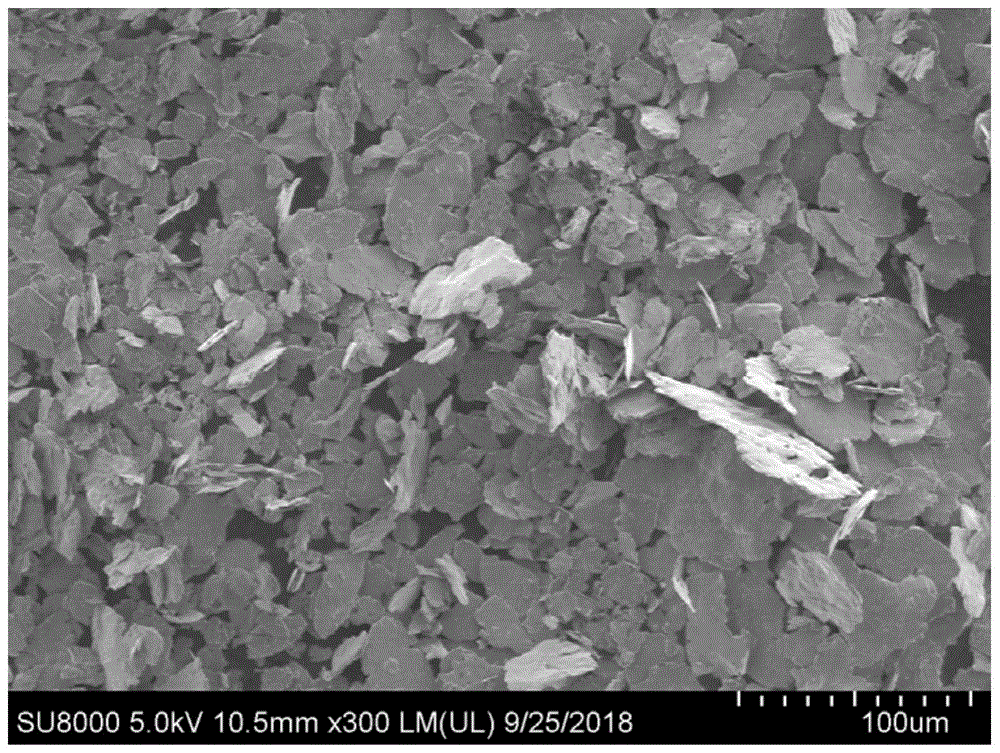
本发明涉及电磁功能复合材料
技术领域:
,尤其涉及一种片状铁氧体电磁复合材料及制备方法。
背景技术:
:随着高端电子设备的快速发展,设备中电子元器件性能的技术要求也越来越高。其中,在有限空间内元器件之间的电磁干扰就不可避免,对天线系统的通信功能具有严重的干扰,削弱信号的传输强度,甚至使天线彻底失效,为此必须在器件之间添加具有高磁导率、磁损耗的电磁屏蔽材料来有效的解决这个问题。铁氧体具有价格低廉、制备工艺简单、吸波性能好等特点,是目前研究较多且比较成熟的微波衰减吸收剂。铁氧体对电磁波的损耗同时包括介电损耗和磁损耗,其中最主要的损耗机制为剩余损耗中的铁磁自然共振吸收。目前,传统生产中所得铁氧体粉体大部分为球形结构。但随着设备单元中使用频段的不断提高,球形铁氧体材料已难以满足。有鉴于此,特提出本发明。技术实现要素:本发明目的是为了将片状结构铁氧体粉体与环氧树脂粘结复合,提供一种具备优异电磁特性的功能复合材料的制备方法,满足在高性能电子元器件与新型电磁材料方面的应用。为了实现上述目的,本发明提供了如下技术方案:一种片状铁氧体电磁复合材料的制备方法,所述制备方法以通过球磨制成的片状铁氧体、偶联改性剂、树脂、固化剂和稀释剂为原料,将各原料组分混合、成型,制得所述复合材料;其中,通过球磨制备片状铁氧体的工艺条件为:将铁氧体粉、钢球、球磨助剂和易挥发性溶剂在400-500r/min转速条件下球磨7-8h;所述刚球包括8mm直径钢球和6mm直径钢球。优选地,所述铁氧体粉、所述钢球、所述球磨助剂和所述易挥发性溶剂的质量比为(100-130):(350-500):(0.01-0.05):(200-300);优选地,所述铁氧体粉、所述钢球、所述球磨助剂和所述易挥发性溶剂的质量比为(115-120):(400-450):(0.02-0.03):(250-300)。优选地,所述8mm直径钢球和所述6mm直径钢球的质量比为5:7。优选地,所述铁氧体为fesial铁氧体;所述球磨助剂为硬脂酸钙;和/或所述易挥发性溶剂为丙酮。优选地,所述片状铁氧体和所述树脂的质量比为(70-80):(15-25),优选为(75-80):(15-20);所述偶联改性剂的质量为所述片状铁氧体质量的0.2-0.5wt%;所述固化剂的质量为所述树脂质量的20-25wt%;和/或所述稀释剂的质量为所述树脂质量的15-20wt%。优选地,所述偶联改性剂为3-氨基丙基三乙氧基硅烷;和/或所述树脂为环氧树脂。优选地,所述成型采用热压罐固化成型法,压力条件为1-5mpa,温度条件为110-120℃;或所述成型采用超声固化成型法,温度条件为90-100℃。优选地,所述制备方法包括如下步骤:(1)球磨步骤:将铁氧体粉、钢球、球磨助剂和易挥发性溶剂在400-500r/min转速条件下球磨7-8h,所述刚球包括8mm直径钢球和6mm直径钢球,得到片状铁氧体;(2)偶联改性步骤:将偶联改性剂和步骤(1)制得的片状铁氧体混合,得到偶联处理后的片状铁氧体;(3)配制浆料步骤:将步骤(2)制得的片状铁氧体和树脂、固化剂和稀释剂混合,得到混合浆料;(4)成型步骤:将步骤(3)配制的混合浆料固化成型,得到所述复合材料。