,其中的部分特征和优点对本领域的技术人员而言根据所作描述即容易理解,或者通过实施包括以下具体实施方式、权利要求书以及附图在内的本文所述的要求保护的主题而被认识。
29.应当理解的是,前面的一般性描述和以下的具体实施方式都描述了本公开的各个实施方式且都旨在提供用于理解所要求保护的主题的性质和特性的总体评述或框架。所包含的附图供进一步理解本公开,附图被结合在本说明书中并构成说明书的一部分。附图例示了各个实施方式,且与说明书一起用于解释所要求保护的主题的原理和操作。
30.附图简单说明
31.图1示意性地描绘了包含径向裂痕的玻璃或玻璃陶瓷基材中的铜金属化贯穿孔的顶视图;
32.图2示意性描绘了包含径向裂痕的具有多个铜金属化贯穿孔的玻璃或玻璃陶瓷制品的顶视图;
33.图3以图表描绘了在加热包含铜金属化贯穿孔的玻璃或玻璃陶瓷制品期间发生的径向应力和周向应力;
34.图4以图表描绘了加热包含铜金属化贯穿孔的玻璃或玻璃陶瓷制品的周向应力相对于热处理温度;
35.图5a以图表描绘了对于加热包含铜金属化贯穿孔的玻璃或玻璃陶瓷制品,在温度相对于时间中的基本上恒定的加热速率;
36.图5b以图表描绘了对于加热包含铜金属化贯穿孔的玻璃或玻璃陶瓷制品,在温度相对于时间中的可变的加热速率;
37.图6是当在26.0℃/分钟的基本上恒定的加热速率下加热时,具有径向裂痕的包含铜金属化贯穿孔的玻璃或玻璃陶瓷制品的放大照片;
38.图7a是当在13.0℃/分钟的基本上恒定的加热速率下加热时,具有径向裂痕的包含铜金属化贯穿孔的玻璃或玻璃陶瓷制品的50倍放大照片;
39.图7b是当在13.0℃/分钟的基本上恒定的加热速率下加热时,具有径向裂痕的包含铜金属化贯穿孔的玻璃或玻璃陶瓷制品的200倍放大照片;
40.图8a是当在8.7℃/分钟的基本上恒定的加热速率下加热时,具有径向裂痕的包含铜金属化贯穿孔的玻璃或玻璃陶瓷制品的50倍放大照片;
41.图8b是当在8.7℃/分钟的基本上恒定的加热速率下加热时,具有径向裂痕的包含铜金属化贯穿孔的玻璃或玻璃陶瓷制品的500倍放大照片;
42.图9a是根据本文公开和所述的实施方式,当在6.5℃/分钟的加热速率下加热时,不具有径向裂痕的包含铜金属化贯穿孔的玻璃或玻璃陶瓷制品的50倍放大照片;
43.图9b是根据本文公开和所述的实施方式,当在6.5℃/分钟的基本上恒定的加热速
率下加热时,不具有径向裂痕的包含铜金属化贯穿孔的玻璃或玻璃陶瓷制品的200倍放大照片;
44.图10是根据本文公开和所述的实施方式,当在变化的加热速率和2.3℃/分钟的平均加热速率下加热时,不具有径向裂痕的包含铜金属化贯穿孔的玻璃或玻璃陶瓷制品的200倍放大照片;
45.图11以图表描绘了包含铜金属化贯穿孔的玻璃或玻璃陶瓷制品的加热裂痕密度与加热速率的关系;
46.图12a
‑
12c显示了在20.5℃/分钟下加热的铜金属化贯穿孔随着时间形成径向裂痕;及
47.图13以图表描绘了铜突出与退火加热速率的关系。
具体实施方式
48.电子装置中的许多部件需要导电穿过基材的厚度。这使用导电孔来实现,导电孔通常通过在诸如玻璃或玻璃陶瓷基材之类的基材中制造贯穿孔来构建,导电孔的构建是通过计算机数字控制(cnc)钻孔或激光钻孔,然后用诸如例如铜之类的导电金属涂覆和/或填充贯穿孔来进行。在固体填充的导电孔洞的情况中,施加均匀导电层,然后完成电解/伽伐尼(galvanic)镀覆直到贯穿孔得到填充。通过这些方法,形成了具有铜金属化贯穿孔的玻璃或玻璃陶瓷制品。然而,许多过程要求在铜已经填充进入到贯穿孔中之后加热具有铜金属化贯穿孔的玻璃或玻璃陶瓷制品。
49.然而,当加热具有铜金属化贯穿孔的玻璃或玻璃陶瓷制品时,由于玻璃或玻璃陶瓷基体与铜之间的热膨胀系数(cte)失配,产生了热机械问题。在玻璃或玻璃陶瓷中的一种热机械引发失效模式是径向裂痕的形成。径向裂痕在加热处理过程的加热或升温步骤期间形成。不被任何特定理论所局限,认为由于贯穿孔中的铜与玻璃或玻璃陶瓷基体之间的cte失配导致了在玻璃或玻璃陶瓷中的周向方向上具有高的拉伸应力,由于该高的拉伸应力,因此形成了径向裂痕。此cte差异致使高的应力积累,其造成了不同的失效模式,例如玻璃或玻璃陶瓷中的裂痕,空隙,侧壁脱层及更多的失效。
50.防止裂痕形成的惯例包括使用cte匹配更佳的玻璃或玻璃陶瓷组合物,使用环形或保形镀覆的贯穿孔,降低退火温度(经常<300℃,对应于无铅焊料的回流焊温度),较小的孔尺寸,或使用比铜的电导率更低、但与玻璃或玻璃陶瓷有较佳的cte匹配的金属化材料。然而,这些解决方案会限制金属化贯穿孔的应用。例如,并不优选环形孔和较小直径的孔用于高载流应用,例如电源装置,其中需要厚的金属化层。又,对于高频应用,通常使用高二氧化硅含量的玻璃。
