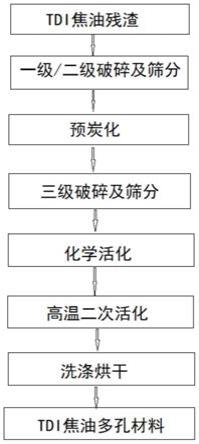
乙基己基酯,二(2,4,4-三甲基戊基)膦酸中为络合剂,正辛醇、异辛醇、仲辛醇为助溶剂,煤油或环己烷为稀释剂,配制络合萃取剂来处理废水,tda萃取去除率只有95~99%。上述公开专利的萃取方法仍对tda废水的处理效率不高,且处理成本偏高。
技术实现要素:10.有鉴于此,本发明的主要目的在于提供一种采用tdi固体焦油残渣制备多孔材料的方法及应用,该方法能够将固体焦油制备成多孔的材料,并用于tda废水的深度处理中,在减少碳排放的同时可大幅度降低废水的处理成本。
11.为实现上述发明目的,本发明采用以下技术方案:一种采用tdi固体焦油残渣制备多孔材料的方法,包括如下步骤:
12.1)将tdi固体焦油残渣先进行一级破碎和筛分,除去夹带的大颗粒残渣;
13.2)将经步骤1)筛分得到的固体颗粒继续进行二次破碎和筛分,得到粒径均匀的颗粒;
14.3)将经步骤2)筛分得到的固体颗粒在400-700℃下进行预炭化处理;
15.4)将经步骤3)预炭化后的固体颗粒继续进行三次破碎和筛分,以除去夹带的灰分;
16.5)将活化剂和经步骤4)筛分得到的焦油颗粒进行充分混合,以对焦油颗粒进行一级活化;
17.6)将经步骤5)一级活化后的混合物在惰性气体保护及600-900℃下进行高温二次活化;
18.7)将经步骤6)得到的活化产物冷却,洗涤除去夹带的灰分,烘干,即得tdi焦油多孔材料。
19.在本发明中,步骤1)及步骤2)中,tdi焦油固体残渣是经过list捏合机等设备在250-300℃下高温干燥造粒得到的固体残渣;通过步骤1)二次破碎和筛分和步骤2)二级破碎和筛分,可以降低残渣夹带的灰分,一级破碎粒径在300-2000μm,优选500-1200μm;二级破碎粒径在500-1600μm,优选600-1200μm,进一步优选800-1200μm。
20.在本发明中,步骤3)中,固体焦油颗粒的预炭化处理包括:预炭化温度优选为450-550℃,并采用氮气等惰性气体氛围保护,升温速率为1-5℃/min,炭化时间为5-12h,优选6-8h,进一步优选6-7h。预炭化可置于炭化炉等高温加热设备中,比如高温烘箱或马弗炉。
21.在本发明中,步骤4)中,对预炭化后的固体颗粒进行三级精细破碎,通过筛分得到粒径在600-1000μm的均匀颗粒。
22.在本发明中,步骤5)中,所述活化剂选自氢氧化钾、氯化锌和氯化镁中的一种或多种,其中,活化剂和固体焦油颗粒的混合质量比例为0.3-1:1,优选0.5-0.8:1。焦油颗粒进行该活化后,从无定形不规则的碳结构,转化为规则的,结构更稳定的石墨结构。
23.在本发明中,步骤6)中,所述高温二次活化条件包括:在惰性气体氛围下,从室温以2-10℃/min升温速率升温到600-900℃,优选600-800℃,活化时间为2-10h,优选4-8h,进一步优选5-6h;其中,惰性气体可选择为常用的氮气,高温活化设备可采用高温炭化炉,将经步骤5)活化剂活化后的固体焦油颗粒混合物置于其内部。在高温二次活化过程中,固体焦油颗粒中约200-500ppm的氯元素在约800℃下与氢元素结合,生成氯化氢气体从焦油中
得以脱除。
24.在本发明中,步骤7)中,可将经步骤6)得到的活化产物冷却至常温,例如15-25℃,例如20℃、25℃等。
25.在本发明中,步骤7)中,所述洗涤可包括:先采用稀酸洗涤,再用去离子水洗涤至ph为4-7,优选ph为6-7;稀酸的浓度为1-3mol/l,采用稀硫酸、稀盐酸或稀磷酸的一种或两种混合物。