优选地,在配制浆料的步骤中,在真空辅助下进行混合;或在80-90℃、40-50khz下超声分散。一种片状铁氧体电磁复合材料,采用本发明提供的制备方法制得,所述复合材料具有如下性能:相对复介电常数的实部:36.88-66.22;相对复介电常数的虚部:7.51-34.02;相对复磁导率的实部:0.47-3.42;相对复磁导率的虚部:0.43-6.64。有益效果本发明的上述技术方案具有如下优点:本发明采用球磨法制备片状铁氧体粉体,通过偶联改性与环氧树脂复合,运用热压罐工艺或超声固化成型电磁负载复合材料,其在1-18ghz表现出较高的电磁参数,可广泛应用于雷达、导航、卫星通信、电子对抗、广播电视、移动通讯等各领域电子设备中。本发明提供的这一制备方法将球磨得到的片状铁氧体和树脂复合制备成电磁复合材料,通过特定的球磨工艺赋予片状铁氧体在1-18ghz频段优异的电磁参数,从而确保与树脂复合后的复合材料在1-18ghz频段表现出优异的电磁性能;另外,通过这一特定的球磨工艺制得的片状铁氧体还能与树脂实现较好的阻抗匹配,避免难以实现阻抗匹配的优化设计。利用该球磨工艺制得的片状铁氧体的平均粒径(指片长)在30-35μm,该粒径的片状铁氧体可在后期成型阶段轻松成型,无须较大的压力条件,从而使得制备工艺更加便利。本发明提供的制备方法在球磨阶段按照所述铁氧体粉、所述钢球、所述球磨助剂和所述易挥发性溶剂的质量比为(100-130):(350-500):(0.01-0.05):(200-300)这一配料关系进行球磨,从而确保球磨后的片状铁氧体的粒度的均匀性以及电磁性能的均一性。更优选的配料关系为:所述铁氧体粉、所述钢球、所述球磨助剂和所述易挥发性溶剂的质量比为(115-120):(400-450):(0.02-0.03):(250-300),其它条件相同的情况下,该配料关系下球磨得到的片状铁氧体的粒度最均匀且电磁性能最均一。本发明提供的制备方法在球磨时将8mm直径钢球和6mm直径钢球按照5:7质量比使用时,确保球磨后的片状铁氧体的粒度的均匀性以及电磁性能的均一性。为了兼顾材料性能和工艺可操作性,本发明提供的制备方法片状铁氧体和树脂按照质量比(70-80):(15-25)进行复合。附图说明图1是片状fesial粉体sem形貌图。具体实施方式为使本发明的目的、技术方案和优点更加清楚,下面将结合本发明实施例,对本发明的技术方案进行清楚、完整地描述。显然,所描述的实施例是本发明的一部分实施例,而不是全部的实施例。基于本发明中的实施例,本领域普通技术人员在没有做出创造性劳动的前提下所获得的所有其他实施例,都属于本发明保护的范围。本发明在第一方面提供了一种片状铁氧体电磁复合材料的制备方法,所述制备方法以通过球磨制成的片状铁氧体、偶联改性剂、树脂、固化剂和稀释剂为原料,将各原料组分混合、成型,制得所述复合材料;其中,通过球磨制备片状铁氧体的工艺条件为:将铁氧体粉、钢球、球磨助剂和易挥发性溶剂在400-500r/min(可以为该范围内的任意数值,例如,可以为400r/min、410r/min、420r/min、430r/min、440r/min、450r/min、460r/min、470r/min、480r/min、490r/min、500r/min)转速条件下球磨7-8h(可以为该范围内的任意数值,例如,可以是7h、7.5h、8h);所述刚球包括8mm直径钢球和6mm直径钢球。