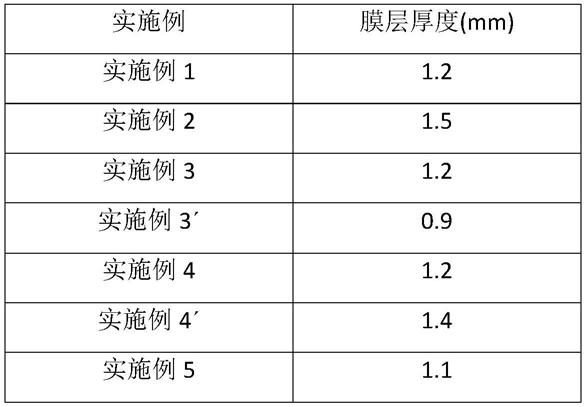
1.本发明属于建筑材料技术领域,具体涉及到一种离子吸收陶粒及其制备方法。
背景技术:2.水泥基材料是国家基础设施中应用最广泛的建筑材料之一,但是水泥基材料的应用也存在诸多挑战,尤其是将其应用到码头、跨海大桥以及海上风电平台等周围环境中富含氯离子及硫酸根等离子的环境中,这些离子会侵入水泥基材料中,影响水泥基材料耐久性和服役期限。
3.陶粒是一种人造轻质骨料,通常是在一定的条件下,发生化学反应,生成一种稳定、质硬的固相。人造陶粒具有很多优异的性能,如密度低、抗冻性好、软化系数好等。陶粒具有性能可设计性,可设计出不同密度、不同强度和吸水率的陶粒,如利用陶粒可设计性,制备出满足混凝土用基础材料,可替代部分砂石骨料。
4.现有技术中,采用陶粒制备水泥基材料仅处于常规的混合添加的方式,但这种方式制备的陶粒水泥基材料在混合过程中强制搅拌会破坏材料,导致吸收剂过早释放。
技术实现要素:5.本发明的目的是提供一种离子吸收陶粒及其制备方法,利用城市污泥制备出具有一定强度、孔隙率较大的陶粒,并以陶粒为载体,将氯离子和硫酸根离子吸收剂装入陶粒孔隙中,最后用封装材料封装陶粒,形成离子吸收陶粒。当水泥基材料中有相应离子渗入时,自由离子与封装材料发生反应,膜材破裂,离子吸收剂发挥作用,吸收自由离子,减小自由离子对水泥基材料的影响。
6.为达上述目的,本发明提供了一种离子吸收陶粒,包括以下重量份组分:离子吸收剂为10~30份、成膜材料10~30份和多孔陶粒50~100份;离子吸收剂为氯离子吸收剂或硫酸根离子吸收剂;成膜材料包括高分子树脂、乳液、稀释剂以及固化剂,其中高分子树脂与乳液的质量比为1:0.2~0.5,稀释剂用量不小于高分子树脂质量的10%,固化剂用量为高分子树脂质量的0~25%。
7.进一步地,氯离子吸收剂为活性氧化亚铜、活性镁铝水滑石、活性三氧化二铝、氢氧化钙、偏铝酸钠、铝酸三钙、铝酸钙粉、三硫型硫铝酸钙和单硫型硫铝酸钙中的至少一种。
8.进一步地,硫酸根离子吸收剂为蒙脱石粉、水滑石粉、矿石粉、石灰和聚合氯化铝粉中的至少一种。
9.进一步地,离子吸收剂颗粒粒径不大于75μm。
10.进一步地,高分子树脂为聚氨酯、环氧树脂、丙烯酸树脂、醇酸树脂、羟基丙烯酸树脂、乙烯树脂和过氯乙烯树脂中的至少一种。
11.优选的,高分子树脂为环氧树脂、热塑性丙烯酸树脂和羟基丙烯酸树脂。
12.进一步地,乳液为苯丙类乳液、丁苯类乳液或丙烯酸类乳液。
13.优选的,乳液为苯丙乳液、丁苯乳液、丙烯酸酯乳液和丙烯酸酯聚合物乳液。
14.进一步地,稀释剂为酯类、酮类、醇类或醇醚类;固化剂为脂肪族二胺、脂肪族多胺、芳香族多胺、有机酸、酸酐或三氟化硼及其络合物。
15.稀释剂优选丙酮、丁酮、甲醇、乙醇、乙酸乙酯、乙二醇一乙醚、乙二醇一丁醚及二甲苯中的一种或几种,固化剂优选多胺类。
16.进一步地,多孔陶粒吸水率不小于6%/h,筒压强度不小于3mpa。
17.一种离子吸收陶粒的制备方法,其特征在于,包括以下步骤:
