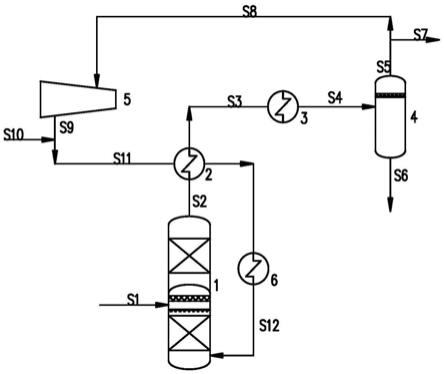
1.本发明属于乙二醇生产技术领域,涉及一种由碳酸乙烯酯生产乙二醇联产甲醇的工艺。
背景技术:2.当今,二氧化碳导致的温室效应及环境破坏日益加剧,作为储量丰富的碳一化合物,二氧化碳是一种稳定且廉价的碳资源,发展二氧化碳资源绿色转化利用具有重要的资源、环境与经济意义。
3.甲醇和乙二醇是碳一化学利用的两种重要产物。其中,甲醇有“甲醇经济”之称,在能源和化工方面均具有重要作用,可作为有机化工原料、液体燃料、储氢载体及良好溶剂。而乙二醇作为一种基础化工原料,可用于生产聚酯树脂,醇酸树脂和聚酯纤维,还可用于胶黏剂、增塑剂、油漆、炸药、非离子型表面活性剂等领域。利用二氧化碳资源,化学转化合成甲醇与乙二醇等化学品,对能源、环境和经济具有重要意义。
4.由于二氧化碳分子的热力学稳定性好和动力学惰性等特点,二氧化碳直接加氢转化路线存在反应条件要求高、催化剂活性低等问题。目前,工业上已实现二氧化碳与环氧乙烷生产碳酸乙烯酯的过程,该反应具有很高的反应活性和选择性。因此,以二氧化碳为原料,首先制备碳酸乙烯酯,然后将碳酸乙烯酯与氢气在温和条件下反应生产乙二醇同时联产甲醇,可实现二氧化碳的高效间接利用,具有较大的应用潜力。
5.cn108816227a公开了一种通过金属框架衍生的一步水解沉淀法制得的金属框架衍生负载型铜基催化剂,利用碳与铜的协同作用,进一步提升催化剂活性及稳定性,采用该催化剂,碳酸乙烯酯转化率可达100%,乙二醇选择性可达100%,甲醇选择性可达75%以上。cn108554407a公开了一种纳米铜基催化剂及其制备方法,利用有机物积碳作用抑制活性铜物种的团聚,为铜基催化剂高温易烧结难题提供了一种解决手段,催化剂稳定性好。cn106881143a公开了一种利用蒸氨法制得的cuau双金属催化剂,将其应用于碳酸乙烯酯加氢体系时,碳酸乙烯酯转化率可达100%,乙二醇选择性可达100%,甲醇选择性可达70%以上。cn110227545a公开了一种以铜为活性组分,与糖类有机物利用蒸氨法制得的铜基催化剂,该催化剂低温活性好,寿命长,碳酸乙烯酯转化率可达99%,甲醇选择性可达85%以上,乙二醇选择性可达99%以上,催化剂可稳定运行500小时以上。cn110586094a公开了一种铜基纳米花催化剂及其制备方法,该催化剂具有特殊的纳米花状形貌,促进了活性铜物种的分散,在低氢酯摩尔比下具有优异的反应性能。
6.目前,有关于碳酸乙烯酯催化加氢反应的研究都偏重于催化剂本身的性能与制备过程,比如如何提高催化剂的活性、选择性及稳定性等方面,对加氢工艺流程的研究和优化几乎未见任何公开报道。已有资料中,催化剂的考评多采用搅拌釜间歇操作,反应体系需加入一定量的溶剂如四氢呋喃,1,4-二氧六环,环己烷等。然而在工业应用中,间歇操作效率较低,难以进行大规模生产,且气液固三相体系需在后续分离单元增加溶剂回收装置,提高设备投资及能耗。为解决上述问题,研究碳酸乙烯酯的气固相连续化催化加氢工艺具有重
要意义。
技术实现要素:7.本发明的目的就是为了克服上述现有技术存在的缺陷而提供一种由碳酸乙烯酯生产乙二醇联产甲醇的工艺。