本发明提供的这一制备方法将球磨得到的片状铁氧体和树脂复合制备成电磁复合材料,通过特定的球磨工艺赋予片状铁氧体在1-18ghz频段优异的电磁参数,从而确保与树脂复合后的复合材料在1-18ghz频段表现出优异的电磁性能;另外,通过这一特定的球磨工艺制得的片状铁氧体还能与树脂实现较好的阻抗匹配,避免难以实现阻抗匹配的优化设计。发明人还发现,利用该球磨工艺制得的片状铁氧体的平均粒径(指片长)在30-35μm,该粒径的片状铁氧体可在后期成型阶段轻松成型,无须较大的压力条件,从而使得制备工艺更加便利。除了球磨转速、所用钢球大小以及球磨时间外,发明人建议在球磨阶段按照所述铁氧体粉、所述钢球、所述球磨助剂和所述易挥发性溶剂的质量比为(100-130):(350-500):(0.01-0.05):(200-300)这一配料关系进行球磨,从而确保球磨后的片状铁氧体的粒度的均匀性以及电磁性能的均一性。更优选的配料关系为:所述铁氧体粉、所述钢球、所述球磨助剂和所述易挥发性溶剂的质量比为(115-120):(400-450):(0.02-0.03):(250-300),其它条件相同的情况下,该配料关系下球磨得到的片状铁氧体的粒度最均匀且电磁性能最均一。所述球磨助剂优选为硬脂酸钙。所述易挥发性溶剂优选为丙酮。具体地,在配料关系上,上述各组分的用量可以为上述范围内的任意数值。例如,所述铁氧体粉的质量数可以为100、105、110、115、120、125、130;例如,所述钢球的质量数可以为350、360、370、380、390、400、410、420、430、440、450、460、470、480、490、500;例如,所述球磨助剂的质量数可以为0.01、0.02、0.03、0.04、0.05;例如,所述易挥发性溶剂的质量数可以为200、210、220、230、240、250、260、270、280、290、300。在一些优选的实施方法中,所述8mm直径钢球和所述6mm直径钢球的质量比为5:7。发明人也发现在将8mm直径钢球和6mm直径钢球按照这一质量比使用时球磨效果最佳,确保球磨后的片状铁氧体的粒度的均匀性以及电磁性能的均一性。在一些优选的实施方式中,所述片状铁氧体和所述树脂的质量比为(70-80):(15-25),优选为(75-80):(15-20)。为了获得较大的磁损耗,提高片状铁氧体的添加量是一个有效的手段。随着片状铁氧体添加量的增大,复合材料的磁损耗会得以提高。但当其添加量过高时,分散的难度以及后续成型的难度都大幅度增加。因此,工艺可操作性角度考虑,建议将片状铁氧体和树脂按照质量比(70-80):(15-25)进行复合。所述树脂可以选用环氧树脂。环氧树脂在固化剂的作用下,生成立体网状结构的产物,显示出各种优良的性能。具体地,在配料关系上,上述各组分的用量可以为上述范围内的任意数值。例如,所述片状铁氧体的质量数可以为70、71、72、73、74、75、76、77、78、79、80。例如,所述树脂的质量数可以为15、16、17、18、19、20、21、22、23、24、25。在实际操作中,偶联改性剂优选先与片状铁氧体混合,对片状铁氧体进行偶联改性处理,再与树脂混合。