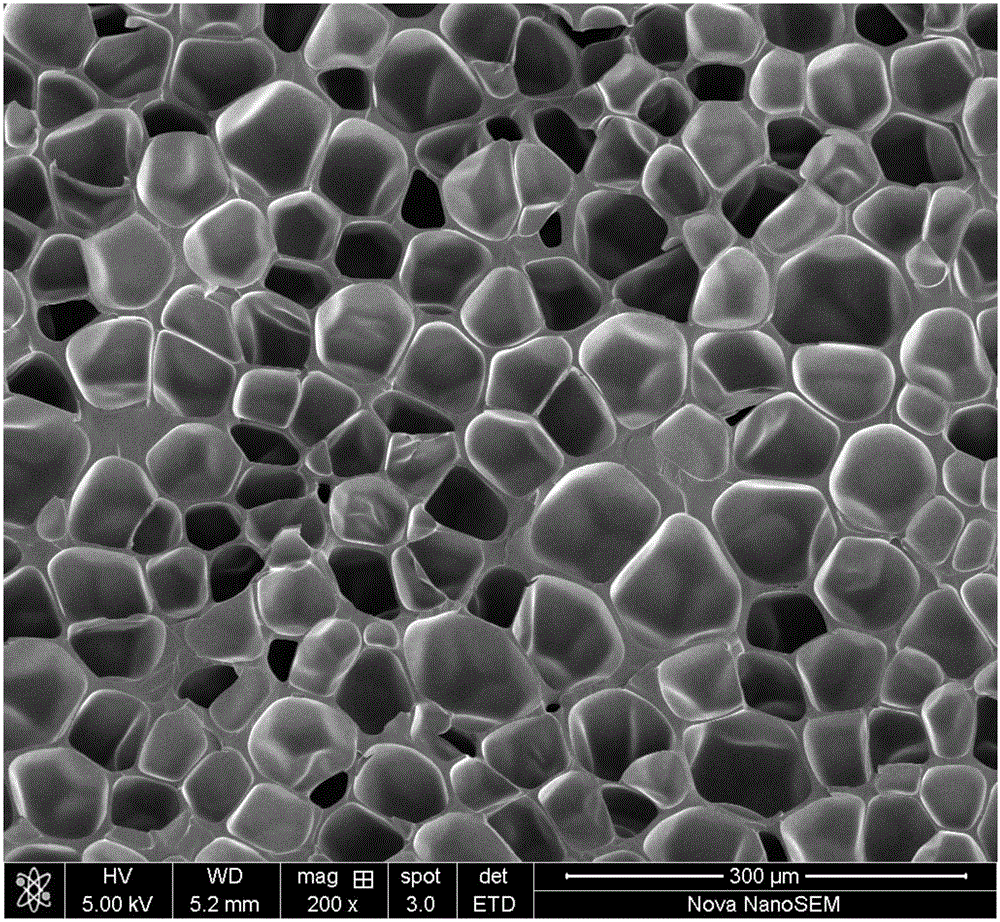
本发明涉及一种高倍率热塑性聚氨酯微孔发泡板材及其生产方法。
背景技术:
:利用发泡技术制得的软质弹性高分子泡沫具有优良的减震缓冲、隔热保温、降噪吸音、防尘防水等性能,在鞋材,家具、电子设备、交通工具、运动器材、防护包装等领域应用广泛。多孔结构和内部形成的化学交联网络结构是软质弹性高分子泡沫的基本特征,如交联EVA发泡材料,各种橡胶发泡材料,PVC发泡材料等。这些通过化学交联发泡形成的软质弹性材料,制程复杂,污染较大,产品有毒有异味,并且较难回收再利用,造成了环境污染,对人类的健康构成了危害。热塑性聚氨酯(TPU)是由热力学上不相容的软段和硬段交替组成的线性嵌段聚合物,其独特的微相分离结构提供了其突出的弹性性能,同时其具有高强度、高耐磨、高耐油、高耐寒等特征。TPU发泡材料具有优于交联发泡材料的弹性和压缩变形性能。同时相比交联的软质弹性发泡材料,TPU发泡材料清洁环保,可循环利用,不含邻苯二甲酸盐,不含卤素。通过化学交联发泡仅能得到2~3倍的TPU发泡板材。更高倍率的TPU发泡材料目前主要是通过珠粒发泡技术获得的。TPU发泡珠粒可在模具内通过蒸汽加热,使之表面熔接,形成TPU发泡制品。国际专利WO2007/082838,美国专利US2012/0329892A1,中国专利200780002602.9公开了两种制备TPU发泡珠粒的方法。一种方法是将TPU实心粒子置于高压釜内的热悬浮液中,通入发泡剂气体,使之溶解扩散进入TPU粒子,形成含发泡剂的可发性的TPU珠粒,再将冷却解压得到的可发性TPU珠粒突然升温,使之发生膨胀,得到TPU发泡珠粒,或是将高压釜内的热悬浮液在高温高压下突然解压,引发气泡生长,得到TPU发泡珠粒。另一种方法是通过在挤出机里通入发泡剂气体,通过螺杆剪切使发泡剂气体溶解于TPU熔体,通过在模头处直接发泡形成TPU发泡珠粒,或在模头处水下切粒形成含发泡剂的可发性TPU珠粒,再升温发泡得到TPU发泡珠粒。TPU珠粒模压成型易于制造具有复杂结构的异形TPU发泡制品,但珠粒熔接形成的制品表面粗糙,外观较差,没有细腻的表面触感。且蒸汽熔接过程能耗较大,成本较高。模压成型过程会引起TPU发泡珠粒的进一步收缩,导致TPU珠粒成型制品的发泡倍率普遍较低。中国专利201110054581.3公开了一种利用超临界CO2制备热塑性聚合物发泡板材的技术,但由于发泡温度低于聚合物的流动温度,CO2在聚合物中的扩散速率较低,不能实现厚度较大的TPU微孔发泡板材的高效生产。技术实现要素:本发明要解决的技术问题就是提供一种高倍率热塑性聚氨酯微孔发泡板材及其生产方法,解决现有TPU珠粒成型制品的发泡倍率低的缺陷。为了解决上述技术问题,本发明是通过以下技术方案实现的:一种高倍率热塑性聚氨酯微孔发泡板材,包括以下组分:70~100重量份的TPU、0~30重量份的聚二甲基硅氧烷。优选的,包括以下组分:90~100重量份的TPU、0~10重量份的聚二甲基硅氧烷。优选的,TPU的分子量为4~9万,硬度为shoreA65~95。优选的,聚二甲基硅氧烷为双端氨基聚二甲基硅氧烷、a,w-二羟基聚二甲基硅氧烷、单端双羟烃基聚二甲基硅氧烷、羟基封端聚二甲基硅氧烷、氢封端聚二甲基硅氧烷中的一种或两种的组合物或两种以上的组合物。