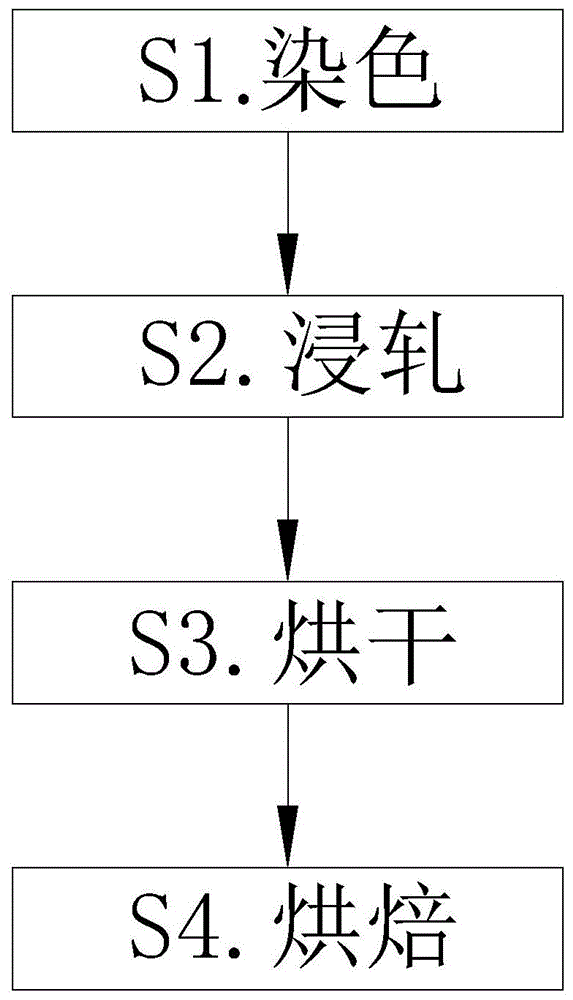
本发明涉及纺织助剂的
技术领域:
,尤其是涉及一种超纤革固色用无醛固色剂及固色工艺。
背景技术:
:超细纤维合成革由锦纶超细纤维和聚氨酯两部分构成,它们紧密连接在一起。在基布结构中,超细纤维三维交联在一起,起到骨架和支撑作用,形成类似于真皮胶原纤维的结构。分布在超细纤维四周的是聚氨酯,它使整个合成革基布形成一个整体,并具备了许多功能。它在革体中不是简单的填充,而是具有许多圆形的、针形的发泡结构,整体呈立体网状。其间的发沟结构交错连通,形成微细的通透结构,使革体具有一定的透气透湿性能。合成革在整体上是均匀的,不存在部位差,这也正是合成革在应用中的一大优势。但是在具体的点与点之间,在正面与反面之间,在纤维和聚氨酯的点状分布上,是存在差异的。超细纤维在革体中尤其是表面存在的点状差别会大大增加超细纤维合成革的固色难度,导致超细纤维合成革染色过程中出现固色牢度效果差、固色不均匀、存在色斑等一系列缺陷。目前,公告号为cn102887989a的中国发明专利公开了一种新型无醛固色剂,由二乙烯三胺(ae)、环氧氯丙烷(ep)、二甲基二烯丙基氯化铵(dmdaac)配制而成,其配制工艺步骤如下:a)取一定量水和二乙烯三胺(ae)加入反应器中,搅拌;b)滴加环氧氯丙烷(ep),控制温度在40~50℃;c)反应1-2小时后,测试反应溶液的ph值,若为碱性,则用冰醋酸调节为弱酸性;d)滴加二甲基二烯丙基氯化铵(dmdaac),控制温度在60~80℃;e)反应2~4小时后测试反应溶液的ph值并用试剂将体系溶液调节为中性或者弱碱性,合格后冷却至室温,出料即得成品。上述中的现有技术方案存在以下缺陷:上述方案采用二乙烯三胺与环氧氯丙烷反应,以二甲基二烯丙基氯化铵为催化剂制备固色剂,生成的固色剂中的阳离子基团活性较低,与超细纤维以及染料结合度低,导致固色剂的固色性能较差,导致制备出的超纤革上的染料耐磨性差,易在摩擦中褪色。技术实现要素:针对现有技术存在的不足,本发明的目的一是提供一种超纤革固色用无醛固色剂,其具有良好的固色性能,使得染料在超纤革上固着更加牢固。本发明的目的二是提供一种使用目的一中的无醛固色剂的超纤革固色工艺。本发明的上述目的一是通过以下技术方案得以实现的:一种超纤革固色用无醛固色剂,按质量分数包括以下组分:乙二胺10-15%、二乙烯三胺5-7%、二甲胺3-7%、环氧氯丙烷20-30%、去离子水40-65%、冰醋酸0.4-0.6%以及催化剂0.005-0.015%。通过采用上述技术方案,乙二胺、二乙烯三胺以及二甲胺均与环氧氯丙烷进行加成反应,生成的聚合物含有高活性阳离子基团,阳离子基团与阴离子染料以离子键结合,在超细纤维上形成难溶或不溶的色淀,封闭染料分子的水溶性基团,起到固色作用;同时,聚合物分子结构中的反应性基团可以与超细纤维上的羟基发生交联反应,使得染料在纤维上固着的更加牢固;二甲胺溶液碱性较大,在与环氧氯丙烷加成之余,还有利于调节反应液的碱性,加成反应在碱性溶液中生成聚合物的单一性与稳定性更高,从而减少杂质物的生成数量以及提高聚合物的反应效率,以此确保固色剂的品质;乙二胺分子结构中含有二官能团,二乙烯三胺分子结构中含有三官能团,使得两种组分均可发生局部交联反应,从而使固色剂在超细纤维上成膜,以此将染料包覆在膜体内,从而提高超纤革的耐水性以及耐磨性;二甲胺、乙二胺以及二乙烯三胺三者按照适当的比例混合并与环氧氯丙烷反应制备的固色剂相较于单独添加一种单体与环氧氯丙烷反应制成的固色剂具有更高的固色性能;由于固色剂分子交联度不高,因此成膜质地柔软,超纤革手感柔软;反应制成的固色剂不含甲醛成分,因此无甲醛释放,使用更安全、更环保。