51.为了解决上述及其他问题,根据本文公开和所述的实施方式的方法包括:将包含铜金属化贯穿孔的玻璃或玻璃陶瓷制品从第一温度加热至第二温度,其中第一温度大于或等于200℃且小于或等于300℃,及其中第二温度大于或等于350℃且小于或等于450℃,其中在将包含铜金属化贯穿孔的玻璃或玻璃陶瓷制品从第一温度加热至第二温度期间的平均加热速率大于0.0℃/分钟且小于8.7℃/分钟。实施方式还包括玻璃或玻璃陶瓷制品,所述玻璃或玻璃陶瓷制品包含玻璃或玻璃陶瓷基材,所述玻璃或玻璃陶瓷基材包含在厚度方向上穿透玻璃或玻璃陶瓷基材的至少一个贯穿孔,并且包括存在于至少一个贯穿孔中的
铜,其中玻璃或玻璃陶瓷制品不包含径向裂痕。
52.如上论述并参照图1,玻璃或玻璃陶瓷制品100的实施方式包含玻璃或玻璃陶瓷基材110和铜金属化贯穿孔120。铜金属化贯穿孔120是圆柱形且包含在贯穿孔的至少一部分中的铜金属。应理解,根据本文公开和所述的实施方式可使用任何贯穿孔几何结构。此种几何结构包括但不限于圆锥形贯穿孔、截头圆锥形贯穿孔、或收缩的贯穿孔(例如,具有沙漏型形状的贯穿孔)。铜金属化贯穿孔120具有半径“r”。玻璃或玻璃陶瓷基材110与贯穿孔中存在的铜的cte之间的cte失配可致使裂痕130的形成,裂痕130径向方向上从铜金属化贯穿孔120在延伸。在径向方向上从铜金属化贯穿孔120延伸的这些裂痕130在本文指称为径向裂痕。不受任何特定理论所局限,认为当加热包含铜金属化贯穿孔的玻璃或玻璃陶瓷制品100时,玻璃或玻璃陶瓷基材110的相对较低的膨胀限制了存在于铜金属化贯穿孔120中的铜的自由膨胀,使得在玻璃或玻璃陶瓷基材110中累积了高应力并形成径向裂痕。
53.虽然实施方式关于铜金属化贯穿孔,但应理解,本文公开和所述的过程可用在以任何金属材料金属化的贯穿孔上。特别地,因为本文公开和所述的过程涉及与存在于贯穿孔中的材料具有cte失配的玻璃与玻璃陶瓷基材,因此可最大程度地减少或消除在具有以任何金属材料金属化的贯穿孔的玻璃或玻璃陶瓷基材中的径向裂痕。
54.在某些实施方式中,且现在参照图2,玻璃或玻璃陶瓷基材110可包含沿着玻璃或玻璃陶瓷基材110中的直线定位的多个铜金属化贯穿孔120a
‑
102f。在这种构造中,多个径向裂痕130a
‑
130e可能形成于玻璃或玻璃陶瓷基材110中,使得径向裂痕130a
‑
130e横跨相邻铜金属化贯穿孔120a
‑
120f之间的距离。例如,径向裂痕130a可在相邻的铜金属化贯穿孔120a与120b之间延伸,而径向裂痕130b可在相邻的铜金属化贯穿孔120b与120c之间延伸。以此方式,径向裂痕130a
‑
130e可在玻璃或玻璃陶瓷基材110中的铜金属化贯穿孔120a
‑
120f每一者之间横跨。
55.如上所述,当加热玻璃或玻璃陶瓷制品100时,存在于带有铜金属化贯穿孔的玻璃或玻璃陶瓷制品100中的应力可能致使裂痕130形成。可能造成径向裂痕130的这些应力理论上可近似于如下所示,且根据本文公开和所述的实施方式,可开发控制应力及最大程度地减少或消除带有铜金属化贯穿孔的玻璃或玻璃陶瓷制品100中的径向裂痕的方法。
56.因为玻璃或玻璃陶瓷基材110中的铜金属化贯穿孔120通常是圆柱形且被玻璃或玻璃陶瓷基体所围绕,因此玻璃或玻璃陶瓷中的应力可使用lam
é’
s厚/固体壁圆柱等式(lam
é’
s thick/solid wall cylinder equation)来确定,其中平面中应力—径向和周向应力—在玻璃或玻璃陶瓷厚度的中心区是相等但是相反的,如下方等式1所示:
57.σ
r
=
‑
σ
θ
ꢀꢀꢀꢀꢀꢀꢀꢀꢀ
(1)
58.其中σ
r
是径向应力而σ
θ
是周向(或环向)应力。
59.围绕单个铜通孔的玻璃或玻璃陶瓷中的平面中热机械应力可使用以下等式2来计算,并且随后为示例性值:
[0060][0061]
其中α
cu
是铜的cte(16.7ppm/℃);α
玻璃
是玻璃或玻璃陶瓷的cte(0.6ppm/℃);υ
玻璃
和
υ
cu
分别是玻璃或玻璃陶瓷的泊松比(0.26)和铜的泊松比(0.35);r是玻璃或玻璃陶瓷中距离孔的中心的距离。这意味着在玻璃或玻璃陶瓷基材与铜之间的界面处,r是金属化贯穿孔的半径。d
cu
是贯穿孔的直径(50μm);e
cu
和e
玻璃
