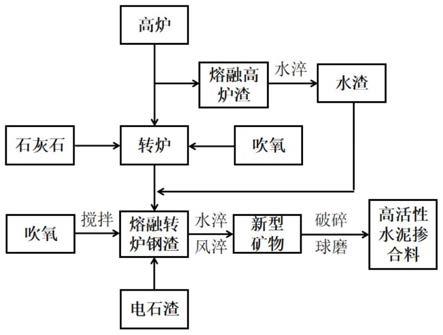
1.本发明属于转炉钢渣处理应用、工业固废建材资源化利用的技术领域,涉及一种高活性水泥掺合料的制备方法。
背景技术:2.转炉钢渣是钢铁冶金工业的固体废弃物,约占钢产量的11-15%,是钢铁工业的主要固体废物之一。转炉钢渣的利用回收技术难题造成大部分钢渣作为废物暂时被堆积遗弃,这不仅占用了大量的土地资源,还给周围环境带来严重的危害(破坏土壤、植被,污染空气、水源等)。
3.目前,转炉钢渣主要利用途径之一是将磁选过后的转炉钢渣尾渣,球磨得到转炉钢渣微粉,以作为水泥掺合料替代部分水泥,实现转炉钢渣尾渣的利用。但是,该种利用方式存在活性不足导致的混凝土早期强度问题和安定性差导致的混凝土体积稳定性问题,不仅利用方式较差,而且利用率也较低。
4.针对钢渣中早期活性较低和安定性不良等问题,国内外许多专家学者从钢渣产生的源头进行工艺和技术改进,到末端对落地钢渣尾渣的活性激发等各个流程阶段都对钢渣进行了改性实验,但改性后的钢渣的易磨性、在混凝土中用作矿物掺合料的活性、制备的混凝土早期强度、混凝土体积稳定性都很差;或者替换钢渣,或者加入外加剂,这些水泥掺合料的替换率低于30%。
5.例如:中国专利cn109336437a公开了一种石灰石微粉-钢渣粉-矿渣粉复合掺合料及其制备工艺,其中的矿渣粉性能满足gb/t18046-2017《用于水泥、砂浆和混凝土中的粒化高炉矿渣粉》标准中s95级技术要求,矿渣粉成本较高,而且石灰石微粉成本也比电石渣较高,转炉钢渣的利用率较低,不利于工业生产。
6.中国专利cn104961413a公开了一种利用钢渣微粉、矿渣微粉、粉煤灰做掺合料制备道路混凝土的方法,其中的钢渣微粉利用率也较低,钢渣微粉、矿渣微粉、粉煤灰的含量选择范围相同,所起作用相同,没有主辅料的区别。
7.中国专利cn112430005a公开了一种抑制碱骨料反应的水泥掺合料及其制备方法,其中的组成按重量份数计如下:废弃玻璃粉30-40份,炉渣15-20份,矿渣15-20份,羊毛3份,明胶0.3-0.5份,烷基苯磺硫酸盐3-5份,硫酸锂10-22份。故而水泥掺合料中的废弃玻璃粉为主要原料,炉渣和矿渣的利用率低,替换水泥的含量也低于30%。
8.中国专利cn104402266a公开了一种水泥掺合料的制备方法及应用,所述水泥掺合料原料包括重量百分比为1-80%的电石渣、1-80%的硅灰、2-50%的硝酸和/或硝酸铵、8-50%的尿素、以及0-50%的水;将所述混合料置入烧结炉中加热至300℃-1200℃至混合料燃烧;燃烧完毕后冷却至室温,得到以硅酸二钙为主要成分的炉渣,获得所述水泥掺合料。该种水泥掺合料中的主要原料结合实施例可知为尿素,对电石渣的利用率不高,并未利用转炉钢渣作为主要原料制备水泥掺合料,替换水泥的含量也低于30%。
9.中国专利cn1792972a公开了一种高抗硫水泥掺合料及其制备方法,其主要由高炉
14.9mpa,7天抗压强度为21.6-23.1mpa,28天抗压强度为41.9-44.5mpa。
23.优选地,所述的高活性水泥掺合料中按质量百分比计:cao 43.58-43.98%,sio
2 14.97-15.84%,al2o
3 5.21-6.70%,fe2o
3 17.60-19.35%,mgo 7.29-7.73%,p2o
5 1.85-2.16%,mno 2.50-2.76%,c/s 2.97-3.11,s/a 4.01-4.88。
24.本发明实施例提供的上述技术方案,至少具有如下有益效果:
