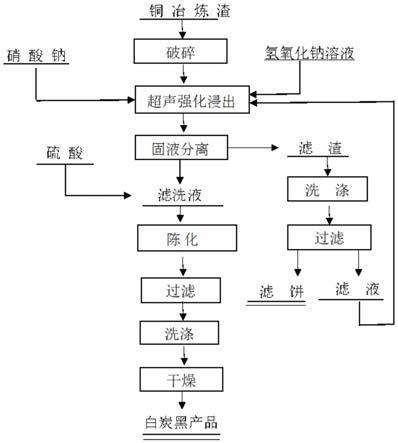
1.本发明涉及工业固体废弃物综合利用领域,具体涉及一种超声强化分离铜冶炼炉渣中的硅和铁并利用硅制备白炭黑的方法。
背景技术:2.铜冶炼渣是铜冶金行业中的一种主要的大宗固体废弃物,因组成结构复杂,综合利用率极低。多年来,冶金企业一直将铜冶炼渣堆弃于露天环境中,不但占用大量的土地资源,渣中砷铅等有毒有害元素和镍钴等重金属,也会随着雨水的冲蚀及地表径流而进入地表水系和土壤中,从而对水体、土壤及农作物产生污染。从1996年以来,我国一直是全球最大的有色金属生产国,但冶金原料中的金属含量往往不高,且常常同铅、砷等有毒元素伴生或者共生,冶炼过程中也需配入大量氧化钙、二氧化硅等熔剂,因此冶金炉渣的产量巨大。2020年,精炼铜的生产量达1003万吨,每生产一吨精炼铜就会产生2.5吨以上的铜冶炼渣,新产生的以及自然环境中累积的铜冶金炉渣数量可见一斑,西南及南方诸省土地、河流和粮食农作物受重金属污染的报道此起彼伏,矿业产生的固体废弃物对人类的生存环境造成了巨大威胁。
3.铜冶炼炉渣中含有磁铁矿、玻璃质相和铁橄榄等矿物相组分,其中非晶态玻璃质相和铁橄榄石相是主要组成相,二者的占比分别达到45%
±
和40%
±
,玻璃质、铁橄榄石和磁铁矿中的铁占渣中全铁的比例分别为44.94%、44.30%和10.34%。铜冶炼炉渣中feo与sio2的含量和接近80%,而cao含量却偏低,与硅酸盐水泥建材的成分差异较大,因此不能直接大量用于建材行业,只能作为辅料在建筑行业中应用。尽管最近的研究报道称,铜渣与其他材料搭配后烧制的水泥熟料可以获得优异的性能(秦守婉,申建军,吴春丽.熔渣、铜矿渣在水泥生产中的应用研究[j].硅酸盐通报,2013,32(4):572
‑
576,582.)。然而,铜渣中的氧化铁等碱性物质同大气中的水分和co2发生化学反应而风化和溶解,碱性环境下也会引起膨胀,造成对建筑物破坏,限制了其在建材中的应用(胡纯清,衡晓志,喻国安.钢铜渣碱性膨胀造成建筑物破坏的调查研究[j].土工基础,2000,14(1):35
‑
38.;王枫,高波.某学校混凝土爆裂事故原因分析[j].混凝土与水泥制品,2011,(12):53
‑
55.)。
[0004]
铜冶炼渣中铁的利用方法主要有高温氧化、磁选分离得到铁精矿,高温熔融还原富集提铁,以及高温煤基直接还原等方法。高温氧化、磁选分离的方法的主要工艺如下:在高温熔融铜冶炼炉渣中鼓入富氧空气或者氧气进行改性处理,促使渣中的氧化铁相转移、迁移、富集和结晶,实现粗化fe3o4相的晶粒尺寸,达到有利于磁选分离、回收铁的目的。高温氧化、磁选分离可得到含铁54%的铁精矿,铁的回收率为90%左右。
[0005]
高温熔融氧化铜渣、富集提取铁的工艺主要为:向1350℃的铜冶炼熔融体中加入氧化钙并通入氧气氧化铜渣,先将铁橄榄石中的铁组分转化为fe3o4,再通过磁选得到铁精矿,铁精矿品位在61%以上,但铁的回收率为70%左右(刘纲,朱荣,王昌安,等.铜渣熔融氧化提铁的试验研究[j].中国有色冶金,2009,(1):71
‑
74;黄自力,罗凡,李密,等.从炼铜水
淬渣中回收铁的试验研究[j].矿产保护与和利用,2009,(3):51
‑
54.)。在铜渣中添加一定造渣剂cao,在高温熔融状态还原熔炼铜渣中的铁,渣相和还原所得金属相澄清后分离得到金属铁,但熔融还原过程中铜进入铁水相中,导致铁水中铜含量高,而铁水中有效分离和去除铜仍然还是世界性的难题,这是该方案的不足之处(李磊,胡建杭,王华.铜渣熔融还原炼铁过程反应热力学分析[j].材料导报b,2011,25(7):114
‑
