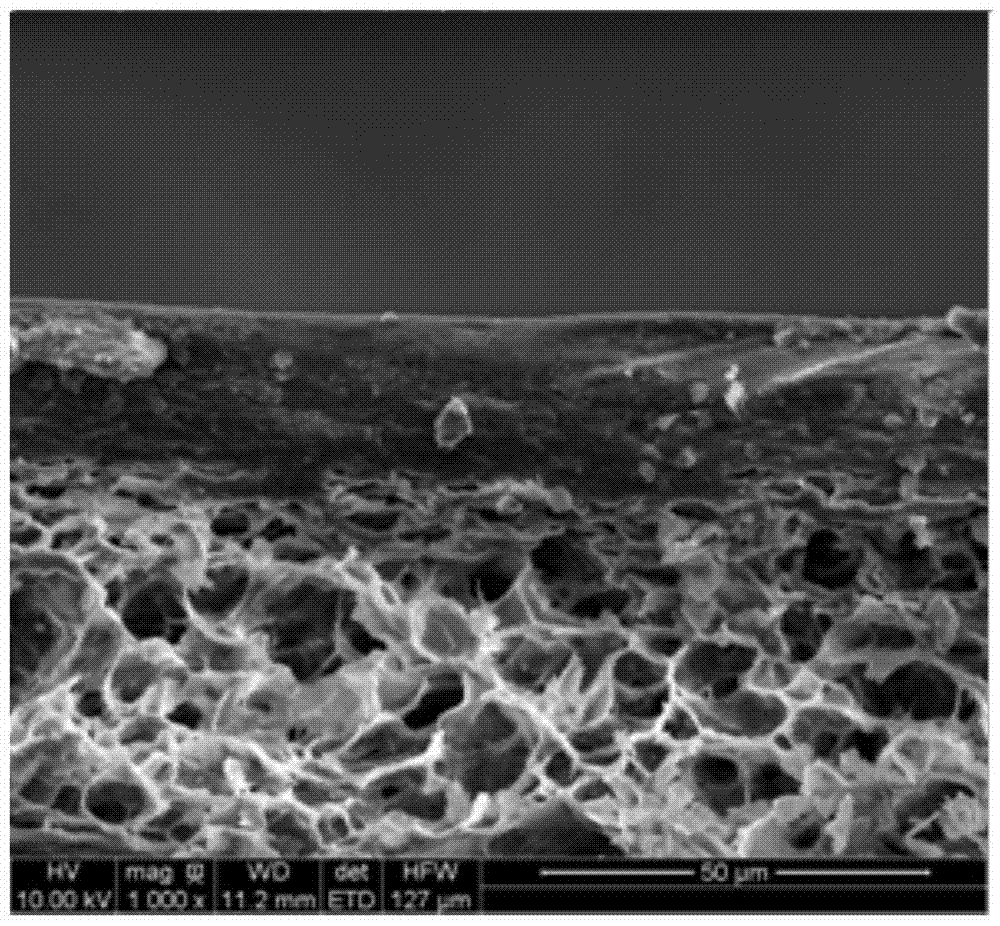
一种超亲水-超疏油纤维素海绵及其制备方法技术领域本发明属于功能性材料技术领域,具体涉及一种超亲水-超疏油纤维素海绵及其制备方法,该纤维素海绵主要用于油水分离。
背景技术:随着现代工业、农业以及生产生活的发展,无论发展中国家还是在发达国家,水污染的范围越来越大,含油污水便是其中之一,含油污水主要有餐饮业的地沟油,石油化工企业的含油废水,日常生活的含油废水以及海洋中的石油泄漏等。油中的苯类物质直接威胁到人类的健康,然而,这些油污染物的数量之多已远远超出了自然的净化能力。含油污水的处理也越来越受到人们的重视。近年来,人们设计发明了许多具有特殊浸润性的功能性材料来进行油水分离,例如亲油疏水类的海绵、金属网、膜、织物等,高效去除水面上的浮油。对于相分离的油水混合物,由于油水两种物质的不相容性以及油水两相的密度差异,其分离相对容易。而油水乳液,由于其尺寸微小、稳定性较高,特别是表面活性剂的稳定的油水乳液,分离难度更大。油水乳液分离关键在于乳液的破乳,传统的油水乳液分离方法主要包括添加化学破乳剂、高电压破乳、离心、蒸馏破乳等。然而,传统油水分离方法由于存在分离效率低,能耗高,二次污染等缺陷而逐渐受到限制。随着材料科学的发展,利用水和油之间的表面张力的不同,通过多孔材料对水或油的选择浸润性可使其中一相选择性透过而另一相不能透过来进行油水分离的方法逐渐受到人们的青睐。亲水疏油材料可依靠水的重力实现油水分离,并具有不易被油污污染、堵塞、可重复使用性强的特点而优于亲油疏水材料。CN102029079B、CN1387932A、CN1721030A、CN101518695A和CN200910217895.3分别公开了具有超疏水与超亲油功能的油水分离网膜或油水分离网。虽然以上几种技术方案都有较好的油水分离效果,但是其制备工艺的复杂性、材料价格昂贵、不耐酸碱腐蚀、涂层受磨损后疏油效果降低等使其广泛应用性受到限制。而且这些大孔的膜或金属网使其只能分离油滴大于20µm的乳液。
技术实现要素:本发明的目的在于提供一种超亲水-超疏油纤维素海绵及其制备方法,以克服现有技术中的不足。为实现上述目的,本发明提供如下技术方案:本发明实施例公开了一种超亲水-超疏油纤维素海绵,所述纤维素海绵的表面分布有有多个纳米级孔洞,所述纳米级孔洞的下方连通有微米级孔洞,并且微米级孔洞之间也相互连通。进一步的,所述纤维素海绵包括上、下两层,所述纳米级孔洞上下贯穿所述纤维素海绵的上层,所述微米级孔洞上下贯穿所述纤维素海绵的下层。优选的,在上述的超亲水-超疏水纤维素海绵中,所述纳米级孔洞的孔径为0.2~1μm,所述微米级孔洞的孔径为2~20μm。优选的,在上述的超亲水-超疏水纤维素海绵中,所述纤维素海绵上层的厚度为1~5mm,所述纤维素海绵下层的厚度为1~10mm。优选的,在上述的超亲水-超疏水纤维素海绵中,所述纤维素海绵在空气中对水的接触角接近0°,在水下对油的接触角大于150°。相应地,本发明还公开了一种超亲水-超疏水纤维素海绵的制备方法,包括步骤:s1、在纤维素溶解液中溶解纤维素原料分别配置成纤维素溶液C1和C2;s2、在纤维素溶液C1中加入成孔剂,均匀分散后获得混合溶液C3;s3、在模具中铺展一层混合溶液C3,然后再铺展一层纤维素溶液C2;s4、依次进行固化、脱模、水洗和冷冻干燥,获得具有两层结构的纤维素海绵。