分别是铜的弹性模量(120gpa)和玻璃或玻璃陶瓷的弹性模量(70gpa);及δt是温度的变化。使用等式2与上文提供的铜和玻璃或玻璃陶瓷的值,可计算在从室温(约25℃)加热至最大温度期间,玻璃或玻璃陶瓷基材中的应力;其中假设铜和玻璃或玻璃陶瓷为弹性材料。计算得出的来自贯穿孔边缘的玻璃或玻璃陶瓷应力呈现在图3中,其中显示出周向与径向应力在数值上是相等的但在方向上相反。在图3中,因为已知裂痕是由于拉伸应力场而形成,因此预期玻璃或玻璃陶瓷中的周向拉伸应力是加热期间形成径向裂痕的主要原因。最大应力发生在通孔边缘,其从贯穿孔边缘起指数地衰减,其中贯穿孔不紧密地邻近另一贯穿孔。
[0062]
上文的等式2可用于确定随温度变化的最大周向拉伸应力值。图4显示了热处理温度(℃)对于周向应力(mpa)的图表。图4中的图表显示,在热处理期间温度的增加造成周向应力基本上线性增加,其显示了形成径向裂痕的可能性随着热处理温度增加而增加。因此,温度越高,越容易发生径向裂痕。
[0063]
使用上文的等式和分析,根据本文公开和所述的实施方式制定用于加热包含铜金属化贯穿孔的玻璃或玻璃陶瓷制品的方法,以最大程度地减少或消除包含铜金属化贯穿孔的玻璃或玻璃陶瓷中的径向裂痕的形成。不被任何特定理论所局限,认为在热处理的高温部分期间使用低平均加热速率容许应力松弛机制活化,使存在于高温下的较高周向应力的影响最小化,从而减少或消除包含铜金属化贯穿孔的玻璃或玻璃陶瓷制品中的径向裂痕形成。
[0064]
现在将描述根据实施方式所述的用于加热包含铜金属化贯穿孔的玻璃或玻璃陶瓷制品的过程。如上所述,使用等式2,确定了包含铜金属化贯穿孔的玻璃或玻璃陶瓷制品中的周向应力—其可能导致径向裂痕的形成—随着热处理温度增加而增加。因此确定,根据实施方式,在用于加热包含铜金属化贯穿孔的玻璃或玻璃陶瓷制品的过程中,存在第一温度,在此温度下径向裂痕形成的可能性变得显著,并且将高于此第一温度的平均加热速率控制为低平均加热速率,从而减少或消除径向裂痕的形成。根据一些实施方式,不需要限制在低于此第一温度的加热速率。因此,可使用任何平均加热速率将包含铜金属化贯穿孔的玻璃或玻璃陶瓷制品加热至第一温度。因此,用于加热包含铜金属化贯穿孔的玻璃或玻璃陶瓷制品的过程的实施方式涉及控制在包含铜金属化贯穿孔的玻璃或玻璃陶瓷制品的温度大于或等于第一温度且小于或等于热处理完成时常所述的第二温度的过程期间的平均加热速率。应理解,本文公开的温度指用于加热包含铜金属化贯穿孔的玻璃或玻璃陶瓷制品的装置(例如烘箱、炉、窑、退火窑、或类似物)的测得的气氛温度。
[0065]
使用此信息,对包含铜金属化贯穿孔的玻璃或玻璃陶瓷制品实施热处理以确定径向裂痕形成的温度。通过各种热处理的目视观测,发现,径向裂痕会形成的可能性在大于或等于200℃的温度时显著增加,例如在温度大于或等于210℃、温度大于或等于220℃、温度大于或等于230℃、温度大于或等于240℃、温度大于或等于250℃、温度大于或等于260℃、温度大于或等于270℃、温度大于或等于280℃、或温度大于或等于290℃时。因此,在根据实施方式的用于加热包含铜金属化贯穿孔的玻璃或玻璃陶瓷制品的过程中,因为在低于第一温度的温度下,径向裂痕形成的可能性很低,所以不需要控制在低于第一温度的温度下的
加热速率。在实施方式中,第一温度大于或等于200℃且小于或等于300℃,例如大于或等于210℃且小于或等于300℃、大于或等于220℃且小于或等于300℃、大于或等于230℃且小于或等于300℃、大于或等于240℃且小于或等于300℃、大于或等于250℃且小于或等于300℃、大于或等于260℃且小于或等于300℃、大于或等于270℃且小于或等于300℃、大于或等于280℃且小于或等于300℃、或大于或等于290℃且小于或等于300℃。在一些实施方式中,第一温度大于或等于200℃且小于或等于290℃,例如大于或等于200℃且小于或等于280℃、大于或等于200℃且小于或等于270℃、大于或等于200℃且小于或等于260℃、大于或等于200℃且小于或等于250℃、大于或等于200℃且小于或等于240℃、大于或等于200℃且小于或等于230℃、大于或等于200℃且小于或等于220℃、或大于或等于200℃且小于或等于210℃。在一些实施方式中,第一温度大于或等于220℃且小于或等于280℃,例如大于或等于225℃且小于或等于275℃,或大于或等于240℃且小于或等于260℃。
[0066]
在从上述的第一温度到通常完成热处理的第二温度中,具有铜金属化贯穿孔的玻璃或玻璃陶瓷制品中的径向裂痕形成的可能性是高的。在实施方式中,第二温度大于或等于350℃且小于或等于450℃,例如,大于或等于360℃且小于或等于450℃、大于或等于370℃且小于或等于450℃、大于或等于380℃且小于或等于450℃、大于或等于390℃且小于或等于450℃、大于或等于400℃且小于或等于450℃、大于或等于410℃且小于或等于450℃、大于或等于420℃且小于或等于450℃、大于或等于430℃且小于或等于450℃、或大于或等于440℃且小于或等于450℃。在一些实施方式中,第二温度大于或等于350℃且小于或等于440℃,例如大于或等于350℃且小于或等于430℃、大于或等于350℃且小于或等于420℃、大于或等于350℃且小于或等于410℃、大于或等于350℃且小于或等于400℃、大于或等于350℃且小于或等于390℃、大于或等于350℃且小于或等于380℃、大于或等于350