25.上述方案中,本发明提出一种利用工业固废电石渣和高炉矿渣作为熔融转炉钢渣调质剂,在钢渣熔融状态下按照一定质量配比进行混合调质,再进行水淬/风淬急冷,球磨成粉得到一种高活性水泥掺合料的方法。
26.本发明辅料电石渣作为高钙含量的固废,可作为造渣剂石灰的替代品,从而调节钢渣中的c/s比,促进更多硅酸二钙、硅酸三钙的生成;同时,辅料高炉矿渣作为硅铝调质剂,降低调质产品的s/a,增加铝酸三钙等容易在早期水化的矿物含量;补充和丰富了转炉钢渣中的硅钙类潜在胶凝矿物和硅铝氧化物含量,提高了原转炉钢渣的早起胶凝活性。
27.本发明在反应炉进行升温直至熔融态转炉钢渣温度,且不需要频繁的磁选工艺,简化了原有工艺方法,之后进行保温和急冷,通过控制该保温时间和急冷冷却制度来降低f-cao的含量,早期胶凝活性较原转炉钢渣相比提高了将近一倍。
28.本发明实现了以熔融态转炉钢渣为主要原料,以工业固废为调质剂,利用全固废制备了活性达到s95级的高活性水泥掺合料,不仅实现了协同利用多种工业固废的目的,还有效提高了转炉钢渣的后续利用的质量水平。
29.本发明不仅解决了转炉钢渣因为活性和安定性导致的利用问题,还有效降低了其作为水泥掺合料的铁含量,在一定程度上提高了水泥的替代比例。
附图说明
30.为了更清楚地说明本发明实施例中的技术方案,下面将对实施例描述中所需要使用的附图作简单地介绍,显而易见地,下面描述中的附图仅仅是本发明的一些实施例,对于本领域普通技术人员来讲,在不付出创造性劳动的前提下,还可以根据这些附图获得其他的附图。
31.图1为本发明的一种高活性水泥掺合料的制备方法的工艺流程图;
32.图2为本发明实施例1的高活性水泥掺合料的制备方法的工艺流程图;
33.图3为本发明实施例1-6中转炉钢渣的xrd衍射图谱;
34.图4为本发明实施例1所制备的高活性水泥掺合料的xrd衍射图谱;
35.图5为本发明实施例2所制备的高活性水泥掺合料的xrd衍射图谱;
36.图6为本发明实施例1-2中的转炉钢渣和高活性水泥掺合料分别制备的水泥胶砂的强度对比图。
具体实施方式
37.为使本发明要解决的技术问题、技术方案和优点更加清楚,下面将结合附图及具体实施例进行详细描述。
38.下表1为水泥、转炉钢渣、电石渣、高炉矿渣的化学组成,wt%;如图3所示,转炉钢渣的xrd衍射图谱列出了转炉钢渣的矿物组成。
39.表1转炉钢渣、电石渣、高炉矿渣的化学组成,wt%
40.成分caosio2al2o3fe2o3mgop2o5mno水泥52.3526.187.633.764.590.130.13转炉钢渣41.0415.962.1720.037.772.306.39矿粉38.7833.0616.450.816.37
‑‑‑‑‑‑‑
电石渣84.44.534.010.901.990.050.12
41.如图1所示,一种高活性水泥掺合料的制备方法,所述方法是通过利用转炉生产过程中产生的转炉钢渣作为主要原料、电石渣和高炉矿渣作为辅料混合后在反应炉进行升温,直至熔融态转炉钢渣温度,经过保温处理后通过水淬或者风淬急冷至室温后的新型矿物,之后破碎球磨成粉末,从而得到高活性水泥掺合料。其中:高炉炼铁过程中产生的熔融高炉渣经过水淬得到的水渣即为辅料中的高炉矿渣,转炉炼钢过程中需要加入石灰石和吹氧从而得到未被磁选的转炉钢渣,在升温过程中需要吹氧和搅拌从而制得熔融的转炉钢渣。
42.实施例1
43.取转炉钢渣320g,掺量占比为80%;电石渣40g,掺量占比为10%;高炉矿渣40g,掺量占比为10%。将三者混合均匀后盛入坩埚,再将坩埚放入箱式马弗炉中升温到1350℃。具体升温过程为:20-200℃为10℃/min,200-1350℃为15℃/min。保温30min结束后,将样品连同坩埚取出进行风机急冷降温。将冷却后的样品进行破碎,通过振动磨磨成粉,分别进行xrd和化学成分测试,测试结果如表2和图4所示。
