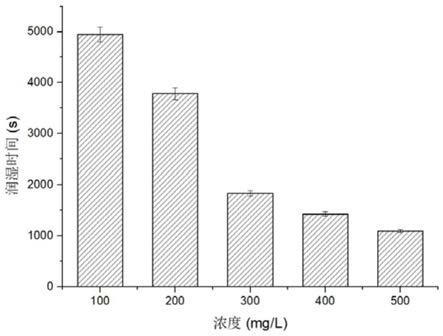
1.本发明属于金属铸造技术领域,具体涉及一种表面改性剂及其在制备硅基复合功能涂层材料中的用途。
背景技术:2.我国对涂料的研究相对落后,虽然有相关研究人员分别对不同类型精密铸造涂层材料系统进行了一定程度研究,但很多在使用中存在存储运输、使用性能差、剥离性能差等缺点;目前也有相关研究人员分别对不同类型精密铸造硅基复合功能涂层材料系统进行了研究,但真正满足精密铸造硅基复合功能涂层材料,国内尚为空白,以至于急需的精密铸造硅基复合功能涂层的关键材料还不得不依赖进口,价格昂贵且国内部分军用产品精密铸造用功能涂层材料常因为军事用途而断货。尽管在前期硅基复合功能涂层配方、有机均匀分散稳定悬浮浆料制备工艺,以及与功能添加调控的大量研究与探索,并取得良好结果的基础,但目前复合功能涂层材料仍存在一些不足。
技术实现要素:3.本发明的目的在于提供一种润湿性能好、乳化性能好、可用于金属涂层材料的表面改性剂的制备方法。
4.本发明为实现上述目的所采取的技术方案为:
5.一种表面改性剂的制备方法,包括:
6.将八甲基环四硅氧烷、聚甲基氢硅氧烷、六甲基二硅醚在浓酸作用下制备得到含氢硅氧烷,浓酸为浓硫酸;
7.将烯丙基缩水甘油醚与n-(3-羟丙基)酞亚胺在碱的作用下制备得到烯丙基化合物,碱为氢氧化钠或氢氧化钾;
8.含氢硅氧烷、烯丙基化合物于溶剂中在催化剂作用下制备得到表面改性剂。本发明通过上述方法在含氢硅氧烷分子链上连接烯丙基化合物,制备得到表面活性剂,将上述表面活性剂与水混合后,具有好的润湿性能,相比于含氢硅氧烷,润湿性能大大提高,将上述表面活性剂与液体石蜡混合形成乳液后,具有优异的乳化性能,将上述表面活性剂用于制备得到硅基复合功能涂层浆料后,硅基复合功能涂层浆料的抗滴淌性能好,硅基复合功能涂层浆料固化后的强度提高。
9.优选地,催化剂为卡斯泰德催化剂。
10.优选地,溶剂为异丙醇。
11.优选地,聚甲基氢硅氧烷的使用量为八甲基环四硅氧烷的50-70wt%。
12.优选地,烯丙基缩水甘油醚的使用量为n-(3-羟丙基)酞亚胺的40-60wt%。
13.优选地,含氢硅氧烷的制备中,将八甲基环四硅氧烷、聚甲基氢硅氧烷、六甲基二硅醚混合,在氮气氛围下在温度40-50℃的条件下,加入浓硫酸,搅拌反应24-96h,反应完成后,调节ph至中性,在80-90℃的温度下处理3-9h,然后冷却至室温,抽滤除去杂质,得到含
氢硅氧烷。
14.更优选地,聚甲基氢硅氧烷的使用量为八甲基环四硅氧烷的50-70wt%。
15.更优选地,六甲基二硅醚的添加量为八甲基环四硅氧烷的6-12wt%。
16.更优选地,浓硫酸的添加量为八甲基环四硅氧烷的1.5-3wt%。
17.优选地,烯丙基化合物的制备中,将烯丙基缩水甘油醚与n-(3-羟丙基)酞亚胺混合,在氮气保护下,加入氢氧化钠,在温度90-95℃的温度下搅拌反应2-6h,反应完成后,室温下真空蒸馏除去水和低沸点物,得到烯丙基化合物。
18.更优选地,烯丙基缩水甘油醚的使用量为n-(3-羟丙基)酞亚胺的40-60wt%。
19.更优选地,氢氧化钠的使用量为烯丙基缩水甘油醚的1.3-1.9wt%。