优选的,在上述的超亲水-超疏水纤维素海绵的制备方法中,所述步骤s2中,纤维素溶液C1中还添加有增强纤维。所述增强纤维优选为棉花,但不限于此。优选的,在上述的超亲水-超疏水纤维素海绵的制备方法中,所述纤维素原料可选自纤维素粉或棉短绒纤维素,但不限于此。优选的,在上述的超亲水-超疏水纤维素海绵的制备方法中,所述纤维素溶解液为非衍生化的溶剂,包括但不限于离子液体、氢氧化钠/尿素/水溶液、氯化锌溶液。优选的,在上述的超亲水-超疏水纤维素海绵的制备方法中,所述纤维素溶解液为质量分数67%的氯化锌溶液,溶解温度为80℃。优选的,在上述的超亲水-超疏水纤维素海绵的制备方法中,所述步骤s2中,成孔剂包括但不限于氯化钠、无水碳酸钠或无水硫酸钠,其用量为纤维素原料用量的2~20倍,所述增强纤维的用量为纤维素原料用量的5%~10%。与现有技术相比,本发明的优点在于:(1)本发明制备方法制的纤维素海绵与水下超疏油涂层、分子刷相比水下超疏油性更加稳定,而且在高酸、碱、盐环境下依然具有稳定的超疏油性。(2)本发明制备方法得到的纤维素海绵的超亲水性可保证在无外力作用下仅靠重力作用依然具有较高水通量,仅靠重力作用即可实现油水分离。(3)本发明制备方法得到的纤维素海绵表层纳米孔可以有效阻止微尺寸的油粒渗入海绵,下层的微米级孔的次层则可以加速水的渗透,该海绵具有抗污及自清洁性,可重复使用性高。(4)该纤维素海绵的制备方法简单,经过简单的纤维素溶解和再生即可得到,而且原料绿色、来源广泛.。附图说明为了更清楚地说明本发明实施例或现有技术中的技术方案,下面将对实施例或现有技术描述中所需要使用的附图作简单地介绍,显而易见地,下面描述中的附图仅仅是本发明中记载的一些实施例,对于本领域普通技术人员来讲,在不付出创造性劳动的前提下,还可以根据这些附图获得其他的附图。图1a-图1b分别是本发明实施例1制备的超亲水-水下超疏油纤维素海绵于吸水后和冷冻干燥后的照片;图2a是海绵的截面图,图2b是图2a海绵下层SEM图、图2c是图2a海绵上层SEM图。图3是本发明实施例1制备的超亲水-水下超疏油纤维素海绵的石油醚接触角图;图4a、图4b、图4c分别是本发明实施例1制备的超亲水-水下超疏油纤维素海绵的10wt%NaCl甲苯接触角图、1MHCl甲苯接触角图以及1MNaOH甲苯接触角图。具体实施方式本发明实施例公开了一种超亲水-超疏油纤维素海绵及其制备方法。本领域技术人员可以借鉴本文内容,适当改进工艺参数实现。特别需要指出的是,所有类似的替换和改动对本领域技术人员来说是显而易见的,它们都被视为包括在本发明。本发明的应用已经通过较佳实施例进行了描述,相关人员明显能在不脱离本发明内容、精神和范围内对本文所述的应用进行改动或适当变更与组合,来实现和应用本发明技术。为了进一步理解本发明,下面结合若干实施例对本发明进行详细说明。实施例1:本实施例纤维素海绵的制备方法包括以下步骤:步骤1:配置100g质量分数为67%的氯化锌水溶液。