117.;胡建杭,王华,刘慧利,等.铜渣在不同煅烧温度的晶相结构[j].湖南科技大学学报(自然科学版),2011,26(2):97
‑
100.)。
[0006]
以褐煤为还原剂、在高温(1250℃)下直接还原铜渣中铁的研究,结果表明渣中的fe3o4、2feo
·
sio2能直接还原为铁,而且加入铜渣质量10%的氧化钙能提高渣中铁的还原效率,通过控制还原温度、还原时间及物料的粒度,实现还原产物中金属铁颗粒的尺寸和金属铁的界面特性定向控制的目的,金属铁易于解离和磁选分离而获得铁质量分数为92.05%的铁粉(杨慧芬,景丽丽,党春阁.铜渣中铁组分的直接还原与磁选回收[j].中国有色金属学报,2011,21(5):1165
‑
1170.)。
[0007]
高温氧化方案在温度高达1350℃的条件下将渣中的铁化合物转变为fe3o4,然后通过磁选回收渣中的铁资源。中低温氧化工艺也只涉及铜渣中铁橄榄石相中铁氧化为磁性氧化铁、进而磁选为铁精矿产品。然而,无论是高温氧化还是中低温氧化工艺,铁达到合格铁精矿品位时回收率皆不高,且以磁性氧化铁的形式回收铜渣中的铁,进入高炉进行炼铁作业时消耗的还原剂量增加,后续工艺的能耗高。高温熔融还原要求的温度在1380℃以上,煤基直接还原也高达1250℃,能耗高是致命的硬伤。而且还原过程需消耗大量的碳,也会产生大量的温室气体co2。
[0008]
综上,目前铜冶炼渣中硅未能有效利用,且渣中铁的利用技术存在回收率低、能耗高、污染环境的缺陷,也未在工业实践中加以应用。
技术实现要素:[0009]
针对上述现有技术存在的问题及不足,本发明提供一种超声强化分离铜冶炼炉渣中的硅和铁并利用硅制备白炭黑的方法。通过在铜冶炼炉渣中加入氢氧化钠和硝酸钠,在超声强化条件下将渣中的硅转化为硅酸钠,使结构和组成复杂的铜冶炼渣中的硅与渣中的铁、钙、铜等杂质元素分离,制备出白炭黑产品后,其副产品滤渣直接用于炼铁作业的优质炼铁原料,从而实现高效利用铜冶炼渣中硅和铁的目的。本发明通过以下技术方案实现。
[0010]
一种超声强化分离铜冶炼炉渣中的硅和铁并利用硅制备白炭黑的方法,其特征在于按以下步骤进行:
[0011]
步骤1、粉碎:将铜冶炼渣进行粉碎,得到粉状铜冶炼渣;
[0012]
步骤2、超声强化浸出:将步骤1得到的粉状铜冶炼渣称取100g加入到超声加压反应釜中,加入质量浓度为20%~60%的氢氧化钠溶液400~800ml,加入硝酸钠,硝酸钠的加入量为粉状铜冶炼渣质量的5%~20%,在120~200℃并超声波辐照下搅拌反应1.0~3.0h,待反应结束后,将反应物冷却至温度低于80℃;
[0013]
步骤3、固液分离:将步骤2中冷却后的反应产物进行固液分离和洗涤,得到滤洗液和滤渣;
[0014]
步骤4、陈化:将步骤3中得到的滤洗液加热至80~90℃,在搅拌状态下加入10%~
30%的稀硫酸溶液将滤洗液的ph调整至2.5~3.5,继续搅拌反应1.0~2.0h,待反应结束后静置陈化1.5~2.5h,得陈化后的沉淀物;
[0015]
步骤5、过滤:将步骤4中得到的沉淀物进行过滤并洗涤,得到滤饼;
[0016]
步骤6、干燥:将步骤5中得到的滤饼于105~110℃干燥后1~2h即得到白炭黑。
[0017]
由于上述方法,通过在铜冶炼炉渣中加入氢氧化钠和硝酸钠,在超声强化条件下将渣中的硅转化为硅酸钠,使结构和组成复杂的铜冶炼渣中的硅与渣中的铁、钙、铜等杂质元素分离,制备出白炭黑产品,并副产能用于炼铁作业的优质原料——赤铁矿。即,上述粉状铜冶炼炉渣在硝酸钠和超声波协同催化下、于氢氧化钠溶液中实现矿物相的转化和分离,能使铜冶炼渣中98.0%以上的二氧化硅转化、进入液相,对反应产物进行固液分离和洗涤,进而制备成高附加值的白炭黑产品,所制白炭黑产品的质量符合白炭黑国家a级标准;分离硅后得到的滤渣(副产物)为能用于炼铁作业的优质原料——赤铁矿。
