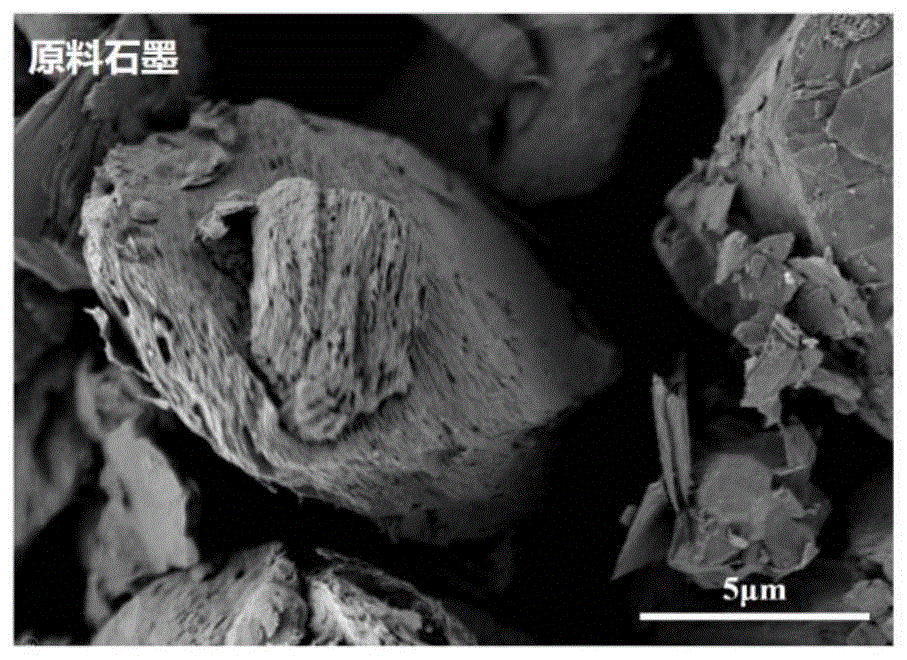
本发明属于石墨烯
技术领域:
,具体涉及一种机械剥离制备石墨烯的方法及其应用。
背景技术:
:石墨烯,一种碳结构材料,碳原子以sp2杂化形式排列成平面二维蜂窝状结构,被认为是世界上最薄的材料。特殊的结构赋予石墨烯优异的光学、电学、力学等特性,可应用于防腐涂层、导热涂层、导电添加剂等众多领域,是一种未来具有革命性的新材料。石墨烯的制备方法可以分为两大类:剥离制备与原位生成。剥离制备是以石墨为原料,在力的作用下,对石墨进行逐层剥离。这种力可以是机械力、化学力、甚至是流体、气体所产生的力。第一片石墨烯就是由英国的曼切斯特大学的两位科学家通过胶带在高定向热解石墨上剥离得到,可见胶黏所产生的力也足以从石墨上剥离出石墨烯,因这一创举,两位科学家共同获得了2010年诺贝尔物理学奖。原位生成石墨烯指碳源(烷、烯烃等碳化物)经高温裂解,在基面上生长出石墨烯。典型制备方法如:气相化学沉积(cvd)、焦耳闪蒸技术(fjh)。cvd法所制备的石墨烯质量高、片层薄、尺寸可控,但由于制备成本高、石墨烯难以转移出基面等问题限制其后端应用的开发。相关技术公开了一种通过粘性机械剪切剥离制备石墨烯的方法。该方法是将石墨原料分散于粘性溶液中,通过胶粘性溶液的粘性剪切力,在搅拌过程中将石墨逐层剥离制备石墨烯。然而所述的粘性溶液的主体成分为水溶性聚合物,为了使粘性溶液具有较好的粘性,通常需要添加大量的水溶性聚合物,从而导致石墨逐层剥离成石墨烯后,难以从粘性溶液中直接分离出来,需要大量的水清洗或高温热解去除非石墨烯成分。该石墨烯的制备方法降低了制备成本,但是增加了石墨烯从粘性物质中提取的难度和处理成本,不利与规模化生产。相关技术公开了一种快速制备高质量石墨烯的方法。该方法是将石墨粉与受热后能完全分解成气体的固态插层剂混合球磨并适当加热插层,然后通过微波加热。插层剂受热后分解气体,气体分子渗入石墨片层中,并克服层间范德华力,使石墨剥离。该方法制备过程简单、制造成本低,但石墨层间距为0.335nm,加热固体插层剂生成的气体分子只能少部分渗入石墨层间,无法实现有效的剥离。通过该方法所剥离的石墨烯质量不稳定、产率低,不利于大范围推广。技术实现要素:本发明旨在至少解决上述现有技术中存在的技术问题之一。为此,本发明提出一种实施简便、绿色经济的机械剥离制备石墨烯的方法及其应用。根据本发明的一个方面,提出了一种机械剥离制备石墨烯的方法,包括以下步骤:(1)将石墨原料分散于泡沫剂水溶液中,得到石墨预分散液;(2)将所述石墨预分散液进行研磨,再通过水洗、离心分级,即得所述石墨烯;所述泡沫剂水溶液包括以下组分:α-烯基磺酸钠、脂肪醇聚氧乙烯醚硫酸钠、椰子油二乙醇基酰胺、聚乙二醇和水。在本发明的一些实施方式中,所述泡沫剂水溶液的组分按以下重量份计:α-烯基磺酸钠1-10份、脂肪醇聚氧乙烯醚硫酸钠1-10份、椰子油二乙醇基酰胺5~15份、聚乙二醇10~20份和水60~80份。