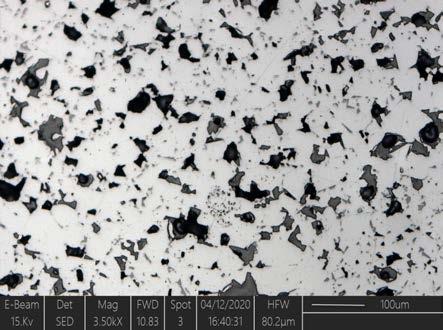
1.本发明涉及耐火材料制备技术领域,具体涉及一种铝灰制备铁铝尖晶石的方法。
背景技术:2.铝灰是指电解铝、铝加工及再生铝加工过程中排除的固体废弃物,根据其来源可分为铝电解过程中产生的铝灰,铝合金熔铸过程中的铝灰,再生铝加工过程中的铝灰。主要成分有金属铝、氧化铝、氮化铝以及一定量的氯化物和氟化物,若不回收直接堆放填埋,则会对土壤和地下水造成危害,另外铝灰中的氮化铝和水反应产生氨气,具有刺鼻性气味污染空气,因此,在2016年将铝灰列入《国家危险废物名录》。
3.铝灰根据来源不同,其成分有所不同,综合分析成分主要以金属铝(5
‑
20%)、氧化铝和氮化铝(30
‑
70%)冶金过程中添加的部分盐类等,根据成分含量,具有一定的利用价值。二次铝灰当前处理工艺主要分为无害化和资源化两类,无害化指二次铝灰经过处理去除氮化物、氟化物、盐分等杂质后得到无害化铝灰进行安全填埋,无害化工艺主要为酸浸、碱浸、洗涤等方式。资源化是指脱除有毒有害物质后二次铝灰经过高温或冷加工制成不同的产品如耐火材料、刚玉磨料、精炼剂和净水剂等,或是返回电解槽作为电解铝原料。铁铝尖晶石是是近几年作为镁铁铝尖晶石砖用于回转窑烧成带的新型耐火原料。其具有良好的挂窑皮性能、抗热震性以及抗侵蚀性等,同时还具有良好的柔韧性,更能适应窑壳的变形。不仅避免了回转窑用镁铬尖晶石砖使用过程中产生的六价铬对环境造成长期污染,同时也弥补了镁铝尖晶石耐火材料导热率高、挂窑皮性能差和白云石耐火材料易水化的缺陷。
4.铁铝尖晶石因为其成分为氧化铝和氧化亚铁所合成的,而氧化亚铁在空气中极易氧化为氧化铁,从而无法和氧化铝形成铁铝尖晶石结构,所以制备铁铝尖晶石大多数以电熔法生产,其能耗高,生产成本大。近几年,铁铝尖晶石也有采用烧结法生产的,专利“一种铁铝尖晶石的合成方法(cn102583462b)”中使用金属铝粉为原料,利用金属铝对氧化铁的还原作用,同时加入过量的氧化铁,实现氧化亚铁生成的条件,在真空的条件下烧结合成出纯的铁铝尖晶石。cn200510019267.6的“一种合成铁铝尖晶石及其制备方法”,是采用180目的al2o3、al(oh)3、al2o3
·
h2o以及矾土等与fe2o3、feo及fe3o4等含铁化合物混合,采用埋碳工艺合成。
5.上述专利采用真空气氛或埋碳工艺合成,其存在烧成工艺复杂、操作繁琐,生产成本高,市场竞争力小,不易推广等实际问题。
技术实现要素:6.针对背景技术所提出的问题,本发明旨在提供一种铝灰制备铁铝尖晶石的方法,其利用铝灰和氧化铝合成的铁铝尖晶石,不仅实现了铝灰的综合利用,减少了环境污染,同时获得高品质、工艺简单、成本低的的铁铝尖晶石。
7.本发明技术方案:1,一种铝灰制备铁铝尖晶石的方法,包括如下步骤:
(1)配比:取铝灰30
‑
55%、氧化铝0
‑
15%,含铁原料 35
‑
45%为主原料,外加0.1
‑
0.3%粘结剂和1
‑
3%高碳材料准确称量;(2)球磨:将配比中所称原料和自来水共同加入间歇式球磨机内进行研磨均化,研磨时间为13
‑
20h,研磨细度为20
‑
30um占95
‑
98%;(3)搅拌:将球磨均化合格的泥浆放入搅拌池内进行搅拌,搅拌时间60
‑