20.优选地,表面改性剂的制备:在80-90℃的温度下,将卡斯泰德催化剂、含氢硅氧烷、烯丙基化合物加入异丙醇中,反应2-9h,反应完成后蒸馏除去溶剂异丙醇,得到改性有机硅烷表面活性剂。
21.更优选地,卡斯泰德催化剂的使用量为含氢硅氧烷的0.006-0.03wt%。
22.更优选地,含氢硅氧烷的使用量为异丙醇的15-30wt%。
23.更优选地,烯丙基化合物的使用量为异丙醇的20-40wt%。
24.本发明公开了上述方法制备得到的表面改性剂。
25.本发明的目的在于提供一种干燥后强度好、抗滴淌性能好的硅基复合功能涂层浆料。
26.本发明为实现上述目的所采取的技术方案为:
27.一种硅基复合功能涂层浆料,包括:含有上述的表面改性剂。
28.优选地,浆料中含有填料、粘结剂、溶剂。
29.优选地,硅基复合功能涂层浆料的成分:填料、粘结剂、功能剂、溶剂。
30.优选地,填料中至少含有sio2,还可含有y2o3。
31.优选地,粘结剂为醋酸锆、水玻璃中至少一种。
32.优选地,功能剂为kh602、表面改性剂中至少一种。
33.优选地,溶剂为水和乙醇中任一种或混合。
34.优选地,硅基复合功能涂层浆料的配制中,将填料和粘结剂加入溶剂中,搅拌混合均匀,然后加入活性剂,搅拌混合均匀得到硅基复合功能涂层浆料。
35.更优选地,溶剂为乙醇溶液,溶剂中乙醇的含量为20-60wt%。
36.更优选地,填料为sio2和y2o3的混合物,填料中sio2和y2o3以质量比1:0.1-0.4的比例混合。
37.更优选地,填料的使用量为溶剂的60-80wt%。
38.更优选地,粘结剂为醋酸锆。
39.更优选地,粘结剂的使用量为溶剂的20-40wt%。
40.更优选地,功能剂为表面改性剂。
41.更优选地,功能剂的使用量为溶剂的0.6-4.2wt%。
42.更优选地,硅基复合功能涂层浆料中还可加入增强剂,增强剂为二棕榈酸-3,4-吡哆醇二酯。按本发明方法制备及使用硅基复合功能涂层浆料时,向其中加入增强剂二棕榈酸-3,4-吡哆醇二酯后,可以增强硅基复合功能涂层浆料的抗滴淌性能及固化后的强度,具
有优异的增强效果。
43.更进一步优选地,增强剂的使用量为溶剂的0.4-3.2wt%。
44.一种具有硅基复合功能涂层的铸件,包括:基体以及附着基体上由上述浆料经干燥和/或烧结的硅基复合功能涂层,所述基体为金属和/或非金属固体材料。
45.本发明公开了上述表面改性剂在制备精密铸造和/或金属涂料中的用途。
46.本发明由八甲基环四硅氧烷、聚甲基氢硅氧烷、六甲基二硅醚制备得到含氢硅氧烷,由烯丙基缩水甘油醚与n-(3-羟丙基)酞亚胺制备得到烯丙基化合物,然后将含氢硅氧烷与烯丙基化合物在卡斯泰德催化剂的催化下得到表面改性剂,采用上述表面改性剂制备成硅基复合功能涂层浆料,因而具有如下有益效果:本发明得到的表面改性剂的润湿性能好;表面改性剂的乳化性能好;本发明得到的硅基复合功能涂层浆料干燥后的强度高;硅基复合功能涂层浆料的抗滴淌性能好。因此,本发明是一种润湿性能好、乳化性能好、可用于金属涂层材料的表面改性剂及其在制备硅基复合功能涂层材料中的用途。
附图说明
47.图1为表面改性剂的润湿性能测试结果图;