18.(1)将多孔陶粒破碎后过筛网后,选取细度模数为2.1-3.7的多孔陶粒,超声振动后于负压条件下与离子吸收剂混合,制得陶粒载体;
19.(2)将高分子树脂、乳液、稀释剂及固化剂混合均匀后制得成膜材料,将成膜材料涂抹于陶粒载体表面,制得。
20.进一步地,成膜材料涂抹的膜层厚度不超过2mm。
21.综上所述,本发明具有以下优点:
22.1、本发明制备方法较为简单,原材料成本低,多孔陶粒载体具有较高强度,可抵抗预拌水泥基材料过程中的剪切应力而完整存在;
23.2、因成膜材料的存在,离子吸收陶粒能在水泥基材料水化前期稳定存在,避免吸收剂对水泥基材料水化、水化产物和性能的影响,在水泥水化后期,成膜材料与强碱性的水泥基材料反应,膜材破裂,当自由离子进入后,可吸收大量的自由离子,减小自由离子对混凝土性能的影响;
24.3、本发明所制得的离子吸收陶粒能吸收混凝土中自由氯离子或自由硫酸根离子,增强了水泥基材料的耐久性,且制备方法简单,可实现大规模工业化生产。
附图说明
25.图1为本发明制备的离子吸收陶粒的示意图;
26.图2为氯离子的浓度变化示意图;
27.图3为硫酸根离子的浓度变化示意图;
28.图4为硫酸盐环境下混凝土质量抗压强度变化示意图。
具体实施方式
29.以下结合实施例对本发明的原理和特征进行描述,所举实例只用于解释本发明,并非用于限定本发明的范围。实施例中未注明具体条件者,按照常规条件或制造商建议的条件进行。所用试剂或仪器未注明生产厂商者,均为可以通过市售购买获得的常规产品。
30.实施例1
31.本实施例提供了一种离子吸收陶粒的制备方法,包括以下步骤:
32.(1)选择筒压强度为4.5mpa,1h吸水率为10.4%的陶粒,破碎后过筛,选择细度模数为2.1的多孔陶粒,超声振动、鼓吹3min;
33.(2)称取60份多孔陶粒和30份三氧化二铝于负压条件下混合搅拌,其中三氧化二铝d
50
为45μm,使活性三氧化二铝进入陶粒孔隙,待三氧化二铝填充孔隙后取出陶粒;
34.(3)取20份环氧树脂、7份苯丙乳液、3份稀释剂和1.5份固化剂,混合均匀后,均匀地涂抹于步骤(2)制得的陶粒表面,形成薄膜层,自然晾干即得氯离子吸收陶粒。
35.其中,稀释剂为丙酮和甲醇按照质量比为1:1混合均匀;固化剂为脂肪族二胺。
36.如图1所示,由于成膜材料为树脂和乳液,氯离子吸收陶粒的表面较为光滑。
37.实施例2
38.本实施例提供了一种离子吸收陶粒的制备方法,包括以下步骤:
39.(1)选择筒压强度为6.4mpa,1h吸水率为7.4%的陶粒,破碎后过筛,选择细度模数为2.5的多孔陶粒,超声振动、鼓吹3min;
40.(2)称取60份多孔陶粒和30份活性偏铝酸钠于负压条件下混合搅拌,其中活性偏铝酸钠d
50
为34μm,使偏铝酸钠进入陶粒孔隙,待偏铝酸钠填充孔隙后取出陶粒;
41.(3)取30份干燥醇酸树脂、15份丙烯酸乳液和6份稀释剂,混合均匀后,均匀地涂抹于步骤(2)制得的陶粒表面,形成薄膜层,自然晾干即得氯离子吸收陶粒。
42.其中,稀释剂为二甲苯和乙醇按照质量比为2:1混合,本实施例不需要固化剂,树脂具有自干燥作用(下同)。