°
且小于或等于370℃、或大于或等于350℃且小于或等于360℃。在实施方式中,第二温度大于或等于375℃且小于或等于450℃,例如大于或等于375℃至小于或等于425℃。
[0067]
如上所述,当包含铜金属化贯穿孔的玻璃或玻璃陶瓷制品在大于或等于第一温度且小于或等于裂痕形成的可能性较高的第二温度时,根据本文公开和所述的实施方式的用于加热包含铜金属化贯穿孔的玻璃或玻璃陶瓷制品的方法控制平均加热速率。如本文中所使用,平均加热速率是第二温度与第一温度之间的差除以将包含铜金属化贯穿孔的玻璃或玻璃陶瓷制品从第一温度加热至第二温度所花的时长。因此,如本文中所使用,平均加热速率包括使包含铜金属化贯穿孔的玻璃或玻璃陶瓷制品处于大于或等于第一温度且小于或等于第二温度的温度的任何温度保持。作为一实例,若包含铜金属化贯穿孔的玻璃或玻璃陶瓷制品用10分钟从300℃的第一温度加热至350℃,保持在350℃持续10分钟,然后用10分钟从350℃加热至400℃的第二温度,平均加热速率为3.33℃/分钟(即,)。
[0068]
在实施方式中,从第一温度至第二温度的平均加热速率大于0.0℃/分钟且小于8.7℃/分钟,例如大于0.0℃/分钟且小于或等于8.5℃/分钟、大于0.0℃/分钟且小于或等于8.2℃/分钟、大于0.0℃/分钟且小于或等于8.0℃/分钟、大于0.0℃/分钟且小于或等于7.8℃/分钟、大于0.0℃/分钟且小于或等于7.5℃/分钟、大于0.0℃/分钟且小于或等于7.2℃/分钟、大于0.0℃/分钟且小于或等于7.0℃/分钟、大于0.0℃/分钟且小于或等于6.8℃/分钟、大于0.0℃/分钟且小于或等于6.5℃/分钟、大于0.0℃/分钟且小于或等于6.2℃/分
钟、大于0.0℃/分钟且小于或等于6.0℃/分钟、大于0.0℃/分钟且小于或等于5.8℃/分钟、大于0.0℃/分钟且小于或等于5.5℃/分钟、大于0.0℃/分钟且小于或等于5.2℃/分钟、或大于0.0℃/分钟且小于或等于5.0℃/分钟。在一些实施方式中,从第一温度至第二温度的平均加热速率大于或等于2.0℃/分钟且小于8.7℃/分钟,例如大于或等于2.2℃/分钟且小于8.7℃/分钟、大于或等于2.5℃/分钟且小于8.7℃/分钟、大于或等于2.8℃/分钟且小于8.7℃/分钟、大于或等于2.8℃/分钟且小于8.7℃/分钟、大于或等于3.0℃/分钟且小于8.7℃/分钟。在实施方式中,从第一温度至第二温度的平均加热速率大于或等于2.0℃/分钟且小于或等于6.5℃/分钟,例如大于或等于2.2℃/分钟且小于或等于6.5℃/分钟、大于或等于2.5℃/分钟且小于6.5℃/分钟、大于或等于2.8℃/分钟且小于6.5℃/分钟、或大于或等于3.0℃/分钟且小于6.5℃/分钟。在上述平均加热速率下将包含铜金属贯穿孔的玻璃或玻璃陶瓷制品从第一温度加热至第二温度不致使包含铜金属贯穿孔的玻璃或玻璃陶瓷制品中发生径向裂痕。
[0069]
根据一些实施方式,从第一温度至第二温度的加热速率基本上保持恒定,使得在从第一温度至第二温度的整个温度范围中使用一致的加热速率。如本文中所使用,基本上恒定的加热速率是指通过用于加热包含铜金属贯穿孔的玻璃或玻璃陶瓷制品的装置可控制的加热速率尽可能地保持接近加热速率设定点。例如,可确定在第一温度至第二温度的温度范围中的加热速率应为恒定且设定在6.5℃/分钟。然而,即使打算将加热速率维持在6.5℃/分钟,但是考虑到用于加热包含铜金属贯穿孔的玻璃或玻璃陶瓷制品的装置中的固有的不一致与低效性,加热速率可能降低至例如6.2℃/分钟或增加至例如6.8℃/分。如本文所用,该状况会是“基本上恒定”的加热速率。在一些实施方式中,从第一温度至第二温度的加热速率是可变的。如本文中所使用,“可变的”加热速率是指在从第一温度至第二温度的温度范围中有意地改变加热速率。具有可变的加热速率的实施方式的一个实例会是包含铜金属贯穿孔的玻璃或玻璃陶瓷制品从300℃的第一温度以6.5℃/分钟的加热速率加热至350℃的温度,然后有意地从350℃以2.3℃/分钟的加热速率加热至400℃的第二温度。
[0070]