在本发明的一些实施方式中,所述聚乙二醇的分子量为2000-6000。在本发明的一些实施方式中,所述石墨原料和泡沫剂水溶液的固液比为10-15mg/ml。在本发明的一些实施方式中,所述石墨原料为天然鳞片石墨、微晶石墨、氧化石墨、可膨胀石墨、人造石墨或高定向热解石墨中的至少一种。在本发明的一些实施方式中,所述离心分级的过程为:在离心速度1000-3000rmp下处理1-10min获得石墨烯上层液。离心分级可以去除非石墨烯部分。在本发明的一些实施方式中,所述研磨采用砂磨机,所述砂磨机的搅拌速度为500-2000rmp。砂磨机操作简单,可移植性高。在本发明的一些实施方式中,所述研磨可以采用球磨机。在本发明的一些实施方式中,所述砂磨机的研磨时间为0.1-10h。在本发明的一些实施方式中,所述砂磨机的研磨介质的粒径为0.3-3mm,填充量为70-80%。在本发明的一些实施方式中,所述砂磨机的温度为30-80℃。本发明还提供所述方法在制备催化剂或电池活性物质中的应用。根据本发明的一种优选的实施方式,至少具有以下有益效果:1、本发明采用石墨为原料,石墨浸润于泡沫剂水溶液中,然后进行研磨,研磨设备的高速搅拌作用,带动研磨介质高速运动从而对石墨产生冲击、磨擦和剪切力。同时,在高速搅拌下,泡沫剂在封闭的研磨腔中产生大量稳定、细腻的泡沫,大量的泡沫可产生推挤作用,并支撑石墨,增大石墨与研磨介质的接触面,从而达到很好的剥离效果。2、本发明配置的泡沫剂是由多种表面活性剂组成的复配体系,其泡沫性能优于单一表面活性剂,可以产生大量稳定的泡沫,这是普通表面活性剂所达不到的。3、本发明以纯物理的方式进行制备,不涉及化学氧化还原过程,最大限度的保留了石墨的本征结构,获得的石墨烯片层薄、缺陷少、且具有一定分散稳定性。4、本发明制备过程简单,原料来源广泛,成本低,对环境污染小,所制备的石墨烯易从基体中分离,使用能提供连续剪切力的高速研磨设备,实现石墨烯连续化、规模化制备。附图说明下面结合附图和实施例对本发明做进一步的说明,其中:图1为本发明实施例1的原料石墨的sem形貌图;图2为本发明实施例1制备的石墨烯的sem形貌图;图3为本发明实施例1制备的石墨烯的tem图;图4为本发明实施例1制备的石墨烯片层边缘的tem图;图5为本发明实施例1制备的石墨烯与原料石墨的xrd衍射图;图6为本发明实施例1制备的石墨烯raman谱图;图7为本发明实施例1制备的石墨烯在水/异丙醇混合溶剂中的分散效果图;图8为本发明对比例1制备的石墨烯的sem形貌图。具体实施方式以下将结合实施例对本发明的构思及产生的技术效果进行清楚、完整地描述,以充分地理解本发明的目的、特征和效果。显然,所描述的实施例只是本发明的一部分实施例,而不是全部实施例,基于本发明的实施例,本领域的技术人员在不付出创造性劳动的前提下所获得的其他实施例,均属于本发明保护的范围。