8.加氢反应通常在带压条件下进行,当反应压力在3mpa时,碳酸乙烯酯的沸点高达443℃,远远超过加氢反应的温度区间。本发明通过实验研究发现,碳酸乙烯酯为热敏性物质,高温下易结焦聚合,因此,碳酸乙烯酯的汽化温度不宜过高。为降低碳酸乙烯酯的汽化温度,可利用大量氢气降低混合物中碳酸乙烯酯的分压,实现碳酸乙烯酯的汽化。在催化剂要求的氢酯摩尔比范围内,碳酸乙烯酯与氢气混合物的汽化温度与加氢反应的温度区间温差较小,过热度较低,汽化难度大。实际生产中,尽管可通过增加氢酯比来降低汽化温度,但过高的氢酯比会大幅增加循环圈负荷,从而增加设备投资与能耗。若汽化不完全使得反应床层进料时带液,会造成催化剂结焦,影响原料转化率和产物选择性,并降低催化剂寿命。前期实验过程中,经常由于碳酸乙烯酯汽化不充分而使上段催化剂结焦,增加了床层阻力降,并导致原料转化率和产物选择性下降。因此,如何在合适的氢酯摩尔比范围内,通过有效的汽化手段,并尽可能降低反应器入口段的热损以避免气体冷凝使得反应器进料时带液就显得尤为重要。为此,本发明进一步将碳酸乙烯酯的汽化与加氢反应耦合于一台加氢反应塔中,中间无需管路连接,最大程度降低了热损,通过填料汽化或者喷雾汽化的方式,有效增加气液接触面积,解决了该工艺中原料汽化难、催化剂易结焦失活等问题,有效延长了催化剂寿命,有利于连续化生产。整个加氢过程在无溶剂条件下连续化进行,无需增加溶剂脱除单元,节能降耗,全工艺流程简单,经济实用,为碳酸乙烯酯的气固相催化加氢过程提供了一种工业可行的解决方案。
9.本发明的目的可以通过以下技术方案来实现:
10.一种由碳酸乙烯酯生产乙二醇联产甲醇的工艺,包括以下步骤:
11.(1)氢气原料经预热后得到热氢气,再与碳酸乙烯酯一起送入加氢反应塔下部的汽化段汽化后,进入加氢反应塔上部的加氢反应段进行气固相催化加氢反应,得到加氢反应产物:
12.(2)所得加氢反应产物冷却后,送往气液分离罐中进行气液分离;
13.(3)气液分离罐顶部所得气相一部分排出,另外一部分作为氢气原料循环利用,气液分离罐底部即得到乙二醇和甲醇的液相混合产物。
14.进一步的,碳酸乙烯酯在汽化段汽化的方式为喷雾汽化或填料汽化。优选的,当采用喷雾汽化时,氢气原料和碳酸乙烯酯采用并流接触方式,当采用填料汽化时,氢气原料和碳酸乙烯酯采用逆流接触方式。加氢反应塔下部汽化段的内径需满足整个汽化过程中,碳酸乙烯酯雾滴不与加氢反应塔下部汽化段的内壁碰撞接触,避免雾化后的小液滴重新在汽化段的内壁形成液膜,影响汽化效果。
15.更进一步的,喷雾汽化具体为:在汽化段处设置有一个或多个喷嘴,碳酸乙烯酯经喷嘴雾化成雾滴后,与热氢气接触混合,即完成汽化。喷嘴数量及排布方式由汽化段尺寸及碳酸乙烯酯进料量决定,碳酸乙烯酯液体通过喷嘴雾化成直径为1~200微米的小液滴后与热氢气充分接触并瞬间汽化,雾化后的碳酸乙烯酯具有较大的表面积,有效增加了气液接
触面积,强化了热氢气与碳酸乙烯酯的热传递过程,实现了碳酸乙烯酯的瞬间汽化。
16.更进一步优选的,碳酸乙烯酯喷雾形成的雾滴直径为1~200微米。
17.更进一步的,填料汽化具体为:在汽化段布置有一段或分段串联布置的多段填料层,每段填料层的上方安装有液体分布器,碳酸乙烯酯经液体分布器均匀分布在填料层的填料表面并形成液膜,再与底部通入的热氢气接触混合,即完成汽化。
18.更进一步优选的,填料层所用填料为规整填料或者散堆填料。
19.进一步的,汽化段的出口位置还安装有丝网除沫器。
20.进一步的,加氢反应段的入口温度为170-220℃,反应压力为2-5mpa,氢酯摩尔比(即氢气与碳酸乙烯酯的摩尔比)为150-300:1。更优选的,入口温度为180-200℃,反应压力为2.5-4mpa,氢酯摩尔比为160-210。
21.进一步的,步骤(2)中,加氢反应产物进入气液分离罐前,被冷却至25-45℃。
22.进一步的,步骤(1)中,氢气原料先与从加氢反应段出来的加氢反应产物换热后,再被加热至180-240℃。
23.进一步的,步骤(3)中,气液分离罐顶部排出的气相占顶部所得气相总量的比值为0.01-0.1。
24.进一步的,作为氢气原料循环利用的气液分离罐顶部气相的摩尔浓度为90%-100%。
25.与现有技术相比,本发明具有以下优点:
26.(1)首次提出了一种碳酸乙烯酯经气固相催化加氢连续化生产乙二醇联产甲醇的新工艺;该工艺采用一台加氢反应塔实现碳酸乙烯酯的汽化和反应过程,汽化段与反应段无需管路连接,最大程度降低了热损以避免气体冷凝使得反应器进料时带液。
27.(2)通过填料汽化或者喷雾汽化的方式,有效增加了气液接触面积,解决了原料汽化难、催化剂易结焦失活的问题,从而有效延长了催化剂寿命。
28.(3)整个加氢过程在无溶剂条件下连续化进行,无需增加溶剂脱除单元,节能降耗。
29.(4)全工艺流程简单,经济实用,为碳酸乙烯酯的气固相加氢过程提供了一种工业可行的解决方案。
附图说明
30.图1为实施例1和实施例3的工艺流程示意图;
31.图2为实施例2的工艺流程示意图;
32.图3为对比例1的工艺流程示意图;
33.图中标记说明:
34.1-加氢反应塔,2-进出料交叉换热器,3-产物冷却器,4-气液分离罐,5-循环氢压缩机,6-氢气加热器,7-喷嘴。
具体实施方式
35.下面结合附图和具体实施例对本发明进行详细说明。本实施例以本发明技术方案为前提进行实施,给出了详细的实施方式和具体的操作过程,但本发明的保护范围不限于
下述的实施例。
36.以下各实施方式或实施例中,加氢反应段内还装填有可用于碳酸乙烯酯加氢反应的常规铜基催化剂。其余如无特别说明的原料产品或技术,则也表明均为本领域的常规市售产品或常规处理技术。
37.本发明提出了一种由碳酸乙烯酯生产乙二醇联产甲醇的工艺,其结构参见图1或图2所示,包括以下步骤:
38.(1)氢气原料经预热后得到热氢气,再与碳酸乙烯酯一起送入加氢反应塔1下部的汽化段汽化后,进入加氢反应塔1上部的加氢反应段进行气固相催化加氢反应,得到加氢反应产物:
39.(2)所得加氢反应产物冷却后,送往气液分离罐4中进行气液分离;
40.(3)气液分离罐4顶部所得气相一部分排出,另外一部分作为氢气原料循环利用,气液分离罐4底部即得到乙二醇和甲醇的液相混合产物。
41.在本发明的一种具体的实施方式中,请再参见图1或图2所示,碳酸乙烯酯在汽化段汽化的方式为喷雾汽化或填料汽化。优选的,当采用喷雾汽化时,氢气原料和碳酸乙烯酯采用并流接触方式,当采用填料汽化时,氢气原料和碳酸乙烯酯采用逆流接触方式。
42.更具体的实施方式中,请再参见图2所示,喷雾汽化具体为:在汽化段处设置有一个或多个喷嘴7,碳酸乙烯酯经喷嘴7雾化成雾滴后,与热氢气接触混合,即完成汽化。喷嘴7数量及排布方式由汽化段尺寸及碳酸乙烯酯进料量决定,碳酸乙烯酯液体通过喷嘴7雾化成直径为1~200微米的小液滴后与热氢气充分接触并瞬间汽化,雾化后的碳酸乙烯酯具有较大的表面积,有效增加了气液接触面积,强化了热氢气与碳酸乙烯酯的热传递过程,实现了碳酸乙烯酯的瞬间汽化。
43.更进一步具体的实施方式中,碳酸乙烯酯喷雾形成的雾滴直径为1~200微米。
44.更具体的实施方式中,请再参见图1所示,填料汽化具体为:在汽化段布置有一段或分段串联布置的多段填料层,每段填料层的上方安装有液体分布器,碳酸乙烯酯经液体分布器均匀分布在填料层的填料表面并形成液膜,再与底部通入的热氢气接触混合,即完成汽化。
45.更进一步具体的实施方式中,填料层所用填料为规整填料或者散堆填料。
46.在本发明的一种具体的实施方式中,汽化段的出口位置还安装有丝网除沫器。
47.在本发明的一种具体的实施方式中,加氢反应段的入口温度为170-220℃,反应压力为2-5mpa,氢酯摩尔比(即氢气与碳酸乙烯酯的摩尔比)为150-300:1。更优选的,入口温度为180-200℃,反应压力为2.5-4mpa,氢酯摩尔比为160-210。
48.在本发明的一种具体的实施方式中,步骤(2)中,加氢反应产物进入气液分离罐4前,被冷却(即经产物冷却器3冷却)至25-45℃。
