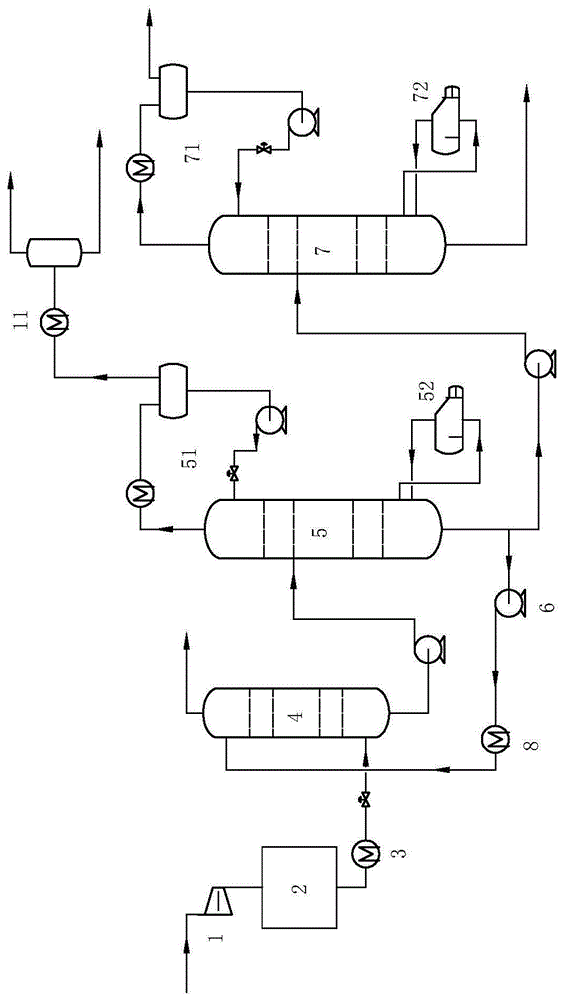
本发明涉及一种回收炼厂加氢装置尾气中各种有效组分的方法。
背景技术:
:炼油厂的加氢装置在生产过程中,会产生一定量的加氢装置尾气,其组分含酸性气、氢气、甲烷、乙烷以及c2以上的烷烃。目前多数炼厂加氢装置尾气直接作为燃料使用,利用价值较低,而如果能将加氢装置尾气中的各个成分进行提纯回收,其作为化工产品的价值则要远高于其作为燃料的价值。为了加氢装置尾气中的各个成分进行提纯回收,诸多企业和学术机构对瓦斯中高价值组分提取方法做了深入的探索。目前业界主要关注的是从干气瓦斯等副产气中提取c2及其以上组分进行回收,特别是高价值的烯烃。回收方法也是各有不同,例如:美国abb公司对炼厂气低温分离回收c2及c2以上组分;中石油北京化工研究院利用浅冷吸收技术回收加氢装置尾气中的烯烃等,均取得了良好的投资回收效益。还有其他诸多机构也提出了从炼厂气、油田伴生气和天然气等原料中回收c2及c2以上组分的技术方法。然而,目前的回收方法仅能实现对c2及c2以上组分的分离,对于c2以下的组分例如甲烷、氢气等则无法分离,导致加氢装置尾气的资源利用率受到限制。技术实现要素:本发明所要解决的技术问题是针对现有技术的现状,提供一种回收炼厂加氢装置尾气中各种有效组分的方法,该方法能对氢气、甲烷、c2及c2以上的烯烃和烷烃均进行分离回收,从而提高加氢装置尾气的资源利用率、将加氢尾气的价值最大化。本发明解决上述技术问题所采用的技术方案为:一种回收炼厂加氢装置尾气中各种有效组分的方法,其特征在于包括以下步骤:(1)杂质脱除对炼厂加氢装置尾气中的水分、酸性气及其它杂质进行脱除;(2)尾气冷却将步骤(1)所得尾气进行冷却,冷却至甲烷吸收塔的适宜入口温度;(3)甲烷吸收步骤(2)所得尾气送入甲烷吸收塔,同时在甲烷吸收塔的塔顶送入低温液体吸收剂,在甲烷吸收塔内完成对甲烷及其以上碳氢化合物组分的吸收过程,其中,c1及其以上碳氢化合物组分以液相从塔底离开甲烷吸收塔,塔顶输出气相的主要成分为氢气;上述吸收剂是干气的甲烷、氢气和杂质被剥离后,剩下的c2及其以上组分,该吸收剂是干气的一部分在液化之后循环做吸收剂在使用;吸收剂的组分是可以调整的、可以根据干气中c2及其以上组分的变化而变化的;(4)脱甲烷塔精馏甲烷吸收塔塔底输出的液相送入脱甲烷精馏塔,使得甲烷组分同其他碳氢化合物组分分离开来,甲烷从塔顶以气相输出,c2及其以上组分从塔底以液相输出;(5)乙烷精馏脱甲烷精馏塔塔底的液相送入乙烷精馏塔,在塔内完成乙烷与c3及其以上组分的分离,其中,乙烷从塔顶以气相输出,c3及其以上组分从塔底以液相输出。步骤(1)中,杂质脱除之前,可选择的对来自装置的加氢尾气进行压缩,提升其压力,使原料气能够达到后续杂质脱除、甲烷吸收塔所需的压力要求,如原料气压力足够高,这一步骤可以省略。所述杂质脱除过程包括去除酸性气、水分和其他杂质,最后在塔压2.5-3bara、温度-135℃~-140℃下,将气相中的甲烷吸收到液相中。