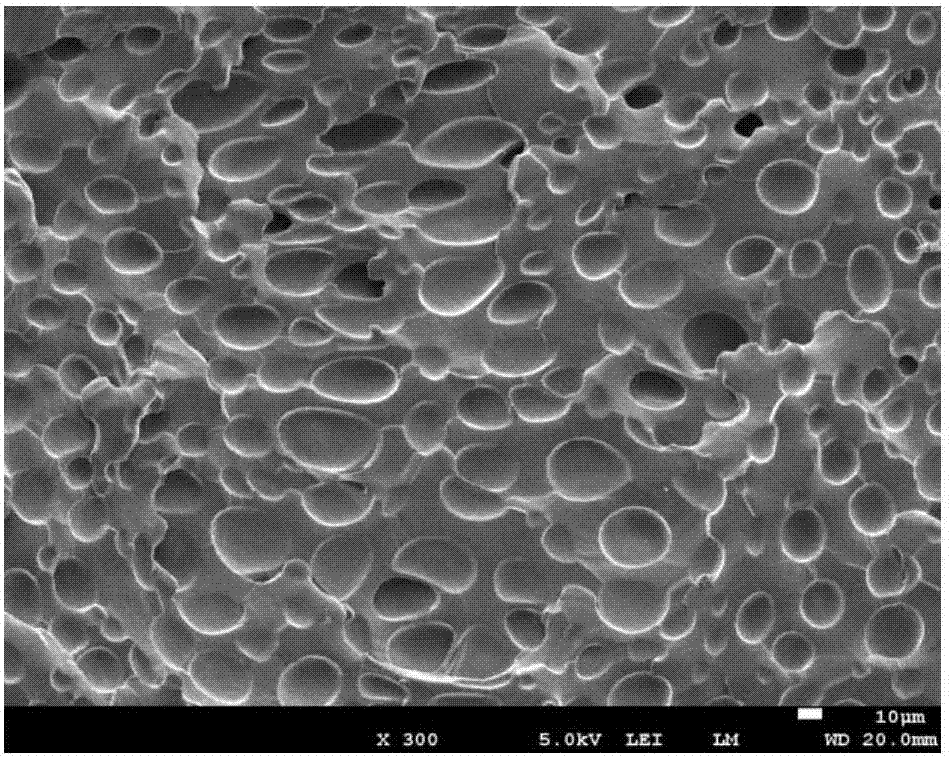
本发明属于高分子材料领域,具体涉及一种丁腈橡胶微孔发泡材料及其制备方法。
背景技术:
:聚合物发泡材料是一种由聚合物和包含气体泡孔组成的特殊材料,与普通聚合物材料相比具有以下特性:(1)密度低:由于发泡材料中含有大量气孔存在,因此,其密度仅为同类非发泡制品的几分之一甚至是十几分之一。(2)比强度高:由于发泡材料的密度仅为非发泡制品的几分之一甚至更低,所以具有较高的比强度。(3)隔音效果好:发泡材料中曲折相连的孔隙,改变了声音的直线传播,由于粘滞流动而使其能量损失。多孔体内部存在的许多表面,在气流压力作用下彼此之间能相对的发生很短距离的位移,这种移动会造成内耗,因此,许多发泡材料具有良好的声音阻尼能力,是理想的防噪声材料。(4)减震性能好:发泡材料具有较大的变形性,可以较高的吸收机械能量并将其转化为势能,因此,发泡材料具有较好的减震防护性能。(5)隔热性能好:限制发泡材料热流的因数有:固相中的低体积分数降低了材料的热传导;小的孔穴尺寸能通过孔壁的反复吸收和反射,从而抑止了热对流和减少了热辐射;封闭孔体能限制气体的对流。基于上述因素,导致发泡材料具有较低的热导率,所以材料的隔热性能较好。(6)发泡材料还有其他特殊性能:根据不同需求,发泡材料还可应用其他方面,如阻燃等。由于聚合物发泡材料具有质轻、料省、隔音、减震、比强度高等优异性能,与不发泡的基体材料相比,各方面性能都有较大提高(如冲击强度可比未发泡前提高6-7倍,韧性可提高4倍,疲劳寿命可延长5倍),并且可通过对其进行共混、填充、增强等改性以制得具有不同特殊性能的聚合物发泡材料,满足各种不同用途的需求。发泡材料广泛应用于航空、汽车、仪器仪表、家电、包装、医疗器械、体育用品等以及工农业生 产、国防建设等领域。丁腈橡胶是由丁二烯和丙烯腈经乳液聚合法制得的一种合成橡胶,简称nbr。丁腈橡胶主要采用低温乳液聚合法生产,化学性质稳定,加工性能良好;耐油性极好,耐磨性较高,耐热性较好;还具有良好的耐水性、气密性及优良的粘结性能。其缺点是耐低温性差、耐臭氧性差,绝缘性能低劣,弹性稍低。随着其结构中的丙炼腈含量的增加其相对密度增大,硫化速度加快,拉伸强度性能提高,但回弹性能下降,耐寒性能下降。广泛用于制各种耐油橡胶制品、多种耐油垫圈、垫片、套管、软包装、软胶管、印染胶辊、电缆胶材料等,在汽车、航空、石油、复印等行业中成为必不可少的弹性材料。目前丁腈橡胶的发泡材料基本都是nbr/pvc橡塑共混的发泡材料,nbr/pvc橡塑发泡材料一般应用在电器的包装、鞋底、运动手柄、管路保温性能等方面。nbr/pvc橡塑共混发泡材料具有柔性,柔性泡沫绝热制品具有质轻、柔软、耐热、阻燃、耐腐蚀、成本低、效率高等特点,具有广阔的市场前景。但是,现在市面上的发泡材料都是用化学发泡剂来发泡的,而发泡剂存在甲酰胺残留,从而限制了此种材料在高端领域的应用,因此一种新型环保发泡材料需要被开发。技术实现要素:本发明的目的是提供一种丁腈橡胶微孔发泡材料及其制备方法,与传统的发泡制品相比,本发明所制得发泡材料的泡孔均匀可控,力学性能较好,质量稳定,且无毒环保,可用于高档制品中,可用作汽车发动减震材料,密封材料、发泡地垫等各种领域。