44.如表2所示,转炉钢渣、电石渣、高炉矿渣在高温条件下模拟利用电石渣和高炉矿渣作为熔融态转炉钢渣调质剂制备的高活性水泥掺合料的钙、铝含量有明显增加,铁含量降低,且c/s水平已经达到3.0以上,接近甚至超过一般水泥熟料的c/s。而且s/a与原来相比大大降低。由图4中的xrd衍射图谱分析可以得到,制备的高活性水泥掺合料中出现了原转炉钢渣中没有的硅酸三钙衍射峰;feo在高温条件下转变成磁铁矿和赤铁矿。同时,还出现了铝酸三钙和莫来石等水化活性较高的矿物组分。
45.表2原转炉钢渣与实施例1中高活性水泥掺合料的化学成分对比,wt%
46.材料caosio2al2o3fe2o3mgop2o5mnoc/ss/a钢渣41.0415.962.1720.037.772.306.392.7512.50实施例143.5814.975.2119.357.732.162.763.114.88
47.实施例2
48.取转炉钢渣280g,掺量占比为70%;电石渣60g,掺量占比为15%;高炉矿渣60g,掺量占比为15%。将三者混合均匀后盛入坩埚,再将坩埚放入箱式马弗炉中升温到1350℃。具体升温过程为:20-200℃为10℃/min,200-1350℃为15℃/min。保温30min结束后,将样品连同坩埚取出进行水淬急冷降温。将冷却后的样品进行破碎,通过振动磨磨成粉,分别进行xrd和化学成分测试,测试结果如表3和图5所示。
49.如表3所示,转炉钢渣、电石渣、高炉矿渣在高温条件下模拟利用电石渣和高炉矿渣作为熔融态转炉钢渣调质剂制备的高活性水泥掺合料的钙、铝含量有明显增加,铁含量降低,且c/s水平已经达到3.0以上,接近甚至超过一般水泥熟料的c/s。而且s/a与原来相比大大降低。由图5中的xrd衍射图谱分析可以得到,制备的高活性水泥掺合料中出现了原转
炉钢渣中没有的硅酸三钙衍射峰;feo在高温条件下转变成磁铁矿和赤铁矿。同时,还出现了铝酸三钙和莫来石等水化活性较高的矿物组分。获得的高活性水泥掺合料在达到国家标准42.5mpa的基础上最高替代料可达35%。
50.表3原转炉钢渣与实施例2中高活性水泥掺合料的化学成分对比,wt%
51.材料caosio2al2o3fe2o3mgop2o5mnoc/ss/a钢渣41.0415.962.1720.037.772.306.392.7512.50实施例243.9815.846.7017.607.291.852.502.974.01
52.实施例3
53.如图2所示,取转炉钢渣300g,掺量占比为75%;电石渣50g,掺量占比为12.5%;高炉矿渣50g,掺量占比为12.5%。将三者混合均匀后盛入坩埚,再将坩埚放入箱式马弗炉中升温到1350℃。具体升温过程为:20-200℃为10℃/min,200-1350℃为15℃/min。保温30min结束后,将样品连同坩埚取出进行风机急冷降温。将冷却后的样品进行破碎,通过振动磨磨成粉,分别进行xrd和化学成分测试,测试结果如表4所示。
54.如表4所示,转炉钢渣、电石渣、高炉矿渣在高温条件下模拟利用电石渣和高炉矿渣作为熔融态转炉钢渣调质剂制备的高活性水泥掺合料的钙、铝含量有明显增加,铁含量降低,且c/s水平已经达到3.0以上,接近甚至超过一般水泥熟料的c/s。而且s/a与原来相比大大降低。制备的高活性水泥掺合料中出现了原转炉钢渣中没有的硅酸三钙衍射峰;feo在高温条件下转变成磁铁矿和赤铁矿。同时,还出现了铝酸三钙和莫来石等水化活性较高的矿物组分。获得的高活性水泥掺合料在达到国家标准42.5mpa的基础上最高替代料可达33%。
