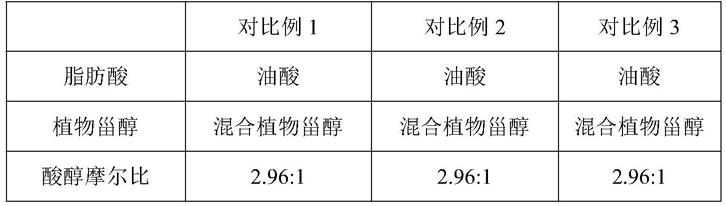
1.本发明属于植物甾醇酯合成技术领域,具体涉及到一种植物甾醇酯的制备方法。
背景技术:2.植物甾醇作为一种常见的生物活性化合物,在蔬菜、谷物和豆类中广泛存在。多数研究证明发现,植物甾醇可以抑制人和动物肠道内的胆固醇吸收,从而有效降低血液中总胆固醇(tc)和低密度胆固醇(ldl
‑
c)浓度。此外,植物甾醇还具有多种健康益处,包括抗炎、抗氧化、神经保护等。但是,通常以结晶粉末状形式存在的植物甾醇具有低油溶性和高熔点的特征,这限制了它们在疏水性基质中的应用。目前,将植物甾醇与脂肪酸酯化制备植物甾醇酯是改善植物甾醇油溶性的重要手段。
3.植物甾醇酯的制备主要通过化学法和酶法进行。其中,酶法反应条件温和,特异性强,最终所得产品的副产物少,但由于酶的高成本限制了其在工业化生产中的广泛应用,因此化学催化仍然是当前工业生产的主要方法。酸性催化剂,包括均相酸和非均相酸,通常用于植物甾醇酯的化学催化中,然而,一些酸性催化剂催化的酯化反应往往需要苛刻的反应温度(通常为130~180℃),在高温反应过程中很容易导致不饱和脂肪酸的氧化以及植物甾醇的脱水等副反应,同时也耗费了大量能量。此外,在反应过程中还需要及时除去产生的水分,以推动反应的正向进行。
4.目前,在植物甾醇酯的生产过程中多使用常规加热的方法,其本身的热传递效率较低,因此在反应过程中通常需要更长的反应时间和更高的能量需求。由于常规加热本身存在一定的传输损耗,与实际供应的能量相比,净能量的利用率也较低。
5.现有技术中,通过采用温和的本发明特定催化剂辅助微波辐射高效合成植物甾醇酯尚未见报道。
技术实现要素:6.本部分的目的在于概述本发明的实施例的一些方面以及简要介绍一些较佳实施例。在本部分以及本技术的说明书摘要和发明名称中可能会做些简化或省略以避免使本部分、说明书摘要和发明名称的目的模糊,而这种简化或省略不能用于限制本发明的范围。
7.鉴于上述和/或现有技术中存在的问题,提出了本发明。
8.因此,本发明的目的是,克服现有技术中的不足,提供一种植物甾醇酯的制备方法。
9.为解决上述技术问题,本发明提供了如下技术方案:一种植物甾醇酯的制备方法,包括,将植物甾醇、脂肪酸、催化剂加入到反应容器中,置于微波反应器中进行酯化反应,将反应液经分离纯化得到脂肪酸植物甾醇酯。
10.作为本发明所述植物甾醇酯制备方法的一种优选方案,其中:所述植物甾醇包括豆甾醇、β
‑
谷甾醇、菜籽甾醇、菜油甾醇中的一种或多种。
11.作为本发明所述植物甾醇酯制备方法的一种优选方案,其中:所述脂肪酸为c6~
c
20
的饱和脂肪酸或不饱和脂肪酸中的一种或多种。
12.作为本发明所述植物甾醇酯制备方法的一种优选方案,其中:所述脂肪酸包括油酸、亚油酸、亚麻酸、大豆脂肪酸、葵花籽油脂肪酸中的一种或多种。
13.作为本发明所述植物甾醇酯制备方法的一种优选方案,其中:所述脂肪酸与植物甾醇的投料量摩尔比为1:1~5:1。
14.作为本发明所述植物甾醇酯制备方法的一种优选方案,其中:所述脂肪酸与植物甾醇的投料量摩尔比为2:1~3:1。
15.作为本发明所述植物甾醇酯制备方法的一种优选方案,其中:所述催化剂包括十二烷基苯磺酸和十二烷基苯磺酸盐。
16.作为本发明所述植物甾醇酯制备方法的一种优选方案,其中:所述催化剂用量为植物甾醇质量的8%~12%。
17.作为本发明所述植物甾醇酯制备方法的一种优选方案,其中:所述微波反应器的微波功率为300~500w/500g反应物,所述微波辐照反应温度为30~80℃,所述微波辐照酯化反应的时间为20~80min。
18.作为本发明所述植物甾醇酯制备方法的一种优选方案,其中:所述分离纯化,包括,用100~200目活化硅胶装柱,随后将植物甾醇酯混合物用环己烷、无水乙醚、乙酸混合溶剂进行洗脱,收集洗脱液,减压下旋转蒸发得到植物甾醇酯;
19.其中,环己烷、无水乙醚、乙酸混合溶剂中环己烷、无水乙醚、乙酸的体积比为15:1:0.1。
20.本发明有益效果:
21.(1)本发明首次提出将微波与本发明特定催化剂结合制备植物甾醇酯,其中本发明特定催化剂在反应过程中形成的油包水型(w/o)微乳液,酯化反应产生的水分会自动进入水相,微波辐射作用可以快速促进微乳液中液滴的成核,同时可以有效降低液滴聚集的几率,因此与常规加热方式相比,微波可以使形成的水相粒径分布均一,从而可以在反应界面处有效聚集催化物质,两者协同作用,更高效地催化酯化反应。
22.(2)本发明通过微波辅助方法合成植物甾醇酯,反应速率快,反应时间短,所用催化剂反应条件温和,避免了一般化学催化过程中温度过高造成的不饱和脂肪酸的氧化以及植物甾醇的脱水反应,其中在反应过程中形成的本发明特定体系可以将水与疏水体系自动分离,避免了逆反应水解,因此无需使用额外的除水操作或设备,简化了生产工艺,降低了成本。
附图说明
23.为了更清楚地说明本发明实施例的技术方案,下面将对实施例描述中所需要使用的附图作简单地介绍,显而易见地,下面描述中的附图仅仅是本发明的一些实施例,对于本领域普通技术人员来讲,在不付出创造性劳动性的前提下,还可以根据这些附图获得其它的附图。其中:
24.图1为本发明实施例3中反应结束后反应粗产物的高效液相色谱图。
具体实施方式
25.为使本发明的上述目的、特征和优点能够更加明显易懂,下面结合说明书实施例对本发明的具体实施方式做详细的说明。
26.在下面的描述中阐述了很多具体细节以便于充分理解本发明,但是本发明还可以采用其他不同于在此描述的其它方式来实施,本领域技术人员可以在不违背本发明内涵的情况下做类似推广,因此本发明不受下面公开的具体实施例的限制。
27.其次,此处所称的“一个实施例”或“实施例”是指可包含于本发明至少一个实现方式中的特定特征、结构或特性。在本说明书中不同地方出现的“在一个实施例中”并非均指同一个实施例,也不是单独的或选择性的与其他实施例互相排斥的实施例。
28.本发明中微波专用反应容器为mcr
‑
3型微波反应器,微波频率为2450mhz,微波功率为0~800w连续自动可调,控温范围为0~250℃。
29.本发明中酯化率的测定方法:使用高效液相色谱(hplc)进行酯化率分析测定。首先配置系列不同浓度的植物甾醇酯溶液,进样后根据峰面积与浓度的关系制作标准曲线。将过膜后的混合液进样,根据峰面积计算出反应液中所含植物甾醇酯的浓度,再按照以下公式即可计算出酯化率。
30.酯化率(%)=植物甾醇酯的摩尔浓度/植物甾醇的初始摩尔浓度
×
100
31.hplc条件:lichrospher si液相色谱柱(250mm
×
4.6mm
×
5μm);流动相:正己烷:异丙醇:甲酸为15:1:0.003(v/v/v);采用等度洗脱,流速为1.0ml/min;柱温:30℃;进样量:20μl。
32.实施例1
33.将油酸、植物甾醇(油酸与植物甾醇摩尔比为2.96:1)加入微波专用反应容器中,反应物总质量500g,加入植物甾醇质量8%的催化剂十二烷基苯磺酸,将反应容器置于微波反应器中,微波功率为300w,控制反应温度为60℃条件下进行酯化反应40min。
34.反应结束后得到植物甾醇酯粗产品,通过硅胶柱层析法分离纯化得到植物甾醇酯产品;其中,硅胶柱色谱条件为:流动相为环己烷/无水乙醚/乙酸(15:1:0.1,v/v/v),柱填充高度40cm,洗脱液收集速度10min/管,并用tlc检测分离产物,将收集得到的产物合并旋蒸得到植物甾醇酯。
35.实施例2
36.将亚油酸、植物甾醇(亚油酸与植物甾醇摩尔比为2.03:1)加入微波专用反应容器中,反应物总质量约500g,加入植物甾醇质量12%的催化剂十二烷基苯磺酸,将反应容器置于微波反应器中,微波功率为400w,控制温度为70℃条件下进行酯化反应30min。
37.反应结束后得到植物甾醇酯粗产品,通过硅胶柱层析法分离纯化得到植物甾醇酯产品;其中,硅胶柱色谱条件为:流动相为环己烷/无水乙醚/乙酸(15:1:0.1,v/v/v),柱填充高度40cm,洗脱液收集速度10min/管,并用tlc检测分离产物,将收集得到的产物合并旋蒸得到植物甾醇酯。
38.实施例3
39.将α
‑
亚麻酸、植物甾醇(α
‑