虽然在实施方式中未限制包含铜金属贯穿孔的玻璃或玻璃陶瓷制品在处于从室温(约25℃)至第一温度的温度时的平均加热速率,但在一些实施方式中,也将包含铜金属贯穿孔的玻璃或玻璃陶瓷制品在处于从室温(约25℃)至第一温度的温度时的平均加热速率保持低的平均加热速率,以助于确保不形成径向裂痕。因此,在实施方式中,从室温至第一温度的平均加热速率大于0.0℃/分钟且小于8.7℃/分钟,例如,大于0.0℃/分钟且小于或等于8.5℃/分钟、大于0.0℃/分钟且小于或等于8.2℃/分钟、大于0.0℃/分钟且小于或等于8.0℃/、大于0.0℃/分钟且小于或等于7.8℃/、大于0.0℃分钟且小于或等于7.5℃/分钟、大于0.0℃/分钟且小于或等于7.2℃/分钟、大于0.0℃/分钟且小于或等于7.0℃/分钟、大于0.0℃/分钟且小于或等于6.8℃/分钟、大于0.0℃/分钟且小于或等于6.5℃/分钟、大于0.0℃/分钟且小于或等于6.2℃/分钟、大于0.0℃分钟且小于或等于6.0℃/分钟、大于0.0℃/分钟且小于或等于5.8℃/、大于0.0℃/分钟且小于或等于5.5℃/分钟、大于0.0℃分钟且小于或等于5.2℃/分钟、或大于0.0℃分钟且小于或等于5.0℃/分钟。在某些实施方式中,从室温至第一温度的平均加热速率大于或等于1.0℃/分钟且小于8.7℃/分钟,例如,大于或等于2.0℃/分钟且小于8.7℃/分钟、大于或等于2.5℃/分钟且小于8.7℃/分钟、大于或等于2.8℃/分钟且小于8.7℃/分钟、大于或等于2.8℃/分钟且小于8.7℃/分钟、大于或
等于3.0℃/分钟且小于8.7℃/分钟。在实施方式中,从室温至第一温度的平均加热速率大于或等于1.0℃/分钟且小于或等于6.5℃/分钟,例如,大于或等于2.0℃/分钟且小于或等于6.5℃/分钟、大于或等于2.2℃/分钟且小于6.5℃/分钟、大于或等于2.5℃/分钟且小于6.5℃/分钟、大于或等于2.7℃/分钟且小于6.5℃/分钟、或大于或等于3.0℃/分钟且小于6.5℃/分钟。
[0071]
如上所述,将包含铜金属化贯穿孔的玻璃或玻璃陶瓷制品从第一温度加热至第二温度的过程可包括各种温度保持,此时温度保持恒定达一段时间。不被任何特定理论所局限,认为通过将包含铜金属化贯穿孔的玻璃或玻璃陶瓷制品保持在恒定温度,在温度保持期间发生松弛,且包含铜金属化贯穿孔的玻璃或玻璃陶瓷制品中的应力可减小。因此,若在发生裂痕形成之前执行温度保持,由温度保持造成的松弛可充分降低包含铜金属化贯穿孔的玻璃或玻璃陶瓷制品中的应力,以至于无裂痕形成。此外,温度维持可用于第一温度和第二温度中的一者或多者以容许松弛包含铜金属化贯穿孔的玻璃或玻璃陶瓷制品中的应力。
[0072]
在实施方式中,包含铜金属化贯穿孔的玻璃或玻璃陶瓷制品可保持在第一温度达一段时间,此段时间大于或等于十(10)分钟且小于或等于120分钟,例如,大于或等于十五(15)分钟且小于或等于120分钟、大于或等于三十(30)分钟且小于或等于120分钟、大于或等于四十五(45)分钟且小于或等于120分钟、大于或等于六十(60)分钟且小于或等于120分钟、大于或等于七十五(75)分钟且小于或等于120分钟、大于或等于九十(90)分钟且小于或等于120分钟、或大于或等于105分钟且小于或等于120分钟。在实施方式中,包含铜金属化贯穿孔的玻璃或玻璃陶瓷制品可保持在第一温度达一段时间,此段时间大于或等于十(10)分钟且小于或等于105分钟,例如大于或等于十(10)分钟且小于或等于九十(90)分钟、大于或等于十(10)分钟且小于或等于七十五(75)分钟、大于或等于十(10)分钟且小于或等于六十(60)分钟、大于或等于十(10)分钟且小于或等于四十五(45)分钟、大于或等于十(10)分钟且小于或等于三十(30)分钟、或大于或等于十(10)分钟且小于或等于十五(15)分钟。
[0073]
在实施方式中,包含铜金属化贯穿孔的玻璃或玻璃陶瓷制品可保持在第二温度达一段时间,此段时间大于或等于十(10)分钟且小于或等于120分钟,例如大于或等于十五(15)分钟且小于或等于120分钟、大于或等于三十(30)分钟且小于或等于120分钟、大于或等于四十五(45)分钟且小于或等于120分钟、大于或等于六十(60)分钟且小于或等于120分钟、大于或等于七十五(75)分钟且小于或等于120分钟、大于或等于九十(90)分钟且小于或等于120分钟、或大于或等于105分钟且小于或等于120分钟。在实施方式中,包含铜金属化贯穿孔的玻璃或玻璃陶瓷制品可保持在第二温度达一段时间,此段时间大于或等于十(10)分钟且小于或等于105分钟,例如大于或等于十(10)分钟且小于或等于九十(90)分钟、大于或等于十(10)分钟且小于或等于七十五(75)分钟、大于或等于十(10)分钟且小于或等于六十(60)分钟、大于或等于十(10)分钟且小于或等于四十五(45)分钟、大于或等于十(10)分钟且小于或等于三十(30)分钟、或大于或等于十(10)分钟且小于或等于十五(15)分钟。