26.在本发明中,所述一级破碎、二级破碎及三级破碎可根据其粒径需求具体选择适用的设备,例如采用研磨机进行二次破碎,或采用破碎机进行三级精细破碎。
27.本发明另一方面提供由上述方法制备的tdi固体焦油残渣多孔材料,其比表面积可达到4000-5500m2/g,碳元素为61-88%,氮元素为10-22%,氧元素为1-10%,氢元素为1-7%(均为质量分数)。
28.在本发明中,通过对焦油颗粒进行预炭化,可以降低可挥发分的含量,同时在400-700℃条件下将焦油颗粒中的部分碳和氮元素通过高温热解生成二氧化碳和氨气释放出去,用以调整焦油中碳原元素和氮元素的比例。采用高效活化剂在600-900℃下进行二次高温活化,进一步将焦油颗粒从无定形不规则的碳结构,转化为规则的,结构更稳定的类石墨多孔结构,由于该材料具有较高的比表面积,同时富含碳元素和氮元素,对于苯胺、甲基苯胺和甲苯二胺等有机胺类有机物具有较强的吸附效果。
29.本发明另一方面提供由上述方法制备的tdi固体焦油残渣多孔材料的应用,将其用于吸附处理tda废水。
30.为此本发明同时提供了一种tda废水深度处理的工艺方法,包括以下步骤:
31.将tda生产中的废水汽提脱除废水中的基环己醇,再通过本发明所制备的多孔材料进行吸附处理。
32.本发明所述的tda废水,来自于粗tda精馏脱水过程和含tda尾气捕集过程,废水中特征有机物为甲基环己醇、甲基苯胺和甲苯二胺。
33.在具体的实施方案中,将tda生产中的废水在汽提塔中采用低压蒸汽进行汽提,汽提蒸汽的压力为2-4barg,蒸汽和废水的汽提比例为0.3-1:10(体积比),优选0.6-1:10。
34.在具体的实施方案中,所述吸附处理包括:将本发明制备的多孔材料装填在吸附设备内,填充比例为0.3-0.8t/t废水,优选0.4-0.6t/t废水,吸附温度为30-60℃,优选35-45℃。
35.本发明与现有技术相比,具有以下优点:
36.(1)本发明通过对tdi焦油固体残渣资源化利用,可以制备出具有较高比表面积和较高饱和吸附容量的多孔材料,减少焦油的焚烧量,减少碳排放,具有显著的环境友好性;由以上步骤所制备的多孔材料的比表面积可达到4000-5500m2/g。
37.(2)本发明将制备的tdi焦油多孔吸附材料用于tda废水深度处理,有机物脱除效果好,且可以大幅度降低废水的处理成本;tda废水经过本发明吸附材料处理后,甲基环己醇含量可降至未检出,甲基苯胺和甲苯二胺含量可降至1ppm以下,cod含量可从3500-5000mg/l降至50mg/l以下。
38.综上,tdi固体焦油中含有较多的氯离子,直接用于废水处理领域中时,会缓慢产生大量的氯离子,对设备产生严重的腐蚀性,因此在水处理领域也对焦油吸附提出了更严
格的要求。为此,本发明从吸附材料的制备工艺上进行创新,通过一/二级破碎和筛分
‑‑
预炭化
‑‑
三级破碎和筛分—化学活化
‑‑
高温二次活化—洗涤烘干等工艺,可以实现tdi固体焦油颗粒的碳和氮元素组成比例的可调整性,提高对tda废水有机物的吸附效率;同时采用上述化学活化和高温二次活化工艺将tdi焦油颗粒进行处理,将焦油杂乱结构转化为规则的,结构更稳定的类石墨多孔结构,提高了材料的硬度和机械强度,因此在废水处理工艺中,大大降低吸附材料中有效组分的流失率和粉化速率,延长了材料的长周期使用寿命。
附图说明
39.图1是本发明实施例1中用于制备的tdi焦油多孔材料的工艺步骤示意图。
40.图2是本发明实施例1所采用的tda废水处理工艺流程简图。
