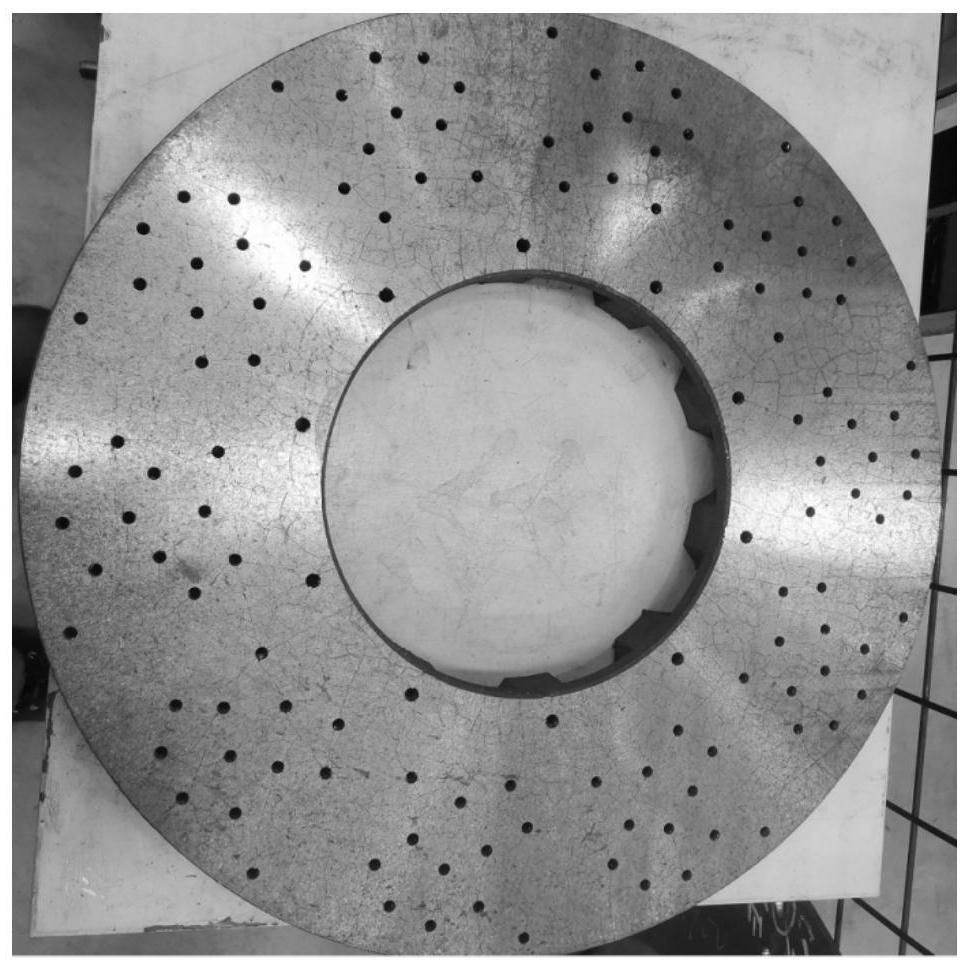
1.本发明属于轨道交通制动盘技术领域,具体涉及一种一体成型碳陶涂层盘及其制备方法。
背景技术:2.目前,碳陶制动盘作为一类新型产品被用于汽车、地铁、高铁等轨道交通领域,而随着技术的更新替代,耐磨性、抗氧化性更强的碳陶涂层盘被开发应用于高端汽车、赛车、改装车等汽车制动领域,但现阶段的碳陶涂层盘多采用浆料法(形成界面层结合)、模压法(通过粘接层结合)等,但由于涂层与基体间的热膨胀系数间的差异、结合处的粘接技术性能不一等问题造成涂层盘在制动过程中常常发生掉块剥落等质量问题,尤其在稍微恶劣的工况下,出现砂石撞击涂层盘盘面后极大的概率会出现以上质量问题;轻度时加剧盘片的磨损,中度时持续的掉块剥落会撞击损坏制动系统造成经济损失,重度时可能出现盘、片、卡钳崩坏造成安全事故。
3.由于碳陶涂层盘现阶段的种种问题对它的应用有了极大的制约,严重影响了该行业的进一步发展与突破;但碳陶涂层盘自身的优势也是十分明显,如相较于传统碳陶盘有着更好的外观、高硬高耐磨的涂层在正常使用下制动盘寿命得到成倍乃至数倍的增长、摩擦面没有了传统碳陶盘的无纬布,变成了高陶瓷含量的涂层,有着极佳的抗氧化能力和较低的摩擦系数热衰退。
4.因此,整合碳陶涂层盘的劣势和优势,对碳陶涂层盘涂层与基体结合处层间剪切强度的改善显得尤为重要,可以进一步提升该产品的行业竞争度和市场认可度。
技术实现要素:5.针对现有碳陶涂层盘的涂层结合强度等技术问题,本发明的目的在于提供一种一体成型碳陶涂层盘及其制备方法,利用粘接编制或编制工艺(针刺方式、穿刺等)制备出涂层盘预制体基体,经增密、陶瓷化后大大提高了耐磨涂层与碳陶复合材料支撑层结合处的层间剪切强度和性能一致性;同时耐磨涂层中一定量的超薄型网状织物提升了耐磨涂层的综合力学性能,使之不易崩坏、掉块、剥落;本发明操作简单,在传统碳陶盘生产的基础上几乎没有增加生产作业流程(现阶段的碳陶涂层盘生产基本需增加2
‑
4道工序),大大提高了生产效率、节约了生产成本、提升了产品质量。
6.本发明所述的一种一体成型碳陶涂层盘的应用领域也随之更为广泛,如在地铁和高铁制动领域,本发明碳陶涂层盘的环境适应能力大大提升,涂层在砂石撞击等其他恶劣工况下也不会出现掉块脱落现象,同时涂层的抗氧化能力和系数抗热衰减能力能有效保证高铁在高速下的制动性能。
7.本发明一种一体成型碳陶涂层盘,其预制体包括支撑预制体、耐磨涂层预制体,所述摩擦涂层预制体通过粘接和/或编制工艺与支撑预制体构成一个整体;所述耐磨涂层预制体的密度小于支撑预制体的密度;所述耐磨涂层预制体由碳质材料构成,且所述涂层预
制体采用短纤维增强;所述基体经增碳后进行陶瓷化,得到产品,经渗碳陶瓷化后耐磨涂层预制体转化为耐磨陶瓷涂层;支撑预制体转化为碳陶复合材料结构支撑层;所述耐磨涂层中的陶瓷含量为碳陶复合材料支撑层中陶瓷含量的1.2倍以上;所述碳陶复合材料支撑层和耐磨涂层构成所述的碳陶涂层盘。
8.本发明一种一体成型碳陶涂层盘,先制备出支撑预制体,然后通过粘接和/或编制工艺在预制体阶段制备出耐磨涂层预制体得到涂层盘预制体基体,即在支撑预制体的至少一个面上制备出耐磨涂层预制体,所述编制工艺选自针刺、穿刺中的至少一种;