[0074]
在实施方式中,包含铜金属化贯穿孔的玻璃或玻璃陶瓷制品可保持在第一温度与第二温度之间的恒定温度达一段时间,此段时间大于或等于十(10)分钟且小于或等于120分钟,例如大于或等于十五(15)分钟且小于或等于120分钟、大于或等于三十(30)分钟且小于或等于120分钟、大于或等于四十五(45)分钟且小于或等于120分钟、大于或等于六十(60)分钟且小于或等于120分钟、大于或等于七十五(75)分钟且小于或等于120分钟、大于
或等于九十(90)分钟且小于或等于120分钟、或大于或等于105分钟且小于或等于120分钟。在实施方式中,包含铜金属化贯穿孔的玻璃或玻璃陶瓷制品可保持在第一温度与第二温度之间的恒定温度达一段时间,此段时间大于或等于十(10)分钟且小于或等于105分钟,例如大于或等于十(10)分钟且小于或等于九十(90)分钟、大于或等于十(10)分钟且小于或等于七十五(75)分钟、大于或等于十(10)分钟且小于或等于六十(60)分钟、大于或等于十(10)分钟且小于或等于四十五(45)分钟、大于或等于十(10)分钟且小于或等于三十(30)分钟、或大于或等于十(10)分钟且小于或等于十五(15)分钟。
[0075]
虽然本文公开的过程可用在包含任何尺寸的铜金属化贯穿孔的玻璃或玻璃陶瓷制品上,但本文公开的过程可特别地适用于包含相对较小的铜金属化贯穿孔的玻璃或玻璃陶瓷制品。在实施方式中,铜金属化贯穿孔的直径可以大于或等于25μm且小于或等于75μm,例如大于或等于30μm且小于或等于70μm、大于或等于35μm且小于或等于70μm、大于或等于40μm且小于或等于70μm、大于或等于45μm且小于或等于70μm、大于或等于50μm且小于或等于70μm、大于或等于55μm且小于或等于70μm、大于或等于60μm且小于或等于70μm、或大于或等于65μm且小于或等于70μm。在实施方式中,铜金属化贯穿孔的直径可以大于或等于25μm且小于或等于65μm,例如大于或等于25μm且小于或等于60μm、大于或等于25μm且小于或等于55μm、大于或等于25μm且小于或等于50μm、大于或等于25μm且小于或等于45μm、大于或等于25μm且小于或等于40μm、大于或等于25μm且小于或等于35μm、或大于或等于25μm且小于或等于30μm。在实施方式中,铜金属化贯穿孔的直径可以大于或等于35μm且小于或等于65μm,例如大于或等于40μm且小于或等于60μm。
[0076]
应理解,本文公开和所述的过程可使用于具有任何节距的贯穿孔。具体地,通过根据本文公开和所述的实施方式加热玻璃或玻璃陶瓷制品,无论贯穿孔的节距为何,皆可最大程度地减少或消除径向裂痕。另外,基材中的贯穿孔的节距会取决于贯穿孔的直径。然而,在某些实施方式中,当贯穿孔的直径为约50μm时,铜金属化贯穿孔可具有大于或等于60μm且小于或等于800μm的节距,例如大于或等于100μm且小于或等于750μm、大于或等于150μm且小于或等于700μm、大于或等于200μm且小于或等于650μm、大于或等于250μm且小于或等于600μm、大于或等于300μm且小于或等于550μm、大于或等于350μm且小于或等于500μm、或大于或等于400μm且小于或等于450μm。在实施方式中,铜金属化贯穿孔可具有大于或等于60μm且小于或等于140μm的节距,例如大于或等于60μm且小于或等于130μm、大于或等于60μm且小于或等于120μm、大于或等于60μm且小于或等于110μm、大于或等于60μm且小于或等于100μm、大于或等于60μm且小于或等于90μm、大于或等于60μm且小于或等于80μm、或大于或等于60μm且小于或等于70μm。
[0077]
应理解,本文公开和所述的过程可使用于具有任何深度的贯穿孔。具体地,通过根据本文公开和所述的实施方式加热玻璃或玻璃陶瓷制品,无论贯穿孔的深度为何,皆可最大程度地减少或消除径向裂痕。然而,在一些实施方式中,铜金属化贯穿孔可具有大于或等于50μm且小于或等于600μm的深度,例如大于或等于75μm且小于或等于575μm、大于或等于100μm且小于或等于550μm、大于或等于125μm且小于或等于525μm、大于或等于150μm且小于或等于500μm、大于或等于175μm且小于或等于475μm、大于或等于200μm且小于或等于450μm、大于或等于225μm且小于或等于425μm、大于或等于250μm且小于或等于400μm、大于或等于275μm且小于或等于375μm、或大于或等于300μm且小于或等于350μm。在实施方式中,铜金