41.图中标记如下:1-未处理的tda废水,2-汽提用蒸汽,3-汽提后尾气,4-汽提后tda废水,5-吸附后tda废水,t1-废水汽提塔,d1-废水吸附罐。
具体实施方式
42.下面结合实施例,对本发明予以进一步的说明,但本发明不限于所列出的实施例,还应包括在本发明申请所附权利要求书定义的技术方案的等效改进和变形。
43.其中本发明实施例及对比例中涉及到的测量方法及原料说明如下:
44.tdi焦油多孔材料的比表面积采用多点bet方法测量(仪器厂家,asap2020plus);
45.tdi焦油多孔材料的元素含量采用xrf光谱仪分析(厂家,德国斯派克);
46.tda废水中的甲基环己醇、甲苯二胺和甲基苯胺的含量采用气相色谱分析(厂家,agilent);
47.tda废水的cod含量采用哈希cod分析仪(厂家,哈希中国);
48.tdi焦油残渣和tda废水来源于万华化学tdi装置;活性炭为椰壳类活性炭,从市场购得。
49.如未特别说明,以下所用化学品为分析纯,本发明所涉及到含量均为质量含量。
50.实施例1
51.称量400g的tdi焦油固体颗粒通过研磨机进行一级和二级破碎和筛分后,除去掺杂的大块颗粒,得到粒径为600-1200μm的颗粒。将得到的焦油颗粒在550℃和氮气氛围中进行预炭化8h,控制升温速率为2℃/min。
52.取出炭化后的焦油颗粒,继续进行三级破碎和筛分,得到粒径为800-1000μm的焦油颗粒。
53.将焦油颗粒与氢氧化钾按照质量比为1:0.8进行均匀混合后转入高温炭化炉进行二次高温活化5h,在氮气氛围中控制升温速率为5℃/min,直至升温到800℃。
54.将高温活化后的焦油颗粒冷却至25℃,用1mol/l的稀硫酸洗涤两遍,然后再用去离子水洗涤至ph值为6-7,在95℃烘干,即得tdi焦油多孔吸附材料,然后填充到吸附罐d1中备用。
55.测定该材料的比表面积为5000m2/g,其中碳元素占82%,氮元素占15%,氧元素占2%,氢元素占1%(均为质量百分比)。
56.现有粗tda精馏脱水得到的一股废水,其有机物组成为甲基环己醇570ppm,甲苯二
胺90ppm,甲基苯胺145ppm。先在汽提塔t1中采用2barg蒸汽汽提后,继续在吸附罐d1进行吸附处理。
57.蒸汽和废水的汽提比例为0.3:10,吸附罐内多孔材料与废水的填充比例为0.7t/t废水,吸附温度为33℃。
58.废水经过上述方法处理后,甲基环己醇含量未检出,甲基苯胺和甲苯二胺含量0.5ppm,cod含量从3800mg/l降至42mg/l。多孔材料使用6个月后,吸附罐d1进出口的压差增加0.6kpa。
59.实施例2
60.称量400g的tdi焦油固体颗粒通过研磨机进行一级和二级破碎和筛分后,除去掺杂的大块颗粒,得到粒径为500-1400μm的颗粒。继续在450℃和氮气氛围中进行预炭化处理6h,控制升温速率为3℃/min,预炭化后的颗粒,继续进行三级破碎和筛分,得到粒径为800-1000μm的固体颗粒。
61.将固体颗粒与氢氧化钾按照质量比为1:0.8进行均匀混合后转入高温炭化炉进行高温活化5h,在氮气氛围中控制升温速率为5℃/min,直至升温到800℃。然后冷却至25℃后,用1mol/l的稀硫酸和去离子水洗涤至ph值为6-7,在95℃烘干,即得tdi焦油多孔吸附材料,然后填充到吸附罐d1中备用。
62.测定该材料的比表面积为4850m2/g,其中碳元素占80%,氮元素占14%,氧元素占4%,氢元素占2%(均为质量百分比)。