49.在本发明的一种具体的实施方式中,步骤(1)中,氢气原料先与从加氢反应段出来的加氢反应产物换热后(即在进出料交叉换热器2处换热),再被加热(即经氢气加热器6加热)至180-240℃。
50.在本发明的一种具体的实施方式中,步骤(3)中,气液分离罐4顶部排出的气相占顶部所得气相总量的比值为0.01-0.1。
51.在本发明的一种具体的实施方式中,作为氢气原料循环利用的气液分离罐4顶部
气相的摩尔浓度为90%-100%。
52.以上各实施方式可以任一单独实施,也可以任意两两组合或更多的组合实施。
53.下面结合具体实施例来对本发明进行更详细的说明。
54.实施例1:
55.如图1所示,进料量为210nm3/h的新鲜氢s10与进料量为5898nm3/h的循环氢s9混合后,得到氢气原料s11,经进出料交叉换热器2、氢气加热器6两级预热,加热至196℃后作为热氢气s12进入加氢反应塔1底部的气相进料口。进料量为125kg/h的碳酸乙烯酯原料s1进入加氢反应塔1中段的液相进料口,经液体分布器均匀分布于填料表面并形成液膜,与自下而上的热氢气s12逆流接触并汽化,汽化后的混合物进入上部催化剂床层进行加氢反应,反应压力控制在3.0mpa,反应入口温度为183℃,氢酯摩尔比为185。反应结束后的加氢产物s2经进出料交叉换热器2换热得到初步预冷产物s3,再经产物冷却器3冷却至40℃,得到终冷产物s4,进入气液分离罐4,气液分离罐4控制压力为2.9mpa,罐顶得到摩尔组成为95.8%的氢气气相s5,该气相按2%/98%的比例分为两股,其中一股作为驰放气s7外排,另一股氢气流s8经循环氢压缩机5增压至3.1mpa后,与新鲜氢s10混合并升温后,循环回加氢反应塔1入口,罐底得到甲醇和乙二醇的混合物。反应结果如下:碳酸乙烯酯转化率为99.1%,乙二醇选择性为98.7%,甲醇选择性为91.2%,催化剂连续稳定运行500h后活性未见明显下降。
56.实施例2:
57.如图2所示,进料量为1025nm3/h的新鲜氢s10与进料量为8595nm3/h的循环氢s9混合后,经进出料交叉换热器2、氢气加热器6两级预热,加热至180℃后进入加氢反应塔1底部的气相进料口。进料量为125kg/h的碳酸乙烯酯原料s1进入加氢反应塔1底部的液相进料口,碳酸乙烯酯经喷嘴7雾化成微米级小液滴后,与自下而上的热氢气s12并流接触并汽化。汽化后的混合物进入上部催化剂床层进行加氢反应,反应压力控制在2mpa,反应入口温度为170℃,氢酯摩尔比为300。反应结束后的加氢产物s2经进出料交叉换热器2、产物冷却器3冷却至45℃,进入气液分离罐4,气液分离罐4控制压力为1.9mpa,罐顶得到摩尔组成为98.6%的氢气气相s5。该气相按10%/90%的比例分为两股,一股作为驰放气外排,一股经循环氢压缩机5增压至2.1mpa后,与新鲜氢混合并升温后,循环回加氢反应塔1入口,罐底得到甲醇和乙二醇的混合物。反应结果如下:碳酸乙烯酯转化率为95%,乙二醇选择性为99.0%,甲醇选择性为90.7%,催化剂连续稳定运行500h后活性未见明显下降。
58.下述对比例1中,由于采用管道喷雾汽化,雾化后的碳酸乙烯酯小液滴会与管壁接触,重新形成液膜,失去了通过雾化增加气液相接触面积的效果,因此大大影响了汽化效果,而实施例2中在汽化段内汽化,汽化段的壳体直径满足雾化后的碳酸乙烯酯小液滴在整个汽化过程中不与器壁碰撞接触,从而避免在器壁形成液膜,通过雾化有效增加了气液相接触面积,从而使得汽化快速完成,保证了汽化效果,因此,两者的转化率等数据有着明显差异。