180min;(4)脱水:将搅拌好的泥浆进行压滤脱水,压滤压力为2.0
‑
2.5mpa,压滤泥饼水分为15
‑
20%;(5)预干燥:将压滤脱水后的泥饼输送至带式干燥器中,在150
‑
250℃温度下进行预干燥,预干燥后的泥饼水分控制在8
‑
14%;(5)成型:将预干燥泥饼用皮带输送至真空硬塑挤出集中进行挤出成型,获得半成品,真空度<
‑
0.085mpa;(6)干燥:所得半成品在带式干燥器中150
‑
300℃温度下干燥,干燥水分在0.5
‑
1%;(7)煅烧:将干燥物料输送至回转窑氛中在1300
‑
1600℃温度下煅烧,冷却后获得成品。
8.优选的,步骤(1)中所述铝灰为:al:5
‑
15%、al2o3:40
‑
60%、aln:10
‑
30%、mgo:5
‑
10%、sio2:0.5
‑
1.5%,细度为100
‑
200目。
9.优选的,步骤(1)中所述氧化铝为α
‑ꢀ
al2o3、γ
‑ꢀ
al2o3或al(oh)3。
10.优选的,步骤(1)中所述含铁原料为铁精粉或海绵铁粉。
11.优选的,步骤(1)中所述高碳材料为鳞片石墨或土状石墨。
12.优选的,步骤(1)中所述粘结剂为羧甲基纤维素或木质素磺酸钙。
13.优选的,步骤(2)中所述球磨机中球料水比例为:1.5
‑
2:0.8
‑
1:1
‑
1.5。
14.优选的,步骤(2)中所述球磨转速电频30
‑
50hz。
15.优选的,步骤(6)中所述半成品为φ10
‑
20mm*20
‑
25mm的条状。
16.本发明所述方法具有以下特点:1、利用铝灰制备铁铝尖晶石,其不仅对铝灰进行了合理使用,减少了铝灰危废对环境污染,同时铝灰来源广,成本低,大大降低了生产成本;2、利用铝灰所制备的铁铝尖晶石,铝灰中所含的金属铝、氮化铝在高温下,对氧化铁具有还原作用,促进了氧化亚铁的生成;铝灰中所含的氧化镁具有稳定氧化亚铁的作用,使其形成稳定的铁铝尖晶石,其铁铝尖晶石含量高达95%;3、配比中添加合适量的含碳材料,保证了氧化铁还原程度,解决了埋碳烧结存在的还原程度不易控制的问题;4、在湿法球磨机中进行长时间球磨获得超细粒度,降低了烧结温度,获得适中密度的铁铝尖晶石,对比电熔生产的铁铝尖晶石,在制备的镁铁铝尖晶石耐火材料中,因具有合适的气孔率和密度,其热震稳定性和荷重软化温度较好,也更易挂窑皮;5、本发明煅烧时不再要求烧成气氛,解决了目前非氧化气氛生产铁铝尖晶石工艺繁琐、不易控制的问题;6、本发明所采用全湿法、全封闭连续生产工艺,其优点是生产过程中无扬尘,生产环境良好,同时因为采用压滤脱水、真空成型、带式干燥的连续自动化生产方法,解决了以往湿法生产时间长、劳动强度大的问题,其生产运行成本约降低10
‑
30%;极具有市场竞争
力。
附图说明
17.图1本发明一种铝灰制备铁铝尖晶石的显微结构图;图2本发明一种铝灰制备铁铝尖晶石的xrd图谱。
具体实施方式
18.本发明结合下面实施例,对本发明进行详细、清楚、完整的描述,显然,本发明所保护的包含但不局限于以下实施例。
19.实施例1:1、配比:按照重量百分比,取铝灰55%、α
‑ꢀ
al2o33%,铁精粉 42%为主原料,外加0.1
‑
0.3%羧甲基纤维素钠和2%鳞片石墨准确称量;表1:铝灰检测指标进一步说明,实施例1中所述羧甲基纤维素钠为威怡化工有限公司生产,其型号为c1002;进一步说明,实施例1中所述α