步骤2:将3g纤维素粉缓慢加入到步骤1的纤维素溶解液中,搅拌至纤维素粉完全溶解,溶液呈现无色透明状,将其分为两份备用,记为C1和C2;步骤3:在步骤2中的C1纤维素溶液(80g)中加入0.4g增强纤维及60g无水硫酸钠,并不断搅拌使其均匀分散,记为C3;步骤4:先在模具中倒入1mm厚度的步骤3中的C3纤维素溶液,使其铺展,静置,再在其上倒入5mm厚度的步骤2的C2溶液,静置30mim;步骤5:将步骤4得到的纤维素溶胶置于去离子水中反相析出1h;步骤6:将步骤5得到的纤维素凝胶50℃下水洗固化2天;步骤7:将步骤6得到的将纤维素凝胶置于冰箱中冷冻,再真空冷冻干燥处理,即得到两层结构的纤维素海绵。该海绵的双层结构中,表层的纳米孔孔径为0.5~1µm,次层的微米孔孔径为5~20µm。断裂强度测试显示,该海绵断裂强度约为0.92MPa。吸湿性能测试显示,该海绵的吸湿率可达10倍,保湿率可达6.5倍。孔隙率测试显示,该海绵孔隙率可达80%,透气率可达65%。水通量测试显示,仅在重力作用下,该海绵的水通量为180Lm-2h。将上述制得的纤维素海绵进行油水分离性能测试,结果如下:配置两种不同体积比的甲苯/水乳液(O/W),体积比分别是10:90和4:120,记两种乳液分别为R1和R2,将该海绵置于油水分离器中,仅在重力作用下,对油水乳液进行油水分离,并对分离前后的乳液进行紫外吸收表征,计算结果显示:该纤维素海绵对乳液R1的分离效率为99.90%,对乳液R2的分离效率为99.88%。实施例2:本实施例中所采用的纤维素海绵与实施例1中纤维素海绵制备方法基本相同,所不同的是纤维素粉的用量为5g。该海绵双层结构与实施例1中纤维素海绵的双层结构相同,表层的纳米孔孔径为0.3~0.5µm,次层的微米孔孔径为2~14µm。断裂强度测试显示,该海绵断裂强度约为1.7MPa。吸湿性能测试显示,该海绵的吸湿率可达7倍,保湿率可达4.5倍。孔隙率测试显示,该海绵孔隙率可达70%,透气率可达50%。水通量测试显示,仅在重力作用下,该海绵的水通量为150Lm-2h。将上述制得的纤维素海绵进行油水分离性能测试,测试方法与实施例1中的测试方法完全相同,结果如下:该纤维素海绵对乳液R1的分离效率为99.94%,对乳液R2的分离效率为99.92%。实施例3:本实施例中所采用的纤维素海绵与实施例1中纤维素海绵制备方法基本相同,所不同的是纤维素粉的用量为8g。该海绵双层结构与实施例1中纤维素海绵的双层结构相同,表层的纳米孔孔径为0.2~0.5µm。次层的微米孔孔径为2~14µm。断裂强度测试显示,该海绵断裂强度约为1.1MPa。吸湿性能测试显示,该海绵的吸湿率可达4倍,保湿率可达2倍。孔隙率测试显示,该海绵孔隙率可达55%,透气率可达35%。水通量测试显示,仅在重力作用下,该海绵的水通量为120Lm-2h。将上述制得的纤维素海绵进行油水分离性能测试,测试方法与实施例1中的测试方法完全相同,结果如下:该纤维素海绵对乳液R1的分离效率为99.93%,纤维素海绵对乳液R2的分离效率为99.93%。实施例4:本实施例纤维素海绵的制备方法包括以下步骤:步骤1:配置100g质量分数为67%的氯化锌水溶液。