48.图2为表面改性剂的乳化性能测试结果图;
49.图3为硅基复合功能涂层浆料干燥后的强度图;
50.图4为硅基复合功能涂层浆料的滴淌质量图。
具体实施方式
51.以下结合具体实施方式和附图对本发明的技术方案作进一步详细描述:
52.实施例1:
53.一种硅基复合功能涂层浆料的制备方法,
54.含氢硅氧烷的制备:将八甲基环四硅氧烷、聚甲基氢硅氧烷、六甲基二硅醚混合,在氮气氛围下在温度50℃的条件下,加入浓硫酸,搅拌反应72h,反应完成后,调节ph至中性,在90℃的温度下处理6h,然后冷却至室温,抽滤除去杂质,得到含氢硅氧烷。聚甲基氢硅氧烷的使用量为八甲基环四硅氧烷的60wt%,六甲基二硅醚的添加量为八甲基环四硅氧烷的10wt%,浓硫酸的添加量为八甲基环四硅氧烷的2.4wt%。
55.烯丙基化合物的制备:将烯丙基缩水甘油醚与n-(3-羟丙基)酞亚胺混合,在氮气保护下,加入氢氧化钠,在温度95℃的温度下搅拌反应4h,反应完成后,室温下真空蒸馏除去水和低沸点物,得到烯丙基化合物。烯丙基缩水甘油醚的使用量为n-(3-羟丙基)酞亚胺的50wt%,氢氧化钠的使用量为烯丙基缩水甘油醚的1.6wt%。
56.表面改性剂的制备:在90℃的温度下,将卡斯泰德催化剂、含氢硅氧烷、烯丙基化合物加入异丙醇中,反应6h,反应完成后蒸馏除去溶剂异丙醇,得到改性有机硅烷表面活性剂。卡斯泰德催化剂的使用量为含氢硅氧烷的0.02wt%,含氢硅氧烷的使用量为异丙醇的20wt%,烯丙基化合物的使用量为异丙醇的30wt%。
57.硅基复合功能涂层浆料的配制:将填料和粘结剂加入溶剂中,搅拌混合均匀,然后加入活性剂,搅拌混合均匀得到硅基复合功能涂层浆料。溶剂为乙醇溶液,溶剂中乙醇的含量为50wt%,填料为sio2,填料的使用量为溶剂的70wt%,粘结剂为醋酸锆,粘结剂的使用
量为溶剂的30wt%,功能剂为表面改性剂,功能剂的使用量为溶剂的1.2wt%。
58.实施例2:
59.一种硅基复合功能涂层浆料的制备方法,
60.本实施例与实施例1相比,不同之处仅在于硅基复合功能涂层浆料的配制。
61.硅基复合功能涂层浆料的配制:将填料和粘结剂加入溶剂中,搅拌混合均匀,然后加入活性剂,搅拌混合均匀得到硅基复合功能涂层浆料。溶剂为乙醇溶液,溶剂中乙醇的含量为50wt%,填料为sio2和y2o3的混合物,填料中sio2和y2o3以质量比1:0.2的比例混合,填料的使用量为溶剂的70wt%,粘结剂为水玻璃,粘结剂的使用量为溶剂的30wt%,功能剂为表面改性剂,功能剂的使用量为溶剂的1.8wt%。
62.实施例3:
63.一种硅基复合功能涂层浆料的制备方法,
64.本实施例与实施例1相比,不同之处仅在于硅基复合功能涂层浆料的配制。
65.硅基复合功能涂层浆料的配制:将填料和粘结剂加入溶剂中,搅拌混合均匀,然后加入活性剂,搅拌混合均匀得到硅基复合功能涂层浆料。溶剂为乙醇溶液,溶剂中乙醇的含量为50wt%,填料为sio2和y2o3的混合物,填料中sio2和y2o3以质量比1:0.2的比例混合,填料的使用量为溶剂的70wt%,粘结剂为水玻璃,粘结剂的使用量为溶剂的30wt%,功能剂为kh602,功能剂的使用量为溶剂的2.4wt%。