亚麻酸与植物甾醇摩尔比为2.52:1)加入微波专用反应容器中,反应物总质量约500g,加入植物甾醇质量10%的催化剂十二烷基苯磺酸,将反应容器置于微波反应器中,微波功率为400w,控制温度为60℃条件下进行酯化反应40min。
40.反应结束后得到植物甾醇酯粗产品,通过硅胶柱层析法分离纯化得到植物甾醇酯产品;其中,硅胶柱色谱条件为:流动相为环己烷/无水乙醚/乙酸(15:1:0.1,v/v/v),柱填充高度40cm,洗脱液收集速度10min/管,并用tlc检测分离产物,将收集得到的产物合并旋蒸得到植物甾醇酯。
41.实施例4
42.将大豆脂肪酸、植物甾醇(大豆脂肪酸与植物甾醇摩尔比为2.96:1)加入微波专用反应容器中,反应物总质量约500g,加入植物甾醇质量8%的催化剂十二烷基苯磺酸,将反应容器置于微波反应器中,微波功率为300w,控制温度为50℃条件下进行酯化反应50min。
43.反应结束后得到植物甾醇酯粗产品,通过硅胶柱层析法分离纯化得到植物甾醇酯产品;其中,硅胶柱色谱条件为:流动相为环己烷/无水乙醚/乙酸(15:1:0.1,v/v/v),柱填充高度40cm,洗脱液收集速度10min/管,并用tlc检测分离产物,将收集得到的产物合并旋蒸得到植物甾醇酯。
44.实施例1~4的反应条件和酯化率结果见表1。
45.表1
[0046] 实施例1实施例2实施例3实施例4脂肪酸油酸亚油酸α
‑
亚麻酸大豆脂肪酸植物甾醇混合植物甾醇混合植物甾醇混合植物甾醇混合植物甾醇酸醇摩尔比2.96:12.03:12.52:12.96:1催化剂用量8%12%10%8%微波功率300w400w400w300w反应温度60℃70℃60℃50℃反应时间40min30min40min50min酯化率93.67%92.38%95.49%91.51%
[0047]
从表1可以看出,通过微波辅助本发明特定催化剂合成植物甾醇酯的酯化效率高,反应条件温和,且反应速率快,解决了一般化学法合成中反应温度高、反应时间长的问题。
[0048]
对比例1
[0049]
将油酸、植物甾醇(油酸与植物甾醇摩尔比为2.96:1)加入到配有搅拌、水浴控温的反应容器中,反应物总质量约500g,加入植物甾醇质量8%的催化剂十二烷基苯磺酸,置于水浴锅中进行酯化反应10h,反应温度为60℃。
[0050]
反应结束后得到植物甾醇酯粗产品,通过硅胶柱层析法分离纯化得到植物甾醇酯产品;其中,硅胶柱色谱条件为:流动相为环己烷/无水乙醚/乙酸(15:1:0.1,v/v/v),柱填充高度40cm,洗脱液收集速度10min/管,并用tlc检测分离产物,将收集得到的产物合并旋蒸得到植物甾醇酯。
[0051]
对比例2
[0052]
将油酸、植物甾醇(油酸与植物甾醇摩尔比为2.96:1)加入微波专用反应容器中,反应物总质量约500g,置于微波反应器中,微波功率为300w,控制反应温度为180℃条件下进行酯化反应50min。
[0053]
反应结束后得到植物甾醇酯粗产品,通过硅胶柱层析法分离纯化得到植物甾醇酯产品;其中,硅胶柱色谱条件为:流动相为环己烷/无水乙醚/乙酸(15:1:0.1,v/v/v),柱填
充高度40cm,洗脱液收集速度10min/管,并用tlc检测分离产物,将收集得到的产物合并旋蒸得到植物甾醇酯。
[0054]
对比例3
[0055]
将油酸、植物甾醇(油酸与植物甾醇摩尔比为2.96:1)加入微波专用反应容器中,反应物总质量约500g,加入植物甾醇质量8%的催化剂硫酸氢钠,将反应容器置于微波反应器中,微波功率为300w,控制温度为60℃条件下进行酯化反应40min。
[0056]
反应结束后得到植物甾醇酯粗产品,通过硅胶柱层析法分离纯化得到植物甾醇酯产品;其中,硅胶柱色谱条件为:流动相为环己烷/无水乙醚/乙酸(15:1:0.1,v/v/v),柱填充高度40cm,洗脱液收集速度10min/管,并用tlc检测分离产物,将收集得到的产物合并旋蒸得到植物甾醇酯。
[0057]
对比例1~3的反应条件和酯化率结果见表2。
[0058]
表2
[0059][0060][0061]