优选的,TPU以多异氰酸酯、多元醇、扩链剂为生产原料制备而成,多异氰酸酯为二苯基甲烷二异氰酸酯或甲苯二异氰酸酯;多元醇为聚酯多元醇或聚醚多元醇或聚丙烯酸多元醇或聚碳酸酯多元醇或聚烯烃多元醇;扩链剂为丁二醇或乙二醇或丙二醇。优选的,聚二甲基硅氧烷的平均摩尔质量为2000~5000g/mol。一种高倍率热塑性聚氨酯微孔发泡板材的生产方法,包括以下步骤:a)将组分除湿干燥后加入挤出机,然后通过衣架式模头成型、冷却、定长切割,得到TPU实心板材;b)将步骤a)得到的TPU实心板材放入耐高压发泡模具中,模具合模密封,模具升温至140~160℃,然后向模具内通入超临界流体,使超临界流体在高温高压下快速扩散进入TPU实心板材,当超临界流体达到扩散平衡时间后,再将温度降低至90~130℃并瞬间释放模具内的超临界流体压力,TPU实心板材在模具内膨胀生长直至充满整个模具空间,最后快速打开模具,TPU发泡板材继续生长,直至生长停止,形成TPU微孔发泡板材。优选的,模具包括上模和下模,上模和下模之间形成模腔,上模上设有进气阀门和排气阀门,模腔与TPU实心板材的体积比为6:5~5:1,进气阀门能实现超临界流体的通入,排气阀门能实现模具内的超临界流体快速瞬间释放,便于TPU板材在模具内膨胀生长。优选的,模腔的内表面铺设有一层多孔透气金属层,使超临界流体在TPU板材内的扩散路径缩短,减少超临界流体的饱和时间。优选的,超临界流体为超临界CO2、超临界丁烷、超临界戊烷中的一种或两种混合的超临界流体或两种以上混合的超临界流体,且超临界流体的压力为5~20MPa,超临界流体的扩散平衡时间为10~240min,能根据不同的需求对超临界流体进行组合,实用性能好。综上所述,本发明的优点:由于超临界流体在聚二甲基硅氧烷具有较大的溶解度和聚二甲基硅氧烷具有较低的界面张力,在TPU中混入的少量聚二甲基硅氧烷,极大地加速了超临界流体在TPU中的扩散速度,缩短了超临界流体在TPU中的扩散平衡时间;模腔体积稍大于TPU板材体积,并且模具表面铺有透气金属材料的模具,使超临界流体可以通过TPU板材的上下两个表面同时扩散进入TPU板材,相比于超临界流体只能通过上表面扩散进入TPU板材,扩散距离缩短,同样缩短了扩散平衡时间,提高了生产效率。先使超临界流体在高温下以较高的扩散速率进入TPU基体,再根据目标发泡倍率将发泡温度降至适当温度,开模发泡,同样也是利用超临界流体在TPU中的扩散速率随着温度的增加而提高的特点,实现了发泡时间的缩短,有利于提高生产效率。通过清洁的超临界流体快速泄压发泡,制程简单,同时产品无毒无污染,制得的TPU板材泡孔尺寸较小,泡孔密度较大,发泡倍率较大,机械性能优异。附图说明下面结合附图对本发明作进一步说明:图1为实施例一得到的TPU微孔发泡片材的内部泡孔的扫描电镜图;图2为实施例二得到的TPU微孔发泡片材的内部泡孔的扫描电镜图;图3为实施例三得到的TPU微孔发泡片材的内部泡孔的扫描电镜图;图4为实施例四得到的TPU微孔发泡片材的内部泡孔的扫描电镜图。具体实施方式实施例一:如图1所示,一种高倍率热塑性聚氨酯微孔发泡板材,包括以下组分:100重量份的TPU,TPU的分子量为6万,硬度为shoreA75,TPU为聚酯型TPU粒子。