66.实施例4:
67.一种硅基复合功能涂层浆料的制备方法,
68.本实施例与实施例1相比,不同之处仅在于硅基复合功能涂层浆料的配制。
69.硅基复合功能涂层浆料的配制:将填料和粘结剂加入溶剂中,搅拌混合均匀,然后加入活性剂,搅拌混合均匀得到硅基复合功能涂层浆料。溶剂为乙醇溶液,溶剂中乙醇的含量为50wt%,填料为sio2和y2o3的混合物,填料中sio2和y2o3以质量比1:0.2的比例混合,填料的使用量为溶剂的70wt%,粘结剂为醋酸锆,粘结剂的使用量为溶剂的30wt%,功能剂为表面改性剂,功能剂的使用量为溶剂的1.2wt%。
70.实施例5:
71.一种硅基复合功能涂层浆料的制备方法,
72.本实施例与实施例4相比,不同之处仅在于,硅基复合功能涂层浆料的配制中,功能剂的使用量为溶剂的3.6wt%。
73.实施例6:
74.一种硅基复合功能涂层浆料的制备方法,
75.含氢硅氧烷的制备:将八甲基环四硅氧烷、聚甲基氢硅氧烷、六甲基二硅醚混合,在氮气氛围下在温度50℃的条件下,加入浓硫酸,搅拌反应72h,反应完成后,调节ph至中性,在90℃的温度下处理6h,然后冷却至室温,抽滤除去杂质,得到含氢硅氧烷。聚甲基氢硅氧烷的使用量为八甲基环四硅氧烷的60wt%,六甲基二硅醚的添加量为八甲基环四硅氧烷的10wt%,浓硫酸的添加量为八甲基环四硅氧烷的2.4wt%。
76.烯丙基化合物的制备:将烯丙基缩水甘油醚与n-(3-羟丙基)酞亚胺混合,在氮气保护下,加入氢氧化钠,在温度95℃的温度下搅拌反应4h,反应完成后,室温下真空蒸馏除去水和低沸点物,得到烯丙基化合物。烯丙基缩水甘油醚的使用量为n-(3-羟丙基)酞亚胺
的50wt%,氢氧化钠的使用量为烯丙基缩水甘油醚的1.6wt%。
77.表面改性剂的制备:在90℃的温度下,将卡斯泰德催化剂、含氢硅氧烷、烯丙基化合物加入异丙醇中,反应6h,反应完成后蒸馏除去溶剂异丙醇,得到改性有机硅烷表面活性剂。卡斯泰德催化剂的使用量为含氢硅氧烷的0.02wt%,含氢硅氧烷的使用量为异丙醇的20wt%,烯丙基化合物的使用量为异丙醇的30wt%。
78.硅基复合功能涂层浆料的配制:将填料和粘结剂加入溶剂中,搅拌混合均匀,然后加入活性剂和增强剂,搅拌混合均匀得到硅基复合功能涂层浆料。溶剂为乙醇溶液,溶剂中乙醇的含量为50wt%,填料为sio2和y2o3的混合物,填料中sio2和y2o3以质量比1:0.2的比例混合,填料的使用量为溶剂的70wt%,粘结剂为醋酸锆,粘结剂的使用量为溶剂的30wt%,功能剂为表面改性剂,功能剂的使用量为溶剂的3.6wt%,增强剂为二棕榈酸-3,4-吡哆醇二酯,增强剂的使用量为溶剂的0.9wt%。
79.实施例7:
80.一种硅基复合功能涂层浆料的制备方法,
81.本实施例与实施例6相比,不同之处仅在于,硅基复合功能涂层浆料的配制中,增强剂的使用量为溶剂的2.6wt%。
82.实施例8:
83.一种具有硅基复合功能涂层的铸件的制备方法,
84.将硅基复合功能涂层浆料涂刷到金属固体表面,干燥。硅基复合功能涂层浆料源自实施例5。金属为铁。
85.实施例9:
86.一种具有硅基复合功能涂层的铸件的制备方法,
