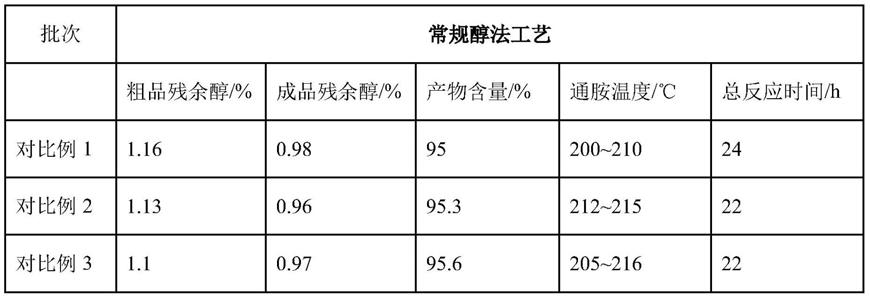
1.本发明属于有机合成技术领域,具体涉及一种低残余醇单烷基脂肪叔胺的制备方法。
背景技术:2.脂肪叔胺是单烷基脂肪叔胺、双烷基脂肪叔胺和三烷基脂肪叔胺的总称,其中单烷基脂肪叔胺需求最大,全球需求大于20万吨,国外生产叔胺公司主要为花王和eastman。中国是需求大国,年需求增长率在5%左右。主要用于工业杀菌剂、稀土金属萃取剂、农药绿色溶剂、催化剂、特种阳离子表面活性剂等领域,特别是民用洗涤济、杀菌剂的需求提升。随着人们生活水平提高以及安全、卫生意识加强,全球洗手液、杀菌剂和抑菌剂个人护理产品需求迅速增长,从而使脂肪叔胺系列产品需求增加明显,并且对品质要求明显提升。原来残余脂肪醇控制要求小于1%,残余醇的浓度为1%左右时,往下游做季铵盐时,发现产品有发浑的现象,严重影响外观,通过研究发现是叔胺中残余的脂肪醇导致的,因此需要进一步降低残余醇的含量。
3.脂肪胺合成方法主要有:脂肪酸和脂肪醇胺化法、卤代烷胺解法、烯烃胺化法等。
4.目前工业上的生产大多数是以天然或合成的脂肪酸、脂肪醇为原料进行生产,原料来源方便,生产过程中的腐蚀较小,反应转化率高,副反应少,反应产物经分馏纯化,适用于工业上大规模的制备。
5.卤代烃与胺的反应是脂肪胺的传统合成方法,卤代烷与氨水或氨乙醇溶液作用,生成伯胺的盐,和氨形成平衡,得到脂肪胺。该法生成的脂肪胺可以和卤代烷继续反应,生成仲胺、叔胺及季铵盐的混合物,该法合成工艺简单,易于工业化,缺点是产品纯度不高。
6.烯烃胺解法在工业上有非常好的前景,在热力学上该反应是有利的,但是如果缺少适当的催化剂,反应速度很慢,选择性也比较差。而且烯烃胺化制备脂肪胺,易受到烯烃质量的影响,产物难以分离,增加生产成本。
技术实现要素:7.为解决上述问题,本发明的目的在于提供一种低残余醇单烷基脂肪叔胺的制备方法。
8.为达到上述目的,提出以下技术方案:
9.一种低残余醇单烷基脂肪叔胺的制备方法,包括如下步骤:
10.1)将脂肪醇和铜镍催化剂放到胺化釜中,分别用氮气和氢气置换,然后充氢气至0.1mpa,开启氨气循环压缩机,升温到160~200℃,使催化剂还原1小时;
11.2)分段升温,分段通入二甲胺,进行胺化反应,循环气通过一级冷凝器降温到120~140℃,未反应的醇和叔胺回流至胺化釜中,未冷凝的成分通过二级冷凝器冷却到一定温度后进入油水分离器进行分离;
12.3)油水分离后,上层油层回流至胺化釜,下层水层收集回收至胺回收釜中进行再
利用;
13.4)当胺化釜中的压力不下降时取样分析残余醇的含量,含量小于0.3%合格,否则适当延长保温时间,出料,得到粗品;
14.5)出料粗品经过过滤器过滤后去除催化剂,进入精馏釜,由于产品和原料脂肪醇沸点接近,如果不采取任何措施,很难通过精馏保证产品残余脂肪醇《0.1%,粗品精馏时加入少量有机酸,其和残余的微量脂肪醇反应成高沸点的酯,精馏时与产品可以很好的分离,得到纯度更高的单烷基脂肪叔胺产品。
15.在高温条件下,循环气中含有脂肪醇、叔胺、二甲胺、氢气和生成水,一级冷凝到水的沸点以上的温度,此时循环气中的脂肪醇和叔胺成分被冷却回流,而水未被冷却成液态,经过二级冷凝后,水被冷凝成液态,进入油水分离器进行分离,经过油水分离器,少量脂肪醇和叔胺回流至胺化釜中,而水层进入胺回收釜回收。
16.进一步地,步骤2)中的分段升温,分段通入二甲胺的具体操作过程为升温至200~220℃,并维持4~5小时,同时通入质量总量的80%的二甲胺进行胺化反应,然后继续升温至230~240℃,维持2小时,同时通入剩余的20%的二甲胺,继续进行胺化反应;前期催化剂活性号,醇浓度较高,反应迅速,后期催化剂活性下降,且醇浓度下降,提高胺化温度,进一步降低醇,加速反应进行。