43.实施例3
44.本实施例提供了一种离子吸收陶粒的制备方法,包括以下步骤:
45.(1)选择筒压强度为6.7mpa,1h吸水率为8.9%的陶粒,破碎后过筛,选择细度模数为3.0的多孔陶粒,超声振动、鼓吹3min;
46.(2)称取60份多孔陶粒和30份活性偏铝酸钠于负压条件下混合搅拌,其中性偏铝酸钠d
50
为25μm,使活性偏铝酸钠进入陶粒孔隙,待偏铝酸钠填充孔隙后取出陶粒;
47.(3)取30份热塑性丙烯酸树脂、15份稀释剂,混合均匀后,均匀地涂抹于步骤(2)制得的陶粒表面,形成薄膜层,自然晾干即得氯离子吸收陶粒。
48.其中稀释剂为乙醇、丙酮和乙二醇一丁醚按照质量为2:1:1混合。
49.实施例4
50.本实施例提供了一种离子吸收陶粒的制备方法,包括以下步骤:
51.(1)选择筒压强度为6.7mpa,1h吸水率为9.8%的陶粒,破碎后过筛,选择细度模数为3.5的多孔陶粒,超声振动、鼓吹3min;
52.(2)称取70份多孔陶粒和30份蒙脱石粉于负压条件下混合搅拌,使活性蒙脱石粉进入陶粒孔隙,活性蒙脱石粉d50为30μm,待蒙脱石粉填充孔隙后取出陶粒;
53.(3)取20份热塑性丙烯酸树脂、4份丙烯酸酯聚合物乳液、4份稀释剂和,混合均匀后,均匀地涂抹于步骤(2)制得的陶粒表面,形成薄膜层,自然晾干即得硫酸根离子吸收陶粒。
54.稀释剂为乙酸乙酯和乙醇按照质量比3:1混合。
55.实施例5
56.本实施例提供了一种离子吸收陶粒的制备方法,包括以下步骤:
57.(1)选择筒压强度为7.7mpa,1h吸水率为8%的陶粒,破碎后过筛,选择细度模数为3.7的多孔陶粒,超声振动、鼓吹3min;
58.(2)称取50份多孔陶粒和20份聚合氯化铝粉于负压条件下混合搅拌,其中聚合氯化铝粉的d
50
为15μm,使氯化铝粉进入陶粒孔隙,待氯化铝粉填充孔隙后取出陶粒;
59.(3)取25份羟基丙烯酸树脂、5份稀释剂,混合均匀后,均匀地涂抹于步骤(2)制得的陶粒表面,形成薄膜层,自然晾干即得硫酸根离子吸收陶粒。
60.稀释剂为乙酸乙酯、甲醇和丁酮按照质量比为1:1:1混合。
61.实施例6
62.本实施例提供了一种离子吸收陶粒的制备方法,包括以下步骤:
63.(1)选择筒压强度为8.5mpa,1h吸水率为9.1%的陶粒,破碎后过筛,选择细度模数为2.1的多孔陶粒,超声振动、鼓吹3min;
64.(2)称取60份多孔陶粒、20份铝酸三钙和15份矿石粉于负压条件下混合搅拌,其中铝酸三钙d50为25μm,矿粉d50为30μm,使离子吸收剂进入陶粒孔隙,待离子吸收剂填充孔隙后取出陶粒;
65.(3)取15份羟基丙烯酸树脂、7.5份丁苯乳液、1.8份稀释剂,混合均匀后,均匀地涂抹于步骤(2)制得的陶粒表面,形成薄膜层,自然晾干即得氯离子和硫酸根离子吸收陶粒。
66.其中稀释剂为乙酸乙酯、甲醇和丁酮按照质量比为1:1:1混合。
67.实施例7
68.本实施例提供了一种离子吸收陶粒的制备方法,包括以下步骤:
69.(1)选择筒压强度为7.5mpa,1h吸水率为8.7%的陶粒,破碎后过筛,选择细度模数为2.1的多孔陶粒,超声振动、鼓吹3min;
70.(2)称取60份多孔陶粒、15份单硫型硫铝酸钙和20份水滑石粉于负压条件下混合搅拌,其中单硫型硫铝酸钙d50为35μm,水滑石粉d50为27μm,使离子吸收剂进入陶粒孔隙,待离子吸收剂填充孔隙后取出陶粒;
71.(3)取15份乙烯树脂、6份丙烯酸酯乳液和2.25份稀释剂,混合均匀后,均匀地涂抹于步骤(2)制得的陶粒表面,形成薄膜层,自然晾干即得氯离子和硫酸根离子吸收陶粒。
72.稀释剂为二甲苯和苯乙烯按照质量比为1:2混合,固化剂为过氧化甲乙酮。
73.试验例1
74.测试实施例1-7制备得到的经表面处理的混凝土用陶粒的膜层厚度及其耐碱性能,其中膜层厚度利用金相显微镜测试,结果如下表1所示。
75.表1成膜厚度
76.[0077][0078]
由表1可知,各实施例成膜厚度均小于2mm,满足设计要求。
[0079]
测试实施例1-3以及实施例6-7中制备得到的离子吸收陶粒对氯离子的吸收情况,包括以下步骤:
[0080]
(1)配制0.05mol/l naoh+0.35mol/l koh的m溶液,其可模拟水泥浆体孔溶液,溶液ph=12;
[0081]
(2)在m溶液中加入0.02mol/l nacl溶液后,得到溶液a,在m溶液中加入0.02mol/l naso4溶液,得到溶液b;
[0082]
(3)将实施例1~3、6~7中的离子吸收陶粒分别放置在a溶液中,并低速搅拌,搅拌速率不大于20r/min;搅拌至4h后开始取a溶液试样,并用贝尔分析仪器有限公司生产的氯离子浓度测试计监测溶液中氯离子变化情况。测试结果如图2所示,溶液测试起始浓度为200mg/l;
[0083]
(4)将实施例4~7中的离子吸收陶粒分别放置在b溶液中,并低速搅拌,搅拌速率不大于20r/min;搅拌至4h后开始取b溶液试样,并用贝尔分析仪器有限公司生产的氯离子浓度测试计监测溶液中氯离子变化情况。测试结果如图3所示,溶液测试起始浓度为200mg/l。
[0084]
由图2可知,各实施例在一定的时间内氯离子浓度会不断减小,表明成膜材料破裂后氯离子吸附剂与溶液中氯离子反应,使得氯离子浓度减小。
[0085]
其中,实施例1和实施例2在400min左右氯离子浓度开始减小,表明膜材破裂,氯离子吸附剂开始吸附溶液中氯离子;
[0086]
实施例3中至500min时氯离子浓度材开始变化,与实施例1、2相比较,实施例3中的成膜材料无乳液,这说明单独用树脂配制的成膜材料具有较高的耐碱性能,膜材破裂时间较晚;
[0087]
实施例6、7均为包裹有氯离子和硫酸根离子吸收剂的陶粒,从图中可以看到,实施例7中氯离子浓度起始变化时间较实施例6早,实施例6采用的是羟丙烯酸树脂与丁苯乳液的制备的成膜材料,而实施例7是用乙烯树脂和丙烯酸酯乳液制备的成膜材料,说明实施例7的膜材破裂较早。
[0088]
由图3可知,各实施例中硫酸根离子浓度随着时间增加逐渐减小,表明随着时间增加,成膜材料破裂,硫酸根离子吸附剂与溶液中硫酸根离子发生反应,减小溶液中自由硫酸根;