9.当支撑预制体的2个面上制备出耐磨涂层预制体时,其制备方法为:
10.以超薄型网状织物为原料,采用低残炭型树脂将超薄型网状织物粘接到支撑预制体上;和/或
11.以超薄型网状织物为原料,采用穿刺工艺和/或针刺工艺将超薄型网状织物连接到支撑预制体上;
12.穿刺工艺控制穿刺密度20
±
10针/cm2、优选为20
±
5针/cm2;针刺工艺控制针刺密度为20
±
10针/cm2、优选为20
±
5针/cm2,针刺深度15
±
10mm、优选为15
±
5mm,针刺2
‑
3层后更换至另一面继续针刺耐磨涂层预制体,如此反复交替,直至耐磨涂层预制体达到设定厚度;避免单侧持续受压导致涂层预制体阶段密度差异大。
13.所述原料包括12k
‑
pancf超薄型网状织物;所述低残炭型树脂选自环氧树脂、酚醛树脂中的一种;
14.避免单侧持续受压导致涂层预制体阶段密度差异大。
15.本发明一种一体成型碳陶涂层盘,支撑预制体的密度为0.45
±
0.20g/cm3、优选为0.55
±
0.10g/cm3,耐磨涂层预制体的密度为0.18
±
0.10g/cm3、优选为0.18
±
0.05g/cm3。
16.本发明一种一体成型碳陶涂层盘,沿着一体成型碳陶涂层盘轴向方向,在支撑预制体一侧的耐磨涂层预制体的厚度大于1mm;优选为2
‑
10mm、进一步优选为5
‑
7mm。
17.本发明一种一体成型碳陶涂层盘,其特征在于:一体成型碳陶涂层盘的密度为2.00
‑
2.50g/cm3、2.30
‑
2.50g/cm3,开孔率为1
‑
10%、优选为1
‑
3%;
18.碳陶复合材料支撑层的密度为2.00
‑
2.50g/cm3优选为2.20
‑
2.50g/cm3,开孔率1
‑
10%、优选为1
‑
3%,陶瓷含量为50~60wt%、优选为55wt%;
19.耐磨涂层的密度为2.10
‑
2.60g/cm3优选为2.30
‑
2.60g/cm3,开孔率1
‑
8%,陶瓷含量为60
‑
80wt%、优选为70wt%,且耐磨涂层的陶瓷含量大于碳陶复合材料结构支撑层中的陶瓷含量。
20.耐磨涂层与碳陶复合材料支撑层之间的剪切强度大于20mpa。
21.本发明一种一体成型碳陶涂层盘的制备方法,包括如下步骤:
22.(1)在密度0.45
±
0.20g/cm3、优选为0.55
±
0.10g/cm3的支撑预制体两面针刺一定厚度的超薄型网状织物,形成密度在0.18
±
0.10g/cm3、优选为0.18
±
0.05g/cm3的超薄型网状织物涂层预制体,制得涂层盘预制体基体;
23.(2)惰性气氛下,将涂层盘预制体基体于1700
‑
2200℃、优选为1800
‑
2000℃下进行热处理;
24.(3)通过进行两次或以上的化学气相沉积工艺将涂层盘预制体基体增密至1.20
±
0.10g/cm3,第一次气相沉积使得涂层盘预制体基体增密至0.90
±
0.10g/cm3、优选为0.95
±