一种高倍率热塑性聚氨酯微孔发泡板材的生产方法,包括以下步骤:a)将TPU除湿干燥后加入挤出机,然后通过衣架式模头成型、冷却、定长切割,裁切成宽150mm,长400mm,厚度10mm的TPU实心板材;b)将步骤a)得到的TPU实心板材放入耐高压发泡模具中,且模具中的模腔与TPU实心板材的体积比为3:1,模具通过液压压力合模,模具通过密封圈受力密封,模具通过导热油升温至140℃,向模具内通入10MPa的超临界CO2,超临界流体的扩散平衡时间为180min,再将温度降低至110℃,通过排气阀门迅速排放模具内的CO2气体,TPU实心板材在模具内膨胀生长直至充满整个模具空间,最后快速打开模具,TPU发泡板材继续生长,直至生长停止,形成TPU微孔发泡板材。将TPU微孔发泡板材在常温常压放置熟化后,测量TPU微孔发泡板材的尺寸为宽225mm,长600mm,厚度15mm。实施例二:如图2所述,一种高倍率热塑性聚氨酯微孔发泡板材,包括以下组分:95重量份的TPU、5重量份的聚二甲基硅氧烷,TPU的分子量为6.5万,硬度为shoreA80,TPU为聚醚型TPU粒子,聚二甲基硅氧烷为双端氨基聚二甲基硅氧烷。一种高倍率热塑性聚氨酯微孔发泡板材的生产方法,包括以下步骤:a)将TPU和聚二甲基硅氧烷混合并除湿干燥后加入挤出机,然后通过衣架式模头成型、冷却、定长切割,裁切成宽150mm,长400mm,厚度10mm的TPU实心板材;b)将步骤a)得到的TPU实心板材放入耐高压发泡模具中,且模具中的模腔与TPU实心板材的体积比为2:1,模具通过液压压力合模,模具通过密封圈受力密封,模具通过导热油升温至150℃,向模具内通入15MPa的超临界CO2,超临界流体的扩散平衡时间为100min,再将温度降低至130℃,通过排气阀门迅速排放模具内的CO2气体,TPU实心板材在模具内膨胀生长直至充满整个模具空间,最后快速打开模具,TPU发泡板材继续生长,直至生长停止,形成TPU微孔发泡板材。将TPU微孔发泡板材在常温常压放置熟化后,测量TPU微孔发泡板材的尺寸为宽300mm,长800mm,厚度30mm。实施例三:如图3所示,一种高倍率热塑性聚氨酯微孔发泡板材,包括以下组分:100重量份的TPU,TPU的分子量为8万,硬度为shoreA85,TPU为聚醚型TPU粒子。一种高倍率热塑性聚氨酯微孔发泡板材的生产方法,包括以下步骤:a)将TPU除湿干燥后加入挤出机,然后通过衣架式模头成型、冷却、定长切割,裁切成宽500mm,长1500mm,厚度20mm的TPU实心板材;b)将步骤a)得到的TPU实心板材放入耐高压发泡模具中,且模具中的模腔与TPU实心板材的体积比为3:2,模具通过液压压力合模,模具通过密封圈受力密封,模具通过导热油升温至155℃,向模具内通入17MPa的超临界流体,超临界流体为超临界CO2和超临界丁烷,且超临界CO2和超临界丁烷的重量比为9:1,超临界流体的扩散平衡时间为80min,再将温度降低至120℃,通过排气阀门迅速排放模具内的超临界流体,TPU实心板材在模具内膨胀生长直至充满整个模具空间,最后快速打开模具,TPU发泡板材继续生长,直至生长停止,形成TPU微孔发泡板材。