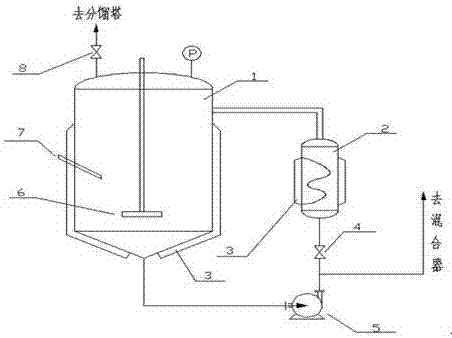
本发明属于有机合成应用
技术领域:
,涉及采用一种来自化纤废液回收的半纤维素连续法制造糠醛技术,具体为一种利用连续流微通道反应器将半纤维素制备糠醛的方法。
背景技术:
:糠醛是一种目前尚不能通过化学方法合成的重要的基础有机化工原料,是从糖类化合物中所获得的唯一一种不饱和大比容有机化学品,其化学性质十分活泼,糠醛及其衍生物都是应用广泛的有机化工中间体。此外,糠醛还可通过与甲醛的羟甲基化作用生成5-羟甲基糠醛,也可作为原料制备汽油、柴油和航空煤油,由糠醛通过加氢作用生成的甲基四氢呋喃可直接作为汽油的基料。随着世界范围内能源危机和环境问题的日益严峻,各化工领域对糠醛的需求量将会持续增长。但是,现有的糠醛生产工艺能耗巨大,环境污染极其严重,生产成本偏高且收率低下,以上诸多不利因素使欧盟和美国在过去数十年中已严令禁止在本国范围内生产糠醛。中国是糠醛生产和出口大国,占世界糠醛总产量70%左右。鉴于糠醛在有机化工及能源领域中的重要作用,现有的糠醛生产工艺亟待改进。生物质水解制糠醛的反应机理是酸在水中电离出的h+与水结合为h3o+,它使半纤维素中的糖苷键的氧原子迅速质子化,糖苷键因减弱而断裂,末端形成的碳正离子与水相互作用最终形成单糖,同时释放出h+,继续与水结合。水在高温高压条件下也可以电离出h+与oh-,具备酸碱自催化功能,因此生物质半纤维素在高温高压水中的反应机理也符合生物质水解的机理。半纤维素水解产生的木糖上的羟基与氢离子结合脱去一分子水,同时环断裂形成碳碳双键与碳氧双键,再次脱去两分子水成环得糠醛。工业上,糠醛由木质纤维素生物质中的半纤维素在稀酸,最常采用的催化剂是h2so4。理论上,所有富含多缩戊糖的生物质都可以作为原料来生产糠醛,其中玉米芯中多缩戊糖的含量最高,是生产糠醛最常采用的原料。目前,糠醛的工业生产采用批处理反应器使原料与稀酸水溶液在水解锅内混合,并采用高压蒸汽提供反应所需要的热量,同时,蒸汽的另一个重要作用是将糠醛从反应体系中及时移除,减小因二次反应而造成的糠醛产率降低,常用的工艺条件是在高温(140~185℃)高压(0.5~1mpa)下反应6~10h,h2so4用量为3%,固液比在(2~3)∶1,受多种条件限制,工业生产上最大糠醛收率只能达到理论值的45%~55%。反应器出口蒸汽中糠醛的质量分数约为3%,糠醛和水的混合物(即粗醛)通过汽提塔进行浓缩,形成富含糠醛的蒸汽。由于糠醛在水中的溶解能力有限(20℃,8.3%),相分离现象非常明显,下层富含糠醛相进一步通过连续的精馏塔进行精制和提纯,从而得到糠醛成品,上层含水相则回流至汽提塔。在分离过程中,甲醇和乙酸是有价副产物。水解后的废渣(主要成分是纤维素和木质素)作为锅炉燃料生产蒸汽。由半纤维素生成糠醛的机理及水解动力学半纤维素在酸和水的作用下发生水解生成戊糖,而后木糖经过异构化作用和连续三步脱水反应生成糠醛。以酸为催化剂由木质纤维素的半纤维素部分生成的糠醛及木糖进一步发生副反应。首先,在酸的作用下,糖苷键被打破,半纤维素水解为戊糖,此步反应条件温和,反应速度较快。随后,生成的木糖在酸的作用下脱去3分子水生成糠醛。由于糠醛性质不稳定,会进一步与木糖及反应中间产物发生反应生成胡敏素,糠醛自身也会发生树脂化反应。当反应时间较长或温度较高时,胡敏素的产生尤为明显。在水相中,木糖脱水反应的活化能(ea=124kj/mol),高于糠醛与木糖交互反应的活化能(ea=72kj/mol)及糠醛自身树脂化反应的活化能(ea=68kj/mol),而在所有副反应中,糠醛与木糖的反应是生成胡敏素的主要途径。以酸为催化剂,由木糖生成糠醛的反应过程是其中木糖的异构化是整个反应的限速步骤。