在这个条件下,水和含氧组分可能存在结冰或其他安全隐患、且会显著影响降低产品甲烷的纯度,硫化物本身就是污染组分,这些杂质都需要在进入甲烷吸收塔前清除。步骤(2)中,所述甲烷吸收塔的塔压为2.5~3bara条件下,干气冷却至-135℃~-140℃。优选地,所述甲烷吸收塔中设置有中段制冷,甲烷吸收塔内的操作压力为2.5~3.0bara、操作温度为-137.8℃~-139.8℃;甲烷吸收塔的塔顶送入低温液体吸收剂温度为-135℃~-145℃。采用下一步脱甲烷精馏塔塔底产物循环冷却回流液体作为吸收剂(以炼厂加氢尾气为例主要包括乙烷、丙烷以及少量c4以上碳氢化合物),将尾气中的c1及c1以上的碳氢化合物吸收到液体,并尽量防止h2等杂质组分进入液相产品。从脱甲烷精馏塔来的循环吸收剂需要被冷却到与吸收塔塔顶温度相接近的温度。另外,对于甲烷含量较高的尾气的吸收,放热效应较为显著,在吸收塔设置中段制冷,以减少吸收剂循环量。采用上述参数,吸收塔塔顶气相产品可以做到高纯度(99%+摩尔分率)氢气产品。步骤(4)中,在脱甲烷塔精馏过程中,在塔顶设置能使部分输出物经冷凝回流至脱甲烷精馏塔中的塔顶冷凝器,在塔底设置有使塔底液相经升温回流至脱甲烷精馏塔中的塔底再沸器。所述脱甲烷精馏塔内压力在2.0~2.5bara,且塔顶气相c2摩尔分数不超过0.001的情况下,塔顶冷凝器操作温度为-149.6℃,塔底再沸器操作温度为-39.2℃。该参数可轻易实现95%以上的甲烷产品浓度分离。步骤(5)中,在乙烷精馏过程中,在塔顶设置能使部分输出物经冷凝回流至乙烷精馏塔中的塔顶冷凝器,在塔底设置有使塔底液相经升温回流至乙烷精馏塔中的塔底再沸器。所述乙烷精馏塔塔顶塔底压力分别为8.0bara、9.0bara,丙烷在塔顶气相的摩尔浓度不超过0.01%,乙烷在塔底的摩尔浓度不超过0.1%条件下,冷凝温度为-39.2℃,再沸温度为48℃。步骤(3)中,可选的对塔顶输出气相中的氢气进行回收,回收方法为膜分离、变压吸附、深冷工艺中的一种;步骤(5)中,可选的对塔顶的乙烷进行液化处理、产生天然气产生。为了便于调控吸收剂压力,所述脱甲烷精馏塔塔底作为低温液体吸收剂送入甲烷吸收塔的部分液相经过吸收剂冷却器降温,而在进入吸收剂冷却器之前,可选的进入吸收剂循环泵加压处理。与现有技术相比,本发明的优点在于:本发明利用深冷技术实现了对炼厂加氢装置尾气中各种有效组分进行分离回收,特别是利用干气中c2及其以上组分做循环吸收剂、通过深冷吸收的分离方式实现了对甲烷组分的分离回收,从而将干气中的甲烷组分作为单独的产品加以生产。此外,经过甲烷吸收塔输出的气体中氢气浓度较高,便于回收。整体而言,本发明实现了对加氢尾气中的氢气、甲烷、c2及c2以上的烯烃和烷烃的完整分离回收,提高了加氢装置尾气的资源利用率、将加氢装置尾气的价值最大化。附图说明图1为本发明实施例的工艺流程示意图。具体实施方式以下结合附图实施例对本发明作进一步详细描述。