17.进一步地,二甲胺和脂肪醇的用量摩尔比为1~1.2:1,优选为1.03~1.1:1,二甲胺的用量稍多于脂肪醇的用量,使反应完全。
18.进一步地,步骤2)中未冷凝的成分通过二级冷凝器冷却到30~50℃后进入油水分离器进行分离。
19.进一步地,步骤3)中水层进入胺回收釜,胺回收釜连有胺回收塔,胺回收釜用蒸汽加热回收生成水中溶解的胺,直至胺回收塔顶温》90℃,视作二甲胺回收毕;水层中还含有少量的二甲胺,二甲胺的沸点是6.1℃,由于二甲胺和水的沸点相差加大,观察检测胺回收塔顶温,当顶温超过90℃,确定为二甲胺基本回收完毕,降低废水中的二甲胺含量,同时回收的二甲胺可以回流至胺化釜中使用。
20.进一步地,步骤6)中加入的酸为磷酸、癸酸、硼酸、辛酸中的一种或俩种混合物,加入量和残余脂肪醇的摩尔比为0.5~2,优选0.8~1.2。
21.进一步地,单烷基脂肪叔胺的结构式为如式(ⅰ)所示化合物
[0022][0023]
其中r为c8h
17
、c
10h21
、c
12h25
、c
14h29
、c
16h33
、c
18h37
、c
20h21
或c
24h49
。
[0024]
反应方程式:
[0025][0026]
除醇反应方程式(以硼酸为例)
[0027][0028]
精馏时以酸和残余醇酯化反应,生成高沸点的酯,除去微量脂肪醇,确保脂肪醇可以降低到0.1%以下。
[0029]
本发明的有益效果在于:
[0030]
1)采用多级冷凝的方式,分段对醇和脂肪胺以及水进行降温,使醇和叔胺与水分离,醇和叔胺以热态(120~140℃)回流进行反应,而水进行回收收集,相对于直接一级冷却至低温,不仅降低了能耗,还减少物料以冷态形式回至胺化塔中,物料以冷态形式回到胺化塔对移除上升的气态生成水是不利的,通过多级冷凝可以使反应更加快速,完全;
[0031]
2)采用胺回收釜对水层中的水进行收集,然后进行二甲胺的回收,降低二甲胺的单耗,实现物料的循环;
[0032]
3)通过本发明的方法,有效降低了产品中残余醇的含量,粗品中残余醇含量小于0.3%,成品中残余醇含量小于0.1%。
附图说明
[0033]
图1为本发明的工艺流程示意图;
[0034]
图2为常规醇法工艺流程示意图。
具体实施方式
[0035]
下面结合实施例对本发明做进一步地说明,但本发明的保护范围并不仅限于此。
[0036]
实施例1
[0037]
将10000kgc12/14醇(c12醇:75%,c14醇:25%)和100kg的铜镍催化剂投入胺化釜,氮气,氢气置换后,充氢气至0.1mpa,开启胺循环泵,升温到180~190℃,保持温度1h,开启冷凝器循环水自动调节阀,一级冷凝器温度控制在120~125℃,二级冷凝器温度控制在35~40℃,然后胺化釜升温到200~210℃,4~5h内通完2000kg二甲胺,然后胺化釜升温到230~240℃,2小时内通500kg二甲胺,进行胺化反应,油水分离器中下层水也去胺回收釜,分水毕后,打开胺回收釜阀门,同时胺回收釜升温,控制回收塔顶温温度小于90℃,超过90℃则二甲胺回收完成,胺回收完成的生成水去污水处理,胺化釜再保温1h左右,待压力不下降,取样gc分析,含量97.9%,残余醇0.27%。
[0038]
粗品经过过滤掉催化剂去精馏釜,同时加入6kg硼酸,按照正常工艺精馏,得到11029kg成品,含量98.2%,残余醇0.07%,收率96.8%。
[0039]
实施例2:
[0040]