这样操作的优势在于:球磨后得到的片状铁氧体的片状化结构使得其在与树脂这一具有一定粘度的物料混合时不易分散,而通过偶联改性后可以在很大程度上避免这一问题。除此之外,还可以在将片状铁氧体和树脂混合时借助真空辅助条件,在真空辅助下进行混合或者借助超声,在80-90℃(可以为80℃、81℃、82℃、83℃、84℃、85℃、86℃、87℃、88℃、89℃、90℃)、40-50khz(可以为40khz、41khz、42khz、43khz、44khz、45khz、46khz、47khz、48khz、49khz、50khz)下超声分散。在一些优选的实施方式中,所述偶联改性剂的质量为所述片状铁氧体质量的0.2-0.5wt%,可以为该范围内的任意值,例如,可以为0.2wt%、0.3wt%、0.4wt%、0.5wt%。所述偶联改性剂优选为3-氨基丙基三乙氧基硅烷,又名kh550或kh-550,使用kh-550对片状铁氧体进行偶联改性有助于铁氧体与树脂粘结力提升,从而提高复合材料力学性能。所述固化剂的质量为所述树脂质量的20-25wt%,可以为该范围内的任意值,例如,可以为20wt%、21wt%、22wt%、23wt%、24wt%、25wt%。所述固化剂可以选用本领域常见的用于固化环氧树脂的固化剂,例如,2-乙基-4-甲基咪唑。所述稀释剂的质量为所述树脂质量的15-20wt%,可以为该范围内的任意值,例如,可以为15wt%、16wt%、17wt%、18wt%、19wt%、20wt%。所述稀释剂可以选用本领域常见的适用于环氧树脂的稀释剂,例如市售的501稀释剂。在一些优选的实施方式中所述制备方法可以按照如下制备过程进行:(1)球磨步骤:将铁氧体粉、钢球、球磨助剂和易挥发性溶剂在400-500r/min转速条件下球磨7-8h,所述刚球包括8mm直径钢球和6mm直径钢球,得到片状铁氧体;(2)偶联改性步骤:将偶联改性剂和步骤(1)制得的片状铁氧体混合,得到偶联处理后的片状铁氧体;(3)配制浆料步骤:将步骤(2)制得的片状铁氧体和树脂、固化剂和稀释剂混合,得到混合浆料;(4)成型步骤:将步骤(3)配制的混合浆料固化成型,得到所述复合材料。更为全面地,本发明提供的这一制备方法可以包括如下制备步骤:(1)球磨步骤:将铁氧体粉、钢球、球磨助剂和易挥发性溶剂在400-500r/min转速条件下球磨7-8h,所述刚球包括8mm直径钢球和6mm直径钢球,得到片状铁氧体。所述铁氧体粉、所述钢球、所述球磨助剂和所述易挥发性溶剂的质量比优选为(100-130):(350-500):(0.01-0.05):(200-300),更优选为(115-120):(400-450):(0.02-0.03):(250-300)。所述8mm直径钢球和所述6mm直径钢球的质量比优选为5:7。所述球磨助剂可以为硬脂酸钙。所述易挥发性溶剂可以为丙酮。(2)偶联改性步骤:将偶联改性剂和步骤(1)制得的片状铁氧体混合,得到偶联处理后的片状铁氧体。所述偶联改性剂优选为3-氨基丙基三乙氧基硅烷,其质量为所述片状铁氧体质量的0.2-0.5wt%。(3)配制浆料步骤:将步骤(2)制得的片状铁氧体和树脂、固化剂和稀释剂混合,得到混合浆料。