63.将实施例1中的tda废水,先在汽提塔t1中采用2barg蒸汽汽提后,继续在吸附罐d1进行吸附处理。
64.蒸汽和废水的汽提比例为0.7:10,吸附罐内多孔材料与废水的填充比例为0.5t/t废水,吸附温度为38℃。
65.废水经过处理后,甲基环己醇含量未检出,甲基苯胺和甲苯二胺含量0.8ppm,cod含量从3800mg/l降至45mg/l。多孔材料使用6个月后,吸附罐d1进出口的压差增加0.9kpa。
66.实施例3
67.称量400g的tdi焦油固体颗粒通过研磨机进行一级和二级破碎和筛分后,除去掺杂的大块颗粒,得到粒径为800-1600μm的颗粒。继续在450℃和氮气氛围中进行预炭化处理12h,控制升温速率为5℃/min,预炭化后的颗粒,继续进行三级破碎和筛分,得到粒径为600-800μm的固体颗粒。
68.将固体颗粒与氯化锌按照质量比为1:0.5进行均匀混合后转入高温炭化炉进行二次高温活化5h,在氮气氛围中控制升温速率为3℃/min,直至升温到600℃。
69.冷却至25℃后,采用1mol/l的稀磷酸和去离子水洗涤至ph值为6-7,在95℃烘干,即得tdi焦油多孔吸附材料,然后填充到吸附罐d1中备用。
70.测定该材料的比表面积为4000m2/g,其中碳元素占78%,氮元素占16%,氧元素占3%,氢元素占3%(均为质量百分比)。
71.将实施例1中的有tda废水,先在汽提塔t1中采用2barg蒸汽汽提后,继续在吸附罐d1进行吸附处理。
72.蒸汽和废水的汽提比例为0.7:10,吸附罐内多孔材料与废水的填充比例为0.3t/t废水,吸附温度为50℃。
73.废水经过处理后,甲基环己醇含量未检出,甲基苯胺和甲苯二胺含量1.0ppm,cod含量从3800mg/l降至49.5mg/l。多孔材料使用6个月后,吸附罐d1进出口的压差增加1.2kpa。
74.实施例4
75.称量400g的tdi焦油固体颗粒通过研磨机进行一级和二级破碎和筛分后,除去掺杂的大块颗粒,得到粒径为800-1200μm的颗粒。将得到的焦油颗粒在550℃和氮气氛围中进行预炭化7h,控制升温速率为4℃/min。
76.取出炭化后的焦油颗粒,继续进行三级破碎和筛分,得到粒径为800-1000μm的焦油颗粒。
77.将焦油颗粒与氢氧化钾按照质量比为1:0.8进行均匀混合后转入高温炭化炉进行二次高温活化6h,在氮气氛围中控制升温速率为5℃/min,直至升温到800℃。
78.将高温活化后的焦油颗粒冷却至25℃,用1mol/l的稀硫酸洗涤两遍,然后再用去离子水洗涤至ph值为7,在95℃烘干,即得tdi焦油多孔吸附材料,然后填充到吸附罐d1中备用。
79.测定该材料的比表面积为5500m2/g,其中碳元素占73%,氮元素占20%,氧元素占2%,氢元素占5%(均为质量百分比)。
80.将实施例1中的tda废水,先在汽提塔t1中采用2barg蒸汽汽提后,继续在吸附罐d1进行吸附处理。
81.蒸汽和废水的汽提比例为0.8:10,吸附罐内多孔材料与废水的填充比例为0.5t/t废水,吸附温度为42℃。
82.废水经过上述方法处理后,甲基环己醇含量未检出,甲基苯胺和甲苯二胺含量0.2ppm,cod含量从3800mg/l降至30mg/l。多孔材料使用6个月后,吸附罐d1进出口的压差增加0.3kpa。
83.对比例1
84.称取400g从市场采购的椰壳类活性炭,填充到吸附柱中进行备用。
85.将实施例1中的tda废水,在相同的条件下进行蒸汽汽提和吸附处理。
