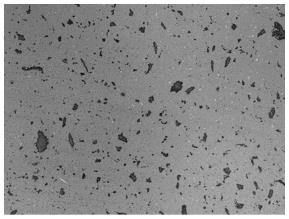
1.本发明涉及无机非金属碳化硅陶瓷领域,特别涉及一种通过多步反应烧结得到的具有极低残硅的碳化硅陶瓷及其制备方法。
背景技术:2.碳化硅陶瓷材料及其复合材料热导率高、硬度高、热膨胀系数低、熔点高、抗腐蚀性及抗氧化性能好,除此之外还具有优异的抗辐照性能,这使得它成为十分重要的高温结构陶瓷材料,广泛应用于机械、化工、能源、半导体、军工等领域。当碳化硅陶瓷材料及其复合材料应用于核燃料包壳材料时,其自身具有的高温稳定性、高温强度以及耐辐照特性可以在极大程度上提高核反应的安全性,避免核泄漏等严重事故的发生。
3.反应烧结碳化硅陶瓷的烧结原理是熔融的液态硅渗入素坯与碳发生反应,这就直接导致烧结体中存在残余硅,残余硅的存在会直接导致碳化硅应用范围缩小、力学性能差、耐腐蚀性差、在核环境下存在中子辐照肿胀等问题,破坏构件结构的稳定性。
4.武七德发表的《反应烧结碳化硅研究进展》指出可以用高温合金浸渗的方法降低反应烧结碳化硅中的残余硅,即耐高温合金组成物如si-mo取代si渗入坯体,溶解的mo析出mosi2同时消耗掉微量的残余硅。但是这种方法实际的反应过程尚不清楚,在反应后仍然存在一定数量的残余硅,同时目前的技术还无法使游离硅完全转化为高温相。此外该工艺要求事先将硅用耐高温金属饱和以保证熔体进入坯体,工艺复杂度很高,不适合于大规模生产应用。
5.根据suocheng song等人在《microstructural development and factors affecting the performance of areaction-bonded silicon carbide composite》一文中的研究可知,反应烧结碳化硅残余硅含量较高的原因是硅碳反应的进行堵塞了毛细管通道,可以通过构建新型毛细管通道或者引入惰性碳源消耗残余硅的方法降低残余硅含量。其中构建新型毛细管通道的方法需要引入碳化硼,影响材料的纯度,且得到的残余硅含量仍有4vol%;专利号为201610850564.3的专利公开一种多步反应烧结法制备低残硅的碳化硅陶瓷材料的方法;通过引入惰性碳源的方法降低残余硅含量,在设计残余硅和惰性碳源恰好反应的前提下目前已经将残余硅含量降至3vol%。这些结果虽然与传统反应烧结碳化硅存在的12vol%的残余硅含量相比有明显的降低,但是仍然不满足极端复杂环境下对残余硅含量的要求。
技术实现要素:6.为了克服上述现有技术的缺陷,本发明的目的在于通过多步反应烧结得到的具有极低残硅的碳化硅陶瓷及其制备方法,采用碳化硅粉、纳米炭黑粉、石油焦粉、中间相碳微球粉作为原料,其中纳米炭黑、石油焦以及部分中间相碳微球实现一次渗硅反应,剩余的中间相碳微球完成二次反应,采用凝胶注模成型法制备素坯,成型后二次渗硅烧结,得到最终
残碳量为0%-20%的反应烧结碳化硅陶瓷。
7.为实现上述目的,本发明采用如下技术方案:
8.通过多步反应烧结得到的具有极低残硅的碳化硅陶瓷,其原料组分及比例为:
9.按体积比百分比计,碳化硅粉体积比1%-40%,纳米炭黑粉体积比1%-20%,石油焦粉体积比0%-15%,中间相碳微球粉体积比1%-55%,酚醛树脂体积分数为13-25%、乙二醇体积分数为11-29%;另外,加入碳化硅粉体质量1%-2%的聚乙二醇400,酚醛树脂质量10%-16%的苯磺酰氯。
10.通过多步反应烧结得到的具有极低残硅的碳化硅陶瓷的制备方法,包含以下步骤:
11.步骤一、等质量称取酚醛树脂和乙二醇,机械搅拌得到混合充分的预混液;
12.步骤二、称取碳化硅粉、纳米炭黑粉、石油焦粉、中间相碳微球粉、聚乙二醇400和苯磺酰氯混合;
13.步骤三、将步骤二的混料加入到步骤一的预混液中球磨4h-8h,得到混合均匀的陶瓷浆料;
14.其中,碳化硅粉体积比1%-40%,纳米炭黑粉体积比1%-20%,石油焦粉体积比0%-15%,中间相碳微球粉体积比1%-55%,酚醛树脂体积分数为13-25%、乙二醇体积分数为11-29%;另外,加入碳化硅粉体质量1%-2%的聚乙二醇400,酚醛树脂质量10%-16%的苯磺酰氯;
15.步骤四、步骤三得到的陶瓷浆料真空消泡处理,得到陶瓷浆料;
16.步骤五、将步骤四得到的陶瓷浆料注入模具中,预固化处理,脱模后再固化处理;
17.步骤六、将步骤五得到的样品放入管式炉中,碳化处理;
18.步骤七、将步骤六得到的陶瓷素坯放入石墨坩埚内,再用硅粉将其掩埋,放入真空电阻炉中,通入保护气体,并将温度升至2200℃,在不同温度和不同保温时间进行两步处理,得到具有极低残余硅的反应烧结碳化硅陶瓷材料。
19.所述步骤四中,浆料真空消泡时间为0.5h-1h,同时配合磁力搅拌,得到陶瓷浆料。
20.所述步骤五中,预固化处理温度为60℃-80℃,保温0.5h-1.5h;固化处理温度为110℃-180℃,保温10h-20h。
21.所述步骤六中,碳化处理过程在管式炉中完成,在其中通入n2保护气体,并以1℃/min-3℃/min的升温速率升温至700℃-900℃,并保温3h-5h。
22.所述步骤七中,从室温到1100℃的升温速率是15℃/min-25℃/min,从1100℃-1600℃时升温速率是4℃/min-6℃/min,从1600℃-2200℃时升温速率是4℃/min-6℃/min;其中,在1450℃-1600℃下保温5min-60min,在1700-2200℃下保温1h-3h。
23.相对于现有技术,本发明方法具有如下优点:
24.本发明最终烧结体中的预设硅完全反应后的残碳量为0%-20%,分别对应总碳密度为0.96g
·
cm-3-1.21g
·
cm-3
;在原料中,纳米炭黑、石油焦以及部分中间相碳微球实现一次反应,剩余的中间相碳微球完成二次反应,所以一次碳密度是参与一次反应的碳在其体积中的占比,以硅碳反应最充分的碳密度0.85g
·
cm-3
为基准,一次碳密度的选取区间为0.75g
·
cm-3-0.90g
·
cm-3
。通过调整惰性碳的比例以及一次碳密度的高低,得到组织可控的具有极低残余硅含量的反应烧结碳化硅材料。碳化硅材料的密度为2.88g
·
cm-3
.13g
·
cm-3
,残余硅的比例为6.55%-0.03%,残余碳的比例为0%-22%,抗弯强度为200mpa-600mpa。
25.(2)通过采用复合碳源(纳米炭黑粉、石油焦粉作为活性碳源,碳微球粉作为惰性碳源)来代替单一活性碳源的方法,实现了二步法反应烧结,利用过量的惰性碳在极大程度上降低了残余硅的含量,为改善反应烧结碳化硅的应用范围以及碳化硅反应烧结法应用于核反应堆包壳管的封接奠定良好的基础。
26.(3)本发明成型方法采用凝胶注模成型法,制备的材料具有结构均匀、力学性能好、成本低廉等优点,适合于工业生产中制备大尺寸、形状复杂的部件。
27.(4)烧结方法采用反应烧结,具有成本低的特点,有利于投入实际工业生产之中。