55.表4原转炉钢渣与实施例3中高活性水泥掺合料的化学成分对比,wt%
56.材料caosio2al2o3fe2o3mgop2o5mnoc/ss/a钢渣41.0415.962.1720.037.772.306.392.7512.50实施例343.7815.235.9218.237.451.932.633.014.43
57.实施例4
58.取转炉钢渣290g,掺量占比为72.5%;电石渣55g,掺量占比为13.75%;高炉矿渣55g,掺量占比为13.75%。将三者混合均匀后盛入坩埚,再将坩埚放入箱式马弗炉中升温到1350℃。具体升温过程为:20-200℃为10℃/min,200-1350℃为15℃/min。保温30min结束后,将样品连同坩埚取出进行水淬急冷降温。将冷却后的样品进行破碎,通过振动磨磨成粉,分别进行xrd和化学成分测试,测试结果如表5所示。
59.如表5所示,转炉钢渣、电石渣、高炉矿渣在高温条件下模拟利用电石渣和高炉矿渣作为熔融态转炉钢渣调质剂制备的高活性水泥掺合料的钙、铝含量有明显增加,铁含量降低,且c/s水平已经达到3.0以上,接近甚至超过一般水泥熟料的c/s。而且s/a与原来相比大大降低。制备的高活性水泥掺合料中出现了原转炉钢渣中没有的硅酸三钙衍射峰;feo在高温条件下转变成磁铁矿和赤铁矿。同时,还出现了铝酸三钙和莫来石等水化活性较高的矿物组分。获得的高活性水泥掺合料在达到国家标准42.5mpa的基础上最高替代料可达34%。
60.表5原转炉钢渣与实施例4中高活性水泥掺合料的化学成分对比,wt%
61.材料caosio2al2o3fe2o3mgop2o5mnoc/ss/a钢渣41.0415.962.1720.037.772.306.392.7512.50实施例443.6515.095.5417.867.361.892.572.994.25
62.实施例5
63.如图2所示,取转炉钢渣310g,掺量占比为77.5%;电石渣45g,掺量占比为11.25%;高炉矿渣45g,掺量占比为11.25%。将三者混合均匀后盛入坩埚,再将坩埚放入箱式马弗炉中升温到1350℃。具体升温过程为:20-200℃为10℃/min,200-1350℃为15℃/min。保温30min结束后,将样品连同坩埚取出进行风机急冷降温。将冷却后的样品进行破碎,通过振动磨磨成粉,分别进行xrd和化学成分测试,测试结果如表6所示。
64.如表6所示,转炉钢渣、电石渣、高炉矿渣在高温条件下模拟利用电石渣和高炉矿渣作为熔融态转炉钢渣调质剂制备的高活性水泥掺合料的钙、铝含量有明显增加,铁含量降低,且c/s水平已经达到3.0以上,接近甚至超过一般水泥熟料的c/s。而且s/a与原来相比大大降低。制备的高活性水泥掺合料中出现了原转炉钢渣中没有的硅酸三钙衍射峰;feo在高温条件下转变成磁铁矿和赤铁矿。同时,还出现了铝酸三钙和莫来石等水化活性较高的矿物组分。获得的高活性水泥掺合料在达到国家标准42.5mpa的基础上最高替代料可达31%。
65.表6原转炉钢渣与实施例5中高活性水泥掺合料的化学成分对比,wt%
66.材料caosio2al2o3fe2o3mgop2o5mnoc/ss/a钢渣41.0415.962.1720.037.772.306.392.7512.50实施例543.8515.536.3318.767.612.032.693.074.65
67.实施例6
