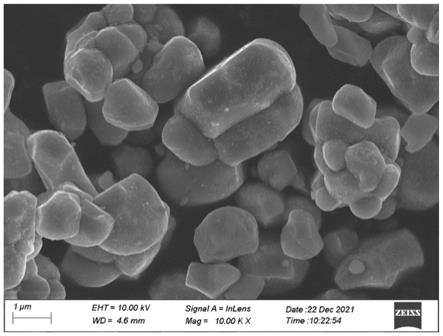
1.本发明涉及电池技术领域,涉及一种改善无钴正极材料压实密度的方法、无钴正极材料和锂离子电池。
背景技术:2.随着环境的持续恶化,以及化石燃料的逐渐匮乏,人类对能源的需求更多地向清洁化,便携化发展。由于锂离子二次电池无污染,储能大,易携带的优点,其被广泛应用于手机电池、计算机、摄像机等3c设备之中。随着技术的发展,高能量密度的锂离子电池越来越广泛地应用在混合式动力汽车,甚至纯电动汽车,为人们的出行提供动力。
3.镍锰钴酸锂三元正极材料具有能量密度大,循环性能好,安全环保等优点,是目前电池正极材料研究的一个重要方向。然而由于钴资源储存较少,造成了钴价格较贵,同时易被操控价格,且钴对环境污染较大。因此,无钴镍锰酸锂材料的开发在控制成本,增强市场耐受性方面有着巨大的优势。
4.无钴镍锰酸锂材料中镍主要起到增加比容量的作用,锰主要起到稳定材料骨架的作用。随着政府补贴的逐渐退坡以及新能源安全事故的频发,人们对材料成本和安全性变得尤为关注,无钴镍锰酸锂材料的开发逐渐向中低镍方向发展。
5.随着无钴正极材料的广泛应用,提高能量密度也是主要的研究方向之一。尤其地,由于无钴中低镍正极材料锰含量较高,电芯制造的涂布以及辊压工序中存在压实偏低的问题,这无形中造成电芯体积能量密度低,如何提高中低镍材料的压实成为待解决的一个重要问题。
6.现有技术材料混锂一次烧结后,材料颗粒分布较为均匀,在匀浆涂布后,进行极片辊压过程中,压实难以达到,同时颗粒粒径容易压碎。同时,无钴正极材料作为一种新型的正极材料,尚无相关有效的提高其压实密度的方案。
7.因而,有必要提供一种改善无钴正极材料压实密度的方法。
技术实现要素:8.针对现有技术中存在的上述问题,本发明的目的在于提供一种改善无钴正极材料压实密度的方法、无钴正极材料和锂离子电池。本发明利用高温固相法来合成无钴单晶正极材料,不需要增加额外的工艺即可拓宽材料的粒度分布,改善材料的压实和电化学性能。
9.为达上述目的,本发明采用以下技术方案:
10.第一方面,本发明提供一种改善无钴正极材料压实密度的方法,所述方法包括以下步骤:
11.(1)制备一烧料:
12.(a)将锂源和镍锰氢氧化物前驱体按照li/(ni+mn)摩尔比=m混合,一次烧结,得到小粒径一烧料;
13.(b)将锂源、镍氧化物和锰氧化物按照li/(ni+mn)摩尔比=n混合,一次烧结,得到大粒径一烧料,其中,m《n;
14.(2)共混包覆:
15.将所述的小粒径一烧料、大粒径一烧料和包覆物混合,二次烧结,得到无钴正极材料。
16.本发明的方法中,步骤(a)和步骤(b)无顺序限定,可以先制备小粒径一烧料,再制备大粒径一烧料;也可以先制备大粒径一烧料,再制备小粒径一烧料;还可以二者同时制备。本发明不作具体限定。
17.本发明利用高温固相法来合成无钴单晶正极材料,通过调整li/(ni+mn)摩尔比和原料,可以在相同烧结条件下控制形成两种形貌各异的大小颗粒,不需要增加额外的工艺,包覆的同时完成大小颗粒混掺,拓宽材料的粒度分布,改善材料的压实和电化学性能。
18.本发明对锂源的具体种类不作限定,例如可以是lioh和碳酸锂中的至少一种。
19.本发明对锂源的形态不作限定,例如可以是粉末。
20.以下作为本发明优选的技术方案,但不作为对本发明提供的技术方案的限制,通过以下优选的技术方案,可以更好的达到和实现本发明的技术目的和有益效果。
21.优选地,m为1.03-1.05,例如1.03、1.04或1.05等;n为1.1-1.2,例如1.1、1.12、1.13、1.15、1.17或1.2等。
22.优选地,所述镍氧化物和锰氧化物对应的ni/mn摩尔比与所述镍锰氢氧化物前驱体对应的ni/mn摩尔比保持一致。
23.优选地,所述镍锰氢氧化物前驱体的化学式为ni
x