一种丁腈橡胶微孔发泡材料,其配方如下:配方包括丁腈橡胶共混料100份,ca/zn稳定剂0-4份,填料0-200份,增塑剂0-50份,硫化剂0.6-5份;硫化促进剂0.5-6份,防老剂40102-5份。其中,丁腈橡胶共混料包括丁腈橡胶50-100份,聚氯乙烯0-50份,丁腈橡胶和聚氯乙烯的含量之和为100份。其中,丁腈橡胶为丁腈橡胶、氢化丁腈、羧基丁腈橡胶中的任一种。其中,填料为炭黑、白炭黑、碳酸钙、高岭土、短纤维中的一种或多种。其中,增塑剂为芳烃油、石蜡油、邻苯二甲酸二辛酯中的一种或多种。其中,硫化剂为硫磺或过氧化二异丙苯中的一种。其中,硫化促进剂为dm,tmtd,taic、cbs,hva-2中的一种或多种。其中,所述配方中还包括活化剂,所述活化剂3-15份,所述活化剂为氧化锌,硬脂酸并用。一种丁腈橡胶微孔发泡材料的制备方法,其步骤如下:1)丁腈橡胶微孔发泡材料制备方法(1)在开炼机上,丁腈橡胶塑炼后依次加入防老剂、填料、增塑剂、活化剂、硫化剂、促进剂等混炼均匀,薄通三次后,下片停放24小时。(2)之后将混炼胶进行返炼,下片后称取一定量的胶料放入已预热的模具中,在平板硫化机上进行加压加热预硫化,硫化机压力10mpa,预硫化温度100-160℃,时间2-40min。(3)将预硫化材料装入高压釜内,先用少量co2吹洗2-3min,然后密封,反应釜温度为25-80℃,用高压泵将物理发泡剂注入高压釜内,使压力达到5-60mpa,恒压饱和5-30h,然后迅速卸压至常压,取出。(4)将步骤(3)所得微孔材料放入140-180℃的烘道中二次硫化3-20min,得到发泡材料成品。2)丁腈/聚氯乙烯微孔发泡材料制备方法(1)将pvc、dop、ca/zn热稳定剂等搅拌均匀,在150~160℃密炼机中进行塑炼,然后加入nbr、填料进行混炼,制成nbr/pvc母胶。然后在低温辊上,向一定量的nbr/pvc母胶中加入防老剂、填充剂、硫化体系混炼,薄通三次后下片停放24h。(2)通过挤出机挤出板材或管材,挤出机温度40-60℃。(3)挤出的板材或管材在140-180℃烘道中预硫化10-40min。(4)将预硫化材料装入高压釜内,先用少量co2吹洗2-3min,然后密封,反应釜温度为80-140℃,用高压泵将物理发泡剂注入高压釜内,使压力达到5-60mpa,恒压饱和0.5-4h,然后迅速卸压至常压,取出,得到发泡材料。其中步骤(4)中,所述物理发泡剂为co2,n2中的一种或两种气体的混合气体。附图说明图1本发明制备方法中,实施例1的扫描电镜图;图2本发明制备方法中,实施例2的扫描电镜图;图3本发明制备方法中,实施例3的扫描电镜图;图4本发明制备方法中,实施例3表皮层扫描电镜图的放大图;图5本发明制备方法中,实施例3中间层扫描电镜图的放大图;图6本发明制备方法中,实施例4扫描电镜图。具体实施方式下面通过具体的实施例对本发明的技术方案进行详细的说明,但是本发明的范围不受这些实施例的限制。实施例1nbr100份,填料10份,防老剂40101份,硫化剂2份,硫化促进剂2.5份,活性剂3份。其中,填料为炭黑;所述硫化剂为硫磺,硫化促进剂为tmtd,cz;活性剂为硬脂酸和氧化锌并用。先将nbr橡胶在开炼机上塑炼,接着加入填充剂、软化剂、硫化促进剂,硫化剂最后加入。薄通三次后出片,制得混炼胶。胶料放置一天后,返炼。将混炼胶放入所需 模具中,硫化机压力为10mpa,温度140℃,预硫化时间为10min。