属化贯穿孔可具有大于或等于200μm且小于或等于400μm的深度,例如大于或等于200μm且小于或等于375μm、大于或等于200μm且小于或等于350μm、大于或等于200μm且小于或等于325μm、大于或等于200μm且小于或等于300μm、大于或等于200μm且小于或等于275μm、大于或等于200μm且小于或等于250μm、或大于或等于200μm且小于或等于225μm。
[0078]
任何玻璃或玻璃陶瓷材料可用作根据本文公开和所述的实施方式的包含铜金属化贯穿孔的玻璃或玻璃陶瓷制品的玻璃或玻璃陶瓷基材。具体地,通过根据本文公开和所述的实施方式加热玻璃或玻璃陶瓷制品,无论玻璃或玻璃陶瓷的组成为何,皆可最大程度地减少或消除径向裂痕。然而,如上所述,当用作包含铜金属化贯穿孔的玻璃或玻璃陶瓷制品的玻璃或玻璃陶瓷基材的玻璃或玻璃陶瓷材料与铜的cte具有高cte失配时,实施方式的过程是特别有用的。因此,在一些实施方式中,包含铜金属化贯穿孔的玻璃或玻璃陶瓷制品的玻璃或玻璃陶瓷基材包含大量的二氧化硅。在一些实施方式中,基材包含大于或等于50摩尔%的二氧化硅,例如大于或等于55摩尔%的二氧化硅、大于或等于60摩尔%的二氧化硅、大于或等于65摩尔%的二氧化硅、大于或等于70摩尔%的二氧化硅、大于或等于75摩尔%的二氧化硅、大于或等于80摩尔%的二氧化硅、大于或等于85摩尔%的二氧化硅、大于或等于90摩尔%的二氧化硅、大于或等于95摩尔%二氧化硅、或约100摩尔%的二氧化硅。在实施方式中,基材包含至少90重量%的二氧化硅。
[0079]
当以50倍放大倍数或更大倍数观察时,根据本文公开和所述的过程制成的包含铜金属化贯穿孔的玻璃或玻璃陶瓷制品在热处理之后会是无径向裂痕。
[0080]
实施例
[0081]
将通过接下来的实施例进一步阐明实施方式。
[0082]
使用在包含至少90重量%的二氧化硅的玻璃基材中由下至上电镀而充分填充的圆柱形铜金属化贯穿孔。在通过由下至上电镀,用铜充分填充贯穿孔之后,使用化学机械抛光(cmp)以移除铜过载。之后将基材切割成14mm
×
14mm的晶片尺寸,得到196mm2的晶片面积。每个晶片含有四列铜金属化贯穿孔阵列,并且合计有952个铜金属化贯穿孔。铜金属化贯穿孔直径、节距和深度分别为50μm、100μm与300μm。接着采用不同的加热速率,使样品经受退火处理至420℃的最大温度,然后使样品炉冷却至室温(约25℃)。图5a以图表描绘了具有基本上恒定的加热速率,即,6.5℃/分钟、8.7℃/分钟、13.0℃/分钟、及26.0℃/分钟的四个样品的退火分布曲线。图5b以图表描绘了具有可变动的热速率的退火分布曲线,其中平均加热速率为2.3℃/分钟。因此,研究了从2.3℃/分钟至26.0℃/分钟的加热速率而其完整细节呈现在表1中。
[0083]
表1
[0084][0085]
除了平均加热速率为2.3℃/分钟的测试状况(其具有60分钟持续时间的恒定温度保持)之外,对于所有的测试状况使用在420℃下30分钟的持续时间的恒定温度保持。通过炉冷却达成的冷却不变动且花费约120分钟。
[0086]
在退火处理之后,执行晶片的光学检查以确定升温速率对于径向裂痕形成的相依性。对于不同的升温速率,对晶片上的裂痕数目进行计数并使用等式3计算各测试状况的裂痕密度。通过光学显微镜以50倍至500倍放大倍数观察裂痕。每种加热速率使用一个样品来研究。
[0087][0088]
为了确定裂痕引发时的温度,进行原位温度依赖性研究。在此研究中,以20.5℃/分钟的升温速率将样品加热至高达420℃。通过使用原位成像系统,每10秒获得随温度变化的相同特定组的通孔的图像,之后对其进行分析以确定裂痕引发时的温度。
[0089]
此外,使用zygo拓扑学测量方法来确定关于所使用的退火加热速率有多少铜突出出现。基于此测量,确定突出的铜的高度。
[0090]
图6呈现了具有26.0℃/分钟的加热/升温速率的样品的50倍光学图像。观察到使用此快速加热速率造成样品中裂痕的形成。由于发现裂痕从相邻的铜金属化贯穿孔连结,致使产生径向裂痕的网络,径向裂痕显示为形成全部穿过样品的裂痕链。在14mm
×
14mm晶片上的径向裂痕的总数目是375个裂痕;产生1.91个裂痕/mm2的裂痕密度。
[0091]