实施例1本实施例制备了一种石墨烯,具体过程为:(1)将α-烯基磺酸钠、脂肪醇聚氧乙烯醚硫酸钠、椰子油二乙醇基酰胺、聚乙二醇5000、水按照质量比为4:4:8:15:69配置泡沫剂水溶液;(2)将人造石墨均匀预分散于上述配置的泡沫剂水溶液中,获得人造石墨预分散液,其浓度为10mg/ml;(3)将人造石墨预分散液加入棒销砂磨机中,研磨介质粒径0.5mm,填充量80%,搅拌速度1500rmp,搅拌时间2h;(4)通过水洗,并在离心速度为1000rmp下处理10min获得石墨烯上层液,即得石墨烯。从图1所示原料石墨的sem形貌可以观察到,人造石墨出现明显的石墨堆叠结构,其厚度接近6μm,可以称其为块体或颗粒材料。经上述方法剥离后得到如图2所示的石墨烯,石墨厚度明显减薄,其厚度达到纳米级别,可作为纳米材料,加上特殊的二维导电性,使其成为催化剂、活性物质的优良载体。进一步探究其厚度大小,通过对剥离的石墨烯片进行tem分析,如图3所示,并对石墨烯边缘进行局部放大,如图4所示,可以发现石墨烯晶格条纹在3.8nm,表明其厚度值小于5nm。石墨沿c轴方向的堆叠为002晶面,对应xrd图谱(图5)在26.4°左右,具有非常强的衍射峰。经过剥离后,石墨沿c轴方向堆叠的结构被破坏,片层减薄,表现出图三所示的26.4°的弱峰。石墨经砂磨剥离后,产生的缺陷值可以使用raman进行分析,其结果如图6所示,经该方案剥离的石墨烯,其缺陷浓度id/ig为0.2326,略大于原料(id/ig<0.1),但小于氧化还原法制备的石墨烯(id/ig>0.5)。对剥离后的石墨烯进行分散性测试,如图7所示,通过超声处理获得1mg/ml的石墨烯分散液(水/异丙醇),将其静置一周后,容器倒置,观察容器底部沉淀,可以发现,静置7天后,石墨烯仍保持良好分散性,容器底部仅有少量石墨烯,这是因为石墨烯片层较薄,可较稳定的分散在与自身表面张力相匹配的溶剂当中。上述结果表明人造石墨经本实施例的方案可得到有效剥离,获得片层薄、缺陷少、且具有一定分散稳定性的石墨烯。实施例2本实施例制备了一种石墨烯,具体过程为:(1)将α-烯基磺酸钠、脂肪醇聚氧乙烯醚硫酸钠、椰子油二乙醇基酰胺、聚乙二醇4000、水按照质量比为5:2.5:7.5:15:70配置泡沫剂水溶液;(2)将鳞片石墨均匀预分散于上述配置的泡沫剂水溶液中,获得鳞片石墨预分散液,其浓度为10mg/ml;(3)将鳞片石墨预分散液加入棒销砂磨机中,研磨介质粒径0.3mm,填充量80%,搅拌速度1500rmp,搅拌时间2h;(4)通过水洗,并在离心速度为2000rmp下处理7min获得石墨烯上层液,即得石墨烯。实施例3本实施例制备了一种石墨烯,具体过程为:(1)将α-烯基磺酸钠、脂肪醇聚氧乙烯醚硫酸钠、椰子油二乙醇基酰胺、聚乙二醇3000、水按照质量比为3:2:5:15:75配置泡沫剂水溶液;(2)将可膨胀石墨均匀预分散于上述配置的泡沫剂水溶液中,获得可膨胀石墨预分散液,其浓度为10mg/ml;(3)将可膨胀石墨预分散液加入棒销砂磨机中,研磨介质粒径0.8mm,填充量80%,搅拌速度1000rmp,搅拌时间3h;(4)通过水洗,并在离心速度为2500rmp下处理5min获得石墨烯上层液,即得石墨烯。