0.10g/cm3,第二次化学气相沉积时,先调转盘面方向,然后增密;除第一次气相沉积外,以后的每次气相沉积均需调整盘面方向,直至达到设定密度,得到涂层盘c/c基体;此沉积二调转盘面为关键性步骤,否则会出现严重的密度偏差质量问题;
25.(4)在1750
±
100℃、优选为1700
±
50℃下高温渗硅,通过液硅或硅蒸汽渗入涂层盘c/c基体孔隙内部发生硅碳反应制得高层间剪切强度、高耐磨的一体成型碳陶涂层盘。
26.本发明一种一体成型碳陶涂层盘的制备方法,步骤(1)中,超薄型网状织物涂层预制体的针刺密度为20
±
10针/cm2、优选为20
±
5针/cm2,针刺深度15
±
10mm、优选为15
±
5mm,针刺1层后旋转90
°
,针刺2
‑
3层后更换至另一面继续针刺,如此反复交替,确保针刺压痕和涂层密度的均一性。
27.作为优选,步骤(1)中,所述超薄型网状织物涂层预制体针刺密度20针/cm2,针刺深度为15mm,制备所得涂层密度为0.18
±
0.02g/cm3,通常情况下,针刺密度越高会使得超薄型网状织物涂层预制体密度相应增高,合适的超薄型网状织物涂层预制体密度可以使得耐磨涂层具有良好的力学性能和耐磨性;较低的密度会导致涂层预制体易变形,耐磨涂层力学性能差、结合差等等;较高的密度会使得针刺孔过多过密过大,增密难以填充,外观变差,同时增密的均匀性变差,碳含量升高,陶瓷化后的碳陶涂层盘耐磨性降低。合适的针刺深度可以给碳陶涂层盘提供良好的力学性能和优美的外观等;过低的针刺深度将导致耐磨涂层结合差,耐磨涂层与碳陶复合材料支撑层结合处层间剪切强度低而出现掉块分层等现象;过高的针刺深度将导致针刺孔深而粗大,导致碳陶涂层盘外观极差(其原因可能是针刺孔在增密的过程中均匀填充相对较难)。
28.同时在本技术探索过程中还发现:超薄型网状织物沉积效率更高,增密更快,过高的超薄型网状织物涂层预制体密度容易导致沉积增密过程中结合处封孔且无法处理,使得后续陶瓷化进行不够彻底,或是增密过程中超薄型网状织物涂层预制体达到设计要求而支撑预制体未达到要求导致最终碳陶复合材料支撑层力学性能较差。
29.作为进一步的优选,步骤(3)中,所述涂层盘c/c基体密度为1.20
±
0.05g/cm3。适当的涂层盘c/c基体密度内部孔隙大小适中孔隙分布均匀有利于陶瓷化的进行和获得较为理想的力学性能;过低的涂层盘c/c基体密度会使得陶瓷化后的碳陶涂层盘综合力学性能偏低;过高的涂层盘c/c基体密度会使得陶瓷化不彻底(孔隙细小不均匀,涂层c/c基体与支撑层c/c基体结合处可能存才封孔现象),耐磨涂层碳含量偏高、陶瓷含量偏低而不耐磨。
30.本发明一种一体成型碳陶涂层盘的制备方法,步骤(3)中,涂层盘c/c基体的上、中、下三层密度差低于0.20g/cm3;作为优选步骤(3)中,涂层盘c/c基体的上、中、下三层密度差低于0.10g/cm3。
31.作为优选,步骤(4)中,涂层盘c/c基体高温渗硅温度为1750
±
20℃。高温渗硅的过程中,温度过低时硅的粘度高,渗透性差,且极易出现粘锅现象;温度过高时碳陶涂层盘的致密度越低,尤其是涂层部分会出现较为明显的针刺孔洞现象,对耐磨及抗氧化性能都有着较大的影响,且温度越高,综合力学性能越差。