mny(oh)2,其中,0.40≤x≤0.70,例如x可以是0.40、0.45、0.50、0.55、0.60、0.65或0.70等;0.30≤y≤0.60,例如y可以是0.30、0.35、0.40、0.45、0.50、0.55或0.60等。本发明的方法对于改善无钴中低镍正极材料的压实密度的效果尤其突出。
24.优选地,步骤(a)所述锂源的粒径d50≤10μm,例如10μm、9μm、8μm、7μm、6μm、5μm、4μm、3μm、2μm或1μm等。
25.优选地,步骤(a)所述混合的转速为1000-2500rpm,例如1000rpm、1200rpm、1500rpm、1700rpm、2000rpm、2200rpm、2400rpm或2500rpm等;时间为5-15min,例如5min、8min、10min、13min或15min等。
26.优选地,步骤(b)所述锂源的粒径d50≤10μm,例如10μm、9μm、8μm、7μm、6μm、5μm、4μm、3μm、2μm或1μm等。
27.优选地,步骤(b)所述混合的转速为1000-2500rpm,例如1000rpm、1200rpm、1500rpm、1700rpm、2000rpm、2200rpm、2400rpm或2500rpm等;时间为5-15min,例如5min、8min、10min、13min或15min等。
28.作为本发明所述方法的一个优选技术方案,步骤(a)所述一次烧结和步骤(b)所述一次烧结的温度在950-1020℃范围内,温度例如950℃、960℃、970℃、980℃、990℃、1000℃、1010℃或1020℃等。
29.优选地,步骤(a)所述一次烧结和步骤(b)所述一次烧结的时间在8-12h范围内,时间例如8h、9h、10h、10.5h、11h或12h等。
30.优选地,步骤(a)所述一次烧结和步骤(b)所述一次烧结的升温速率在1-4℃/min
范围内,升温速率例如1℃/min、2℃/min、2.5℃/min、3℃/min或4℃/min等。
31.优选地,步骤(a)所述一次烧结和步骤(b)所述一次烧结的气氛为空气。
32.优选地,步骤(a)所述一次烧结和步骤(b)所述一次烧结的温度相同。
33.优选地,步骤(a)所述一次烧结和步骤(b)所述一次烧结在同一辊道窑炉中进行。
34.本发明的方法可以在相同烧结条件下,仅仅通过改变li/(ni+mn)摩尔比和原料即可获得高压实的无钴正极材料,不需要增加额外的工艺,适合大规模工业化生产。
35.上述“相同烧结条件”指的是制备小粒径一烧料和大粒径一烧料的烧结过程相同,可以在同一台设备中烧结,例如可以简便地将二者对应的混合原料放入同一辊道窑炉中,以某一温度烧结一定时间。也即在相同的烧结温度、气氛、时间,可一次性获得小粒径一烧料和大粒径一烧料。
36.优选地,步骤(2)所述包覆物包括zro2、tio2、al2o3、wo3和h3bo3中的至少一种。
37.优选地,步骤(2)中,小粒径一烧料和大粒径一烧料的质量比为1:(1-3),例如1:1、1:1.5、1:2、1:2.5、1:2.8或1:3等。
38.优选地,步骤(2)所述二次烧结的温度在300-700℃范围内,温度例如300℃、350℃、370℃、400℃、450℃、500℃、550℃、600℃、650℃或700℃等。
39.优选地,步骤(2)所述二次烧结的时间在4-7h范围内,时间例如4h、5h、5.5h、6h或7h等。
40.优选地,步骤(2)所述二次烧结的升温速率在1-3℃/min范围内,升温速率例如1℃/min、2℃/min或3℃/min等。
41.第二方面,本发明提供一种无钴正极材料,所述无钴正极材料由第一方面所述的方法制备得到。
42.第三方面,本发明提供一种锂离子电池,所述所述锂离子电池包括如第二方面所述的无钴正极材料。
43.与已有技术相比,本发明具有如下有益效果:
44.本发明利用高温固相法来合成无钴单晶正极材料,通过调整li/(ni+mn)摩尔比和原料,可以在相同烧结条件下控制形成两种形貌各异的大小颗粒,不需要增加额外的工艺,包覆的同时完成大小颗粒混掺,拓宽材料的粒度分布,改善材料的压实和电化学性能。