本发明在一较佳示例中可以进一步配置为:按质量分数包括以下组分:乙二胺12%、二乙烯三胺6%、二甲胺5%、环氧氯丙烷25%、去离子水51.49%、冰醋酸0.5%以及催化剂0.01%。本发明在一较佳示例中可以进一步配置为:所述固色剂的制备方法为:a1.稀释:向反应釜内加入乙二胺以及二乙烯三胺,再加入去离子水进行稀释;a2.冷却:对稀释液进行冷水循环,将温度冷却至22-27℃;a3.加成反应1:向稀释液中缓慢滴加环氧氯丙烷,滴加过程保持温度为35-40℃;a4.保温反应1:环氧氯丙烷滴加完毕后,添加催化剂并将反应液升温至45℃,保温反应1.8-2.2h;a5.加成反应2:缓慢滴加二甲胺溶液,继续反应0.7-1.2h;a6.保温反应2:将反应液升温至60℃,保温反应4.5-5.5h;a7.测试ph:通过ph显示仪观测反应液的ph,当ph值为6.8-7.2时,反应完成,将反应液冷却至20-25℃,制得固色剂。通过采用上述技术方案,在稀释过程中会伴随放热,造成稀释液温度升高,导致滴加环氧氯丙烷时反应加剧而容易造成副产物过多、且合成成品颜色偏深的问题,因此,在滴加环氧氯丙烷之前需要对稀释液进行冷却处理;环氧氯丙烷滴加完成后,需要进行保温反应以使反应完全,反应液在较低的温度下,反应更加稳定,生成的聚合物数量更加单一,因此,将保温反应1温度设置为45℃,将保温反应2温度设置为60℃;当反应液的ph为中性时才可判断反应完全,反应完成后,还需将反应液冷却至20-25℃,降温的过程有利于提高固色剂的稳定性。本发明在一较佳示例中可以进一步配置为:向固色剂溶液中滴加冰醋酸,将固色剂的ph调节至5-6。通过采用上述技术方案,随着固色剂ph的升高,超纤上的羧酸基离子逐渐质子化,染料阴离子与氨基、固色剂阳离子结合,导致部分染料从织物表面脱落,造成超纤革色牢度下降;在较强的酸性条件下,超纤在染浴中以两性离子存在,会对超纤革表面造成损伤,导致其表面粗糙度增加,从而导致固色剂分子在超纤革表面分布不均,影响固色效果;当固色剂ph为5-6时,超纤呈现阴离子性,固色剂阳离子在染料阴离子和织物之间起架桥作用,从而提高其固色效率以及固色均匀性,固色前后色光变化更小。本发明在一较佳示例中可以进一步配置为:所述催化剂为有机胺类催化剂。通过采用上述技术方案,有机胺类催化剂为弱碱性催化剂,一方面具有加快加成反应正向反应效率的作用,另一方面,有利于调节反应液的ph,使得加成反应更加稳定,生成的聚合物数量更加单一,从而进一步确保固色剂的固色性能。本发明的上述目的二是通过以下技术方案得以实现的:一种超纤革固色工艺,具体包括以下制备步骤:s1.染色:对超纤革进行染色处理;s2.浸轧:将染色完成的超纤革浸渍在固色整理液中,浴比为15:1,固色温度为45-55℃,浸渍时间为3-7min,并采用二浸二轧方式对超纤革进行浸轧处理;s3.烘干:对浸轧完成的超纤革进行烘干处理,烘干温度为75-85℃,烘干时间为2-5min,制得预成品;s4.焙烘:对预成品进行烘焙处理,烘焙温度为120-140℃,烘焙时间为1-5min,制得成品。