通过以上机理分析可知,有两种途径可提高糠醛的产率和选择性,一是优化反应条件减少副反应的发生,二是寻找恰当的催化剂加快木糖的异构化反应。现有的糠醛生产工艺存在诸多弊端:首先是收率问题,目前世界范围内约70%的糠醛生产企业采用批处理反应器,糠醛收率只有理论值的50%左右,但是消耗蒸汽量却是糠醛产量的30~50倍,且反应时间较长。现有的催化体系副反应较多,水相、强酸、高温、与氧气接触、较长的反应时间等都会导致糠醛的缩合和树脂化,同时,糠醛与木糖及反应中间产物之间也会发生交互聚合反应,糠醛还会进一步降解生成丙酮醛、甲醛、甘油醛、乙醇醛等,这些副反应会降低戊糖生成糠醛的选择性。其次,稀酸易腐蚀设备,且其分离和循环使用非常困难,而稀酸水解法还会导致大量酸性糠醛废水产生,治理难度极大。再次,使用蒸汽作为热源和萃取剂耗能巨大。因此有人希望解决上述问题,专利cn102391218a中公开了一种固定床催化木糖脱水制备糠醛的方法:反应釜中进入-3mol/l的酸催化剂溶液,再加助催化剂nacl至饱和,升温至回流,搅拌形成一个固定体积和浓度的催化剂层的旋转液面,再将经稀酸催化水解秸秆得到的10-20%的木糖按一定速度喷加到反应釜中,进行木糖脱水反应,糠醛溶液经精馏得到纯度达到99%以上的糠醛,收率达到50~70wt%。专利cn102399203a公开了一种溶解浆木片水解液硫酸连续法制造糠醛技术,具体地说是利用生产溶解浆的阔叶木桉木、杨木等的预水解液为原料,连续水解、连续生产糠醛的技术。其技术方案为:一种溶解浆木片水解液硫酸连续法制造糠醛技术,预水解液采用连续的无酸条件下制得,过滤分离水解液和少量的溶解木质素;预水解液脱水反应生产糠醛,采用以硫酸为催化剂、连续化生产工艺。所用生物质为资源丰富的阔叶木桉木、杨木等,为糠醛生产开辟了新的丰富的原料资源和方法;水解液用于生产糠醛,而水解后的木片进一步生产溶解浆,进而实现木材中半纤维素和纤维素的高效资源化利用;连续化的水解工艺和连续的糠醛生产工艺,糠醛转化率高达到76.6%;无酸的水解工艺,水解催化剂为木片本身水解产生的乙酸、甲酸等,大大降低对设备的腐蚀。以上方法均未给出反应时间,同时收率仍较低。技术实现要素:本发明正是基于以上技术问题,提供一种利用连续流微通道反应器将半纤维素制备糠醛的方法。该方法可利用化纤行业废碱液回收的半纤维素为原料,采用连续微通道反应器将半纤维素直接转化成糠醛,通过分离,回收催化剂的方式,使产率、经济效益、降低污染、改善生态环境等方面均有较大提高。微反应工艺,即采用微通道反应器代替传统的化学反应器进行化学反应的工艺,并实现工业生产的技术。本发明的技术方案为:一种利用连续流微通道反应器将半纤维素制备糠醛的方法,该方法包括以下步骤:(1)为使反应达到最佳得率,将半纤维素的原料配置成半纤维素含量为8-15wt%的水溶液,催化剂配成6-12wt%的水溶液,超出这个范围,将有固体析出,堵塞反应器,影响反应的进行;(2)向半纤维素水溶将中添加阻聚剂,再将含有阻聚剂的半纤维素水溶液和催化剂,经由各自计量泵控制,分别进入微通道反应器的混合模块,再进入预热模块通道中进行预热,设定温度为180-220℃,压力1.6~2.2mpa,再同步进入增强传质型模块内进行混合反应,反应温度控制在180-220℃;该步骤反应的温度均由外部换热器进行,换热介质为导热油;所述的半纤维素原料来自化纤废液回收的半纤维素含量为10-15wt%的水溶液或70-80%的固体物。所述的催化剂为硫酸或盐酸,含有阻聚剂的半纤维素水溶液和催化剂的重量比为1:0.2~4。所述的阻聚剂为羟基苯甲醚、对叔丁基邻苯二酚、对苯二酚、n-苯基取代脲、硫脲、萘胺和三苯基磷中的任意一种或多种的混合物,添加量为0.1wt%~1wt%。