32.本发明一种一体成型碳陶涂层盘的制备方法,步骤(4)中,一体成型碳陶涂层盘的密度为2.00
‑
2.50g/cm3、优选为2.30
‑
2.50g/cm3,开孔率为1
‑
10%、优选为1
‑
3%;
33.碳陶复合材料支撑层的密度为2.00
‑
2.50g/cm3、优选为2.20
‑
2.50g/cm3,开孔率1
‑
10%、优选为1
‑
3%,陶瓷含量为50~60wt%、优选为55wt%;
的涂层盘预制体基体;(针刺方式为单面针刺一层后旋转90
°
针刺第二层,针刺两层后调转至反面针刺,如此反复交替直至达设计厚度与设计密度)
50.(2)预制体热处理
51.将涂层盘预制体基体在2000℃氩气保护氛围下进行高温热处理,密度变化为0.41g/cm3;
52.(3)预制体增密
53.①
:将热处理后的涂层盘预制体基体在化学气相沉积炉内以丙烯或天然气为碳源、氮气为保护气的工况下增密至0.95g/cm3;(上下表面各车削1.0mm见光)
54.②
:将工序
①
中加工后的涂层盘翻转一面在化学气相沉积炉内以丙烯或天然气为碳源、氮气为保护气的工况下增密至1.20g/cm3制得涂层盘c/c基体;
55.(4)按图纸加工成形
56.(5)高温渗硅
57.将涂层盘c/c基体在高温渗硅炉内按设计密度2.45g/cm3铺放硅粉,然后在1700℃、控制升降温速率、设置多段保温的工艺下高温渗硅制得碳陶涂层盘;
58.本实施例中,涂层盘c/c基体上、中、下三层密度分别为1.16g/cm3、1.21g/cm3、1.17g/cm3,开孔率分别为39.76%、35.53%、38.95%,密度均匀性非常理想;
59.制备所得碳陶涂层盘密度2.39g/cm3,开孔率2.21%,上、中、下三层密度分别为2.48g/cm3、2.36g/cm3、2.46g/cm3;
60.所得碳陶涂层盘耐磨涂层与碳陶复合材料支撑层处层间剪切强度高达27.3mpa,碳陶复合材料支撑层抗压强度为385.6mpa、抗弯强度为245.4mpa、冲击韧性为61.3kj/m2,碳陶复合材料支撑层力学性能十分优异,为碳陶涂层盘提供了足够强度的骨架支撑;
61.所得碳陶涂层盘匹配合成刹车片完成j2522汽车台架实验后,特征系数为0.42,碳陶涂层盘磨损0.003mm,刹车片磨损分别为0.395mm、0.411mm。
62.实施例2
63.实施2在实施例1的基础上只改变涂层盘c/c密度为1.30g/cm3,其余制备工艺相同;
64.本实施例中,涂层盘c/c基体上、中、下三层密度分别为1.31g/cm3、1.28g/cm3、1.36g/cm3,开孔率分别为27.49%、27.94%、24.58%,密度均匀性较为理想;
65.制备所得碳陶涂层盘密度2.32g/cm3,开孔率3.01%,上、中、下三层密度分别为2.40g/cm3、2.30g/cm3、2.34g/cm3;
66.所得碳陶涂层盘耐磨涂层与碳陶复合材料支撑层处层间剪切强度高达28.1mpa,碳陶复合材料支撑层抗压强度为393.4mpa、抗弯强度为258.6mpa、冲击韧性为59.4kj/m2,整体力学性能较实施例1有所提升;