本发明在一较佳示例中可以进一步配置为:所述固色整理液为4%固色剂稀释液。本发明在一较佳示例中可以进一步配置为:所述4%固色剂稀释液所采用的稀释剂按质量分数包括以下组分:丙酮90-98%以及硅油1-12%。通过采用上述技术方案,固色剂与丙酮相溶性良好,且丙酮自身偏中性,对固色剂的影响较小;丙酮可吸收一定波长范围内的紫外线,从而防止紫外线对超纤革上染色结构的破坏,以此提高染料的日晒固色牢度;硅油具有良好的平滑作用,有利于减少超细纤维表面的摩擦系数,从而提高染料与超纤革之间的摩擦牢度。综上所述,本发明包括以下至少一种有益技术效果:1.二甲胺、乙二胺以及二乙烯三胺三者按照适当的比例混合并与环氧氯丙烷反应制备的固色剂相较于单独添加一种单体与环氧氯丙烷反应制成的固色剂具有更高的固色性能;2.二甲胺溶液碱性较大,有利于调节反应液的碱性,从而减少杂质物的生成数量以及提高聚合物的反应效率,以此确保固色剂的品质;3.丙酮可吸收一定波长范围内的紫外线,从而防止紫外线对超纤革上染色结构的破坏,以此提高染料的日晒固色牢度;4.当固色剂ph为5-6时,超纤呈现阴离子性,固色剂阳离子在染料阴离子和织物之间起架桥作用,从而提高其固色效率以及固色均匀性,固色前后色光变化更小。附图说明图1是本实施例中固色工艺的流程示意图;图2是本实施例中固色剂的制备方法流程示意图。具体实施方式以下结合附图对本发明作进一步详细说明。实施例1,为本发明公开的一种超纤革固色用无醛固色剂及固色工艺,固色剂按质量分数包括以下组分:组分质量分数/%组分质量分数/%乙二胺12去离子水51.49二乙烯三胺6冰醋酸0.5二甲胺5有机胺类催化剂0.01环氧氯丙烷25固色剂的制备方法为:a1.稀释:向反应釜内加入乙二胺、二乙烯三胺以及二甲胺,再加入去离子水进行稀释;a2.冷却:对稀释液进行冷水循环,将温度冷却至25℃;a3.加成反应:向稀释液中缓慢滴加环氧氯丙烷,滴加过程保持温度为35℃;a4.保温反应:环氧氯丙烷滴加完毕后,添加催化剂并将反应液升温至45℃,保温反应2h;a5.加成反应2:缓慢滴加二甲胺溶液,继续反应1h;a6.保温反应2:将反应液升温至60℃,保温反应5h;a7.测试ph:通过ph显示仪观测反应液的ph,当ph值为7时,反应完成,将反应液冷却至25℃,制得固色剂;a8.调节ph:向固色剂溶液中滴加冰醋酸,将固色剂的ph调节至5.5;超纤革固色工艺具体包括以下步骤:s1.染色:对超纤革进行染色处理;s2.浸轧:将染色完成的超纤革浸渍在4%固色剂稀释液中,浴比为15:1,固色温度为50℃,浸渍时间为5min,并采用二浸二轧方式对超纤革进行浸轧处理;s3.烘干:对浸轧完成的超纤革进行烘干处理,烘干温度为80℃,烘干时间为3min,制得预成品;s4.焙烘:对预成品进行烘焙处理,烘焙温度为130℃,烘焙时间为3min,制得成品;超纤革固色工艺中,4%固色剂稀释液所采用的稀释剂按质量分数包括以下组分:丙酮94.5%以及硅油5.5%。实施例2,为本发明公开的一种超纤革固色用无醛固色剂及固色工艺,固色剂按质量分数包括以下组分:组分质量分数/%组分质量分数/%乙二胺10去离子水55.595二乙烯三胺7冰醋酸0.4二甲胺7有机胺类催化剂0.005环氧氯丙烷20固色剂的制备方法同实施例1;超纤革固色工艺同实施例1;超纤革固色工艺中,4%固色剂稀释液所采用的稀释剂按质量分数包括以下组分:丙酮94.5%以及硅油5.5%。