将TPU微孔发泡板材在常温常压放置熟化后,测量TPU微孔发泡板材的尺寸为宽1250mm,长3750mm,厚度50mm。实施例四:如图4所示,一种高倍率热塑性聚氨酯微孔发泡板材,包括以下组分:100重量份的TPU,TPU的分子量为7.5万,硬度为shoreA90,TPU为聚碳酸酯型TPU粒子。一种高倍率热塑性聚氨酯微孔发泡板材的生产方法,包括以下步骤:a)将TPU除湿干燥后加入挤出机,然后通过衣架式模头成型、冷却、定长切割,裁切成宽500mm,长1500mm,厚度20mm的TPU实心板材;b)将步骤a)得到的TPU实心板材放入耐高压发泡模具中,且模具中的模腔与TPU实心板材的体积比为5:1,模具通过液压压力合模,模具通过密封圈受力密封,模具通过导热油升温至145℃,向模具内通入20MPa的超临界流体,超临界流体为超临界CO2和超临界丁烷,且超临界CO2和超临界丁烷的重量比为4:1,超临界流体的扩散平衡时间为60min,再将温度降低至110℃,通过排气阀门迅速排放模具内的超临界流体,TPU实心板材在模具内膨胀生长直至充满整个模具空间,最后快速打开模具,TPU发泡板材继续生长,直至生长停止,形成TPU微孔发泡板材。将TPU微孔发泡板材在常温常压放置熟化后,测量TPU微孔发泡板材的尺寸为宽1350mm,长4050mm,厚度54mm。按照GB/T6343-2009标准测试得到TPU微孔发泡板材的表观密度,可以计算得到最终微孔发泡材料的发泡倍率。发泡倍率(Rex)=ρTPU/ρTPUfoam,其中ρTPU为未发泡TPU板材的密度,ρTPUfoam为TPU微孔发泡材料的密度。将TPU微孔发泡板材经液氮淬断,断面喷金,采用扫描电镜(SEM)考察发泡材料内部的泡孔形态,拍摄得到泡孔的SEM图片,并根据SEM片测量泡孔尺寸和计算泡孔密度。泡孔密度N(单位:个/cm3)=(n/A)3/2×Rex,n为SEM图片上的泡孔数,A为SEM图片的实际拍摄面积(单位:cm2)。按照GB/T6669-2008标准考察TPU微孔发泡板材的压缩永久变形性能。将调节后的TPU发泡板材切割成50mm(长)×50mm(宽)×25mm(厚)的样品,常温下压缩至厚度的50%,保持72小时后解除压缩。压缩永久变形按下式计算:CS=d0-drd0×100%]]>其中,CS----压缩永久变形,以百分数(%)表示。d0----试样初始厚度。dr----试样最终厚度。按照ASTMD3574测定TPU微孔发泡板材的落球回弹性能。将调节后的TPU微孔发泡板材置于落球回弹测试仪的测试位置,钢球从500mm高度自由落下,落球回弹测试仪自动计算钢球回弹的最大高度和钢球落下的高度比值的百分率,即回弹率。发泡材料的表面硬度通过手持式shoreC型硬度计测试。检测结果如表一所示项目实施例1实施例2实施例3实施例4发泡倍率3.3815.619.6硬度,shoreC48413427平均孔径,μm456289113孔密度,个/cm31.4×1085.5×1072.8×1075.7×106落球回弹率,%43515963压缩永久变形率,%131197表一除上述优选实施例外,本发明还有其他的实施方式,本领域技术人员可以根据本发明作出各种改变和变形,只要不脱离本发明的精神,均应属于本发明所附权利要求所定义的范围。当前第1页1 2 3