附图说明
45.图1为实施例1中的第一一烧料(简称ys-1)的sem图。
46.图2为实施例1中的第二一烧料(简称ys-2)的sem图。
47.图3为实施例1中的无钴正极材料(简称es-1)的sem图。
具体实施方式
48.下面结合附图并通过具体实施方式来进一步说明本发明的技术方案。
49.实施例1
50.本实施例提供了一种改善无钴正极材料压实密度的方法,所述方法包括以下步骤:
51.第一混合料:将lioh粉末和无钴前驱体ni
0.60
mn
0.40
(oh)2以li/(ni+mn)摩尔比=
1.05在高速混合设备中进行混合,混合条件:转速2000rpm混料10min。
52.第二混合料:将lioh粉末、nio和mno2在高速混合设备中进行混合,其中,li/(ni+mn)摩尔比=1.1,nio和mno2的摩尔比为0.6:0.4,混合条件:转速2000rpm混料10min。
53.煅烧阶段:将混合好的第一混合料和第二混合料在空气氛围(氧浓度大于20%,空气流量:60l/min),在辊道窑中将第一混合料和第二混合料分别投入窑炉进行烧结,以4℃/min升温至990℃高温反应10h,然后自然降温到室温,使用破碎设备进行粉碎,得到的第一一烧料(简称ys-1,其sem图参见图1)和第二一烧料(简称ys-2,其sem图参见图2)。此处第一一烧料和第二一烧料未进行混合步骤。
54.包覆阶段:将第一一烧料与第二一烧料和包覆物质进行混合,其中,第一一烧料和第二一烧料的质量比为1:3,包覆物质为zro2+al2o3(zro2和al2o3的包覆量分别为2000ppm和1000ppm),在辊道窑炉中以2℃/min升温至600℃高温反应5h,自然降温到室温,得到包覆二烧的成品材料,也即无钴正极材料(简称为es-1,其sem图参见图3)。
55.通过图1、图2和图3可知,从形貌上来看,ys-1颗粒粒径较小,ys-2颗粒粒径较大,最终成品材料的颗粒粒径适中。
56.分别采用上述的ys-1、ys-2和成品材料es-1(也即无钴正极材料)作为正极材料进行匀浆涂布,匀浆涂布工艺:取适量上述的成品材料进行匀浆涂布,其中,正极材料:sp:pvdf胶液中的pvdf(质量比)=92:4:4,pvdf胶液固含量为6.25%。
57.涂布后进行极片压实测试和扣电测试,其中,极片压实测试按照下述方法测试:用匀浆涂布后极片在辊压机进行辊压,辊压后测量厚度计算压实的大小,材料的压实为滚压后极片对折断裂时的压实(结果参见表1)。
58.扣电测试采用上述涂布后的极片辊压至极限压实密度,采用cr2032壳体进行扣电组装,电解液选用新宙邦a60电解液,测试条件如下:
59.测试电压范围为3v~4.2v;测试0.1c首次充放电容量以及0.1c充电、1c放电容量,以及0.5c/1c循环50周容量保持率,测试结果如表1所示。
60.表1
[0061][0062]
从压实的结果上来看,经过该方法合成的正极材料压实密度得到了明显提高。通过对比图表中数据可以发现,经过该种方法合成正极材料由于压实的提高,容量得到了明显的提高。
[0063]
实施例2
[0064]
本实施例提供了一种改善无钴正极材料压实密度的方法,所述方法包括以下步骤:
[0065]
第一混合料:将li2co3粉末和无钴前驱体ni
0.60
mn
0.40
(oh)2以li/(ni+mn)摩尔比=
1.03在高速混合设备中进行混合,混合条件:转速2500rpm混料5min。
[0066]
第二混合料:将li2co3粉末、nio和mno2在高速混合设备中进行混合,其中,li/(ni+mn)摩尔比=1.1,nio和mno2的摩尔比为0.6:0.4,混合条件:转速2000rpm混料10min。
[0067]
煅烧阶段:将混合好的第一混合料和第二混合料在空气氛围(氧浓度大于20%,空气流量:50l/min),在辊道窑中将第一混合料和第二混合料分别投入窑炉进行烧结,以3℃/min升温至1000℃高温反应8h,然后自然降温到室温,使用破碎设备进行粉碎,得到的第一一烧料和第二一烧料。