将10000kgc16醇(99.2%)和80kg的铜镍催化剂投入胺化釜,氮气,氢气置换后,充氢气至0.1mpa,开启胺循环泵,升温到190~200℃,保持温度1h,开启冷凝器循环水自动调节阀,一级冷凝器温度控制在130~135℃,二级冷凝器温度控制在40~50℃,然后升温到200~210℃,4~5h内通完1532kg二甲胺,然后升温到230~240℃,2小时内通383kg二甲胺,油水分离器中下层水也去胺回收釜,分水毕后,打开胺回收釜的阀门,同时胺回收釜升温,控制回收塔顶温温度小于90℃,超过90℃则二甲胺回收毕,胺回收毕的生成水去污水处理,胺化釜再保温1h左右,待压力不下降,取样gc分析,含量98.1%,残余醇0.25%。
[0041]
粗品经过过滤掉催化剂去精馏釜,同时加入26kg癸酸,按照正常工艺精馏,得到10782kg成品,含量98.9%,残余醇0.09%,收率97%。
[0042]
实施例3:
[0043]
将10000kgc18/16醇(c18醇:75%,c16醇:25%)和80kg的铜镍催化剂投入胺化釜,氮气,氢气置换后,充氢气至0.1mpa,开启胺循环泵,升温到190~200℃,保持温度1h,开启冷凝器循环水自动调节阀,一级冷凝器温度控制在135~140℃,二级冷凝器温度控制在30~40℃,然后升温到200~210℃,4~5h内通完1434kg二甲胺,然后升温到230~240℃,2小时内通359kg二甲胺,油水分离器中下层水也去胺回收釜,分水毕后,打开胺回收釜去胺化釜的阀门,同时胺回收釜升温,控制回收塔顶温温度小于90℃,超过90℃则二甲胺回收毕,胺回收毕的生成水去污水处理,胺化釜再保温1h左右,待压力不下降,取样gc分析,含量97.6%,残余醇0.22%。
[0044]
粗品经过过滤掉催化剂去精馏釜,同时加入8kg硼酸,按照正常工艺精馏,得到10815kg成品,含量98.5%,残余醇0.07%,收率98.1%。
[0045]
实施例4-13
[0046]
改变分段通胺的温度,其它操作过程和操作参数与实施例1相同,操作的流程同图1,得到的结果如表2所示。
[0047]
对比例1
[0048]
如图2所示,常规醇法工艺的具体实施方法为,将10000kgc18/16醇(c18醇:75%,c16醇:25%)和80kg的铜镍催化剂投入胺化釜,氮气,氢气置换后,充氢气至0.1mpa,开启氨循环泵,加热,开启冷凝器冷却水,冷凝器控制在30~40℃,然后升温到200~210℃,并通入二甲胺进行反应,经过一凝器冷凝后的物料经过水油分离,醇和叔胺回流至胺化釜中继续参加反应,粗品的残余醇含量为1.16%,粗品经过过滤送入精馏釜中,成品的残余醇含量为0.98%,含量为95%。
[0049]
对比例2-10
[0050]
改变通胺的温度,其他操作过程和操作参数与对比例1相同,操作的流程同图2,得到的结果如表1所示。
[0051]
表1常规醇法工艺制备得到的脂肪叔胺的醇残余对比
[0052]
[0053][0054]
表2实施例的工艺制备得到的脂肪叔胺的醇残余对比
[0055][0056]
对比表1和表2发现,相比于常规法,采用本发明的制备方法,产物脂肪叔胺的纯度得到提高,醇的残余量明显降低,成品醇残余量小于0.1%,同时本发明的方法,提高了反应速率,单批总的反应时间小于常规法的反应时间,大大提高的生产效率和产能。
[0057]
结论:在高温下,循环气中含有脂肪醇、叔胺、二甲胺、氢气和生成水,常规方法采用一级冷凝法,由于冷却量大,冷却器面积需要很大,同时水,脂肪醇和叔胺都被冷却到30
~50℃,通过油水分离器,上层未反应的脂肪醇和叔胺回至胺化塔,大流量的冷料(30~50℃)回流,碰到上升的气流(含水,醇,叔胺),会有部分被冷却回到釜中,既增加了能耗,又不利于汽化生成水带出反应体系,其回到釜中后会使铜镍催化剂部分失活,导致反应变慢,生产效率下降,并且催化剂单耗会增加,精馏时加入有机酸,可以使产品残余脂肪醇进一步降低(《0.1%),满足下游高端生产的需求。