87.将硅基复合功能涂层浆料涂刷到金属固体表面,干燥,烧结。硅基复合功能涂层浆料源自实施例5。金属为铜。
88.实施例10:
89.一种具有硅基复合功能涂层的铸件的制备方法,
90.将硅基复合功能涂层浆料涂刷到非金属固体表面,干燥,烧结。硅基复合功能涂层浆料源自实施例5。非金属为陶瓷。
91.对比例1:
92.本对比例与实施例5相比,不同之处仅在于,硅基复合功能涂层浆料的配制中未使用功能剂。
93.试验例:
94.1.润湿性能测试
95.测试样品:实施例4中制备得到的表面改性剂。
96.根据国标gb/t 11983-2008的方法测试上述样品的润湿性能。将上述样品分别配制成100、200、300、400、500mg/l浓度的样品溶液进行测试。
97.本发明制备得到的表面改性剂的润湿性能如图1所示,可知,表面改性剂的润湿性能随着溶液中含量的增加而呈现上升趋势,表现为润湿时间减少,在表面改性剂的浓度为100mg/l时,润湿时间最长,所需要时间为4944s,在表面改性剂的浓度为500mg/l时,润湿时间最短,所需要时间为1096s。
98.设置对比组,以本发明制备得到的含氢硅氧烷作为对比样品。本发明将含氢硅氧烷配制成500mg/l的浓度,进行润湿性能测试,所需要时间1832s。
99.2.乳化性能测试
100.测试样品:实施例4中制备得到的表面改性剂。
101.将上述样品分别配制成100、200、300、400、500mg/l浓度的样品溶液,取40ml上述样品溶液与40ml液体石蜡加入100ml量筒中,以90度角大幅度剧烈振荡5次,静置再重复3次。在最后一次振荡停止的瞬间开始记录至水相分出10ml水为止。重复多次得到平均值。表面活性剂的分水时间越长,表明其乳化能力越强。
102.本发明制备得到的表面改性剂的乳化性能如图2所示,可知,表面改性剂的润湿性能随着溶液中含量的增加而呈现上升趋势,表现为分水时间延长,在表面改性剂的浓度为100mg/l时,分水时间最短,所需要时间为17s,在表面改性剂的浓度为500mg/l时,润湿时间最长,所需要时间为528s。
103.设置对比组,以本发明制备得到的含氢硅氧烷作为对比样品。本发明将含氢硅氧烷配制成500mg/l的浓度,进行乳化性能测试,所需要时间319s。
104.3.耐酸碱盐稳定性
105.测试样品:实施例4中制备得到的表面改性剂。
106.将上述样品配制成质量分数为1%的样品溶液,取50ml溶液,调节ph至5,在25℃的温度下测试上述样品的稳定性,观察是否有分层、浮油和粘壁现象。测试时间72h。
107.将上述样品配制成质量分数为1%的样品溶液,取50ml溶液,调节ph至9,在25℃的温度下测试上述样品的稳定性,观察是否有分层、浮油和粘壁现象。测试时间72h。
108.将上述样品配制成质量分数为1%的样品溶液,溶液中加入氯化钾拿含量达到2wt%,取50ml溶液,调节ph至5,在25℃的温度下测试上述样品的稳定性,观察是否有分层、浮油和粘壁现象。测试时间72h。
109.本发明制备得到的表面改性剂具有乳化性能,并且具有优异的耐酸、耐碱及耐盐的性能,经上述方法测试72h,未观察到分层、浮油和粘壁现象,稳定性佳。