将加热速率变慢至13.0℃/分钟和8.7℃/分钟继续造成径向裂痕的形成。在13.0℃/分钟的加热速率下形成的裂痕显示在图7a(50倍)和图7b(200倍)中。在8.7℃/分钟的加热速率下形成的裂痕显示在图8a(50倍)和图8b(500倍)中。然而,观察到裂痕数目的显著持续下降。发现13.0℃/分钟的加热速率的裂痕总数仅为8个裂痕,而8.7℃/分钟的加热速率的裂痕总数仅为4个裂痕;分别产生了0.04个裂痕/mm2和0.02个裂痕/mm2的裂痕密度。
[0092]
然而,在6.5℃/分钟的加热速率下,没有观察到裂痕,如图9a(50倍)与图9b(200倍)所示。类似地,对于使用2.3℃/分钟的平均加热速率的可变加热速率退火的样品,没有观察到裂痕,如图10图(200倍)所示。
[0093]
下表2总结了上述测试的结果。
[0094]
表2
[0095][0096]
根据表2呈现的总结结果,观察到对于低于8.7℃/分钟的加热速率,径向裂痕在最小值,而在加热速率≥8.7℃/分钟时,晶片上的径向裂痕的数目随着增长的加热而增加。然而,在加热速率低于8.7℃/分钟时,裂痕数目是最小的且最终在加热速率≤6.5℃/分钟时,不存在裂痕。这清楚地指示径向裂痕的形成是时间相依的现象。
[0097]
此外,计算裂痕密度,如表2所示并以图表呈现在图11。发现裂痕密度随着所使用的退火加热速率指数地增长。图11清楚地指示径向裂痕是速率相依的现象。此也显示径向裂痕受应力的驱动作用,由铜与其周围的玻璃基体的cte失配而产生。因此,加热速率≤6.5℃/分钟时不存在裂痕的情况说明,在铜金属化贯穿孔中充分激活了速率控制的应力松弛机制。另外,因为在低于8.7℃/分钟的加热速率下观察到的裂痕的数目有限,这意味着对于<8.7℃/分钟的加热速率,铜金属化贯穿孔中的应力较低,致使在玻璃中得到较低的诱导应力,该诱导应力低于在玻璃中引发裂痕所需的阈值临界应力值。
[0098]
图12a
‑
12c是铜金属化贯穿孔的原位温度相依图像。如可见到的,在317℃,没有观察到径向裂痕(图12a)。然而,在10秒后,观察到裂痕左起第三个铜金属化贯穿孔扩展,这对应于321℃的温度(图12b)。进一步增加温度造成裂痕的成长,直到60秒后裂痕最终连接至相邻的铜金属化贯穿孔(即,左起第四个铜金属化贯穿孔),如图12c所示。虽然最初在321℃观察到径向裂痕,由于测试方案的设定,径向裂痕可在较低的温度发展。例如,仅每10秒来捕捉图像。
[0099]
为了更完整地理解应力松弛机制的活动,通过在关于退火加热速率的退火之后测量铜突出来完成进一步的实验研究,如图13所呈现。铜突出是非弹性平面外变形。由于铜与周围玻璃基材的cte失配导致在铜中积累高压缩应力,因此在加热期间发生该铜突出。铜突出是塑性变形的铜及小丘形成的组合。由于达到铜的屈服强度,因此发生塑性变形,屈服强度随着温度升高而降低。另一方面,小丘形成是铜晶粒因为晶界滑动(gbs)现象而优先平面外位移。gbs是应力松弛机制,该应力松弛机制是一种扩散控制机制,导致一个晶粒在另一个晶粒上平行于晶界界面近似平移。由于在平移期间晶粒的垂直位移,gbs致使铜突出的形成。
[0100]
在图13中,测量出随着加热时间增加,铜突出高度增加,换言之,铜突出随着减少加热速率而增加。例如,在26.0℃/分钟的加热速率下,cu突出的量经测量为400nm,然而,当使用6.5℃/分钟的加热速率时,铜突出高度经测量为约1100nm。图13显示了铜突出对所使用的退火加热速率的强相依性。基于表2与图13,可推论出铜突出的增加造成形成的径向裂痕的数目的减少。此是由于随着增加的加热时间或减少的加热速率使得应力松弛机制的活
动增加。gbs已知为速率控制的应力松弛机制,其也伴随着微空隙的形成,因此,其活动随着较低的退火加热速率而增加。这意味着当使用<8.7℃/分钟(例如≤6.5℃/分钟)的升温速率时,gbs的活动与塑性变形将铜中的累积应力充分松弛到低于形成径向裂痕所需的临界应力阈值。
[0101]
如本文所用,术语“约”指量、尺寸、公式、参数和其他数量和特征不是精确的且无需精确的,而可按照要求是大致的和/或更大或者更小,如反映公差、转化因子、四舍五入、测量误差等,以及本领域技术人员所知的其他因子。当使用术语“约”来描述范围的值或端点时,应理解本公开包括所参考的具体值或者端点。无论说明书中的范围的数值或端点是否使用“约”列举,范围的数值或端点旨在包括两种实施方式:一种用“约”修饰,另一种未用“约”修饰。还应理解,每个范围的端点在与另一个端点有关及独立于另一个端点时都是重要的。
[0102]
对本领域的技术人员显而易见的是,可以对本文所述的实施方式进行各种修改和变动而不偏离要求保护的主题的精神和范围。因此,本说明书旨在涵盖本文所述的各个实施方式的修改和变化形式,条件是这些修改和变化形式落入所附权利要求及其等同内容的范围之内。