(2)在该模块中经混合并发生反应后,继续通过一系列增强传质型微通道模块以及直流型微通道模块,反应时间5-30min,反应过程完成后,产物从微通道反应器的出口流出;(3)将自微通道反应器出口得到的反应液进入分离器,分离器内预先置入2-5mol/l的硫酸或盐酸水溶液,并加热维持温度180-220℃,生成的糠醛与水蒸汽通过节流阀进入分馏塔,得到粗糠醛后再通过精馏得到成品糠醛。由微通道反应器出来的反应液以切线方式进入分离器,在此进行气液分离,糠醛与水蒸气混合气体,由上部导气管通过节流阀排出进入分馏塔,液体落入分离器内,该液体为未反应的的半纤维素和酸性催化剂,落入分离器下部液体中继续反应,用泵从分离器底部抽出,将液体物料一部分通过循环反应器返回分离器,在维持分离器液面的同时,多余液体打回打回微通道反应器混合反应器内,根据测定结果补加催化剂,维持催化剂的浓度为2-5mol/l。所用的微通道反应器为美国康宁公司的增强传质型微通道反应器,该反应系统由多块模块组装而成;该模块的材质为碳化硅或特种玻璃;模块内微通道结构分直流型通道结构和增强混合型通道结构两种,直流型通道为管状结构,增强混合型通道结构为心型结构,通道水力直径为0.5mm~10mm。所述的分离器为用于连续反应器的物料分离器,该分离器包括分离器罐体和循环反应器,在所述的分离器罐体和循环反应器外部均设有蒸汽夹套,物料泵的进料口与分离器罐体的底部连通,物料泵的出料口通过三通,一端通向混合器,另外一出口通过分流阀与循环反应器连接,循环反应器通过管道与分离器罐体连通,搅拌器设置在分离器罐体内,温度计设置在分离器罐体上。所述的分离器罐体为圆柱形锥体结构,具有球形封头,在分离器罐体的顶部设置有压力传感器,压力传感器与压力显示器相连接;在所述的分离器罐体上设置气体物料排出节流阀,物料排出节流阀设置在气体排出口处。所述反应物料通过循环反应器以切线方向进入分离器上部;所述的循环反应器内装有sv型原件;所述的搅拌器为涡轮式搅拌器,距离所述分离器罐体圆筒直筒底部5cm-10cm。与现有技术相比,本发明的有益效果为:(一)、微流体工艺过程连续,系统密闭,瞬间反应物料量小,可精确控制反应条件自动控制程度高,较好的实现了反应过程。在收率、选择性或安全性等方面得到提高。本发明采用连续流微通道反应器,反应时间从传统的数小时缩短到3至10分钟,显著提高了反应效率。(二)、由于原料在微通道中混合极佳,温度精确控制,反应过程中,浓硫酸的用量可以大大减少,还可回用,降低了成本,且产物的选择性明显提高。(三)、本发明中使用连续流微通道反应器材质为特种玻璃,计量泵的材质为聚四氟乙烯和碳化硅或玻璃,耐腐蚀性优良,解决了在常规反应器中腐蚀设备严重的问题。(四)、在微通道反应器中,从进料、预热、混合以及反应过程全程为连续流反应,避免了常规间歇反应中需要额外配置装置和转移中出现的泄露,环保安全,生产效率高。(五)、糠醛生产中主反应是木糖脱水环化生成糠醛,同时有副反应发生,主要的副反应有在高温和酸性条件下糠醛聚合生成低聚产物以及高温下糠醛分解等反应。因此如果能把生成的糠醛立即从反应系统(酸性、高温)中移出,减少其在反应器中的停留时间,应是提高糠醛得率的有效的途径之一,本申请中所述的装置即可完成该操作。(六)、我们利用用化纤行业废碱液回收的半纤维素为原料,采用连续流微通道反应器将半纤维素直接转化成糠醛,通过分离,回收催化剂的方式,在产率、经济效益、降低污染改善生态环境等方面均有了较大的提高。(七)、反应中没有废酸液排出,全部回用,减少了对环境的污染。附图说明:图1为本发明中利用连续流微通道反应器将半纤维素制备糠醛方法的流程示意图。