‑ꢀ
al2o3含量>95%;2、球磨:将配比中所称原料和自来水共同加入间歇式球磨机内进行研磨均化,研磨时间为15h,研磨细度为28um占95
‑
98%;进一步说明,所述球磨机水料球重量比例为1.0:1.0:2.0;进一步说明,所述球磨机转速电频为45hz3、搅拌:将球磨均化合格的泥浆放入搅拌池内进行搅拌,搅拌时间60
‑
180min;4、脱水:将搅拌好的泥浆进行压滤脱水,压滤压力为2.0
‑
2.5mpa,压滤泥饼水分为17
‑
20%;5、预干燥:将压滤脱水后的泥饼自动输送至带式干燥器中,在150
‑
250℃温度下进行预干燥,预干燥后的泥饼水分控制在8
‑
15%;6、成型:将预干燥泥饼用皮带输送至真空硬塑挤出集中进行挤出成型,获得半成品,其中控制真空度<
‑
0.085mpa;7、干燥:所得半成品在带式干燥器中150
‑
300℃温度下进行干燥,干燥水分在0.5
‑
1%;8、煅烧:将干燥物料输送至回转窑氛中在1450℃温度下煅烧,冷却后获得成品;煅烧成品的显微结构和xrd见图1和图2。
20.实施例21、配比:按照重量百分比,取铝灰50%、γ
‑
al2o310%,海绵铁粉 40%为主原料,外加0.25%木质磺酸钙和2.5%土状石墨准确称量;
进一步说明,实施例2中铝灰化学指标同实施例1中所用化学指标;进一步说明,实施例1中所述γ
‑ꢀ
al2o3含量>90%;进一步说明,实施例2中所述木质素磺酸钙为上海庭若化工有限公司生产,其木质素含量≥65%;2、球磨:将配比中所称原料和自来水共同加入间歇式球磨机内进行研磨均化,研磨时间为17h,研磨细度为20um占95
‑
98%;进一步说明,所述球磨机水料球重量比例为1.0:1.0:1.8;进一步说明,所述球磨机转速电频为45hz;3、搅拌:将球磨均化合格的泥浆放入搅拌池内进行搅拌,搅拌时间60
‑
180min;4、脱水:将搅拌好的泥浆进行压滤脱水,压滤压力为2.5mpa,压滤泥饼水分为17%;5、预干燥:将压滤脱水后的泥饼自动输送至带式干燥器中,在150
‑
250℃温度下进行预干燥,预干燥后的泥饼水分控制在8
‑
15%;6、成型:将预干燥泥饼用皮带输送至真空硬塑挤出集中进行挤出成型,获得半成品,其中控制真空度<
‑
0.085mpa;7、干燥:所得半成品在带式干燥器中150
‑
300℃温度下进行干燥,干燥水分在0.5
‑
1%;8、煅烧:将干燥物料输送至回转窑中在1500℃温度下煅烧,冷却后获得成品;实施例31、配比:按照重量百分比,取铝灰:30%、γ
‑ꢀ
al2o3:20%,α
‑ꢀ
al2o3:7%、铁精粉 43%为主原料,外加0.25%木质磺酸钙和2.5%土状石墨准确称量;进一步说明,实施例3中铝灰化学指标同实施例1中所用化学指标;进一步说明,实施例3中所述木质素磺酸钙为上海庭若化工有限公司生产,其木质素含量≥65%;2、球磨:将配比中所称原料和自来水共同加入间歇式球磨机内进行研磨均化,研磨时间为14h,研磨细度为30um占95%;进一步说明,所述球磨机水料球重量比例为0.8:1.0:1.8;进一步说明,所述球磨机转速电频为40hz;3、搅拌:将球磨均化合格的泥浆放入搅拌池内进行搅拌,搅拌时间60