[0018]
所述铜冶炼渣的质量百分比组分为:fe 30%~50%、sio
2 25%~35%、cao 1.0%~10.0%、mgo 1.0%~5.0%、al2o
3 0.5%~5.0%、cu 0.1%~1.0%、s 0.05%~1.0%。
[0019]
所述步骤1中粉碎后的铜冶炼渣粒度小于0.075mm。
[0020]
所述步骤3中的滤渣的主要成分是赤铁矿,是能用于炼铁作业的优质炼铁原料。
[0021]
由于上述从铜冶炼炉渣中分离出硅并制备得到白炭黑产品的同时,其副产品(主要成分为赤铁矿的滤渣)直接能用于炼铁作业的优质炼铁原料,本发明方法实现了高效利用铜冶炼渣中硅和铁的目的。
[0022]
所述步骤5中的过滤为,将陈化后的沉淀物进行过滤,并用50ml去离子水进行三次洗涤,再用50ml无水乙醇进行三次洗涤得到所述滤饼。
[0023]
本发明的有益效果是:
[0024]
1、本发明在超声强化条件下将渣中的硅转化为硅酸钠,使结构和组成复杂的铜冶炼渣中的硅与渣中的铁、钙、铜等杂质元素分离,利用分离出的硅制备出高附加值的白炭黑产品;铜冶炼渣将硅分离后,滤渣为以fe2o3为主要成分,滤渣中cu及s的含量皆低于0.5%,是能直接用于炼铁作业的优质原料,从而实现高效利用铜冶炼渣中硅和铁的技术效果。
[0025]
2、本发明能够将铜冶炼炉渣中99.0%以上的铁转化为赤铁矿相,铁的回收率高,不产生二氧化硫及温室气体,过程环保、且能耗低。
[0026]
3、本发明将固体废弃物中的硅高值利用,硅的利用率大于95.0%,制备得到的白炭黑产品质量达到国家标准。
[0027]
4、硝酸钠和超声协同催化强化,可使二氧化硅的浸出率提升10%以上。
附图说明
[0028]
图1是本发明工艺流程图。
[0029]
图2是本发明铜冶炼渣中元素的质量百分比组分图。
具体实施方式
[0030]
应该指出,以下详细说明都是例示性的,旨在对本申请提供进一步的说明。除非另有指明,本文使用的所有技术和科学术语具有与本申请所属技术领域的普通技术人员通常
理解的相同含义。
[0031]
需要注意的是,这里所使用的术语仅是为了描述具体实施方式,而非意图限制根据本申请的示例性实施方式。如在这里所使用的,除非上下文另外明确指出,否则单数形式也意图包括复数形式,此外,还应当理解的是,当在本说明书中使用术语“包含”和/或“包括”时,其指明存在特征、步骤、操作、器件、组件和/或它们的组合。
[0032]
下面结合具体实施方式,对本发明作进一步说明。
[0033]
实施例1
[0034]
如图1所示,利用超声强化分离铜冶炼炉渣中的硅和铁并利用硅制备白炭黑的方法:
[0035]
(1)将铜冶炼渣破碎至90%以上的粒度小于为0.075mm,铜冶炼渣包括以下质量百分比组分:fe 40%、sio
2 32.5%、cao 3.2%、mgo 1.5%、al2o
3 0.5%、cu 0.3%、s 0.4%。
[0036]
(2)将破碎至90%以上的粒度小于为0.075mm的铜冶炼渣100g加入到超声加压反应釜中,加入质量浓度为60%的naoh溶液400ml,在加入含量为工业品硝酸钠20g,在温度为180℃、机械搅拌并超声辐照下反应2.0h;浸出结束后,停止加热并通入冷却水将溶液冷却至温度低于60℃,取出矿浆进行固液分离,同时用50ml的85℃的热水分三次洗涤滤渣,得到滤洗液435ml,滤渣置于烘箱中120℃干燥2h称重为65.2g,滤渣中fe2o3、cu和s的质量含量分别为86.7%,0.45%,和0.31%,能直接用于炼铁作业。