67.所得碳陶涂层盘匹配合成刹车片完成j2522汽车台架实验后,特征系数为0.39,碳陶涂层盘磨损0.006mm,刹车片磨损分别为0.456mm、0.463mm,较实施例1磨损有显著提升,这是因为该实施例中涂层盘c/c基体密度提升,使得碳陶涂层盘耐磨涂层中c含量提升,陶瓷含量下降,整体耐磨性降低导致碳陶涂层盘磨损量提升;刹车片磨损增加是因为盘面在高速高压等恶劣工况下出现轻微划痕,略微不平整的盘面使得盘片间摩擦及振动加剧,故导致刹车片磨损量增加。
68.实施例3
69.实施3在实施例1的基础上只改变涂层盘c/c密度为1.10g/cm3,其余制备工艺相同;
70.本实施例中,涂层盘c/c基体上、中、下三层密度分别为1.06g/cm3、1.12g/cm3、1.01g/cm3,开孔率分别为47.76%、45.06%、51.68%,密度均匀性一般;
71.制备所得碳陶涂层盘密度2.46g/cm3,开孔率3.48%,上、中、下三层密度分别为2.54g/cm3、2.44g/cm3、2.58g/cm3,对比实施例1密度显著提升,碳陶涂层盘涂层陶瓷含量也随之提升;
72.所得碳陶涂层盘耐磨涂层与碳陶复合材料支撑层处层间剪切强度25.0mpa,碳陶复合材料支撑层抗压强度为300.1mpa、抗弯强度为184.5mpa、冲击韧性为50.3kj/m2,对比实施例1碳陶复合材料支撑层力学性能有所下降;
73.所得碳陶涂层盘匹配合成刹车片完成j2522汽车台架实验后,特征系数为0.43,碳陶涂层盘磨损0.002mm,刹车片磨损分别为0.419mm、0.415mm;
74.该实施例下虽然碳陶涂层盘磨损略有下降,但对偶刹车片磨损有所上升,同时最为关键是碳陶涂层盘碳陶复合材料支撑层力学性能出现下降,骨架支撑能力不足。
75.实施例4
76.实施4在实施例1的基础上只改变涂层盘预制体基体针刺密度为10针/cm2,所制备出超薄型网状织物涂层随之降低为0.13g/cm3,其余制备工艺相同;
77.本实施例与实施例1主要差别在于涂层盘c/c基体芯部达到合适密度时,涂层密度任旧偏低,涂层盘c/c基体上、中、下三层密度分别为1.08/cm3、1.23g/cm3、1.09g/cm3,导致碳陶涂层盘中耐磨涂层的c含量降低,陶瓷含量进一步提升,耐磨涂层脆性相应增大;其次该实施例碳陶涂层盘耐磨涂层与碳陶复合材料支撑层结合处层间剪切强度有所下降,为22.9mpa。
78.实施例5
79.实施5在实施例1的基础上只改变涂层盘预制体基体针刺深度为10针/cm2,其余制备工艺相同;
80.本实施例与实施例1主要差别在于碳陶涂层盘耐磨涂层与碳陶复合材料支撑层结合处层间剪切强度也有所下降,为22.5mpa。
81.对比例1
82.对比例1将实施例1中涂层盘预制体基体两次增密调整为一次增密至1.20g/cm3,其余制备工艺相同;
83.本对比例中,涂层盘c/c基体上、中、下三层密度分别为1.35g/cm3、1.19g/cm3、1.10g/cm3,密度各区间存在极大的差异,尤其是上下层,这将导致力学、摩擦磨损等性能全面的下降,成分的差异将导致盘两面磨损状态的差异,进而加剧振动等情况的发生,导致进一步加剧磨损,严重时可能出现安全隐患。