‑
180min;4、脱水:将搅拌好的泥浆进行压滤脱水,压滤压力为2.3mpa,压滤泥饼水分为15
‑
20%;5、预干燥:将压滤脱水后的泥饼自动输送至带式干燥器中,在150
‑
250℃温度下进行预干燥,预干燥后的泥饼水分控制在8
‑
15%;6、成型:将预干燥泥饼用皮带输送至真空硬塑挤出集中进行挤出成型,获得半成品,其中控制真空度<
‑
0.085mpa;7、干燥:所得半成品在带式干燥器中150
‑
300℃温度下进行干燥,干燥水分在0.5
‑
1%;8、煅烧:将干燥物料输送至回转窑中在1550℃温度下煅烧,冷却后获得成品;实施例4:1、配比:按照重量百分比,取铝灰45%、γ
‑
al2o3:10%,al(oh)3: 8%、铁精粉 37%为
主原料,外加0.25%羧甲基纤维素钠和1.5%鳞片石墨准确称量;进一步说明,实施例4中铝灰化学指标同实施例1中所用化学指标;进一步说明,实施例1中所述羧甲基纤维素钠为威怡化工有限公司生产,其型号为c1002;2、球磨:将配比中所称原料和自来水共同加入间歇式球磨机内进行研磨均化,研磨时间为15h,研磨细度为30um占95%;进一步说明,所述球磨机水料球重量比例为1.0:1.0:1.8;进一步说明,所述球磨机转速电频为40hz;3、搅拌:将球磨均化合格的泥浆放入搅拌池内进行搅拌,搅拌时间60
‑
180min;4、脱水:将搅拌好的泥浆进行压滤脱水,压滤压力为2.3mpa,压滤泥饼水分为15
‑
20%;5、预干燥:将压滤脱水后的泥饼自动输送至带式干燥器中,在150
‑
250℃温度下进行预干燥,预干燥后的泥饼水分控制在8
‑
15%;6、成型:将预干燥泥饼用皮带输送至真空硬塑挤出集中进行挤出成型,获得半成品,其中控制真空度<
‑
0.085mpa;7、干燥:所得半成品在带式干燥器中150
‑
300℃温度下进行干燥,干燥水分在0.5
‑
1%;8、煅烧:将干燥物料输送至回转窑中在1500℃温度下煅烧,冷却后获得成品;对比例将开封特耐工程材料股份有限公司的电熔铁铝尖晶石作为对比例1和实施例1分别制备镁铁铝尖晶石砖进行检测对比表1:镁铁铝尖晶石砖配比镁铁铝尖晶石砖的制备方法:将上述配比1#和2#中各类原料分别加入混练机中干混5min,然后加入4%亚硫酸纸浆废液再混15min,然后用150mpa的自动压砖机压制成150mm*50mm*50mm的砖坯,经110℃*24h干燥后1600℃*5h烧制而成。
21.测定结果如下:表2为对比例、实施例1理化指标检测结果:
通过上述理化指标对比,可以明显看出实施例1中烧结铁铝尖晶石对比电熔铁铝尖晶石的sio2%降低15%。
22.表3为对比例、实施例1制备镁铁铝尖晶石砖各项性能指标:通过上述常规性能对比,利用实施例1烧结铁铝尖晶石制备的镁铁铝尖晶石砖2#其热震稳定性和荷重软化温度略高于对比例电熔铁铝尖晶石制备的镁铁铝尖晶石砖1#,这是因为实施例1的杂质含量低、体积密度小、显气孔率大的原因,直接影响了制品的热震稳定性和荷重软化温度。
23.另将上述制备的镁铁铝尖晶石砖进行挂窑皮试验,因实施例1烧结铁铝尖晶石体积密度低、吸水率高,造成撩粉渗透量大,其挂窑皮性能明显优于对比例电熔铁铝尖晶石,其使用寿命更长,性价比更高。