[0037]
(3)将上述得到滤洗液435ml加热至80℃,在搅拌状态下加入30%的稀硫酸溶液,加入量以将溶液的ph调整至2.5为终点,继续再搅拌下反应1.0h后,停止搅拌陈化2.5h,过滤并用50ml去离子水份三次洗涤,再用50ml无水乙醇分三次洗涤得到的滤饼,滤饼置于干燥箱于110℃干燥后1.5h得到白炭黑产品31.1g。所制白炭黑产品吸油值为2.2ml/g,比表面积达到295.60m2/g,符合白炭黑国家a级标准。
[0038]
实施例2
[0039]
如图1所示,利用超声强化分离铜冶炼炉渣中的硅和铁并利用硅制备白炭黑的方法:
[0040]
(1)将铜冶炼渣破碎至90%以上的粒度小于为0.075mm,铜冶炼渣包括以下质量百分比组分:fe 50%、sio
2 25%、cao 1.0%、mgo 1.0%、al2o
3 0.9%、cu 0.4%、s 1.0%。
[0041]
(2)将破碎至90%以上的粒度小于为0.075mm的铜冶炼渣100g加入到超声加压反应釜中,加入质量浓度为20%的naoh溶液700ml,在加入含量为工业品硝酸钠15g,在温度为200℃、机械搅拌并超声辐照下反应3.0h;浸出结束后,停止加热并通入冷却水将溶液冷却至温度低于80℃,取出矿浆进行固液分离,同时用50ml的80℃的热水分三次洗涤滤饼,得到滤洗液730ml,滤渣置于烘箱中120℃干燥2h称重为73.5g,滤渣中fe2o3、cu和s的质量含量分别为95.6%,0.48%,和0.48%,能直接用于炼铁作业。
[0042]
(3)将上述得到滤洗730ml加热至90℃,在搅拌状态下加入10%的稀硫酸溶液,加入量以将溶液的ph调整至3.5为终点,继续再搅拌下反应2.0h后,停止搅拌陈化1.5h,过滤并用50ml去离子水份三次洗涤,再用50ml无水乙醇分三次洗涤得到的滤饼,滤饼置于干燥箱于105℃干燥后2.0h得到白炭黑产品24.25g。所制白炭黑产品吸油值为2.5ml/g,比表面积达到298.50m2/g,符合白炭黑国家a级标准。
[0043]
实施例3
[0044]
如图1所示,利用超声强化分离铜冶炼炉渣中的硅和铁并利用硅制备白炭黑的方法:
[0045]
(1)将铜冶炼渣破碎至90%以上的粒度小于为0.075mm,铜冶炼渣包括以下质量百分比组分:fe 30%、sio235%、cao 10.0%、mgo 5.0%、al2o35.0%、cu 0.2%、s 0.7%。
[0046]
(2)将破碎至90%以上的粒度小于为0.075mm的铜冶炼渣100g加入到超声加压反应釜中,加入质量浓度为30%的naoh溶液800ml,在加入含量为工业品硝酸钠10g,在温度为120℃、机械搅拌并超声辐照下反应1.0h;浸出结束后,停止加热并通入冷却水将溶液冷却至温度低于60℃,取出矿浆进行固液分离,同时用50ml的85℃的热水分三次洗涤滤渣,得到滤洗液836ml,滤渣置于烘箱中120℃干燥2h称重为65.2g,滤渣中fe2o3、cu和s的质量含量分别为65.0%,0.28%,和0.46%,能直接用于炼铁作业。
[0047]
(3)将上述得到滤洗液836ml加热至85℃,在搅拌状态下加入20%的稀硫酸溶液,加入量以将溶液的ph调整至3.0为终点,继续再搅拌下反应1.5h后,停止搅拌陈化2.0h,过滤并用50ml去离子水份三次洗涤,再用50ml无水乙醇分三次洗涤得到的滤饼,滤饼置于干燥箱于110℃干燥后1.0h得到白炭黑产品33.6g。所制白炭黑产品吸油值为2.8ml/g,比表面积达到290.60m2/g,符合白炭黑国家a级标准。
[0048]
实施例4
[0049]