68.取转炉钢渣306g,掺量占比为76.5%;电石渣47g,掺量占比为11.75%;高炉矿渣47g,掺量占比为11.75%。将三者混合均匀后盛入坩埚,再将坩埚放入箱式马弗炉中升温到1350℃。具体升温过程为:20-200℃为10℃/min,200-1350℃为15℃/min。保温30min结束后,将样品连同坩埚取出进行水淬急冷降温。将冷却后的样品进行破碎,通过振动磨磨成粉,分别进行xrd和化学成分测试,测试结果如表7所示。
69.如表7所示,转炉钢渣、电石渣、高炉矿渣在高温条件下模拟利用电石渣和高炉矿渣作为熔融态转炉钢渣调质剂制备的高活性水泥掺合料的钙、铝含量有明显增加,铁含量降低,且c/s水平已经达到3.0以上,接近甚至超过一般水泥熟料的c/s。而且s/a与原来相比大大降低。制备的高活性水泥掺合料中出现了原转炉钢渣中没有的硅酸三钙衍射峰;feo在高温条件下转变成磁铁矿和赤铁矿。同时,还出现了铝酸三钙和莫来石等水化活性较高的矿物组分。获得的高活性水泥掺合料在达到国家标准42.5mpa的基础上最高替代料可达32%。
70.表7原转炉钢渣与实施例6中高活性水泥掺合料的化学成分对比,wt%
71.材料caosio2al2o3fe2o3mgop2o5mnoc/ss/a钢渣41.0415.962.1720.037.772.306.392.7512.50实施例643.8215.386.1517.497.541.972.502.664.56
72.将实施例1和2所制备的高活性水泥掺合料与原转炉钢渣按照国家标准《gb/
t17671-1999》制备水泥胶砂来检测三者的活性。其具体配比如表4所示。
73.表4原转炉钢渣与案例1、案例2中的高活性水泥掺合料制备水泥胶砂的配比
[0074][0075]
将制备的水泥胶砂按照国家标准《gb/t17671-1999》进行养护和强度检测。其抗压强度对比如图4所示。
[0076]
如图4结果所示,使用所述方法中的高活性水泥掺合料制备水泥胶砂的强度较原转炉钢渣相比有大幅度提升。尤其是实施例2中3天强度提高接近一倍,同样活性指数也提高一倍。原转炉钢渣作为水泥掺合料的活性指数为68%,而该发明所得的高活性水泥掺合料28天活性指数高达86%。
[0077]
上述方案中,本发明提出一种利用工业固废电石渣和高炉矿渣作为熔融转炉钢渣调质剂,在钢渣熔融状态下按照一定质量配比进行混合调质,再进行水淬/风淬急冷,球磨成粉得到一种高活性水泥掺合料的方法。
[0078]
本发明辅料电石渣作为高钙含量的固废,可作为造渣剂石灰的替代品,从而调节钢渣中的c/s比,促进更多硅酸二钙、硅酸三钙的生成;同时,辅料高炉矿渣作为硅铝调质剂,降低调质产品的s/a,增加铝酸三钙等容易在早期水化的矿物含量;补充和丰富了转炉钢渣中的硅钙类潜在胶凝矿物和硅铝氧化物含量,提高了原转炉钢渣的早起胶凝活性。
[0079]
本发明在反应炉进行升温直至熔融态转炉钢渣温度,且不需要频繁的磁选工艺,简化了原有工艺方法,之后进行保温和急冷,通过控制该保温时间和急冷冷却制度来降低f-cao的含量,早期胶凝活性较原转炉钢渣相比提高了将近一倍。
[0080]
本发明实现了以熔融态转炉钢渣为主要原料,以工业固废为调质剂,利用全固废制备了活性达到s95级的高活性水泥掺合料,不仅实现了协同利用多种工业固废的目的,还有效提高了转炉钢渣的后续利用的质量水平。
[0081]
本发明不仅解决了转炉钢渣因为活性和安定性导致的利用问题,还有效降低了其作为水泥掺合料的铁含量,在一定程度上提高了水泥的替代比例。
[0082]
以上所述是本发明的优选实施方式,应当指出,对于本技术领域的普通技术人员来说,在不脱离本发明所述原理的前提下,还可以做出若干改进和润饰,这些改进和润饰也应视为本发明的保护范围。