59.本实施例中,为了进一步加强汽化段的汽化效果,整个汽化段内还可以设有加强分布混合的内构件,具体可以为在热氢气s12进入加氢反应塔1汽化段的位置处布置气体分布器,使得热氢气在汽化段内以旋流状态向上运动,并与雾化的碳酸乙烯酯雾滴高效混合接触,使得其迅速汽化。
60.实施例3:
61.如图1所示,进料量为144nm3/h的新鲜氢s10与进料量为5056nm3/h的循环氢s9混合后,经进出料交叉换热器2、氢气加热器6两级预热,加热至236℃后进入加氢反应塔1底部气相进料口。进料量为125kg/h的碳酸乙烯酯原料s1进入加氢反应塔1中段液相进料口,经液体分布器均匀分布于填料表面并形成液膜,与自下而上的热氢气逆流接触并汽化,汽化后的混合物进入上部催化剂床层进行加氢反应,反应压力控制在5.0mpa,反应入口温度为220℃,氢酯摩尔比为150。反应结束后的加氢产物经进出料交叉换热器2、产物冷却器3冷却至25℃,进入气液分离罐4,气液分离罐4控制压力为4.9mpa,罐顶得到摩尔组成为90.0%的氢气气相s5。该气相按1%/99%的比例分为两股,一股作为驰放气外排,一股经循环氢压缩机5增压至5.1mpa后,与新鲜氢混合并升温后,循环回加氢反应塔1入口,罐底得到甲醇和乙二醇的混合物。反应结果如下:碳酸乙烯酯转化率为100%,乙二醇选择性为91.1%,甲醇选择性为83.4%,催化剂连续稳定运行500h后活性开始下降。
62.对比例1:
63.如图3所示,进料量为125kg/h的碳酸乙烯酯原料s1经管道内安装的喷嘴7雾化成微米级的小液滴后,与来自氢气加热器6,温度为178℃,进料量为9656nm3/h的循环氢气流s12在管道中混合汽化,汽化后的物料进入加氢反应器底部进料口,在催化剂的作用下进行加氢反应,反应压力控制在2mpa,反应器入口温度为170℃,氢酯摩尔比为300。反应结束后的加氢产物经进出料交叉换热器2、产物冷却器3冷却至45℃,进入气液分离罐4,气液分离罐4控制压力为1.9mpa,罐顶得到摩尔组成为98.5%的循环氢气。该气相按10%/90%的比例分为两股,一股作为驰放气外排,一股经循环氢压缩机5增压至2.1mpa后,与新鲜氢混合并升温后,循环回加氢反应器入口,罐底得到甲醇和乙二醇的混合物。反应结果如下:碳酸乙烯酯转化率为77.5%,乙二醇选择性为94.8%,甲醇选择性为86.1%,装置连续运行72h后,催化剂开始逐渐结焦失活。
64.通过实施例与对比例中的数据比较可以得出,当采用简单的管道喷雾汽化时,碳酸乙烯酯转化率大幅下降,催化剂在连续运行72h后逐渐结焦失活,分析其原因为该条件下,雾化后的碳酸乙烯酯小液滴与管壁碰撞接触,重新形成液膜,从而使得碳酸乙烯酯未能充分汽化,未汽化的碳酸乙烯酯进入反应器中导致催化剂床层局部带液,影响了催化剂活性及寿命。为达到与实施例相同的反应效果,在对比例1的工艺流程基础上,继续增加循环氢用量,当氢酯比上升至600时,反应效果仍无明显改善,但此时循环圈负荷已增加至实施例2中的2倍左右,循环圈负荷的增加意味着投资与能耗的增加,对实际的工业化生产装置是不利的。
65.由上可知,采用本发明的方法,通过在加氢反应器中增设汽化段,采用填料汽化或者喷雾汽化的方式,可有效解决实际生产中原料碳酸乙烯酯汽化难的问题,保证汽化效果,延长催化剂寿命,全工艺流程简单,经济实用,为碳酸乙烯酯的气固相加氢过程提供了一种工业可行的解决方案。
66.上述的对实施例的描述是为便于该技术领域的普通技术人员能理解和使用发明。熟悉本领域技术的人员显然可以容易地对这些实施例做出各种修改,并把在此说明的一般原理应用到其他实施例中而不必经过创造性的劳动。因此,本发明不限于上述实施例,本领域技术人员根据本发明的揭示,不脱离本发明范畴所做出的改进和修改都应该在本发明的保护范围之内。