[0089]
其中,实施例4和实施例6在325min左右离子浓度开始变化,说明实施例4和实施例6成膜材料破裂时间相近,主要是因为两者均用了优选树脂和乳液作为成膜材料;
[0090]
实施例5中溶液浓度开始变化时间为420min左右,主要是因为其成膜材料只用了树脂,没有用乳液类,膜材破裂时间较晚,而实施例7中在200min时,硫酸跟离子浓度已经降至180mg/l左右,主要是因为成膜材料破裂较早。
[0091]
试验例2
[0092]
由试验例1的测试结果可知,通过变化成膜材料组成,可在强碱溶液中实现不同时
间下成膜材料破裂,释放离子吸收剂,并与自由离子反应,达到设计目的。为进一步验证其在真实水泥基材料中的效果,将实施例1~7中制备的陶粒作为混凝土用砂,其配合比如下表2所示。
[0093]
表2 c30混凝土配合比/kg/m3[0094][0095]
测试掺加实施例1~3,实施例6~7中离子吸收陶粒的混凝土水化7天后抗压强度和抗氯离子渗透性能,试件成型、测试及强度计算按照gb/t gb/t 50107-2010《混凝土强度检测评定标准》进行,依据gb/t 50082-2009《普通混凝土长期性能和耐久性能试验方法标准》中7.2测试混凝土的电通量,结果如表3所示,其中对照组为不掺加离子吸收陶粒的试样。
[0096]
表3 c30混凝土抗压强度和电通量
[0097][0098]
由表3可知,与对照组相比,掺加实施例的离子吸收陶粒后混凝土强度有所变化,部分实施例混凝土强度较对照组有所降低,而部分有所提升。对于混凝土电通量,对比对照组,掺加离子吸收陶粒后的试样其电通量均有所减小,即氯离子通过混凝土的能力有所降低。结合成膜材料、离子吸收剂及表2所示性能分析,实施例1、2、6、7中混凝土强度较对照组有所下降,且实施例7强度明显下降,而实施例3强度明显提升,主要原因在于成膜材料所致,部分成膜材料对混凝土力学性能带来不利影响,而单掺加热塑性丙烯酸树脂作为成膜材料的离子吸收陶粒可提升混凝土强度。
[0099]
试验例3
[0100]
测试掺加实施例4~7中离子吸收陶粒的混凝土水化7天后的抗硫酸盐腐蚀性能,测试方法依据gb/t 50082-2009《普通混凝土长期性能和耐久性能试验方法标准》进行,结果如图4所示。
[0101]
从图4可以看出,各试样混凝土抗压强度随着循环次数的增多而不断减小,对比基准组混凝土试样,掺加离子吸收陶粒的混凝土循环到一定次数后,其抗压强度减小速率变得平缓。实施例4循环20次后开始抗压强度变化开始平缓,表明膜材破裂后使得离子吸收剂吸收自由离子,弱化对混凝土抗压强度的影响。实施例5直至60次循环次数时才减弱,主要是因为成膜材料具有较好的耐碱性,破裂时间较晚导致的,同理,实施例6、7的变化也是因为成膜材料的耐碱性导致其抗压强度开始减缓时间有所不同。
[0102]
虽然结合附图对本发明的具体实施方式进行了详细地描述,但不应理解为对本专利的保护范围的限定。在权利要求书所描述的范围内,本领域技术人员不经创造性劳动即可作出的各种修改和变形仍属本专利的保护范围。