实施例3,为本发明公开的一种超纤革固色用无醛固色剂及固色工艺,固色剂按质量分数包括以下组分:固色剂的制备方法同实施例1;超纤革固色工艺同实施例1;超纤革固色工艺中,4%固色剂稀释液所采用的稀释剂按质量分数包括以下组分:丙酮94.5%以及硅油5.5%。实施例4,与实施例1的不同之处在于:超纤革固色工艺中,4%固色剂稀释液所采用的稀释剂按质量分数包括以下组分:丙酮90%以及硅油10%。实施例5,与实施例1的不同之处在于:超纤革固色工艺中,4%固色剂稀释液所采用的稀释剂按质量分数包括以下组分:丙酮98%以及硅油2%。实施例6,与实施例1的不同之处在于:固色剂的制备方法:a8.调节ph:向固色剂溶液中滴加冰醋酸,将固色剂的ph调节至5。实施例7,与实施例1的不同之处在于:固色剂的制备方法:a8.调节ph:向固色剂溶液中滴加冰醋酸,将固色剂的ph调节至6。实施例8,与实施例的不同之处在于删除固色剂的制备方法中的a8。对比例1,为本发明公开的一种超纤革固色用无醛固色剂及固色工艺,固色剂按质量分数包括以下组分:组分质量分数/%组分质量分数/%乙二胺0去离子水51.49二乙烯三胺23冰醋酸0.5二甲胺0有机胺类催化剂0.01环氧氯丙烷25固色剂的制备方法同实施例1;超纤革固色工艺同实施例1;超纤革固色工艺中,4%固色剂稀释液所采用的稀释剂按质量分数包括以下组分:丙酮94.5%以及硅油5.5%。对比例2,为本发明公开的一种超纤革固色用无醛固色剂及固色工艺,固色剂按质量分数包括以下组分:固色剂的制备方法同实施例1;超纤革固色工艺同实施例1;超纤革固色工艺中,4%固色剂稀释液所采用的稀释剂按质量分数包括以下组分:丙酮94.5%以及硅油5.5%。对比例3,为本发明公开的一种超纤革固色用无醛固色剂及固色工艺,固色剂按质量分数包括以下组分:组分质量分数/%组分质量分数/%乙二胺15.3去离子水51.49二乙烯三胺7.7冰醋酸0.5二甲胺0有机胺类催化剂0.01环氧氯丙烷25固色剂的制备方法同实施例1;超纤革固色工艺同实施例1;超纤革固色工艺中,4%固色剂稀释液所采用的稀释剂按质量分数包括以下组分:丙酮94.5%以及硅油5.5%。对比例4,为本发明公开的一种超纤革固色用无醛固色剂及固色工艺,固色剂按质量分数包括以下组分:组分质量分数/%组分质量分数/%乙二胺16.2去离子水51.49二乙烯三胺0冰醋酸0.5二甲胺6.8有机胺类催化剂0.01环氧氯丙烷25固色剂的制备方法同实施例1;超纤革固色工艺同实施例1;超纤革固色工艺中,4%固色剂稀释液所采用的稀释剂按质量分数包括以下组分:丙酮94.5%以及硅油5.5%。对比例5,为本发明公开的一种超纤革固色用无醛固色剂及固色工艺,固色剂按质量分数包括以下组分:乙二胺10-15%、二乙烯三胺5-7%、二甲胺3-7%、环氧氯丙烷20-30%、去离子水48-54%、冰醋酸0.4-0.6%以及催化剂0.005-0.015%;固色剂的制备方法同实施例1;超纤革固色工艺同实施例1;超纤革固色工艺中,4%固色剂稀释液所采用的稀释剂按质量分数包括以下组分:丙酮94.5%以及硅油5.5%。对比例6,为本发明公开的一种超纤革固色用无醛固色剂及固色工艺,固色剂按质量分数包括以下组分:组分质量分数/%组分质量分数/%三乙胺12去离子水51.49四乙烯五胺6冰醋酸0.5二甲胺5有机胺类催化剂0.01环氧氯丙烷25固色剂的制备方法同实施例1;超纤革固色工艺同实施例1;超纤革固色工艺中,4%固色剂稀释液所采用的稀释剂按质量分数包括以下组分:丙酮94.5%以及硅油5.5%。