图2为本发明中所述用于连续反应器的物料分离器的结构示意图。其中,1——分离器筒体;2——循环反应器;3——蒸汽夹套;4——分流阀;5——物料泵;6——搅拌器;7——温度计;8——节流阀。具体实施方式为了使本发明的内容更加便于理解,下面将结合附图和具体实施方式对本发明中所述的工艺做进一步的阐述。但不应将此理解为本发明上述主题的范围仅限于下述实施例。本申请文件中的%,如无特殊说明,均表示wt%。向半纤维素水溶将中添加阻聚剂,再将含有阻聚剂的半纤维素水溶液和催化剂,经由各自计量泵控制,分别进入微通道反应器的混合模块,再进入预热模块通道中进行预热,设定温度为180-220℃,压力1.6~2.2mpa,再同步进入增强传质型模块内进行混合反应,反应温度控制在180-220℃;该步骤反应的温度均由外部换热器进行,换热介质为导热油;所述的半纤维素原料来自化纤废液回收的半纤维素含量为10-15wt%的水溶液或70-80%的固体物。所述的催化剂为硫酸或盐酸,含有阻聚剂的半纤维素水溶液和催化剂的重量比为1:0.2~4。所述的阻聚剂为羟基苯甲醚、对叔丁基邻苯二酚、对苯二酚、n-苯基取代脲、硫脲、萘胺和三苯基磷中的任意一种或多种的混合物,添加量为0.1wt%~1wt%。在该模块中经混合并发生反应后,继续通过一系列增强传质型微通道模块以及直流型微通道模块,反应时间5-30min,反应过程完成后,产物从微通道反应器的出口流出进入分离器,一种用于连续流微反应器的物料分离器,包括分离器罐体和循环反应器,在所述的分离器罐体上设置有进料口、出料口、气体物料排出节流阀和搅拌器;所述的气体物料排出节流阀设置在分离器罐体顶端的气体排出口处,使反应生成的糠醛和水的共沸物排出并控制分离器内压力恒定。物料泵的进料口与分离器罐体的底部连通,物料泵的出口连接有三通,一端通过管道与混合器连接,另外一端通过分流阀与循环反应器底部连接,循环反应器的出口通过管道以切线方向进入分离器罐体的上部,可使一部分物料通过循环反应器进入分离器,一部分物料返回混合器以保证分离器内液位恒定。分离器罐体上的出料口与物料泵入口连接,物料泵出口设置卸料控制阀,物料泵将分离器内物料抽出进入循环反应器,使未反应物料更好混合进行反应。搅拌器设置在分离器罐体内,搅拌器使进入分离器的物料中未反应物继续反应。在分离器罐体外部和管式反应器的外部均设置蒸汽加热夹套,维持分离器所需的温度。所述的分离器罐体为圆柱形锥体结构,具有球形封头,在分离器罐体的顶部设置压力传感器,压力传感器与压力显示器相连接,同时有现场显示压力表。所述进料口以切线方向设置于所述的分离器上部。所述的搅拌器为涡轮式搅拌器,该搅拌器设置在分离器罐体内,距离所述分离器罐体圆筒直筒部分底部5cm~10cm。所述的温度计设置在分离器罐体上,用于测量分离器内温度。以下实施例中所采用的分离器均为实施方式中记载的分离器。实施例1:所用连续流微通道反应器为美国康宁公司的增强传质型微通道反应器,(该反应器的模式为“直通道功能模块”+“心型”结构功能模块)水利直径10mm,参照图1、确定微通道反应器连接模式,混合反应模块数根据流速与反应停留时间确定,加热介质为导热油。半纤维素原料来自化纤废液回收的半纤维素含量为15-25%的混浊液或70-80%的固体物,将其配成半纤维素含量为12wt%的水溶液,向半纤维素水溶液中添加阻聚剂,将含有阻聚剂的半纤维素水溶液和催化剂浓硫酸,经计量泵控制半纤维素水溶液和催化剂浓硫酸重量比为1:0.3;分别进入微通道反应器中混合模块中混合后进入预热模块,设定温度为190℃,压力1.8mpa由外部换热器进行控制,换热介质为导热油,再同步进入增强传质型模块内进行混合反应,混合温度同样由外部换热器进行控制在190℃,压力1.8mpa,;糠醛转化率88%。