110.4.强度测试
111.测试样品:各实施例和对比例制备得到的硅基复合功能涂层浆料,将硅基复合功能涂层材料涂敷到玻璃片上,烘干。
112.将涂4粘度杯安放在距离上述样品1000mm的地方,测试样品倾斜放置与水平面成45度角。涂4粘度杯内部装有沙子。测量时粘度杯向测试样品上落沙,直到测试样品上出现2-4mm左右的圆孔为止。收集落下的沙子,称出总质量作为判断涂层强度的性能指标。
113.本发明制备得到的硅基复合功能涂层浆料的强度测试结果如图3所示,其中,实施例4制备的硅基复合功能涂层材料涂敷到玻璃片上烘干后的强度为98g,实施例5制备的硅基复合功能涂层材料涂敷到玻璃片上烘干后的强度为104g,对比例1制备的硅基复合功能涂层材料涂敷到玻璃片上烘干后的强度为87g,实施例5与对比例1相比,表明有制备硅基复合功能涂层材料中使用表面改性剂后,具有更优的效果,表现为硅基复合功能涂层材料涂敷到玻璃片上烘干后的强度提升,相比于对比例1,实施例5制备得到的硅基复合功能涂层材料涂敷到玻璃片上烘干后的强度提高了19.54%;实施例6制备的硅基复合功能涂层材料涂敷到玻璃片上烘干后的强度为113g,实施例7制备的硅基复合功能涂层材料涂敷到玻璃
片上烘干后的强度为119g,实施例7与实施例5相比,实施例7制备得到的硅基复合功能涂层材料涂敷到玻璃片上烘干后的强度提高了14.42%,表明增强剂二棕榈酸-3,4-吡哆醇二酯的使用,提高了硅基复合功能涂层材料涂敷到玻璃片上烘干后的强度。
114.5.抗滴淌性测试
115.测试样品:各实施例和对比例制备得到的硅基复合功能涂层浆料。
116.采用的是80
×
30mm的载玻片40
×
30mm的面积浸入上述样品中,夹住载玻片上端垂直取出,让其表面涂料自由滴到准备好的玻璃片上。最后称量出滴落涂料的质量即涂料的滴淌性。质量越小,抗滴淌性越好。
117.本发明制备得到的硅基复合功能涂层浆料的抗滴淌性测试结果如图4所示,其中,实施例4制备的硅基复合功能涂层材料于载玻片上的滴淌质量为0.39g,实施例5制备的硅基复合功能涂层材料于载玻片上的滴淌质量为0.36,对比例1制备的硅基复合功能涂层材料于载玻片上的滴淌质量为0.46g,实施例5与对比例1相比,表明有制备硅基复合功能涂层材料中使用表面改性剂后,具有更优的效果,表现为制备的硅基复合功能涂层材料于载玻片上的滴淌质量的下降,相比于对比例1,实施例5制备的硅基复合功能涂层材料于载玻片上的滴淌质量下降了15.21%,即抗滴淌性能提高了15.21%;实施例6制备的硅基复合功能涂层材料于载玻片上的滴淌质量为0.32g,实施例7制备的硅基复合功能涂层材料于载玻片上的滴淌质量为0.28g,实施例7与实施例5相比,实施例7制备的硅基复合功能涂层材料于载玻片上的滴淌质量下降了28.21%,即抗滴淌性能提高了28.21%,表明增强剂二棕榈酸-3,4-吡哆醇二酯的使用,提高了硅基复合功能涂层材料的抗滴淌性能。
118.以上实施方式仅用于说明本发明,而并非对本发明的限制,本领域的普通技术人员,在不脱离本发明的精神和范围的情况下,还可以做出各种变化和变型。因此,所有等同的技术方案也属于本发明的范畴,本发明的专利保护范围应由权利要求限定。