84.对比例2
85.对比例2将实施例1中针刺方式由单面针刺一层后旋转90
°
针刺第二层,针刺两层后调转至反面针刺,如此反复交替直至达设计厚度与设计密度调整为一侧直接针刺至指定厚度和密度后翻面针刺加工,其余制备工艺相同;
86.本对比例中先行针刺完超薄型网状织物涂层的一面在另一面针刺过程中持续受压,导致先行针刺面厚度一定幅度下降,涂层密度略微升高,而另一面则导致涂层密度在整体的计算过程中出现偏差,导致密度偏低。
87.本对比例涂层盘c/c基体上、中、下三层密度分别为1.27g/cm3、1.21g/cm3、1.10g/cm3,上下层密度出现严重偏差,则使得碳陶涂层盘成分也随之出现偏差;在摩擦磨损实验中碳陶涂层盘磨损0.014mm,刹车片磨损分别为0.506mm、0.637mm,磨损量相较于实施例1有显著上升,且刹车片两面磨损量有显著差异,这是因为两摩擦面成分差异大,摩擦制动过程中振动加剧,故导致磨损量上升,成分差异也会导致两面摩擦受力状态差异,导致两面磨损情况差异大。
88.对比例3
89.对比例3在实施例1的基础上只高温渗硅温度为1600℃,其余制备工艺相同;
90.本对比例在高温渗硅出炉后碳陶涂层盘粘死在坩埚内部,破坏坩埚取出碳陶涂层盘后表面依然粘有相当多硅渣,散热孔、风道全面堵死,涂层盘加工难度极大,将制动盘直接切割开,发现内部呈现灰黑色,证明硅未完全渗透进内部反应;造成该现象是因为熔渗温度低,硅液的粘度很大,向涂层盘孔隙内渗透能力差,且反应完毕后,多余硅无法被抽出坩埚内而造成粘锅等质量问题;
91.对比例4
92.对比例3在实施例1的基础上只高温渗硅温度为1900℃,其余制备工艺相同;
93.该对比例制备所得碳陶涂层盘密度2.22g/cm3,开孔率12.31%,碳陶涂层盘表面出现非常多的细小针孔;
94.所得碳陶涂层盘涂层与芯部处层间剪切强度仅为17.4mpa,芯部抗压强度为263.3mpa、抗弯强度为170.5mpa、冲击韧性为45.1kj/m2,整体力学性能相比于实施例1全面下降;
95.所得碳陶涂层盘匹配合成刹车片完成j2522汽车台架实验后,碳陶涂层盘磨损0.022mm,刹车片磨损分别为0.755mm、0.781mm,盘片磨耗量显著增加,这是由于熔渗温度高,开孔率升高,涂层陶瓷含量降低,尤其是硅含量的降低,形成的摩擦膜强度不够易剥落导致磨损量上升。
96.实施例1、对比例3与对比例4三者对比得出控制较低温度熔渗的目的是为了提高碳陶涂层盘的致密度,熔渗温度越低,碳陶涂层盘的致密度越高,进而抗氧化能力越强;另一方面,温度越低残留在涂层中的硅越多,整体陶瓷含量高,同时硅有利于形成一定强度的摩擦膜,二者相互作用下使得碳陶涂层盘耐磨性大大增强;同时1.20g/cm3涂层盘c/c基体使用较低熔渗温度(1700℃)具有自身的优势,因为该温度下熔渗硅液的粘度仍然相对低,而该密度下涂层盘c/c基体具有合适的内部孔径和均匀分布的孔隙使硅液能向涂层盘c/c基体内部均匀渗透参加反应,最终制得综合力学性能和摩擦磨损性能都相对理想的碳陶涂层盘。