从表2可以看出,采用常规加热方式合成植物甾醇酯所需的反应时间较长,至少需要10h的反应时间才可以达到90%以上的酯化率;在无催化剂条件下仅使用微波辐照合成植物甾醇酯所需的反应温度较高,当反应温度为180℃、反应时间50min时可以达到90%以上的酯化率;而当微波辅助其他非本发明特定催化剂,如典型的酸性催化剂如硫酸氢钠时,在反应条件同实施例1的情况下酯化率仅为15.28%。
[0062]
对比例4
[0063]
参考实施例1,改变反应条件,其余步骤不变,测定植物甾醇酯酯化率,结果见表3。
[0064]
表3
[0065] 实施例1试验1试验2试验3试验4脂肪酸油酸油酸油酸油酸油酸植物甾醇混合植物甾醇混合植物甾醇混合植物甾醇混合植物甾醇混合植物甾醇酸醇摩尔比2.96:11.02:12.96:12.96:12.96:1催化剂用量8%8%4%8%8%
微波功率300w300w300w100w300w反应温度60℃60℃60℃60℃40℃反应时间40min40min40min40min40min酯化率94.67%83.04%72.49%86.23%69.56%
[0066]
从表3可以看出,酸醇摩尔比过低、催化剂用量过少、微波功率过低或反应温度低的情况下,植物甾醇酯的酯化率均较低。原因可能是酸醇摩尔比过低的情况下不能推动反应的正向进行;催化剂用量少时不能有效形成本发明特定体系,从而不能有效催化酯化反应;微波功率较低时不能促进反应体系中分子的快速耦合,且在低微波功率下形成的油包水型微乳液粒径分布不均,从而不能在反应界面处有效聚集催化物质。
[0067]
对比例5
[0068]
参考实施例1,改变反应条件,其余步骤不变,测定植物甾醇酯酯化率,结果见表4。
[0069]
表4
[0070] 实施例1试验5试验6试验7试验8脂肪酸油酸油酸油酸油酸油酸植物甾醇混合植物甾醇混合植物甾醇混合植物甾醇混合植物甾醇混合植物甾醇酸醇摩尔比2.96:14:15:12.96:12.96:1催化剂用量8%8%8%12%14%微波功率300w300w300w300w300w反应温度60℃60℃60℃60℃60℃反应时间40min40min40min40min40min酯化率94.67%92.13%90.56%95.53%95.89%
[0071]
从表4可以看出,当酸醇摩尔比例过大时,植物甾醇的酯化效率会有一定的降低,原因可能是过量的酸会稀释植物甾醇和催化剂在反应体系中的浓度,从而导致催化效果降低。当催化剂过量时,酯化效率并无明显上升,然而反应体系的颜色会明显加深,这增加了后续分离纯化的难度。
[0072]
因此,根据以上实验结果,从保证催化效果和节约生产成本考虑,本发明优选的工艺参数为:酸醇摩尔比为2.52:1,催化剂用量10%,微波功率400w,反应温度60℃,反应时间40min,植物甾醇酯酯化率达到95.49%。
[0073]
对比例6
[0074]
参考实施例1,改变反应条件,其余步骤不变,测定植物甾醇酯酯化率,结果见表5。
[0075]
表5
[0076]
[0077][0078]
从表5可以看出,当选用其他本发明特定催化剂进行酯化反应时,酯化效果不佳,原因可能是不同的催化剂反应所需的最佳反应温度不同,在该反应温度条件下不能充分发挥该催化剂的催化活性,需要进一步升高反应温度来提高催化效果,然而过高的反应温度将会产品品质造成不利影响,同时也增大了反应的能耗。
[0079]
本发明催化剂在反应过程中形成的油包水型(w/o)微乳液,酯化反应产生的水分会自动进入水相,微波辐射作用可以快速促进微乳液中液滴的成核,缩短粒子的成核时间,减小“二次成核”几率,同时也减小了液滴聚集的几率,因此与常规加热方式相比,微波可以使形成的水相粒径分布均一,从而可以在反应界面处聚集催化物质,更有效地催化酯化反应。当非本发明特定体系下时,其催化效果不佳,导致酯化率降低。
[0080]
因此,本发明体系与微波技术相结合合成植物甾醇酯,在植物甾醇酯制备工业化应用中是非常有意义的集成技术。
[0081]
应说明的是,以上实施例仅用以说明本发明的技术方案而非限制,尽管参照较佳实施例对本发明进行了详细说明,本领域的普通技术人员应当理解,可以对本发明的技术方案进行修改或者等同替换,而不脱离本发明技术方案的精神和范围,其均应涵盖在本发明的权利要求范围当中。