[0068]
包覆阶段:将第一一烧料、第二一烧料和包覆物质进行混合包覆,其中,第一一烧料和第二一烧料的质量比为1:1.5,包覆物质为zro2(zro2的使用量为3000ppm)、在辊道窑炉中以3℃/min升温至650℃高温反应4h,自然降温到室温,得到包覆二烧的成品材料,也即无钴正极材料(简称为es-2)。
[0069]
实施例3
[0070]
本实施例提供了一种改善无钴正极材料压实密度的方法,所述方法包括以下步骤:
[0071]
第一混合料:将li2co3粉末和无钴前驱体ni
0.70
mn
0.30
(oh)2以li/(ni+mn)摩尔比=1.04在高速混合设备中进行混合,混合条件:转速2500rpm混料5min。
[0072]
第二混合料:将li2co3粉末、nio和mno2在高速混合设备中进行混合,其中,li/(ni+mn)摩尔比=1.2,nio和mno2的摩尔比为0.7:0.3,混合条件:转速1000rpm混料15min。
[0073]
煅烧阶段:将混合好的第一混合料和第二混合料在空气氛围(氧浓度大于20%,空气流量:60l/min),在辊道窑中将第一混合料和第二混合料分别投入窑炉进行烧结,以2℃/min升温至970℃高温反应11h,然后自然降温到室温,使用破碎设备进行粉碎,得到的第一一烧料和第二一烧料。
[0074]
包覆阶段:将第一一烧料、第二一烧料和包覆物质进行混合包覆,其中,第一一烧料和第二一烧料的质量比为1:2,包覆物质为wo3(wo3的使用量为2000ppm)、在辊道窑炉中以3℃/min升温至550℃高温反应6h,自然降温到室温,得到包覆二烧的成品材料,也即无钴正极材料(简称为es-3)。
[0075]
实施例4
[0076]
本实施例与实施例1的区别在于,第一一烧料和第二一烧料的质量比为1:0.5。得到的无钴正极材料简称为es-4。
[0077]
实施例5
[0078]
本实施例与实施例1的区别在于,第一一烧料和第二一烧料的质量比为1:3.5。得到的无钴正极材料简称为es-5。
[0079]
对比例1
[0080]
本对比例与实施例1的区别在于,预先将制备第一混合料和第二混合料的所有原料混合,进行一次烧结。
[0081]
对比例2
[0082]
本对比例与实施例1的区别在于,制备第一混合料时,li/(ni+mn)摩尔比=1.1。
[0083]
对比例3
[0084]
本对比例与实施例1的区别在于,将nio和mno2替换为ni
0.60
mn
0.40
(oh)2。
[0085]
采用与实施例1相同的方法进行匀浆涂布、极片压实测试和扣电测试,结果参见表2。
[0086]
表2
[0087][0088]
压实密度是电芯生产过程中一个重要指标,不仅影响电芯体系的体积能量密度,同时对容量发挥,电芯的功率性能都会有影响,实施例es-3由于压实高,同时ni含量高,容量较高,其他材料均呈现出压实越大,容量越高的特点。
[0089]
通过实施例1与实施例4-5的对比可知,第一一烧料和第二一烧料的质量比在优选范围1:(1-3)内有利于获得更高的压实密度,更好地提升材料的容量。
[0090]
对比例1性能压实差的原因在于,一混将所有原料混合后,一烧材料也是较为均一的,难以形成粒度梯度,无法有效提升压实。
[0091]
对比例2和对比例3单独调控镍锰原料的种类或者单独调控li/(ni+mn)摩尔比,均无法达到有效提升压实的目的,影响容量发挥。
[0092]
综上可知,本专利所述方法可以有效改善压实。
[0093]
申请人声明,本发明通过上述实施例来说明本发明的详细方法,但本发明并不局限于上述详细方法,即不意味着本发明必须依赖上述详细方法才能实施。所属技术领域的技术人员应该明了,对本发明的任何改进,对本发明产品各原料的等效替换及辅助成分的添加、具体方式的选择等,均落在本发明的保护范围和公开范围之内。