如图1所示,利用超声强化分离铜冶炼炉渣中的硅和铁并利用硅制备白炭黑的方法:
[0050]
(1)将铜冶炼渣破碎至90%以上的粒度小于为0.075mm,铜冶炼渣包括以下质量百分比组分:fe 40%、sio233.5%、cao 6.0%、mgo 2.5%、al2o33.5%、cu 0.1%、s 0.05%。
[0051]
(2)将破碎至90%以上的粒度小于为0.075mm的铜冶炼渣100g加入到超声加压反应釜中,加入质量浓度为40%的naoh溶液500ml,在加入含量为工业品硝酸钠5g,在温度为150℃、机械搅拌并超声辐照下反应1.5h;浸出结束后,停止加热并通入冷却水将溶液冷却至温度低于60℃,取出矿浆进行固液分离,同时用50ml的85℃的热水分三次洗涤滤渣,得到滤洗液532ml,滤渣置于烘箱中120℃干燥2h称重为66.0g,滤渣中fe2o3、cu和s的质量含量分别为86.1%,0.15%,和0.03%,能直接用于炼铁作业。
[0052]
(3)将上述得到滤洗液532ml加热至80℃,在搅拌状态下加入15%的稀硫酸溶液,加入量以将溶液的ph调整至2.5为终点,继续再搅拌下反应2.0h后,停止搅拌陈化2.0h,过滤并用50ml去离子水份三次洗涤,再用50ml无水乙醇分三次洗涤得到的滤饼,滤饼置于干燥箱于110℃干燥后1.5h得到白炭黑产品32.1g。所制白炭黑产品吸油值为2.5ml/g,比表面积达到290.80m2/g,符合白炭黑国家a级标准。
[0053]
实施例5
[0054]
如图1所示,利用超声强化分离铜冶炼炉渣中的硅和铁并利用硅制备白炭黑的方法:
[0055]
(1)将铜冶炼渣破碎至90%以上的粒度小于为0.075mm,铜冶炼渣包括以下质量百分比组分:fe 40%、sio233.5%、cao 2.2%、mgo 1.5%、al2o32.8%、cu 0.2%、s 0.3%。
[0056]
(2)将破碎至90%以上的粒度小于为0.075mm的铜冶炼渣100g加入到超声加压反应釜中,加入质量浓度为25%的naoh溶液600ml,在加入含量为工业品硝酸钠10g,在温度为140℃、机械搅拌并超声辐照下反应3.0h;浸出结束后,停止加热并通入冷却水将溶液冷却
至温度低于70℃,取出矿浆进行固液分离,同时用50ml的80℃的热水分三次洗涤滤渣,得到滤洗液622ml,滤渣置于烘箱中120℃干燥2h称重为65.5g,滤渣中fe2o3、cu和s的质量含量分别为85.7%,0.30%,和0.20%,能直接用于炼铁作业。
[0057]
(3)将上述得到滤洗液622ml加热至80℃,在搅拌状态下加入20%的稀硫酸溶液,加入量以将溶液的ph调整至3.0为终点,继续再搅拌下反应3.0h后,停止搅拌陈化2.5h,过滤并用50ml去离子水份三次洗涤,再用50ml无水乙醇分三次洗涤得到的滤饼,滤饼置于干燥箱于110℃干燥后2.0h得到白炭黑产品32.1g。所制白炭黑产品吸油值为2.3ml/g,比表面积达到296.60m2/g,符合白炭黑国家a级标准。
[0058]
在本说明书的描述中,参考术语“一个实施例”、“一些实施例”、“示例”、“具体示例”、或“一些示例”等的描述意指结合该实施例或示例描述的具体特征、结构、材料或者特点包含于本发明的至少一个实施例或示例中。在本说明书中,对上述术语的示意性表述不一定指的是相同的实施例或示例。而且,描述的具体特征、结构、材料或者特点可以在任何的一个或多个实施例或示例中以合适的方式结合。
[0059]
尽管已经示出和描述了本发明的实施例,本领域的普通技术人员可以理解:在不脱离本发明的原理和宗旨的情况下可以对这些实施例进行多种变化、修改、替换和变型,本发明的范围由权利要求及其等同物限定。