如图1所示,以某炼油厂加氢装置尾气为例(表1为尾气成分),对本发明回收炼厂加氢装置尾气中各种有效组分的方法进行说明,方法如下:表1:来自加氢装置的混合尾气的组分流量(1)尾气压缩:来自装置的混合尾气的原始压力为1.5bara,进入压缩机1对其进行压缩,提升其压力至7.5bara。(2)脱除杂质:加氢尾气进入杂质脱除单元2,经过去除酸性气、水分和其他杂质各部,将上述杂质去除。此时混合尾气的压力约14.5bara,组成如表2所示:表2:脱除杂质后的混合尾气的流量和组成质量流量kg/h摩尔分率氢气719.178.2%氧气0.00.0%氮气0.00.0%一氧化碳0.00.0%二氧化碳0.00.0%甲烷419.65.7%乙烯0.00.0%乙烷579.34.2%丙烯0.00.0%丙烷1018.95.1%c4+1919.76.8%硫化氢0.00.0%水0.00.0%(3)尾气冷却:去除杂质的混合尾气经冷却器3从常温冷却至约-134℃,且降压至3.0bara。(4)甲烷吸收:混合尾气自塔底进入甲烷吸收塔4,同时塔顶部送入循环液体吸收剂(温度约-140℃)。整个塔的操作压力为2.5-3.0bara,操作温度在-137.8℃~-139.8℃之间。甲烷吸收塔4内部设中段制冷。表3展示了甲烷吸收塔的吸收剂、塔顶塔底产物的组分和流量。表3:甲烷吸收塔相应流股的组分和流量(5)脱甲烷塔精馏:甲烷吸收塔塔底液体送入脱甲烷精馏塔5,脱甲烷精馏塔5操作压力为2.0-2.5bara。塔顶气相产物要求乙烷摩尔分数不超过0.001,塔底液相要求甲烷摩尔分数不超过0.0001。塔顶冷凝器51控制操作温度约-149.6℃,塔底再沸器52控制温度要求约-39.2℃。塔底液相产品中48317kg/h送入吸收剂循环泵6,经冷却器8冷却后送入甲烷吸收塔4作为冷却剂,3489kg/h送入后续乙烷精馏塔7。塔顶和塔底产物的流量和组分见表4:表4:脱甲烷塔塔顶和塔底流股的组分和流量(6)吸收剂循环和冷却:从脱甲烷精馏塔7塔底来的48317kg/h循环吸收剂先送入循环泵,后送入循环吸收剂冷却至-140℃,并送返回甲烷吸收塔4。(7)乙烷精馏:将脱甲烷精馏塔5塔底的液相产物加热到送入乙烷精馏塔7,从塔顶分馏出乙烷,塔底出c3及其以上产品。乙烷精馏塔7的塔顶塔底压力分别设定为8.0bara和9.0bara。精馏要求丙烷在塔顶气相的摩尔浓度不超过0.01%,乙烷在塔底的摩尔浓度不超过0.1%。该塔塔顶冷凝器71和塔底再沸器72所提供的温度分别是-39.2℃和48.0℃。塔顶收548.7kg/h乙烷,摩尔浓度为99.9%。塔底剩余2940kg/h的c3及其以上组分。由于一般炼厂的都有气体分离装置精制c3、c4,因此乙烷精馏塔塔底产品可以直接送入现有气分装置。本实施例甲烷吸收塔塔顶气相产品氢气摩尔分率已超过99%,因此不再增设额外的氢气提纯设备。(8)甲烷液化:将脱甲烷精馏塔5塔顶气相经冷凝单元11进一步冷却到-162℃,1.25bara,可以获得362.5kg/h甲烷含量为99.8%的液化天然气。同时获得34.1kg/h、甲烷含量79.0%的不凝气。当前第1页12