在该模块中经混合并发生反应后,继续通过一系列增强传质型微通道模块以及直流型微通道模块,反应时间6min,反应过程完成后,产物从反应器的出口流出。由微通道反应器出来的反应液以切线方式进入气液分离器,在此进行气液分离,糠醛与水蒸气混合气体,由上部导气管通过节流阀排出进入分馏塔,液体落入分离器内,该液体为未反应的的半纤维素和酸性催化剂,落入分离器下部液体中继续反应,用泵从分离器底部抽出,将液体物料一部分通过循环反应器返回分离器,在维持分离器液面的同时,多余液体打回打回微通道反应器混合反应器内,根据测定结果补加催化剂,维持催化剂的浓度;气液分离器内预先置入3mol/l的硫酸水溶液,并加热维持温度190℃,压力1.8mpa。所用的微通道反应器该反应系统由多块模块组装而成;该模块的材质为碳化硅和特种玻璃等;模块内微通道结构分直流型通道结构和增强混合型通道结构两种,直流型通道为管状结构,增强混合型通道结构为心型结构,通道水力直径为8mm;为防止反应产物在过程中的聚合,加入阻聚剂为羟基苯甲醚、硫脲的混合物(混合质量比为1:1),添加量为0.2wt%。本发明方法与传统釜式反应的转化率及反应时间的对比,见下表:不同反应方法对转化率及反应时间的影响反应时min糠醛转化率率%间歇釜水解24075本发明水解688实施例2微通道反应器为美国康宁公司的增强传质型微通道反应器,该反应系统由多块模块组装而成;该模块的材质为碳化硅和特种玻璃等;模块内微通道结构分直流型通道结构和增强混合型通道结构两种,直流型通道为管状结构,增强混合型通道结构为心型结构,通道水力直径为8mm;所用连续流微通道反应器(直通道功能模块+“心型”结构功能模块)流程,参照图1、确定微通道反应器连接模式,混合反应模块数根据流速与反应停留时间确定,加热介质为导热油。所述的半纤维素原料来自化纤废液回收的半纤维素含量为15-25wt%的混浊液或70-80%的固体物,将其配成半纤维素含量为12wt%水溶液,纤维素水溶液和催化剂浓硫酸的重量比为1:2;含有阻聚剂的半纤维素水溶液和催化剂浓硫酸,经计量泵控制半纤维素与盐酸重量比:1:0.3;分别进入微通道反应器中混合模块混合,然后进入预热模块中进行预热,设定温度为180℃,压力1.8mpa由外部换热器进行控制,换热介质为导热油,再同步进入增强传质型模块内进行混合反应,混合温度同样由外部换热器进行控制在180℃压力1.8mpa,;在该模块中经混合并发生反应后,继续通过一系列增强传质型微通道模块,反应时间5min,反应过程完成后,产物从反应器的出口流出。由微通道反应器出来的反应液以切线方式进入气液分离器,在此进行气液分离,糠醛与水蒸气混合气体,由上部导气管通过节流阀排出进入分馏塔,液体落入分离器内,该液体为未反应的的半纤维素和酸性催化剂,落入分离器下部液体中继续反应,用泵从分离器底部抽出,将液体物料一部分通过循环反应器返回分离器,在维持分离器液面的同时,多余液体打回打回微通道反应器混合反应器内,根据测定结果补加催化剂,维持催化剂的浓度;气液分离器内预先置入2mol/l的盐酸水溶液,并加热维持温度190℃,压力1.8mpa。糠醛转化率90%。为防止反应产物在过程中的聚合,加入阻聚剂为羟基苯甲醚、硫脲的混合物(混合重量比为1:1),添加量为0.2wt%。本发明方法与传统釜式反应的转化率及反应时间的对比,见下表:不同反应方法对糠醛转化率及反应时间的影响反应时min糠醛转化率%间歇釜水解22077本发明水解590虽然本发明已经通过具体实施方式对其进行了详细阐述,但是,本专业普通技术人员应该明白,在此基础上所做出的未超出权利要求保护范围的任何形式和细节的变化,均属于本发明所要保护的范围。当前第1页12