对比例7,与实施例1的不同之处在于:超纤革固色工艺中,4%固色剂稀释液所采用的稀释剂为水。对比例8,与实施例1的不同之处在于:超纤革固色工艺中,4%固色剂稀释液所采用的稀释剂为丙酮。对比例9,与实施例1的不同之处在于:固色剂的制备方法:a8.调节ph:向固色剂溶液中滴加冰醋酸,将固色剂的ph调节至4.8。对比例10,与实施例1的不同之处在于:固色剂的制备方法:a8.调节ph:向固色剂溶液中滴加冰醋酸,将固色剂的ph调节至6.2。性能检测试验采用由实施例1-8以及对比例1-10中的固色剂以及固色工艺对超纤革进行固色处理,并对处理后的超纤革进行取样,对样品进行以下性能检测试验。色斑沉淀观察:肉眼观察超纤革上的色斑沉淀情况,并根据色斑面积的大小对样品品质进行分级:无色斑记为1级;色斑面积<4%记为2级,4%≤色斑面积<8%记为3级,8%≤色斑面积<12%记为4级,12%≤色斑面积记为5级;将结果记录在表1中。耐摩擦牢度检测试验:按gb3920-1997标准对样品进行检测,并将检测结果记录在表1中;干摩擦牢度的测定方法:将样品固定在耐摩擦色牢度试验仪的摩擦头上,并使摩擦头运行方向呈45度角,在样品的长度方向上10s内摩擦10次,往复动程为100mm,垂直压力为9n,然后用灰色样卡评定摩擦位置的干摩擦牢度等级,等级越大,牢度越强;湿摩擦牢度测定方法:将样品用蒸馏水浸湿,用耐摩擦色牢度试验仪的轧液使样品带液率达到100%;将样品固定在耐摩色牢度试验仪的摩擦头上,并使摩擦布的经向与摩擦头运行方向呈45度角,在样品的长度方向上10s内摩擦10次,往复动程为100mm,垂直压力为9n。摩擦结束后,在室温下晾干,用灰色样卡评定摩擦位置的湿摩擦牢度等级,等级越大,牢度越强。皂洗牢度检测试验:按gbgb3921-1997标准对样品进行检测,纺织品耐洗色牢度试验方法,用灰色样卡评定沾色等级,等级越大,牢度越强,并将检测结果记录在表1中。表1为样品的各项性能测试数据根据表1中实施例1-3的样品检测数据可知:在合适的范围内改变组分之间的配比对于样品的耐摩擦牢度以及皂洗牢度影响不大,且样品表面无色斑,但三个实施例中实施例1的组分配比为最佳配比。根据实施例1以及对比例1-6的样品检测数据可知:二乙烯三胺、乙二胺以及二甲胺三者按适当的比例添加反应制备的固色剂固色性能最佳。根据实施例1、实施例4-5以及对比例7-8的样品检测数据可知:稀释液中丙酮与硅油的配比不同,样品的耐摩擦牢度以及皂洗牢度会有所改变,实施例1中丙酮与硅油的配比是三个实施例中的最佳配比;使用丙酮代替水来稀释固色剂,样品的色斑面积有所减少,耐摩擦牢度以及皂洗牢度均有所提升;向丙酮中添加硅油有利于进一步提高样品的耐摩擦牢度以及皂洗牢度,缩小样品的色斑面积。根据实施例1以及实施例6-8以及对比例9-10的样品检测数据可知:固色剂的ph值对于样品的耐摩擦牢度以及皂洗牢度具有一定的影响;固色剂的ph值过高或过低,样品表面均会形成色斑沉淀,且样品的耐摩擦牢度以及皂洗牢度均有所下降,因此,固色剂的ph值应调节至合适的范围内。本具体实施方式的实施例均为本发明的较佳实施例,并非依此限制本发明的保护范围,故:凡依本发明的结构、形状、原理所做的等效变化,均应涵盖于本发明的保护范围之内。当前第1页12