在该步骤中,所述片状铁氧体和所述树脂的质量比优选为(70-80):(15-25),更优选为(75-80):(15-20)。所述固化剂的质量优选为所述树脂质量的20-25wt%。所述稀释剂的质量优选为所述树脂质量的15-20wt%。可以借助真空辅助条件进行混合,即在真空辅助下进行混合或者是借助超声手段进行混合,在80-90℃、40-50khz下超声分散。(4)成型步骤:将步骤(3)配制的混合浆料固化成型,得到所述复合材料。所述成型可以采用热压罐固化成型法,压力条件为1-5mpa(可以为该范围内的任意数值,例如,可以为1mpa、2mpa、3mpa、4mpa、5mpa),温度条件为110-120℃(可以为该范围内的任意数值,例如,可以为110℃、111℃、112℃、113℃、114℃、115℃、116℃、117℃、118℃、119℃、120℃),还可以采用超声固化成型法,温度条件为90-100℃(可以为该范围内的任意数值,例如,可以为90℃、91℃、92℃、93℃、94℃、95℃、96℃、97℃、98℃、99℃、100℃)。本发明在第二方面提供了一种片状铁氧体电磁复合材料,采用本发明提供的制备方法制得,所述复合材料具有如下性能:相对复介电常数的实部:36.88-66.22;相对复介电常数的虚部:7.51-34.02;相对复磁导率的实部:0.47-3.42;相对复磁导率的虚部:0.43-6.64,可广泛应用于雷达、导航、卫星通信、电子对抗、广播电视、移动通讯等各领域电子设备中。以下是本发明列举的实施例。实施例1称取18g环氧树脂、4g501稀释剂、3g2-乙基-4-甲基咪唑,常温下混合搅拌0.5h。随后加入75g未处理fesial粉,再添加0.24gkh-550,在真空辅助下混合搅拌8h,得到混合浆料。最后,将混合浆料倒入模具中,在1.2mpa压力、110℃下热压罐固化成型,最终得铁氧体/环氧树脂复合材料。实施例2将400g钢球(8mm直径钢球167g+6mm直径钢球233g)与120gfesial粉混合,随后一起加入0.02g硬脂酸钙与250ml丙酮再置于球磨罐中,固定转速450r/min高能球磨7.5h,得到平均片长为30-35μm的片状铁氧体,其微观形貌图参考图1。称取18g环氧树脂、4g501稀释剂、3g2-乙基-4-甲基咪唑,常温下混合搅拌0.5h,随后加入75g球磨处理的片状fesial粉,再添加0.24gkh-550,在真空辅助下混合搅拌8h,得到混合浆料。最后,将复合浆料倒入模具中,在1.2mpa压力、110℃下热压罐固化成型,最终得片状fesial/环氧树脂复合材料。实施例3将400g钢球(8mm直径钢球167g+6mm直径钢球233g)与120gfesial粉混合,随后一起加入0.02g硬脂酸钙与250ml丙酮再置于球磨罐中,固定转速450r/min高能球磨7.5h,得到平均片长为30-35μm的片状铁氧体。称取18g环氧树脂、4g501稀释剂、3g2-乙基-4-甲基咪唑,常温下混合搅拌0.5h,随后加入75g球磨处理的片状fesial粉,再添加0.24gkh-550,置于80℃、40khz条件下的超声分散器中缓慢搅拌2h,得到混合浆料。最后,在90-100℃下超声固化1.5h,最终得片状fesial/环氧树脂复合材料。