附图说明
28.图1为采用本发明实施例11制备得到的反应烧结碳化硅的显微组织图。
具体实施方式
29.以下实施例用于说明本发明,但不用来限制本发明的范围。
30.本发明中的极低残余硅含量的碳化硅陶瓷,其实施例组成如表1所示,在表1所示的实施例中,纳米炭黑添加量均小于20%。若纳米炭黑添加量大于20%时,则导致陶瓷浆料粘度过高,不利于浆料消泡和注模工艺的进行。以下以实施例11做详细说明,其余实施例则参考表1即可。
31.实施例11
32.通过多步反应烧结得到的具有极低残硅的碳化硅陶瓷,原料组分见表1,聚乙二醇400是碳化硅颗粒的分散剂,加入量为碳化硅质量的1wt%,苯磺酰氯是浆料的固化促进剂,加入量为酚醛树脂的16wt%;其余各组分参照表1。
33.本实施例通过凝胶注模制备极低残硅量的反应烧结碳化硅陶瓷方法,按以下步骤进行:
34.步骤一、设计烧结体组织中的残碳量为8%,同时参与一次反应烧结的一次反应碳密度为0.81g
·
cm-3
,计算出酚醛树脂、乙二醇、碳化硅粉、纳米炭黑粉、石油焦粉、中间相碳微球体粉积比分别为19%、19%、24%、10%、0%、29%;
35.步骤二、将酚醛树脂、乙二醇加入烧杯中搅拌1h,根据步骤一的配比分别加入碳化硅粉、纳米炭黑粉、石油焦粉、中间相碳微球粉、聚乙二醇400球磨3h,再加入苯磺酰氯继续球磨0.5h,再利用水泵和机械泵分别真空消泡30min得到几乎不含气泡的混合均匀的浆料;其中,聚乙二醇400是碳化硅颗粒的分散剂,加入量为碳化硅质量的1wt%,苯磺酰氯是浆料的固化促进剂,加入量为酚醛树脂的16wt%;各组分加入量参照表1。
36.步骤三、将步骤二中的混合浆料倒入模具并放入烘箱中,在70℃保温1h预固化后脱模处理,然后以1℃/min升温速度升温至140℃,继续保温15h后制得均匀的固化体;
37.步骤四、将步骤三中的固化体放入管式炉中,通入保护气体n2,以2℃/min升温至800℃,保温4h后制得sic/c的陶瓷素坯;
38.步骤五、将步骤四中的sic/c陶瓷素坯放入底部含有硅颗粒的石墨坩埚内,并在表面铺一层硅颗粒,在真空渗硅炉中通入保护气体n2,升温至1550℃,保温5min,再升温至
2000℃,保温2h,制得极低残硅量的反应烧结碳化硅陶瓷。从室温到1100℃的升温速率为15℃/min,从1100℃到1600℃的升温速率为4℃/min,从1600℃到2000℃的升温速率为4℃/min。
39.表1本发明多孔碳化硅陶瓷的组成和制备工艺
40.41.[0042][0043]
由上述方法设计的碳化硅烧结体通过阿基米德排水法测得密度,采用像素统计法测得残余硅和残余碳的含量,最后用万能试验机测得抗弯强度,测试得到的性能如表2所示。
[0044]
表2本发明碳化硅的性能
[0045]
[0046][0047]
本发明选定纳米碳黑粉、石油焦粉作为体系的活性碳源,中间相碳微球粉作为惰性碳源,其中全部活性碳源与部分惰性碳源参与一次反应,剩余的惰性碳源参与二次反应。
为了通过两步法烧结降低反应烧结碳化硅中的残硅含量,首先根据理论残碳量设计总碳密度,保证第一次渗硅反应完全渗透并且极大程度上降低残余硅含量。
[0048]
此外,虽然本说明书已经用一般性说明及具体实施例作了详尽的描述,但在本发明基础上,可以对之作一些修改或改进,这对本领域技术人员而言是显而易见的。因此,在不偏离本发明精神与技术思想的基础上所完成的这些修改或改进,仍应由本发明的权利要求所涵盖。