之后,将预硫化材料装入高压釜内,然后密封,反应釜温度为60℃,将n2注入高压釜内,使压力达到18mpa,恒压饱和5h。然后迅速卸压至常压,最后在150℃温度的烘箱中放置4min,得到发泡材料。此实施例的扫描电镜图片见图1。实施例2hnbr100份,防老剂40101份,硫化剂2.5份,硫化促进剂1.5份,活性剂6份。其中,所述硫化剂为硫磺,硫化促进剂为tmtd;活性剂为硬脂酸和氧化锌并用。先将nbr橡胶在开炼机上塑炼,接着加入填充剂、软化剂、硫化促进剂,硫化剂最后加入。薄通三次后出片,制得混炼胶。胶料放置一天后,返炼。将混炼胶放入所需模具中,硫化机压力为10mpa,温度140℃,预硫化时间为12min。之后,将预硫化材料装入高压釜内,然后密封,反应釜温度为60℃,将n2注入高压釜内,使压力达到18mpa,恒压饱和5h。然后迅速卸压至常压,最后在150℃温度的烘箱中放置6min,得到发泡材料。此实施例的扫描电镜图片见图2。实施例3xnbr100份,填料15份,增塑剂3份,防老剂40101.5份,硫化剂1份,硫化促进剂1.5份,活性剂3份。其中,填料为炭黑;增塑剂为芳烃油;硫化剂为过氧化二异丙苯,硫化促进剂为taic;活性剂为硬脂酸和氧化锌并用。先将nbr橡胶在开炼机上塑炼,接着加入填充剂、软化剂、硫化促进剂,硫化剂 最后加入。薄通三次后出片,制得混炼胶。胶料放置一天后,返炼。将混炼胶放入所需模具中,硫化机压力为10mpa,温度150℃,预硫化时间为8min。之后,将预硫化材料装入高压釜内,然后密封,反应釜温度为80℃,将n2注入高压釜内,使压力达到18mpa,恒压饱和3h。然后迅速卸压至常压,最后在160℃温度的烘箱中放置4min,得到发泡材料。此种发泡材料成品为三明治结构,中间层泡孔直径大,泡孔数量多;两边层泡孔数量极少,而且泡孔直径小。可应用于要求质轻、耐磨的发泡材料。其中图3为实施例3的扫描电镜图;图4为本实施例中表皮层扫描电镜图的放大图;图5为本实施例中中间层扫描电镜图的放大图。实施例4nbr70份,pvc30份,ca/zn稳定剂2份,填料80份,增塑剂20份,防老剂40101份,硫化剂1.4份,硫化促进剂2份,活性剂4份。其中,填料为高岭土;增塑剂为邻苯二甲酸二辛酯;硫化剂为过氧化二异丙苯,硫化促进剂为taic;活性剂为硬脂酸和氧化锌并用。首先将pvc、dop、ca/zn热稳定剂等搅拌均匀,在150~160℃密炼机中进行塑炼,然后加入nbr、高岭土进行混炼,制成nbr/pvc母胶。然后在80℃辊上,向nbr/pvc母胶中加入防老剂、硫化剂,硫化促进剂,活性剂进行混炼,薄通三次后下片停放24h。设置挤出机温度40℃,通过挤出机挤出板材。将板材放入170℃烘道中预硫化15min。将预硫化材料装入高压釜内,先用少量co2吹洗2-3min,然后密封,反应釜温度为120℃,用高压泵将n2入高压釜内,使压力达到15mpa,恒压饱和2h,然后迅速卸压至常压,取出,得到发泡材料。此实施例的扫描电镜图片见图6。按常规方法对上述实施例所制得的发泡材料的各项性能指标进行检测,实施例1-4检测结果见表1检测项目实施例1实施例2实施例3实施例4发泡后密度/g·cm-30.6740.3830.5690.358硬度(邵氏a)53374840以上所述仅为本发明的实施例,并不限制本发明,凡采用等同替换或等效变换的方式所获得的技术方案,均落在本发明的保护范围内。当前第1页12