实施例4本实施例制备了一种石墨烯,具体过程为:(1)将α-烯基磺酸钠、脂肪醇聚氧乙烯醚硫酸钠、椰子油二乙醇基酰胺、聚乙二醇4000、水按照质量比为3:2:5:15:75配置泡沫剂水溶液;(2)将微晶石墨均匀预分散于上述配置的泡沫剂水溶液中,获得微晶石墨预分散液,其浓度为10mg/ml;(3)将微晶石墨预分散液加入棒销砂磨机中,研磨介质粒径2mm,填充量80%,搅拌速度1000rmp,搅拌时间4h;(4)通过水洗,并在离心速度为3000rmp下处理5min获得石墨烯上层液,即得石墨烯。对比例1本对比例制备了一种石墨烯,与实施例1的区别在于泡沫剂水溶液的组成不同,具体过程为:(1)将α-烯基磺酸钠、水按照质量比为4:96配置泡沫剂水溶液;(2)将人造石墨均匀预分散于上述配置的泡沫剂水溶液中,获得人造石墨预分散液,其浓度为10mg/ml;(3)将人造石墨预分散液加入棒销砂磨机中,研磨介质粒径0.5mm,填充量80%,搅拌速度1500rmp,搅拌时间2h;(4)通过水洗,并在离心速度为1000rmp下处理10min获得石墨烯上层液,即得石墨烯。对比例1与实施例1最大区别在于泡沫剂水溶液液组分不同,实施例1中的泡沫水分散液组分:椰子油二乙醇基酰胺、聚乙二醇5000具有增稠及泡沫稳定作用。由于对比例1泡沫剂水溶液缺少高分子增稠及泡沫稳定作用,所产生的泡沫不稳定、容易破裂,造成机械剥离效果差,石墨烯得率低。进一步的观察对比例1中制备的石墨烯sem形貌图,可以发现所剥离的石墨烯依然保持较厚的片层,其片层厚度在10-100nm,与实施例1制备的石墨烯存在明显差别。跟据石墨烯的定义及分类,可认为对比例1所制备的石墨烯为石墨烯纳米片或石墨微片。相应的,系统对比了对比例1与石墨原料、实施例1中的石墨烯的关键指标,其结果如表1所示:表1得率bet(m2/g)id/ig厚度(nm)石墨原料02.60.035-10μm对比例110%13.50.1210-100nm实施例165%80.50.235-10nm由表1可以看出,由于对比例1的泡沫剂水溶液缺少发泡助剂、增稠剂、泡沫稳定剂,所产生的泡沫不稳定,细腻度不够,造成所剥离的石墨烯在得率、厚度、形貌上均不如实施例1的石墨烯。对比例1的结果表明,泡沫剂水溶液为单组分、具有一定发泡作用的表面活性剂时,虽然可以产生泡沫,但泡沫不稳定、容易破裂,造成石墨机械剥离效果差。本发明通过复配的方式,使泡沫稳定、细腻,并且保持表面活性剂的作用,从而增益石墨的机械剥离效果。上面结合附图对本发明实施例作了详细说明,但是本发明不限于上述实施例,在所属
技术领域:
普通技术人员所具备的知识范围内,还可以在不脱离本发明宗旨的前提下作出各种变化。此外,在不冲突的情况下,本发明的实施例及实施例中的特征可以相互组合。当前第1页12