86.废水经过活性炭处理后,甲基环己醇含量72ppm,甲基苯胺和甲苯二胺含量28ppm,cod含量从3800mg/l降至200mg/l。活性炭使用6个月后,吸附罐d1进出口的压差增加3.8kpa。
87.对比例2
88.按照实施例4提供的方法制备一定量的tdi焦油多孔吸附材料,填充到吸附罐d1中备用。
89.然后将实施例1中的tda废水,不经过蒸汽汽提,直接通过吸附罐d1进行吸附处理,其他条件均一致。
90.废水经过处理后,甲基环己醇含量20ppm,甲基苯胺和甲苯二胺含量10ppm,cod从3800mg/l降至102mg/l。多孔材料使用6个月后,吸附罐d1进出口的压差增加0.3kpa。
91.对比例3
92.称量400g的tdi焦油固体颗粒进行破碎和筛分后,直接与氢氧化钾按照质量比为1:0.8进行均匀混合后转入高温炭化炉进行高温活化,冷却至25℃后,采用1mol/l的稀硫酸
和去离子水洗涤至ph值为6-7,在95℃烘干,即得tdi焦油多孔吸附材料,然后填充到吸附罐d1中备用。
93.测定该材料的比表面积为2550m2/g,其中碳元素占72%,氮元素占8%,氧元素占12%,氢元素占8%(均是质量百分比)。
94.将实施例1中的tda废水,先在汽提塔t1中采用2barg蒸汽汽提后,继续在吸附罐d1进行吸附处理。
95.废水经过处理后,甲基环己醇含量10ppm,甲基苯胺和甲苯二胺含量3ppm,cod含量从3800mg/l降至68mg/l。多孔材料使用6个月后,吸附罐d1进出口的压差增加1.8kpa。
96.对比例4
97.称量400g的tdi焦油固体颗粒通过研磨机进行一级和二级破碎和筛分后,除去掺杂的大块颗粒,得到粒径为800-1200μm的颗粒。将得到的焦油颗粒在550℃和氮气氛围中进行预炭化7h,控制升温速率为4℃/min。
98.取出炭化后的焦油颗粒,继续进行三级破碎和筛分,得到粒径为800-1000μm的焦油颗粒。
99.将上述焦油颗粒不经过化学活化和高温二次活化处理,直接用1mol/l的稀硫酸洗涤两遍,然后再用去离子水洗涤至ph值为7,在95℃烘干,即得tdi焦油多孔吸附材料,然后填充到吸附罐d1中备用。
100.测定该材料的比表面积为1750m2/g,其中碳元素占84%,氮元素占4%,氧元素占10%,氢元素占2%(均为质量百分比)。
101.将实施例1中的tda废水,先在汽提塔t1中采用2barg蒸汽汽提后,继续在吸附罐d1进行吸附处理。
102.蒸汽和废水的汽提比例为0.8:10,吸附罐内多孔材料与废水的填充比例为0.5t/t废水,吸附温度为42℃。
103.废水经过上述方法处理后,甲基环己醇含量15ppm,甲基苯胺和甲苯二胺含量25ppm,cod含量从3800mg/l降至160mg/l。多孔材料使用6个月后,吸附罐d1进出口的压差增加2.5kpa。
104.本文中吸附材料长周期使用后吸附材料床层压降变化数据,可用于表征吸附材料的粉化程度和使用寿命。
105.综上,将本发明各实施例之间对比以及与对比例1-4对比可得出如下结论:通过本发明实施例制备的焦油多孔材料,具有非常高的比表面积和对tda废水较好的处理效果,且有效组分的流失率低,延长了吸附材料长周期使用的寿命。对实现tdi固体焦油资源化利用,减少碳排放,具有显著的技术价值。
106.显然,本发明的上述实施例仅仅是为清楚地说明本发明所作的举例,而并非是对本发明的实施方式的限定。对于所属领域的普通技术人员来说,在上述说明的基础上还可以做出其它不同形式的变化或变动。这里无法对所有的实施方式予以穷举。凡是属于本发明的技术方案所引伸出的显而易见的变化或变动均在本发明涵盖的保护范围之内。