实施例4将400g钢球(8mm直径钢球167g+6mm直径钢球233g)与120gfesial粉混合,随后一起加入0.02g硬脂酸钙与250ml丙酮再置于球磨罐中,固定转速450r/min高能球磨7.5h,得到平均片长为30-35μm的片状铁氧体。称取18g环氧树脂、4g501稀释剂、3g2-乙基-4-甲基咪唑,常温下混合搅拌0.5h,随后加入58g球磨处理的片状fesial粉,再添加0.18gkh-550,在真空辅助下混合搅拌6h,得到混合浆料。最后,将混合浆料倒入模具中,在1.2mpa压力、110℃下热压罐固化成型,最终得片状fesial/环氧树脂复合材料。表1记载了实施例1至4的制备工艺。表1编号是否球磨片状fesial粉用量环氧树脂用量实施例1否75g*18g实施例2是75g18g实施例3是75g18g实施例4是58g18g注明:此处75g指未球磨fesial粉的用量。按照sj20512-1995对实施例1至4制得的复合材料的电磁参数进行测试,复合材料的电磁参数测试结果见表2。表2注:ε’为相对复介电常数的实部;ε”为相对复介电常数的虚部;μ’为相对复磁导率的实部;μ”为相对复磁导率的虚部;tanσd为电损耗正切角;tanσm为磁损耗正切角。从实施例1(未进行球磨)与实施例2和实施例3的测试结果对比可看出,通过球磨处理后所得片状fesial/环氧树脂复合材料在高频点具有较高的磁导率与介电常数。从实施例2与实施例3结果对比可看出,采用超声固化所制备的复合材料具有较高的磁损耗。从实施例3与实施例4结果对比可看出,随着片状铁氧体添加量的提高,会提高复合材料磁损耗。结合实施例1和实施例4的对比结果可知,当铁氧体的填充量较低时无法达到显著提高复合材料磁损耗的效果。但铁氧体的添加量也不易过多,太多会导致粘度过大,分散均匀性变差,气泡难以排除,工艺性变差。本发明在制备过程中将片状铁氧体和树脂(70-80):(15-25)用量配比混合,最优选按照(75-80):(15-20)这一用量配比混合,即可显著提高复合材料的磁导率和磁损耗,又可降低制备工艺的难度。实施例5与实施例2的制备方法基本上相同,不同之处在于:所用的偶联改性剂为kh-570(化学名为:γ-(甲基丙烯酰氧)丙基三甲氧基硅烷)。实施例6与实施例2的制备方法基本上相同,不同之处在于:球磨时转速为600r/min。实施例7与实施例2的制备方法基本上相同,不同之处在于:球磨时间为9h。实施例8与实施例2的制备方法基本上相同,不同之处在于:球磨时所用钢球包含5mm直径的钢球200g+3mm直径的钢球200g。表3本发明采用球磨法制备片状铁氧体粉体,通过偶联改性与环氧树脂复合,运用热压罐工艺或超声固化成型(优选采用超声固化成型)电磁负载复合材料,其在1-18ghz频段表现出较高的电磁参数,可广泛应用于雷达、导航、卫星通信、电子对抗、广播电视、移动通讯等各领域电子设备中。最后应说明的是:以上实施例仅用以说明本发明的技术方案,而非对其限制;尽管参照前述实施例对本发明进行了详细的说明,本领域的普通技术人员应当理解:其依然可以对前述各实施例所记载的技术方案进行修改,或者对其中部分技术特征进行等同替换;而这些修改或者替换,并不使相应技术方案的本质脱离本发明各实施例技术方案的精神和范围。当前第1页12