步骤2:将5g纤维素粉缓慢加入到步骤1的纤维素溶解液中,搅拌至纤维素粉完全溶解,溶液呈现无色透明状,将其分为两份备用,记为C1和C2;步骤3:在步骤2中的C1纤维素溶液(80g)中加入0.4g增强纤维及40g无水硫酸钠,并不断搅拌使其均匀分散,记为C3;步骤4:先在模具中倒入1mm厚度的步骤3中的C3纤维素溶液,使其铺展,静置,再在其上倒入5mm厚度的步骤2的C2溶液,静置30mim;步骤5:将步骤4得到的纤维素溶胶置于去离子水中反相析出1h;步骤6:将步骤5得到的纤维素凝胶50℃下水洗固化2天;步骤7:将步骤6得到的将纤维素凝胶置于冰箱中冷冻,再真空冷冻干燥处理,即得到两层结构的纤维素海绵。该海绵双层结构与实施例1中纤维素海绵的双层结构相同,表层的纳米孔孔径为0.2~0.5µm,次层的微米孔孔径为2~14µm。断裂强度测试显示,该海绵断裂强度约为1.7MPa。吸湿性能测试显示,该海绵的吸湿率可达5倍,保湿率可达4倍。孔隙率测试显示,该海绵孔隙率可达62%,透气率可达42%。水通量测试显示,仅在重力作用下,该海绵的水通量为88Lm-2h。将上述制得的纤维素海绵进行油水分离性能测试,测试方法与实施例1中的测试方法完全相同,结果如下:该纤维素海绵对乳液R1的分离效率为99.92%,纤维素海绵对乳液R2的分离效率为99.91%。实施例5:本实施例中所采用的纤维素海绵与实施例4中纤维素海绵制备方法基本相同,所不同的是硫酸钠的质量为60g。该海绵双层结构与实施例1中纤维素海绵的双层结构相同,表层的纳米孔孔径为0.3~0.5µm,次层的微米孔孔径为3~14µm。断裂强度测试显示,该海绵断裂强度约为1.5MPa。吸湿性能测试显示,该海绵的吸湿率可达8倍,保湿率可达6倍。孔隙率测试显示,该海绵孔隙率可达70%,透气率可达50%。水通量测试显示,仅在重力作用下,该海绵的水通量为150Lm-2h。将上述制得的纤维素海绵进行油水分离性能测试,测试方法与实施例1中的测试方法完全相同,结果如下:该纤维素海绵对乳液R1的分离效率为99.93%,纤维素海绵对乳液R2的分离效率为99.93%。实施例6:本实施例中所采用的纤维素海绵与实施例4中纤维素海绵制备方法基本相同,所不同的是硫酸钠的质量为100g。该海绵双层结构与实施例1中纤维素海绵的双层结构相同,表层的纳米孔孔径为0.5~1µm,次层的微米孔孔径为3~16µm。断裂强度测试显示,该海绵断裂强度约为1.1MPa。吸湿性能测试显示,该海绵的吸湿率可达10倍,保湿率可达7倍。孔隙率测试显示,该海绵孔隙率可达78%,透气率可达65%。水通量测试显示,仅在重力作用下,该海绵的水通量为200Lm-2h。将上述制得的纤维素海绵进行油水分离性能测试,测试方法与实施例1中的测试方法完全相同,结果如下:该纤维素海绵对乳液R1的分离效率为99.92%,纤维素海绵对乳液R2的分离效率为99.90%。在此,还需要说明的是,为了避免因不必要的细节而模糊了本发明,在附图中仅仅示出了与根据本发明的方案密切相关的结构和/或处理步骤,而省略了与本发明关系不大的其他细节。最后,还需要说明的是,术语“包括”、“包含”或者其任何其他变体意在涵盖非排他性的包含,从而使得包括一系列要素的过程、方法、物品或者设备不仅包括那些要素,而且还包括没有明确列出的其他要素,或者是还包括为这种过程、方法、物品或者设备所固有的要素。